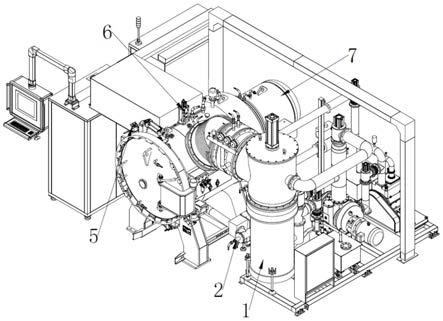
1.本发明属于电阻炉领域,涉及真空钎焊炉。
背景技术:2.常规脱脂热处理工艺主要是将待热处理成型的工件送入炉体内,关闭炉门,向炉内送入 载流气体后升温并抽真空,检测炉内气压和收集排出气体的捕蜡罐组气压,并以此调节载流 气体的流量和捕蜡罐组的真空度,保持炉内气压与捕蜡罐组的压差在设定范围内,即常规脱 脂热处理工艺需向炉内送入载流气体(氢气或氮气),且在运行过程中不断运算炉内气压与 捕蜡罐组的压差,运算过程及结构较为复杂,同时在热处理过程中,存在炉内压力较高,不 利于有些产品的热处理的问题,本发明有效地解决了这种问题。
技术实现要素:3.本发明为了克服现有技术的不足,提供真空钎焊炉。
4.为了实现上述目的,本发明采用以下技术方案:真空钎焊炉,其特征在于:包括真空系 统、冷凝脱脂系统和炉体,炉体内设置有控温系统、冷却系统、工艺管路系统、装载系统和 接线柱系统,真空系统至少包括一级真空管路、二级真空管路和三级真空管路,一级真空管 路、二级真空管路和三级真空管路控制不同工艺阶段的炉体压力,冷凝脱脂系统包括冷凝脱 脂装置和油脂收集装置,冷凝脱脂装置包括一级冷凝机构和二级冷凝机构,油脂收集装置包 括一级油脂收集件和二级油脂收集件,混合气体依次经一级冷凝机构和二级冷凝机构脱脂, 脂类物质通过一级油脂收集件和二级油脂收集件收集;控温系统包括隔热组件、加热组件和 水冷电极,控温系统用于工件加热;冷却系统包括热风循环机构和冷却机构,热风循环机构 包括风机和排气组件,冷却机构包括热交换器,热风循环机构和冷却机构将炉体内的热量通 过热量交换排出炉体,冷却系统用于工件冷却;工艺管路系统包括真空解除回路、氮气注入 回路和工艺气体注入回路,真空解除回路、氮气注入回路和工艺气体注入回路分别用于炉体 的不同工艺,真空解除回路包括真空解除阀,氮气注入回路包括氮气注入阀,工艺气体注入 回路包括工艺气体注入阀,真空解除阀、氮气注入阀以及工艺气体注入阀控制炉体的工艺; 装载系统用于装载工件。
5.进一步的;所述一级真空管路包括初级泵、一级初级阀、二级初级阀、三级初级阀和尾 箱,二级真空管路包括次级泵、一级次级阀、二级次级阀和三级次级阀,三级真空管路包括 主泵和主阀,主阀固设在主泵上侧,两者相互连通,主阀通过进气管与炉体连通,一级真空 管路、二级真空管路以及三级真空管路各部件通过管道连通,尾箱与初级泵连通,三级初级 阀通过管道与进气管连通,二级初级阀通过管道与初级泵连接,三级初级阀通过通过管道与 初级泵连接,二级初级阀与冷凝脱脂系统的出气端连接,冷凝脱脂系统的进气端与炉体连接, 冷凝脱脂系统和二级初级阀,形成混合气体由冷凝脱脂系统导入和脱脂、二级初级阀导出的 工件脱脂通路,炉体、冷凝脱脂系统、二级初级阀、初级泵以及尾箱形成一级压力控制通路, 压力范围设置在1-10pa。
6.进一步的;所述二级次级阀与主阀通过管道连通,二级次级阀与次级泵通过管道连通, 次级泵与一级初级阀连通,一级初级阀与初级泵连通,炉体、进气管、主阀、二级次级阀、 次级泵、一级初级阀、初级泵以及尾箱形成二级压力控制通路,次级泵以及初级泵控制炉体 压力,压力范围设置在10-1-10-2
pa,一级次级阀通过管道与主泵连通,二级次级阀与次级泵 的连通管道与一级次级阀连通,炉体、进气管、主阀、主泵、一级次级阀、次级泵、一级初 级阀、初级泵以及尾箱形成三级压力控制通路,主泵、次级泵以及初级泵控制炉体压力,压 力范围设置在10-3-10-4
pa。
7.进一步的;所述一级冷凝机构设置为倾斜结构,一级冷凝机构通过进气组件与炉体连通, 混合气体经进气组件向一级冷凝机构流通,一级冷凝机构包括一级冷凝管和一级进气管,一 级进气管与二级冷凝机构连通,一级冷凝管的一级冷却介质入口和一级冷却介质出口位于一 级进气管外部,一级冷凝管通过冷却介质将混合气体中的脂类物质状态转化为液态和固态; 二级冷凝机构包括二级冷凝管和二级进气管,二级进气管与油脂收集装置连通,一级进气管 与二级进气管连通,二级冷凝管的二级冷却介质入口和二级冷却介质出口位于二级进气管外 部,二级冷凝管通过冷却介质将混合气体中的脂类物质状态转化为液态和固态,混合气体经 一级冷凝机构部分脱脂后通过二级冷凝机构进一步脱脂。
8.进一步的;所述油脂收集装置包括箱体、设置在箱体内的一级油脂收集件和二级油脂收 集件,一级油脂收集件位于二级油脂收集件的上方,且两者连通,一级油脂收集件与二级冷 凝机构的二级进气管连通,液态脂类物质以及混合气体与一级油脂收集件热交换冷凝的液态 脂类物质通过穿孔流向二级油脂收集件。
9.进一步的;所述炉体包括炉门、炉膛和炉尾,炉门、炉膛和炉尾的壳体分别采用双层结 构,包括位于外侧的外层以及位于内侧的内层,外层与内层之间形成夹层,冷却介质通入夹 层,控制炉体的外表面温升不大于25℃,内层采用真空气密结构,控制炉体的漏率不大于 1.3x10-7
pa.l/s,外层和内层采用钢质材料,炉膛内设置为炉腔。
10.进一步的;所述控热系统包括隔热组件、加热组件和水冷电极,隔热组件包括若干层叠 设置的隔热屏,加热组件包括若干加热器,加热组件位于隔热组件内,加热组件控制炉体内 炉腔的温度,隔热组件将加热组件辐射的热量进行反射,防止热量散失,水冷电极用于对加 热器供电,通过冷却水对水冷电极进行冷却;隔热组件包括隔热密封盖、隔热膛和隔热安装 盖,隔热密封盖固定安装在隔热膛的一端,隔热安装盖可拆卸安装在隔热膛的另一端,隔热 密封盖、隔热膛和隔热安装盖形成隔热腔体,加热组件安装在隔热腔体内,所述隔热密封盖、 隔热膛和隔热安装盖分别由若干隔热屏层叠设置,位于隔热密封盖、隔热膛和隔热安装盖位 置的隔热屏形状分别与隔热密封盖、隔热膛和隔热安装盖形状相配,隔热膛的若干隔热屏沿 隔热膛径向依次向内层叠;冷却系统包括热风循环机构和冷却机构,热风循环机构包括风机 和排气组件,冷却机构包括热交换器,热风循环机构和冷却机构将炉腔内热量通过热量交换 排出炉体;工艺管路系统包括真空解除回路、氮气注入回路和工艺气体注入回路,真空解除 回路、氮气注入回路和工艺气体注入回路分别用于炉体的不同工艺,真空解除回路包括真空 解除阀,氮气注入回路包括氮气注入阀,工艺气体注入回路包括工艺气体注入阀,真空解除 阀、氮气注入阀以及工艺气体注入阀控制炉体的工艺;装载系统包括升降结构和石墨盒体, 升降结构包括升降动力机构和顶盖,石墨盒体固设有观察孔,工件安装在石墨盒体内,升降动 力机构控制顶盖移动,用于密封或远离观察孔,观察
孔用于观察石墨盒体内的工件。
11.进一步的;所述接线柱系统包括底座、压板、限位套、紧固密封机构和固定密封机构, 风机包括电极,紧固密封机构将限位套和底座密封固设连接,固定密封机构将限位套和电极 密封固设连接。
12.进一步的;所述底座上设置有矩形阵列分布的多组紧固孔,压板上固设有与紧固孔位置 相对的连接孔,紧固孔和连接孔一一对应,紧固件穿过紧固孔和连接孔将底座和压板固设连 接;底座包括面向炉腔的炉腔侧和面向炉尾的炉尾侧,压板固设在底座的炉尾侧,底座固设 有相互连通的第一安装腔和第二安装腔,第一安装腔与炉腔侧连通,第二安装腔与炉尾侧连 通,电极安装在第一安装腔和第二安装腔内;限位套包括方端和圆端,限位套的圆端贯穿第 二安装腔,限位套的方端安装至第一安装腔内,方端上固设有环腔,环腔内套设有第一o形 圈,紧固密封机构包括平垫圈、弹簧垫圈和薄螺母,平垫圈、弹簧垫圈和薄螺母依次安装在 限位套上,调节薄螺母将限位套与底座固设连接;所述限位套内固设有相互连通的第一贯穿 腔和第二贯穿腔,第一贯穿腔贯穿限位套方端,第二贯穿腔贯穿限位套圆端,电极包括用于 拧紧的扁平端和用于安装的安装端,扁平端对称固设在安装端的两端,电极贯穿第一贯穿腔 和第二贯穿腔,安装端位于第一贯穿腔和第二贯穿腔,扁平端分别位于限位套方端和圆端的 端面的外侧,固定密封机构位于第二贯穿腔与电极间的间隙内,固定密封机构包括第二o形 圈、隔套、第三o形圈、垫圈和调节螺母,第二o形圈、隔套、第三o形圈、垫圈和调节螺 母依次安装在电极上,通过调节螺母使固定密封机构与电极固设连接。
13.进一步的;所述真空系统还包括压力维持机构,压力维持机构包括维持泵,维持泵分别 与三级次级阀和尾箱通过管道连通,炉体、进气管、主阀、主泵、三级次级阀、维持泵以及 尾箱形成压力维持通路,维持泵将压力范围维持在10-3-10-4
pa。
14.综上所述,本发明的有益之处在于:
15.1)、本发明采用高真空气动挡板阀作为各回路的开关阀,采用旋片泵获得炉体低真空 1-10pa,满足脱脂工艺要求和油扩散泵的启动要求,采用罗茨泵作为炉体二级泵,是油扩散 泵的前级泵,通过旋片泵与罗茨泵的组合运行,炉体获得压力值为10-1-10-2
pa的真空,采用 油扩散泵作为炉体主泵,通过旋片泵、罗茨泵及油扩散泵的组合运行,炉体获得压力值为 10-3-10-4
pa的真空,本发明采用一级真空管路、二级真空管路和三级真空管路控制不同工艺 阶段的炉体压力,降低设备复杂程度和成本;本发明通过真空管路获得压力值为10-3-10-4pa 的真空度,扩大工件的热处理数量和热处理种类;本发明采用压力维持机构,保证炉体真空 值。
16.2)、本发明采用四重脱脂方式对混合气体进行脱脂,一重为一级冷凝机构脱脂,二重 为二级冷凝机构脱脂,三重为一级油脂收集件脱脂,四重为箱体脱脂,一级冷凝机构和二级 冷凝机构将混合气体中大量的脂类脱脂,一级油脂收集件和箱体将经过冷凝脱脂装置脱脂后 的混合气体中的少量脂类进行脱脂处理,实现脂类与气体有效分离,提高了排放气体的洁净 度,减少对设备和环境的污染。
17.3)、本发明的一级冷凝机构设置为倾斜结构,液态脂类物质在重力作用下向二级冷凝 机构流动直至流向油脂收集装置,相比于与水平面无角度的一级冷凝机构,采用倾斜设置提 高了油脂收集的速度,同时尽可能保证一级进气管内的液态油脂无遗留,避免遗留
的液态油 脂影响一级冷凝与混合气体的热交换,降低脱脂速度;本发明将一级冷凝机构设置为倾斜结 构,二级冷凝机构设置为水平结构,且二级进气管的长度小于一级进气管的长度,通过上述 的结构设计一级冷凝机构将混合气体中大部分的脂类物质脱出,二级冷凝机构将混合气体中 小部分的脂类物质脱出,冷凝二级进气管转化的液态脂类物质通过一级冷凝机构转化的液态 脂类物质的重力作用共同流向油脂收集装置,优化设备的结构,有效实现提高了脱脂的效率。
18.4)、本发明的炉体采用双层结构,冷却介质通入夹层,保证炉体的外表面温升不大于 25℃,内层采用真空气密结构,保证炉体的漏率不大于1.3x10-7 pa.l/s,同时将炉体作为相 关设备的安装载体减小设备占地面积。
19.5)、本发明利用层叠设置的隔热屏,逐层将加热器辐射的热量进行反射,有效防热量 散失以及降低炉膛内表面温度,本发明在隔热膛外表面沿轴线方向设计若干隔热环杆,隔热 环杆外表面弧度与炉腔内表面的弧形相配,隔热环杆可加强隔热屏层叠安装的强度,保证稳 定性,本发明加热器采用高温电阻发热元件,若干加热器沿隔热膛轴向依次间隔均匀排布, 保证隔热腔体内热量分布均匀,获得高精度的炉内温度均匀性,从而提高工件品质,减少能 源消耗,提高了生产效率,本发明设计连接固定器连接加热器与隔热屏,连接固定杆套设的 第一定位器位于相邻的隔热屏之间,使相邻隔热屏的间距相同,同时方便隔热屏的安装,连 接固定杆套设的第二定位器位于内层隔热屏与加热器之间,使若干加热器与隔热屏的间距保 持恒定,本发明采用水冷电极对加热器供电,使水冷电极受到辐射升高后,冷却水对水冷电 极进行冷却,能有效提高水冷电极的使用寿命。
20.6)、本发明通过冷风连接杆固定连接冷风固定端和冷风连接端,加强冷风分配器的强 度本发明将冷风管一端设置为密封端,从而使氮气沿气流通通道通过冷风出气管向炉腔喷出, 提高氮气的喷出量以及喷出速度,同时保证氮气喷出的均匀性,本发明通过冷却装置,保证 炉腔内的换热均匀性,保证工件冷却速度一致性,有效提高工件质量,提高了生产效率;本 发明的真空解除阀、氮气注入阀以及工艺气体注入阀采用高真空气动挡板阀作为各回路的开 关阀,通过真空解除阀、氮气注入阀以及工艺气体注入阀的开启实现向炉体送入氮气,或解 除炉内真空,以便开启炉门;或向炉内送入工艺气体,实现了不同工艺要求。
21.7)、本发明通过限位套将电极安装在底座上,并通过紧固密封机构将限位套和底座密 封连接,固定密封机构将限位套和电极密封连接,从而改善接线柱的密封性能,同时方便维 护调整;本发明减小了密封材料向炉腔内油脂的蒸发量,减小了对炉膛的污染;本发明无需 灌胶机和专用工装,从而降低制造和使用成本。
附图说明
22.图1为本发明真空钎焊炉示意图。
23.图2为本发明的真空系统和冷凝脱脂系统装配示意图。
24.图3为本发明装置示意图。
25.图4为本发明装置的俯视图示意图。
26.图5为图4中a方向的示意图。
27.图6为图5中b-b的剖切示意图。
28.图7为图6中c-c的剖切示意图。
29.图8为本发明的炉体内装置半剖示意图。
30.图9为本发明的控温系统示意图。
31.图10为图8中d的放大示意图。
32.图11为本发明的冷却系统示意图。
33.图12为本发明的冷风分配器示意图。
34.图13为本发明的冷风分配器半剖示意图。
35.图14为本发明的工艺管路系统示意图。
36.图15为本发明的装载系统示意图。
37.图16为本发明的装置示意图。
38.图17为本发明的装置正视图。
39.图18为本发明的装置俯视图。
40.图19为本发明的装置后视图。
41.图20为图17中e-e的剖切图。
42.图21为图20中f的放大示意图。
43.图22为图20中g的放大示意图。
具体实施方式
44.以下通过特定的具体实例说明本发明的实施方式,本领域技术人员可由本说明书所揭露 的内容轻易地了解本发明的其他优点与功效。本发明还可以通过另外不同的具体实施方式加 以实施或应用,本说明书中的各项细节也可以基于不同观点与应用,在没有背离本发明的精 神下进行各种修饰或改变。需说明的是,在不冲突的情况下,以下实施例及实施例中的特征 可以相互组合。
45.需要说明的是,以下实施例中所提供的图示仅以示意方式说明本发明的基本构想,遂图 式中仅显示与本发明中有关的组件而非按照实际实施时的组件数目、形状及尺寸绘制,其实 际实施时各组件的型态、数量及比例可为一种随意的改变,且其组件布局型态也可能更为复 杂。
46.本发明实施例中所有方向性指示(诸如上、下、左、右、前、后、横向、纵向
……
)仅用 于解释在某一特定姿态下各部件之间的相对位置关系、运动情况等,如果该特定姿态发生改 变时,则该方向性指示也相应地随之改变。
47.实施例一:
48.如图1-22所示,真空钎焊炉包括真空系统1、冷凝脱脂系统2和炉体7,炉体7内设置 有控温系统3、冷却系统4、工艺管路系统5、装载系统6和接线柱系统8,真空系统1至少 包括一级真空管路、二级真空管路和三级真空管路,一级真空管路、二级真空管路和三级真 空管路控制不同工艺阶段的炉体7压力,冷凝脱脂系统2包括冷凝脱脂装置和油脂收集装置, 冷凝脱脂装置包括一级冷凝机构和二级冷凝机构,油脂收集装置包括一级油脂收集件28和二 级油脂收集件29,混合气体依次经一级冷凝机构和二级冷凝机构脱脂,脂类物质通过一级油 脂收集件28和二级油脂收集件29收集;控温系统3包括隔热组件、加热组件和水冷电极33, 控温系统3用于工件加热;冷却系统4包括热风循环机构和冷却机构,热风循环机构
包括风 机41和排气组件,冷却机构包括热交换器44,热风循环机构和冷却机构将炉体内的热量通 过热量交换排出炉体7,冷却系统4用于工件冷却;工艺管路系统5包括真空解除回路、氮 气注入回路和工艺气体注入回路,真空解除回路、氮气注入回路和工艺气体注入回路分别用 于炉体7的不同工艺,真空解除回路包括真空解除阀512,氮气注入回路包括氮气注入阀533, 工艺气体注入回路包括工艺气体注入阀541,真空解除阀512、氮气注入阀533以及工艺气体 注入阀541控制炉体7的工艺;装载系统6用于装载工件。
49.一级真空管路包括初级泵161、一级初级阀111、二级初级阀112、三级初级阀113和尾 箱151,二级真空管路包括次级泵124、一级次级阀121、二级次级阀122和三级次级阀123, 三级真空管路包括主泵142和主阀141,主阀141固设在主泵142上侧,两者相互连通,主 阀141通过进气管131与炉体7连通,一级真空管路、二级真空管路以及三级真空管路各部 件通过管道(图未标识)连通,本实施例中,尾箱151设置有两组,一组尾箱151与初级泵161 连通,三级初级阀113通过管道与进气管131连通,二级初级阀112通过管道与初级泵161 连接,三级初级阀113通过通过管道与初级泵161连接,二级初级阀112与冷凝脱脂系统2 的出气端连接,冷凝脱脂系统2的进气端与炉体7连接,冷凝脱脂系统2和二级初级阀112, 形成混合气体由冷凝脱脂系统2导入和脱脂、二级初级阀112导出的工件脱脂通路,炉体7、 冷凝脱脂系统2、二级初级阀112、初级泵161以及尾箱151形成一级压力控制通路(或称脱 脂通路),压力范围设置在1-10pa,控温系统3以及冷却系统4控制工件的温度,本实施例 中,控温系统3按照50-100℃/h的速率升温,控温系统3将位于炉体7有效区的工件以及环 境温度控制在300-400℃,该温度范围下将工件内的粘结剂及成型剂逐步气化形成混合气体, 混合气体沿一级压力控制通路流通,混合气体中油脂经过冷凝脱脂系统2脱脂处理,进一步 的,设定炉体7的脱脂时间,脱脂时间范围设置在1.5h-2.5h,优选为2h,保证工件脱脂完 全,上述压力控制以及温度控制不仅满足工件的脱脂要求,同时满足主泵142的启动要求。
50.二级次级阀122与主阀141通过管道连通,二级次级阀122与次级泵124通过管道连通, 次级泵124与一级初级阀111连通,一级初级阀111与初级泵161连通,由上可知,炉体7、 进气管131、主阀141、二级次级阀122、次级泵124、一级初级阀111、初级泵161以及尾 箱151形成二级压力控制通路,次级泵124以及初级泵161控制炉体7压力,压力范围设置 在10-1-10-2
pa,本实施例中,控温系统3按照50-100℃/h的速率升温,控温系统3将工件温 度控制在400-1200℃,上述压力控制以及温度控制,满足主泵142的启动要求。
51.一级次级阀121通过管道与主泵142连通,二级次级阀122与次级泵124的连通管道与 一级次级阀121连通,炉体7、进气管131、主阀141、主泵142、一级次级阀121、次级泵124、一级初级阀111、初级泵161以及尾箱151形成三级压力控制通路,主泵142、次级泵 124以及初级泵161控制炉体7压力,压力范围设置在10-3-10-4
pa,本实施例中,控温系统3 按照50-100℃/h的速率升温,控温系统3将工件温度控制在400-1200℃并转定温,上述压 力控制以及温度控制,满足工件热处理的真空要求。
52.真空系统1还包括压力维持机构,压力维持机构包括维持泵171,维持泵171分别与三 级次级阀123和另一组尾箱151通过管道连通,炉体7、进气管131、主阀141、主泵142、 三级次级阀123、维持泵171以及尾箱151形成压力维持通路,维持泵171将压力范围维持 在10-3-10-4
pa,满足工件正常热处理的真空要求。
53.进一步的,当炉体7压力大于10-3
pa后,主阀141开启,主泵142运行,通过主阀141 和主泵142调节炉体7压力,将炉体7压力范围控制在10-3-10-4
pa,依此循环,直至工件加 热完成。
54.本实施例中,初级泵161和维持泵171采用旋片泵,次级泵124采用罗茨泵,主泵142 采用油扩散泵,主阀141采用三级阀。
55.在其他实施例中,尾箱151的数量也可设置为一组,维持泵171以及初级泵161可与一 组尾箱151连通。
56.本实施例中,一级初级阀111、二级初级阀112、三级初级阀113、一级次级阀121、二 级次级阀122、三级次级阀123以及主阀141采用高真空气动挡板阀。
57.如图3-7所示,冷凝脱脂系统2包括冷凝脱脂装置和油脂收集装置,冷凝脱脂装置包括 一级冷凝机构和二级冷凝机构,油脂收集装置包括一级油脂收集件28和二级油脂收集件29, 混合气体依次经一级冷凝机构和二级冷凝机构脱脂,脂类物质通过一级油脂收集件28和二级 油脂收集件29收集。
58.冷凝脱脂装置与炉体7连通,油脂收集装置与真空系统1连通,由炉体7导出的混合气 体经冷凝脱脂装置的冷凝作用脱脂,油脂收集装置收集油脂,脱脂气体导入真空系统1。
59.一级冷凝机构通过冷凝进气组件27与炉体7连通,混合气体经冷凝进气组件27向一级 冷凝机构流通,具体来说,一级冷凝机构包括一级冷凝管251和冷凝一级进气管250,冷凝 一级进气管250一端可拆卸连接有冷凝封盖2501,另一端与二级冷凝机构连通,一级冷凝管 251贯穿冷凝封盖2501延伸至冷凝一级进气管250内部并与冷凝封盖2501固设连接,一级 冷凝管251的一级冷却介质入口2511和一级冷却介质出口2512位于冷凝一级进气管250外 部,实现冷却介质的循环流通,本实施例中,冷却介质控制一级冷凝管251的管壁温度不高 于30℃,通过一级冷凝管251将混合气体中的脂类物质的状态转化为液态和固态,方便油脂 的收集,进一步的,如图6所示,一级冷凝机构设置为倾斜结构,与水平面的倾斜角度本实 施例优选为5
°
,从而使冷凝一级进气管250内转化的液态脂类物质在重力作用下向二级冷 凝机构流动直至流向油脂收集装置,相比于与水平面无角度的一级冷凝机构,采用倾斜设置 提高了油脂收集的速度,同时尽可能保证冷凝一级进气管250内的液态油脂无遗留,避免遗 留的液态油脂影响一级冷凝管251与混合气体的热交换,降低脱脂速度。
60.二级冷凝机构与一级冷凝机构连通,如图6所示,一级冷凝机构设置为倾斜结构,二级 冷凝机构与水平面平行,二级冷凝机构与一级冷凝机构的脱脂原理相同,具体来说,二级冷 凝机构包括二级冷凝管252和冷凝二级进气管253,根据图4的视觉角度,一级冷凝机构与 二级冷凝机构垂直或近似垂直连接,本实施例中,冷凝二级进气管253的长度设置为小于冷 凝一级进气管250的长度,一级冷凝机构将混合气体中大部分的脂类物质脱出,二级冷凝机 构将混合气体中小部分的脂类物质脱出,由一级冷凝机构转化的液态脂类物质在重力作用下 流向冷凝二级进气管253,并带动由冷凝二级进气管253转化的液态脂类物质共同流向油脂 收集装置;冷凝二级进气管253一端可拆卸连接有冷凝端盖2531,另一端与油脂收集装置连 通,冷凝一级进气管250与冷凝二级进气管253连通,混合气体经一级冷凝机构部分脱脂后 通过冷凝一级进气管250向二级冷凝机构的冷凝二级进气管253流通,并通过二级冷凝机构 进一步脱脂,二级冷凝管252贯穿冷凝端盖2531延伸至冷凝二级进气管253部并与冷凝端盖 2531固设连接,二级冷凝管252的二级冷却介质入口2521和二
级冷却介质出口2522位于冷 凝二级进气管253外部,实现冷却介质的循环流通,本实施例中,冷却介质控制二级冷凝管 252的管壁温度不高于30℃,通过二级冷凝管252将混合气体中的脂类物质的状态转化为液 态和固态,方便油脂的收集。
61.冷凝脱脂装置的脱脂实施过程如下,需要脱脂时,在真空系统1的作用下,混合气体从 炉体7通过冷凝进气组件27进入冷凝一级进气管250,一级冷凝管251降低冷凝一级进气管 250管壁温度,混合气体与一级冷凝管251和冷凝一级进气管250管壁发生热交换,降低脂 类物质温度,当脂类物质温度降到一定的温度范围,本实施例优选温度范围在120℃~80℃ 之间,脂类物质冷凝为液态,并沿一级冷凝管251外管壁、冷凝一级进气管250和冷凝二级 进气管253流向油脂收集装置,已部分脱脂的混合气体由冷凝一级进气管250进入冷凝二级 进气管253,二级冷凝机构采用与一级冷凝机构相同的脱脂原理,已部分脱脂的混合气体通 过二级冷凝管252的冷凝作用继续将脂类物质转化为液态脂类,并流向油脂收集装置,另外, 附着在一级冷凝管251以及冷凝二级进气管253外管壁的液态脂类物质,通过冷却介质的作 用,温度进一步降低,本实施例优选降低的温度范围在80℃~30℃之间,液态脂类物质转化 为固态,即附着在一级冷凝管251以及冷凝二级进气管253外管壁表面成为凝聚核,促使其 周围的液态脂类物质在其表面凝聚,转变为固态,一级冷凝管251以及二级冷凝管252表面 的固态脂类温度达到一定厚度,会影响一级冷凝管251以及二级冷凝管252与混合气体的热 交换,在具备关断脱脂设备条件时,拆卸冷凝封盖2501以及冷凝端盖2531,将一级冷凝机 构和二级冷凝机构分别从冷凝一级进气管250和冷凝二级进气管253抽出,清理掉一级冷凝 管251和二级冷凝管252外管壁的固态脂类物质,同时清洗冷凝一级进气管250和冷凝二级 进气管253,清理完成后的一级冷凝管251和二级冷凝管252重新安装。
62.油脂收集装置包括冷凝管脱脂箱体21、设置在冷凝管脱脂箱体21内的一级油脂收集件 28和二级油脂收集件29,一级油脂收集件28位于二级油脂收集件29的上方,且两者连通, 一级油脂收集件28与冷凝二级进气管253连通,冷凝二级进气管253延伸至一级油脂收集件 28,本实施例中,一级油脂收集件28设置为桶装结构,一级油脂收集件28由冷凝固定板281、 冷凝盲板284以及连接冷凝固定板281和冷凝盲板284的冷凝侧板282构成,冷凝固定板281 与冷凝管脱脂箱体21连接,冷凝二级进气管253贯穿冷凝固定板281向一级油脂收集件28 内部延伸,冷凝侧板282上固设有若干冷凝穿孔283,液态油脂物质先流向一级油脂收集件 28,之后通过冷凝穿孔283流向二级油脂收集件29的冷凝收集腔291内,同时通过二级冷凝 管252的冷凝作用,使一级油脂收集件28的温度与冷凝二级进气管253保持在同一温度范围 内,经冷凝脱脂装置脱脂的混合气体通入一级油脂收集件28,冷凝盲板284位于混合气体的 流动方向上,混合气体受到冷凝盲板284的阻挡,降低了运行速度及温度,使其内设置的状 态冷凝为液态,通过冷凝穿孔283流向二级油脂收集件29,进一步的为保证经冷凝脱脂装置 脱脂的混合气体能够尽可能与一级油脂收集件28进行热交换,而不是直接通过冷凝穿孔283 向冷凝管脱脂箱体21流通,本实施例中,冷凝二级进气管253延伸至一级油脂收集件28的 端面设置为倾斜面,根据图6的视觉角度,倾斜面与冷凝二级进气管253的上端面所成角度 设置为锐角,倾斜面与冷凝二级进气管253的下端面所成角度设置为钝角,有效限制了混合 气体向上流通的路径,从而可使混合气体与一级油脂收集件28进行充分的热交换,进一步对 混合气体进行脱脂,提高了脱脂效率。
63.判断二级油脂收集件29内的液态脂类物质达到一定量时,打开冷凝管脱脂箱体21,将 二级油脂收集件29取出,把液态脂类物质统一收集到指定容器内,进行统一处理;冷凝管脱 脂箱体21上可设置有观察窗,通过视觉观察判断二级油脂收集件29是否需要取出,或在二 级油脂收集件29内设置液位传感器,通过液态脂类物质的高度进行判断二级油脂收集件29 是否需要取出,或在二级油脂收集件29内设置重量传感器,通过液态脂类物质的重量判断二 级油脂收集件29是否需要取出,上述判断方式仅仅只是一部分,本系统适用所有可以判断液 态脂类物质是否达到需要二级油脂收集件29取出清理的程度。
64.冷凝管脱脂箱体21分别连通设置有尾气排放口22和排液口23,排液口23位于冷凝管 脱脂箱体21的下方,尾气排放口22位于冷凝管脱脂箱体21的上方,且尾气排放口22与一 级油脂收集件28位于冷凝管脱脂箱体21的不同侧,根据图6的视觉角度,一级油脂收集件 28位于冷凝管脱脂箱体21的右侧,尾气排放口22位于冷凝管脱脂箱体21的左侧,增加了 混合气体的流通路径,从而增加了混合气体与冷凝管脱脂箱体21内壁的接触面积,进一步对 混合气体进行脱脂,提高了排放气体的洁净度,尾气排放口22与二级初级阀112通过管道连 通,通过尾气排放口22将脱脂气体沿二级初级阀112流通,具体来说,经一级油脂收集件 28脱脂的混合气体通过冷凝穿孔283扩散至冷凝管脱脂箱体21内,混合气体与冷凝管脱脂 箱体21内壁接触进行热交换,混合气体中的脂类物质冷凝成液态,液态脂类物质通过排液口 23排出至指定容器进行统一处理,进一步脱脂的气体从尾气排放口22流通至真空设置,避 免脂类物质在管道中积累以及污染真空系统1,本实施例采用四重脱脂方式对混合气体进行 脱脂,一重为一级冷凝机构脱脂,二重为二级冷凝机构脱脂,三重为一级油脂收集件28脱脂, 四重为冷凝管脱脂箱体21脱脂,一级冷凝机构和二级冷凝机构将混合气体中大量的脂类脱 脂,一级油脂收集件28和冷凝管脱脂箱体21将经过冷凝脱脂装置脱脂后的混合气体中的少 量脂类进行脱脂处理,实现脂类与气体有效分离,提高了排放气体的洁净度,减少对设备和 环境的污染。
65.本实施例中,冷凝管脱脂箱体21上方固设有冷凝把手213,便于搬运。
66.本实施例中,冷凝管脱脂箱体21下方设置有冷凝支撑组件211和冷凝滚动组件212,冷 凝支撑组件211和冷凝滚动组件212分别设置有四组,分别位于冷凝管脱脂箱体21的四周, 冷凝支撑组件211保证对冷凝管脱脂箱体21的平稳支撑,冷凝滚动组件212保证对冷凝管脱 脂箱体21的平稳滚动,从而便于冷凝管脱脂箱体21的移动。
67.如图8所示,炉体7包括炉门71、炉膛72和炉尾73,炉门71、炉膛72和炉尾73的壳 体分别采用双层结构,具体分为位于外侧的外层以及位于内侧的内层,外层与内层之间形成 夹层,夹层除进口与出口外,保持密封状态,冷却介质通入夹层,保证炉体的外表面温升不 大于25℃,冷却介质可采用冷却水或气体,只要能实现对炉体7的冷却作用即可,内层采用 真空气密结构,保证炉体7的漏率不大于1.3x10-7 pa.l/s,外层和内层均可采用钢质材料,炉膛 72内设置为炉腔74,炉腔74内安装控温系统3、冷却系统4、装载系统6以及其他相关设备, 控温系统3安装在冷却系统4内部,装载系统6安装在控温系统3内部,真空系统1、工艺 管路系统5以及其他相关设备安装在炉体7的外部,从而减小设备占地面积;炉体7下方固设 有炉体支撑架75,炉体支撑架75用于支撑炉体7。
68.如图9所示,控温系统3包括隔热组件、加热组件和水冷电极33,隔热组件包括若干层 叠设置的隔热屏31,加热组件包括若干加热器32,加热组件位于隔热组件内,加热组件
控制 炉体7内炉腔74的温度,隔热组件将加热组件辐射的热量进行反射,防热量散失以及降低炉 膛内表面温度。
69.隔热组件包括隔热密封盖35、隔热膛30和隔热安装盖37,隔热密封盖35固定安装在 隔热膛30的一端,隔热安装盖37可拆卸安装在隔热膛30的另一端,隔热密封盖35、隔热 膛30和隔热安装盖37形成隔热腔体,加热组件安装在隔热腔体内。
70.隔热密封盖35、隔热膛30和隔热安装盖37分别由若干隔热屏31层叠设置,位于隔热 密封盖35、隔热膛30和隔热安装盖37位置的隔热屏31形状分别与隔热密封盖35、隔热膛 30和隔热安装盖37形状相配,本实施例中,隔热膛30采用圆柱筒状结构,若干隔热屏31 沿隔热膛30径向依次向内层叠,隔热屏31采用耐高温材料,逐层将加热器32辐射的热量反 射回隔热腔体,防止热量散失,隔热膛30外表面沿轴线方向设置有若干隔热环杆301,隔热 环杆301外表面弧度与炉腔74内表面的弧形相配,隔热环杆301可加强隔热屏31层叠安装 的强度,保证稳定性,隔热膛30一端还设置有隔热安装角302,隔热安装角302用于隔热膛 30和隔热安装盖37的安装;隔热膛30上固设有隔热安装块34,隔热安装块34用于控温系 统3与炉膛72内表面的安装。
71.加热组件位于隔热腔体,加热器32采用筒状结构,采用高温电阻发热元件,如镍铬合 金、钼、石墨和钨等,可根据设备不同的工作温度选用适合的材料,若干加热器32沿隔热膛 30轴向依次间隔均匀排布,保证隔热腔体内热量分布均匀,加热器32与隔热屏31通过若干 连接固定器36固定连接,具体来说,连接固定器36沿隔热膛30圆周方向均匀分布,保证加 热器32安装的稳定性,连接固定器36包括连接固定杆362,根据图7的视觉角度,连接固 定杆362的上端向上依次贯穿隔热屏31并延伸至隔热膛30外侧并通过相应的固定件使连接 固定杆362的上端固定在隔热膛30的外表面,连接固定杆362的下端贯穿加热器32并通过 相应的固定件使连接固定杆362的下端固定在加热器32内表面,进一步的,连接固定杆362 套设有若干第一定位器361和第二定位器363,第一定位器361位于相邻的隔热屏31之间, 使相邻隔热屏31的间距相同,同时方便隔热屏31的安装,第二定位器363位于内层隔热屏 31与加热器32之间,使若干加热器32与隔热屏31的间距保持恒定。
72.水冷电极33依次贯穿炉膛72、隔热膛30并与加热器32连接,本实施例采用水冷电极 33对加热器32供电,水冷电极33自身以及受到辐射温度升高后,冷却水对水冷电极33进 行冷却,能有效提高水冷电极33的使用寿命。
73.如图11-13所示,冷却系统4包括热风循环机构和冷却机构,热风循环机构包括风机41 和排气组件,冷却机构包括热交换器44,热风循环机构和冷却机构将炉腔74内热量通过热 量交换排出炉体7。
74.热风循环机构包括风机41和排气组件,风机41安装在炉尾73内,排气组件位于炉腔 74内,排气组件包括冷风分配器42和冷风管43,冷风分配器42一侧与风机41安装,另一 侧与冷风管43安装。
75.冷风分配器42包括冷风固定端421和冷风连接端422,冷风固定端421和冷风连接端 422一体成型,冷风固定端421与风机41连接,冷风连接端422与冷风管43连接,冷风固 定端421、冷风连接端422以及冷风管43形成气体或氮气流通通道。
76.本实施例中,冷风连接端422的宽度大于冷风固定端421的宽度,两者形成几字型,冷 风连接端422和冷风固定端421设置为壳体结构,冷风连接端422内设置有冷风分配腔
4211, 冷风分配腔4211整体设计为圆柱型,风机1的输出端安装在冷风分配腔4211,冷风连接端 422内设置有冷风腔4222,冷风腔4222整体同样设计为圆环型,但相较于冷风分配腔4211, 冷风腔4222的厚度更小,形成较为扁平的结构,冷风分配腔4211与冷风腔4222连通,氮气 在由冷风分配腔4211流通至扁平结构的冷风腔4222中,氮气受到压缩,氮气压强增大,可 提高氮气的出气速度,冷风连接端422上还设置有若干冷风连通孔4221,若干冷风连通孔4221 呈环形分布在冷风连接端422的圆周方向,冷风连通孔4221与冷风腔4222连通,冷风管43 安装在冷风连通孔4221,使冷风分配腔4211、冷风腔4222、冷风连通孔4221以及冷风管43 构成氮气流通通道。
77.冷风分配器42还包括冷风安装板423,冷风安装板423用于安装冷却机构,冷风固定端 421、冷风连接端422以及冷风安装板423通过冷风连接杆424固设连接,冷风连接杆424还 可用于加强冷风分配器42的强度。
78.本实施例中,若干冷风管43以冷风分配器42轴线为中心呈环形分布在冷风管43圆周 方向,若干冷风管43形成用于放置控温系统3的冷风装载腔,即控温系统3整体位于冷风装 载腔内,冷风管43分布在隔热膛30的外部,冷风管43设置为中空的管状结构,冷风管43 连通设置有若干冷风出气管431,冷风出气管431的出口方向朝向冷风装载腔,冷风管43的 一端与冷风连通孔4221安装,冷风管43的另一端设置为密封端,从而使氮气沿气流通通道 通过冷风出气管431向炉腔74喷出,提高氮气的喷出量以及喷出速度,同时保证氮气喷出的 均匀性。
79.冷却机构包括热交换器44,热交换器44安装在冷风安装板423,热交换器44设置有水 冷装置,水冷装置设置有水冷进口和水冷出口45,水冷进口和水冷出口45延伸至炉体7外 部,实现水循环。
80.本实施例实施过程中,控温系统3完成加热后,风机41将氮气通过热风循环机构送入 炉腔74内,氮气吸收炉腔74内的热量使温度升高后,在风机41的作用下,氮气经过热交换 器44将热量传递给热交换器44内的水冷装置,受热的冷却水由水冷出口45将热量传递到炉 体7外部,即风机41将送进炉腔74内的氮气在炉腔74内进行定向循环,热交换器44通过 热交换作用实现将降低炉腔74温度的目的,通过本实施例的换热结构,保证炉腔74内的换 热均匀性,使不同位置的工件冷却速度基本相同,有效提高工件质量,冷却速度保持在 50-100℃/h。
81.如图16-22所示,接线柱系统8包括底座81、压板82、限位套83、紧固密封机构和固 定密封机构,风机41包括电极84,紧固密封机构将限位套83和底座81密封固设连接,固 定密封机构将限位套83和电极84密封固设连接,保证密封性。
82.本实施例中,底座81设置为方型结构,底座81优选采用赛钢,压板82设置为方环型 结构,底座81上设置有矩形阵列分布的多组紧固孔813,压板82上固设有与紧固孔813位 置相对的连接孔821,紧固孔813和连接孔821一一对应,紧固件穿过紧固孔813和连接孔 821将底座81和压板82固设连接。
83.根据图20的视觉角度,底座81设置有左右对称的两组侧面,包括面向炉腔74的炉腔 侧811和面向炉尾73的炉尾侧812,压板82固设在底座81的炉尾侧812,底座81沿宽度方 向固设有相互连通的第一安装腔814和第二安装腔815,第一安装腔814与炉腔侧811连通, 第二安装腔815与炉尾侧812连通,第一安装腔814的横截面设置为方形,第二安装腔815 的
机构611和顶盖613,石墨盒体62固设有观察孔64,工件安装在石墨盒体62内,升降动力机 构611控制顶盖613移动,用于密封或远离观察孔64,观察孔64用于观察石墨盒体62内的 工件是否安装到位。
97.升降结构61包括升降动力机构611和顶盖613,升降动力机构611包括升降杆612,顶 盖613固设在升降杆612端面,升降动力机构611通过驱动升降杆612升降控制顶盖613在 竖直方向的移动。
98.石墨盒体62设置为通过若干盖板拼装成的箱型结构,并通过盖门622实现石墨盒体62 的封装,盖门622与石墨盒体62可拆卸安装,盖门622的安装方向为工件进出石墨盒体62 的方向,盖门622与石墨盒体62具体通过盖门压杆624实现可拆卸安装,具体来说,石墨盒 体62上固设有两组对称的安装块623,安装块623上固设有安装卡腔6231,盖门压杆624的 两端对称固设有压杆槽口6241,压杆槽口6241与安装卡腔6231配合,实现盖门压杆624与 安装块623扣合安装,从而通过盖门压杆624将盖门622压紧在石墨盒体62上,整体结构简 单,操作方便。
99.本实施例中,观察孔64位于石墨盒体62上方的盖板,观察孔64尺寸小于顶盖613尺 寸,顶盖613可将观察孔64完全封闭,使石墨盒体62内部形成密封盒体。
100.石墨盒体62还设置有排气阀63,排气阀63优选安装在石墨盒体62上方的盖板,当石墨 盒体62内的真空度大于隔热腔体的真空度时,排气阀63打开,石墨盒体62内的气体向腔体 排放。
101.本实施例中,盖板、盖门622采用等静压石墨材料。
102.本实施例中,装载系统6安装在控温系统3的隔热腔体内,升降动力机构611安装在炉 体7的炉膛72外表面,升降杆612依次贯穿炉膛72和隔热膛30,并延伸至隔热腔体内,升 降杆612与炉膛72和隔热膛30滑动连接,升降动力机构611驱动升降杆612升降控制顶盖 613与观察孔64保持密封状态或远离状态。
103.本发明实施过程中,氮气注入回路向炉体7的炉腔74注入氮气进行吹扫,工件放置在 石墨盒体62,炉体7通过真空系统1进行进行抽真空处理,保证炉腔74的真空度保持在10-3
~ 10-4
pa,控温系统3对炉腔74加热,工艺气体注入回路向炉腔74注入工艺气体,对工件进 行热处理,混合了粘结剂及成型剂的混合气体抽取至真空系统1的脱脂机构进行脱脂处理, 减小对炉膛72的污染,工件热处理后,冷却系统4启动,有效控制工件冷却速度,保证工件 冷却速度一致性,提高了生产效率,工件冷却至工艺设定温度后,真空解除回路向炉腔74输 送真空空气,解除炉腔74内的真空状态,开启炉门71,将装载工件的石墨盒体62取出,拆 卸盖门压杆624,将工件取出即可。
104.显然,所描述的实施例仅仅是本发明的一部分实施例,而不是全部的实施例。基于本发 明中的实施例,本领域普通技术人员在没有做出创造性劳动前提下所获得的所有其他实施例, 都应当属于本发明保护的范围。