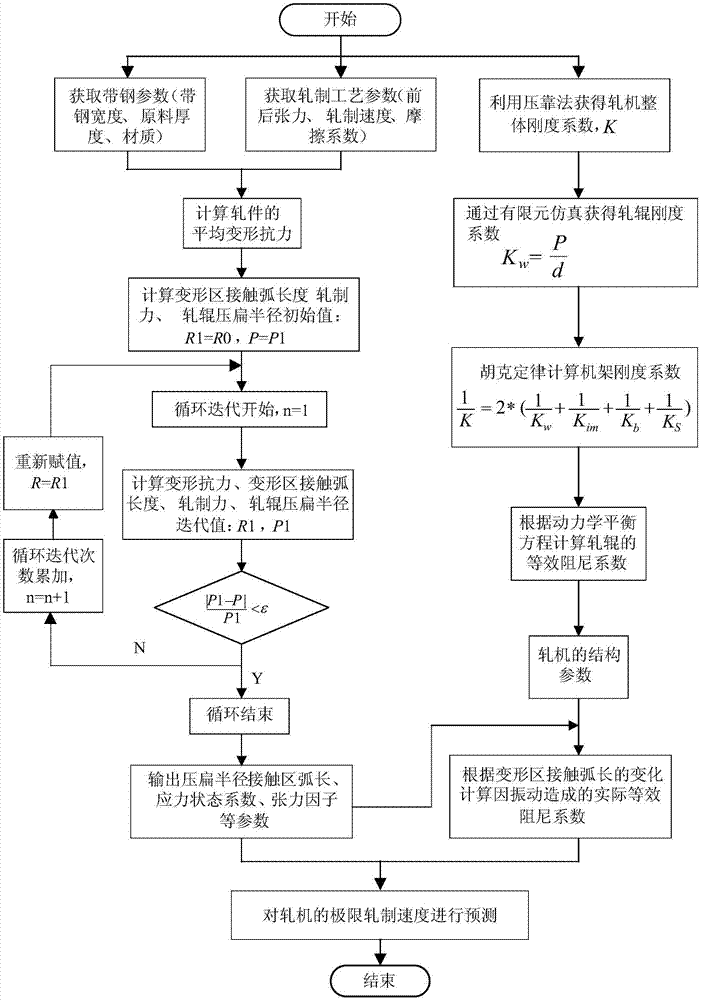
本发明涉及轧制过程自动控制
技术领域:
,尤其涉及一种六辊冷轧机的极限轧制速度预测方法。
背景技术:
轧机的异常振动是板带材轧制生产过程中频繁出现并且亟待解决的问题。冷轧机在发生振动时会使轧件的表面产生明暗相间的振动条纹,影响产品的表面质量;轧机发生三倍频振动时会严重影响带钢的厚度与板形质量;轧机振动会加剧轧辊和轴承的不均匀磨损,缩短了工作辊的使用周期,导致设备运行维护费用增加;严重时,轧机振动甚至会造成断带或者设备的损坏,严重威胁人员与设备的安全。目前大部分冷轧机组在不同程度上都存在着振动或者失稳的问题。轧制工艺参数的合理选取是实现轧制过程高速与稳定进行的关键。在冷轧过程中当轧制速度超过某一极限时,轧机会发生明显的自激共振现象,严重影响带钢产品的质量,制约企业的经济效益。在轧制过程中工艺参数繁多,各种工艺参数之间、工艺参数与轧机的结构参数之间相互耦合在一起,这就造成轧机在不同的轧制工艺参数下轧机的极限稳定轧制速度差别很大。轧机极限轧制速度的确认可以避免因轧制速度过高而引起的自激共振,保证良好的产品质量以及人员设备安全。现在大部分轧机在进行轧制速度设定与调整时一般考虑的是轧机的负荷、设备极限以及金属秒流量相等的原则,并且结合现场实际轧制过程进行修订。这种方法没有考虑到轧制速度与轧机的异常振动对带钢产品质量的影响。轧机极限轧制速度的确定是保证轧制过程的高速稳定进行的关键,同时也是对轧制工艺参数进行协调优化的基础。技术实现要素:本发明要解决的技术问题是针对上述现有技术的不足,提供一种六辊冷轧机的极限轧制速度预测方法,在轧制过程中,根据实测的带钢参数、轧机结构参数、轧制工艺参数,计算出极限轧制速度的预测值,以达到有效避免因轧制速度过高而引起的轧机自激振动的目的,实现轧制过程的高速稳定运行。为解决上述技术问题,本发明所采取的技术方案是:一种六辊冷轧机的极限轧制速度预测方法,包括以下步骤:步骤1:获取带钢参数、轧机结构参数和轧制参数;所述带钢参数包括带钢宽度、带钢原料厚度、带钢材质;所述轧机结构参数包括轧辊原始辊径、轧辊质量、轧辊刚度系数、轧辊等效阻尼系数;所述轧制参数包括各机架出口带钢厚度、各机架轧制速度、轧辊的转速、摩擦系数、机架间前后张力;步骤2:根据带钢参数、轧机结构参数和轧制参数计算轧件的平均变形抗力、工作辊压扁半径、变形区接触弧长、轧制力、应力状态系数、张力因子;步骤2.1:根据带钢材质以及各机架入口与出口带钢厚度利用冷轧变形抗力模型计算带钢每变形道次的平均变形抗力;所述各机架入口与出口带钢厚度满足hout,i=hin,i+1,1≤i≤4,其中hin,i为第i机架入口带钢厚度,hout,i为第i机架出口带钢厚度;第一机架入口厚度为带钢参数中的带钢原料厚度;所述冷轧变形抗力模型是指与带钢材质、机架入口与出口带钢厚度相关的抵抗塑性变形的能力;步骤2.2:根据带钢每变形道次的平均变形抗力,求出轧辊的压扁半径、变形区接触弧长、轧制力、应力状态系数、张力因子;步骤3:根据机架出口带钢的厚度波动情况计算当前机架的张力、轧制力的波动值;根据得到的轧制力波动数据得到因张力波动而产生的负阻尼大小,并计算出此时轧辊的实际等效阻尼系数;步骤4:根据轧辊实际等效阻尼系数对轧机的极限轧制速度进行预测;根据轧机的垂直振动动力学平衡模型预测轧机的极限稳定轧制速度;所述的六辊轧机极限轧制速度是指轧机在不发生自激振动的前提下能达到的最高出口带钢轧制速度。所述步骤1中的参数获取具体按照如下方法进行:所有带钢参数、所有轧制参数与轧机结构参数中的轧辊原始辊径、轧辊质量直接从冷轧现场产线上的一级以及二级系统进行获取;所述轧机结构参数中的轧辊刚度系数、轧辊等效阻尼系数通过测出轧机的刚度系数之后进行求解,所述轧机的刚度系数包括所有轧辊的刚度系数与轧机机架的等效刚度系数,所述轧机的刚度系数通过现场压靠法,在轧辊转速一定的情况下,使工作辊压靠,同时记录轧制压力与辊缝,然后通过回归给出轧机的刚度系数;轧辊的刚度系数利用有限元仿真模型记录不同压力作用下轧辊的动态位移,然后通过计算获得;机架等效刚度系数通过胡克定律计算获得;轧辊等效阻尼系数通过对系统动力学微分方程等效阻尼矩阵的计算获得。所述步骤2.1计算带钢每变形道次的平均变形抗力具体按照如下方法进行:平均变形抗力是带钢材质、机架入口与出口带钢厚度相关的函数,如下式所示:式中,为道次平均变形抗力,单位为mpa;k0为与带钢材质有关的变形抗力常量;h0为原料厚度,单位为mm;hin为机架入口带钢厚度,单位为mm;hout为机架出口带钢厚度,单位为mm;所述步骤2.2具体按照如下步骤进行:计算压扁半径,压扁半径是与轧辊原始辊径、轧辊弹性模量、机架入口、出口带钢厚度、带钢宽度、轧制力有关的函数,如下式所示:r′=g(r,e1,w,hin,hout,p,υ)式中,r′为轧辊的压扁半径,单位为mm;r为轧辊的原始半径,单位为mm;p为总轧制压力,单位为n;υ为泊松比,取值为0.3;e1为工作辊弹性模量,取值为2.11×105mpa;w为带钢的宽度,单位为mm;计算变形区接触弧长,如下式所示:l'=h(r,p,δh,e1,υ)式中,l′为变形区接触弧长度,单位为mm;p为平均单位压力,单位为n;δh为道次压下量,δh=hin-hout,单位为mm;计算轧制力p,所述轧制力是与带钢宽度、机架入口、出口带钢厚度、变形区弧长、带钢变形抗力、前后张力、轧辊压扁半径、变形区摩擦系数有关的函数,如下式所示:式中,μ为辊缝变形区摩擦系数;tf为前张力,单位为mpa;tb为后张力,单位为mpa;计算应力状态系数、张力因子,如下式所示:式中,qp为应力状态系数;nt为张力因子;ε为压下率;μt为加权系数,μt=0.7。所述步骤3具体按照如下方法进行:机架出口带钢厚度hout近似表示为:式中,hm为带钢平均出口厚度,单位为mm;δhout为机架出口处带钢的厚度变化,单位为mm;δhn为中性面处带钢的厚度变化,单位为mm;a、b为振动幅值,单位为mm;α为相位角,单位为rad;ω为振动角频率,单位为rad/s;δs为辊缝的变化量,单位为mm;y为轧辊的振动位移,单位为mm;假设上游机架出口速度恒定,根据胡可定律,当前机架的张力变化δtbi为:式中,e2为带钢的弹性模量,取值为2.11×105mpa;li为第i-l机架与第i机架间距,单位为m;vr,i为第i机架轧辊的线速度,单位为m/s;k′w为工作辊等效刚度系数,单位为n/m;hin,i为第i机架入口带钢厚度,单位为mm;机架出口带钢厚度变化造成的轧制力变化δp为:式中,qp为应力状态系数;假设振动造成的变形区接触弧长的变化为:根据工作辊的动力学平衡微分方程,并考虑出口带钢厚度波动的振动角频率ω与相位角α难以确定,同时负阻尼效应是由于振动导致轧制力波动而产生的,得到振动造成的实际等效阻尼系数cact为:式中,cact为实际的工作辊阻尼系数,单位为n.s/m;c′w为工作辊的等效阻尼系数,单位为n.s/m;vout为机架出口带钢速度,单位为m/s;nt为张力因子。所述步骤4具体按照如下方法进行:当cact≤0时,轧机出现自激振动,此时的轧制速度为轧机的极限轧制速度,得到的六辊轧机的极限轧制速度vlimit为:采用上述技术方案所产生的有益效果在于:本发明提供的六辊冷轧机的极限轧制速度预测方法,利用轧制工艺-轧机结构耦合模型计算出轧机稳定轧制状态下的极限轧制速度,在大部分六辊冷轧机极限轧制速度的确定上都能方便实现,不需要成本上的额外投入。本发明方法效果显著,通过本发明中提供的方法可以有效避免因轧制速度过高而产生的轧机自激振动,从而有效的保证带钢的产品尺寸精度,同时能避免因轧机异常振动而产生的设备损耗,保证企业的经济效益,可以广泛推广到单机架及多机架连轧机的极限轧制速度的计算中。附图说明图1为本发明实施例提供的六辊冷轧机的极限轧制速度预测方法的流程图;图2为本发明实施例提供的轧辊压扁半径-轧制力解耦过程计算流程图;图3为本发明实施例提供的压下率-摩擦系数对极限轧制速度的影响的曲线示意图。具体实施方式下面结合附图和实施例,对本发明的具体实施方式作进一步详细描述。以下实施例用于说明本发明,但不用来限制本发明的范围。本实施例中针对某1450mmucm六辊冷连轧机组的极限轧制速度进行预测,其中工作辊、中间辊、支撑辊均为平辊。如图1所示,本实施例的六辊冷轧机的极限轧制速度预测方法如下所述。步骤1:获取带钢参数、轧机结构参数和轧制参数;所述带钢参数包括带钢宽度、带钢原料厚度、带钢材质;所述轧机结构参数包括轧辊原始辊径、轧辊质量、轧辊刚度系数、轧辊等效阻尼系数;所述轧制参数包括各机架出口带钢厚度、各机架轧制速度、轧辊的转速、摩擦系数、机架间前后张力;其中各机架出口带钢厚度为后一个机架的入口厚度,即第i机架出口厚度等于第i+1机架入口厚度。本实施例中,带钢宽度为900mm,带钢原料厚度为2mm,轧制带钢的材质为mrt5。轧机的刚度系数通过现场压靠法,在轧辊转速一定的情况下,使工作辊压靠,同时记录轧制压力与辊缝,然后通过回归给出轧机的刚度系数。本实施例通过对某1450mmucm六辊冷连轧机组进行压靠实验,得到轧机的刚度系数为k=4.4×109n/m。轧辊的刚度系数利用有限元仿真模型记录不同压力作用下轧辊的动态位移,然后通过计算获得。根据胡克定律可以得到机架的等效刚度系数为:轧辊等效阻尼系数通过对系统动力学微分方程正则化得出等效阻尼的正则矩阵,并计算获得。最终得到的轧机结构参数如表1所示。表1轧机结构参数参数名称数值参数名称数值工作辊质量mw(kg)3914机架下部分等效刚度ks(n/m)11.73×1010中间辊质量mim(kg)5410工作辊等效阻尼系数cw(n.s/m)0支撑辊质量mb(kg)31330中间辊等效阻尼系数cim(n.s/m)5.10×106机架上部分质量ms(kg)79739支撑辊等效阻尼系数cb(n.s/m)0.57×106工作辊等效刚度kw(n/m)0.91×1010工作辊直径(mm)425中间辊等效刚度kim(n/m)1.03×1010中间辊直径(mm)490支撑辊等效刚度kb(n/m)5.85×1010支撑辊直径(mm)1300获取的轧制参数如表2所示。表2轧制参数步骤2:根据带钢参数、轧机结构参数和轧制参数计算工作辊压扁半径、变形区接触弧长、轧件的平均变形抗力、轧制力、应力状态系数、张力因子,具体如下:步骤2.1:根据带钢材质以及各机架入口与出口带钢厚度利用冷轧变形抗力模型计算带钢每变形道次的平均变形抗力;所述带钢变形抗力模型是指与带钢材质、机架入口、出口带钢厚度相关的抵抗塑性变形的能力。其中,各机架入口与出口带钢厚度满足hout,i=hin,i+1,1≤i≤4,其中hin,i为第i机架入口带钢厚度,hout,i为第i机架出口带钢厚度;第一机架入口厚度为带钢参数中的带钢原料厚度。平均变形抗力是带钢材质、机架入口与出口带钢厚度相关的函数,本实施例中按下式计算带钢在每道次的平均变形抗力:式中,为道次平均变形抗力,单位为mpa;ε∑为带钢的累积变形量;h0为原料厚度,单位为mm;hin为机架入口带钢厚度,单位为mm;hout为机架出口带钢厚度,单位为mm;a、b为考虑材料特性的变形抗力参考常量,单位为mpa;σ0、c、d为自学习系数。在本实施例中,与带钢材质有关的各变形抗力常量的取值为a=474.00、b=167.00、c=0.20、d=5.00、σ0=1。步骤2.2:根据2.1中求得的带钢每变形道次平均变形抗力并与西齐柯克(hitchcook)公式结合,利用循环迭代法求出轧辊的压扁半径、变形区接触弧长、轧制力、应力状态系数、张力因子。压扁半径是与轧辊原始辊径、轧辊弹性模量、机架入口、出口带钢厚度、带钢宽度、轧制力有关的函数,本实施例针对冷轧过程中轧辊的弹性压扁,利用轧机结构参数、轧制工艺参数,根据hitchcock公式计算轧辊的压扁半径,如下式所示:式中,r′为轧辊的压扁半径,单位为mm;r为轧辊的原始半径,单位为mm;p为总轧制压力,单位为n;υ为泊松比,取值为0.3;e1为工作辊弹性模量,取值为2.11×105mpa;w为带钢的宽度,单位为mm。当轧件弹性变形很小时,若只考虑轧辊的弹性压扁,变形区接触区弧长的hitchcook公式为:式中,l′为变形区接触弧长度,单位为mm;p为平均单位压力,单位为n;δh为道次压下量,δh=hin-hout,单位为mm。轧制力是与带钢宽度、机架入口、出口带钢厚度、变形区弧长、带钢变形抗力、前后张力、轧辊压扁半径、变形区摩擦系数有关的函数,根据bland-ford-hill公式计算轧制力如下式所示:计算应力状态系数、张力因子,如下式所示:式中,μ为辊缝变形区摩擦系数;tf为前张力,单位为mpa;tb为后张力,单位为mpa;qp为应力状态系数;nt为张力因子;μt为加权系数,μt=0.7。通过分析发现,工作辊的弹性压扁半径、轧制力、接触区弧长、应力状态系数等相关参数是彼此影响、相互耦合的,因此直接使用原始值进行计算直接得出。本实施例中采用循环迭代法进行解耦运算求解得出这些参数。图2是本实施例中轧辊压扁半径-轧制力解耦过程计算流程图。通过解耦计算得到的部分参数及误差如表3所示。表3解耦计算结果步骤3:根据机架出口带钢的厚度波动情况计算当前机架的张力、轧制力的波动值;根据得到的轧制力波动数据得到因张力波动而产生的负阻尼大小,并计算出此时轧辊的实际等效阻尼系数。因轧机振动导致的机架出口带钢厚度近似呈现为一余弦曲线。假设因振动造成的带钢出口厚度近似表示为:式中,hm为带钢平均出口厚度,单位为mm;δhout为机架出口处带钢的厚度变化,单位为mm;δhn为中性面处带钢的厚度变化,单位为mm;a、b为振动幅值,单位为mm;α为相位角,单位为rad;ω为振动角频率,单位为rad/s;δs为辊缝的变化量,单位为mm;y为轧辊的振动位移,单位为mm。假设上游机架出口速度恒定,根据胡可定律,当前机架的张力变化为:式中,e2为带钢的弹性模量,取值为2.11×105mpa;li为第i-1机架与第i机架间距,单位为m;vr,i为第i机架轧辊的线速度,单位为m/s;k′w为工作辊等效刚度系数,单位为n/m;hin,i为第i机架入口带钢厚度,单位为mm。机架出口带钢厚度变化造成的轧制力变化为:工作辊的动力学平衡微分方程为:式中,mw为工作辊的质量,单位为kg;c′w为工作辊的等效阻尼系数,单位为n.s/m。根据工作辊的动力学平衡微分方程,得到因张力波动造成的实际等效阻尼系数为:cact=c'w-0.7wl’qpb1考虑到出口带钢厚度波动的振动角频率ω与相位角α难以确定,同时负阻尼效应是由于振动导致轧制力波动而产生的。假设振动造成的变形区接触弧长的变化为:振动造成的的实际等效阻尼系数为:式中,cact为实际的工作辊阻尼系数,单位为n.s/m;vout为机架出口带钢速度,单位为m/s。步骤4:根据步骤3中得到的轧辊实际等效阻尼系数对轧机的极限轧制速度进行预测。当cact≤0时,轧机出现自激振动,此时的轧制速度为轧机的极限轧制速度,得到六辊轧机的极限轧制速度为:将本实施例中的各参数代入到上式中,根据该方法通过计算得到的六辊轧机极限轧制速度为24.80m/s。所述极限速度表明当轧机实际轧制速度超过24.80m/s时,轧机会产生自激振动,在此速度之上进行轧制时带钢会产生严重的厚度与板形缺陷,严重时甚至会造成断带或者轧机设备的损坏。如图3所示,为本发明实施例中基于六辊轧机的极限轧制速度预测公式对第五机架的压下率-摩擦系数进行协调优化的效果示意图,从图3中可知,当摩擦系数与压下率越小时,轧机的极限轧制速度越高。最后应说明的是:以上实施例仅用以说明本发明的技术方案,而非对其限制;尽管参照前述实施例对本发明进行了详细的说明,本领域的普通技术人员应当理解:其依然可以对前述实施例所记载的技术方案进行修改,或者对其中部分或者全部技术特征进行等同替换;而这些修改或者替换,并不使相应技术方案的本质脱离本发明权利要求所限定的范围。当前第1页12