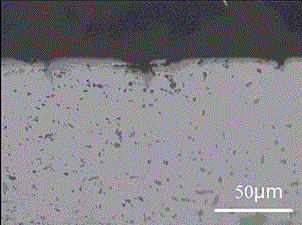
本发明属于有色金属
技术领域:
,涉及一种高强度、耐海水腐蚀的新型Al-Mg-Si合金材料及其制备方法。
背景技术:
:铝及铝合金因具有较低的密度、良好的力学性能、加工性能、导热性、导电性以及耐蚀性,已在船舶及船用设备中作为结构件和功能件而广泛应用,对减轻船体结构质量、提高航行速度和耐海水腐蚀能力、减少能耗等方面有着重要作用。船舶用材料要求具有高的抗拉强度、伸长率和抗冲击等力学性能,同时具有高的耐蚀性能。现今多选用具有中等强度的耐蚀可焊铝合金,如:5xxx系和6xxx系合金。根据其具体化学成分的不同,这些合金在海水环境下的应用性能也表现出较大的差异,但大多在力学性能能满足使用要求下,仍存在耐腐蚀性不足,影响服役寿命。为了解决目前船用5xxx系及6xxx系铝合金存在的问题,我们开发了一种新型的Al-Mg-Si合金,通过适当的调控Mg、Si在合金中的含量和Mg/Si比,并且加入微量元素Mn、Cr、Zr等,以改变含铁等有害相结构,消除不利影响,提高合金再结晶温度和腐蚀电位,细化晶粒,提升合金强度和塑形;另外Ag的加入能有效增强热处理强化效果,增加时效过程中强化相析出密度,提高合金力学性能,改变强化相元素原子百分比,降低析出相与基体电位差,提高合金的耐腐蚀性能。技术实现要素:本发明的目的是针对目前船舶用铝合金耐蚀性差,强度低的特性,提供一种既具有优异的耐海水腐蚀性能又具有高强度特点的Al-Mg-Si合金材料及其制备方法,从而满足船舶在复杂海面环境中的使用。为了实现上述目的,本发明公开了一种高强度、耐海水腐蚀Al-Mg-Si合金材料及其制备方法。本发明的目的是通过以下技术方案实现:1.一种高强度耐腐蚀的新型铝合金,其成分如下:Mg:1.8~3.6wt.%;Si:1.6~3.3wt.%;Mn:0.45~0.65wt.%;Cr:0.25~0.35wt.%;Zr:0.15~0.3wt.%;Ti:0.2~0.3wt.%;Ag:0.2~0.5wt.%;其它杂质单个≤0.03wt.%,总和≤0.1wt.%,余量为铝。2.一种Al-Mg-Si合金材料的制备方法,按如下步骤进行:步骤1:制备合金铸锭(a)熔化:在熔铸过程中,室温相对湿度要严格控制在40%以下,待铝块熔化50%左右时,加特制覆盖剂,随后按顺序加入Al-Mn中间合金、Al-Si中间合金、Al-Zr中间合金、Al-Cr中间合金,最后等熔体温度升到740℃时,加入铝箔包覆的Mg块,在中间合金熔化过程中,保证有覆盖剂覆盖在液面上,防止氧化,阻隔气体进入熔体;(b)除气、除渣:待中间合金完全熔化后,静置一定时间,当升温至720~740℃后,在熔体中分三次加入约为合金总质量0.6%的C2Cl6(具体步骤C2Cl6浸没于熔体中至无黄色气体冒出),主要是带走熔体中的H2气体除完之后,把熔体上漂浮的渣子全部扒出;(c)精炼:然后在720~740℃的温度下静置一定时间,保证熔体中的合金成分完全扩散均匀,无成分偏析存在;(d)浇注:加入Al-Ti中间合金,经搅拌,静置一定时间,降温至710-720℃,在水冷模中浇注成型。为了保证凝固期间金属液体能够畅通无阻地由冒口向铸件补缩流动,冒口与铸件之间必须形成楔形通道。步骤2:对合金铸锭进行均匀化处理对其进行均匀化处理,具体处理方法为在520-540℃的温度下,保温24-72h,然后冷却至室温。步骤3:轧制工艺控制具体操作为将均匀化处理后的合金铸锭在460℃条件下保温一定时间,之后热轧5道次,始轧温度为460℃,终轧温度不低于380℃,道次变形量需严格控制,第一、二道次加工率为10~15%,第三、四道次加工率为25~35%,第五道次加工率为20~25%。获得Al-Mg-Si合金板材。步骤4:对Al-Mg-Si合金板材进行热处理(a)固溶处理:将轧制后的Al-Mg-Si合金板材加热到520-530℃,保温4-12h,然后水淬至室温,其中淬火转移时间不大于25s;(b)两步时效处理:将固溶处理后的Al-Mg-Si合金板材升温190-240℃预时效0.2-2h,使合金形成一定的基体和高密度析出相的组织特点,之后150-160℃时效48-120h,扩大晶界与基体之间的扩散速率差,控制晶界析出相的长大,达到不牺牲合金力学性能的情况下消除海水腐蚀敏感性的目的。本发明的有益效果:1、本发明的高强度、耐腐蚀Al-Mg-Si系铝合金是在优化调整Mg、Si主要元素质量百分比和各元素配比,去除不利元素,并添加少量Ag元素后的合金,旨在不影响Al-Mg-Si合金时效析出序列的情况下,通过微合金化改善Al基体固溶体微结构及第二相的析出,利用镁银原子团簇的形成和Ag元素原子对β’和β’’等亚稳相中部分边界元素原子的替换,进一步增加和控制主要强化相的数量与分布,改变强化相化学活性和腐蚀电位,改善合金组织耐蚀性能。2、本发明通过优化加工和热处理工艺,实现在热加工制备板材的同时,调控组织,使β’’、β’和β-Mg2Si相及剩余Si细小、均匀分布,消除元素的偏聚与PFZ的形成,降低合金的腐蚀电化学动力,使得合金在强度上得到提升的同时,具有优异的耐腐蚀性能。新型铝合金除了具有良好的铸造性能和加工性能,可实现复杂构件的成形和加工及大规模工业化生产,同时具有很高力学性能及耐海水腐蚀性能,将极大提高我国军民船舶等耐蚀铝合金制件使用寿命。附图说明图1为本发明实施例1制得的合金与对比例合金的晶间腐蚀形貌。图2为本发明实施例2制得的合金与对比例合金的晶间腐蚀形貌。图3为本发明对比例3制得的合金与对比例合金的晶间腐蚀形貌。图4为本发明对比例4制得的合金与对比例合金的晶间腐蚀形貌。图5为本发明实施例1制得的合金与对比例合金的剥落腐蚀形貌。图6为本发明实施例2制得的合金与对比例合金的剥落腐蚀形貌。图7为本发明对比例3制得的合金与对比例合金的剥落腐蚀形貌。图8为本发明对比例4制得的合金与对比例合金的剥落腐蚀形貌。具体实施方式以下实施例旨在进一步说明本
发明内容,而不是限制本发明权利要求保护的范围。一种高强度耐腐蚀的铝合金,其特征在于包含以下成分:Mg:1.8~3.6wt.%;Si:1.6~3.3wt.%;Mn:0.45~0.65wt.%;Cr:0.25~0.35wt.%;Zr:0.15~0.3wt.%;Ti:0.2~0.3wt.%;Ag:0.2~0.5wt.%。其他杂质单个≤0.03wt.%,总和≤0.1wt.%,余量为铝。实施例1按照以下元素质量百分比进行配料:Mg:3.15%;Si:2.91%;Mn:0.6%;Cr:0.25%;Zr:0.25%;Ti:0.2%;Ag:0.4%;Fe≤0.01%。制备2mm厚板材。具体制备工艺:熔铸前先将铝锭、中间合金、坩埚分别在一定温度下预热一定时间,去除水分和杂质。在熔铸过程中,室温相对湿度要严格控制在40%以下,待铝块熔化50%左右时,加特制覆盖剂,随后按顺序加入Al-Mn中间合金、Al-Si中间合金、Al-Zr中间合金、Al-Cr中间合金,最后等熔体温度升到740℃时,加入铝箔包覆的Mg块,在中间合金熔化过程中,要保证有覆盖剂覆盖在液面上,防止氧化,阻隔气体进入熔体。待中间合金完全熔化后,静置10分钟,当升温至720~740℃后,在熔体中分三次加入约为合金总质量0.6%的C2Cl6(具体步骤C2Cl6浸没于熔体中至无黄色气体冒出),主要是带走熔体中的H2气体除完之后,把熔体上漂浮的渣子全部扒出。然后在720~740℃的温度下静置20-30min,保证熔体中的合金成分完全扩散均匀,无成分偏析存在。加入Al-Ti中间合金,经搅拌后静置15min,降温至710-720℃,在水冷模中浇注成型。然后对合金铸锭进行均匀化处理,处理工艺为在520-540℃的温度下,保温36h。均匀化处理后将合金铸锭在460℃下保温30min,之后热轧5道次,始轧温度为460℃,终轧温度不低于380℃,第一、二道次加工率为10~15%,第三、四道次加工率为25~35%,第五道次加工率为20~25%。轧制后的Al-Mg-Si合金板材进行固溶时效热处理,具体为在520-530℃下保温4h,然后水淬至室温,其中淬火转移时间不大于25s。随后在190-240℃预时效0.2h,最后在150-160℃时效72h,获得Al-Mg-Si合金板材。实施例2按照以下元素质量百分比进行配料:Mg:2.6%;Si:1.78%;Mn:0.48%;Cr:0.28%;Zr:0.25%;Ti:0.2%;Ag:0.3%;Fe≤0.01%。制备2mm厚板材。具体制备工艺:熔铸前先将铝锭、中间合金、坩埚分别在一定温度下预热一定时间,去除水分和杂质。在熔铸过程中室温相对湿度要严格控制在40%以下,待铝块熔化50%左右时,加特制覆盖剂,随后按顺序加入Al-Mn中间合金、Al-Si中间合金、Al-Zr中间合金、Al-Cr中间合金,最后等熔体温度升到740℃时,加入铝箔包覆的Mg块,在中间合金熔化过程中,要保证有覆盖剂覆盖在液面上,防止氧化,阻隔气体进入熔体。待中间合金完全熔化后,静置10分钟,当升温至720~740℃后,在熔体中分三次加入约为合金总质量0.6%的C2Cl6(具体步骤C2Cl6浸没于熔体中至无黄色气体冒出),主要是带走熔体中的H2气体除完之后,把熔体上漂浮的渣子全部扒出。然后在720~740℃的温度下静置20-30min,保证熔体中的合金成分完全扩散均匀,无成分偏析存在。加入Al-Ti中间合金,经搅拌后静置15min,降温至710-720℃,在水冷模中浇注成型。然后对合金铸锭进行均匀化处理,处理方法为在520-540℃的温度下,保温36h。均匀化处理后将合金在460℃下保温30min,之后热轧5道次,始轧温度为460℃,终轧温度不低于380℃,第一、二道次加工率为10~15%,第三、四道次加工率为25~35%,第五道次加工率为20~25%。轧制后的Al-Mg-Si合金板材进行固溶时效热处理,具体为在520-530℃下保温4h,然后水淬至室温,其中淬火转移时间不大于25s。随后在190-240℃预时效0.2h,最后在150-160℃时效72h,获得Al-Mg-Si合金板材。实施例1和实施例2所制备的Al-Mg-Si合金材料,对其进行室温拉伸试验、抗晶间腐蚀(按照GB/T7998-2005)和抗剥落腐蚀(按照GB/T22639-2008)测试。其中对比例3和对比例4为5A06(H116态,2mm厚板材)和6061铝合金(CS态,2mm厚板材)。实施例与对比例的力学性能和腐蚀性能详见表1,图1与图2分别为实施例与对比例的剥落腐蚀和晶间腐蚀形貌。从表1可以看出实施例的抗拉强度可达到370MPa以上,延伸率为12.0%以上,晶间腐蚀和剥落腐蚀分别为1级和N级。d(%)s0.2(MPa)sb(MPa)IGCEXC实施例112.313453951N实施例213.243153752N对比例3152703553PB对比例4122753103PA本发明中所描述的具体实施例仅是对本发明精神作举例说明。本发明所属
技术领域:
的技术人员可以对所描述的具体实施例做的修改或补充或采用类似的方式替代,但并不会偏离本发明的精神或者超越所附权利要求书所定义的范围。尽管对本发明已作出了详细的说明并引证了一些具体实施例,但是对本领域熟练技术人员来说,只要不离开本发明的精神和范围可作各种变化或修正是显然的。当前第1页1 2 3