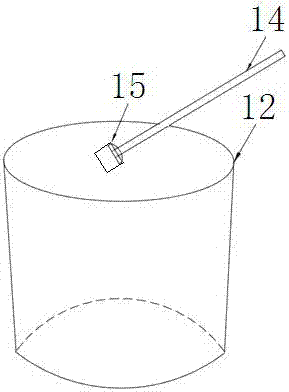
本发明涉及铁水预脱硫生产的领域,具体涉及一种HG铁水脱硫装置及其脱硫方法以及脱硫剂和扒渣器。
背景技术:
:随着特钢的发展,一些特殊钢种对钢水残余硫的要求越来越高,入炉铁水的深脱硫处理已是炼钢生产过程必须环节。目前铁水脱硫的两大主要方法为颗粒镁喷吹脱硫和KR搅拌脱硫。两种脱硫工艺相比:KR法具有很好的脱硫动力学条件而脱硫率高,脱硫剂价格低廉、安全。但因其脱硫粉料从铁水包上部加入,脱硫剂不能完全进入铁水,部分浮于渣面或者沾在搅拌头部,以及被除尘器吸走,存在一定量的浪费,难到达深脱硫,铁水温降大;颗粒镁喷吹法可以做到铁水的深脱硫,但脱硫后渣难扒易回硫,脱硫剂消耗量大等问题。技术实现要素:本发明的目的在于:克服现有技术的不足,提供一种HG铁水脱硫装置及其脱硫方法以及脱硫剂和扒渣器,通过搅拌管的搅拌杆的搅拌作用,不仅加强了脱硫的动力性条件,并且通过与脱硫剂喷管连通的搅拌管伸入铁水、以及搅拌管的搅拌杆的搅拌作用,使脱硫剂与铁水深度地、完全地、充分混合并反应脱硫,提高了脱硫剂的利用率,避免了脱硫剂的浪费,另外还防止了搅拌装置的结瘤;结合使用脱硫剂中的颗粒镁,可以有效快速的进行铁水深脱硫,缩短了脱硫时间和降低了铁水的温降,利于生产节奏控制;使用扒渣头可以很好的将脱硫渣从铁水包中扒取避免回硫,为后续工段钢水冶炼脱硫提供了有利条件,降低钢水脱硫石灰的消耗和冶炼时间;脱硫剂从脱硫剂料仓借助氮气的吹扫进入铁水中并使铁水翻腾,使得脱硫剂能够与铁水充分的接触,提高脱硫剂的脱硫效果;搅拌管的下管口包覆有耐火层,延长了搅拌管的使用寿命;通过氮气通入铁水是铁水翻腾和搅拌杆对铁水的搅拌,起到了双重搅拌效果,进一步使脱硫剂与铁水充分接触,提高脱硫剂的脱硫效果;脱硫剂加入的时间在2~3min的范围内,并且对脱硫剂中各成分的粒径进行限定,有利于脱硫剂中的各成分与铁水进行充分混合,提高脱硫剂的脱硫效果;所述支架包括下部的支撑部和上部的连接部,所述支架对称设于套管的两侧,形成“凸”字型结构,便于铁水包的周转。本发明所采取的技术方案是:HG铁水脱硫装置,包括支架,所述支架上设有脱硫剂喷管,所述脱硫剂喷管固定于套管内,所述套管与支架上下活动连接,所述套管的下方转动连接有搅拌管,所述脱硫剂喷管的一端与脱硫剂料仓连通,脱硫剂喷管的另一端与搅拌管的下管口连通,所述脱硫剂喷管内连通设有氮气管,所述氮气管的出气方向指向搅拌管的下管口,所述搅拌管位于下管口位置处的外侧管壁固定有搅拌杆,所述搅拌管与固定于套管外侧壁的旋转电机传动连接。本发明进一步改进方案是,所述套管通过上下行程小车与支架上下活动连接。本发明更进一步改进方案是,当上下行程小车位于最高行程处时,搅拌管的下管口和搅拌杆的所在高度高于铁水包的顶口;当上下行程小车位于最低行程处时,搅拌管的下管口和搅拌杆的所在高度低于铁水包内的铁水液面。本发明更进一步改进方案是,所述支架包括下部的支撑部和上部的连接部,所述支架对称设于套管的两侧,形成“凸”字型结构。本发明更进一步改进方案是,两侧支架的支撑部之间的距离大于或等于铁水包的外壁最大直径。本发明更进一步改进方案是,所述搅拌管的下管口为喇叭型结构,并且包覆有耐火层。本发明更进一步改进方案是,所述搅拌管通过旋转接头与套管转动连接。本发明更进一步改进方案是,所述搅拌管的外侧壁、位于旋转接头一端固定有齿圈,旋转电机下方的输出轴固定有与齿圈匹配的齿轮。本发明更进一步改进方案是,所述套管的上口与脱硫剂喷管的脱硫剂出料口之间密封。本发明更进一步改进方案是,所述脱硫剂喷管的脱硫剂出料口位于搅拌管内。本发明更进一步改进方案是,所述氮气管的出气口位于脱硫剂喷管内的脱硫剂出料口位置处。利用上述的HG铁水脱硫装置进行HG铁水脱硫的方法,包括以下步骤:1)将待脱硫操作的铁水包周转至搅拌管的正下方之后,脱硫剂喷管在套管的带动下沿支架向下移动,进行铁水取样、测温;2)测温达到脱硫条件后,脱硫剂喷管4在套管2的带动下沿支架1向下移动;3)当搅拌管的下管口即将与铁水包中的铁水液面接触时,打开氮气管的气阀;4)脱硫剂喷管在套管的带动下沿支架继续向下移动,直至搅拌管的下管口和搅拌杆伸入铁水包中的铁水内,达到预定插入深度后,启动旋转电机,使搅拌管转动;5)打开脱硫剂料仓的料阀,根据铁水中的含硫量加入脱硫剂,使脱硫剂借助氮气作为载体而进入铁水中;6)关闭脱硫剂料仓的料阀,并使氮气继续通入铁水内、并保持搅拌杆的继续搅拌直至完成铁水的脱硫;7)脱硫剂喷管在套管的带动下沿支架向上移动,当搅拌杆即将离开铁水时关闭旋转电机,当搅拌管的下管口刚离开铁水液面时,关闭氮气管的气阀;8)脱硫剂喷管在套管的带动下沿支架继续向上移动,直至移动至最高行程处;9)将铁水包周转至扒渣工位,并通过通过扒渣器将铁水包的铁水液面进行扒渣;10)扒渣结束后对铁水包中的铁水进行取样、测温;11)铁水测温结束后,将铁水包周转到下一工序。本发明更进一步改进方案是,所述步骤3)和步骤4)中,所述氮气管的氮气流量在90~110Nm3/h的范围内。本发明更进一步改进方案是,所述步骤5)中,所述脱硫剂加入的时间在2~3min的范围内。本发明更进一步改进方案是,所述步骤5)~步骤7)中,所述氮气管的氮气流量在50~80Nm3/h的范围内。本发明更进一步改进方案是,所述所述步骤4)中,所述搅拌管的下管口或搅拌杆伸入铁水包中的铁水内距离贴水液面1~1.5米范围内的深度。本发明更进一步改进方案是,所述步骤4)~7)中,所述搅拌管的转速在70~120r/min的范围内。本发明更进一步改进方案是,所述步骤1)和步骤11)中,所述铁水包通过周转小车进行周转移动。上述的HG铁水脱硫方法中所使用的脱硫剂,包括石灰粉粒、萤石粒和颗粒镁,所述石灰粉粒、萤石粒和颗粒镁的质量份数比为70~90:0~15:0~15。本发明更进一步改进方案是,所述石灰粉粒的粒径在0~1.0mm的范围内。本发明更进一步改进方案是,所述萤石粒的粒径在0~1.5mm的范围内。本发明更进一步改进方案是,所述颗粒镁的粒径在0.5~1.6mm的范围内。上述的HG铁水脱硫方法中所使用的扒渣器,包括扒渣头,所述扒渣头为弧面结构,所述扒渣头的弧面半径与铁水包的内壁半径相等。本发明更进一步改进方案是,所述扒渣头通过连接孔与扒渣器的操作杆固定连接。本发明更进一步改进方案是,所述扒渣头的下端向弧面的凹面一侧设有翻边。本发明更进一步改进方案是,所述翻边与扒渣头之间的夹角在150~175度的范围内。本发明的有益效果在于:第一、本发明的HG铁水脱硫装置及其脱硫方法以及脱硫剂和扒渣器,通过搅拌管的搅拌杆的搅拌作用,不仅加强了脱硫的动力性条件,并且通过与脱硫剂喷管连通的搅拌管伸入铁水、以及搅拌管的搅拌杆的搅拌作用,使脱硫剂与铁水深度地、完全地、充分混合并反应脱硫,提高了脱硫剂的利用率,避免了脱硫剂的浪费,另外还防止了搅拌装置的结瘤。第二、本发明的HG铁水脱硫装置及其脱硫方法以及脱硫剂和扒渣器,结合使用脱硫剂中的颗粒镁,可以有效快速的进行铁水深脱硫,缩短了脱硫时间和降低了铁水的温降,利于生产节奏控制。第三、本发明的HG铁水脱硫装置及其脱硫方法以及脱硫剂和扒渣器,使用扒渣头可以很好的将脱硫渣从铁水包中扒取避免回硫,为后续工段钢水冶炼脱硫提供了有利条件,降低钢水脱硫石灰的消耗和冶炼时间。第四、本发明的HG铁水脱硫装置及其脱硫方法以及脱硫剂和扒渣器,脱硫剂从脱硫剂料仓借助氮气的吹扫进入铁水中并使铁水翻腾,使得脱硫剂能够与铁水充分的接触,提高脱硫剂的脱硫效果。第五、本发明的HG铁水脱硫装置及其脱硫方法以及脱硫剂和扒渣器,搅拌管的下管口为喇叭型结构,有利于脱硫剂能够更好地扩散至铁水中、与铁水充分接触,提高脱硫剂的脱硫效果。第六、本发明的HG铁水脱硫装置及其脱硫方法以及脱硫剂和扒渣器,搅拌管的下管口包覆有耐火层,延长了搅拌管的使用寿命。第七、本发明的HG铁水脱硫装置及其脱硫方法以及脱硫剂和扒渣器,通过氮气通入铁水是铁水翻腾和搅拌杆对铁水的搅拌,起到了双重搅拌效果,进一步使脱硫剂与铁水充分接触,提高脱硫剂的脱硫效果。第八、本发明的HG铁水脱硫装置及其脱硫方法以及脱硫剂和扒渣器,脱硫剂加入的时间在2~3min的范围内,并且对脱硫剂中各成分的粒径进行限定,有利于脱硫剂中的各成分与铁水进行充分混合,提高脱硫剂的脱硫效果。第九、本发明的HG铁水脱硫装置及其脱硫方法以及脱硫剂和扒渣器,所述支架包括下部的支撑部和上部的连接部,所述支架对称设于套管的两侧,形成“凸”字型结构,便于铁水包的周转。附图说明图1为本发明的结构示意图。图2为扒渣操作的结构示意图。图3为扒渣头结构的放大示意图。具体实施方式如图1所示,本发明包括支架1,所述支架1上设有脱硫剂喷管4,所述脱硫剂喷管4固定于套管2内,所述套管2与支架1上下活动连接,所述套管2的下方转动连接有搅拌管3,所述脱硫剂喷管4的一端与脱硫剂料仓5连通,脱硫剂喷管4的另一端与搅拌管3的下管口10连通,所述脱硫剂喷管4内连通设有氮气管18,所述氮气管18的出气方向指向搅拌管3的下管口10,所述搅拌管3位于下管口10位置处的外侧管壁固定有搅拌杆11,所述搅拌管3与固定于套管2外侧壁的旋转电机9传动连接;所述套管2通过上下行程小车6与支架1上下活动连接;当上下行程小车6位于最高行程处时,搅拌管3的下管口10和搅拌杆11的所在高度高于铁水包12的顶口;当上下行程小车6位于最低行程处时,搅拌管3的下管口10和搅拌杆11的所在高度低于铁水包12内的铁水液面;所述支架1包括下部的支撑部和上部的连接部7,所述支架1对称设于套管2的两侧,形成“凸”字型结构;两侧支架1的支撑部之间的距离大于或等于铁水包12的外壁最大直径;所述搅拌管3的下管口10为喇叭型结构,并且包覆有耐火层;所述搅拌管3通过旋转接头8与套管2转动连接;所述搅拌管3的外侧壁、位于旋转接头8一端固定有齿圈,旋转电机9下方的输出轴固定有与齿圈匹配的齿轮(说明书附图未示出齿轮与齿圈);所述套管2的上口与脱硫剂喷管4的脱硫剂出料口之间密封;所述脱硫剂喷管4的脱硫剂出料口位于搅拌管3内;所述氮气管18的出气口19位于脱硫剂喷管4内的脱硫剂出料口位置处。结合图1~图3所示,利用上述的HG铁水脱硫装置进行HG铁水脱硫的方法,包括以下步骤:1)将待脱硫操作的铁水包12周转至搅拌管3的正下方之后,进行铁水取样、测温;2)测温达到脱硫条件后,脱硫剂喷管4在套管2的带动下沿支架1向下移动;3)当搅拌管3的下管口10即将与铁水包12中的铁水液面接触时,打开氮气管18的气阀;4)脱硫剂喷管4在套管2的带动下沿支架1继续向下移动,直至搅拌管3的下管口10和搅拌杆11伸入铁水包12中的铁水内,达到预定插入深度后,启动旋转电机9,使搅拌管3转动;5)打开脱硫剂料仓5的料阀,根据铁水中的含硫量加入脱硫剂,使脱硫剂借助氮气作为载体而进入铁水中;6)关闭脱硫剂料仓5的料阀,并使氮气继续通入铁水内、并保持搅拌杆11的继续搅拌直至完成铁水的脱硫;7)脱硫剂喷管4在套管2的带动下沿支架1向上移动,当搅拌杆11即将离开铁水时关闭旋转电机9,当搅拌管3的下管口10刚离开铁水液面时,关闭氮气管18的气阀;8)脱硫剂喷管4在套管2的带动下沿支架1继续向上移动,直至移动至最高行程处;9)将铁水包12周转至扒渣工位,并通过通过扒渣器14将铁水包12的铁水液面进行扒渣;10)扒渣结束后对铁水包12中的铁水进行取样、测温;11)铁水测温结束后,将铁水包12周转到下一工序。所述步骤3)和步骤4)中,所述氮气管18的氮气流量在90~110Nm3/h的范围内;所述步骤5)中,所述脱硫剂加入的时间在2~3min的范围内;所述步骤5)~步骤7)中,所述氮气管18的氮气流量在50~80Nm3/h的范围内;所述所述步骤4)中,所述搅拌管3的下管口10或搅拌杆11伸入铁水包12中的铁水内距离贴水液面1~1.5米范围内的深度;所述步骤3)~7)中,所述搅拌管3的转速在70~120r/min的范围内;所述步骤1)和步骤11)中,所述铁水包12通过周转小车13进行周转移动。上述的HG铁水脱硫方法中所使用的脱硫剂,包括石灰粉粒、萤石粒和颗粒镁,所述石灰粉粒、萤石粒和颗粒镁的质量份数比为70~90:0~15:0~15;所述石灰粉粒的粒径在0~1.0mm的范围内;所述萤石粒的粒径在0~1.5mm的范围内;所述颗粒镁的粒径在0.5~1.6mm的范围内。结合图2河图3所示,上述的HG铁水脱硫方法中所使用的扒渣器,包括扒渣头15,所述扒渣头15为弧面结构,所述扒渣头5的弧面半径与铁水包12的内壁半径相等;所述扒渣头15通过连接孔16与扒渣器14的操作杆固定连接;所述扒渣头15的下端向弧面的凹面一侧设有翻边17;所述翻边17与扒渣头15之间的夹角在150~175度的范围内。实施例11)将待进行脱硫铁水包12行进至搅拌管3的正下方之后,进行铁水取样、测温;2)测温结束后,脱硫剂喷管4在套管2的带动下沿支架1向下移动;3)当搅拌管3的下管口10即将与铁水包12中的铁水液面接触时,打开氮气管18的气阀,氮气流量为100Nm3/h;3)脱硫剂喷管4在套管2的带动下沿支架1继续向下移动,直至搅拌管3的下管口10和搅拌杆11伸入铁水包12中的铁水内,插入深度为1.25米。同时启动旋转电机9,使搅拌管3转动,并转动到正常工作转速在70~100r/min范围;4)打开脱硫剂料仓5的料阀,根据原始铁水硫含量从上料仓配加550kg脱硫剂(脱硫剂为石灰粒、萤石粒、颗粒镁质量份数比按照75:10:15的配比混合而成,其中石灰粉粒的粒径在0~1.0mm的范围内;所述萤石粒的粒径在0~1.5mm的范围内;所述颗粒镁的粒径在0.5~1.6mm的范围内)。脱硫剂借助氮气作为载体而进入铁水中,脱硫剂加入的时间为2min。从加脱硫剂开始,将氮气流量调整至70Nm3/h左右;5)关闭脱硫剂料仓5的料阀,并使氮气继续通入铁水内、并保持搅拌杆11的继续搅拌直至完成铁水的脱硫;6)脱硫剂喷管4在套管2的带动下沿支架1向上移动,当搅拌杆11即将离开铁水时关闭旋转电机9,当搅拌管3的下管口10刚离开铁水液面时,关闭氮气管18的气阀;7)脱硫剂喷管4在套管2的带动下沿支架1继续向上移动,直至移动至最高行程处;8)将铁水包12周转至扒渣位置;9)将扒渣器14行进至将铁水包12上方,对铁水液面进行扒渣。10)扒渣结束后进行铁水的取样、测温;11)铁水测温结束后,将铁水包周转到下一工序。具体生产过程脱硫数据如表1所示:表1各时间段数据实施例21)将待进行脱硫铁水包12行进至搅拌管3的正下方之后,进行铁水取样、测温;2)测温结束后,脱硫剂喷管4在套管2的带动下沿支架1向下移动;3)当搅拌管3的下管口10即将与铁水包12中的铁水液面接触时,打开氮气管18的气阀,氮气流量为110Nm3/h;3)脱硫剂喷管4在套管2的带动下沿支架1继续向下移动,直至搅拌管3的下管口10和搅拌杆11伸入铁水包12中的铁水内,插入深度为1.35米。同时启动旋转电机9,使搅拌管3转动,并转动到正常工作转速在80~110r/min范围;4)打开脱硫剂料仓5的料阀,根据原始铁水硫含量从上料仓配加600kg脱硫剂(脱硫剂为石灰粒、萤石粒、颗粒镁质量份数比按照75:10:15的配比混合而成,其中石灰粉粒的粒径在0~1.0mm的范围内;所述萤石粒的粒径在0~1.5mm的范围内;所述颗粒镁的粒径在0.5~1.6mm的范围内)。脱硫剂借助氮气作为载体而进入铁水中,脱硫剂加入的时间为3min。从加脱硫剂开始,将氮气流量调整至65Nm3/h左右;5)关闭脱硫剂料仓5的料阀,并使氮气继续通入铁水内、并保持搅拌杆11的继续搅拌直至完成铁水的脱硫;6)脱硫剂喷管4在套管2的带动下沿支架1向上移动,当搅拌杆11即将离开铁水时关闭旋转电机9,当搅拌管3的下管口10刚离开铁水液面时,关闭氮气管18的气阀;7)脱硫剂喷管4在套管2的带动下沿支架1继续向上移动,直至移动至最高行程处;8)将铁水包12周转至扒渣位置;9)将扒渣器14行进至将铁水包12上方,对铁水液面进行扒渣。10)扒渣结束后进行铁水的取样、测温;11)铁水测温结束后,将铁水包周转到下一工序。具体生产过程脱硫数据如表2所示:表2各时间段数据实施例31)将待进行脱硫铁水包12行进至搅拌管3的正下方之后,进行铁水取样、测温;2)测温结束后,脱硫剂喷管4在套管2的带动下沿支架1向下移动;3)当搅拌管3的下管口10即将与铁水包12中的铁水液面接触时,打开氮气管18的气阀,氮气流量为95Nm3/h;3)脱硫剂喷管4在套管2的带动下沿支架1继续向下移动,直至搅拌管3的下管口10和搅拌杆11伸入铁水包12中的铁水内,插入深度为1.3米。同时启动旋转电机9,使搅拌管3转动,并转动到正常工作转速在90~120r/min范围;4)打开脱硫剂料仓5的料阀,根据原始铁水硫含量从上料仓配加600kg脱硫剂(脱硫剂为石灰粒、萤石粒、颗粒镁质量份数比按照75:10:15的配比混合而成,其中石灰粉粒的粒径在0~1.0mm的范围内;所述萤石粒的粒径在0~1.5mm的范围内;所述颗粒镁的粒径在0.5~1.6mm的范围内)。脱硫剂借助氮气作为载体而进入铁水中,脱硫剂加入的时间为3min。从加脱硫剂开始,将氮气流量调整至70Nm3/h左右;5)关闭脱硫剂料仓5的料阀,并使氮气继续通入铁水内、并保持搅拌杆11的继续搅拌直至完成铁水的脱硫;6)脱硫剂喷管4在套管2的带动下沿支架1向上移动,当搅拌杆11即将离开铁水时关闭旋转电机9,当搅拌管3的下管口10刚离开铁水液面时,关闭氮气管18的气阀;7)脱硫剂喷管4在套管2的带动下沿支架1继续向上移动,直至移动至最高行程处;8)将铁水包12周转至扒渣位置;9)将扒渣器14行进至将铁水包12上方,对铁水液面进行扒渣。10)扒渣结束后进行铁水的取样、测温;11)铁水测温结束后,将铁水包周转到下一工序。具体生产过程脱硫数据如表3所示:表3各时间段数据工序时间铁水温度/℃硫含量/%铁水到站13260.049脱硫扒渣后13110.0014转炉出钢后/0.0103当前第1页1 2 3