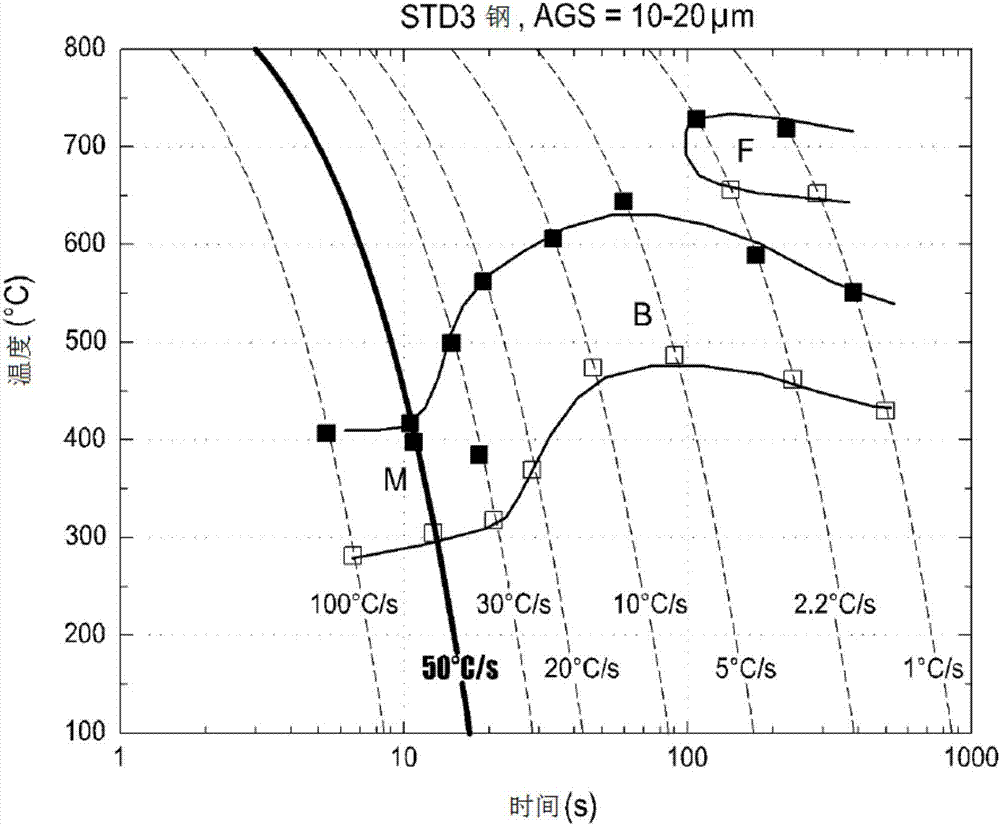
用于连续管应用的高性能材料及其生产方法通过引用对任何优先权申请的结合任何和所有的申请,其在随本申请递交的申请资料表中表明是被要求外国或本国优先权要求,在37CFR1.57规定下通过引用结合于此。相关申请本申请涉及申请人的共同未决申请,该未决申请题为“COILEDTUBEWITHVARYINGMECHANICALPROPERTIESFORSUPERIORPERFORMANCEANDMETHODSTOPRODUCETHESAMEBYACONTINUOUSHEATTREATMENT(具有优越性能的可变机械性能的连续管及通过连续热处理生产该连续管的方法)”,于2011年9月9日提出申请,序列号为13/229517,并在2012年7月26日公开,公开号为US2012/0186686A1,该未决申请通过引用整个地结合于此。
背景技术:近年来,连续管(coiledtubing)广泛运用于要求高压和延伸到达操作(extendedreachoperations)的应用中。结果,需要生产具有提高的拉伸性能的连续管,以经受:i)在悬挂或共用(pooling)长柱上的轴向负载,和ii)在操作过程中施加的升高的压力。连续管的标准生产将热轧条带用作原材料,其具有在轧制过程中通过微结构细化(microstructuralrefinement)而获得的机械性能。该细化通过采用不同的微合金添加剂(Ti、N、V)和合适地选择热轧处理条件而获得。其目的在于控制材料再结晶和晶粒生长,以获得超精细的微结构。该材料受限于固溶体合金元素的使用和沉淀硬化,因为细化是同时允许高强度和韧性的唯一机制。该原材料对每个供应者来说是指定的,并在热轧条带中可能要求不同的机械性能,以生产具有不同机械性能的连续管。随着性能的提高,生产成本进而原材料成本也增加。已知的是,在“长条带”的组装过程中使用的条带到条带焊接过程会使得连接区域劣化,其中该“长条带”将被ERW成型/焊接为连续管。此后,具有改进性能的连续管在条带焊接区域倾向于具有相对较低的性能。该劣化由这样的事实引起,即焊接过程破坏了在热轧过程中引入的细化,且没有简单的焊后热处理能够再生拉伸和韧性性能。通常,拉伸得以恢复,而韧性及其相关的疲劳寿命在该区域中劣化。当今的工业路线可以生产高强度的连续管,但只在提高的成本下,且条带焊接接头相对于管体具有较差的性能。用于生产连续管的一种选择是通过整体的热处理。该处理运用于已经形成为管的处于所谓的“未处理(green)”状态的材料上,因为其性能还需要通过热处理条件来定义。在这种情形下,影响最终产品性能的主要变量是钢化学成分和热处理条件。此后,通过合适地组合钢成分与焊接材料和热处理,可以生产在长度上具有均匀性能的连续管,而排除了条带到条带连接的薄弱环节,这样的条带到条带连接在高强度的现有连续管上是关键的。这个一般概念已经在以前描述,但是从未成功地应用于高强度连续管(屈服强度在从80到140ksi的范围中)的生产。其理由是,在(获得高生产率所需的)升高的线速度下,热处理通常导致需要复杂和延伸的设施。如果选择专用的化学成分和处理条件,可以简化该过程。选择与合理尺寸的工业热处理设施兼容的化学成分要求理解影响测量到的连续管性能的许多变量,例如:a)轴向机械性能;b)微结构的均匀性和性能;c)韧性;d)耐疲劳性;e)耐酸性,等等。
技术实现要素:下面描述设计用于生产热处理连续管的化学成分,其大部分在API5ST标准设定的连续管当前限定之外。(Max.C:0.16%,Max.Mn:1.2%(CT70-90)Max.Mn:1.65(CT100-110),Max.P:0.02%(CT70-90)Max.P:0.025(CT100-CT110),Max.S:0.005,Si.Max:0.5)。本发明的实施方式涉及钢连续管(coiledsteeltube)及其生产方法。在一些实施方式中,该管可以具有大于大约80ksi的屈服强度。该管的成分可以包括0.16-0.35重量%的碳、0.30-2.00重量%的锰、0.10-0.35重量%的硅、多至0.005重量%的硫、多至0.018重量%的磷,余量为铁和不可避免的杂质。该管还包括最终微结构,该最终微结构包括回火马氏体和贝氏体的混合物,其中连续管的最终微结构包括多于90体积%的回火马氏体,其中该微结构在管体、ERW线和条带端对端连接中是均质的。这里公开的是由多个焊接条带形成的钢连续管,其中该管可以包括基础金属区域、焊接连接及其热影响区,并可以具有大于大约80ksi的屈服强度,包括铁和0.17-0.35重量%的碳、0.30-2.00重量%的锰、0.10-0.30重量%的硅、0.010-0.040重量%的铝、多至0.010重量%的硫和多至0.015重量%的磷的成分,和最终微结构,该最终微结构包括回火马氏体和贝氏体的混合物,其中连续管的最终微结构在基础金属区域、焊接连接和热影响区中包括多于90体积%的回火马氏体,其中该最终微结构在所有基础金属区域、焊接连接和热影响区中是均质的,和其中该最终微结构在基础金属区域、焊接连接和热影响区中包括精细碳化物的均匀分布。在一些实施方式中,该成分还包括多至1.0重量%的铬、多至0.5重量%的钼、多至0.0030重量%的硼、多至0.030重量%的钛、多至0.50重量%的铜、多至0.50重量%的镍、多至0.1重量%的铌、多至0.15重量%的钒、多至0.0050重量%的氧,和多至0.05重量%的钙。在一些实施方式中,该成分包括:0.17到0.30重量%的碳、0.30到1.60重量%的锰、0.10到0.20重量%的硅、多至0.7重量%的铬、多至0.5重量%的钼、0.0005到0.0025重量%的硼、0.010到0.025重量%的钛、0.25到0.35重量%的铜、0.20到0.35重量%的镍、多至0.04重量%的铌、多至0.10重量%的钒、多至0.0015重量%的氧、多至0.03重量%的钙、多至0.003重量%的硫,和多至0.010重量%的磷。在一些实施方式中,该管可以具有125ksi的最小屈服强度。在一些实施方式中,该管可以具有140ksi的最小屈服强度。在一些实施方式中,该管可以具有在125ksi到140ksi之间的最小屈服强度。在一些实施方式中,该最终微结构在基础金属区域、焊接连接和热影响区中可以包括至少95体积%的回火马氏体。在一些实施方式中,该管在基础金属区域、焊接连接和热影响区中可以具有20μm以下的最终晶粒尺寸。在一些实施方式中,该管在基础金属区域、焊接连接和热影响区中可以具有15μm以下的最终晶粒尺寸。在一些实施方式中,所述焊接连接可以包括斜焊(biasweld)。在一些实施方式中,在斜焊处的疲劳寿命可以是基础金属区域的至少大约80%。在一些实施方式中,焊接连接包括其热影响区的百分比硬度可以是基础金属硬度的110%或更小。这里还公开了形成钢连续管的方法,其包括:提供条带,该条带具有包括铁和0.17-0.35重量%的碳、0.30-2.00重量%的锰、0.10-0.30重量%的硅、0.010-0.040重量%的铝、多至0.010重量%的硫,和多至0.015重量%的磷的成分;和将所述条带焊接在一起,由焊接条带形成管,其中该管包括基础金属区域、连接焊接和它们的热影响区;在900-1000℃之间奥氏体化该管;淬火该管以形成马氏体和贝氏体的最终淬火态微结构(asquenchedmicrostructure),其中该淬火态微结构在基础金属区域、焊接连接和热影响区中包括至少90%的马氏体,和在550-720℃之间对该淬火的管进行回火,其中对淬火的管进行回火产生大于大约80ksi的屈服强度,其中在所有基础金属区域、焊接连接和热影响区中的微结构是均质的,和其中该微结构在基础金属区域、焊接连接和热影响区中包括精细碳化物的均匀分布。在一些实施方式中,焊接所述条带可以包括斜焊。在一些实施方式中,形成该管可以包括形成线连接(linejoint)。在一些实施方式中,该方法还可以包括在卷轴上卷绕回火的管。在一些实施方式中,奥氏体化可以在基础金属区域、焊接连接和热影响区中形成小于20μm的晶粒尺寸。在一些实施方式中,该成分还可以包括:多至1.0重量%的铬、多至0.5重量%的钼、多至0.0030重量%的硼、多至0.030重量%的钛、多至0.50重量%的铜、多至0.50重量%的镍、多至0.1重量%的铌、多至0.15重量%的钒、多至0.0050重量%的氧,和多至0.05重量%的钙。在一些实施方式中,该成分可以包括:0.17到0.30重量%的碳、0.30到1.60重量%的锰、0.10到0.20重量%的硅、多至0.7重量%的铬、多至0.5重量%的钼、0.0005到0.0025重量%的硼、0.010到0.025重量%的钛、0.25到0.35重量%的铜、0.20到0.35重量%的镍、多至0.04重量%的铌、多至0.10重量%的钒、多至0.00015重量%的氧、多至0.03重量%的钙、多至0.003重量%的硫,和多至0.010重量%的磷。在一些实施方式中,该回火的管可以具有大于或等于125ksi的屈服强度。在一些实施方式中,该回火的管可以具有140ksi的最小屈服强度。在一些实施方式中,该回火的管可以具有在125ksi到140ksi之间的最小屈服强度。附图说明图1A-B示例了对应于STD2(A)和STD3(B)钢的CCT图。图2A-B示例了对应于BTi2(A)和CrMoBTi3(B)钢的CCT图。图3示例了在内管表面的冷却速率,其是壁厚(WT)的函数,用于在喷水下从外部淬火的连续管。图4示例了BTi2钢的拉伸性能,其是最大回火温度(Tmax)的函数。峰状回火循环用于这些仿真。(右侧)720℃处,作为保持时间的函数的相同钢的拉伸性能(等温回火循环)。图5A-B示例了在焊缝退火(seamannealing)(PWHT)后,出现在靠近ERW线的中心偏析带处的未回火的马氏体。图5A-B对应于常规的连续管等级90(Grade90)。图6A-B示例了在等级110连续管的疲劳测试过程中产生的在中心偏析带处的局部损坏。图7A-B示例了等级100连续管在具有高的内部压力(9500psi)下的疲劳测试过程中产生的在中心偏析带处的局部损坏。图8A-B示例了基础金属微结构,其对应于标准连续管(A)和通过本发明的实施方式制造的连续管(B)。在两种情形下,连续管都具有对应于等级110的拉伸性能(从110Ksi到120Ksi的屈服强度)。图9A-B示例了ERW线微结构,其对应于标准连续管(A)和通过本发明的实施方式制造的连续管(B)。在两种情形下,连续管拉伸性能都对应于等级110(从110Ksi到120Ksi的屈服强度)。图10A-B示例了对应于ERW的HAZ的微结构,用于标准连续管(A)和通过本发明的实施方式制造的连续管(B)。在两种情形下,连续管拉伸性能都对应于等级110(从110Ksi到120Ksi的屈服强度)。图11A-B示例了对应于斜焊的HAZ的微结构,用于标准连续管(A)和通过本发明的实施方式制造的连续管(B)。在两种情形下,连续管拉伸性能都对应于等级110(从110Ksi到120Ksi的屈服强度)。图12示例了使用过程中在斜焊的融合区中形成的裂纹(从内管面生长)。该裂纹处于大的上贝氏体条的方向上。图13示例了通过现有过程和根据本发明的实施方式的过程获得的典型斜焊上的硬度的变化(基础金属硬度=100%)。融合区(FZ,fusionzone)近似地位于在距焊接中心≈+/-5mm之间的区域中。图14A-B示例了微结构,其对应于在斜焊和ERW线之间的交叉处,用于标准连续管(A)和通过本发明的实施方式制造的连续管(B)。在两种情形下,连续管拉伸性能都对应于等级110(从110Ksi到120Ksi的屈服强度)。图15示例了疲劳测试机的示意图。图16示例了为BW样品测量的疲劳寿命,相对于对应于BM样品的那些。结果是在不同测试条件和连续管等级下的平均值(对于现有管是80、90和110,对于根据本发明生产的连续管是80、90、110、125和140)。图17示例了根据本发明的化学成分和处理条件的实施方式生产的连续管疲劳寿命的改进。该改进取决于与类似条件下相同等级的现有连续管测量得到的疲劳寿命的比较。结果在不同测试条件下对每个等级进行平均。在非标准的等级125和140的情形下,疲劳寿命比较是针对等级110中的STD3进行的。图18A-B示例了在根据NACETM0177(90%SMYS,方案A,1barH2S)测试材料等级80之后的C环样品。A:现有过程;B:本发明公开的实施方式。具体实施方式在钢厂生产出作为热轧条带的连续管原材料。控制的轧制用于通过微结构细化保证高强度和良好的韧性。条带纵向切割到用于管的生产的宽度,然后通过连接过程(例如等离子弧焊或搅拌摩擦焊)端对端地接合,以形成更长的条带。此后,采用ERW过程形成管。最终的产品性能根据下述测量:a)轴向机械性能,b)微结构和性能的均匀性,c)韧性,d)耐疲劳性,e)耐酸性,等等。采用现有的处理路线,连续管机械性能通过热轧条带性能和在焊接操作和管形成过程中引入的改变的组合而获得。这样获得的性能在连续管性能如上所列那样测量时受到限制。理由是用于连接条带的焊接过程这样改变了细化的轧制的微结构,即使采用了焊后热处理,最终的性能仍然受损。减少的疲劳寿命和差的耐酸性能与微结构中的不均匀性和焊接上脆弱的组分相关。已经提议,新的路线至少应包括整体热处理。该路线已经被概括地描述,但是从未具体化。本发明描述了化学成分和原材料特性,其与合适的焊接过程以及热处理条件结合,将产生经淬火和回火的产品,该产品在管体和条带连接焊接中都具有高的性能。该材料设计用于连续管,这样的选择不仅是因为相对成本,而且优选地是为了最大化应用于连续管操作的特殊条件下的疲劳寿命(在同时发生轴向负载和内部压力下弯曲的低周疲劳)。本发明涉及高强度连续管(最小屈服强度从80ksi到140ksi),其与通过API5ST限定的标准产品相比具有增加的低周疲劳寿命。此外,抗硫化物应力开裂(SSC,SulfideStressCracking)性也在本发明中提高。性能的这种出色组合通过钢化学成分和处理条件的合适选择而获得。工业过程不同于整体热处理(FBHT,FullBodyHeatTreatment)应用中的标准路线,该过程在美国申请US2012/0186686A1中公开。该FBHT是在连续管通过ERW(ElectricalResistanceWelding,电阻焊接)形成之后进行的,并包括至少一个周期的奥氏体化、淬火和回火。上述公开更特别地涉及钢化学成分和处理参数,以生产具有上述性能的淬火和回火的连续管。尽管通过对具有给定成分的基础材料进行热处理产生某些机械性能是一般知识的一部分,但是用于连续管的特殊应用采用具有特殊化学成分的原材料,以最小化特殊变量的有害作用,例如在本发明的特殊性能上的偏析模式(segregationpattern)。对于连续管最重要的一个性能是提高的耐低周疲劳性。这是因为在标准的现场操作过程中,连续管频繁地卷起和展开,引入周期的塑性变形,这最终将产生破坏。在低周疲劳过程中,在较软的材料区域中,变形偏向于位于微观尺度处。当脆化组分(brittleconstituents)出现在这些应变集中区域处或其附近时,裂纹可以容易地成核并扩展。因此,疲劳寿命的减少与不均匀的微结构(具有较软的区域,其中局部变形)和脆化组分(其成核和/或扩展裂纹)相关。所有这些微结构特征出现在焊接的热影响区(HAZ,HeatAffectedZone)。具有一些类型的管体微结构,其也具有上述特征。这是因为它们包括硬的和软的组分的混合物,例如铁素体、珠光体和贝氏体。在这种情形下,应变局限于较软的铁素体中,靠近贝氏体的边界,其中裂纹成核并扩展。高强度的连续管现在具有这类微结构。为了避免在低周疲劳过程中应变局部化,微结构必须不仅在整个管体和连接上都均匀,而且是在微观尺度下如此。对于低碳钢,包括回火的马氏体的微结构是理想的,其基本上是铁素体基质,具有均匀和精细的碳化物分布。其后,本发明描述的化学成分选择和处理条件的目的在于通过FBHT实现均匀的微结构(在管体、斜焊和ERW线中),其包括至少90%的回火马氏体,优选地多于95%的回火马氏体。此外,回火马氏体更适合于产生比标准连续管微结构(包括铁素体、珠光体和贝氏体)高的超高强度等级,为此,需要十分昂贵的合金添加剂,以达到高于大约125Ksi的屈服强度。当与含有贝氏体的结构比较时,回火马氏体的其他重要好处在于其改进的抗SSC性。钢化学成分已经定义为最适合于采用FBHT生产热处理连续管,并可以描述为碳(重量%C),锰(重量%Mn),硅(重量%Si),铬(重量%Cr),钼(重量%Mo)和微合金元素,例如硼(重量%B),钛(重量%Ti),铝(重量%Al),铌(重量%Nb)和钒(重量%V)的含量。另外,上限可能在于不可避免的杂质上,例如硫(重量%S),磷(重量%P)和氧(重量%O)。为了生产包括回火马氏体的最终结构,本发明的钢化学成分主要不同于连续管的现有技术,因为其具有较高的碳含量(例如参见API5ST,其中连续管允许的最大碳含量是0.16%),这允许通过包括至少一个周期的奥氏体化、淬火和回火的FBHT来获得想要的微结构。这里使用的术语“几乎”、“大约”和“基本上”表示接近所述量的量,但仍然执行想要的功能或实现想要的结果。例如,术语“几乎”、“大约”和“基本上”可以指在所述量的小于10%内、小于5%内、小于1%内、小于0.1%内和小于0.01%内。碳是这样的元素,通过在热处理过程中提高可淬硬性和促进碳化物沉淀,其不昂贵的添加增加了钢的强度。如果碳减少到0.17%以下,可淬硬性不能够保证,在热处理过程中可能形成大的贝氏体片段。贝氏体的外形使其难以达到具有想要的疲劳寿命和抗SSC性的80ksi以上的屈服强度。当前的连续管路线不适于热处理,因为API5ST所允许的最大碳含量是0.16%。现有的连续管的微结构呈现大的贝氏体片段,其在更高强度等级削弱了韧性、疲劳寿命和抗SSC性,也即连续管具有在110Ksi以上的最小屈服强度。另一方面,具有大于0.35%的碳的钢将具有差的可焊性,在焊接和焊接后热处理操作中容易出现脆化组分和裂纹。此外,较高的碳含量可能导致淬火后大量保留的奥氏体,其随着回火而转变为脆化组分。这些脆化组分削弱了疲劳寿命和抗SSC性。因此,钢成分的C含量在从大约0.17%到大约0.35%的范围内变化,优选地是从大约0.17%到大约0.30%。锰的添加提高了可淬硬性和强度。Mn也有助于在制钢过程中去氧和硫控制。如果Mn含量小于大约0.30%,其可能难以获得想要的强度水平。然而,当Mn含量增加时,可以形成大的偏析模式。在热处理过程中,Mn偏析区域将倾向于形成脆化组分,这将削弱韧性并减少疲劳寿命。此外,这些偏析区域增加了材料对硫化物应力开裂(SSC)的敏感性。相应地,在采用改进的抗SSC性的应用中,钢成分的Mn含量在从0.30%到2.0%的范围内变化,优选地从0.30%到1.60%,更优选地从0.30%到0.80%。硅是这样的元素,其的添加在制钢过程中具有脱氧作用,还增加了钢的强度。在一些实施方式中,如果Si超出大约0.30%,韧性可能下降。此外,可能形成大的偏析模式。因此,钢成分的Si含量在大约0.10%到0.30%之间的范围内变化,优选地在大约0.10%到大约0.20%的范围内。铬的添加增加了钢的可淬硬性和回火稳定性。Cr可以用于部分地替换钢成分中的Mn,以实现高的强度而不产生大的偏析模式,该偏析模式将削弱疲劳寿命和抗SSC性。然而,Cr是昂贵的添加剂,且因为其对热成形负载的作用,使得连续管更难以生产。因此,在一些实施方式中,Cr限制到大约1.0%,优选地到大约0.7%。钼是这样的元素,其的添加对于增加钢的强度是有效的,还有助于在回火过程中延迟软化。对回火稳定性允许在减少Mn含量下生产高强度的钢,增加了疲劳寿命和抗SSC性。Mo添加剂还可以减小磷到晶粒边界的偏析,改进了抗晶粒间破裂性。然而,该铁合金是昂贵的,使其需要减小钢成分内的最大Mo含量。因此,在某些实施方式中,最大的Mo是大约0.5%。硼是这样的元素,其的添加对于改进钢的可淬硬性非常有效。例如,通过抑制铁素体在淬火过程中形成,B可以提高可淬硬性。在一些实施方式中,B用于实现钢中良好的可淬硬性(也即作为包括至少90%马氏体的淬火结构),通过Mn含量的减少提高疲劳寿命和抗SSC性。如果B含量小于大约0.0005重量%,在这些实施方式中可能难以获得钢想要的可淬硬性。然而,如果B含量过高,粗的碳化硼可能形成在晶粒边界处,负面地影响韧性。相应地,在一个实施方式中,在该成分中,B的含量低于大约0.0030%,在另一个实施方式中,B的含量从大约0.0005%到0.0025%。钛是这样的元素,通过将氮杂质固定为氮化钛(TiN)并抑制氮化硼的形成,其的添加对于提高钢中B的作用是有效的。如果Ti含量太低,在一些实施方式中可能难以获得硼对于钢的可淬硬性的想要的作用。另一方面,如果Ti含量高于0.03重量%,粗的氮化钛和碳化物(TiN和TiC)可能形成,负面地影响延展性和韧性。相应地,在某些实施方式中,Ti的含量可以限制到大约0.030%。在其他实施方式中,Ti的含量可以在从大约0.010%到大约0.025%的范围内。考虑到低机械性能的连续管的生产受益于低回火稳定性,B和Ti添加剂改进了可淬硬性而不增加回火稳定性。其后,其允许80ksi等级的生产而在回火过程中没有显著大的均热时间,从而提高了生产率。由于连续管生产在热处理线中的一个限制是线的长度,以在回火过程中对材料进行充分的均热,B和Ti的使用特别地涉及低屈服强度连续管的生产。铜在钢成分的某些实施方式中不是必需的元素。然而,在一些连续管应用中,Cu可能需要用于改进耐大气腐蚀性。这样,在某些实施方式中,钢成分的Cu含量可以限制于或小于大约0.50%。在其他实施方式中,Cu含量在从大约0.25%到大约0.35%的范围内。镍是这样的元素,其的添加增加了钢的强度和韧性。如果Cu添加到钢成分中,Ni可以用于避免已知为热脆性(hotshortness)的热轧缺陷。然而,Ni非常昂贵,在某些实施方式中,钢成分的Ni含量限制于或小于或等于大约0.50%。在其他实施方式中,Ni的含量可以在从大约0.20%到大约0.35%的范围内。铌是这样的元素,其到钢成分的添加可以在对奥氏体区域再加热的过程中细化钢的奥氏体晶粒尺寸。Nb还可以在回火过程中沉淀,通过颗粒弥散硬化而增加钢的强度。在一个实施方式中,钢成分的Nb含量可以在大约0%到大约0.10%之间的范围内变化,有效地在大约0%到大约0.04%的范围内。钒是这样的元素,通过在回火过程中碳化物的沉淀,其的添加可以用于提高钢的强度。然而如果钢成分的V含量大于大约0.15%,可能形成大体积的碳化钒晶粒,伴随着钢韧性的减小。由此,在某些实施方式中,钢的V含量限制于大约0.15%,优选地大约0.10%。铝是这样的元素,其到钢成分的添加在制钢过程中具有脱氧作用,并进一步细化钢的晶粒尺寸。在一个实施方式中,如果钢成分的Al含量小于大约0.010%,钢可能易受氧化影响,展现出高水平的夹杂物。在其他实施方式中,如果钢成分的Al含量大于大约0.040%,可能形成粗的沉淀物,这将削弱钢的韧性。因此,钢成分的Al含量可以在大约0.010%到大约0.040%的范围内变化。硫是这样的元素,其引起钢的韧性和可加工性下降。相应地,在一些实施方式中,钢成分的S含量限制于最大大约0.010%,优选地大约0.003%。磷是这样的元素,其引起钢韧性的下降。相应地,钢成分的P含量限制于最大大约0.015%,优选地大约0.010%。氧可以是在钢成分内的杂质,其主要以氧化物的形式出现。在钢成分的实施方式中,当O含量增加时,钢的冲击性能被削弱。相应地,在钢成分的某些实施方式中,想要相对低的O含量,小于或等于大约0.0050重量%,优选地小于或等于大约0.0015重量%。钙是这样的元素,其到钢成分的添加通过改变硫化夹杂物的形状而改进韧性。在一个实施方式中,钢成分可以包括Ca/S>1.5的Ca对S的最小含量比。在钢成分的其他实施方式中,过多的Ca是不必要的,钢成分可以包括最大大约0.05%的Ca含量,优选地大约0.03%。不可避免的杂质,包括但是不限于N、Pb、Sn、As、Sb、Bi等,其含量优选地保持为尽可能地低。然而,假如这些杂质保持在选择的水平之下,根据本发明的钢成分的实施方式形成的钢的性能(例如强度、韧性)可以基本上不削弱。在一个实施方式中,钢成分的N含量可以小于大约0.010%,优选地小于或等于0.008%。在另一个实施方式中,钢成分的Pb含量可以小于或等于大约0.005%。在其他实施方式中,钢成分的Sn含量可以小于或等于大约0.02%。在其他实施方式中,钢成分的As含量可以小于或等于大约0.012%。在另一个实施方式中,钢成分的Sb含量可以小于或等于大约0.008%。在其他实施方式中,钢成分的Bi含量可以小于而等于大约0.003%。本发明的特定钢化学成分的选择将根据最终产品规格和工业设施约束(例如在感应热处理线中,难以在回火过程中获得大的均热时间)。可能时,Mn的添加将减少,因为其通过形成大的偏析模式而削弱疲劳寿命和抗SSC性。Cr和较小含量的Mo将用于取代Mn,整体热处理将保持为尽可能的简单。这两种元素都增加了碳化物稳定性和耐软化性,其将导致回火过程中大的均热时间。其后,这些元素优选地用于更高的强度等级(例如等级110和更高),其中想要回火稳定性,并在较低的等级(等级80)中避免,其中需要长的和不切实际的工业热处理线。在较低等级(等级80)的情形下,优选地是B和Ti微合金添加剂与合适的C含量组合。这些元素允许获得良好的可淬硬性而不使用高的Mn添加剂。而且,B和Ti不增加回火稳定性。其后,简单和短的回火处理可以用于实现想要的强度水平。对应于本发明的工业处理方法在下面的段落中描述,其集中于整体热处理(FBHT)条件。用于连续管的原材料在钢厂生产为具有可以从大约0.08英寸到大约0.30英寸变化的壁厚的热轧条带。控制的轧制可以由钢供应者用于细化轧态微结构(asrolledmicrostructure)。然而,轧态条带的重要的微结构细化是不需要的,因为在本发明中,微结构和机械性能主要通过最终的FBHT限定。在热轧处理中的该灵活性有助于减少原材料成本,允许采用钢化学成分,所述钢化学成分在可以使用复杂的热轧过程时不能使用(通常,控制的轧制可以仅用于低碳微合金钢中)。钢条带纵向切割为用于管生产的宽度。其后,条带通过焊接过程端对端地连接(例如等离子弧焊或搅拌摩擦焊),以形成更长的条带,允许获得管的长度。这些焊接的条带例如通过ERW过程形成为管。典型的连续管外径在1英寸和5英寸之间。管长度为大约15000英尺,但是长度可以在大约10000英尺到大约40000英尺之间。在形成管后,采用整体热处理(FBHT)。热处理的目的在于生产均匀的最终微结构,其包括至少90%的回火马氏体,其余为贝氏体。该微结构,其具有均匀的碳化物分布和在20μm以下、优选地15μm以下的晶粒尺寸,保证了强度、延展性、韧性和低周疲劳寿命的良好组合。而且,如前所述,通过合适地选择钢化学成分,与现有结构相比,其中包括铁素体、珠光体和大体积百分率的上贝氏体,该类微结构适合于改进抗硫化物应力开裂(SSC)性。FBHT包括跟随有回火处理(T)的至少一个奥氏体化和淬火循环(Q)。奥氏体化在900℃和1000℃之间的温度下进行。在该阶段中,在平衡温度Ae3以上的总的持续时间应当选择为保证铁碳化物完全分解而没有多余的奥氏体晶粒生长。目标晶粒尺寸在20μm以下,优选地在15μm以下。必须进行淬火,控制最小冷却速率,以获得最终的淬火态微结构,其在整个管中包括至少90%的马氏体。回火在550℃和720℃之间的温度下进行。在720℃之上的热处理可以导致部分马氏体转变为高碳奥氏体。该组分必须避免,因为其倾向于转变为脆化组分,这可能削弱韧性和疲劳寿命。另一方面,如果回火在550℃以下进行,位错的淬火态结构的恢复过程没有完成。其后,韧性可能再次大大地减小。回火循环必须选择在上述温度范围内,以获得想要的机械性能。最小的屈服强度可以从80ksi变化为140ksi。在温度下的合适的持续时间必须选择为保证在基础管和焊接区域中(ERW线和条带到条带连接)均匀的碳化物分布。在一些情形下,为了提高强度和韧性的组合,可能需要进行多于一次的奥氏体化、淬火和回火循环。在FBHT之后,管可以经受定尺寸过程,以保证指定的尺寸容差、应力释放,并卷绕成卷。例子:例子A:改进可淬硬性的化学成分选择如前所述,本发明的微结构包括至少90%的回火马氏体,其中精细碳化物均匀分布,其余为贝氏体。该微结构允许生产连续管,该连续管具有高强度、延伸的低周疲劳寿命和改进的抗SSC性的想要的组合。回火马氏体通过至少一个淬火和回火热处理获得,该热处理在管通过ERW形成之后进行。如果需要额外的细化以改进抗SSC性,热处理可以重复两次或更多次。这是因为随后的奥氏体化和淬火循环减小的不仅仅是先前的奥氏体晶粒尺寸,还有马氏体块和马氏体束的尺寸。为获得具有良好可淬硬性的目标微结构,至少90%的马氏体必须在淬火过程的末尾形成。充分的化学成分选择对于获得这样的马氏体的体积百分率是至关重要的。合适的钢成分的选择基于试验结果,所述试验在热机械模拟器3500中进行。随后进行工业测试,以确认实验室发现。在实验室中分析的一些钢化学成分列在表A1中。对于所有这些化学成分,都在中进行了膨胀测试(dilatometrictests),以构建连续冷却转换(CCT,ContinuousCoolingTransformation)图。这些CCT图,结合对从模拟器获得的样品的金相分析,用于确定最小冷却速率,以获得多于90%的马氏体。该临界冷却速率,其主要依赖于钢化学成分,将称为CR90。钢CMnSiCrMoNiCu其他STD10.130.800.350.52-0.150.28TiSTD20.140.800.330.550.100.170.27Nb-TiSTD30.140.800.340.570.320.220.28Nb-TiCMn10.172.000.20-----CMn20.251.600.20-----BTi10.171.600.20----B-TiBTi20.251.300.20----B-TiCrMo10.171.000.251.000.50---CrMo20.250.600.201.000.50---CrMoBTi10.170.600.201.000.50--B-TiCrMoBTi20.240.400.151.000.25--B-TiCrMoBTi30.240.400.151.000.50--B-TiCrMoBTi40.260.600.150.500.25B-Ti表A1:实验研究的钢的化学成分。元素含量表示为重量百分比(wt%)。获得的CCT图的例子呈现在图1-2中。在所有情形下,奥氏体化在900-950℃下进行,以获得10-20μm的精细奥氏体晶粒尺寸(AGS)。STD1、STD2和STD3钢具有在API5ST规格内的化学成分,但是在本发明的范围之外,因为它们具有低的碳添加(表A1)。在STD1和STD2的情形下,临界冷却CR90大于100℃/秒,对于STD3为大约50℃/秒。图1A-B表示对应于STD2(A)和STD3(B)钢的CCT图。粗体表示产生最终微结构的临界冷却条件,该微结构包括大约90%的马氏体,其余为贝氏体。图2A-B表示对应于BTi2和CrMoBTi3钢的CCT图。粗体表示产生最终微结构的临界冷却条件,该微结构包括大约90%的马氏体,其余为贝氏体。第一个是与B-Ti微合金的C-Mn钢(参见表A1)。CrMoBTi2是具有Cr和Mo添加的中碳钢,也与B-Ti微合金。测量的临界冷却速率(对应于CCT图中粗体所示的冷却曲线)对于BTi2和CrMoBTi3分别是25℃/s和15℃/s。在图3中示出的是在工业淬火喷头设备中处理的管的平均冷却速率(喷射水,从外表面冷却管)。值示出为管壁厚(WT,WallThickness)的函数。图中阴影区域对应于连续管应用中典型的壁厚范围。清楚的是,当选择适用于获得大于90%回火马氏体的钢化学成分时,合金的临界冷却速率应等于或小于30℃/s。另外,在上述设备中对更厚的管(WT=0.3英寸)淬火的过程中,将形成多于10%的贝氏体。STD1,STD2和STD3具有在30℃/s以上的临界冷却速率,其后这些钢不适合于本发明。另一方面,可淬硬性在BTi2和CrMoBTi3钢中是足够的。可淬硬性的改进原因在于增加的碳含量和B-Ti添加。表A2中示出了对表A1的钢测量得到的临界冷却速率。STD1,STD2和STD3是当前用于连续管等级80、90和110的化学成分,并满足API5ST。然而,甚至更多的合金STD3具有临界冷却速率,以保证在具有相关范围内的WT的管中多于90%的回火马氏体。清楚的是,标准材料不足以产生本发明的目标微结构,且可淬硬性必须提高。在低合金钢中,影响可淬硬性的最重要的元素是碳。其后,C提高到API5ST规定的最大值(0.16重量%)之上,使得临界冷却速率不高于30℃/s。在本发明中,碳添加在从0.17%到0.35%的范围中(选择最大水平以保证良好的可焊性和韧性)。如同刚刚提到的,该化学成分的其余部分必须调节到具有等于或小于30℃/s的CR90值。表A2:获得高于多于90%的马氏体的临界冷却速率(CR90),对所分析的钢测量。值由膨胀测试和金相分析而确定。下面用于选择足够的钢化学成分的原则从对表A2中的实验结果的分析中获得。C-Mn钢:可淬硬性主要取决于碳和锰的添加剂。当C处于下限时,大约2%的Mn可以用于获得想要的可淬硬性(CMn1钢)。然而,Mn是产生强的偏析模式的元素,而偏析模式将减少疲劳寿命。其后,Mn添加剂在较高碳的配方中下降。例如,当碳含量为大约0.25%时,1.6%的Mn足以获得可淬硬性(CMn2钢)。B-Ti钢:这些合金是与硼和钛微合金的普通碳钢。由于增加了与硼作用相关的可淬硬性,Mn可以进一步减少。对于在下限中的碳,大约1.6%的Mn可以用于获得可淬硬性。当碳含量为大约0.25%时,1.3%的Mn足以获得可淬硬性(BTi2钢)。Cr-Mo钢:这些钢具有Cr和Mo添加剂,它们对于增加回火稳定性是有用的,这使得它们适合于超高强度等级。此外,Cr和Mo是改进可淬硬性的元素;所以Mn添加剂可以进一步减少。然而,Cr和Mo是昂贵的添加剂,其减小了钢的热加工性,它们的最大含量分别限制到1%和0.5%。在一个例子中,其中碳处于下限,大约1%的Mn可以用于实现CR90(CrMo1)。如果钢也是与B-Ti的微合金,可以实现Mn进一步减少到0.6%(CrMoBTi1)。例子B:用于不同连续管等级的化学成分选择为分析表A1呈现的钢的回火行为,以进行了工业热处理的仿真。这些仿真包括在900-950℃的奥氏体化,以30℃/秒的淬火和回火。在STD1、STD2和STD3钢的特殊情形下,采用了更高的冷却速率,以在淬火过程中获得至少90%的马氏体。对于STD1和STD2,采用大约150℃/s的淬火速率,而对于STD3,冷却是在50℃/s。当提供外部水冷却时,这些更高的冷却速率可以在小样品中在处获得。在淬火之后,样品采用两类循环回火:-峰状循环:以50℃/s加热到最大温度(Tmax),其在从550℃到720℃的范围中。以大约1.5℃/s冷却到室温。这些循环旨在仿真在感应炉中实际的回火条件,其特征在于高的加热速率,在最大温度处没有均热时间,以及空气冷却。-等温循环:以50℃/s加热到710℃/s,在该温度下均热从1分钟到1小时的时间,并以大约1.5℃/s冷却。该循环用于仿真工业线中的回火,其中具有多个均热电感器或隧道炉。在所有的情形下,回火温度在从550℃/s到720℃/s的范围中。高于720℃/s的温度需要避免,因为没有想要的再奥氏体化发生。另一方面,如果回火在550℃/s以下进行,位错(dislocated)结构的恢复不完全,材料出现脆化组分,这将削弱疲劳寿命。峰状回火循环优选用于减少线的长度并提高生产率。其后,获得具有特定钢化学成分的给定等级的可行性主要通过回火曲线确定,该回火曲线采用该类循环获得。如果在720℃/s下进行峰状回火之后,强度仍然对于该等级过高,可以在最大温度下进行均热。然而,随着均热时间增加,可能需要更大、更昂贵和更低生产率的工业线。在图4中(左边图)呈现了对BTi2钢测量的回火曲线。拉伸性能示出为最大回火温度的函数。峰状热循环用于仿真中。从图中可以看到,等级90到125可以通过从大约710℃到575℃地改变最大峰值温度而分别获得。不将回火温度减小到550℃以下的话,该化学成分不可能达到140Ksi的屈服强度。关于较低的等级,710℃下3分钟的均热可以用于获得等级80(图4右侧图)。基从仿真获得的结果,构建出表B1。对于每种分析的钢,该表示出生产不同等级的可行性,其最小屈服强度的范围从80Ksi到140Ksi。例如,在BTi2的情形下,采用峰状回火循环达到等级90到125是可行的。但是720℃下2分钟的均热可以用于等级80的情形下,这是在相应的单元标记“均热”的原因。表B1:采用分析的钢化学成分工业生产等级80到140的可行性。当“均热”出现在单元中时,这意味着720℃下多于1分钟的均热可以用于达到该等级。从获得的结果可以清楚,为了获得较高的等级,可以采用增加的碳和Cr-Mo添加剂。特别地,由于低的碳含量,等级140不能用标准化学成分实现,如在API5ST中所述那样。另一方面,为达到等级80,具有低碳的贫化学成分(leanchemistry),没有Cr或Mo添加剂是最佳的选择。在这种情形下,B-Ti微合金添加剂可以用于保证好的可淬硬性(例如,像BTi1的化学成分是好的替代选择)。重点要指出的是,为了用标准钢(STD1、STD2、STD3)产生马氏体结构,在实验室中需要采用比在工厂中可实现的更高的淬火速率。其后,如果我们将冷却速率限制到该工业上可获得的冷却速率,这些连续管等级都不能用现有的钢采用FBHT处理路线获得。例子C:减少固化过程中偏析负面作用的化学成分选择在钢固化过程中,合金元素倾向于在液体中保持稀释,因为其相比于固体(δ铁素体或奥氏体)具有更高的溶解度。随着固化,富集溶质的区域形成两类非均匀的化学成分模式:微观偏析和宏观偏析。微观偏析由在枝晶间空间中富集溶质的液体凝固而造成。但是其不构成主要问题,因为微观偏析的作用可以在随后的热加工过程中去除。另一方面,宏观偏析是化学成分在较大规模的铸造部分中的非均匀性。这不能够通过在高温下和/或热加工中均热而完全消除。在本发明所关注的情况中,其是连续的厚板铸造,这会产生中线偏析带。显著的中心偏析带必须避免,因为:-作为未回火马氏体的脆化组分可能出现在该区域中,这是作为焊接操作的结果(斜焊和ERW,例如参见图5A-B)。这些不想要的组分在随后的整体热处理中去除。然而,通过在焊接和热处理操作之间弯曲,管可能塑性变形,在工业生产过程中产生破坏。-在FBHT之后,中心偏析带的残余部分是富集替代溶质(如Mn、Si、Mo)的区域,其具有比材料其余部分更高的粗碳化物密度。该区域在低周疲劳过程中易于使裂纹成核,如在图6-7中观察到的那样。此外,显著的偏析带与差的抗SSC性相关。尽管不可能去除宏观偏析,其对于韧性、疲劳寿命和抗SSC性的负面作用可以通过合适选择钢化学成分而减小。基于对对应于大范围的钢化学成分的样品的EDX测量,在中心偏析带中富集因子对不同合金元素进行了估计。结果在表C1中示出。富集因子(EF,enrichmentfactor)是在中心带处每种元素含量和基体中对应于平均值的含量之间的比率。这些因子主要依赖于液体和固体之间的热力学分配系数,和在固化过程中的扩散率。元素EFMn1.6Si3.2Cr1.2Mo2.1Ni1.3Cu3.4表C1:在中心偏析带处的富集因子(EF),对应于不同的替代合金元素。表C1清楚地表示存在一些元素,其具有强的趋势会在固化过程中偏析,如Si和Cu。另一方面,Cr和Ni具有低的富集因子。Ni是昂贵的添加剂,但是当需要在不产生强的偏析模式下需要获得可淬硬性和/或回火稳定性时,可以采用Cr。富集因子给出了关于含量增加的信息,该含量可以为在中心偏析带处的每个元素所期待。然而,关于在焊接或热处理过程中形成脆化组分的材料趋势,不是所有这些元素都具有相同的作用。可以观察到,可淬硬性提高得越高,在处理过程中形成脆化组分的趋势越强。重要的是,具有高扩散系数的元素,例如碳和硼,会在固化过程中偏析,但是在热轧过程中均质化。其后,它们不会有助于在偏析带处形成脆化组分。从对CCT图(例子A)的分析可得出,锰产生最多的可淬硬性增长。这要除去碳和硼,它们在热轧之后不呈现大的偏析模式。另一方面,Si和Cu,其具有偏析的强烈趋势,对可淬硬性不起主要作用。由于其高的富集因子和对可淬硬性的大的作用,当试图减少宏观偏析的负面作用时,如同减少低周疲劳寿命那样,Mn添加剂必须尽可能地减少。高Mn含量普通地添加到钢成分中,因为其对可淬硬性的作用。在本发明中,可淬硬性主要通过较高的碳添加剂实现,所以Mn的含量通常可以减小。采用硼和/或铬添加剂可实现锰的进一步减少。例子可以在表C2中看到,该表表示用于从CCT图中获得的不同的钢成分的临界冷却速率(CR90)(数据从前面例子A中取得)。为了在大约0.25%的碳含量下实现钢中的可淬硬性,当添加硼时,Mn可以从1.6%减少到1.3%,且如果附加地使用Cr-Mo,可进一步减少到0.4%。表2:获得大于90%的马氏体的临界冷却速率(CR90),为所分析的钢测量。值由膨胀测试和金相分析而确定。例子D:微结构的均质化如前所述,连续管的疲劳寿命强烈地依赖于作为微结构异质性的微观特征。软、硬微组分的组合倾向于产生塑性应变局部化,其是裂纹成核和扩展的驱动力。在本部分比较了通过标准生产方法获得的连续管微结构,该方法应用于在API5ST内的化学成分,和在本发明公开的范围内对应于化学成分和处理条件的那些。基准材料所使用的是标准连续管等级110(从110Ksi到120Ksi的屈服强度),其具有表A1中名为STD2的化学成分,这是在API5ST规格内的。该标准材料与通过化学BTi2和采用FBHT生产得到的相同等级的连续管相比较。在该比较中,不同的管位置将被考虑:-基础金属(BM):除去ERW线和斜焊的连续管微结构,当“除去”意味着不包括在该区域中时,在任何焊接操作和它们可能的焊接后热处理(PWHT,Post-WeldHeatTreatment)过程中产生热影响区(HAZ)。-斜焊(BW):对应于条带到条带连接的微结构区域,其可以通过等离子弧焊(PAW,PlasmaArcWelding)、搅拌摩擦焊(FSW,FrictionStirWelding)或任何其他焊接技术进行。在该区域中还包括在焊接和PWHT过程中相应的热影响区。-ERW线:在管形成及其局部化的PWHT过程中,由纵向ERW焊接导致的微结构,该局部化的PWHT过程通常是焊缝退火。如同前面的情形,该区域也包括相应的热影响区。在图8A-B中呈现了对应于标准连续管(A)和本发明(B)的基础金属微结构。在第一情形下,观察到具有精细碳化物分布的铁素体基质。该基质和精细结构由控制的热轧过程导致。本发明的微结构(图8B)主要包括回火马氏体。贝氏体的体积百分率在本例中小于5%。回火马氏体结构也是在铁素体基质中碳化铁的精细分布。现有结构和新结构之间的主要区别涉及铁素体晶粒和子晶粒的形态,和位错密度。然而,关于细化和均匀性,两个结构非常类似。在图9A-B中示出了对应于ERW线的扫描电子显微图。清楚的是,现有结构的两个微组分出现:存在软铁素体晶粒和硬块,其包括精细珠光体、马氏体和一些残留的奥氏体的混合物。在该类结构中,塑性应变在铁素体中局部化,裂纹可以成核并在邻近的脆化组分(未回火马氏体和高碳残留奥氏体)中扩展。另一方面,用本发明范围内的化学成分和处理条件获得的ERW线微结构是均质的,并非常类似于相应的基础金属结构。对应于ERW的HAZ的微结构出现在图10A-B中。在标准材料中,清楚的是中心偏析带的残余部分的出现,其在焊缝退火之后部分地转变为未回火马氏体。再次,这些是脆化组分,其沿着ERW线局部化,并可以在使用过程中成核和扩展裂纹。破坏风险高于前面的例子,因为刚刚提到的组分具有更大的尺寸。另一方面,在淬火和回火过的连续管中,靠近ERW线的结构是均匀的,而看不到中心偏析带的残余部分。在图11A-B中呈现了一些扫描电子显微图,其对应于现有连续管和本发明两者的斜焊HAZ。现有材料中,微结构非常不同于在基础金属(BM)中的。其主要包括上贝氏体,且晶粒尺寸是大的(50微米,比较于BM的小于15微米)。该类粗结构对于低周疲劳是不足够的,因为裂纹可以容易地沿着贝氏体条板扩展。图12中示出了疲劳裂纹的例子,该疲劳裂纹在斜焊中横跨粗贝氏体。这是靠近主要破坏的次级裂纹,该主要破坏发生在标准连续管等级110的使用过程中。另一方面,本发明中的斜焊微结构再次非常类似于对应于基础金属的微结构。没有上贝氏体晶粒被观察到。重要的是,一些贝氏体可能在整体热处理之后出现,但是由于足够的化学成分和处理条件的选择,该组分的相应的体积百分率低于10%。这是本发明所述化学成分良好可淬硬性的主要理由。此外,由于奥氏体化温度的上限,最终的晶粒尺寸是小的(小于20微米),然后会扩展裂纹的大的贝氏体条板得以完全避免。图13-14呈现了通过本发明公开的钢化学成分和处理条件的组合获得的微结构的均匀性的其他例子。在图13中示出了现有生产的连续管中横跨斜焊的硬度的典型变化,比较于采用新化学成分和处理方法所获得的。清楚的是,当使用本发明时,硬度变化大大地减小。结果,材料在局部区域(本例中斜焊的HAZ)累积应力的趋势也得以减小,疲劳寿命得以提高。图14A-B表示一些微结构,其对应于在斜焊和ERW线之间的交叉处。清楚的是,随着现有路线获得大的微结构异质性。这些异质性采用本发明公开的化学成分和处理条件而被成功消除。例子E:连续管疲劳测试为了比较根据本发明生产的连续管相对于标准产品的性能,一系列测试在实验室中进行。连续管样品在如图15中示意性示出的疲劳机中测试。该机器能够仿真卷起和展开操作过程中的弯曲变形,同时施加以内部压力。因此,测试对于低周疲劳条件下的材料进行评级是有用的,其接近在实际现场操作过程中的那些经历。在测试过程中,疲劳样品(管件,5或6英尺长)夹在一端上,而交替力通过液压作动器施加在相反端上。通过在固定半径的弯曲心轴上弯曲样品,将变形周期施加在测试样品上,然后对抗笔直的支撑而将其拉直。钢帽焊接在样品的端部处并连接到液压泵上,从而使得循环得以进行,样品填充以处于恒定内部压力下的水,直至发生破坏。当发生内部压力丢失时,测试结束,因为裂纹发展通过壁厚。测试在具有不同化学成分和等级的连续管上进行,如表E1所示。管几何在所有情形下都一样(OD2”,重量0.19”)。STD1,STD2和STD3是在API5ST中所述限度内的钢,接着进行标准路线的处理。BTi1、BTi2和CrMoBTi4是根据本发明选择和处理的化学成分。重要的是,CrMoBTi4钢用于生产两个非标准的等级,具有125Ksi和140Ksi的最小屈服强度(API5ST中描述的最高等级具有110Ksi的SMYS)。测试在具有和不具有斜焊的管件上进行(在所有情形下,纵向ERW线包括在样品中)。测试的严格性主要依赖于两个参数:弯曲半径和内部压力。在本研究中,弯曲半径是48英寸,其对应于大约2%的塑性应变。考虑在1600psi和13500psi之间的内部压力,这产生在从大约10%到60%的等级最小屈服强度范围中的箍应力(hoopstress)。表E1:在本研究中分析的化学成分和连续管等级。在图16中呈现了一些关于比较的结果,该比较在具有和不具有斜焊(BW)的样品中测量到的疲劳寿命之间进行。图中所示的值对应于在测试现有的和非现有的连续管等级时获得的平均值。在现有材料的情形下,当测试的样品含有斜焊时,疲劳寿命有明显的减小。另一方面,当测试在BW样品上进行时,根据本发明生产的连续管不出现疲劳寿命的重要变化。这是管均匀性结构的结果,在基础金属、ERW线和斜焊之间的机械性能几乎没有区别。图17示出了通过本发明公开的化学成分和处理条件获得的连续管疲劳寿命的提高。对于等级80、90和110,比较针对通过现有方法生产的等效等级。在等级125和140的情形下,这是非标准的,疲劳寿命比较针对等级110中的STD3钢进行,其在类似的条件下(管几何、弯曲半径和内部压力)测试。图中示出的结果对应于每个等级的平均值,误差条表示在使用不同的内部压力时获得的差量。在图17中,清楚的是,当采用根据本发明的化学成分和处理条件时,观察到疲劳寿命的显著改进。例如,在等级110中,疲劳寿命提高了大约100%。这是这样的事实的结果,即在现有的连续管中,疲劳性能受限于斜焊(其通常是关于低周疲劳的弱点,引起其微结构的异质性和脆化组分)。在根据本发明生产的连续管中,在斜焊处没有重要的疲劳寿命减少,这大大地提高了管的总性能。关于非标准等级,疲劳寿命中大的改进是由于这样的事实,即比较是针对在类似处理条件下测试的现有110等级。然而,对于相同的内部压力,施加的箍应力更加接近较低等级的最小屈服强度,而等级110的测试严格性比较于等级125和140提升了。这些结果表明,通过更高的等级(在现有方法中未实现),疲劳寿命对于相同的使用条件有了大大提高。例子F:抗硫化物应力开裂性在含有H2S的环境中关于氢脆化的材料性能涉及腐蚀环境、存在可能局部地增加氢的含量的阱(traps)(例如沉淀和位错),以及存在脆化区域的组合作用,其中裂纹可以容易地扩展。在现有连续管材料中的关键的脆化区域的可能来源是原材料中的替代元素(例如Mn)的偏析模式。不同含量的区域倾向于以不同方式响应在斜焊、PWHT、ERW和焊缝退火过程中施加的热循环,并可能导致脆化组分的局部形成。特别地,当材料在ERW处理之后焊缝退火,管体快速地从焊接区域提取热。如果偏析足够高,由于冷却条件,伸长的高硬区域可能形成,其中可能出现马氏体。这些区域将保持在管中,成为裂纹容易扩展的路径。新的处理用作制造的最后阶段的事实允许过度硬化区域最小化。其他相关差异是:a)在管冷成型过程中引入的位错没有出现在新产品中,b)在新产品中的碳化物比典型的珠光体/贝氏体长脆化碳化物更小并是隔离的。结果,根据本发明的化学成分和处理条件生产的连续管对含H2S的环境中的开裂具有改进的性能。表F1:在本研究中分析的钢化学成分和连续管等级。为了对抗SSC开裂性进行第一分析,连续管等级80样品通过这样生产:i)标准的处理和ii)新的化学成分-处理采用NACETM0177的方法C(C环)进行评估。钢化学成分在表F1中示出。两种材料(在每种情形下由3个样品)都在C环样品的中心处对ERW焊缝缝进行测试,采用了如下条件:负载:80Ksi的90%,方案A,1barH2S,测试时间:720小时在标准连续管的情形下,所有3个样品都失败了。另一方面,对应于新的化学成分-处理的样品通过了测试(图5A-B,具有C环的图片)。尽管进行更多的测试,以分析不同等级的耐脆化性,和斜焊的作用,本第一结果表明,比较于标准条件有了清楚的提高,这归功于新处理方法情形下,基础金属和ERW线更均匀的微结构。如图18A-B所示,通过现有过程形成的C环具有大的下到中间的裂纹,而通过本发明的过程的实施方式形成的C环没有裂纹。在一些实施方式中,B-Ti和Cr-Mo添加剂可以减小最大Mn。在一些实施方式中,等级可以高于110,这不同于采用现有方法所获得的。结合特定方面、实施方式或例子描述的特征、材料、特性或组应理解为可应用于这里描述的其他方面、实施方式或例子,除非与其不兼容。本发明公开的所有特征(包括后面的权利要求、摘要和附图),和/或这样公开的任何方法或过程的所有步骤,可以以任何组合结合,除非至少一些特征和/或步骤互相排斥。保护范围不限于任何前面实施方式的细节。保护范围延伸到本发明公开的特征的任何新颖的一个或任何新颖的组合(包括任何后面的权利要求、摘要和附图),或者这样公开的任何方法或过程的步骤的任何新颖的一个或任何新颖的组合。尽管已经描述了某些实施方式,这些实施方式已经只通过例子呈现,而不旨在限定保护范围。事实上,这里所述的新颖方法和装置可以以许多形式具体化。而且,可以对这里所述的方法、成分和装置的形式作出不同的省略、替换和改变。本领域技术人员将理解的是,在一些实施方式中,在示例的和/或公开的过程中发生的实际步骤可以不同于在图中所示的。根据实施方式,上面所述的某些步骤可以去除,其他的可以增加。而且,上面公开的具体实施方式的特征和属性可以以不同方式组合,以形成其他实施方式。所有这些都落入本发明的范围内。尽管本发明包括某些实施方式、例子和应用,本领域技术人员将理解的是,本发明将具体公开的实施方式延伸到其他替代的实施方式和/或使用和明显的变形及其等同物,包括这样的实施方式,其不具有这里陈述的所有特征和优点。相应地,本发明的范围不旨在通过这里的优选实施方式的具体公开而限定,而可以通过这里呈现或者将来呈现的权利要求限定。