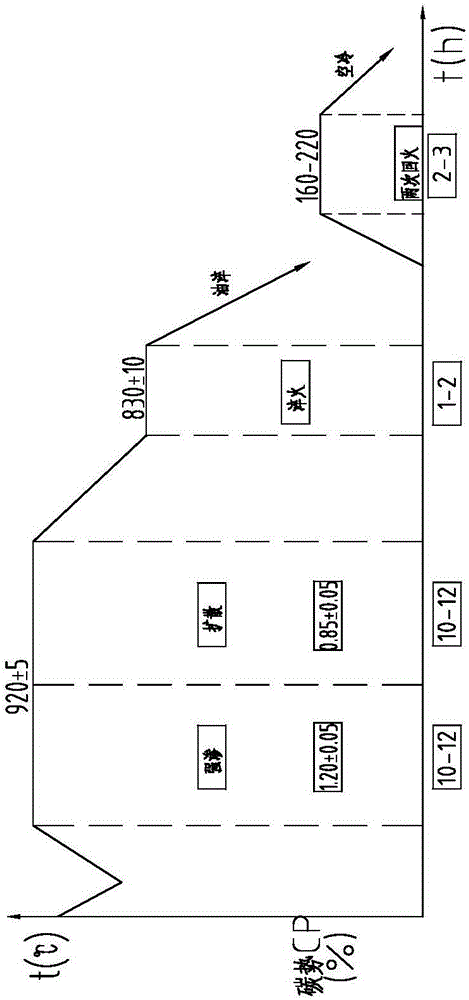
本发明涉及一种大型挖掘机齿轮的渗碳淬火方法,属于热处理
技术领域:
。
背景技术:
:挖掘机一般是由电力驱动,通过电动机运转做功与减速箱齿轮动力来实现连续作业的工程机械。随着我国在道路交通、能源水利、城市建设等各方面基础设施建设的迅猛发展,大型挖掘机市场需求量逐年上升,发展前景强劲。但是大型挖掘机工作环境比较复杂,减速箱内齿轮容易受到载荷冲击与机械振动的影响而失效。因此,大型挖掘机齿轮不仅承载重,冲击力强,而且安全性能要求高,使用时要求有优良的表面硬度、耐磨性能和抗过载能力,既要求齿轮齿面的硬化层深度较深,而且要求齿轮的心部力学性能良好。目前,大型挖掘机齿轮的原材料常采用18Cr2Ni4WA合金钢,渗碳淬火方法如图2所示,将大型挖掘机齿轮放置在渗碳炉内温度升高920±5℃,进行强渗10-12小时,在同温度下进行扩散10-12小时,在强渗时碳势CP控制在1.20±0.05%,而扩散时的碳势CP为0.85±0.05%,随后随炉降至830±5℃保温1-2小时后进行油淬火,再将齿轮放在回火炉中加热至160-220℃进行低温回火,保温时间为2-3h;然后出炉空冷至室温。该方法的渗碳温度低,强渗碳势高,炉内易沉积大量碳黑,导致炉内碳势波动,对碳势控制造成很大困难。同时,该方法渗碳时间长,且处在同一温度,由于钢中的Cr、W等碳化物形成元素会与碳形成稳定的合金碳化物,吸碳能力强,使渗碳层碳浓度升高,不利于碳元素的扩散,渗碳层浓度梯度变陡,易出现大块状、网状碳化物,破坏了基体组织的连续性,严重影响了渗碳层质量,使齿轮在后续磨削加工过程中易产生磨削裂纹,并使齿轮在周期性接触应力作用下易于疲劳,形成麻点和表层剥落。技术实现要素:本发明的目的是提供一种大型挖掘机齿轮的渗碳淬火方法,能大幅缩短渗碳淬火时间,获得高的渗碳速度,节约能耗,还能消除有害碳化物,获得弥散分布的细粒状碳化物,并提高生产效率。本发明为达到上述目的的技术方案是:一种大型挖掘机齿轮的渗碳淬火方法,其特征在于:包括如下步骤,⑴、升温均温步骤,先将齿轮置于渗碳炉内加热至750±10℃,保温3-4h;⑵、强渗步骤,渗碳炉升温,齿轮随炉加热至960-980℃,向渗碳炉内通入渗碳剂渗碳,控制碳势CP在1.30±0.05C%,维持一段渗碳时间t强渗;⑶、扩散步骤,渗碳炉升温,齿轮随炉加热至1040-1060℃,向渗碳炉内通入渗碳剂渗碳,控制碳势CP为0.90±0.05C%,且扩散时间t扩散是强渗时渗碳时间t强渗的1.5倍;⑷、降温均温步骤,降低炉温,齿轮随炉降温降至840±10℃,向渗碳炉内通入渗碳剂渗碳,在降温过程中维持炉内碳势CP在0.90±0.05C%,并保温2-3h,;⑸、一次淬火步骤,将840±10℃的齿轮进行油淬,且淬火油温度在65-95℃;⑹、等温球化退火步骤,将第一次淬火后的齿轮在炉内加热至650±10℃、保温3-4h;再将齿轮升温加热至720±10℃、保温3-4h;随后将齿轮降温至650±10℃、保温5-6h;最后齿轮随炉冷却至550℃,出炉空冷至室温;⑺、二次淬火步骤,将经过等温球化退火后的齿轮在炉内加热至760±10℃、保温3-4h;再将齿轮随炉升温至820±10℃、保温2-3h;然后将在820±10℃的齿轮进行油淬,淬火油温度为65-95℃;⑻、低温回火步骤,将齿轮放在回火炉中加热至180-260℃进行低温回火,保温时间为3-4h;然后出炉空冷至室温。其中,所述强渗步骤中的渗碳时间t强渗和扩散步骤中的扩散时间t扩散之和为总渗碳时间t渗碳,且总渗碳时间t渗碳=(δ/K)2,其中,δ为渗层深度(mm),K为渗碳温度系数。所述强渗步骤中的渗碳时间t强渗在8-10h。所述的扩散步骤中,扩散时间t扩散在12-15h。所述第一次淬火步骤与等温球化退火步骤之间,以及第二次淬火步骤与低温回火步骤之间还包括清洗步骤,清洗去除齿轮零部件表面油渍,清洗时清洗液的温度控制在50-60℃。所述强渗步骤、扩散步骤以及降温均温步骤中,采用的渗碳剂为甲醇、乙烷、丙烷、乙醇、丙醇、醋酸乙酯的任意一种或多种。所述强渗步骤、扩散步骤以及降温均温步骤中,所述碳势通过调节渗碳剂流量来控制。所述的低温回火步骤中,低温回火的次数为两次。所述大型挖掘机齿轮用钢材质为18Cr2Ni4WA。本发明将齿轮依次进行升温均温、强渗、扩散、降温均温、第一次淬火、等温球化退火以及第二次淬火,由于大幅提高了渗碳温度,且扩散温度高于强渗温度,扩散时间t扩散是强渗时渗碳时间t强渗的1.5倍,因碳渗入钢中的最大速度受碳在奥氏体中扩散速度的限制,而这种扩散速度与温度成正比例关系,因此,本发明渗碳淬火方法通过高的强渗温度和强渗碳势,在较短时间内即在工件表面形成了很高的碳浓度,通过更高的扩散温度和更长的扩散时间,使强渗段的富碳区的碳逐渐向深层推移,从而获得高的渗碳速度,缩短热处理时间,降低能耗,也能有效的平缓渗碳层的碳浓度梯度,降低齿轮表面渗碳层易出现的大块状碳化物,获得细粒状碳化物,改善齿轮表面的金相组织,提高齿轮的齿面硬度和耐磨性。本发明对渗碳后的齿轮进行等温球化退火,使其先在Ac1温度以上20℃奥氏体化,使碳化物充分溶解,然后在Ac1温度以下50℃发生等温转变,获得球化的弥散均匀分布的细颗粒碳化物,这种弥散分布的细颗粒碳化物在随后的淬火过程中,弥散度更趋完善,不仅为最终淬火加热准备了大量的结晶核心,而且可以使淬火加热奥氏体进一步均匀化,能够明显细化淬火组织,显著提高齿轮淬火后的强度、硬度等综合性能。本发明采用了两次加热淬火,能有效细化晶粒,对渗碳温度提高导致的晶粒长大起到了良好的优化作用。附图说明下面结合附图对本发明的实施例作进一步的详细描述。图1为本发明对大型挖掘机齿轮的渗碳淬火方法的工艺图。图2为现有技术对大型挖掘机齿轮的渗碳淬火方法的示意图。具体实施方式见图1所示,本发明的大型挖掘机齿轮的渗碳淬火方法,包括如下步骤。⑴、升温均温步骤,先将齿轮置于渗碳炉内加热至750±10℃,保温3-4h。⑵、强渗步骤,渗碳炉升温,齿轮随炉加热至960-980℃,向渗碳炉内通入渗碳剂渗碳,控制碳势CP在1.30±0.05C%,碳势通过调节渗碳剂流量来控制,维持一段渗碳时间t强渗,本发明强渗时的渗碳时间t强渗可控制在8-10h,通过提高强渗的温度和强渗碳势,在较短时间内即在工件表面形成了很高的碳浓度。⑶、扩散步骤,渗碳炉升温,齿轮随炉加热至1040-1060℃,扩散升温速度可控制在150-350℃/h,向渗碳炉内通入渗碳剂渗碳,控制碳势CP在0.90±0.05C%,且扩散时间t扩散是强渗时渗碳时间t强渗的1.5倍,同样碳势通过调节渗碳剂流量来控制,而扩散时间t扩散保持12-15h。本发明通过更高的扩散温度和长的扩散时间,使强渗段的富碳区的碳逐渐向深层推移,从而获得高的渗碳速度,也能有效的平缓渗碳层的碳浓度梯度,降低齿轮表面渗碳层易出现的大块状碳化物,获得细粒状碳化物,改善齿轮表面的金相组织,提高齿轮的齿面硬度和耐磨性。⑷、降温均温步骤,降低炉温,齿轮随炉降温降至840±10℃,降温速度可控制在120-240℃/h,向渗碳炉内通入渗碳剂渗碳,碳势通过调节渗碳剂流量来控制,在降温过程中维持炉内碳势CP在0.90±0.05C%,保温2-3h,以保持渗碳层的碳浓度,并通过控制淬火温度,以获得高质量的渗碳层。⑸、一次淬火步骤,将840±10℃的齿轮进行油淬,且淬火油温度在65-95℃,使奥氏体进行转变。⑹、等温球化退火步骤,将第一次淬火后的齿轮在炉内加热至650±10℃、保温3-4h;再将齿轮升温加热至720±10℃、保温3-4h;随后将齿轮降温至650±10℃、保温5-6h;最后齿轮随炉冷却至550℃,出炉空冷至室温。本发明对渗碳后的齿轮进行等温球化退火,可使碳化物充分溶解,然后在Ac1温度以下50℃发生等温转变,获得球化的弥散均匀分布的细颗粒碳化物。⑺、二次淬火步骤,将经过等温球化退火后的齿轮在炉内加热至760±10℃、保温3-4h;再将齿轮升温至820±10℃、保温2-3h;然后将在820±10℃的齿轮进行油淬,淬火油温度为65-95℃,本发明通过对等温球化退火后的齿轮进行再次淬火处理,使弥散分布的细颗粒碳化物在淬火过程中弥散度更趋完善,以使淬火加热奥氏体进一步均匀化,能够明显细化淬火组织,改善齿轮表面的金相组织,显著提高齿轮淬火后的强度、硬度等综合性能。⑻、低温回火步骤,将齿轮放在回火炉中加热至180-260℃进行低温回火,保温时间为3-4h;然后出炉空冷至室温。本发明的低温回火步骤中,低温回火的次数为两次,通过多次的低温回火,保持淬火工件的高硬度和耐磨性,降低淬火残留应力和脆性。本发明强渗步骤中的渗碳时间t强渗和扩散步骤中的扩散时间t扩散之和为总渗碳时间t渗碳,且总渗碳时间t渗碳=(δ/K)2,其中,δ为渗层深度(mm),K为渗碳温度系数,因此能根据设计要求设定齿轮的渗层深度以及选择的渗碳温度系数来控制总渗碳时间t渗碳。本发明在第一次淬火步骤与等温球化退火步骤之间,以及第二次淬火步骤与低温回火步骤之间还包括清洗步骤,清洗去除齿轮零部件表面油渍,清洗时清洗液的温度控制在50-60℃,而清洗液采用常规的清洗液,例如煤油等。本发明在强渗步骤及扩散步骤中以及降温均温步骤所采用的渗碳剂为甲醇、乙烷、丙烷、乙醇、丙醇、醋酸乙酯的任意一种或多种。本发明大型挖掘机齿轮采用钢材质为18Cr2Ni4WA,用本发明渗碳淬火方法对18Cr2Ni4WA制得的齿轮进行渗碳淬火处理,具体渗碳淬火处理实施例见表1所示。表1采用本发明的渗碳淬火方法制得的试件,按GB/T228、GB/T229标准进行检测,具体数据见表2所示。表2项目实施例1实施例2实施例3实施例4实施例5实施例6抗拉强度(MPa)145014801420142014501460屈服强度(MPa)950975955960955960断后伸长率(%)1413.51414.51413.5断面收缩率(%)585457595757可以看出,齿轮齿面的硬化层深度较深,而且要求齿轮的心部力学性能良好,具有优良的表面硬度、耐磨性能和抗过载能力。当前第1页1 2 3