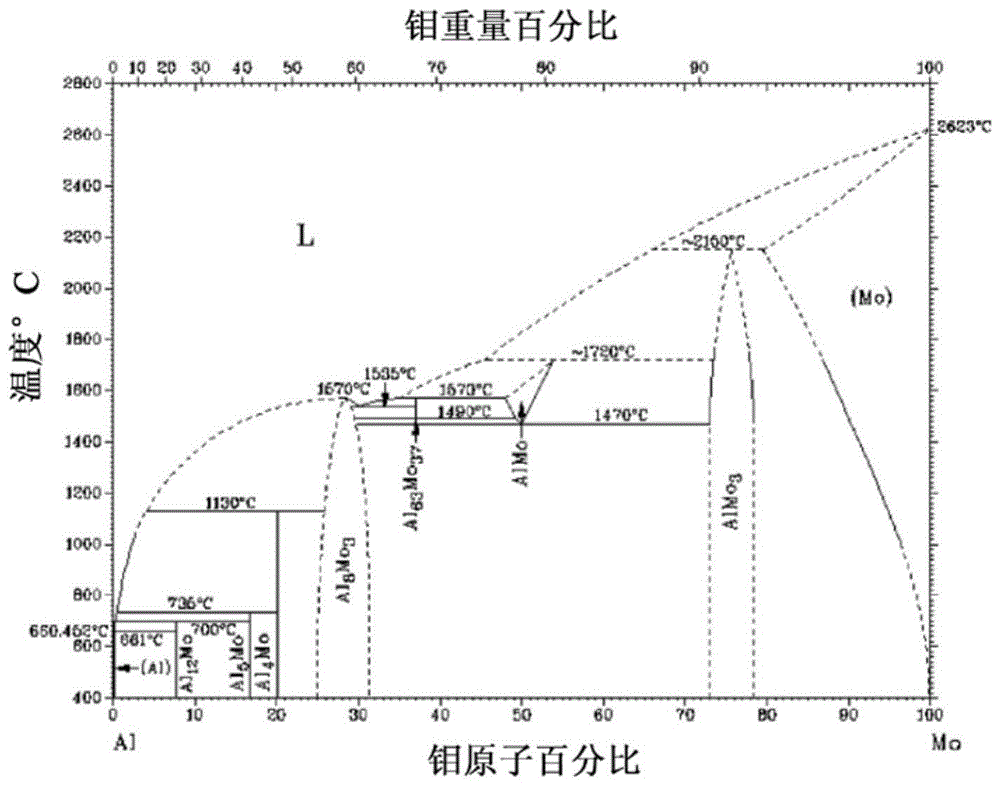
本发明涉及一种薄膜部件的金属镀层以及用于制造金属镀层的方法。本发明还涉及一种由Mo基合金组成的溅镀靶以及制造由Mo基合金组成的溅镀靶的方法。
背景技术:
:用于薄膜部件的金属镀层可通过适当溅镀靶的溅镀制得。溅镀,亦称为阴极雾化,为通过高能离子撞击而使原子从溅镀靶分离且转变成气相的物理方法。用于薄膜部件的金属镀层可为例如导电带及电极(例如薄膜晶体管(thin-filmtransistor;TFT)中的源电极、汲电极与门电极),并且用于诸多电子电气设备中,例如液晶显示器(liquidcrystaldisplay;LCD)或有机发光二极管(organiclight-emittingdiode;OLED)显示器;个人计算机(personalcomputer;PC)系统;或诸如移动电话、智能电话、平板PC、个人数字助理(personaldigitalassistant;PDA)、携带型音乐播放器、太阳能电池等行动设备。此类金属镀层的基本结构由至少一个用作例如导电带或电极的导电层组成。另外,已知该金属镀层的多层的实施方式。此类导电层可例如含有具有良好电导率的金属(例如Al、Cu、Ag或Au)或由其组成。特别为了改良对基层的黏着性,可在至少一个导电层与基层之间提供由Mo、W、Ti、Nb或Ta或基于这些金属中之一的合金组成的金属中间层。在一些应用中,该中间层当与半导体材料(例如Si(a-Si/非晶形Si或LTPS/低温多晶硅层))直接接触时,亦可满足扩散屏障的要求。此外,可另外提供由Mo、W、Ti、Nb或Ta或基于这些金属中之一的合金组成的覆盖层,其充当保护层(例如针对机械破坏、腐蚀、氧化、湿气)和/或用于邻接导电层或透明导电层(TCO,例如氧化铟锡)的扩散屏障。该金属镀层(所提供的通常为由Al、Cu、Ag或Au或基于这些金属中之一的合金组成的金属层的导电层以及任何中间层或覆盖层)通常借助于气相沉积方法(例如溅镀)制造,其中个别层的后续结构化借助于光刻与湿式化学或干式蚀刻法的组合进行。为了制造多层金属镀层,金属镀层的个别层具有类似蚀刻速率或能够在相同蚀刻介质中蚀刻为有利的。在此,蚀刻法可在一个步骤中进行,蚀刻介质不必定适于金属镀层的个别层结构化,并且因此可降低制造成本。除如所描述的足够电导率及有利蚀刻性能的外,此类金属镀层应具有其他特性。在含此类金属镀层的薄膜部件的制造制程期间,含氧氛围中可出现高温,例如在制造LTPS时或当需要空气中的中间热处理时。此可导致金属镀层的氧化且因此金属表面的变色,其又可导致电导率降低或在(自动)光学质量控制的情况下导致废品率增加。特定言的,行动设备在操作期间亦暴露于程度增加的不同环境影响(湿气等),且可能出现腐蚀或其他反应对金属镀层的破坏。再次,电导率可能降低且薄膜部件的功能可能受损。概言的,用于薄膜部件的金属镀层因此必须满足多种电学、化学及光学要求。金属镀层必须具有足够高的电导率(足够低的电阻)以及相对于待接触材料(例如半导体材料、透明导电氧化物(TCO))的极低过渡电阻。金属镀层应具有高抗氧化性以便防止制造制程期间的破坏。此外,金属镀层应具有高耐腐蚀性及耐外部影响性,同时需要金属镀层的极佳蚀刻性能(良好可蚀刻性)。另外,在多层金属镀层的情况下,为了降低制造成本,个别层的蚀刻速率应类似/相似。另外,金属镀层应能够充当针对硅扩散的扩散屏障。该金属镀层使用例如由借助于溅镀(例如磁控溅镀)剥蚀的适当金属或合金组成的溅镀靶制造。因此,已转变成气相的溅镀靶原子再次沉积于待涂布的基层上且形成对应层。由可用于在显示器中产生扩散屏障(Si与Al之间的扩散)的Al合金组成的溅镀靶描述于例如JP2011232654A中。Al合金层的对应用途亦已知,该Al合金层含有含≥30原子%Mo的Al-Mo合金或含Mo及元素X(其中X=(Mn、Nd、Ni、Mg及Fe))中的至少一种的Al-Mo-X合金的单层。然而,该合金层中的过高Al含量可导致该层不再适合作为扩散屏障,因为Al不适合作为针对Si的扩散屏障。另外,Al与Mo之间可能发生不期望的反应。同样已知由Al-稀土合金组成的溅镀靶,例如从US20120301732A1获知。该溅镀靶为具有组成Al-X-稀土金属的溅镀靶,如有必要进一步添加有Ni、Co、Cu、Ge。此处,X为选自组(Ta、Nb、Re、Zr、W、Mo、V、Hf、Ti、Cr及Pt)的至少一种元素且以0.1原子%至5原子%范围内的量存在。各个稀土金属以0.1原子%至4原子%的量存在。然而,含稀土金属的靶因高成本及有限可用性而为极其不利的。此外,借助于该靶所沉积的层作为扩散屏障的适合性因低含量的群X元素而为有限的。其不适于针对Si(与半导体材料接触)的扩散。为了确保良好溅镀特性(例如均匀的溅镀速率、层均质性、均匀层厚度),溅镀靶必须具有高的相对密度。低的相对密度在溅镀期间减小涂布速率且可导致粒子形成增加,其又可对溅镀层的特性(例如不良层均质性)及涂布方法(例如高电弧发生率、短路)具有不良影响。具有大于或等于98%或99%的高的相对密度的Mo-Al及W-Al合金溅镀靶描述于JP2000064033A及JP2000063971A中。然而,该溅镀靶仅含有3重量%至10重量%的Mo或W,且在微观结构中具有至少一种类型的金属间相(例如,MoAl12、MoAl5、MoAl4、Mo3Al8、MoAl及Mo3Al或WAl12、WAl5及WAl4)。然而,可存在于该溅镀靶的微观结构中的该金属间相可同样在溅镀期间导致粒子形成增加且对溅镀层的特性具有不良影响。术语金属间相指出现在二元、三元或多组分系统中的相,并且其存在范围不延续至纯组分。其时常具有不同于纯组分的晶体结构的晶体结构以及非金属接合类型组份。金属间相的特征主要在于不同价数的组成及有限的均质性范围,亦即化学计量的组成窄。金属间相时常为脆性的,亦即具有低韧度,其可随后对溅镀靶具有不良影响。如可从相图(图1)明显可见,二元系统Al-Mo中存在大量可能的金属间相。制造适用于沉积薄膜部件的金属镀层的溅镀靶可通过已知冶金途径或粉末冶金途径进行。经由粉末冶金途径制造Mo-W溅镀靶的实例描述于例如JP2005097697A中。其中描述了添加少量Al可改良Mo-W溅镀靶的烧结性。所指出的溅镀靶具有0.1重量%至70重量%的W含量及0.1重量%至50重量%的Al含量、余量的Mo,并且通过混合Al、W及Mo粉末、压制并在1300℃至1600℃下烧结来制造。以此方式制造的溅镀靶的微观结构在Mo-W合金粒子之间具有Al相区域。此外,一定组份Al在烧结期间溶解于Mo-W相中。所述烧结方法亦引发在烧结温度下形成液相及Al与Mo-W之间出现强不期望的反应的风险。经由粉末冶金途径制造溅镀靶的另一可能方式描述于WO2008137689A2中。其中,溅镀靶通过粉末或粉末混合物的动力喷涂或冷气喷涂制造,该粉末或粉末混合物由金属Nb、Ta、W、Mo、Ti、Zr、Cr、V、Mg、Sn、Pb、Al、Zn、Cu、Rh、Ag、Au、Co、Fe、Ru、Re、Ga、In及Sb中的至少一种组成。同样描述以此方式制造的溅镀靶用于沉积背面接触层或屏障层的用途。所述实例中之一为MoTi溅镀靶,其通过冷气喷涂制造且具有两相微观结构。由于冷气喷涂方法,因此Mo与Ti仍作为基本相;未出现相互扩散所致的合金化。然而,所述二元系统的缺点在于定制的所需特性组合仅可依有限范围设定。因此,同时达成高的耐腐蚀性及抗氧化性、极佳蚀刻性能以及作为扩散屏障的适合性是不可能的或仅在极大困难的情况下是可能的。由Mo、Ti或Ni合金组成并且以类似方式制造的溅镀靶描述于WO2014073633A1中。其中,还提供了适用于冷气喷涂的粉末或粉末混合物的参数。技术实现要素:因此,本发明的目标为提供一种用于薄膜部件的金属镀层,该金属镀层具有关于上述要求的极有利特性组合。此类金属镀层应为低成本的且具有高耐腐蚀性及抗氧化性、极佳蚀刻性能及作为扩散屏障的良好适合性的最佳组合。还应该提供一种用于该层的制造方法。本发明的另一目标为提供通过避免上述缺点的溅镀靶的描述的用途。此外,应提供一种适用于此类溅镀靶的制造方法,其以低成本及可再现方式确保溅镀靶的所需特性。通过权利要求独立权利要求达成该目的。从属权利要求中给出有利的设计方案。根据本发明的用于薄膜部件的金属镀层特征在于,其包含至少一个含Al以及Ti和常见杂质的由Mo基合金组成的层。,常见杂质指在金属镀层的情形下气体或伴随元素引起的制造相关污染,该气体或伴随元素可来源于沉积此类金属镀层所用的溅镀靶以及溅镀氛围。然而,金属性伴随元素的含量在选择性溅镀的情况下与其在所用溅镀靶中的含量相关,并且通常小于1000μg/g。C及气体(Ar、O、N)的含量视溅镀方法(所使用的方法参数、真空)而定,且可为至多若干原子%。此类金属镀层具有耐腐蚀性、抗氧化性及蚀刻性能的极有利组合。蚀刻性能在工业上使用的磷酸、硝酸及乙酸的混合物(PAN溶液)中测定,且在根据本发明金属镀层的情况下特别有利。Al含量及Ti含量的目标设定使待进一步优化的金属镀层达成耐腐蚀性、抗氧化性及蚀刻性能。作为扩散屏障的适合性亦可由Al及Ti含量的设定控制。根据本发明的金属镀层对最高350℃,在特别有利实施方式中甚至最高400℃的氧化具有抗性。出于本发明的目的,“抗氧化性(oxidationresistance)”为金属镀层表面在含氧氛围下在高温下的抗性。透明及保护性薄氧化物层的形成为有利的或在大多数情况下甚至是必需的,只要不存在对呈非均匀氧化形式的表面的相关破坏、氧化所导致的全区域或部分变色和/或光学特性改变。在此类有利情况下,金属镀层表面保持其初始金属光泽度,其可通过大致不变的表面反射率特性化。出于本发明的目的,透明及保护性薄氧化物层的该形成在低抗氧化性意义上不认为破坏。然而,当在含氧氛围下在高温下热处理此类金属镀层产生非均匀氧化、氧化所致的表面变色(在全区域或部分上)和/或反射率降低时,此金属镀层归类为“不抗氧化”。出于本发明的目的,“耐腐蚀性(corrosionresistance)”为金属镀层表面在高大气湿度下的抗性。为了对此进行测试,待检查的金属镀层在温度及湿度控制室中、在85℃及85%相对大气湿度中储存250小时及500小时。亦在此处,表面(在全区域及部分上)的变色和/或反射率降低归类为“不耐腐蚀”。不令人满意的抗氧化性与不令人满意的耐腐蚀性可导致金属镀层功能受到限制。出于本发明的目的,“反射率(reflectivity)”,亦称作反射系数,为反射光与入射光光通量的比。反射光光通量亦包括漫反射或背散射光。考虑人眼(在日光中,光视觉)的波长相关敏感度,其为特性化层的反射能力的亮度参数。为了测量所检查金属镀层的反射系数,使用550nm下的的反射系数R(%)作为第一近似值。在此波长下,人眼的敏感度(亮度敏感度,V-λ曲线)最大。使用PerkinElmerLambda950分光亮度计,使用W几何结构(VW测量附件)直接测量所有所检查的金属镀层的表面的反射率。此外,借助于电阻测量来检验所检查的金属镀层的抗氧化性及耐腐蚀性。在各情况下,使用4点法,借助于可购自JandelandaKeithleySourceMeter的4点测量头进行测量。此处,施加10mA恒定电流且测量电压的降低。为了达成不同金属镀层之间的极好可比较性,从所测量的电压降低来计算与金属镀层的厚度无关的表面电阻,从每个样本6个测量点计算平均值。金属镀层的电学表面电阻增加表示氧化或腐蚀所致的破坏。在单层金属镀层的情况下,亦可考虑层厚度,从其计算比电阻。虽然用于由Mo及Ti组成的Mo基合金的至少一个层的二元比较合金在25原子%及高于约25原子%的Ti含量下显示极好抗氧化性,但其极大缺点在于,其仅可借助于干式蚀刻法或在例外情况下在含氢氟酸的蚀刻水溶液中经蚀刻或结构化。这导致在制造含该金属镀层(例如与作为导电层的Cu组合)的薄膜部件时受到限制。Cu仅借助于干式蚀刻法蚀刻或结构化会出现极大的困难。用于由Mo及Al组成的Mo基合金的至少一个层的二元比较合金显示同等良好的耐腐蚀性及抗氧化性,以及更有利的蚀刻性能。然而,Al缺点在于,其在约400℃或高于约400℃的温度下与Mo反应而形成具有高电阻的金属间相。此外,由Mo及Al组成的Mo基合金层作为针对Si的扩散屏障的适合性仅为有限的。由于Al与Ti组合添加至由Mo基合金组成的至少一个层(其中Ti含量降低)中,因此可保持良好耐腐蚀性及抗氧化性且有时甚至改良,同时维持作为扩散屏障的适合性,且根据本发明的金属镀层另外在PAN溶液中显示改良的蚀刻性能。因此,根据本发明的金属镀层可容易经工业上习用的湿式化学蚀刻法蚀刻或结构化。另外,可在很大程度上抑制Mo与Al的不期望的反应。根据本发明金属镀层的由Mo基合金组成的至少一个层优选含有10原子%至40原子%Al及>0至15原子%Ti,其中Al及Ti的含量总和不超过50原子%。在大于15原子%Ti的含量时,工业上习用的湿式化学蚀刻法的可蚀刻性可能显著降低。10原子%及大于10原子%的优选Al含量对蚀刻性能具有极积极的影响。在约400℃的温度下,大于40原子%的Al含量增加与Mo的不期望的反应的风险。进一步优选地,根据本发明金属镀层的由Mo基合金组成的至少一个层含有15原子%至30原子%Al。15原子%至30原子%范围内的Al含量确保湿式化学蚀刻法中的进一步优化蚀刻性能,及本发明金属镀层的极佳耐腐蚀性及抗氧化性。进一步优选地,根据本发明金属镀层的由Mo基合金组成的至少一个层含有5原子%至10原子%Ti。已发现,就Mo与Al在约400℃下反应的减少而言,5原子%至10原子%范围内的Ti含量提供特别适合的金属镀层。此外,保持作为扩散屏障的良好适合性且存在极好蚀刻性能(良好可蚀刻性)。甚至进一步优选为根据本发明金属镀层的由Mo基合金组成的至少一个层中15原子%至30原子%Al与5原子%至10原子%Ti的组合。从制造观点(高抗氧化性、蚀刻性能)与用途观点(高耐腐蚀性、低电阻)来看,此组合引起本发明的用于薄膜部件的金属镀层的进一步优化。根据本发明金属镀层的由Mo基合金组成的至少一个层中Al及Ti的含量总和极尤佳大于或等于30原子%。在此情况下,Al及Ti的含量总和亦不超过50原子%。此范围中的Al及Ti含量产生在最高400℃的温度下维持的此层的抗氧化性。在优选实施方式中,根据本发明金属镀层的由Mo基合金组成的至少一个层由总共至多50原子%的Al及Ti、余量Mo和常见杂质组成。进一步优选地,根据本发明金属镀层的由Mo基合金组成的至少一个层由10原子%至40原子%Al及>0至15原子%Ti、余量Mo和常见杂质组成。甚至进一步优选地,根据本发明金属镀层的由Mo基合金组成的至少一个层由15原子%至30原子%Al及5原子%至10原子%Ti、余量Mo和常见杂质组成。根据本发明金属镀层的由Mo基合金组成的至少一个层的厚度优选不超过1μm,进一步优选不超过0.5μm。该厚度特别适用于对应薄膜部件中的该层。除由Mo基合金组成的至少一个层的外,根据本发明的金属镀层亦可具有一个或多个由一种或多种其他材料组成的其他层。借助于实例,图2在横截面中展示包含至少一个根据本发明的金属镀层2的薄膜部件结构。金属镀层2充当例如导电带或电极,为薄膜晶体管(TFT)的一部分。此外,所展示薄膜部件包含基层1,例如玻璃、塑料或硅。此类基层可全部或仅部分地预先涂有一个或多个由其他材料组成的层。此外,所描绘用于薄膜部件的金属镀层含有Mo基合金的至少一个层3。另外,可提供至少一个覆盖层(3、6)和/或中间层/扩散屏障(3,5)以及至少一个由Al、Cu、Ag或Au或基于这些金属的合金组成的金属层4。在优选变体中,金属镀层由多层,特别两层或三层组成。在根据本发明的金属镀层的这种优选实施方式中,除由Mo基合金组成的至少一个层的外,至少一个金属层由Al、Cu、Ag或Au或基于(其中“基于(baseon)”意谓合金的主要组分的成分以大于50原子%的量存在)这些金属中的一种的合金组成,因此可达成金属镀层的甚至更高电导率。由Mo基合金组成的至少一个层可已涂覆至由Al、Cu、Ag或Au或基于这些金属的合金组成的金属层的背对基层的一侧,且充当覆盖层以便确保金属镀层的耐腐蚀性及抗氧化性。图2b、2d及2e中展示此类金属镀层的实例。作为替代方案,由Mo基合金组成的至少一个层可已涂覆至由Al、Cu、Ag或Au或基于这些金属的合金组成的金属层的面向基层的一侧,且充当中间层,例如以便防止或限制基层与由Al、Cu、Ag或Au或基于这些金属的合金组成的金属层之间的扩散(扩散屏障)。图2c、图2d及图2f中展示此类金属镀层的实例。本发明金属镀层的另一优选实施方式提供覆盖层以及中间层/扩散屏障,其可在各情况下由如上文所描述的Mo基合金制成(图2d、图2e及图2f)。此处,在各情况下可提供相同类型3或不同类型的覆盖层6或中间层/扩散屏障5。视用于金属镀层的材料(例如其中存在的金属层4)及含对应薄膜部件的电子设备的区域扩展而定,优选使用如图2a至图2d中展示的结构。进一步优选为如图2d中展示的结构。根据本发明的用于薄膜部件的金属镀层最佳地适用于诸多电子设备中,例如液晶显示器(liquidcrystaldisplay;LCD)或有机发光二极管(organiclight-emittingdiode;OLED)显示器;个人计算机(personalcomputer;PC)系统;或诸如移动电话、智能电话、平板PC、个人数字助理(personaldigitalassistant;PDA)、携带型音乐播放器、太阳能电池等行动设备。根据本发明的用于薄膜部件的金属镀层优选用作导电带或电极。根据本发明的金属镀层优选用于液晶显示器(liquidcrystaldisplay;LCD)或(organiclight-emittingdiode;OLED)显示器中的薄膜部件。根据本发明的金属镀层优选借助于诸如物理气相沉积(physicalvapourdeposition;PVD)的已知薄膜涂布技术、通过沉积金属镀层的一个或多个层来制造。根据本发明的制造用于薄膜部件的金属镀层的方法包含至少以下步骤:-提供至少一种溅镀靶-沉积至少一个含Al及Ti和常见杂质的由Mo基合金组成的层-借助于至少一种光刻方法及至少一种后续蚀刻步骤使金属镀层结构化。借助于PVD方法,优选磁控溅镀方法,从至少一种溅镀靶将含Al及Ti的由Mo基合金组成的至少一个层涂覆至适合基层的至少50%表面上。至少一种溅镀靶可为例如根据本发明的由Mo基合金组成的金属溅镀靶,其含Al及Ti和常见杂质并且描述如下。然而,在根据本发明的制造用于薄膜部件的金属镀层的方法中亦可使用其他溅镀靶,例如多个由纯金属组成的溅镀靶。适合的基层为例如玻璃或聚合物膜。此类基层可全部或仅部分地预先涂有一个或多个由其他材料组成的层。根据本发明的金属镀层借助于至少一种光刻方法及至少一个后续蚀刻步骤进一步结构化及处理。至少一个蚀刻步骤优选使用工业上使用的磷酸、硝酸及乙酸的混合物(PAN溶液)进行,但亦有可能使用其他蚀刻溶液。通常重复该光刻方法与后续蚀刻步骤以便使根据本发明的金属镀层及视情况亦存在的其他层结构化。根据本发明的制造用于薄膜部件的金属镀层的方法可进一步包含以下步骤中的一个或多个:-涂覆一个或多个有机层-涂覆一个或多个透明导电氧化物(transparentconductiveoxide;TCO)层-涂覆一个或多个选自组(绝缘层、平坦化层、缓冲层)的层-激光处理-与保护膜或保护玻璃层层压-组装。如上文所陈述,根据本发明的含Al及Ti和常见杂质的由Mo基合金组成的溅镀靶可用于根据本发明的制造用于薄膜部件的金属镀层的方法中。根据本发明的溅镀靶由Mo基合金组成且其特征在于,其含有Al及Ti和常见杂质。常见杂质指由来源于所用原材料的气体或伴随元素产生的制造相关污染。根据本发明的溅镀靶中该杂质的组份优选对于C及气体(H、N、O)而言总计低于2000μg/g(对应于ppm),且对于其他元素而言总计低于500μg/g。适用于化学元素分析的方法已知视元素而定。使用光学发射光谱法与感应耦合电浆(opticalemissionspectrometrywithinductivelycoupledplasma;ICP-OES)、(X射线荧光分析X-rayfluorescenceanalysis;XRF)及辉光放电质谱分析(glowdischargemassspectrometry;GDMS),对根据本发明的溅镀靶进行化学分析。根据本发明的溅镀靶中的杂质组份优选对于C及气体(H、N、O)而言在低于1000μg/g的范围内,且对于其他元素而言在低于200μg/g的范围内。出于本发明的目的,表述Mo基合金指含至少50原子%Mo的合金。根据本发明的由Mo基合金组成的溅镀靶优选含有10原子%至40原子%Al及>0至15原子%Ti,其中Al及Ti的含量总和不超过50原子%。此类溅镀靶实现根据本发明的上述金属镀层,其含有以最佳方式沉积的适当Mo基合金的至少一个层。根据本发明的溅镀靶的用途优选为共溅镀多个靶,因为能够确保大面积基层上的层均质性更好。另外,Al及Ti的这种含量在溅镀靶中亦为有利的,因为其极大增加该靶的耐腐蚀性。从而使得此类溅镀靶的处理更容易且增加其在溅镀单元(其中溅镀靶与冷却介质(例如水)接触)中的使用期限。此外,根据本发明的溅镀靶优选特征在于其不含任何组份的可借助于X射线衍射(XRD)侦测的金属间相。出于本发明的目的,术语金属间相是指例如相图Al-Mo(图1)中的所有可能金属间相,其中同样包括例如三组分系统Mo-Al-Ti中的其他二元或三元相。可侦测组份的金属间相的出现可以简单方式通过记录X射线衍射图建立,在此情况下借助于Bruker的D4Endeavor衍射仪,使用Bragg-Brentano几何结构中的CuKa辐射。此方法中的常见侦测极限为约3体积%的相含量。根据本发明的溅镀靶微观结构中的金属间相特别因为可加工性受该相的通常高硬度及低韧度限制而为不期望的的。另外,金属间相可对溅镀性能具有不良影响,且例如为粒子或电弧来源。此亦降低沉积层的品质。根据本发明的溅镀靶进一步优选含有15原子%至30原子%Al。根据本发明的溅镀靶进一步优选含有5原子%至10原子%Ti。此范围中的Ti含量的另一优点在于使得通过冷气喷涂制造靶甚至更容易。Ti容易以粉末形式处理且可以极好及纯质量获得。根据本发明的溅镀靶甚至进一步优选含有15原子%至30原子%Al与5原子%至10原子%Ti的组合。根据本发明的溅镀靶甚至进一步优选含有大于或等于30原子%的Al及Ti的总组份。Al及Ti的含量总和亦不超过50原子%。在优选实施方式中,根据本发明的溅镀靶由总共至多50原子%的Al及Ti、余量Mo和常见杂质组成。进一步优选地,根据本发明的溅镀靶由10原子%至40原子%Al及>0至15原子%Ti、余量Mo和常见杂质组成。甚至进一步优选地,根据本发明的溅镀靶由15原子%至30原子%Al及5原子%至10原子%Ti、余量Mo和常见杂质组成。根据本发明的溅镀靶优选亦具有低于400HV10的硬度。当溅镀靶具有低于400HV10的硬度(根据DINENISO6507-1的维氏硬度(Vickershardness))时,可最佳地确保机械可加工性。根据本发明的溅镀靶优选具有大于95%的相对密度。大于97%的相对密度为特别有利的。如所知,相对密度可根据阿基米得原理(Archimedesprinciple),借助于浮力法,以简单方式测定。溅镀靶的相对密度愈高,其关于溅镀性能的特性愈有利。具有低相对密度的溅镀靶具有相对高组份的孔隙,该孔隙可为层中杂质及粒子的来源。此外,具有相对低密度的材料的溅镀速率低于具有高密度的材料的溅镀速率。根据本发明的溅镀靶在各种涂布设备中的安装以及用于涂布具有各种几何结构的基层的用途对根据本发明的溅镀靶提出各种几何要求。因此,此类靶可呈平坦靶形式,例如板或盘、棒、管状靶或具有复杂形状的其他物体。根据本发明的由Mo基合金组成的溅镀靶可借助于根据本发明的方法制造。根据本发明的制造由Mo基合金组成的溅镀靶的此类方法包含至少以下步骤:-提供含Mo以及Al及Ti的粉末混合物-冷气喷涂(CGS)粉末混合物至适合载体材料上。所提供粉末混合物可含有纯粉末或先前预合金化的粉末。所用粉末可单独或共同输送。因此,粉末混合物可先前或仅另外在用于冷气喷涂的设备中制备,例如在适当喷嘴中。冷气喷涂方法可特别适合通过分别输送粉末混合物的个别粉末来控制。溅镀靶制造期间的热能输入必须很低以致无法形成金属间相。在诸如热压制或热均压的替代性制造方法中,因高制程温度及保持时间而无法防止或仅不完全防止金属间相的形成。因此,通过该方法制造的毛坯通常具有过高硬度及低韧度,且仅在困难的情况下可以机械方式加工。此外,溅镀靶的微观结构中的金属间相可导致该靶的不利溅镀性能。适用于根据本发明的方法中的载体材料可呈例如板状或管状,且可由钢、Ti、Cu、Al或基于这些金属中的一种的合金制成。根据本发明的方法优选进一步包含以下步骤:-涂覆金属接合层为了改良借助于冷气喷涂涂覆至载体材料上的粉末混合物的黏着性,载体材料上可另外涂覆金属接合层(例如Al)。此类接合层对于具有相对高硬度的载体材料(Ti、钢)特别有利。此接合层可例如同样通过冷气喷涂来涂覆,但亦可设想其他可能性(例如其他喷涂方法、浆料涂布、包层、PVD方法、化学气相沉积(chemicalvapourdeposition;CVD)法)。根据本发明的制造溅镀靶的方法可进一步包含顺序与各别要求匹配的以下步骤中的一个或多个:-机械加工-热处理步骤-成型步骤-焊接(接合)至一种或多种载体组件上。对应机械加工可例如包含一种或多种车削、研磨或碾磨方法,其中可设定溅镀靶的所需尺寸和/或其表面粗糙度。在对应热处理步骤中,例如溅镀靶中的残余应力有可能耗散。此外,亦可设想诱导扩散方法,进一步改良对载体材料的黏着性。对应成型步骤可例如在平坦溅镀靶(平坦靶)的情况下通过滚轧实现,或在管状溅镀靶的情况下通过挤压实现。此类成型步骤可使得密度进一步增加以及微观结构进一步优化,且因此进一步改良溅镀靶的特性。根据本发明的溅镀靶可焊接至一种或多种载体组件上(接合)。出于此目的,可使用呈板或管或管段形式的适当载体组件。具有低熔点的焊接材料(例如In或In合金)优选用于此目的。具体实施方式实施例实施例1:在本发明实施例中,构建如图2a中展示的薄膜部件。在一系列实验中,制造由Mo基合金层组成的,具有不同化学组成的不同的金属镀层。从由纯钼、纯铝、纯钛及含10原子%Ti及20原子%Ti的Mo基合金组成的溅镀靶沉积层。通过共同溅镀2或3种不同溅镀靶来制造含Al及Ti的由Mo基合金组成的层。此处,经由组合不同溅镀靶及施加于溅镀靶的溅镀功率来改变层的化学组成。表1中展示所制造层的化学组成。为了确定由Mo基合金组成的层作为覆盖层的适合性,在玻璃基层(CorningEagle50×50×0.7mm3)上涂布由Mo基合金组成的层,并且随后测试其耐腐蚀性及抗氧化性。在抗氧化性测试中,在空气中在330℃下加热该层1小时。为了测试耐腐蚀性,样品在温度及湿度控制室中、在85℃及85%相对大气湿度下储存250小时及500小时。纯Mo、MoTi10及MoTi20充当参照材料。图3展示抗氧化性测试之后的不同的层。参照材料及由含8原子%Al及8原子%Ti的Mo基合金组成的层具有高度变色表面且因此具有低抗氧化性。图4展示耐腐蚀性测试之后的不同的层。在温度控制及湿度控制室中历时250小时之后,参照材料及含8原子%Al及8原子%Ti的由Mo基合金组成的层以及含9原子%Al及16原子%Ti的由Mo基合金组成的层均具有腐蚀破坏。500小时温度及湿度控制室测试的结果(参见图5)类似于250小时测试的结果。使用PerkinElmerLambda950分光亮度计,使用W几何结构(VW测量附件),在250nm至850nm波长下直接测量所有层的层表面上的反射率。结果同样概括于表1中。测量值与起始状态(“涂覆时”)之间的差异愈大,对表面的破坏愈大。人眼甚至可察觉大于3%的差异。由于可能用途的限制,在此实验中记下反射率相对于5%起始状态的降低量。表1:*表示根据本发明的特别有利实施方式抗氧化性测试之后及耐腐蚀性测试之后,在起始状态下测量层及参照材料的比电阻。选择如图2a展示中的结构以便能够确保比电阻的极精确测量。在各情况下,沉积层厚度为300nm。使用4点法,使用可购自JandelandaKeithleySourceMeter的4点测量头进行测量。此处,施加10mA恒定电流且测量电压的降低。从中计算层厚度内的比电阻。取每个样品6个测量点的平均值。结果概括于表2中。抗氧化性测试不显著影响所检查层的导电性(比电阻)。然而,高度腐蚀样品(耐腐蚀性测试)在表面上具有非均质测量值(无测量测量可能)直至绝缘处。与参照材料相比,具有高含量Al及Ti的样品显示显著改良的耐腐蚀性及抗氧化性。表2:*表示根据本发明的特别有利实施方式为了检查蚀刻性能,在40℃下,在含66%重量磷酸、10重量%乙酸、5重量%硝酸及水(余量)的搅拌PAN溶液中蚀刻在各情况下厚度为300nm的层。所用磷酸由85%浓度水溶液组成,硝酸由65%浓度水溶液组成,且乙酸为纯的(100%)。为了测定蚀刻速率,样品各自于蚀刻溶液中浸渍5秒,且随后用去离子水冲洗且干燥。随后,在精确天平上称量干燥样品。重复该步骤直至整个层溶解。自蚀刻时间内的质量减小量计算蚀刻速率(湿式蚀刻速率)。结果概括于表3中。所检查的所有层可在PAN溶液中蚀刻,蚀刻速率随Ti含量增加而大大降低。表3:*表示根据本发明的特别有利实施方式层组成(原子%)湿式蚀刻速率(nm/min)Mo1550MoTMO1443MoTi20208MoAlTi8-81154MoAlTi16-8*842MoAlTi24-6*611MoAlTi9-16180MoAlTi16-15*165MoAlTi24-14*140实施例2:在一系列实验中,制造含有含20原子%Al与5原子%Ti(MoAlTi20-5)、25原子%Al与5原子%Ti(MoAlTi25-5)及25原子%Al与10原子%Ti(MoAlTi25-10)的由Mo基合金组成的层的金属镀层。从具有对应化学组成的溅镀靶沉积层。为了测定由Mo基合金组成的层作为针对Si的扩散屏障的适合性,在Si晶圆(直径3吋,厚度380μm)上涂布由Mo基合金(层3,参见图2c)组成的对应层及各情况下的Cu层(金属层4,参见图2c)涂布。选择如图2c中展示的结构,因为额外层可有碍检视Cu层。由Mo基合金组成的层的层厚度为50nm,且Cu层的层厚度为200nm。为了测试由Mo基合金组成的层作为扩散屏障的适合性,在各种温度下在减压(10-5毫巴)下热处理金属镀层30分钟。纯Mo及含50原子%Al的Mo合金充当参照材料。当Cu层表面显示银变色且电学表面电阻显著增加时,不再确保层作为扩散屏障的适合性。此指示已形成由Cu及Si组成的金属间相。在涂布之后(起始状态)及热处理之后计算/测量电学表面电阻。使用4点法(市售的4点测量头)进行测量。结果概括于图6中。含20原子%Al及5原子%Ti的由Mo基合金组成的层在约650℃下损失其作为针对硅的扩散屏障的适合性。与在具有Mo层的参照样品的情况(700℃)下相比,此仅为非显著的低温。在层中Al含量较高的情况下(例如在含50原子%Al的Mo合金的情况下),作为扩散屏障的适合性在低至300℃下损失(图6)。由Mo基合金组成的层中的Ti含量增加可在合金中的Al含量相对高的情况下进一步改良作为扩散屏障的适合性(图6中MoAlTi25-5与MoAlTi25-10的比较)。因此,这些层满足作为扩散屏障的适合性,此为以最佳方式与增强的耐腐蚀性及抗氧化性的上述优点一起使用所必需的(参见实施例1)。实施例3:借助于冷气喷涂,将适用于冷气喷涂的商用Mo、Al及Ti粉末喷涂至作为载体材料的Al管上。粉末从单独容器输送。经由个别粉末的传输速率设定化学组成。图7中的横截面(扫描电子显微照相)中展示含20原子%Al及5原子%Ti的所得溅镀靶的微观结构。微观结构典型为通过冷气喷涂制造的材料,其纵向晶粒的较长轴平行于载体材料表面排列。如图8中的X射线衍射图展示,由于冷气喷涂,因此溅镀靶制造中未形成金属间相。此借助于Bruker的D4Endeavor衍射仪,使用Bragg-Brentano几何结构中的CuKα辐射记录。实施例4:在此实施例中构建如图2a中展示的薄膜部件。在一系列实验中,制造各含由Mo基合金组成的层,具有不同化学组成的各种金属镀层。从具有对应化学组成的溅镀靶沉积含Al及Ti的由Mo基合金组成的层。沉积含20原子%Al与5原子%Ti(MoAlTi20-5)、20原子%Al与10原子%Ti(MoAlTi20-10)、25原子%Al与5原子%Ti(MoAlTi25-5)及25原子%Al与10原子%Ti(MoAlTi25-10)的由Mo基合金组成的层。为了测定由Mo基合金组成的层作为覆盖层的适合性,在玻璃基层(CorningEagle50×50×0.7mm3)涂布由Mo基合金组成的层,且随后测试其抗氧化性。测试抗氧化性时,在空气中在400℃下加热该层1小时。图9展示测试之后的各种层。Al及Ti总组份大于或等于30原子%的由Mo基合金组成的层在最高400℃下不显示表面变色且因此具有抗氧化性。附图说明附图中示出了:图1:系统Al-Mo的相图(来源:ASMinternational'sBinaryAlloyPhaseDiagrams,第二版)。图2:在横截面中包含至少一种根据本发明的金属镀层的薄膜部件的可能结构。1:基层;2:金属镀层;3:Mo基合金组成的层;4:Al、Cu、Ag或Au或基于这些金属的合金的层;5:其他中间层/扩散屏障;6:其他覆盖层。图3:抗氧化性测试(在330℃下在空气中加热1小时)之后检查的层的表面照片。*表示根据本发明的特别有利实施方式。图4:耐腐蚀性测试(在85℃及85%相对大气湿度下、在温度及湿度控制室中历时250小时)之后检查的层的表面照片。*表示根据本发明的特别有利实施方式。图5:耐腐蚀性测试(在85℃及85%相对大气湿度下、在温度及湿度控制室中历时500小时)之后检查的层的表面照片。*表示根据本发明的特别有利实施方式。图6:经热处理的样品(位于硅基层上的50nmMo或Mo基合金层及200nmCu层)相对于热处理温度的表面电阻。图7:含20原子%Al及5原子%Ti的溅镀靶的扫描电子显微照片。影像下边缘的暗区域:由Al组成的载体材料。微观结构中的暗区域:Al及Ti。浅色区域:Mo。图8:含20原子%Al及5原子%Ti的溅镀靶的X射线衍射图。未能侦测到金属间相。图9:抗氧化性测试(在400℃下在空气中加热1小时)之后检查的层的表面照片。当前第1页1 2 3