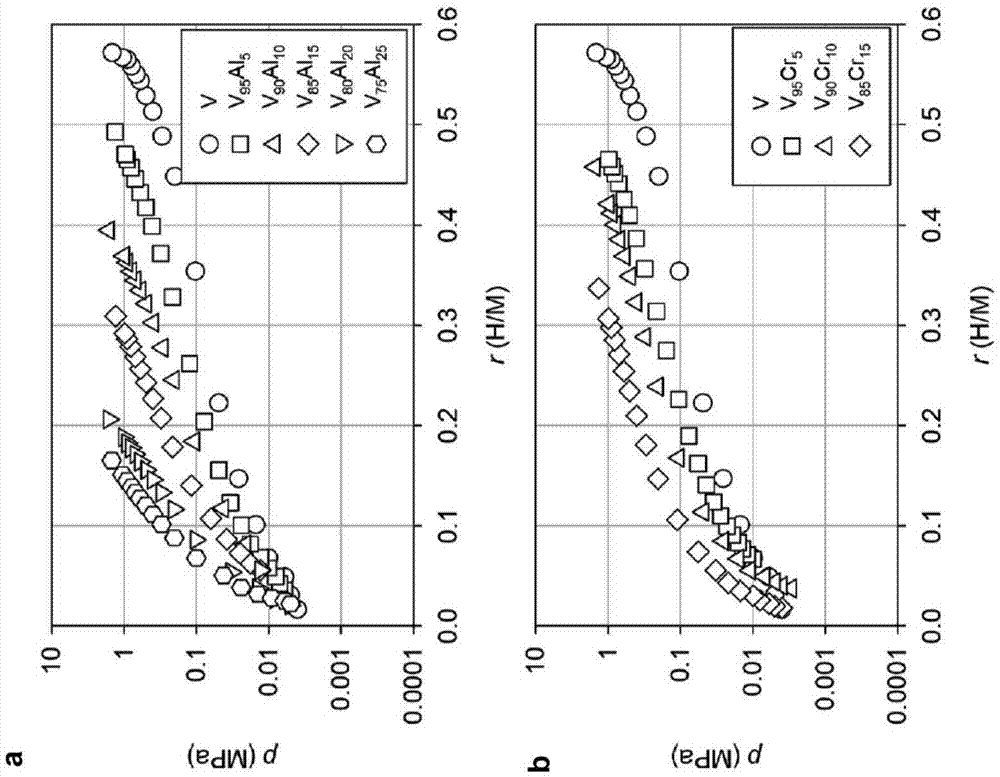
本发明总体涉及用于膜反应器的合金、由所述合金形成的膜和包含所述膜的膜反应器、以及用于操作包含由所述合金形成的膜的催化膜反应器的方法。本发明特别适用于从气流中分离氢,比如在水变换反应中产生的气流,并且方便的是在下文中针对该示例性应用公开本发明。然而,应明白本发明不限于该应用,并且可具有需要选择性氢分离或吸收的更广泛的应用。
背景技术:
:以下对本发明背景的描述旨在促进对本发明的理解。然而,应当明白此描述并非承认或认可所提及的任何资料在本申请的优选权日时已被公开、已知或为常识的一部分。从煤类能量体系中俘获co2排放是一种可以降低煤炭利用中的温室气体强度的手段。俘获可在燃烧前或燃烧后进行,其中来自煤的合成气的能量物质经由水煤气变换(wgs)反应而变换为h2,然后进行co2的分离和俘获,如(1)中所示:目前正在开发从混合气流中分离出h2的基于膜的分离技术。一般而言,膜是对一种物类选择性可透的近二维结构。在气体分离的背景下,膜允许一种物类选择性可透(通常是h2),同时阻挡其它物类(例如co、co2、h2o、n2等)。氢选择性膜可由无机、金属或陶瓷材料形成,其各自具有特征性的氢通量、操作温度和选择性。催化膜反应器(cmr)整合了氢选择性膜与水煤气变换催化剂,从而能够生产并分离h2。cmr一般在约450℃操作以利于wgs反应的快速动力学。此外,cmr允许实现大于平衡的转换,因为透过膜的h2产物的持续消耗将wgs反应推向产物一侧。h2的原位连续提取可实现几乎100%的co转换。钯是已知最佳的合金膜材料,其具有渗透300℃~600℃的氢同时抵挡诸如co和h2o等合成气物类的能力。然而,钯的高成本(约$us330/m2/μm(2014))驱使研究 朝以下方向进行:把其消耗降至最低,最明显的是通过与较廉价的金属进行合金化,并且通过在具有极细的孔的支撑结构上沉积极薄(<5μm)的层来把其厚度降至最低。许多其它金属展现了非常高的氢可透性,最值得注意的是钒、钛、钽和锆。在400℃时,这些金属的氢可透性比钯大大约两个量级,并且原料价格明显更低。在这些金属中,v具有最宽的合金化范围,这意味着其具有将合金特性改性以满足cmr要求的最宽范围。然而,在氢的存在下钒展现出较差的机械稳定性,使其不适用于工业上的氢分离工艺。钒易于吸收高浓度的氢。因此,钒氢化物易发生脆性破坏,原因在于氢对合金内的金属键具有负面影响。用于cmr中的h2选择性膜的任何材料还必须具有合适的成形性/机械特性,这使得该材料能被制成所需构型,比如扁平状或管状膜。例如,用于制造管状产品的合金在大批量生产中通常展现出25%~35%的最大伸长率(通过挤出和拉拔),而若采用定制的变形加工(其中每道次(pass)的变形减少,并且道次间有大量的煅烧),则最大伸长率为至少10%~20%。美国专利7,001,446b2公开了用于从含氢气体中分离氢的氢可透膜。该膜为具有中央氢可透层以及一个或多个催化剂层、阻挡层和/或保护层的多层。在一些实施方式中教导了中央氢可透层包含氢可透金属或金属合金,包括钒合金。据总体教导,大量合适的合金适合于此氢可透层,例如在此美国专利的表1中概述的那些。然而,注意到没有特定的合金据教导能提供用作膜、更具体为适于cmr的管状膜的最佳特性。因此,期望提供一种合金和用所述合金形成的膜,其具有用于cmr、优选用作cmr的管状膜的适当的氢输送、机械稳定性和成形性。技术实现要素:本发明的第一方面提供了一种钒合金,其包括:钒;含量为大于0~10at%的铝;和含量小于0.01at%的ta。本发明第一方面的合金可具体用于催化膜反应器中,特别是用于催化膜反应器的管状膜。本发明人已确定钒类合金应展现出以下关键特性以便最佳地用作cmr反应器内 的合金膜:-良好的扩散性/吸收比,其中,可在将氢脆化效果减到最少的同时实现高h2渗透性;-良好的成形性,包括良好的展延性(ductility)(至少10%伸长),允许优选地使用现存或已知的制造工艺来制造合金膜的期望构型;和-机械稳定性,特别而言,将α至β氢化物相转变抑制在所需的cmr停机温度左右或以下。这能允许所选择的合金可以在所选择的操作温度(例如400℃)和(更低的)停机温度(例如环境温度)之间循环,而不经历潜在的灾难性相变。申请人进行了大量的试验性尝试以确定最适合的v合金(下文中详细描述)。研究了许多合金,包括v-al、v-ni、v-cr和v-ti-al类合金。v-al类合金被鉴定为具有制造管(例如通过管材拉拔、辊轧或挤出)所需的机械特性,而v-ni和v-cr合金对于此制造工艺而言过脆。结合有利的渗透特性,选择了v-al合金,原因在于其具有满足以上标准的出乎意料地良好和最佳的特性,特别是与所研究的其它v合金相比。本发明的合金是钒类合金。在一些实施方式中,钒含量为85at%~98at%,优选为90at%~96at%,优选为91at%~96at%,更优选为90at%~95at%。在一些实施方式中,钒含量为92at%~98at%,优选为92at%~96at%,优选为92at%~97at%。本发明的合金的主要副成分是铝。铝含量确保了合金包含具有体心立方结构的钒固溶体。而且,本发明人发现,随着al含量的增加,氢的吸收减少,从而提高了对氢脆化的抗性。注意在ni和cr的情况中也是如此,但ti不是。然而,如下面提及的,选择铝也是基于赋予与机械特性和机械稳定性有关的其它有利特性,包括α-氢化物和β-氢化物相转变。合金的铝含量为从大于0至10at%。在一些实施方式中,铝含量为0.1at%~9at%,优选为0.5at%~8.5at%,优选为1at%~10at%,更优选为2at%~8at%,还更优选为3at%~7at%。在其他实施方式中,铝含量为1at%~10at%,优选为3at%~10at%,更优选为2at%~6at%。进一步的研究表明添加晶粒细化剂(例如钛(ti)和硼(b))进一步改善了合金的期望特性。因此,在本发明的一些实施方式中,钒合金还包含含量为从大于0至5at%的选自钛(ti)、铬(cr)、铁(fe)、镍(ni)和硼(b)中至少一种的晶粒细化元素。因此,本发明选择的合金包含钒类合金,其具以下固溶体通式:v100-(y+z)alyxz其中x=ti、cr、fe、ni或b中的至少一种;y为>0~10;并且z为0~5。本发明人已发现添加的ti、cr、fe、ni或b充当钒固溶体(vss)的晶粒细化剂。晶粒细化剂优选将晶粒形态从粒状(具有数毫米的晶粒尺寸)变为树枝状(具有小于200微米的一次间距)。优选地,晶粒细化剂为ti或b。晶粒尺寸的减小影响产品的成形性,特别是由合金形成的产品或其它元件的展延性。合金的最大伸长率优选超过10%,优选大于11%,更优选大于15%,从而提供用作膜所需的成形性。本发明人已发现添加含量大于2at%的al、cr、ni皆降低钒的展延性。然而,相比于其它元素,al的该效果要小得多。合金中晶粒细化元素的量为从大于0至5at%,优选为0.2at%~4at%,优选为从大于0至2at%。在一些实施方式中,晶粒细化元素的含量为0.1at%~2at%,优选为0.1at%~2at%,优选为0.2at%~1.5at%,更优选为0.1at%~1at%。合金的钽(ta)含量优选小于0.01at%。优选最小化、且更优选消除合金中的ta含量,因为较高的钽含量提高了合金的刚度,因而限制了用该合金所能实现的伸长量。在一些实施方式中,合金的钽(ta)含量优选小于0.01at%但大于0。重要的是,合金在膜(特别是用于cmr的膜)的操作温度范围内机械稳定。对于纯v,由α-氢化物(具有间隙氢的钒的体心立方固溶体)和β-氢化物(具有间隙氢的体心四方固溶体)的转变发生在约190℃。此种相转变在合金内造成应力,导致破裂。本发明人已发现,添加ni和cr都提高了氢化物形成的临界转变温度(tc)。有利地,本发明人还发现了添加al降低了转变温度。例如,添加10at%的al使转变温度降至小于30℃。这允许由该合金形成的组件(例如膜)可以在氢气氛下经历热循环。在膜的情况下,可使该膜在cmr的启动和停机期间在高温(例如400℃)和低温(例如环境温度)间进行热循环,而不经历可能造成破裂的相转变。在一些实施方式中,优选的是,合金的组成使得钒合金的α-氢化物相和β-氢化物相之间的相转变温度小于100℃,优选小于50℃,更优选小于30℃,还更优选小于20℃。商业形式的钒含有显著水平的溶解氧。氧通过与溶解的氢反应可导致脆化。然而,本发明人发现了al和ti清除来自钒的氧。因此,优选提供包含降低合金氧含量的合金化组分的合金。合金的氧含量优选小于0.15wt%,优选小于0.1wt%、优选小于0.8wt%,更优选小于0.05wt%。应当理解,钒合金可包含杂质成分,尽管通常是较少的杂质成分。在优选实施方 式中,杂质含量小于0.5at%,优选小于0.1at%,更优选小于0.05at%。本发明的合金可通过任何合适的方法制造。在优选形式中,合金包括铸造的合金。本发明的第二方面提供了用于氢选择性合金膜的合金,其包括本发明第一方面的钒合金。在一些实施方式中,氢选择性合金膜包括至少一个管状膜。本发明的第三方面提供了用于氢选择性合金膜的合金的用途,该合金包括本发明第一方面的钒合金。在一些实施方式中,氢选择性合金膜包括至少一个管状膜。本发明的第四方面提供了制造钒合金的方法,其包括:形成本发明第一方面的钒合金;并且在800℃~1500℃的温度和50mpa~500mpa的压力下热处理所形成的钒合金,从而制得适用于形成薄壁管的变形加工的精炼钒合金。管制造期间合金的机械故障通常与孔隙的存在有关,并且与低伸长率有关,该低伸长率归因于较差的微结构,例如晶粒尺寸的不均匀分布或非等轴晶粒。因此,从成形性的角度来看,理想的是以小晶粒尺寸和窄尺寸分布形成合金的微结构。还优选以最低的(或最小化的)孔隙度形成合金。铸造(casting)和其它成形工艺产生组成均匀但微结构不均匀的合金。在本发明的第二方面中,晶粒尺寸的精细化以及更大的微结构均匀性通过以下方式实现:i)向合金中添加本发明第一方面定义的晶粒细化元素;以及ii)热处理步骤。不希望受任一种理论的限制,本申请人发现了在环境压力(0.1mpa)和中等温度范围(200℃~600℃)下的常规热处理对于降低孔隙度和通过再结晶优化微结构而言几乎没有效果,原因在于v-al合金的高液相线和固相线(例如,v95al5合金的熔点超过1900℃)。因此需要不同的热处理方案。本发明的热处理步骤通过施加温度和压力来增强所形成的钒合金的微结构均匀性。相比于没有该热处理步骤的相同合金铸件,精炼的钒合金具有更小的更均匀的晶粒分布以及优选的降低的孔隙度。此微结构增强了合金的成形性,包括提高合金的展延性。精炼的钒合金的展延性优选大于10%伸长,优选大于11%伸长,更优选大于或等于12%伸长。在一些实施方式,精炼的钒合金的展延性大于或等于13%伸长率,优选大于或等于14%伸长率,更优选大于或等于15%伸长率,更优选为11%伸长率~ 20%伸长率,更优选为13%伸长率~20%伸长率,还更优选为13%伸长率~18%伸长率,还更优选为11%伸长率~19%伸长率。本发明的方法优选产生晶粒直线截距(grainlinearintercept)小于5.0mm的钒合金,晶粒直线截距优选小于5.5mm,优选小于4.0mm,优选小于4.5mm,甚至更优选小于3.0mm,还优选小于2.0mm,并且最优选小于1.0mm,其全部基于6个晶粒、优选8个晶粒的最小样本量。在特定实施方式中,微结构包括树枝状晶体(dendrite)。在这些实施方式中,基于6个晶粒、优选8个晶粒的最小样本量,晶粒直线截距值优选小于500微米,优选小于450微米,更优选为50微米~450微米,更优选为50微米~400微米,甚至更优选为50微米~300微米,更优选为100微米~350微米,还更优选为100微米~200微米。此外,还优选的是,精炼的钒合金不包含平均尺寸大于0.5mm的任何空穴(void),空穴的平均尺寸优选不大于0.4mm、优选不大于0.3mm。可采用奥林巴斯的“streamessential”图像分析软件利用astme112-113方法测定晶粒直线截距。除非另作说明,晶粒直线截距是在晶粒不等轴的情况(例如柱状)下与晶粒生长方向垂直的宽度的测量值。成形方法可包括在所形成的合金内产生组成均匀性的任何合适的成形方法。在一些实施方式中,成形方法包括熔铸方法,例如电弧熔炼法或感应熔炼法中的至少一种。在优选的实施方式中,成形方法包括逐层电弧熔炼法或冷坩埚感应熔炼法中的至少一种。成形方法可包括形成合金锭或中小型坯(billet)。热处理步骤可包括能够对所形成的合金施加所需温度和压力的任何合适的过程。在一个实施方式中,热处理步骤包括热等静压(hip)过程。hip涉及在一段规定的时间内同时施加高温和压力。温度和压力的施加对于获得所需的晶粒和微结构精炼而言都是重要的。热处理步骤包括使所述钒合金经历1000℃~1400℃的温度,优选为1050℃~1380℃,更优选为1100℃~1300℃,更优选为至多1350℃的温度,还更优选为至多1400℃的温度。在一个实施方式中,加热处理步骤在约1200℃、优选1150℃~1250℃的温度下进行。类似地,热处理步骤包括使所述钒合金经历50mpa~400mpa、优选75mpa~350mpa、更优选100mpa~300mpa的压力。在一个实施方式中,热处理步骤在约200 mpa、优选150mpa~250mpa的压力下进行。热处理步骤通常以选定的时间长度进行。在一些实施方式中,热处理步骤持续进行至少30分钟,优选至少45分钟,更优选至少1小时,优选至少1.5小时,更优选至少2小时。然而,应当明白持续时间取决于经受处理的合金的组成、用量和构型。在热处理步骤期间对合金施加的加热速度和冷却速度也能影响精炼结果。在一些实施方式中,加热速度或冷却速度中的至少一个为至少4k/分钟,优选为至少4.5k/分钟,优选为至少5k/分钟,更优选为4k/分钟~10k/分钟,优选为5k/分钟~9k/分钟,并且还更优选为4k/分钟~8k/分钟。热处理步骤优选在诸如氩等惰性气氛内进行。在示例性实施方式中,铸造合金经受以下条件:·1200℃的温度;·200mpa的压力;·持续2小时;·5k/分钟的加热/冷却速度;和·氩保护气氛。本发明的第五方面提供了用于催化膜反应器的管状膜的合金,其包括用本发明第四方面的方法形成的钒合金。本发明的第六方面提供了制造管状膜的方法,其包括:根据本发明第四方面的方法形成精炼的钒合金;并且将精炼的钒合金形成为薄壁管。管状膜可具有如上所述的任何合适的尺寸。如下面更详细描述的,在一些实施方式中,薄壁管包括外径为2mm~25mm、优选3mm~20mm且壁厚为0.05mm~1mm、优选0.1mm~1.5mm的管。应理解的是,管的制造是多步过程,首先涉及制造具有所需的组成、微结构和尺寸的棒,然后将这些棒变形为所需的最终形状。可使用任何合适的变形方法来形成管,包括拉拔、辊轧、挤出铸造、棒铸或其组合。本发明的第七方面提供了用本发明第六方面的方法形成的用于催化膜反应器的膜。该膜可具有各种构型,例如扁平型或管状。在优选的实施方式中,所述膜包括管状膜。本发明的第八方面提供了催化膜反应器(cmr),其包含至少一个用本发明第六方面的方法形成的管状膜。本发明的膜可具有任何合适的构型。在一些实施方式中,所述膜可包括基本扁平的膜。在其他实施方式中,所述膜包括至少一个管。应理解的是,膜的各种构型的选择基于该构型所能够为特定cmr构型带来的特定优点。cmr是基本上二维的装置,其通过与膜相邻的催化剂床沿着一个维度输送合成气。平面膜比管状膜更容易制造且更廉价,但由于该膜在其外缘周围被密封,其具有更大的密封区域。此种密封构型提供了更大的密封区域,并因此可以易于发生在残液和渗透物气流之间的泄露。管状膜使得能够使用管状cmr,因此可减少密封区域。在管状反应器中,仅需在管的各末端进行密封(通常为压缩密封)。在一些实施方式中,本发明的膜具有管状构型,优选包括管。所述管可具有任何所需尺寸。在一些实施方式中,外径为2mm~25mm,优选为3mm~24mm,优选为5mm~15mm,优选为6mm~13mm,更优选为8mm~12mm。在一些实施方式中,管壁厚小于或等于1mm,优选为0.1mm~1.5mm,优选为0.05mm~1mm,更优选小于0.5mm,更优选小于或等于0.2mm。在一个示例性实施方式中,管状膜具有以下规格:·长度≥1000mm·外径:9.52mm(3/8”)·壁厚≤0.2mm合金膜是金属氢化物,其中溶解的原子氢占据金属原子之间的间隙位置。钒氢化物在与金属膜相关的温度和压力下可以采取两种主要形式之一,这两种主要形式为α-氢化物(其在结晶学上与主体金属相同,并且其中氢原子随机分布在体心立方主体内的间隙中)和β-氢化物(其在结晶学上不同于α-氢化物,其中氢原子有序地处在体心四方主体内的间隙中)。α相和β相在某些浓度/温度条件下可以共存。然而,在大多数情况下,这些相之间的晶格尺寸的显著差别在合金内造成了显著的应力,其可表现出合金的起皱(最好情况)或碎裂(最坏情况)。因此,在诸如包含合金膜的cmr的停机等过程中,优选在冷却膜时避免此种相转变。如前所述,选择本发明合金的组成以便在操作过程中避免此种相转变。在这方面,v-al合金中的氢化物相转变温度(其中,对于v90al10(at.%),tc<30℃)是有利的,可 以利用其来避免此种相转变。相比之下,v-ni的转变温度(对于v90ni10为>400℃)和v–cr合金的转变温度(对于v90cr10为>200℃)不能使这些合金在所需的操作范围(例如0℃~500℃)内避免相转变。实际上,当从约400℃的操作温度冷却至室温时,这些合金的使用增加了脆性破坏。使用由本发明的钒合金形成的合金膜能够有利地使cmr在从约400℃的操作温度至通常为30℃以下(优选20℃~30℃)的室温的温度下停机,其中反应器在操作性氢与金属(h/m)之比的常见范围(通常大于0.05)内操作,而膜不经历α至β相转变。cmr的操作可以包括:在包括其操作温度和环境温度的温度范围内的启动和停机工序,且不经历相转变,从而允许简单化地操作反应器。这允许cmr和膜可以通过多个操作循环来使用,在操作循环中cmr被启动、操作和停机。特别而言,避免了停机期间由于相转变而造成的膜的脆性破坏。因此,本发明的第九方面提供了操作催化膜反应器的方法,其包括:提供包含至少一个管状膜的催化剂膜反应器,所述管状膜包含本发明第一方面的钒合金或用本发明第六方面的方法形成;并且当反应器处于0℃~350℃的操作温度时,以大于0.05的氢与金属(h/m)之比操作催化膜反应器。操作催化膜反应器的步骤可包括多个工序,包括反应器的反应性操作、反应器的启动和停机工序以及可采用那些条件的其它任何反应器应用或操作行为和/或过程。在一些实施方式中,操作温度为20℃~300℃,优选为25℃~275℃,更优选为30℃~250℃,甚至更优选为40℃~200℃。类似地,在一些实施方式中,h/m比大于0.1,优选大于0.15,优选大于0.2,优选大于0.25,甚至更优选大于0.3。相比于包含由钒或其它常规钒合金形成的管状膜的催化膜反应器,具有含本发明的钒合金/精炼钒合金的管状膜的催化膜反应器提供了显著的操作优势。对于v和其它v合金,α至β相转变在如上所述的操作条件下发生。任何相转变都可以自然而然地影响性质,从而影响管状膜的寿命。因此,具有含本发明的钒合金/精炼钒合金的管状膜的催化膜反应器可有利地启动、在反应温度下操作并在较宽的温度范围内和h/m比条件(>0.05)下停机,而无需显著改变反应器内的条件、特别是h/m比。反应器的操作包括反应器的启动和停机工序。启动通常包括将反应器从室温加热至操作温度。停机通常包括将反应器从操作温度冷却至另一温度,通常为室温。另外, 室温优选包括环境温度。在一些实施方式中,室温包括30℃以下,优选10℃~30℃,更优选20℃~30℃。在一些实施方式中,操作条件包括催化膜反应器的冷却步骤,优选地包括催化膜反应器的环境冷却。然而,应明白可使用其它冷却方案,比如利用诸如热交换器等冷却装置的辅助冷却、流体冷却或对流冷却等。应明白,除非另作说明,将至少六个测量值的均值确定为实验参数。本发明的第十方面提供了用于包含薄壁管的催化膜反应器的膜,所述薄壁管包含钒合金,所述钒合金包括:钒;含量为大于0at%~10at%的铝;和含量小于0.01at%的ta;所述钒合金的展延性大于10%伸长率,优选大于11%伸长率。应明白,本发明第十方面的膜的合金含量和机械性质(特别是展延性)与上面针对本发明第一和第二方面描述的相同,并且应明白其同样适用于本发明的此第十方面。在一些实施方式中,膜还包含选自ti、cr、fe、ni或b的晶粒细化元素,其含量为大于0~5at%,优选为0.2at%~4.5at%。在一些实施方式中,晶粒细化元素的含量为0.1at%~2at%,优选为0.1at%~2at%,更优选为0.1at%~1at%。在一些实施方式中,钒合金的晶粒直线截距小于5.0mm,优选小于5.5mm,优选小于4.0mm,优选小于4.5mm,甚至更优选小于3.0mm,还优选小于2.0mm,并且最优选小于1.0mm,其全部基于6个晶粒、优选8个晶粒的最小样本量。在特定实施方式中,微结构包括树枝状晶体。在这些实施方式中,基于6个晶粒、优选8个晶粒的最小样本量,晶粒直线截距值优选小于500微米,优选小于450微米,更优选为50微米~450微米,更优选为50微米~400微米,甚至更优选为50微米~300微米,更优选为100微米~350微米,还更优选为100微米~200微米。此外,还优选的是,精炼的钒合金不包含平均尺寸大于0.5mm的任何空穴,空穴的平均尺寸优选不大于0.4mm,优选不大于0.3mm。可采用奥林巴斯的“streamessential”图像分析软件利用astme112-113方法测定晶粒直线截距。除非另作说明,晶粒直线截距是在晶粒不等轴的情况(例如柱状)下与晶粒生长方向垂直的宽度的测量值。管状膜可具有如上所述的任何合适的尺寸。如下面更详细描述的,在一些实施方式中,薄壁管包括外径为2mm~25mm、优选3mm~20mm且壁厚为0.05mm~1mm、优选0.1mm~1.5mm的管。在实施方式中,钒合金是已经历了在800℃~1500℃的温度和50mpa~500mpa的压力下的热处理的精炼钒合金。在实施方式中,热处理包括使钒合金经历1000℃~1400℃的温度,优选为1050℃~1380℃,更优选为至多1400℃的温度,还更优选为约1200℃。在实施方式中,热处理步骤包括使钒合金经历50mpa~400mpa的压力,优选为75mpa~350mpa,更优选为约200mpa。在实施方式中,精炼的钒合金的展延性大于10%伸长率,优选大于或等于11%伸长率,更优选大于或等于13%伸长率,还更优选大于或等于14%伸长率。本发明的第十一方面提供了具有薄壁管膜的催化膜反应器,所述薄壁管膜包含钒合金,该钒合金包括:钒;含量为大于0at%~10at%的铝和含量小于0.01at%的ta;所述钒合金的展延性大于10%伸长率,优选大于11%伸长率。应明白本发明的第十一方面可包含上面对于本发明第十方面描述的全部特征。附图说明现将参照附图描述本发明,附图图示了本发明的特定优选实施方式,其中:图1提供了在400℃下对(a)v-al和(b)v-cr(下方)测量的h2通量(j,针对膜厚度的倒数将其归一化,x)与进给的h2压力的图。图2提供了在400℃下在不同的氢分压(p)下对钒以及(a)v-al和(b)v-cr合金测量的氢吸收(r,表达为h/m比)的图。图3提供了在400℃下透过(a)v-al和(b)v-cr合金的氢的浓度依赖性扩散系数(dh)的图。图4显示了在(a)673k和(b)623k下v90-xtixal10合金中的计算出的氢渗透性随不同进给压力的变化。图5提供了在(a)673k和(b)623k下的v90-xtixal10合金中不同的氢压力下溶解的氢浓度(r,以原子氢/金属比为单位)变化的图。图6显示了在(a)673k和(b)623k下v90-xtixal10合金中平均氢扩散系数(dh)随氢浓度(r)的变化。图7提供了以下合金的五个电子显微图(bse模式):(a)v88ti2al10;(b)v86ti4al10;(c)v84ti6al10;(d)v82ti8al10;和(e)v80ti10al10。图8提供了在400℃和10巴下v-ni、v-al和v-cr合金的h吸收减少的图。图9显示了在400℃下v-ni、v-al和v-cr合金的氢扩散系数(dh)和氢浓度之间的关系。图10显示了在400℃的操作温度下ni、cr和al对压力依赖性吸收(h/m)的影响。图11图示了以下情况的0.20mpa时的x射线衍射测量值:(a)时的v;(b)时的v90cr10;(c)时的v90ni10;和(d)时的v90al10。图12图示了在1巴的氢下从400℃冷却至环境温度的以下合金的x射线衍射测量值:(a)v90ni10(原子%,左侧);(b)v95al5合金;(c)v;和(d)v90al10。图13提供了随附sem图像的图表,其显示了v85ni15合金在热处理前后的伸长,其中(a)是对每个样品提供%伸长的图表;(b)是铸态合金的sem图像;(c)是经1000℃热处理的合金的sem图像;(d)是经1200℃热处理的合金的sem图像。图14显示了没有晶粒细化剂的v95al5锭的光学显微截面。图15显示了具有晶粒细化剂的v95al5锭的光学显微截面。图16提供了铸态v95al5合金的光学显微镜图像。图17提供了在与晶粒生长方向垂直的柱状区域中具有b0.1ti0.5(wt%)晶粒细化剂的铸态v95al5合金的光学显微镜图像。图18提供了在等轴区域中具有b0.1ti0.5(wt%)晶粒细化剂的铸态v95al5合金的光学显微镜图像。图19是通过“逐层”工艺制备的合金锭的照片,其中(a)是该锭的侧视图;(b)是该锭的俯视图。图20提供了hip处理之前v-al合金的光学显微照片。图21提供了hip处理之后v-al合金的光学显微照片。图22图示了催化膜反应器的示意图。图23提供了原型管状cmr的照片。图24提供了钒合金管与电镀pd催化剂层之间的界面的照片。图25提供了v和v90al10的避免α至β相转变所需的操作温度和h/m比的对比。具体实施方式本发明涉及一种合金、制造所述合金的精炼形式的方法、以及该合金和精炼合金 作为适合于催化膜反应器(cmr)的管状膜的用途。合金选择所选择的合金是钒类合金,其具有以下固溶体通式:v100-(y+z)alyxz其中x=ti、cr、fe、ni、b;y为>0~10;并且z为0~5。本发明人确定了钒类合金应展现出以下关键特性以便在cmr反应器内得到最佳使用:-良好的扩散性/吸收比,以使得在将氢脆化效果减到最少的同时能够实现高h2渗透性;-良好的成形性,包括良好的展延性(至少10%伸长),使得可以优选地使用现存或已知的制造工艺来制造期望构型的合金膜;和-机械稳定性,特别而言,将α至β氢化物相转变抑制在期望的cmr停机温度附近或以下,这意味着这些合金能够在cmr的常见操作温度(例如400℃)和(更低的)停机温度(例如环境温度)之间循环而不经历潜在的灾难性相变。申请人进行了大量的试验性尝试以确定最适合的v合金(下文中详细描述)。研究了许多合金,包括v-al、v-ni和v-cr类合金。选择试验1:v-al、v-cr和v-ni方法和材料选择若干种二元v-al(v95al5、v90al10、v85al15、v80al20、v75al25,其以原子%表达)和v-cr(v95cr5,v90cr10,v85cr15)合金以确保形成单相体心立方固溶体。用放电线切割加工来切割电弧熔炼的锭,由此制备圆形膜。化学验证合金组成,其处于标定组成的2%(相对)内。在dolanmd.non-pdbccalloymembranesforindustrialhydrogenseparation.jmembrsci2010;362(1-2):12-28(下文中称为“dolan2010”,应理解为将其内容通过此引用并入本说明书中)中详细描述了500nm厚pd催化剂层的制备方法,包括表面处理和沉积。膜约为900mm厚从而确保体扩散是氢渗透中的限速步骤。用恒压方法测量氢通量。用铬镍铁合金模块(其在惰性气氛下加热至400℃并保持12小时)内的铜垫圈将膜压缩密封。以足以防止浓差极化的速度对进料表面供应10%co2在h2中的混合物。此外,以足以防止浓差极化的速度对相反的表面进给ar。每 种条件维持约1小时以确保达到稳态流通条件。将进给压力从约1巴逐步增加至约10巴(a),同时将吹扫压力在整个实验中维持在约1.5巴(a)。利用针对认证标准气体混合物校准的气相色谱来测量渗透物流中的h2含量。然后基于渗透物h2浓度和ar的流速来计算通量。在渗透物流中检测到的co2表示膜的缺陷,并相应地终止试验。以测压方式测量每种合金的氢吸收。将样品在真空下于400℃保持24小时以确保从样品中清除了来自通量测量的任何残余h2。随后在约15巴~0巴之间产生等温线,先利用15巴吸收步骤,然后进行逐步解吸步骤。在渗透和吸收试验之后进行晶格参数测量。用philips行星式微型磨机将合金研磨成粉末。将这些粉末在真空下密封至玻璃管中,然后在450℃进行16小时的去应力煅烧。采用装配有lynxeye硅条检测器的利用cukα辐射(40kv,40ma)的brukerd8advancex射线衍射仪来获得xrd图案。以0.02°2θ的步长和每步3.2秒的计数时间,在2θ范围20°~130°上扫描粉末样品。用diffrac.topas软件包(brukeraxs)确定晶格参数。结果x射线衍射测量确认了各合金是单相钒固溶体(vss)。图1显示了在400℃下对v-al和v-cr系列的合金测量的通量随进给的氢分压(p1)的变化。在各情况中,已将通量针对膜厚度的倒数归一化,以校正各膜样品间样品厚度的微小差异。渗透表面的氢分压(p2)也未被计算在内,这是因为其与进给压力相比小到忽略不计。一些趋势是明显的。首先,对于各合金系列,通量随着al或cr含量的增加而降低。其次,v-cr合金的通量值大于对应的v-al合金。根据菲克第一扩散定律,通过溶剂(v类合金)的溶质(h)的通量是溶质的扩散系数与浓度梯度的乘积。知晓与图1所示通量值对应的氢分压处的溶解氢浓度便能够计算出通过各合金的h扩散系数。图2显示了在400℃下对应于各合金系列的一系列氢吸收等温线,其表达为针对氢分压(p)的溶解氢浓度r(单位是原子氢/金属比,或h/m)。另外,各图中也示出了未合金化的钒的吸收等温线以用于参照。v的吸收数据未展现出平台期(平台期会表示α/β转换),但确实展现出了明显的拐弯(这表示接近了会发生α/β转换的条件)。al的添加使得此拐弯变得较不明确,表明al使v稳定化以抵抗β-氢化物的形成。v-cr等温线具有与v的等温线相似的形状,展现了明显的拐点。不同于al,cr似乎未使 v稳定化以抵抗β-氢化物的形成。当合金有可能经受会发生此氢化物相转变的条件时,在评估这些膜在热循环期间的稳定性时,这是重要的考虑因素。这会在下面更详细地说明。根据前述方法(dolanmd,mclennankg,wayjd.diffusionofatomichydrogenthroughv-nialloymembranesundernondiluteconditions.jphyschemc2012;116(1):1512-8(下文中称为“dolan2012”,应理解为将其内容通过此引用并入本说明书中),利用在进料(r1)和渗透物(r2)表面处测量的通量和相应的h/m值来计算400℃时各合金的浓度依赖性扩散系数(dh)。对于各二元合金系列,由al或cr替代v降低了氢的扩散系数dh,并且如图3所示,al对扩散性的降低作用超过cr。各合金也展现了较强的浓度依赖性,其中dh随着溶解氢浓度的增加而增加。基于上面引用的v-ni系统的dolan2012研究,本文提供了两种二元钒类合金体系(v-al和v-cr)的对比。在所研究的组成范围内,这些系列中的各合金都形成单相的体心立方的固溶体。此趋势没有反映在氢吸收性质中,两种合金化元素皆降低了氢吸收,而铝的效果最显著。计算的氢扩散性遵循v-cr>v-al>v-ni的趋势,并且所有合金的扩散性皆显示了较强的浓度依赖性。选择试验2:v-ti-al合金方法和材料设计了式v90-xtixal10的合金系列,其中x=0、2、4、6、8和10,从而确保100%的vss相形成,并提供由ti代替v将如何影响氢输送的清楚说明。这将确定ti的性质是否可被用来开发用于高温h2/co2分离和膜反应器应用的稳健的氢分离膜。如dolan2012中所述来制备膜,各膜盘的表面被抛光并涂布有500nm的pd层以便使界面氢转移阻力最小。各膜的厚度约为900mm以确保氢的总体转运是渗透的限速步骤。将来自相同锭的样品安装并抛光,然后用背散射电子(bse)模式在扫描电子显微镜中检查。用恒压方法在623k和673k测量氢通量,其中将进给压力和渗透物压力保持在恒定值直至记录到恒定的h2通量为止(通常1800秒~3600秒)。以0.1mpa的增量将进给压力逐步增大至1.0mpa的最大值,并且针对所有测量将渗透物压力维持在0.15 mpa。在渗透物侧上使用吹扫气体(ar),并且改变流速以确保ar中的h2含量为1%至5%。用气相色谱测定吹扫气体中的h2含量,在所需浓度范围上对h2进行校准。在623k和673k,采用sieverts方法来测量处于0~1.5mpa的各合金的整体氢吸收。先进行1.5mpa吸收步骤、然后逐步进行解吸步骤直至0mpa,由此测得吸收等温线。用相同样品测量吸收和渗透以确保一致性。在渗透和吸收试验之后进行晶格参数测量。将合金在行星式磨机中研磨并在723k的氮气下煅烧60,000秒,以减轻应力并去除残留的氢。以0.02°的步长和每步3.2秒的计数时间,在2θ范围20°~130°上用cu-kα源记录xrd图案。用diffrac.topas软件包(bruker)将晶格参数精化。结果图4显示了对于处在673k(上图)和623k(下图)的v90-xtixal10系列中的合金,假定p-0.5浓度依赖性时计算出的氢渗透性随不同进给压力的变化。在各情况中,计算的渗透性随着进给压力的增加而明显降低,表明背离了理想的sieverts型行为。尽管进行了多次尝试,但都无法在623k测量数个合金的渗透性,原因在于合金的脆性破坏。对于在两种温度下都测量的那些合金,渗透性随着温度的降低而增加。一个系列内的曲线几乎重叠,表明在所研究的组成范围内,由ti替代v对渗透性的影响非常小(如p-0.5压力依赖性的图中所确定)。图5显示了针对v90-xtixal10系列中的所有合金的若干种温度下的一系列氢吸收等温线。存在明显的组成依赖性,其中溶解的氢浓度(r)随ti含量的增加而增加。673k等温线几乎是直线,但在623k时整个系列上的拐弯表明了接近但没有进入(α-氢化物+β-氢化物)两相区域的情况。根据菲克第一扩散定律,通过将测量的氢通量(j)除以氢浓度梯度(dc/dx)来计算v–ti–al合金中的平均氢扩散系数。由溶解氢的对应的进料表面(r1)和渗透物表面(r2)的浓度,计算与各通量测量值对应的浓度梯度。图6显示了673k和623k时各合金的氢扩散率随平均氢浓度的变化。在各情况下,存在强氢浓度依赖性,且dh随r的增加而增加。还存在明显的组成依赖性,其中对于给定的r,dh随ti含量的增加而降低。这些数据与观察到的ti依赖性吸收和ti非依赖性渗透性一致,因为吸收和扩散性趋势有效地相互抵消。晶粒细化由ti替代v具有增加氢吸收同时降低氢扩散性的效果。在合金膜发展的背景下,二者皆是对主体v90al10合金的性质的不利改性,并且与先前提到的减少吸收(以便使脆性相关的破坏降至最低)并使扩散率最大化(以便使渗透速率最大化而不引起机械损失)的目的相反。如图7所示,(a)v88ti2al10、(b)v86ti4al10、(c)v84ti6al10、(d)v82ti8al10和(e)v80ti10al10各自的电子显微图的比较显示出各合金仅包含单相,其中阴影的差别反映了不同的晶粒取向。此外,晶粒尺寸随着ti含量的升高而降低,其从2%ti时的>500μm降至10%ti时的约100μm。v90al10合金的微结构在过去的研究中被显示为具有约1000μm的晶粒尺寸。这些结果表明ti充当针对v、更特别是v-al合金的晶粒细化剂,减小vss相的晶粒尺寸。合金的选择在氢扩散率方面,上述结果表明了ni、cr、al和ti都明显降低了氢的扩散率。然而,不同于ti,cr、ni和al都降低了吸收,这给予了更大的脆化抗性。这表明三种具有前景的二元合金体系v-ni、v-al(也称为v-1)和v-cr(也称为v-2)可适用于合金cmr。对这些合金体系的适用性进行了更详细的研究。a.氢吸收减弱钒中的氢吸收从而提高强度的主要手段是合金化。本申请人已发现al、ni和cr给予有利的氢吸收性质,但ti没有。实际上,氢的吸收随着al、ni和cr含量的增加而降低,从而提高对氢脆化的抗性。al(v-1–v95al5)、ni(v95ni5)和cr(v-2–v95cr5)在400℃和10巴的p(h2)时对钒的氢吸收的效果比较在图8中示出。当被合金化至15at%时,各元素使吸收降低了50%~60%。b.质量输送氢能够被输送透过合金膜的透过速率受到膜厚度、温度、各表面吸收的氢浓度(其与合金组成和氢分压有关)以及氢渗透率的影响。图9显示了在400℃下所研究的三种v类合金的氢浓度和扩散率之间的关系。在每个所示的合金中,氢扩散率随着氢浓度的增加而增加。图上的曲线表示恒定的氢通量,即,具有较大的d和较低的h/m的合金与具有较小的d和较大的h/m的合金具有相同的性能。由于高氢吸收导致氢脆化和机械故障,而扩散率不招致机械损失, 所以理想的是扩散率/吸收曲线与朝向图左上角的虚线相交。基于此标准,v-al(v-1)合金是非常优异的,然后分别是v-cr(v-2)和v-ni合金。图10显示出ni、cr和al皆减少了吸收(表达为溶解的氢原子与金属原子之比,或h/m),并如图9所示降低了扩散率。虽然这降低了整体氢渗透性,但渗透性远高于pd的事实意味着在仍传递可接受的氢产率的同时可以容忍一定的渗透性降低。c.相稳定性金属氢化物可采用两种主要形式——α-氢化物(其具有并入间隙氢原子的体心立方结构)和β-氢化物(其具有并入间隙氢的体心四方结构)之一。这些相之间的晶格尺寸的显著差别在合金内造成了显著的应力,其可能表现出合金的起皱(最好情况)或碎裂(最坏情况)。因此,需要在操作过程中避免该相转变。当在诸如反应器停机期间从操作温度冷却至另一温度(如环境温度)时,合金膜最易受此相转变的影响。为了研究合金化条件对模拟停机期间钒的相稳定性的影响,如下所述,使用x射线衍射光束线单元对钒氢化物进行x射线衍射测量。材料和方法合金制备在水冷式铜炉上通过电弧熔炼由高纯度v、cr、ni和al制备致密的均匀v和v类合金(v90cr10、v90ni10、v90al10,以at.%表达)锭。针对衍射测量,利用放电加工将所述锭截成0.8mm的盘。在试验之前,将各样品抛光以去除残余的氧化物,电镀以500nm的pd以促进氢吸收速率,并且在400℃煅烧数小时以促进pd和钒合金之间的密合。将样品碾成粗粉末以用于衍射测量。针对吸收测量,从相同主锭上切割出1mm×3mm×10mm的片。衍射测量在两个单独的同步进程中进行衍射测量。在各进程期间,将样品装载到石英毛细管中并利用具有石墨套环的压力接头将其密封至静压样品池中。该样品池连接至能够用静态氢进行真空除气和增压的气体歧管。用热气送风机加热样品,该送风机在距毛细管壁3mm处垂直于x射线束安装。用nistsrm660a(lab6)校准x射线束波长和仪器参数,并且用pd作为热膨胀标准来校准温度。用等压系列进行测量,其中维持压力,并在若干步骤中温度从高达450℃降至30℃。每个系列的压力逐渐增加。如果在等压系列中检测到相转变,则装载新样品,然 后开始后面的系列。利用粉末衍射光束线在2012年6月期间于australiansynchrotron(墨尔本,澳大利亚)进行了最初的测量进程。用平行光束几何形状和mythenmicrostrip1d检测器进行v90ni10和v90al10合金的粉末衍射测量。所用波长为在测量期间,通过5°弧使0.7mm的od样品毛细管振荡。用极端条件(i15)光束线在2013年3月期间于diamondlightsource(harwell,uk)进行后续测量进程。使用平行光束几何形状和perkinelmer平板1621en检测器,用1.5mmod毛细管安装的样品进行v和v90cr10合金的粉末衍射测量。所用波长为在测量期间,通过30°弧使样品振荡。利用由brukeraxs出品的diffrac.topasrietveld型软件包对衍射图进行精化,从而确定了晶格参数。图11显示了在0.20mpa的压力和30℃~450℃的温度下钒的一系列x射线衍射图案。该图显示出钒在200℃~450℃时作为立方相存在,而在低于200℃时作为四方相存在,这通过(011)、(002)和(211)峰的分裂示出。这与所报导的钒氢化物的临界温度(tc)很好地匹配。对于0.20mpa时的v90cr10(图11b),200℃处指示的(020)和(211)峰的存在表示在200℃和300℃之间发生了转变。对于v90ni10(图11c),400℃处微弱存在的(020)和(211)峰表示此转变发生在略高于400℃的温度。v90al10(图11d)在所有条件下都维持了立方结构。图12中示出了相似的结果,图12显示了在从1巴氢气下的400℃冷却至1巴氢分压下的环境温度的过程中,(a)v90ni10(原子%)、(b)v95al5合金、(c)v和(d)v90al10的xrd图案。显然,v95al5和v90al10合金维持α-氢化物相直到降至30℃,而v-ni合金从300℃起形成β-氢化物相,并且对于纯v而言,从α-氢化物到β-氢化物的转变发生在190℃。类似的实验显示出v-cr(v-2)从200℃起结晶出β-氢化物。添加ni和cr皆可提高转变温度。添加10at%的al将转变温度降至小于30℃。这使膜可以在氢气气氛下经历热循环(例如,在含有具有该组成的合金膜的cmr的启动和停机期间)而不经受会造成破裂的相转变。如图11和12所示,显然v-al(v-1)合金是最佳的合金,因为其在所研究的30℃~400℃的温度范围内未经历相转变。d.氧含量氧含量小于0.15wt%。商业形式的钒含有显著水平的溶解氧。氧通过与溶解的氢 的反应可导致脆化。al和ti从钒中清除氧。e.成形性v类合金材料的成形性,特别是针对伸长率而言,决定了可用于生产扁平或管状膜的制造方法。例如,用于制造管状产品的合金在大批量生产中通常展现出25%~35%的最大伸长率(通过挤出和拉拔),而若采用变形加工,则伸长率为至少10%~20%。一个实例是每道次的变形减少且道次间有大量煅烧的变形加工。为了确定成形性,检查了所研究三种合金体系(v-ni、v-al和v-cr)的材料性质。还测试了v金属以构建这些合金的基准。进行了微结构表征和拉伸试验以测量这些合金在铸态和煅烧态的伸长率。f-1样品制备和试验在电弧炉或感应加热的冷坩埚炉中混合并熔化纯金属,并且使其在水冷式铜炉床上固化。所得锭是直径为50mm且长度为8mm~10mm(电弧熔炼)或50mm~100mm(冷坩埚熔炼)的圆柱形。随后通过弧线切割法从锭上切割出用于拉伸试验的试样。将这些试样在无氧气氛下于1250℃煅烧至多1小时。为了研究变形对v-ni合金的伸长率的影响,通过电弧熔炼和辊轧制造了0.4mm的v85ni15合金(at%)片。切割拉伸试样并在1250℃进行1小时的煅烧。以0.05cm/分钟的十字头速度、2kn的最大负载和8.5mm的规格进行拉伸试验。由于大部分合金过于脆以致不能记录屈服强度,所以仅测量了伸长率和uts。依照astme8/e8m进行了展延性测量。钒如表1所示,钒的最大伸长率为15%(3个样品的平均值)。表1:钒的伸长率和uts(3个单独的测量)组成条件uts(mpa)伸长率(%)纯v金属铸态,通过电弧熔炼铸造18114纯v金属铸态,通过电弧熔炼铸造20915纯v金属铸态,通过电弧熔炼铸造13616钒镍合金在钒中添加5~15原子%的镍导致展延性完全丧失,所记录的最大伸长率小于1%。通过电弧熔炼获得的样品的伸长率略高于冷坩埚铸造的情况,这可归因于电弧熔炼的合金的孔隙度低于冷坩埚熔铸的合金。表2:v-ni合金的伸长率和uts图13显示了热处理对所测量的冷坩埚铸造的v90ni10的伸长率的影响。在1000℃下历时1小时的煅烧减少了伸长率,这是由于不利于伸长率的二次相的沉淀。随着煅烧温度进一步增加至1250℃,伸长率恢复,但仍低于1%。v85ni15合金的辊轧样品实现了最高的伸长率,几乎为2%。然而,这仍可被描述为非常脆的合金。所研究的v-ni类合金具有非常低的展延性,这无法通过合金化、铸造、热处理和变形而得到显著改善。这严重地限制了此合金通过现有工业过程形成为合适的片材或管材的能力。v-al(v-1)合金如表3所示,v95al5(5%)和v90al10(10%)合金显示出远大于同等v-ni合金的伸长率。表3:v-1合金的伸长率和uts所研究的v-al类合金在具有5%al时具有充分的展延性,但在10%al时小于理想的展延性。该结果表明小于10%的al含量是合乎需要的,优选约5%的含量。此合金最适于通过现有工业过程形成片材或管材。v-cr(v-2)合金v-cr合金的机械性质在表4中示出:表4:v-cr合金的伸长率和uts所研究的v-cr类合金具有非常低的展延性,这无法通过合金化、铸造、热处理和变形而得到显著改善。这严重地限制了此合金通过现有工业过程形成为合适的片材或管材的能力。f.合金最佳性质在所研究的合金中,v-al合金明显提供了所需的氢渗透性、相转变和机械性质,显著优于所研究的其它二元合金体系(v-ni和v-cr)。具体而言,v-al类合金具有管材制造(例如通过管材拉拔、辊轧或挤出)所需的机械性质,而v-ni和v-cr合金对于此制造方法而言过脆。结合有利的渗透性,选择了v-al合金,因为其具有满足以上标准的出人意料的优异且最佳的性质,特别是相比于所研究的其它v合金而言。特别受关注的是v95al5合金体系,其相比于所研究的其它二元体系具有最佳的性质。注意,添加0~5%的晶粒细化元素(如ti、fe、ni或cr)改善了如上所述的成形性和微结构。g.v95al5的晶粒细化在添加和不添加晶粒细化剂的情况下分析v95al5合金的微结构。锭制备针对实验室规模的方法,在添加和不添加晶粒细化剂(b0.1ti0.7wt%)的情况下通过电弧熔炼生产v95al5合金锭。没有晶粒细化剂的锭的截面在图14中示出。具有晶粒细化剂的锭的截面在图15中示出。锭显示了两个不同的区域:晶粒垂直于锭表面的柱状区域;和晶粒在锭中央等轴生长的区域。用光学显微镜拍摄暴露的表面,并且分析所得图像以根据astme112确定平均长度截距。结果汇总在表5中。表5:添加和不添加晶粒细化剂的v95al5的晶粒尺寸v95al5合金具有1069微米的平均直线截距。在添加b0.1ti0.7(wt%)之后,合金的平均截距长度在具有等轴晶粒的区域中为171微米,而在具有柱状晶粒(垂直于晶粒生长方向)的区域中为173微米。制造合金膜管的方法利用本发明的合金制造管材需要进一步细化铸造合金的微结构。铸造及其它形成方法产生组成均匀但微结构不均匀(包括孔隙度)的合金。管材制造期间的合金的机械故障通常与孔隙的存在有关,并且与低伸长率有关,该低伸长率是由于较差的微结构造成的(例如晶粒尺寸的不均匀分布)。因此,满足需要的是以小晶粒尺寸和窄尺寸分布形成合金的微结构,并且使其具有最低的(或最小化的)孔隙度。此微结构增强合金的成形性,包括提高合金的展延性。管材生产是多步骤方法,首先包括制造具有所需的组成、微结构和尺寸的棒,然后将这些棒变形为所需的最终形状。用以下一般程序步骤实现晶粒尺寸的细化和更大的微结构均匀性:形成固溶体通式为v100-(y+z)alyxz的钒合金,其中x=ti、cr、fe、ni、b;y为>0~10;并且z为>0~5;并且在800℃~1500℃的温度和50mpa~500mpa的压力下热处理所形成的钒合金。随后如下所述,用管材变形方法(如辊轧、拉拔或挤出等)将精炼的钒合金形成为管材。锭制备第一步是用合适的铸造方法生产块体合金产品,例如锭。针对实验室规模方法,用逐层电弧熔炼生产25mm×25mm×100mm的锭200。通过此方法形成的一个试验锭的实例在图19中示出。应当明白可通过冷坩埚感应熔炼方法生产类似合适的锭。这产生了含有孔隙以及较大的非均匀晶粒结构的锭。合金均化下一步是通过将铸造的锭中的孔隙度最小化来提高合金的伸长率,并优化下游管制造中的微结构制备。这利用热等静压(hip)来实现,hip涉及在一段规定的时间内同时施加高温和压力,因而被用于赋予电弧熔炼的合金棒所需的特性。针对v-al合金的实验性hip运行的操作参数如下:·1200℃的温度;·200mpa的压力;·持续时间2小时;·5k/分钟的加热/冷却速度;和·氩保护气氛。如图20和21中最佳显示的,经hip的样品的确显示出孔隙度降低并且晶粒尺寸分布变得更均匀。图20提供了hip处理前的v-al合金的光学显微照片,示出了一些孔隙50。图21提供了hip处理后的v-al合金的光学显微照片。没有检测到明显的孔隙。此外,相比于铸态合金,经历了精炼的晶粒尺寸导致了更小的晶粒尺寸。●在hip处理之前,厚度为20mm的铸造v95al5合金的晶粒直线截距在平行于柱状生长方向上为15mm,在垂直于生长方向上为3.6mm(用astme112-113方法测定),并且存在大于0.3mm的空穴。●在hip处理之后,同一v95al5合金的晶粒直线截距在平行于生长方向上为3.0mm,在垂直于生长方向上为2.7mm(用astme112-113方法测定),并且不存在大于0.3mm的空穴。来自hip处理的晶粒直线截距减小据预期会使展延性增加至少1%,优选至少2%,更优选至少3%,还更优选至少4%,并且最优选至少5%。因此,本发明的v-al合金的展延性优选为至少10%,更优选至少12%,还更优选至少15%。已经发现hip工艺也导致了更加等轴的晶粒形状,其由于需要在更多的平面上滑移而固有地导致更高的强度和展延性。出于本发明的目的,等轴晶粒形状中,生长方向的晶粒直线截距与垂直于生长方向的晶粒直线截距之比为0.5:1.5至1.5:0.5,更优选为0.8:1.2至1.2:0.8。管状膜本发明的钒合金特别适合用作催化膜反应器(cmr)的催化合金膜。如上所述,合 金的组成和由此所得的性质已被优化以用于形成cmr的管状膜。图22中示出了典型的cmr100,其图示了水煤气变换催化剂106与h2选择性膜108的紧密耦合。图示的cmr100示意图示出了平板膜,其中co+h2+h2o进料101进给至反应器壳体104,催化剂106和膜108位于其间。进料101在催化剂106中经历水煤气变换(wgs)以产生残液110(h2耗尽的合成气)和h2渗透物112。还可对离开膜的h2使用可选的氮气吹扫102。作为放热反应,wgs反应在较低温度时是有利的,但反应动力学在高温下是有利的。为了克服此局限,商业wgs方法包括高温阶段(约450℃,用于实现快速动力学,其减小了所需的反应器尺寸)和低温阶段(约200℃,以使来自高温阶段的残留co的转化最大化)。cmr通过允许高温下的高wgs转化而使得可以消除低温反应器。当应用于煤衍生合成气的加工时,cmr可在单个装置中实现近乎完全的co至h2的转化、h2净化和燃前co2俘获。图23示出了可以包含由本发明的钒合金形成的管状膜的原型管状cmr200。管状cmr200在管状壳体204内并入了管状膜208,并且催化剂占据了壳体204内的环形空间。此构型的最大优点是密封区域减少,仅需在管的各端处(例如214)进行密封。再次,cmr200产生残液210(h2耗尽的合成气)和h2渗透物212。管状cmr也考虑到对现成管材和压缩配件的更大利用,这有助于简单且牢靠的组装。管状膜的制造鉴于显著减少的密封区域和更简单的构造,管状构型相比平面构型提供了明显的优点。当与钯合金膜相比时,钒类合金膜在制造中提供了进一步的优点。pd类膜必须非常薄以使成本最低化并使氢渗透最大化。这需要使用多孔的支持结构。v类合金的更高渗透性允许使用可自支持的更厚的膜。这大大降低了制造工艺的复杂性和成本。所需的合金管材期望具有以下尺寸:·直径(2mm~25mm);和·壁厚(0.05mm~1.00mm)。管状膜的制造利用拉伸变形,其对拉伸变形过程的材料形状尺寸和材料性质有如下要求:-用于变形过程的预成形材料必须以足够的尺寸铸造或烧结,例如,直径为25mm~50mm且高度为100mm~300mm的圆柱形。这对具有高熔点(至多2000℃)、 需要极高熔化能的v类合金而言是重大挑战,并且导致了与耐火围阻材料反应的趋势;以及-进料应具有足够的展延性。据认为,伸长率低于10%的材料可能不适合于旨在产生小管状膜的变形过程。如果满足了以上性质,则可采用制造小尺寸管状组件的标准生产流程,其包括棒铸、挤出和拉拔。所提出的v-al(v-1)合金的制造流程基于所研究的性质,对于迄今为止所研究的所有v类合金,v-al合金(特别是v95al5)具有最高的伸长率,因此其是通过优选的拉伸变形流程来制造管状膜的最佳候选。v-al管的一种制造流程如下:1).通过铸造或固态烧结方法生产预成形的合金棒,其具有25mm~50mm的直径和50mm~300mm的长度;2).煅烧合金棒以使展延性达到最大;3).将棒挤出为粗制管材;4).通过多重机械加工来拉拔粗制管材,从而以中间煅烧制成直径3/8”且壁厚≤0.2mm的管状膜;5).强化热处理;并且6).将管材切割至所需长度。通过此方法生产的膜管的目标尺寸是:-长度:≥1000mm;-外径:2mm~25mm,优选为9.52mm(3/8”);和-壁厚:0.05mm~1.00mm,优选≤0.200mm。催化表面合金膜通过溶解-扩散机制来工作,凭借此机制:·分子h2吸附在高压表面上并分裂成原子氢;·原子h溶于金属中并通过在金属晶格中的间隙位置之间跳跃而迁移,这由浓度梯度来驱动;并且·原子氢在低压表面上重新组合为h2并解吸附。钒形成牢固保持的氧化物层,其催化性较差并充当氢溶解的障碍物。优选将催化表面施加至合金膜以在膜进料表面实现足够的氢分子分裂反应速率。为了起到膜的作用,必须去所述除氧化物,并且必须施加最有名的h2解离催化剂——pd的薄层。本领域可理解,施加pd层需要用一系列机械和化学清洁步骤去除氧化物,然后用电镀或化学镀覆将pd沉积到该表面上。用于这些步骤的各种合适的工艺在本领域中已知。图24显示了v-pd界面的电子显微照片,其示出了钒310、钯涂层312和环氧树脂封固材料314的分层结构。最佳的pd层厚度为200nm~500nm。此pd层厚度提供了耐久性和成本间的良好折衷。一旦对所选择的管的内表面施加了pd层,则该膜管可用作催化膜反应器(cmr)中的h2选择性膜。反应器操作如前所述,选择本发明的合金组成以避免在操作期间的所述相转变。在这方面,如v-al相图所示,v-al合金中的转变温度是有利的,其可用来避免此相转变。相比之下,v-ni和v–cr合金中的转变温度不能使这些合金在所需的操作范围(0~500℃,并且h/m比大于0.05)内避免相转变。实际上,在以大于0.05的h/m比从约400℃的操作温度冷却至室温时,v、v-ni和v–cr合金的使用增加了脆性破坏。这可见于例如图25中所示的对用于避免v和v90al10的α至β的相转变所需的操作温度和h/m的比较。针对停机,v及其它v合金通常需要在停机前将氢吹洗并从金属上解吸附以将h/m比降至约0,而后可降低反应器中的温度。因此,这在停机期间需要两步工序。由于使用本发明的合金时在正常操作条件下可避免α至β的相转变,因此可避免此氢吹洗步骤。因此,使用由本发明钒合金形成的合金膜提供了能够在先前对于v及其它v合金不可行的条件下操作cmr的优点。具体而言,由本发明钒合金形成的合金膜能够以大于0.05的氢与金属(h/m)比和0~350℃的温度进行操作(参见图25)。这在反应器的多种操作条件(包括反应器的启动和停机)中是特别有利的,因为在以上操作条件中进行启动和停机工序时不需要考虑特别的温度或h/r。因此,这使反应器能够在例如20℃~30℃的室温至大约例如200℃~400℃的操作温度下启动,且膜不经历相转变。类似地,这使反应器能够在例如200℃~400℃的操作温度至例如 20℃~30℃的室温下停机,且膜不经历相转变。因此,膜可在操作温度和环境温度之间循环而不经历相转变,从而使反应器的停机简化。这使膜能通过多个操作循环而使用。停机期间脆性破坏的可能性被大大降低。应用主要应用是在高温氢选择性合金膜中。这些装置从还可含有h2o、co、co2、ch4和h2s的混合气流中分离氢。一个具体应用是使用氢选择性合金膜来生产h2并从气化的煤和生物质中俘获co2。其它可能的应用包括用于储存高纯度氢气的介质,其用于移动式或分布式发电的燃料电池、航空航天应用的电离辐射屏蔽以及作为热能储存介质。本领域普通技术人员将明白本文所述的方法易于进行除具体描述的那些之外的其它变型和修改。应理解本发明包括落在本发明主旨和范围内的全部此类变型和修改。当在本说明(包括权利要求书)中使用术语“包括”、“包含”或“含有”时,其应被解读为指定存在所提及的特征、整体、步骤或组分,但不排除存在一种或多种其它特征、整体、步骤、组分或其组合。当前第1页12