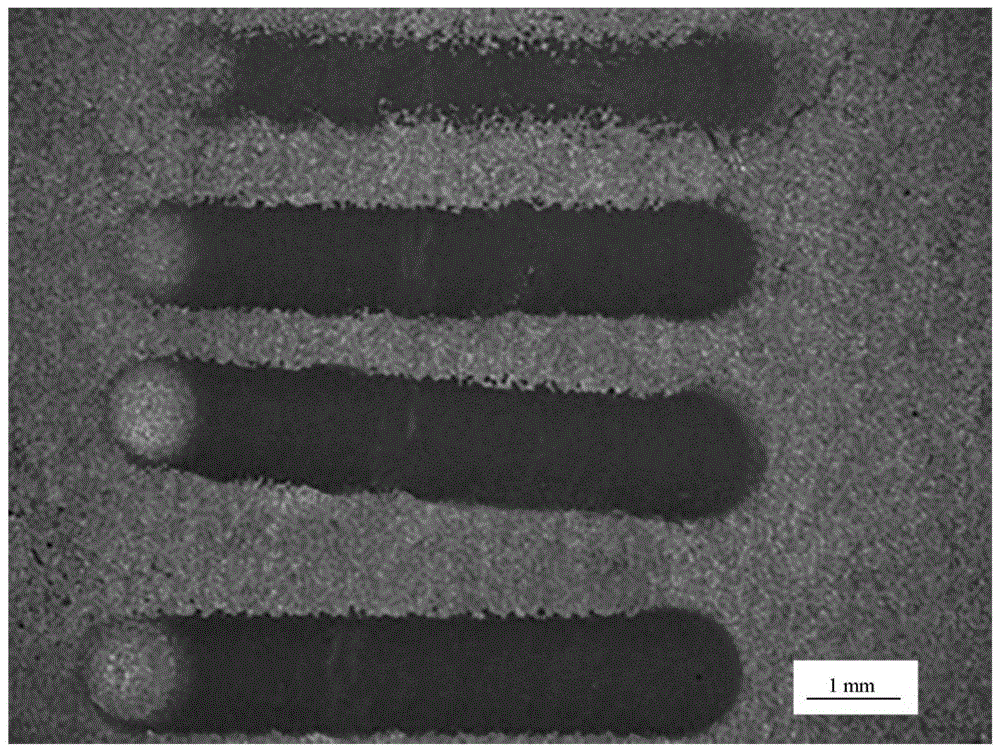
本发明涉及射流电解加工领域,更加具体地说,涉及一种在电解槽中对碳化硅增强铝基复合材料进行射流电解加工的加工方法。
背景技术:
:电解加工(electrochemicalmachining,ecm)是一种基于电化学腐蚀原理,利用可控的阳极溶解定域去除工件材料,从而获得所需形状与尺寸的加工技术。电解加工过程中,阴极为加工工具,阳极为被加工工件,阴阳两极之间维持一个极小的加工间隙。根据法拉第定律,工件阳极的材料溶解由电流密度分布决定。通过采用不同工艺方法,控制电流密度分布,从而获得所需的形状与尺寸。电解加工由于其特殊的加工机理,具有无切削力与切削热影响,加工效率高、加工表面无残余应力与刀痕等优点,在航空航天、汽车、国防装备等工业领域已得到了成功应用。电解射流加工(electrochemicaljetmachining,ecjm,电液束加工或喷射电解加工)是将电解加工技术与水射流加工技术相结合的一种复合加工方法,其原理是将具有一定压力的电解液通过喷嘴向金属工件表面喷射,使其在电解液与工件界面发生阳极溶解而去除的一种加工方法。该方法不需要采用与加工工件形状一样的成型阴极电极工具,对阴极工具没有磨损和损耗,具有很好的灵活性和方便性,可以实现难加工材料、复杂三维型面的加工,加工后工件表面几乎不存在缺陷且表面光滑、没有毛刺,已广泛应用于飞机涡轮叶片和微电子仪器等的小直径孔和复杂形状孔的加工。碳化硅增强铝基复合材料是以铝或者铝合金为基体,以sic颗粒或纤维为增强相的一种复合材料,具有优异的物理和力学性能,如高比强度、高比模量、低膨胀系数、耐磨、耐高温、良好的热稳定性等。其制备工艺简单、成本低,适于批量生产,且可用常规金属加工方法—铸造、挤压、轧制、焊接等制造各种形状的零件和型材,因而成为金属基复合材料(简称mmc)发展的主要方向,也是目前应用最广、发展最快、价格最便宜、能最早实现大规模生产的一种mmc。在航空航天、汽车、电子、医学等领域具有极高的应用价值,是空间
技术领域:
中理想的结构材料。碳化硅增强铝基复合材料拥有优异的性能,但因为碳化硅的高强度和硬度,一般的加工方法很难对其加工,并且会对材料产生磨损和残余应力。因此采用射流电解加工对碳化硅增强铝基复合材料进行加工成为一种潜在加工方法。射流电解加工是一种非接触的方法,通过控制加工条件,可以实现工具材料在无热、力的影响下进行材料去除,因此射流电解加工成为一种潜在的加工碳化硅增强铝基复合材料的加工方法。因此探究一种有利于加工碳化硅增强铝基复合材料的射流电解加工具体方法和参数成为迫切需求。技术实现要素:本发明的目的在于克服现有技术的不足,针对传统的加工方法加工碳化硅增强铝基复合材料的种种缺陷,提供了一种利用射流电解加工的方法,能够成功加工出效果良好的碳化硅增强铝基复合材料工件。本发明的技术目的通过下述技术方案予以实现:一种使用射流电解加工碳化硅增强铝基复合材料的方法,按照下述步骤进行:步骤1,将电解液置于压力容器中并将压力容器气压调节到0.1—0.5mpa,在电解液中,溶剂为去离子水,溶质为硝酸钠或者氯化钠,硝酸钠或者氯化钠的浓度为1—5mol/l;步骤2,将喷射阴极和待加工工件安装在工作台上,打开z轴运动平台以调节两者距离,使喷射阴极垂直于待加工工件上方0.4—0.8mm并对准加工位置,喷射阴极与脉冲电源负极相连,并与压力容器相连,待加工工件与脉冲电源正极相连并设定加工平台的移动参数步骤3,打开电解液喷射开关和电解加工电源开关,开始进行电解加工,具体加工参数为加工电压10-45v,电源频率为100—1000hz,喷射阴极直径为0.1—0.6mm,加工间隙为0.4—0.6mm,加工沟槽时喷射阴极移动速度为1—5mm/min,环境温度为20-25℃。在上述技术方案中,在电解液中,硝酸钠或者氯化钠的浓度为1—3mol/l;选用的nano3或者氯化钠的纯度为ar,杂质不超过1%;使用的去离子水电阻率大于0.5mω·cm。在上述技术方案中,电解液放入压力容器中密封好,开关关闭,用气管把压力容器和气泵连接起来,打开气泵,将压力容器气压调节到0.1—0.5mpa,优选0.1—0.3mpa。在上述技术方案中,加工平台的移动参数包括运动初始坐标,运动终点坐标,运动速度。在上述技术方案中,喷射阴极垂直于待加工工件上方0.5—0.8mm。在上述技术方案中,制备点槽时,同时打开电解液喷射开关和电解加工电源开关,开始进行电解加工,直到将点槽打出;制备沟槽时,同时打开电解液喷射开关、电解加工开关和平台行走开关,进行沟槽制备,直至制备完成,加工沟槽时喷射阴极移动速度为1—5mm/min,优选1—2mm/min。在上述技术方案中,电解加工具体加工参数为加工电压20-40v,电源频率为500—1000hz,喷射阴极直径为0.3—0.6mm,加工间隙为0.4—0.6mm,加工沟槽时喷射阴极移动速度为1—2mm/min,环境温度为20-25℃。与现有的技术相比,本发明提供了一种利用电解液对碳化硅增强铝基复合材料进行射流电解加工的方法,减小了常规加工工艺中对本材料的负面影响,以及提高了加工精度和加工效率,并且能够提高加工质量;探索了射流电解加工中的加工参数对加工质量的影响,提供了良好可靠的加工参数。附图说明图1为采用本发明技术方案加工所得的工件形貌超景深显微镜图片。图2为本发明采用的射流电解加工平台示意图,其中1为电解槽,2为喷射阴极,3为阳极工件。图3为本发明使用的碳化硅铝基复合材料的光学显微镜拍摄的照片。具体实施方式下面通过具体实施例对本发明作进一步描述,其中使用的nano3粉末、去离子水的来源如下表所示:药品名称化学式纯度规格生产厂家硝酸钠nano399%分析纯上海泰坦科技公司去离子水h2o—分析纯天津天利化学试剂厂本研究所用材料为20wt%含量的碳化硅铝基复合材料,并对该材料进行了性能测试和形貌观察,如附图3所示。碳化硅复合材料的机械性能测试如下表。按照下述方法进行实施:1.按照浓度计算所需nano3的质量与去离子水体积,准确称量出所需的nano3与去离子水后在烧杯中充分溶解。2.将配置好的溶液倒入压力容器中,密封好,并连接好气泵和射流阴极,调节好容器压力。3.将射流阴极和工件安装在加工平台上,并通过加工平台调整阴极位置,使得阴极垂直于工件上方,加工间隙为0.5mm。4.设定加工平台的实验参数包括运动初始坐标,运动终点坐标,运动速度,加工电压以及电源频率。5.加工点槽时开启射流开关和加工电源,进行射流电解加工,实验过程根据加工深度计算加工时间;加工沟槽时,同时开启射流开关、加工电源和平台移动机构。6.对所得的加工工件采用超景深显微镜进行观察。实施案例11.按照1mol/l浓度计算所需nano3质量与去离子水体积,准确称量出所需的nano3与去离子水后在烧杯中充分溶解。2.将配置好的溶液倒入压力容器中,密封好,并连接好气泵和射流阴极,调节容器压力为0.2mpa。3.将射流阴极和工件安装在加工平台上,并通过加工平台调整阴极位置,使得阴极垂直于工件上方,加工间隙为0.5mm。4.设定加工平台的实验参数包括运动初始坐标0(μm),运动终点坐标0(μm),运动速度0(μm/s),以及加工电压20v,电源频率1000hz,加工温度25℃。5.同时开启射流开关和加工电源,进行电解加工,进行时间为1min。6.加工所得的工件采用超景深显微镜进行观察。加工出的工件点槽深度为132.4μm,凹坑平均直径为1630.3μm,表面光滑且直径均匀。实施案例21.按照2mol/l浓度计算所需nano3质量与去离子水体积,准确称量出所需的nano3与去离子水后在烧杯中充分溶解。2.将配置好的溶液倒入压力容器中,密封好,并连接好气泵和射流阴极,调节容器压力为0.2mpa。3.将射流阴极和工件安装在加工平台上,并通过加工平台调整阴极位置,使得阴极垂直于工件上方,加工间隙为0.5mm。4.设定加工平台的实验参数包括运动初始坐标0(μm),运动终点坐标0(μm),运动速度0(μm/s),以及加工电压20v,电源频率1000hz,加工温度25℃。5.同时开启射流开关和加工电源,进行电解加工,进行时间为1min。6.加工所得的工件采用超景深显微镜进行观察。加工出的工件点槽深度为159.7μm,凹坑平均直径为1576.3μm,表面光滑且直径均匀。实施案例31.按照2mol/l浓度计算所需nano3质量与去离子水体积,准确称量出所需的nano3与去离子水后在烧杯中充分溶解。2.将配置好的溶液倒入压力容器中,密封好,并连接好气泵和射流阴极,调节容器压力为0.2mpa。3.将射流阴极和工件安装在加工平台上,并通过加工平台调整阴极位置,使得阴极垂直于工件上方,加工间隙为0.5mm。4.设定加工平台的实验参数包括运动初始坐标0(μm),运动终点坐标600(μm),运动速度3(μm/s),以及加工电压45v,电源频率1000hz,加工温度25℃。5.同时开启平台移动机构、射流开关和加工电源,进行电解加工,进行时间为3min。6.加工所得的工件采用超景深显微镜进行观察。加工出的工件沟槽深度为1365μm,宽度为135μm,表面光滑且直径均匀。根据本
发明内容进行工艺参数的调整,均可实现针对碳化硅铝基复合材料的电解加工,且表现出与本发明基本一致的性能。以上对本发明做了示例性的描述,应该说明的是,在不脱离本发明的核心的情况下,任何简单的变形、修改或者其他本领域技术人员能够不花费创造性劳动的等同替换均落入本发明的保护范围。当前第1页12