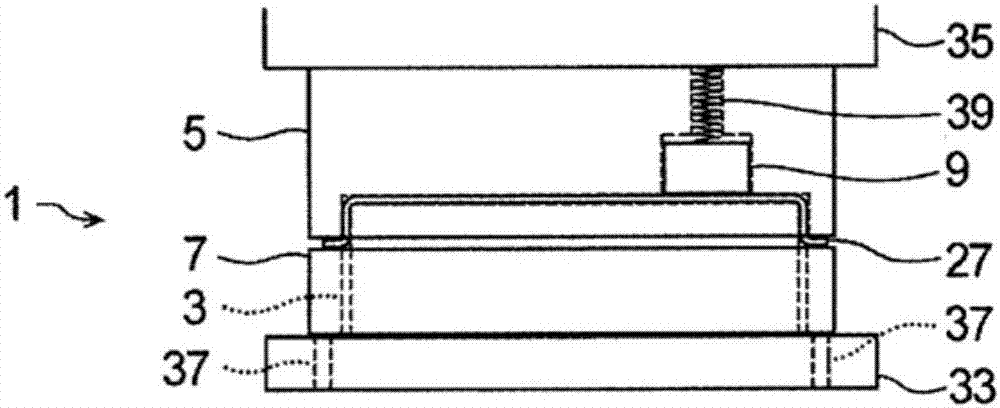
本发明涉及用于利用模具(sheetformingdie)对金属板(metalsheet)进行冲压成型(sheetforming)以制造冲压成型部件的冲压成型方法,所述冲压成型部件在俯视时具有L字形状,并且具备顶板部(topportion)、形成于该顶板部两侧的纵壁部(sidewallportion)、与该纵壁部连续地形成的凸缘部(flangeportion)。
背景技术:通常,在通过冲压成型从金属板制造作为汽车的车体骨架部件(vehiclebodyframeparts)的前柱(pillar)加强件(reinforcement)等具有L字形状部的产品的情况下,使用由冲头(punch)、冲模(die)及压坯料环(防皱)(blankholder)构成的模具来进行。在该情况下,在利用冲模和压坯料环将金属板的周围全部压紧的状态下,使冲头与冲模之间的距离接近,对金属板实施拉深加工(drawing)。在这样的冲压成型中,在冲压成型具有急剧弯曲的弯曲部(bentportion)的L字形状部件的情况下,容易在L字形状部的顶板部产生褶皱(wrinkles)。若提高冲模和压坯料环的压紧力,则抑制该褶皱,但另一方面容易在部件的肩部(shoulderportion)或纵壁部产生裂纹。特别是,近年来,为了实现汽车车体的安全性提高和轻量化(weightreductionofautomotivebody),作为成型坯料(blank)的金属板的强度在不断提高,不能期待像以往的软质钢板那样的延展性(ductility)。因此,针对冲压成型时的裂纹和褶皱的防止对策,成为重要的课题。作为冲压成型L字形状部件的技术,在专利文献1中提出了,首先进行较浅的拉深成型然后利用其他模具进一步进行弯曲成型来形成最终产品形状的方法。另外,在专利文献2中,作为涉及具有L字形状的骨骼部件的其他技术,提出了使用由冲模模具、垫片(pad)及弯曲模具构成的模具单元的冲压成型方法。现有技术文献专利文献专利文献1:国际公开第2012/070623号小册子专利文献2:国际公开第2011/145679号小册子
技术实现要素:发明所要解决的课题然而,在专利文献1、2所记载的技术中,仅能够制作与其他部件接合的L字弯曲部具有顶板、与该顶板延伸设置的一个纵壁、再与该纵壁连接的一个凸缘面的形状的部件(part),而不能制作在L字形状部件的整个长度内形成为帽形截面(hat-shapedcrosssection)形状的L字形状部件。本发明是为解决上述课题而完成的,其目的在于提供一种冲压成型方法,即使将由980MPa级以上的延展性低的超高强度的高强度材料(high-strengthsteelsheet)形成的金属板用作胚料、也能够得到在整个长度内形成为帽形截面的L字形状部件。用于解决课题的技术方案本发明的冲压成型方法用于利用模具对金属板进行冲压成型以制造冲压成型部件,所述冲压成型部件在俯视时具有L字形状,并且具备顶板部、形成于该顶板部两侧的纵壁部、与该纵壁部连续地形成的凸缘部,所述冲压成型方法的特征在于,包括第一冲压成型工序和第二冲压成型工序,在所述第一冲压成型工序中,在具有第一冲头、第一冲模、第一压坯料环以及垫片的第一模具中配置该金属板,使得所述金属板上的与所述L字形状的短边的端部相当的部位不会接触第一冲模和所述第一压坯料环,并且通过利用所述垫片压紧顶板部的一部分,将该金属板冲压成型为具有中间形状的第一冲压成型部件;在所述第二冲压成型工序中,利用具有第二冲头及第二冲模的第二模具将通过该第一冲压成型工序成型的第一冲压成型部件冲压成型为顶板部及纵壁部具有与所述冲压成型部件相同的形状的第二冲压成型部件;关于在所述第一冲压成型工序中成型的所述第一冲压成型部件,包括L字形状的弯曲部的外侧的纵壁部在俯视时比所述冲压成型部件的纵壁部向外侧呈圆弧状鼓出,该鼓出的圆弧的曲率半径(radiusofcurvature)大于所述冲压成型部件的L字形状的弯曲部的曲率半径,并且,L字形状的弯曲部的顶板部的外侧比所述冲压成型部件的顶板部的外侧鼓出,且与鼓出的顶板部相连的肩部在侧视时的截面中的曲率半径大于所述冲压成型部件的L字形状的弯曲部的与顶板部的外侧相连的肩部在侧视时的截面中的曲率半径。在上述本发明的冲压成型方法中,在所述第一冲压成型工序中,由所述垫片压紧的所述顶板部的一部分是至少包括L字形状的弯曲部且与所述第一冲压成型部件中的顶板部的鼓出的部位不发生干涉的部位。在上述本发明的冲压成型方法中,在所述第一冲压成型工序中利用所述垫片开始压紧的时机为,所述第一冲头位于相对于成型深度0%至50%的位置,所述成型深度是指从所述第一冲头开始接触所述金属板的位置至下极限点位置。在上述本发明的冲压成型方法中,在所述第一冲压成型工序中纵壁部与顶板部的鼓出量是使所述第一冲压成型部件的L字形状的弯曲部的鼓出部分的面积相对于与该鼓出部分对应的所述冲压成型部件的L字形状的弯曲部的面积的面积比率增加0.3%至1.2%的量。发明效果根据本发明,即使将由980MPa级以上的延展性低的超高强度的高强度材料(high-strengthsteelsheet)形成的金属板用作板材,也能够得到在整个长度内形成为帽形截面的L字形状部件。附图说明图1A是本发明的一个实施方式的冲压成型方法的说明图。图1B是本发明的一个实施方式的冲压成型方法的说明图。图1C是本发明的一个实施方式的冲压成型方法的说明图。图1D是本发明的一个实施方式的冲压成型方法的说明图。图2是通过本发明的一个实施方式的冲压成型方法成型的冲压成型部件的立体图。图3是通过本发明的一个实施方式的冲压成型方法成型的冲压成型部件的俯视图。图4是沿图3的箭头A-A的向视剖视图。图5是通过本发明的一个实施方式的冲压成型方法的第一冲压成型工序成型的第一冲压成型部件的俯视图。图6是通过本发明的一个实施方式的冲压成型方法的第一冲压成型工序成型的第一冲压成型部件的主要部分的说明图。图7是沿图5中的箭头B-B的向视剖视图,是用于说明通过本发明的一个实施方式的冲压成型方法的第一冲压成型工序成型的第一冲压成型部件的主要部分的说明图。图8是在本发明的一个实施方式的冲压成型方法的第一冲压成型工序中使用的第一模具的包括一部分截面的侧视图。图9是在本发明的一个实施方式的冲压成型方法的第一冲压成型工序中使用的第一模具(第一冲头、第一冲模、压坯料环)的说明图。图10是在本发明的一个实施方式的冲压成型方法的第一冲压成型工序中使用的第一模具(第一冲头)的说明图。图11是在本发明的一个实施方式的冲压成型方法的第一冲压成型工序中使用的第一模具的垫片的配置的说明图。图12是在本发明的一个实施方式的冲压成型方法的第二冲压成型工序中使用的第二模具的包括一部分截面的侧视图。图13是在本发明的一个实施方式的冲压成型方法的第一冲压成型工序中的金属板的配置的说明图。图14是通过本发明的实施例的冲压成型方法成型的第二冲压成型部件(前柱)的立体图。图15是通过本发明的实施例的冲压成型方法成型的第二冲压成型部件(前柱)的与俯视图上的轴线垂直的剖视图的一例。图16是在本发明的实施例的冲压成型方法的第一冲压成型工序中使用的第一模具(第一冲头、压坯料环)的说明图。图17是在本发明的实施例的冲压成型方法的第一冲压成型工序中使用的第一模具(第一冲头)的说明图。图18是沿图17中的箭头C-C的向视剖视图。图19是在本发明的实施例的冲压成型方法的第一冲压成型工序中使用的第一模具(第一冲模、垫片)的说明图。图20是本发明的实施例的冲压成型方法的第一冲压成型工序中的垫片压紧时机的说明图。图21是在本发明的实施例的冲压成型方法的第二冲压成型工序中使用的第二模具(第二冲头)的说明图。图22是在本发明的实施例的冲压成型方法的第二冲压成型工序中使用的第二模具(第二冲模)的说明图。图23A是本发明的实施例的冲压成型方法的第一冲压成型工序中的垫片压紧范围的说明图。图23B是本发明的实施例的冲压成型方法的第一冲压成型工序中的垫片压紧范围的说明图。图24A是本发明的实施例的冲压成型方法的第一冲压成型工序中的金属板的配置的说明图。图24B是本发明的比较例的冲压成型方法的第一冲压成型工序中的金属板的配置的说明图。具体实施方式以下,参照附图,详细说明本发明的一个实施方式。需要说明的是,本发明不由该实施方式限定。另外,在附图的记载中,对于相同部分标以相同的附图标记。本发明的一个实施方式的冲压成型方法包括如图lA~1B所示的第一冲压成型工序和如图lC~1D所示的第二冲压成型工序。在第一冲压成型工序中,利用具有第一冲头3、第一冲模5、压坯料环7及垫片9的第一模具1,将金属板11冲压成型为具有中间形状的第一冲压成型部件27。在第二冲压成型工序中,利用具有第二冲头15和第二冲模17的第二模具13,将通过该第一冲压成型工序成型的第一冲压成型部件27冲压成型为具有产品形状(顶板部及纵壁部为与冲压成型部件19相同的形状)的第二冲压成型部件。由此,制造出如图2及图3所示的作为完成品的冲压成型部件19。首先,对作为完成品的冲压成型部件19、具有中间形状的第一冲压成型部件27、具有产品形状的第二冲压成型部件进行说明。接下来,对第一模具1、第二模具13进行说明。然后,对冲压成型方法(第一冲压成型工序、第二冲压成型工序)进行说明。<冲压成型部件>如图2及图3所示,冲压成型部件19具有顶板部21、形成于两侧的纵壁部23、与纵壁部23连续地形成的凸缘部25,并且在俯视时具有L字形状(参照图3)。冲压成型部件19的与俯视图上的轴垂直的截面在L字形状的整个长度内形成为例如图4所示的帽状。顶板部21在俯视时为由长边和短边构成的L字形状。顶板部21具有多个凸部21a。在短边的端部形成有形状缩小的台阶部,该形状缩小部分为用于与其他部件连接的连接部21b。在该短边的端部未形成有纵壁部23及凸缘部25。需要说明的是,纵壁部23是倾斜的。这样,冲压成型部件19是具有急剧弯曲的弯曲部并在整个长度内具有帽状截面的部件。因此,若使用延展性低的超高强度的高强度材料通过通常的冲压成型制造这样的冲压成型部件19,则容易在L字形状的弯曲部的顶板部21上产生褶皱、或者在弯曲部的纵壁部23的肩部产生裂纹。因此,在本实施方式中,为了制造这样的冲压成型部件19,如以下所说明地,暂且成型为具有中间形状的第一冲压成型部件27,再从第一冲压成型部件27成型为具有产品形状的第二冲压成型部件。<第一冲压成型部件>第一冲压成型部件27是在第一冲压成型工序中成型的部件。对于第一冲压成型部件27,基于图5~图7进行说明。图5是第一冲压成型部件的俯视图。图6示意性地表示了纵壁部23的高度中央的垂直于高度方向的截面图。图7示意性地表示沿图5的箭头B-B的向视剖视图。在图6及图7中,为了比较,用双点划线表示冲压成型部件19的形状。需要说明的是,在图5~图7中,对与冲压成型部件19(参照图2~图4)相同的部分标以相同的附图标记。在第一冲压成型部件27中,在包括L字形状的弯曲部的外侧的纵壁部23上形成有纵壁鼓出部29,该纵壁鼓出部29在俯视时比冲压成型部件19的纵壁部23向外侧呈圆弧状鼓出。并且,如图6所示,纵壁鼓出部29的圆弧的曲率半径RBm大于冲压成型部件19的L字形状的弯曲部的外侧的曲率半径RBp。需要说明的是,所谓外侧的纵壁部23,观察图6可知,是指L字形状的弯曲部中的位于弯曲外侧的纵壁部23。而且,在第一冲压成型部件27中,在L字形状的弯曲部的顶板部21的外侧形成有顶板鼓出(stretching)部31,该顶板鼓出部31在侧视时比冲压成型部件19的L字形状的弯曲部的顶板部21的外侧呈圆弧状鼓出。并且,如图7所示,与顶板鼓出部31相连的肩部在侧视时的截面中的曲率半径Rsm大于冲压成型部件19的L字形状的弯曲部的与顶板部21的外侧相连的肩部在侧视时的截面中的曲率半径Rsp。期望纵壁部23与顶板部21的鼓出量是使第一冲压成型部件27的L字形状的弯曲部的鼓出部分的面积相对于与该鼓出部分对应的冲压成型部件19的L字形状的弯曲部的面积增加0.3%至1.2%的面积比率的量。这里,所谓的鼓出部分是指纵壁鼓出部29及顶板鼓出部31,所谓鼓出部分(在侧视图和/或俯视图中)的面积,是指纵壁鼓出部29与顶板鼓出部31的面积的合计值。若面积比例的增量小于0.3%,则不能避免裂纹。另外,若面积比例的增量超过1.2%,则在第二冲压成型工序中将第一冲压成型部件27冲压成型为冲压成型部件19时,鼓出部分的材料过多,有可能无法形成冲压成型部件19。第一冲压成型部件27的形状,除了纵壁鼓出部29和顶板鼓出部31之外,与冲压成型部件19的形状大致相同。<第二冲压成型部件>第二冲压成型部件是在第二冲压成型工序中成型的部件,在顶板部及纵壁部处具有产品形状(与冲压成型部件19的顶板部21及纵壁部23相同的形状)。需要说明的是,第二冲压成型部件的形状与图2所示的冲压成型部件19大致相同,因此省略图示。接下来,对用于成型上述第一冲压成型部件27与第二冲压成型部件的第一模具1和第二模具13进行说明。<第一模具>第一模具1是在第一冲压成型工序中为将金属板11成型为第一冲压成型部件27而使用的模具。如图8所示,第一模具1具备第一冲头3、第一冲模5、在与第一冲模5之间夹持金属板11的压坯料环7、与第一冲头3联动地夹持金属板11的一部分的垫片9。第一冲头3安装于垫板(bolster)33,并且第一冲模5安装于滑动件(slider)35。以下,基于图8~图11,对第一模具1的各结构进行详细说明。《第一冲头》如图9~图11所示,第一冲头3在俯视时具有L字形状,并且具备成型顶板部21的顶板成型面部41、在顶板成型面部41的周围成型纵壁部23的纵壁成型面部43。需要说明的是,在图10及图11中,纵壁成型面部43倾斜。在顶板成型面部41上设置有用于成型第一冲压成型部件27的顶板鼓出部31的顶板鼓出成型部41a,并且在纵壁成型面部43上设置有用于成型纵壁鼓出部29的纵壁鼓出成型部43a。通过将第一冲头3形成为如上所述的形状,当在第一冲压成型工序中成型第一冲压成型部件27时,能够避免在第一冲压成型部件27的L字形状的弯曲部中,在与顶板部21的外侧相连的肩部产生裂纹(crack)。《第一冲模》如图9所示,第一冲模5的中央凹陷成大致L字形状,并且该凹陷内的表面为与第一冲头3对应的成型面5a。在成型面5a上的包括L字形状的弯曲部的位置设置有垫片收纳部5b,在该垫片收纳部5b中配置有垫片9(参照图8)。第一冲模5的成型面5a的周围的面为挟持面5c,在该挟持面5c与压坯料环7之间夹持金属板11。《压坯料环》如图8所示,压坯料环7由缓冲销(cushionpin)37支承成能够上下移动。另外,如图8及图9所示,在压坯料环7的中央设置有冲头收纳部7a,并且在冲头收纳部7a中配置有第一冲头3。在冲压成型开始前,压坯料环7被支承成位于比第一冲头3的上表面靠上方的位置,并且在冲压成型时压坯料环7能够被第一冲模5压下。当压坯料环7被压下时,第一冲头3相对地从压坯料环7突出,从而第一冲头3的上部插入第一冲模5。《垫片》如图8所示,垫片9设置为能够由弹簧39向第一冲头3侧按压,并且与第一冲头3联动地夹持金属板11。垫片9为能够对图11中由双点划线表示的部位进行按压的形状。即,垫片9能够按压的部位相当于如下部位,即在与图5的第一冲压成型部件27的顶板部21相当的部位中至少包括L字形状的弯曲部、并且在第一冲压成型部件27的L字形状的弯曲部中不与顶板部21的鼓出位置(顶板鼓出部31)重复的位置。由此,能够抑制在顶板部21的L字形状的弯曲部的内侧产生褶皱。<第二模具>第二模具13是在第二冲压成型工序中将第一冲压成型部件27成型为第二冲压成型部件的模具,如图12所示,具有第二冲头15和第二冲模17。第二冲头15安装于垫板33,并且第二冲模17安装于滑动件35。以下,对第二模具13的各结构进行说明。《第二冲头》第二冲头15具有成型出第二冲压成型部件的产品形状的成型面15a,通过对第一冲压成型部件27的鼓出部分(纵壁鼓出部29及顶板鼓出部31)(参照图5~图7)进行按压收缩,能够成型出具有产品形状的第二冲压成型部件。《第二冲模》第二冲模17具有与第二冲头15的成型面15a对应的成型面17a,与第二冲头15联动地将第一冲压成型部件27成型为第二冲压成型部件。需要说明的是,如果需要,还可以在第二冲模17上配置顶销(knock-outpin),使得在成型结束后,在第二冲压成型部件贴在成型面17a上的情况下,容易取出产品。<冲压成型方法>接下来,对本发明的冲压成型方法(第一冲压成型工序、第二冲压成型工序)进行说明。《第一冲压成型工序》第一冲压成型工序是在图8所示的第一模具1内配置金属板11、并且利用垫片9压紧顶板部21的一部分来冲压成型出第一冲压成型部件27的工序。以下,进行更详细的说明。如图13所示,金属板11被配置成,金属板11上的与第二冲压成型部件的L字形状的短边端部相当的部位11a不会接触压坯料环7。若使与短边端部相当的部位11a接触压坯料环7并进行冲压成型,则对该部位的金属板11的负荷大,会在金属板11上的对应于第一冲头3的肩部的部位产生裂纹,或者在部件角部附近的凸缘部25(参照图5)产生褶皱。因此,如上所述地配置金属板11,避免了裂纹或褶皱的产生。如图lA~图1B所示,配置金属板11后,第一冲模5和压坯料环7夹持金属板11。由此,抑制了凸缘部25产生褶皱。若不夹持金属板11,则在第一冲头3压入时,部件形状的变化部周围的金属板11的自由移动的部分会流入,容易产生褶皱。特别是,在成为部件的凸缘部25的金属板11的端部附近,金属板11能够容易变形,因此会产生大的褶皱。因此,需要从冲压成型初期开始,就利用第一冲模5和压坯料环7压紧金属板11。需要说明的是,利用第一冲模5和压坯料环7压紧金属板11的平均压力(压坯料环压力)期望在0.7MPa以上。金属板11被夹持后,通过第一冲模5向下移动,而第一冲头3被按压到金属板11上,进行冲压成型。在冲压成型中,利用垫片9压紧金属板11上的顶板部21的一部分。这里,所谓顶板部21的一部分是指至少包括L字形状的弯曲部、且与第一冲压成型部件27中的顶板鼓出部31不发生干涉的部位。这样,利用垫片9压紧金属板11,有效抑制在L字形状的弯曲部产生褶皱。如上所述,金属板11上的与第二冲压成型部件的短边端部相当的部位11a被配置成不会接触压坯料环7,因此在冲压成型中,材料的金属板11向弯曲部移动而容易产生褶皱。因此在本发明中,为了抑制产生褶皱,利用垫片9压紧金属板11。由垫片9压紧的金属板11的范围只要是至少L字形状的弯曲部,就能够防止产生褶皱。也可以在更广的范围内压紧顶板部21。需要说明的是,由垫片9压紧的金属板11的范围与顶板鼓出部31(参照图7)不发生干涉。相对于直到垫片9的下极限点位置的成型深度,将第一冲头3开始接触金属板11时的位置设为0%,将下极限点位置设为100%。在该情况下,利用垫片9压紧金属板11的时刻(时机)优选是在第一冲头3位于成型深度的0%至50%的位置时开始。需要说明的是,在以后的说明中,所谓垫片压紧开始时机是指开始利用垫片9压紧金属板11的时机。垫片压紧开始时机只要是第一冲头3位于成型深度的0%以后的位置,就能够抑制从第一冲头3与金属板11的接触初期开始的顶板部21上的金属板11的膨胀,从而有效地抑制褶皱的产生。以下,将成型深度的0%位置简单地设为“0%位置”,其他位置也相同。另一方面,如果垫片压紧开始时机在0%位置之前(例如﹣100%(负100%)位置),则在利用第一冲模5和压坯料环7夹持金属板11之前,则垫片9向第一冲头3方向压入金属板11。这样的话,金属板11会发生偏移,从而相对于成型后的部件形状产生过大的材料剩余,因此并非优选。另外,即使在第一冲头3超过成型深度的50%的位置后第一冲头3和垫片9开始压紧金属板11,已经在顶板部21上成为波状的膨胀较大而难以抑制褶皱,因此垫片压紧开始时机优选在50%位置之前。期望第一冲头3和垫片9压紧金属板11的平均压力(垫片压力)在3MPa以上。这样,抑制在顶板部21上产生褶皱。这样,成型出第一冲压成型部件27。在第一冲压成型部件27的弯曲部形成有纵壁鼓出部29和顶板鼓出部31(参照图5~图7),由于形成比冲压成型部件19的弯曲部的形状小的曲率(curvature),因此不会在L字形状的弯曲部上产生裂纹。《第二冲压成型工序》第二冲压成型工序是利用第二模具13将通过第一冲压成型工序成型的第一冲压成型部件27冲压成型为第二冲压成型部件的工序。首先,如图lC所示,在第二冲头15上载置有第一冲压成型部件27,如图1D所示,在该状态下第二冲模17向下移动,由此第一冲压成型部件27的纵壁鼓出部29和顶板鼓出部31被按压收缩而成型为第二冲压成型部件。然后,第二冲压成型部件被切除周围不需要的部分(剪切(trimming))成为第二冲压成型部件19。如上所述,在本实施方式中,在第一冲压成型工序中,金属板11被冲压成型为具有中间形状的第一冲压成型部件27。接下来,在第二冲压成型工序中,在第一冲压成型工序中成型的第一冲压成型部件27被冲压成型为对于顶板部21及纵壁部23具有产品形状的第二冲压成型部件。关于第一冲压成型部件27,包括L字形状的弯曲部的外侧的纵壁部23在俯视时比冲压成型部件19的纵壁部23向外侧呈圆弧状鼓出。该鼓出的圆弧的曲率半径RBm大于冲压成型部件的L字形状的弯曲部的曲率半径RBp。另外,L字形状的弯曲部的顶板部21的外侧比冲压成型部件19的顶板部21的外侧鼓出。与该鼓出的顶板部21相连的肩部在侧视时的截面中的曲率半径RSm大于冲压成型部件19的L字形状的弯曲部的与顶板部21的外侧相连的肩部在侧视时的截面中的曲率半径RSp。由此,即使将由延展性低的超高强度的高强度材料形成的金属板用作板材,也不会在L字形状的弯曲部产生裂纹,高精度且稳定地得到在L字形状的整个长度内形成为帽状截面的L字形状部件即冲压成型部件19。需要说明的是,上述内容中,表示了垫片9利用弹簧39按压金属板11上的例子,但如后述实施例所示,也可以利用气缸按压金属板11。另外,在上述内容中,表示了在第二冲压成型工序后对第二冲压成型部件进行剪切而形成冲压成型部件19的例子,但进行剪切的时间不限于此。例如,可以在第一冲压成型工序后对第一冲压成型部件27进行剪切,并在第二冲压成型工序后作为精加工再次进行剪切。[实施例]为了确认本发明的冲压成型方法的作用效果,进行具体的实验。在实验中,为了制造图14所示的具有L字形状的部件即汽车车体的前柱加强件(以下,简称作前柱51),在各种冲压成型条件下成型第一冲压成型部件,再成型第二冲压成型部件。然后,对各第二冲压成型部件进行剪切,以制造前柱51,对所制造的各前柱51进行褶皱、裂纹的评价。以下,对作为完成部件的前柱51(参照图14及图15)、用于冲压成型前柱51的第一冲压成型部件及第二冲压成型部件的模具(参照图16~图22)进行说明。然后,对第一冲压成型工序中的冲压成型条件(参照表1及图23A、图23B、图24A、图24B)及所制造的前柱51的评价结果(参照表2)进行详细说明。需要说明的是,对于第一冲压成型部件及第二冲压成型部件,与上述实施方式相同,因此省略了它们的详细说明。首先,对前柱51进行说明。如图14所示,前柱51具有在俯视时由长边和短边构成的L字形状的顶板部53、形成在顶板部53的周围的纵壁部55、与纵壁部55连续地形成的凸缘部57。而且,如图15所示,前柱51在整个长度内垂直于俯视图上的轴的截面形成为大致帽形。在顶板部53的短边端部上未形成纵壁部55和凸缘部57。接下来,对用于冲压成型的模具(第一模具、第二模具)进行说明。在第一冲压成型工序中,使用图16~图19所示的第一模具(压坯料环61、第一冲头65、第一冲模69、垫片73)。如图16所示,第一冲头65在俯视时具有L字形状。如图16所示,压坯料环61由缓冲销59支承。在压坯料环61的中央,设置有冲头收纳部61a,在冲头收纳部61a中配置有在俯视时具有L字形状的第一冲头65。为了进行使第一冲压成型部件的鼓出部分(纵壁鼓出部及顶板鼓出部)变化的实验,该第一冲头65在与L字形状的弯曲部的外侧相对应的一部分具有可更换部67。如图17及图18(沿图17的箭头C-C的向视剖视图)所示,在可更换部67上形成有纵壁鼓出成型部67a和顶板鼓出成型部67b,并且通过将可更换部67替换为任意的部件,能够变更鼓出部分(纵壁鼓出部及顶板鼓出部)的形状或鼓出量。例如,若不设置纵壁鼓出成型部67a则不成型纵壁鼓出部而仅成型顶板鼓出部,或者若使顶板鼓出成型部67b的大小变化则顶板鼓出部的鼓出量变化。压坯料环61在与L字形状的弯曲部的外侧相对应的一部分具有可更换部63(参照图16),并且形成为能够与第一冲头65的可更换部67的形状对应。如图19所示,第一冲模69具有用于第一冲头65插入的凹陷部69a。在第一冲模69的凹陷部69a的底面设置有垫片收纳部69b,并且在垫片收纳部69b中配置有垫片73。第一冲模69具有压坯料环61的可更换部63和与第一冲头65的可更换部67对应的可更换部71。如图20所示,第一冲模69安装在滑动件35上。垫片73与设置在滑动件35上的气缸(未图示)相连以产生负荷,并且通过在滑动件35与气缸之间放入厚度不同的金属块(未图示),能够对垫片73的突出位置进行调整。在第二冲压成型工序中,使用图21及图22所示的第二模具(第二冲头75、第二冲模77)。如图21所示,为了将第一冲压成型部件的鼓出部分(纵壁鼓出部及顶板鼓出部)成型为产品形状,第二冲头75的与鼓出部分对应的部分形成为产品形状。如图22所示,第二冲模77具有用于第二冲头75插入的凹陷部77a。接下来,对第一冲压成型工序中的冲压成型条件进行详细说明。在第一冲压成型工序中,对以下所示的参数进行各种组合来进行冲压成型。即,对象的参数是,金属板79的材料、面积增加率(%)、纵壁部的曲率半径的比值、肩部的曲率半径的比值、压坯料环压力(MPa)、垫片压紧范围、垫片压力(MPa)、垫片突出位置(%)、原料金属板配置。以下,对于上述各参数进行详细说明。作为金属板79的材料,使用拉伸强度为980MPa级和1180MPa级的冷轧钢板这两种延展性低的超高强度的高强度材料。需要说明的是,板厚为1.4mm。所谓面积增加率是指,第一冲压成型部件的L字形状的弯曲部的鼓出部分的面积相对于与该鼓出部分对应的产品形状的L字形状的弯曲部的面积的增加率。面积增加率是第一冲压成型部件中的L字形状的弯曲部的外侧的纵壁部与顶板部的鼓出部分相对于产品形状的面积增加率,优选是增加0.3%~1.2%的范围。所谓纵壁部的曲率半径的比值是指,纵壁部的曲率半径RBm相对于曲率半径RBp的比值(参照图6)。纵壁部的曲率半径的比值是通过RBm/RBp求得的值,该值为1.0时意味着未设置纵壁鼓出部,值越大意味着第一冲压成型部件上的纵壁鼓出部的鼓出量越多。纵壁部的曲率半径的比值在1.0~2.0之间变化。肩部的曲率半径的比值是指,肩部的曲率半径RSm相对于曲率半径Rsp的比值(参照图7)。肩部的曲率半径的比值是通过RSm/Rsp求得的值,该值为1.0时意味着未设置顶板鼓出部,值越大意味着第一冲压成型部件上的顶板鼓出部的鼓出量越多。肩部的曲率半径的比值在1.0~2.1之间变化。所谓压坯料环压力是指,由第一冲模69和压坯料环61夹持的金属板79的区域内的平均压力,优选是0.7MPa以上的范围。对于垫片压紧范围,使用两种垫片73而如图23A、23B所示地变更。在图23A、23B中,用双点划线包围垫片压紧范围来进行表示。图23A的垫片压紧范围是包括金属板79上的与L字形状的弯曲部相当的范围,图23B的垫片压紧范围是与弯曲部相当的部位的一部分的范围。在任一情况下,都不压紧第一冲头65(可更换部67(参照图17))的顶板鼓出成型部67b。图23A、23B所示的范围均为本发明的范围。所谓垫片突出位置是指,如图20所示,在卸下垫片73(参照图19)的状态下利用第一冲模69和压坯料环61夹持金属板79,并在该状态下设置垫片73时的垫片73位置。具体而言,将垫片73接触金属板79的位置设为垫片突出位置的0%位置。另外,将原点上方设为正方向,将原点下方设为负方向,将成型深度设为垫片突出位置的100%位置。垫片突出位置优选是0%至50%的位置的范围。原材料金属板配置为如图24A、24B所示的两种模式。图24A表示将金属板79配置成金属板79上的与L字形状的短边端部相当的部位79a不会接触压坯料环61的情况,图24B作为比较例表示将金属板79配置成部位79a会接触压坯料环61的情况。表1是对这些冲压成型条件总结而成的表。【表1】在表1中,关于材料的拉伸强度,980MPa级记作980,1180MPa级记作1180。表1中的本发明例1~本发明例15所示的条件中,纵壁部的曲率半径的比值(**)、肩部的曲率半径的比值(***)、垫片压紧范围、原料金属板配置均在本发明的范围内。本发明例1~本发明例10所示的条件中,面积增加率((%)*)、压坯料环压力(MPa)、垫片压力(MPa)、垫片突出位置(%)为优选范围。比较例1~比较例4所示的条件中,特定的参数的数值在本发明范围之外(参照表1中带有下划线的参数)。基于上述表1的各条件进行第一冲压成型工序以成型出第一冲压成型部件,在第二冲压成型工序中进一步对该第一冲压成型部件冲压成型,得到第二冲压成型部件。然后,将第二冲压成型部件的周围的多余部分剪切以制造前柱51。表2表示在每个冲压成型条件下制造的前柱51的评价结果。【表2】条件肩部裂纹顶板部褶皱凸缘部裂纹凸缘部褶皱综合评价本发明例1○◎○◎OK本发明例2○◎○◎OK本发明例3○◎○◎OK本发明例4○○○○OK本发明例5○◎○◎OK本发明例6○◎○◎OK本发明例7○◎○◎OK本发明例8○◎○◎OK本发明例9○◎○◎OK本发明例10○◎○◎OK本发明例11△◎○◎OK本发明例12○△○◎OK本发明例13○△○△OK本发明例14○△○◎OK本发明例15○△○◎OK比较例1×◎○◎NG比较例2○×○◎NG比较例3×◎○◎NG比较例4×◎○◎NG评价项目为与第一冲头65的肩部对应的部位(以下,简称“肩部”)的裂纹、顶板部53的褶皱、凸缘部57的裂纹及褶皱(参照图14)。褶皱的评价通过目视观察进行。在表2中,未观察到褶皱的情况下记为“◎”,稍稍观察到褶皱但在可接受范围内的情况下记为“○”,微小的情况下记为“△”,明显的情况下记为“×”。另外,裂纹的评价也通过目视观察进行。在表2中,在未观察到裂纹的情况下记为“○”,观察到极细微的裂纹的情况下记为“△”,观察到裂纹的情况下记为“×”。然后,进行褶皱及裂纹的综合评价。在表2中,在作为产品可以接受的情况下记为“OK”,在不可接受的情况下记为“NG”。如表2所示,在本发明例1~本发明例15中,对于裂纹,虽然有时会在肩部观察到极细微的裂纹(本发明例11),但除此之外,在肩部及凸缘部57均未观察到裂纹。同样地,在大部分的发明例中均未观察到褶皱,并且不存在明显情况。根据上述内容可知,在本发明例1~本发明例15的全部发明例中,综合评价被评价为“OK”,能够进行良好的冲压成型。另一方面,在比较例1~比较例4中综合评价为“NG”(不良)。在比较例1中,如图24B所示,金属板79上的与短边端部相当的部位79a被配置成会接触压坯料环61,因此在肩部产生裂纹。在比较例2中,未利用垫片73压紧,因此在顶板部53产生褶皱。在比较例3中,在第一冲压成型部件中未成型出纵壁鼓出部,因此在肩部产生裂纹。在比较例4中,在第一冲压成型部件中未形成顶板鼓出部,因此在肩部产生裂纹。如上所述,在实施例中,通过应用本发明,即使使用延展性低的超高强度的高强度材料,也能够避免裂纹产生,并且抑制褶皱产生,能够高精度且稳定地制造前柱51。另外,上述实施方式只是实施本发明的例子,本发明不限定于此,根据规格等进行各种变更也在本发明的范围内,而且根据上述内容可知,在本发明的范围内可以进行其他各种实施方式。工业可用性本发明可以应用于利用模具对金属板进行冲压成型以制造冲压成型部件的冲压成型方法,所述冲压成型部件在俯视时具有L字形状,并且具备顶板部、形成于该顶板部两侧的纵壁部、与该纵壁部连续地形成的凸缘部。附图标记说明1:第一模具3:第一冲头5:第一冲模5a:成型面5b:垫片收纳部5c:挟持面7:压坯料环7a:冲头收纳部9:垫片11:金属板11a:与L字形状的短边端部相当的部位13:第二模具15:第二冲头15a:成型面17:第二冲模17a:成型面19:冲压成型部件21:顶板部21a:凸部21b:连接部23:纵壁部25:凸缘部27:第一冲压成型部件29:纵壁鼓出部31:顶板鼓出部33:垫板35:滑动件37:缓冲销39:弹簧41:顶板成型面部41a:顶板鼓出成型部43:纵壁成型面部43a:纵壁鼓出成型部51:前柱53:顶板部55:纵壁部57:凸缘部59:缓冲销61:压坯料环61a:冲头收纳部63:可更换部65:第一冲头67:可更换部67a:纵壁鼓出成型部67b:顶板鼓出成型部69:第一冲模69a:凹陷部69b:垫片收纳部71:可更换部73:垫片75:第二冲头77:第二冲模77a:凹陷部79:金属板79a:与L字形状的短边端部相当的部位