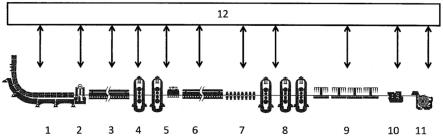
1.本发明涉及用于在热轧带材机组中热成型时控制或调节钢带的温度的方法。
背景技术:2.钢带的热成型通常在热轧带材机组中进行。热轧带材机组包括不同的各个单元,例如,炉子、轧机机架、驱动装置、钢带的开卷和卷绕装置或冷却段。已知大量不同的装置或方法用于这些单元的控制或调节。控制或调节主要基于应达值与实际值的比较,并且得出相应的修正措施以遵循应达值。在此,要遵循的应达值基于经验知识和/或先前的过程分析来限定。此外,通常事先形成在钢带的产品特性和单元的要设定的应达值之间的关系。通常,在生产钢带时,在各种各样的应达值和力求的产品特性之间存在复杂的关系。
3.由于设备技术的数字化程度越来越高,与单元相关的工艺模型被用于产生合适的应达值,其引起期望的产品特性。为此,根据数据状态、关系的复杂性和/或消耗,例如可将统计模型、分析模型或神经网络用于与单元相关的工艺模型。
4.对于具有多个单元的带钢热轧机组的这种调节方案的缺点是,在不同的单元上的应达值预设(sollwert-vorgabe)或实际值改变时的相互影响不会被与单元相关的工艺模型和/或单元的控制部或调节部反映出来。尤其在对材料质量有高要求的钢带生产中,时间、温度、微观结构发展的复杂的相互影响难以优化,并且通过准静态的各单元调节部很难对其进行优化。
5.此外,对热轧带材机组的各个单元的控制或调节在以下方面是不利的:各个单元的工艺控制的优化并不总是必然引起整个生产工艺的优化。尤其在与例如连铸设备组合的设备中,可通过更动态的工艺控制来节省能源和生产成本。
技术实现要素:6.本发明的目的在于改进热轧带材机组的已知的控制或调节,使得在整个设备中在例如钢带的产品特性方面对各单元的应达值预设进行了优化。
7.本发明的目的通过具有权利要求1的特征的方法来实现。在为热轧带材机组分配的数据处理系统中,上级工艺模型与单元的至少两个控制部或调节部在线存储和/或交换应达值和/或实际值,该值具有时间、速度、温度、冷却速率和/或加热速率。上级工艺模型基于交换的应达值和/或实际值和/或存储的值并且借助下级工艺模型,例如炉子的温度模型、冷却段的温度模型或在热轧带材机组中的成型的模型,针对在卷取热轧带材之前的至少一个点在线确定钢带的温度。在该点处的预先确定的温度与应达值预设有偏差时,上级工艺模型确定单元的新的应达值预设,将该应达值预设传输给单元的控制部或调节部,以便遵循用于钢带的温度的应达值预设。借助包含至少一个下级工艺模型的优化算法确定新的应达值预设。
8.上级工艺模型基于单元的应达值和/或实际值描绘出钢带的实际的生产状态。通
过合适的工艺模型,例如用于均化炉的能量和材料平衡或用于钢带的微观结构发展的统计模型,上级工艺模型确定例如在将来卷取之前的温度走向的发展。因此可及早识别在各单元的应达值预设和可能的偏差之间的差异。在上级的优化模型中运行的优化算法可优化应达值预设,使得在考虑事先确定的优化目标的情况下在卷取之前达到热轧带材的应达值预设。事先确定的优化目标例如可为生产目标,尤其是能量、产量或质量目标。
9.方法的优选的形式在权利要求2至14中给出。根据权利要求2,优选的是,来自铸造机的坯料的初级产品具有的厚度为db≥1mm至db≤300mm,优选地为db≥50mm至db≤160mm,并且上级工艺模型在确定应达预设时考虑:铸造速度,其优选地在
vg
≥4m/min和
vg
≤6m/min之间,更优选地在
vg
≥5m/min和
vg
≤6m/min之间;和坯料的铸造机离开温度,其优选地为t
ge
≥800℃。
10.优选地,根据权利要求3,优化目标包括能耗、产量、工艺可靠性、产品特性、生产成本和/或设备损耗,这些目标是钢铁生产领域中的优选的控制参数。
11.此外,根据权利要求4,优选的是,针对优选地在卷取热轧带材之前的至少一个点,下级工艺模型确定钢带在热轧带材机组中的微观结构发展。除了优化的温度控制之外,由此引起的微观结构发展对于钢带的其他材料特性和/或处理具有决定性意义。在工艺过程中更精确地控制或调节微观结构发展能够实现及早对偏差做出反应,并且减少废品量和/或后处理。
12.根据权利要求5,在热成型时,理想地使用初轧机架和精轧机架。通过将热成型部分成初轧机架和精轧机架,可调节有利的温度分布和顺序,并且它们还可通过更多数量的测量和调节点更好地表示。因此,上级工艺模型可更好地对偏差做出反应。此外,由此还有更多的可行途经来干预热轧的应达值预设。
13.根据权利要求6和7,优选的是,针对进入到精轧机架中的进入温度的应达值,通过上级工艺模型预设的温度应达值为t
fs
≥850℃至t
fs
≤1050℃,优选地为t
fs
≥900℃至t
fs
≤1000℃,甚至更优选地为t
fs
≥900℃至t
fs
≤950℃。此外,优选的是,针对离开精轧机架的离开温度的应达值,通过上级工艺模型预设的温度应达值在t
fe
≥750℃至t
fe
≤950℃内,优选地在t
fe
≥750℃至t
fe
≤900℃内,甚至更优选地在t
fe
≥800℃至t
fe
≤850℃内。
14.根据权利要求8,针对进入精轧机架中的进入速度的应达值,通过上级工艺模型预设的速度应达值优选地为vf≥0.4m/s至vf≤1m/s。
15.根据权利要求9和10,针对进入初轧机架的进入温度的应达值,通过上级工艺模型预设的温度应达值为t
vs
≥1000℃至t
vs
≤1150℃。离开初轧机架的离开温度的应达值通过上级工艺模型预设到在t
ve
≥950℃至t
ve
≤1100℃的温度范围中。
16.理想地,根据权利要求11和12,针对进入精轧机架中的进入厚度的应达值,通过上级工艺模型预设的应达值为d
fs
≥20mm至d
fs
≤70mm。卷取温度的应达值通过工艺模型优选地预设到在th≥30℃至t
ve
≤750℃的范围中,更优选地预设到在th≥450℃至th≤550℃的范围中。
17.根据权利要求13,优选的是,将钢带中的合金元素c的含量限制到0.03wt%至0.15wt%,和/或将钢带中的合金元素锰的含量限制到0.50wt%至2.00wt%。
18.根据权利要求14,优选的是,将优化的应达值预设用于生产具有相同的生产目标、尤其机械特性的后续的热轧带材。因此,通过相应的应达值预设说明的已经存在的优化的
工艺过程可与相同的材料或钢带类型的继续生产相关。这样节省了优化时间,并能够实现提前对缓慢的设备变化做出反应。
19.根据权利要求15,优选的是,在为热轧带材机组分配的数据处理系统中,上级工艺模型可与单元的至少两个控制部或调节部在线交换和/或存储应达值和/或实际值,该值具有时间、速度、温度、冷却速率和/或加热速率。上级工艺模型基于交换的应达值和/或实际值和/或存储的值并且借助下级工艺模型,针对在卷取热轧带材之前的至少一个点在线预先确定钢带的温度,并且在该点处的预先确定的温度与应达值预设有偏差时确定相应的单元的新的应达值预设。新的应达值预设通过上级工艺模型传输给相应的单元的控制部或调节部,以便遵循用于钢带的温度的应达值预设。在此,借助包括至少一个下级工艺模型的优化算法确定新的应达值预设。
20.下面参考呈实施例的形式的提及的附图详细说明根据本发明的方法。在所有附图中相同的技术元件由相同的附图标记来表示。
附图说明
21.说明书附有三幅附图,其中,
22.图1示出了热轧带材机组的设备示意图;
23.图2示出了具有上级工艺模型的调节简图;
24.图3示出了温度走向的应达值与实际值的比较。
具体实施方式
25.图1示出了用于生产热轧带材的热轧带材机组的一可行的设备简图,在其中使用根据本发明的方法。热轧带材机组包括铸造设备1、两个剪切机2、10、两个炉子3、6、两个初轧机架4、可转移的冷却部5、感应式加热部7、三个精轧机架8、冷却段9以及用来卷起热轧带材的卷取机11。上级的数据处理系统12具有集成的温度和微观结构模型。应达值和实际值通过不同的设备或相关联的调节部、控制部和/或测量装置进行交换,并且例如以数据库的形式进行存储。
26.图2示出了流程图,其中,两个单元、更确切地说两个单元的调节部与相应的工艺模型示例性地联网。上级的数据处理系统i将应达值传送给热轧带材机组的上级工艺模型ii。基于该应达值,例如强度,上级工艺模型ii确定多个应达值或应达值范围,例如相应具有最小和最大温度的温度走向,其被传送给下级工艺模型iiia、iiib。下级工艺模型iiia、iiib从中导出用于相应的单元的特定的应达值。例如,从具有相关联的时间点的预设的温度曲线得出用于在炉子3中的燃烧控制的应达预设或用于在冷却段9中的水量控制的应达预设。将它们传递给相应的单元的对应的调节部。
27.如果在单元内未达到该值,下级工艺模型iiia、iiib可调整应达预设。同样,在此还可通过自学习算法自动优化工艺模型iiia、iiib。如果目标实际参数与上级工艺模型iia、iib的目标值预设v有偏差,在上级层ii中重新计算应达值,并且必要时进行调整。
28.图3示出了具有应达温度走向b、测得的以及预先计算的温度走向a的图。应达温度走向b从铸造设备1的末端开始,并且说明了直到卷取机11的走向。绘出了从铸造设备1的末端直到初轧机架4的实际值。在此,测得的温度高于应达温度。从这一点开始,上级工艺模型
ii预先计算在热轧带材机组中的不同部位处的温度。基于温度曲线可在不同的部位重新预设不同的应达值,以便修整温度偏差。在此,可使用不同的工艺模型、材料或微观结构模型和/或优化算法,以确定最佳调整策略。
29.表1:附图标记
30.