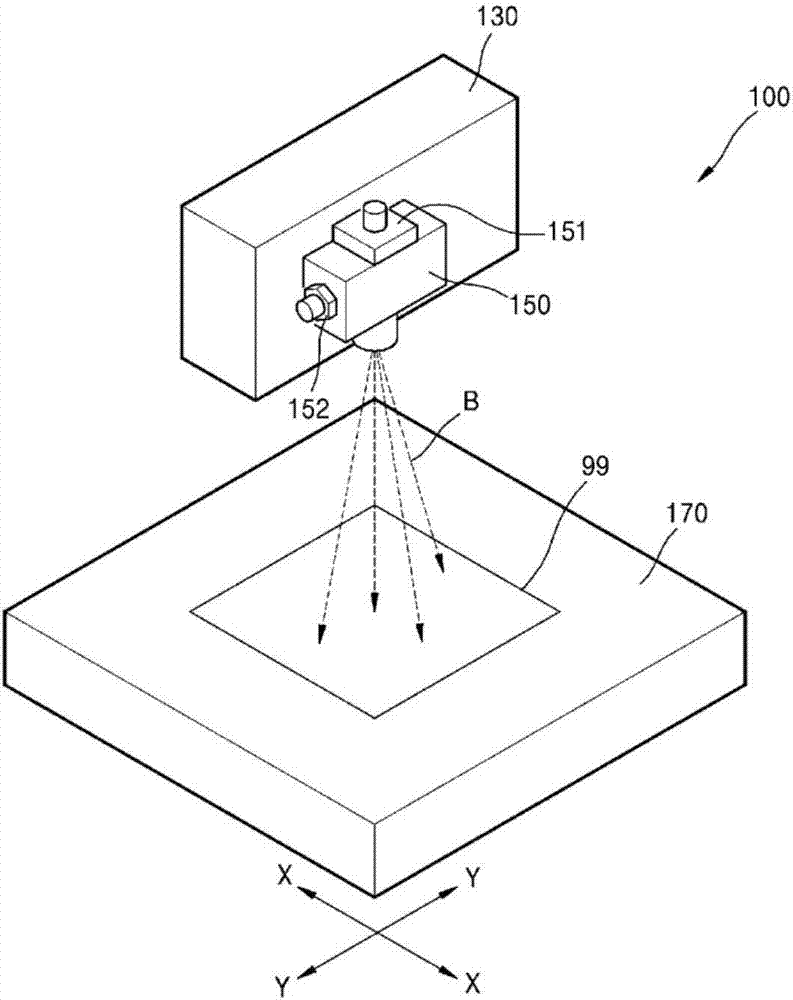
本发明涉及使用激光束的连续加工方法,详细地,本发明涉及根据低速驱动器和高速驱动器的多位置控制的激光加工方法和使用该方法的激光加工系统。
背景技术:一种现有方法是以适应高速驱动器的加工范围的方式将整个加工对象区域面板化为小区域后,将低速驱动器移动至各个面板位置,并通过高速驱动器进行加工的方法。该方法为了将低速驱动器移动至面板位置并停止需要花费大量的时间,且需要根据加工数据分离界限,因此不具有效率。为了解决该问题,提出将低速驱动器和高速驱动器组合并进行连续加工的方法,该方法是为了连续加工将每一时刻的加工路径过滤为高速和低速,并同时给予位置指令的方式。该方式的问题是在处理与不加工而简单移动的情况相对应的加工图案位置间的移动路径时,难以确定速度。考虑加工时间,确保下一个图案在高速驱动器的范围内的情况下,需要将简单移动速度设定为高速驱动器的最大速度,否则,需要将移动速度设定为低速驱动器的最大速度。此时,未能正确地判断移动速度,从而针对低速驱动器根据其不能行进的路径设定为高速驱动器的速度的情况下,发生加工不良,为了防止这种情况,在许多情况下,只能将简单移动速度设定为低速驱动器的最大速度,从而使生产率降低。此外,需要针对所有路径进行移动,因此可能导致不需要的移动或振动等。
技术实现要素:技术问题本发明提出根据高速驱动器和低速驱动器的有效的反馈控制,充分利用高速驱动器的加工范围,从而能够进行最大的高速加工的方法。技术方案根据本发明的利用高速驱动器和低速驱动器进行激光加工的方法包括下列步骤:基于相邻的多个图案中的至少一个图案来设定加工区域;获得所述加工区域内的至少一个图案的中间位置,并将所述低速驱动器定位在所述中间位置;以及在所述低速驱动器开始向中间位置移动后,所述高速驱动器对至少一个加工图案进行加工。根据本发明的一实施例,在设定所述加工区域的步骤中,利用所述高速驱动器的区域,在所述区域内尽可能多地包括能够加工的图案。根据本发明的另一实施例,在设定所述加工区域的步骤中,考虑所述高速驱动器的区域内部的加工图案和高速驱动器的区域外部的加工图案的位置,可以设定加工区域,从而使至外部的加工图案的移动距离最佳。根据本发明的另一实施例,所述区域为所述高速驱动器能够加工且用于计算目标位置的最大区域。根据本发明的另一实施例,在所述低速驱动器向中间位置移动期间,所述高速驱动器加工工件的图案,所述高速驱动器接收对所述低速驱动器的位置的反馈并校正所述低速驱动器的位置。在本发明的另一实施例中,所述中间位置是所述加工区域的区域平均值。根据本发明的另一实施例,所述图案是激光打开并关闭期间激光所加工的形状。根据本发明的其它形式的激光加工方法,包括:第一步骤:获得复数个加工对象图案中相邻的多个图案的中间位置;第二步骤:使低速驱动器移动至所述中间位置;以及第三步骤:在所述中间位置中驱动高速驱动器,从而加工所述多个加工图案,其中,重复所述第一步骤至所述第三步骤,从而对所述复数个加工对象图案进行激光加工。根据本发明的具体实施例,在所述第三步骤中,考虑新的下一个被加工图案的位置,获得新的下一个中间位置,从而使所述低速驱动器移动至所述新的下一个中间位置。根据本发明的另一具体实施例,所述多个图案位于以所述低速驱动器的位置为中心的、所述高速驱动器能够加工的加工区域中。根据本发明的另一具体实施例,所述多个图案位于设置在所述加工区域内的搜索区域内。根据本发明的另一具体实施例,所述中间位置定义在所述多个图案所在的搜索区域内。根据本发明的另一具体实施例,所述复数个图案通过按照连续的一个线性图案的区间划分而定义。根据本发明的另一具体实施例,在所述线性图案的加工方向上,所述低速驱动器的位置相比所述高速驱动器的位置超前。根据本发明的另一具体实施例,所述低速驱动器通过非加工区域朝向所述线性图案移动时,所述高速驱动器朝向所述线性图案的前端,所述低速驱动器从所述前端朝向在加工方向上超前的位置。一种根据本发明的激光加工系统,所述激光加工系统执行所述的激光加工方法,所述系统包括:生成激光的激光器系统;装载工件的低速驱动器;高速驱动器,所述高速驱动器使来自所述激光器系统的激光集中在所述工件上,从而针对所述工件进行预定图案的激光加工;以及控制主机,所述控制主机控制所述低速驱动器和所述高速驱动器。此外,根据本发明的另一形式的激光加工系统,在包括低速驱动器和高速驱动器的激光加工装置中,包括:控制部,所述控制部进行控制,使得基于相邻的多个图案中的至少一个图案来设定加工区域,获得所述至少一个图案的中间位置,并将所述低速驱动器定位在所述中间位置,在所述低速驱动器开始向中间位置移动后,所述高速驱动器对至少一个图案进行加工。有益效果在根据本发明的激光加工方法中,搜索当前需要加工的目标位置和以后需要加工的下一个目标位置,从而在高速驱动器能够加工的范围内具有尽可能多的图案,此外,考虑针对以后的行进方向的方向性,低速驱动器找到最佳的路径(考虑加工方向的超前位置),从而使移动最小化。此外,在简单移动的情况下,假设高速驱动器具有最大速度,若需要加工的位置已经在加工范围内,则立刻进行加工,且若需要低速驱动器进一步移动,则通过实时检查是否可以开始加工的方法,可以缩短加工时间。通过监控低速驱动器的反馈,控制高速驱动器的输出,从而可以进行实时检查是否可以开始加工的方法。若低速驱动器还未处于能够加工的位置,则高速驱动器能够在能够进行自身操作的边界面中移动并进入加工区域时,补偿低速驱动器的反馈,同时移动至加工位置。这样的操作实时应用至高速驱动器,从而能够获得优异的加工品质和高的生产率。面板化并进行加工的现有方法,需要在低速驱动器停止后进行加工,存在相当多的非加工时间,与此相反,本发明的连续加工不使用面板化的概念而能够进行更快地加工。此外,与滤波后的连续位置数据简单地分配至低速驱动器、高度驱动器的现有方法不同,本发明考虑低速驱动器的反馈,能够实时控制高速驱动器的输出和实际加工的开始时间。这意味着在加工和加工之间的非加工区间中,与非加工区间的距离无关,高速驱动器能够以快的速度移动,补偿低速驱动器的输出和实际移动间的误差,从而能够缩短整体加工时间。此外,考虑高速驱动器的加工范围,检索以后需要加工的形状的位置,从而包括尽可能多的形状,缩短移动路径且能够提前移动至下一个位置。这种最佳位置可以补充低速驱动器的反应性,由于不照原样沿着加工轨迹,因此减少不需要的移动和时间,从而可以使生产率最大化。附图说明图1是执行根据本发明的激光加工方法的激光加工系统的局部透视图。图2是根据本发明的激光加工系统的示意性框图。图3是说明根据本发明的激光加工方法的框图。图4至图12是说明根据本发明的激光加工方法的图。具体实施方式下文,将参照附图详细描述根据本发明的激光加工方法的优选实施例。参照图1,激光加工系统(LaserMachiningSystem)100通常也称为激光打标机(marker),包括:工作台系统(以下称为工作台)170,在所述工作台系统中装载工件99;激光器系统(LaserSystem)130,所述激光器系统130生成对所述工件99进行机械加工所需的高能量状态的激光束(LaserBeam)B;以及扫描器系统(以下称为扫描器)150,所述扫描器系统150具有多个电流计(151,152),所述电流计(151,152)使来自所述激光器系统130的激光束集中或定位至工件的特定位置。所述工作台170作为低速驱动器,在与工件99的平面平行的方向的X-Y坐标上移动,所述扫描器系统150通过两个电流计将来自所述激光器系统130的激光束B集中或定位在工件99的表面的特定位置。在本发明中,低速驱动器通常可以选自已知的X-Y台、混合工作台或门式工作台中的任一者。图2是示意性地示出所述激光加工系统100的整体结构的框图。根据本发明的激光加工系统100基本包括如上所述的装载工件99的工作台170及用于驱动该工作台170的工作台控制部160。参照图2,激光加工系统100基本包括生成对工件99进行机械加工所需的高能量状态的激光束B的激光器系统130及驱动该激光器系统130的激光器驱动器120、以及装载通过所述激光束加工的工件99的工作台170及用于驱动该工作台170的工作台控制部160。这种激光加工系统100还包括扫描器150及驱动该扫描器150的扫描器驱动部140,所述扫描器150以光学方式高速控制从所述激光器系统130射出的激光束的行进方向从而将激光束集中或定位在所述工件99的特定位置。此外,所述激光加工系统100还包括控制主机(ControlHost)110,所述控制主机110通过所述激光器驱动器120和扫描器控制部140控制所述激光器系统120和所述扫描器系统130。在上述结构中,所述工作台170利用设置在内部的编码器(encoder)向控制主机110反馈工作台及其上装载的工件99的位置或坐标信息。在激光加工时,实时接收关于连续变更工件的位置的工作台170的移动坐标的反馈信号的控制主机110,为了将激光束准确定位在连续移动的工作台170上的工件99的特定位置的表面,反映工作台的位置信息,控制扫描器系统150。也就是说,通过扫描器系统150确定的激光束的定位坐标通过根据工作台170的移动距离而被补偿,因此,即使工作台被连续驱动,针对工作台上的工件定位激光束也在目标位置上实现。本发明中,搜索当前需要加工的位置和以后需要加工的位置,从而在高速驱动器能够加工的加工范围内具有尽可能多的图案,此外,考虑针对以后的行进方向的方向性,低速驱动器找到最佳的轨迹,从而使移动最小化。补充地,搜索当前需要加工的目标位置和以后需要加工的下一个目标位置,从而在高速驱动器能够加工的范围内具有尽可能多的图案,此外,考虑针对以后的行进方向的方向性,低速驱动器找到最佳的路径(考虑加工方向的超前位置),从而使移动最小化。在本发明中,在低速驱动器操作期间,若在高速驱动器的加工区域内进入图案,则立即开始激光加工。此时,根据低速驱动器的位置移动作为反馈反映高速驱动器的位置控制。如众所周知的,相比具有100us至400us的反应延迟的高速驱动器,低速驱动器发生相当长的约20msec至400msec的反应延迟。作为低速驱动器的工作台到达目标位置所需的加速时间和停止在目标速度消耗的减速时间相当长,而且,最大速度也被限制。加减速特性具有约0.1g~3g的范围,最大速度通常为0.5[m/sec]~2[m/sec]的范围。这种工作台的反应延迟通常为约20msec至400msec。这种反应延迟通过作为高速驱动器的扫描器而实现补偿,尤其,根据工作台的移动的位置变化通过能够高速驱动的扫描器而得到补偿。所述扫描器控制部确定来自工作台的反馈和扫描器的位置。此时,反映扫描器的反应延迟。图3示出在根据本发明的激光加工系统中的示意性控制流程图,图4是根据本发明的激光加工方法的整体流程图。在整个激光加工中,在控制主机110中,基于整个区域内的各个加工位置,考虑扫描器150的加工范围或工作台的反应性(延迟反应),计算低速驱动器的目标位置(S31)。这种目标位置的计算在针对加工范围内的一个图案的激光加工进行的工作台的驱动期间也连续执行。在这样计算目标位置后,接收来自低速工作台170的反馈,从而比较相对于整个加工区域的实际加工区域(S32)。而且,考虑实际加工位置和高速驱动器的加工范围确定低速驱动器的目标位置(S33,S36),并将其输出值扫描器和工作台。此时,作为高速驱动器的扫描器系统150的实际位置通过作为低速驱动器的工作台170的反馈(工作台的移动量信息或位置信息、FB)进行补偿(S34)。也就是说,将扫描器S150的位置补偿(S34)连续操作的工作台的移动距离或位置,从而确定扫描器的实际位置、即激光岀射点。此处,扫描器的位置(激光岀射点)指的是根据针对工件的扫描器的物理位置确定的加工范围内,激光束向实际工件岀射的位置,该位置是激光束所定位的工件的表面的一点。如上所述,低速驱动器相比高速驱动器加减速时间长,最大速度也慢。由此,在整个加工中,重要的是,尽可能利用低速驱动器的最佳位置移动和高速驱动器的快的特性,从而提高效率。计算低速驱动器的最佳位置的方法,根据加工图案可分为加工范围内的小图案(形状)和加工范围外的大图案。此处所说的小图案作为一示例可以是小孔,大图案可以是包括复杂的图形的图案。在下面实施例的说明中,加工小图案(即,小孔)的方法作为实施例进行说明。为了优异的加工品质和提高效率,加工孔的加工范围的条件是重要的。首先,如图4所示,加工范围大体可以分为三种。这三种加工范围是高速驱动器150能够进行最大移动的整个区域51、用于开始实际加工的加工区域52、最后用于找到低速驱动器150的移动目标位置的搜索区域53。上述三种加工范围需要满足下列条件。搜索区域<加工区域<整个区域-孔直径在本发明中,区域包括搜索区域和加工区域,在此,搜索区域是为了计算目标位置而使用的区域,作为加工对象的孔的中心所在的区域。若向目标位置移动的低速驱动器接近目标位置,则需要在减速的同时接近目标位置,因此在获得减速驱动器的目标位置时所使用的搜索区域的尺寸(宽度)需要比实际加工区域的尺寸(宽度)小。若搜索区域具有与加工区域相似的尺寸,则低速驱动器的目标位置的范围变宽,但是低速驱动器到达位置反而可能需要更多的时间,且由于低速驱动器的过冲等特性,也可以发生加工不良。因此,搜索区域为加工区域的约1/2~3/4是合适的。此外,加工区域成为开始加工的条件,其尺寸需要比整个区域的尺寸减去孔的直径而获得的值小,其通过图5的说明可以更好地理解。为了加工如图5所示的孔61,低速驱动器从开始位置62朝向孔61移动。此时,正在移动的低速驱动器的位置63和孔61的中心的差(w)位于用于实际加工的加工区域52中时,开始加工,由于需要基于孔的中心绘制图案,因此需要确保孔61的直径的尺寸。以这样的理由,加工区域52需要比整个区域减去孔的直径而获得的值小。此外,考虑低速驱动器的过冲等特性,有利的是,附加地确保微小的距离裕度。针对使用上述搜索区域53对低速驱动器的最佳位置进行计算的方式进行说明。参照图6可知所计算的低速驱动器的移动形式或轨迹。高速驱动器进行移动,且需要加工的位置、即孔的(加工)位置称为①至⑨时,实际低速驱动器移动的位置分别是1"~9"。在图6中示出,低速驱动器不是完全跟随高速驱动器的移动路径,而是沿最佳路径73移动。计算低速驱动器的移动路径73的方法是这样的方法:利用高速驱动器的移动路径中(即加工范围内)的多个作为加工对象的孔的位置,寻找这些孔之间的中间位置(中间值)。然而,基于当前高速驱动器的位置,只在加工范围内,寻找中间值(中间位置)。作为另一实施例,中间位置或中间值也可为“区域平均值”。区域平均值为加工区域的位置中心值或平均值。例如,在①的低速驱动器的位置中形成(定义)搜索区域“71”。在所述搜索区域“71”的范围内包括孔的位置②、③、④,因此使低速驱动器移动至作为①~③或①~④位置的中间位置的所计算的任一位置(即1")。①加工结束后,在高速驱动器向②移动时,向还未加工的孔位置②,③,④的中间位置2"移动。在低速驱动器向2"移动的过程中,进行针对孔位置②的加工。在这种低速驱动器的移动和高速驱动器的移动(加工)进行的过程中,搜索新定义的搜索区域内的孔,通过此持续进行新的中间值的计算。孔位置②加工结束后,在下一个孔的位置③新定义的搜索区域72内存在的孔为③~⑦。因此,计算③~⑦的中间位置3",因此,低速驱动器向3"移动。若以此方式计算,则可获得在高速驱动器向①~⑨移动期间,低速驱动器沿如73的路径移动的结果。根据本发明,低速驱动器的最佳路径(低速驱动器的移动轨迹,73)没有跟随实际需要加工的孔的位置(即,位置①~⑨),而是基于各个孔,寻找(计算)作为加工范围内的最佳位置的中间位置并进行移动。由此,具有慢的反应性的低速驱动器可以移动最短距离,从而防止不需要的移动,以这种低速驱动器的移动轨迹为中心的其周围的孔的加工可以利用高速驱动器的快的特性来执行。以下,作为根据本发明的另一实施例,在上述寻找中间位置的方式中,进一步积极利用搜索区域的概念,参照图7说明使低速驱动器的路径更优化的方法。参照图7,在搜索区域81内存在孔①~④。此时,在位置①中,在搜索区域81内,通过孔位置①~③计算中间位置,从而可以计算低速驱动器的目标位置1"。在通过高速驱动器完成加工位置①后,使高速驱动器向位置②移动,同时通过孔位置②~③可以找到其中间位置2"。低速驱动器向位置2"移动,在加工位置②的孔后,在高速驱动器向位置③移动时,用于计算低速驱动器的移动位置的其它孔位置不存在,而搜索区域外存在孔位置④。在这种情况下,孔位置③成为低速驱动器的下一个位置3"。在这种状态下,在高速驱动器向孔位置④移动的情况下,低速驱动器的下一个位置4"也与孔位置④一致。在此,连接低速驱动器的移动位置1"至4",绘制移动路径82并进行分析。在孔位置①的基准中,孔②~③包含在搜索区域内,孔④没有包含在搜索区域内。与此相比较时,在计算低速驱动器的目标位置时,考虑孔④的方向设定搜索区域位置,则可以使低速驱动器的位置更靠近④。参照图8,与图7相同,存在孔①~④。与如图5所示使搜索区域的中心和孔的中心一致而确定范围不同,搜索区域(91,92,93)的中心被设定为尽可能靠近地朝向区域外存在的孔④。这样的话,以搜索区域91的中心为中心,孔④位于与孔①、②相反的方向。也就是说,例如,如图8所示,使孔①、②位于搜索区域的第一象限内,使孔④的位置朝向对角线的相反方向的第三象限。此时,优选地,使孔①、②位于搜索区域91的边界,将低速驱动器的目标位置设定为与孔④最近的1"。也就是说,在本发明中,在定位搜索区域时,将搜索区域设置为靠近搜索区域外的孔位置,并进行孔加工,同时将搜索区域设定为越来越靠近搜索区域外的孔位置。另一方面,在通过高速驱动器完成加工孔①后,在高速驱动器向孔②移动时,设定搜索区域92使得孔②也位于搜索区域的边界,从而计算低速驱动器的下一个移动位置2"。而且,激光加工孔②后,高速驱动器向孔③的移动也以与上述相同的方式设定,设定搜索区域93并求低速驱动器的移动位置3"。此时,若将1"至4"全部连接,则可以获得低速驱动器的移动路径95。若以这种方式计算低速驱动器的目标位置,则考虑范围外的下一个孔的方向,可以使低速驱动器的目标位置更靠近范围外的下一个孔。这使低速驱动器的移动优化,从而可以获得更好的效率。下面,针对大形状的低速驱动器的最佳位置计算方法进行说明。低速驱动器的反应时间为约20msec至400msec,与高速驱动器的100usec至400usec比较差异较大。通常,例如,实际加工使用激光的脉冲时,在品质方面优选间隔开配置。这考虑低速驱动器的反应性,来配合与高速驱动器的同步是重要的。参照图9对此进行说明。如果发出低速驱动器向目标位置101移动的命令,则此时实际位置是102。此时,目标位置和实际位置之间的时间差称为反应时间,时间乘以速度的值为根据反映性而生成的距离差103。如果补偿由这种反应性引起的距离差103,来控制低速驱动器的输出,则在没有另外的延迟的情况下可以配合高速驱动器的同步。参照图10,需要加工从位置111a到位置114a的曲线或直线形式的线性图案,在本实施例中为直线图案。该直线图案相比高速驱动器的加工范围大(长),因此,需要在低速驱动器移动的同时,以高速驱动器的加工范围为单位,将直线划分为多个直线(单位图案),从而进行加工。在本实施中,将长的直线例示为一个加工图案,然而本发明不限于此,其也包括曲线或曲线和直线结合而成的线性图案,作为加工对象。当给出各种这样的直线时,为了考虑低速驱动器的反应性为进行阶段性输出时,以任意的长度(l)划分。以竖直的虚线划分的区间可以被理解为各个图案。其结果是,在这里也包括利用多个图案的位置来求中间位置的概念。然而,由于图案为直线,因此,中间位置位于直线状的图案上。利用按照这样划分的区间的图案位置,在各个当前位置中,考虑反应性,计算超前的位置,从而可以找到低速驱动器的目标位置。该目标位置位于当前图案和与该图案连续的下一个图案之间。例如,在位置111a中,考虑反应性,假设低速驱动器的目标位置为111b,即,从位置111b减去位置111a而形成的距离差为由反应时间引起的距离差。同样地,在位置112a中,将低速驱动器控制(移动)到沿加工方向在该位置前的位置112b。如上所述,根据高速驱动器的各个当前位置,低速驱动器的目标位置也继续重新计算,从而存储为位置数据图。参照图11,从当前位置122出发,假设需要加工具有从前端124a到后端128的长度的非常长的直线(图案)。此时,在具有加工区域(设定为比高速驱动器能够移动的整个区域稍微小,121)时,具有高速驱动器的初始目标位置(直线图案的前端,124a)和低速驱动器的考虑反应性的目标位置(124b)。同样,124b-124a成为根据反应性而生成的距离差。在位置、低速驱动器的起始点122中,高速驱动器在非加工区域中的速度快,因此,与开始同时地,位于朝向高速驱动器的目标位置124a的加工区域的边界123。可以看出,低速驱动器在朝向比高速驱动器的目标位置124a超前的目标位置124b的同时,朝向高速驱动器或开始地点124a逐渐移动。若从位置126的位置观看,则不管低速驱动器正朝向目标位置124b移动,高速驱动器的目标位置124a进入加工范围内。通常,在非加工区域中,可以将高速驱动器的速度设定得较快,因此高速驱动器更快到达目标位置。此时,在加工控制部11中,交换激光和高速驱动器的输出,并开始实际加工。若改变高度驱动器的目标位置125a,则根据其改变低速驱动器的目标位置125b,从而可以具有等间隔的加工品质。参照图12,可以看出,从与图11不同的方向开始。也同样地,低速驱动器在出发时间131朝向考虑反应性而形成的目标位置134b移动,且在低速驱动器接近133时,即在进入加工范围内时,速度较快的高速驱动器已经到达目标位置134a,并开始加工。如上所述,若将高速驱动器的输出改变为135a,则低速驱动器的目标位置也改变为135b。计算低速驱动器的目标位置的这种方式,在使高速驱动器和低速驱动器同步的同时,阻止低速驱动器的不需要的移动动作,从而影响整体速度的提高。应当理解,虽然已参照附图中所示的实施例描述了本发明,但这仅是示例性的,本领域的普通技术人员能够进行各种变型和等同的其它实施例。因此,本发明的真正的保护范围仅由所附的权利要求书来进行限定。