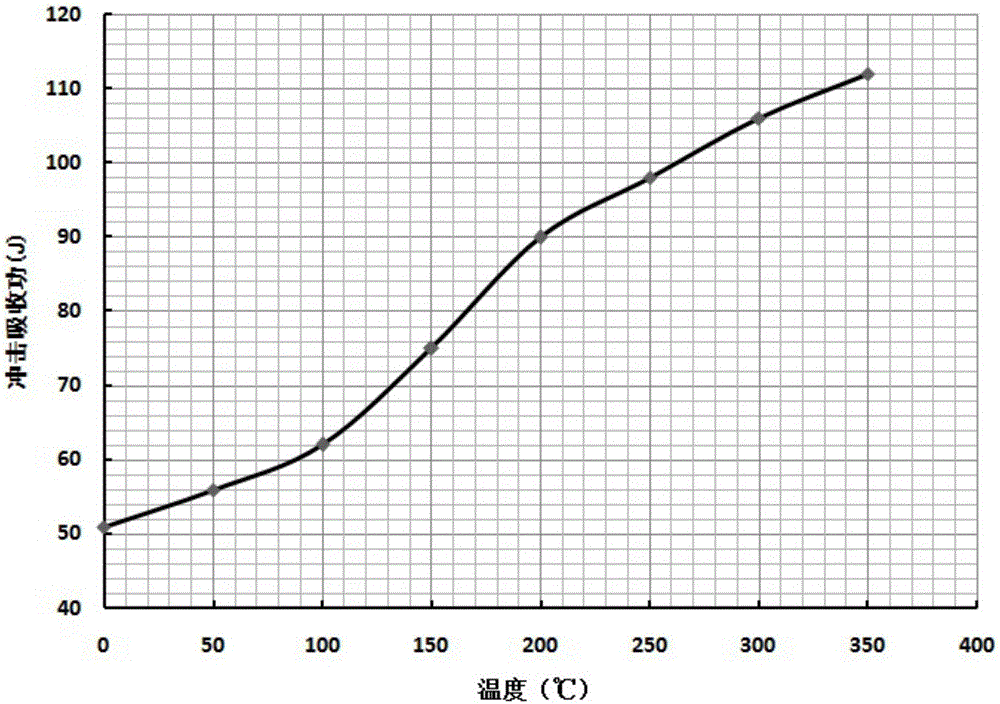
本发明涉及盾构机刀具的
技术领域:
,更具体地说,本发明涉及一种隧道盾构施工用滚刀刀圈。
背景技术:
:随着城市规模的不断发展和扩大,地铁已经成为解决大城市和特大城市交通问题的最优方式。现在全世界己有多个国家的多座城市修建了地铁,运营线路总里程已经达6000Km以上。虽然我国的地铁相比于西方国家起步较晚,但发展迅速,目前我国的地铁运营线路总里程已经达到3000Km左右,而且上海和北京的地铁运营线路里程已经位列城市排名的前两位,而且建设中以及筹划修建的地铁线路众多,发展势头强劲。在地铁隧道施工方法中,盾构法采用盾构机利用盾壳抵御围岩压力的情况下,由刀盘切削前方土体并运至后续运输系统,通过顶推千斤顶的推力自行前进,同时由快速组拼成环的钢筋混凝土管片形成隧道主体结构。由于作业面位于底面以下,盾构施工具有以下优点:对周围环境影响较小,施工中不会引起地下水位降低,而且开挖引起地表沉降较小;掘进速度较快;隧洞成型质量较好;施工环境较好,机械化程度高,具有人性化,噪音小,施工中支护衬砌质量可靠且造价较低;施工穿越河道不受影响,受天气影响较小;在土质差水位高条件下建设埋深较大的隧道,有较高的技术经济优越性。尤其是在现代地铁的隧道施工通常需要穿越建筑物高度密集的城市中心以及城郊地区,受限于城市地面空间条件,盾构施工几乎成了唯一的选择;在城市地下工程不断发展的今天,采用盾构法进行隧道施工越来越广泛,已经成为地铁隧道施工的主流技术。虽然,目前盾构施工法已经在城市地铁建造的主流方法,安装在刀盘上的滚刀是全断面盾构机破碎岩石的主要刀具,而刀圈是安装在滚刀刀体上的可拆的刀刃,是滚刀磨损的主要部位。目前刀具磨损而导致的耗费在隧道施工中占据大约20~30%的费用,而且刀具磨损到一定程度后,必须更换新刀具,而刀具更换必然耽误隧道施工时间,根据不完全统计,刀具更换的时间占总施工时间的比例在约5~25%之间。目前,国产刀圈对磨蚀性强的岩石地段施工的使用寿命低,为此现有技术中通常通过渗碳处理等手段来提高刀圈表面的硬度以期来提高滚刀刀圈的耐磨损性。技术实现要素:为了解决现有技术中的上述技术问题,本发明的目的在于提供一种隧道盾构施工用滚刀刀圈。为了解决发明所述的技术问题并实现发明目的,本发明采用了以下技术方案:本发明的隧道盾构施工用滚刀刀圈,包括圆盘形的刀圈本体,所述刀圈本体包括用于与刀毂焊接装配的台阶装配部以及用于切削的工作刃部,其特征在于:所述刀圈本体的外边缘通过等离子氮化形成有渗氮层。其中,所述刀圈本体由硬质合金钢经过锻造和热处理工艺制备得到,并且所述硬质合金钢的元素组成中含有0.46~0.55wt%的C、0.20~0.80wt%的Mn、1.5~3.5wt%的Cr、0.30~0.80wt%的Mo、0.32~0.80wt%的Cu、0.05~0.20wt%的V,余量为Fe以及不可避免的金属杂质和非金属杂质。其中,所述硬质合金钢的元素组成中含有0.48~0.53wt%的C、0.35~0.60wt%的Mn、1.8~3.0wt%的Cr、0.35~0.60wt%的Mo、0.35~0.60wt%的Cu、0.05~0.15wt%的V,余量为Fe以及不可避免的金属杂质和非金属杂质。其中,[Cu]/[Mo]的比值在1.0~2.0之间,[Cu]表示Cu的重量百分比,[Mo]表示Mo的重量百分比。其中,所述不可避免的非金属杂质包括Si、N、S、P和O,并且Si的含量≤0.20wt%,N的含量≤0.010wt%,P的含量≤0.010wt%,S的含量≤0.010wt%,O的含量≤20ppm。其中,所述不可避免的金属杂质包括Ti、Zr和Al,并且Ti的含量≤0.02wt%,Zr的含量≤0.02wt%,Al的含量≤0.05wt%。所述滚刀刀圈通过以下方法制备得到:首先,将合金原料组分进行配料,利用电弧炉冶炼和电渣重熔工艺制备钢锭,钢锭经过均质化处理后模锻并进行机加工,退火后得到刀圈本体毛坯;然后对刀圈本体毛坯进行软退火、等离子渗氮和热处理。其中,所述等离子渗氮在含氮气的气氛中进行,并且处理温度为420~580℃,氨气流量为20~200sccm,处理时间为10~200分钟。其中,所述热处理包括在1050~1100℃进行的高温淬火,并且随后在550~650℃进行的回火处理。与最接近的现有技术相比,本发明所述的地铁施工用盾构机刀具具有以下有益效果:本发明的地铁施工用盾构机刀具兼有优异的切削性能、耐磨性和高冲击韧性等关键性能指标,能显著提高刀具的使用寿命,从而有利于降低地铁隧道施工成本和建设周期。附图说明图1为本发明的地铁施工用盾构机刀具的结构示意图。图2为实施例5的滚刀刀圈硬质合金钢的吸收冲击功与温度的关系图。图3为硬质合金钢刀圈本体中Si含量与冲击吸收功的关系图。图4为硬质合金钢刀圈本体中Cu含量与冲击吸收功的关系图。具体实施方式以下将结合具体实施例对本发明所述的地铁施工用盾构机刀具做进一步的阐述,以期对本发明的技术方案做出更完整和清楚的说明。如图1所示,本发明的隧道盾构施工用滚刀刀圈,包括圆盘形的刀圈本体10,所述刀圈本体10包括用于与刀毂焊接装配的台阶装配部11以及用于切削的工作刃部12。所述刀圈本体10通常通过硬质合金钢制造而成,现有技术通常在硬质合金钢表面进行渗碳或者碳氮共渗,然而渗碳或碳氮共渗处理虽然可以提高表面硬度,但由于会析出较为粗大的碳化物或碳氮化物,在工作刃部对磨蚀性强的岩石进行掘进的过程中容易在工作刃部的两侧形成微裂纹并使得脆性断裂的概率大增。为此,本发明在刀圈本体10的外边缘通过等离子氮化形成有渗氮层13。所述等离子氮化形成的氮化层13能够为工作刃部12对磨蚀性强的岩石切削时所需要的耐磨性,为工作刃部两侧的磨损提供防护,从而提高滚刀刀圈的使用寿命。关于刀圈本体,现有技术通常采用硬质合金钢制成,通常采用的硬质合金钢有4Cr5MoSiV1、5Cr5MoSiV1、40CrNiMo、9Cr2Mo、6Cr4Mo2W2V等,本发明的发明人研究了上述钢,发现上述钢均不能满足对磨蚀性强的岩石切削掘进所需的高韧性和硬度,刀圈在岩石强烈冲击和摩擦的条件下,容易发生疲劳剥落从而导致脆性破坏。为此本发明的目的在于提供一种具有高韧性和与之匹配硬度的刀圈本体,具体来说其不仅应当具有高水平的韧性和延展性,同时也不得有损于回火稳定性和表面硬度。为此,本发明的刀圈本体加工用硬质合金钢其杂质含量应很低,不应含有任何粗大的初次碳化物,而且具有良好的淬透性和回火稳定性,同时还应具有良好的PVD涂覆性能和对刀毂良好的焊接性能。本发明的硬质合金钢具有均匀分布于钢基体上的弥散碳化物,这种组织结构有利于后续的热处理。在本发明中,所述硬质合金钢的基本组成如下:碳的含量控制在0.46~0.55wt%,优选为0.48~0.53wt%,例如可以为0.50wt%;锰的含量控制在0.20~0.80wt%,优选为0.35~0.60wt%,例如可以为0.36wt%;铬的含量控制在1.5~3.5wt%,优选为1.8~3.0wt%,例如可以为2.0wt%;钼的含量控制在0.30~0.80wt%,优选为0.35~0.60wt%,例如可以为0.42wt%;铜的含量控制在0.32~0.80wt%,优选为0.35~0.60wt%,例如可以为0.50wt%;钒的含量控制在0.05~0.20wt%,优选为0.05~0.15wt%,例如可以为0.15wt%;余量为Fe以及不可避免的金属杂质和非金属杂质,其中所述不可避免的非金属杂质包括Si、N、S、P和O,并且Si的含量≤0.20wt%,N的含量≤0.010wt%,P的含量≤0.010wt%,S的含量≤0.010wt%,O的含量≤20ppm;所述不可避免的金属杂质包括Ti、Zr和Al,并且Ti的含量≤0.02wt%,Zr的含量≤0.02wt%,Al的含量≤0.05wt%。在本发明的硬质合金钢中添加Cu在热处理后可以提高钢的硬度,如此可以弥补因Cr和Mo的添加量较少而导致的硬度损失,而同时Cu的加入还可以降低钢中位错阻力,有利于钢基体保持良好的韧性。添加的Cr、Mo和V在保证淬透性的同时,能够形成MC和M23C6的二次析出碳化物(纳米尺度范围),但如果Cr、Mo的含量超过本发明规定的上限时则有生成初次碳化物的风险,从而降低韧性和延展性。[Cu]/[Mo]的比值在1.0~2.0之间,[Cu]表示Cu的重量百分比,[Mo]表示Mo的重量百分比,将[Cu]/[Mo]的比例设置在上述范围有利于获得更高的韧性。Si通常被认为可以提高钢的固溶强化效果,并可以将晶界碳化物保持得很低,但Si的引入从整体上并不有利于韧性的提高,尤其是在切削加工过程中有形成裂纹的倾向,从而导致有发生剥离脱落的风险,为此在本发明中控制Si的含量在0.2wt%的水平以下,优选控制在0.15wt%即可,进一步降低Si的含量在经济上不利,而且也无必要。N是促进初次碳化物稳定形成的元素,如果在最终成品中含有这些初次碳化物,会导致冲击韧性急剧降低,为此在本发明中将N的含量控制在0.01wt%以下的水平,优选低于0.008wt%。O一般均认为是有害元素,其会导致热脆现象,即因热疲劳而导致的断裂现象,为此在本发明中O的含量控制在10ppm以下。S一般也被认为是有害元素,虽然其在有些情况下可用于提高钢的切割性能,但其对延展性不利而导致塑性降低,并且也会导致冲击韧性降低,为此最好将S的含量控制在0.01%的水平以下。P可能会引起偏析,严重降低塑性、冲击韧性和可焊性,尤其低温时发生冷脆,因此P含量不应超过0.01%。Ti、Zr和Al在钢中有可能于N结合形成初次氮化物和碳氮化物,这些氮化物和碳氮化物在热处理过程中很难去除,从而会对材料的冲击韧性有害,为此在本发明中应当将Ti的含量控制在0.02wt%以下,Zr的含量控制在0.02wt%以下,Al的含量控制在0.05wt%以下。本发明的滚刀刀圈可通过以下工艺制备:首先,将合金原料组分进行配料,利用电弧炉冶炼和电渣重熔工艺制备钢锭,钢锭经过均质化处理后模锻并进行机加工,退火后得到刀圈本体毛坯;然后对刀圈本体毛坯进行软退火、等离子渗氮和热处理。所述等离子渗氮在含氮气的气氛中进行,并且处理温度为420~580℃,优选为420~500℃,氨气流量为20~200sccm,处理时间为10~200分钟。本发明所述的硬质合金钢屈服强度(经过高温淬火和两次高温回火)可以达到1600~2000MPa,断裂伸长率为6.0~10.0%,硬度为45~58HRC,冲击韧性(V型缺口)在-20℃为30~45J。实施例1本实施例涉及滚刀刀圈的制备。该滚刀刀圈的制备包括以下步骤:①钢锭熔炼以滚刀刀圈的化学元素组成进行配料,配料后将原料放入电弧炉中进行熔炼,熔炼温度为1600±30℃,取样测试合金成分为:0.46wt%的C、0.50wt%的Mn、2.1wt%的Cr、0.52wt%的Mo、0.60wt%的Cu、0.12wt%的V、0.10wt%的Si、0.01wt%的N、0.01wt%的P、0.008的S、0.01wt%的Ti、0.008wt%的Zr、0.02wt%的Al,余量基本为Fe,开始浇注得到铸锭,然后经过电渣重熔得到钢锭。②锻造加工:均质化:在1260±20℃保温8~20小时,使合金元素充分扩散,成分均匀化。开锻温度:1150℃;终锻温度:850℃;锻造比6,多次镦粗拔长,经镦粗、冲孔、扩孔、模锻成型得到刀圈毛坯。③软退火将刀圈毛坯加热到900℃保温4~6小时,以0.5~1.0℃/min的冷却速度降温至750℃保温4h,炉冷至500℃出炉空冷至室温。④等离子渗氮将软退火后的刀圈毛坯放入离子氮化炉中,抽真空至1×10-3Pa,在处理温度为480℃,氨气流量为50sccm的条件下处理30分钟。⑤热处理将等离子渗氮后的刀圈毛坯升温到1100℃(加热时分阶段预热,先加热到750℃保温2小时,温度均匀后再升温到1100℃),保温2小时,油冷至室温,然后在加热炉中进行两次高温回火,每次的回火温度均为600℃(保温时间为2小时),得到本实施例的滚刀刀圈。实施例2本实施例涉及滚刀刀圈的制备。该滚刀刀圈的制备包括以下步骤:①钢锭熔炼以滚刀刀圈的化学元素组成进行配料,配料后将原料放入电弧炉中进行熔炼,熔炼温度为1600±30℃,取样测试合金成分为:0.53wt%的C、0.35wt%的Mn、1.8wt%的Cr、0.39wt%的Mo、0.55wt%的Cu、0.15wt%的V、0.12wt%的Si、0.01wt%的N、0.03wt%的P、0.008的S、0.01wt%的Ti、0.008wt%的Zr、0.02wt%的Al,余量基本为Fe,开始浇注得到铸锭,然后经过电渣重熔得到钢锭。②锻造加工:均质化:在1260±20℃保温8~20小时,使合金元素充分扩散,成分均匀化。开锻温度:1150℃;终锻温度:850℃;锻造比6,多次镦粗拔长,经镦粗、冲孔、扩孔、模锻成型得到刀圈毛坯。③软退火将刀圈毛坯加热到900℃保温4~6小时,以0.5~1.0℃/min的冷却速度降温至750℃保温4h,炉冷至500℃出炉空冷至室温。④等离子渗氮将软退火后的刀圈毛坯放入离子氮化炉中,抽真空至1×10-3Pa,在处理温度为480℃,氨气流量为50sccm的条件下处理30分钟。⑤热处理将等离子渗氮后的刀圈毛坯升温到1100℃(加热时分阶段预热,先加热到750℃保温2小时,温度均匀后再升温到1100℃),保温2小时,油冷至室温,然后在加热炉中进行两次高温回火,每次的回火温度均为600℃(保温时间为2小时),得到本实施例的滚刀刀圈。实施例3本实施例涉及滚刀刀圈的制备。该滚刀刀圈的制备包括以下步骤:①钢锭熔炼以滚刀刀圈的化学元素组成进行配料,配料后将原料放入电弧炉中进行熔炼,熔炼温度为1600±30℃,取样测试合金成分为:0.51wt%的C、0.63wt%的Mn、2.7wt%的Cr、0.32wt%的Mo、0.60wt%的Cu、0.13wt%的V、0.08wt%的Si、0.01wt%的N、0.03wt%的P、0.008的S、0.01wt%的Ti、0.008wt%的Zr、0.02wt%的Al,余量基本为Fe,开始浇注得到铸锭,然后经过电渣重熔得到钢锭。②锻造:均质化:在1260±20℃保温8~20小时,使合金元素充分扩散,成分均匀化。开锻温度:1150℃;终锻温度:850℃;锻造比6,多次镦粗拔长,经镦粗、冲孔、扩孔、模锻成型得到刀圈毛坯。③软退火将刀圈毛坯加热到900℃保温4~6小时,以0.5~1.0℃/min的冷却速度降温至750℃保温4h,炉冷至500℃出炉空冷至室温。④等离子渗氮将软退火后的刀圈毛坯放入离子氮化炉中,抽真空至1×10-3Pa,在处理温度为480℃,氨气流量为50sccm的条件下处理30分钟。⑤热处理将等离子渗氮后的刀圈毛坯升温到1100℃(加热时分阶段预热,先加热到750℃保温2小时,温度均匀后再升温到1100℃),保温2小时,油冷至室温,然后在加热炉中进行两次高温回火,每次的回火温度均为600℃(保温时间为2小时),得到本实施例的滚刀刀圈。实施例4本实施例涉及滚刀刀圈的制备。该滚刀刀圈的制备包括以下步骤:①钢锭熔炼以滚刀刀圈的化学元素组成进行配料,配料后将原料放入电弧炉中进行熔炼,熔炼温度为1600±30℃,取样测试合金成分为:0.48wt%的C、0.32wt%的Mn、1.8wt%的Cr、0.60wt%的Mo、0.60wt%的Cu、0.18wt%的V、0.10wt%的Si、0.01wt%的N、0.03wt%的P、0.008的S、0.01wt%的Ti、0.008wt%的Zr、0.02wt%的Al,余量基本为Fe,开始浇注得到铸锭,然后经过电渣重熔得到钢锭。②锻造:均质化:在1260±20℃保温8~20小时,使合金元素充分扩散,成分均匀化。开锻温度:1150℃;终锻温度:850℃;锻造比6,多次镦粗拔长,经镦粗、冲孔、扩孔、模锻成型得到刀圈毛坯。③软退火将刀圈毛坯加热到900℃保温4~6小时,以0.5~1.0℃/min的冷却速度降温至750℃保温4h,炉冷至500℃出炉空冷至室温。④等离子渗氮将软退火后的刀圈毛坯放入离子氮化炉中,抽真空至1×10-3Pa,在处理温度为480℃,氨气流量为50sccm的条件下处理30分钟。⑤热处理将等离子渗氮后的刀圈毛坯升温到1100℃(加热时分阶段预热,先加热到750℃保温2小时,温度均匀后再升温到1100℃),保温2小时,油冷至室温,然后在加热炉中进行两次高温回火,每次的回火温度均为600℃(保温时间为2小时),得到本实施例的滚刀刀圈。实施例5本实施例涉及滚刀刀圈的制备。该滚刀刀圈的制备包括以下步骤:①钢锭熔炼以滚刀刀圈的化学元素组成进行配料,配料后将原料放入电弧炉中进行熔炼,熔炼温度为1600±30℃,取样测试合金成分为:0.50wt%的C、0.36wt%的Mn、2.0wt%的Cr、0.42wt%的Mo、0.50wt%的Cu、0.12wt%的V、0.10wt%的Si、0.01wt%的N、0.03wt%的P、0.008的S、0.01wt%的Ti、0.008wt%的Zr、0.02wt%的Al,余量基本为Fe,开始浇注得到铸锭,然后经过电渣重熔得到钢锭。②锻造:均质化:在1260±20℃保温8~20小时,使合金元素充分扩散,成分均匀化。开锻温度:1150℃;终锻温度:850℃;锻造比6,多次镦粗拔长,经镦粗、冲孔、扩孔、模锻成型得到刀圈毛坯。③软退火将刀圈毛坯加热到900℃保温4~6小时,以0.5~1.0℃/min的冷却速度降温至750℃保温4h,炉冷至500℃出炉空冷至室温。④等离子渗氮将软退火后的刀圈毛坯放入离子氮化炉中,抽真空至1×10-3Pa,在处理温度为480℃,氨气流量为50sccm的条件下处理30分钟。⑤热处理将等离子渗氮后的刀圈毛坯升温到1100℃(加热时分阶段预热,先加热到750℃保温2小时,温度均匀后再升温到1100℃),保温2小时,油冷至室温,然后在加热炉中进行两次高温回火,每次的回火温度均为600℃(保温时间为2小时),得到本实施例的滚刀刀圈。比较例1与实施例5相比,不同之处在于本比较例的滚刀刀圈的化学元素组成为0.50wt%的C、0.36wt%的Mn、2.0wt%的Cr、0.51wt%的Mo、0.50wt%的V、0.10wt%的Si、0.01wt%的N、0.03wt%的P、0.008的S、0.01wt%的Ti、0.003wt%的Zr、0.02wt%的Al,余量基本为Fe。对实施例1~5以及比较例1得到的硬质合金钢滚刀刀圈的刃部以及内圈部进行取样,加工为20mm×20mm×10mm的试样测试其硬度。按照标准GB/T229-2007加工尺寸为10mm×10mm×55mm的冲击试样(V形缺口),利用冲击试验机测量刀圈材料在-20℃下的冲击吸收功,结果如表1所示。表1实施例1实施例2实施例3实施例4实施例5比较例1刃部硬度(HRC)565758575757芯部硬度(HRC)454747464648冲击吸收功(J)423335394312对实施例5制备的硬质合金钢滚刀刀圈的芯部取冲击试样(按照标准GB/T229-2007加工尺寸为10mm×10mm×55mm,V型缺口)测量其冲击吸收功与温度的关系,结果图2所示。比较例2与实施例5相比(Si含量为0.10%),不同之处在于Si的含量不同,在本比较例中Si的含量分别为0.30wt%,0.50wt%,0.60wt%和0.80wt%。对上述不同Si含量的滚刀刀圈,按照标准GB/T229-2007加工尺寸为10mm×10mm×55mm的冲击试样(V形缺口),利用冲击试验机测量刀圈材料分别在0℃和-20℃下的冲击吸收功,结果如图3所示。比较例3与实施例5相比(Cu含量为0.50%),不同之处在于Cu的含量不同,在本比较例中Cu的含量分别为0.20wt%,1.2wt%,1.5wt%,和1.8wt%。对上述不同Cu含量的刀圈本体,按照标准GB/T229-2007加工尺寸为10mm×10mm×55mm的冲击试样(V形缺口),利用冲击试验机测量刀圈材料分别在0℃和-20℃下的冲击吸收功,结果如图4所示。比较例4与实施例5相比区别在于采用气体渗碳步骤替代其中的等离子渗氮处理。气体渗碳在甲醇气氛中进行,渗碳温度为950℃,在碳势为1.2%C的条件下保温时间为3小时,降温至850℃,在碳势为1.1%C的条件下保温时间为2小时,然后空冷至室温。采用比较例4的滚刀刀圈对云母岩(SiO2含量为55~70wt%)进行掘进模拟实验,每开挖1000方岩石平均所消耗的上述刀具为6~12把,并且刀刃两侧的磨损较大。而采用实施例1~5的滚刀刀圈能够减少两侧的点磨损,每开挖1000方岩石平均所消耗的上述刀具减少为5~6把。采用本发明的滚刀刀圈发生断裂的概率显著降低,对失效的刀具进行表面处理并重新涂覆硬质防护涂层可以重新进行利用。对于本领域的普通技术人员而言,具体实施例只是对本发明进行了示例性描述,显然本发明具体实现并不受上述方式的限制,只要采用了本发明的方法构思和技术方案进行的各种非实质性的改进,或未经改进将本发明的构思和技术方案直接应用于其它场合的,均在本发明的保护范围之内。当前第1页1 2 3