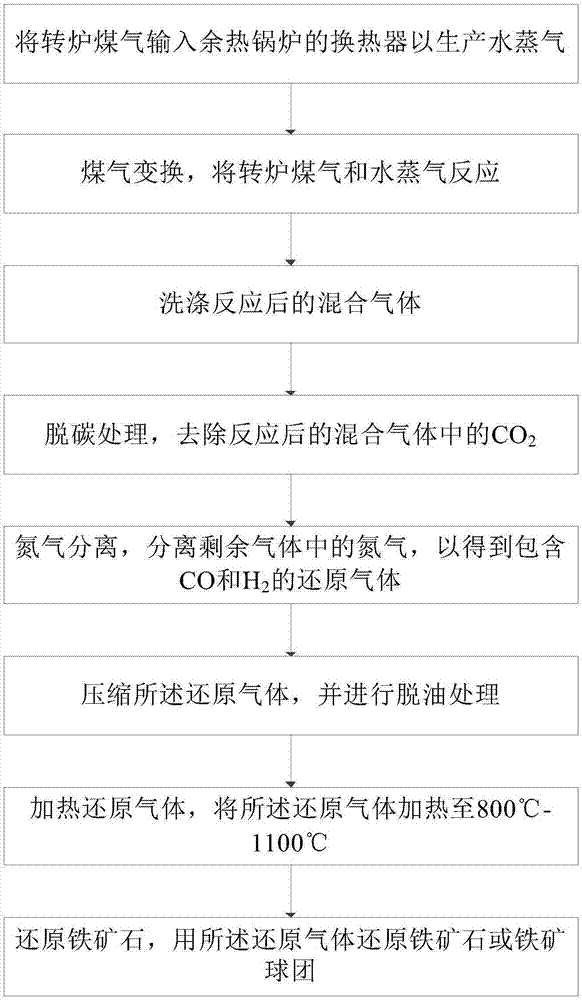
本发明属于煤化工
技术领域:
,具体而言,涉及一种转炉煤气利用系统和利用转炉煤气的方法。
背景技术:
:转炉炼钢在吹炼期间会产生大量煤气,其温度达1400℃-1600℃,转炉煤气中co的含量达到60-85%,其发热值达7mj/m3以上,由于煤气温度和co含量高,出炉口后遇到空气就立即燃烧。相关技术中,对转炉煤气的利用主要有以下几种方式:(1)将煤气随意燃烧后经降温、除尘后放散,这种方式不仅浪费了大量资源还会造成严重的环境污染;(2)煤气回收利用,比如分离co2富集co,co的分离复杂,会残余大量的n2,且co仅作燃料,应用范围窄,可回收的煤气量少,即吨钢回收煤气只有70m3,单位发热值只有5mj/m3左右。技术实现要素:本发明旨在至少解决现有技术中存在的技术问题之一。为此,本发明提出一种转炉煤气利用系统,所述转炉煤气利用系统可以有效地利用转炉煤气进行还原铁的生产。根据本发明实施例的转炉煤气利用系统,包括:转炉、锅炉和转化炉,所述转炉的排气口与所述锅炉的出气口均与所述转化炉相连;脱碳塔,所述转化炉的出口与所述脱碳塔的进口相连;氮气分离装置,所述脱碳塔的出口与所述氮气分离装置的进口相连;气基直接还原装置,所述氮气分离装置的出口与所述气基直接还原装置的进气口相连。根据本发明实施例的转炉煤气利用系统,将转炉煤气通过变换、脱碳、去氮工艺后用于气基直接还原,实现了转炉炼钢与气基直接还原装置的耦合,既可经济有效地利用转炉煤气,又可降低气基直接还原装置的投资,降低直接还原铁的生产成本。根据本发明一个实施例的转炉煤气利用系统,所述锅炉为余热锅炉,且所述转炉的排气口通过排气管与所述余热锅炉的换热器相连,且换热后的转炉煤气输入所述转化炉。根据本发明一个实施例的转炉煤气利用系统,还包括:洗涤塔,所述洗涤塔串联在所述转化炉的出口与所述脱碳塔的进口之间。根据本发明一个实施例的转炉煤气利用系统,所述脱碳塔内放置有碱性溶液。根据本发明一个实施例的转炉煤气利用系统,还包括:加热炉,所述加热炉连接在所述氮气分离装置与所述气基直接还原装置之间。根据本发明一个实施例的转炉煤气利用系统,还包括:压缩机和去油装置,所述压缩机的进口与所述氮气分离装置的出口相连,所述压缩机的出口与所述去油装置的进口相连,所述去油装置的出口与所述加热炉的进口相连。本发明还提出了一种使用上述任一种转炉煤气利用系统来利用转炉煤气的方法,包括如下步骤:煤气变换,将转炉煤气和水蒸气反应;脱碳处理,去除反应后的混合气体中的co2;氮气分离,分离剩余气体中的氮气,以得到包含co和h2的还原气体;还原铁矿石,用所述还原气体还原铁矿石或铁矿球团。根据本发明一个实施例的转炉煤气利用系统,在所述步骤煤气变换前,将所述转炉煤气输入余热锅炉的换热器以生产所述水蒸气。根据本发明一个实施例的转炉煤气利用系统,在所述步骤煤气变换与所述步骤脱碳处理之间还包括步骤:洗涤反应后的混合气体。根据本发明一个实施例的转炉煤气利用系统,在所述步骤还原铁矿石之前还包括步骤:加热还原气体,将所述还原气体加热至800℃-1100℃。根据本发明一个实施例的转炉煤气利用系统,在所述步骤加热还原气体之前还包括步骤:压缩所述还原气体,并进行脱油处理。所述利用转炉煤气的方法与上述的转炉煤气利用系统相对于现有技术所具有的优势相同,在此不再赘述。本发明的附加方面和优点将在下面的描述中部分给出,部分将从下面的描述中变得明显,或通过本发明的实践了解到。附图说明本发明的上述和/或附加的方面和优点从结合下面附图对实施例的描述中将变得明显和容易理解,其中:图1是根据本发明实施例的转炉煤气利用系统的结构示意图;图2是根据本发明实施例的利用转炉煤气的方法示意图。附图标记:转炉煤气利用系统100,转炉1,锅炉2,换热器2a,转化炉3,洗涤塔4,脱碳塔5,氮气分离装置6,加热炉7,气基直接还原装置8。具体实施方式下面详细描述本发明的实施例,所述实施例的示例在附图中示出,其中自始至终相同或类似的标号表示相同或类似的元件或具有相同或类似功能的元件。下面通过参考附图描述的实施例是示例性的,仅用于解释本发明,而不能理解为对本发明的限制。在本发明的描述中,需要说明的是,除非另有明确的规定和限定,术语“安装”、“相连”、“连接”应做广义理解,例如,可以是固定连接,也可以是可拆卸连接,或一体地连接;可以是机械连接,也可以是电连接;可以是直接相连,也可以通过中间媒介间接相连,可以是两个元件内部的连通。对于本领域的普通技术人员而言,可以具体情况理解上述术语在本发明中的具体含义。下面参考图1描述根据本发明实施例的转炉煤气利用系统100。如图1所示,根据本发明一个实施例的转炉煤气利用系统100包括转炉1、锅炉2、转化炉3、脱碳塔5、氮气分离装置6和气基直接还原装置8。其中,转炉1上可以设有排气管,以排出转炉煤气,转炉煤气的主要成分为co、co2和n2,锅炉2可以产生水蒸气,转炉1的排气口与转化炉3相连,以将转炉煤气通入到转化炉3内,锅炉2的出气口与转化炉3相连,以将水蒸气通入到转化炉3内,转化炉3内可以为高温环境,以使转炉煤气中的co与h2o反应得到co2和h2,化学方程式为co+h2o=co2+h2,即部分的co将h2o还原得到h2。转化炉3的出口与脱碳塔5的进口相连,脱碳塔5用于去除co2,即转化后的混合气体通过管道输送到脱碳塔5内,以去除混合气体中的co2,可选地,脱碳塔5内可以放置有碱性溶液,脱碳原理:co2+碱性溶液=碳酸盐液;例如碱性溶液为氢氧化钠溶液或者氢氧化钾溶液。脱碳塔5的出口与氮气分离装置6的进口相连,氮气分离装置6用于分离脱碳处理后的混合气体中的n2,以得到包含co和h2的还原气体,此时还原气体的主要成分即为co和h2。氮气分离可以采用物理方法,比如氮气分离装置6设置为降温冷凝式以分离n2。氮气分离装置6的出口与气基直接还原装置8的进气口相连。转炉煤气经过变换、脱碳、去氮处理后得到以co+h2为主的还原气体,还包含少量氮气、co2、h2o,还原气体进入气基直接还原装置8后可以还原铁矿石或铁矿球团,气基直接还原装置8可以为竖炉。根据本发明实施例的转炉煤气利用系统100,将转炉煤气通过变换、脱碳、去氮工艺后用于气基直接还原,实现了转炉炼钢与气基直接还原装置8的耦合,既可经济有效地利用转炉煤气,又可降低气基直接还原装置8的投资,降低直接还原铁的生产成本。根据本发明的一个优选实施例的转炉煤气利用系统100,如图1所示,锅炉2可以为余热锅炉,且转炉1的排气口通过排气管与余热锅炉的换热器2a相连,且换热后的转炉煤气输入转化炉3。也就是说,转炉1的高温排气管与余热锅炉的换热器2a相连,烟气经过高温排气管输入到余热锅炉的换热器2a来加热锅炉2以生产水蒸气,将换热后的转炉煤气再与水蒸气通过管道输入转化炉3加热反应。通过利用转炉煤气的高温显热进行余热锅炉的加热,充分利用了转炉煤气的显热,整个转炉煤气利用系统100的能效更高。根据本发明的一个实施例的转炉煤气利用系统100,转炉1输出的转炉煤气与锅炉2输出的水蒸气的比例可调。换言之,转炉煤气变换所需水蒸气量可以根据还原气体所要求的h2/co比例可调,以使转化炉3内的反应更充分。比如,锅炉2的输出管路上可以设置调节阀。如图1所示,根据本发明的一个优选实施例的转炉煤气利用系统100,还包括:洗涤塔4,洗涤塔4可以串联在转化炉3的出口与脱碳塔5的进口之间。这样,可以去除转换后的气体中的粉尘等杂质,防止污染后续的设备。如图1所示,转炉煤气利用系统100还可以包括:加热炉7,加热炉7连接在氮气分离装置6与气基直接还原装置8之间,加热炉7用于将还原气体加热至目标温度,防止还原气体影响气基直接还原装置8内的温度。优选地,加热炉7设置为将还原气体加热至800℃-1100℃,比如还原气体加热至800℃-950℃才送入气基直接还原装置8。进一步地,转炉煤气利用系统100还可以包括:压缩机,压缩机的进口与氮气分离装置6的出口相连,压缩机的出口与加热炉7的进口相连,压缩机用于压缩还原气体,以增强气体密度,提高反应效率。进一步地,转炉煤气利用系统100还可以包括:去油装置,去油装置连接在压缩机的出口与加热炉7的进口之间,压缩机的进口与氮气分离装置6的出口相连,压缩机的出口与去油装置的进口相连,去油装置的出口与加热炉7的进口相连,去油装置用于去除还原气体中的油污,防止污染气基直接还原装置8内的反应。也就是说,将变换、脱碳、去氮处理后的还原气体通过压缩机压缩、除油处理后才输入加热炉7加热。下面描述根据本发明实施例的转炉煤气利用系统100的一个具体的实施例。将120t转炉煤气经高温管道进入余热锅炉的换热器2a,转炉煤气经过高温烟气管输入余热锅炉的换热器2a来加热锅炉2以生产水蒸气,将换热后的转炉煤气与水蒸气通过管道输入高温转化炉3加热,并对部分co进行转换,120t转炉煤气量26400nm3/h(煤气成分如表1所示),加入水蒸气量8019kg/h,变换转炉煤气成分,转换后的混合气体送入洗涤塔4洗涤,洗涤后的混合气体通过管道输送至脱碳塔5进行脱除二氧化碳的脱碳处理,脱碳原理:co2+碱液=碳酸盐液,脱碳处理后的混合气体用降温冷凝的物理方法去除氮气,剩余主要成分co+h2,其余为少量氮气、co2、h2o的还原气体18480nm3/h,还原气体的主要成分及含量见表2,将变换、脱碳处理后的还原气体通过压缩机压缩、除油处理后输入加热炉7加热到800℃-950℃,送入气基直接还原装置8还原铁矿石或铁矿球团。1tdri(还原铁)需要新鲜煤气流量686.63nm3/t,燃烧气转炉煤气151.08nm3/t,用作燃料的转炉煤气无需处理。年产800万吨钢的钢铁联合企业可以配套生产80万tdri。表1转炉煤气主要成分及含量成分coco2n2含量,%632215表2还原气体主要成分及含量成分coco2h2n2cnhmh2o含量,%34.665.0055.442.080.212.62下面描述根据本发明实施例的转炉煤气利用系统100的另一个具体的实施例。将120t转炉煤气经高温管道进入余热锅炉的换热器2a,转炉煤气经过高温烟气管输入余热锅炉的换热器2a来加热锅炉2以生产水蒸气,将换热后的转炉煤气与水蒸气通过管道输入高温转化炉3加热,并对部分co进行转换,120t转炉煤气量26400nm3/h(煤气成分如表1所示),加入水蒸气量10935kg/h,变换转炉煤气成分,转换后的混合气体送入洗涤塔4洗涤,洗涤后的混合气体通过管道输送至脱碳塔5进行脱除二氧化碳的脱碳处理,脱碳原理:co2+碱液=碳酸盐液,脱碳处理后的混合气体用降温冷凝的物理方法去除氮气,剩余主要成分co+h2,其余为少量氮气、co2、h2o的还原气体18480nm3/h,还原气体的主要成分及含量见表3,将变换、脱碳处理后的还原气体通过压缩机压缩、除油处理后输入加热炉7加热到800℃-1100℃,送入气基直接还原装置8还原铁矿石或铁矿球团。1tdri需要新鲜煤气流量693.01nm3/t,燃烧气转炉煤气151.08nm3/t,用作燃料的转炉煤气无需处理。年产800万吨钢的钢铁联合企业可以配套生产80万tdri。表3还原气体主要成分及含量成分coco2h2n2cnhmh2o含量,%34.665.0055.442.080.212.62综上所述,根据本发明实施例的转炉煤气利用系统100,可以有效地利用转炉煤气的显热,且实现了转炉炼钢与气基直接还原装置8的耦合,既可经济有效地利用转炉煤气,又可降低气基直接还原装置8的投资,降低直接还原铁的生产成本。本发明还公开了一种使用上述任一种实施例的转炉煤气利用系统利用转炉煤气的方法。如图2所示,根据本发明实施例的利用转炉煤气的方法包括如下步骤:煤气变换、脱碳处理、氮气分离、还原铁矿石。其中,步骤煤气变换包括将转炉煤气和水蒸气反应,转炉煤气的主要成分为co、co2和n2,在高温环境下转炉煤气中的co与h2o反应得到co2和h2,化学方程式为co+h2o=co2+h2,即部分的co将h2o还原得到h2。步骤脱碳处理包括去除反应后的混合气体中的co2,比如可以将混合气体通入到碱性溶液内,脱碳原理:co2+碱性溶液=碳酸盐液。步骤氮气分离包括分离剩余气体中的氮气,以得到包含co和h2的还原气体,此时还原气体的主要成分即为co和h2,其中可以采用降温冷凝的物理方式来分离出氮气。步骤还原铁矿石包括用还原气体还原铁矿石或铁矿球团,比如可以将还原气体通入到气基直接还原装置内。根据本发明实施例的转炉煤气利用系统100,将转炉煤气通过变换、脱碳、去氮工艺后用于气基直接还原,实现了转炉炼钢与气基直接还原生产还原铁的耦合,既可经济有效地利用转炉煤气,又可降低直接还原铁的生产成本。根据本发明一个优选实施例的利用转炉煤气的方法,如图2所示,在步骤煤气变换前,将转炉煤气输入余热锅炉的换热器以生产水蒸气,然后将进行余热利用后的转炉煤气与水蒸气反应。这样充分利用了转炉煤气的显热,利用转炉煤气的方法的能效更高。根据本发明一个优选实施例的利用转炉煤气的方法,如图2所示,在步骤煤气变换与步骤脱碳处理之间还包括步骤:洗涤反应后的混合气体,也就是说,在步骤煤气变换后,将混合气体进行洗涤,去除转换后的气体中的粉尘等杂质,防止污染后续的设备,洗涤后的气体再进行脱碳处理。根据本发明一个优选实施例的利用转炉煤气的方法,如图2所示,在步骤还原铁矿石之前还包括步骤:加热还原气体,将还原气体加热至800℃-1100℃,比如可以将还原气体加热至800℃-950℃,以防止还原气体影响炼铁设备的温度。进一步在步骤加热还原气体之前还包括步骤:压缩还原气体,并进行脱油处理,以增强还原效率防止油污影响还原反应。根据本发明一个具体实施例的利用转炉煤气的方法,如图2所示,包括如下步骤:将转炉煤气输入余热锅炉的换热器以生产水蒸气;煤气变换,将转炉煤气和水蒸气反应;洗涤反应后的混合气体;脱碳处理,去除反应后的混合气体中的co2;氮气分离,分离剩余气体中的氮气,以得到包含co和h2的还原气体;压缩所述还原气体,并进行脱油处理;加热还原气体,将所述还原气体加热至800℃-1100℃;还原铁矿石,用所述还原气体还原铁矿石或铁矿球团。本发明实施例的利用转炉煤气的方法可以通过上述实施例的转炉煤气利用系统100来实现。在本说明书的描述中,参考术语“一个实施例”、“一些实施例”、“示意性实施例”、“示例”、“具体示例”、或“一些示例”等的描述意指结合该实施例或示例描述的具体特征、结构、材料或者特点包含于本发明的至少一个实施例或示例中。在本说明书中,对上述术语的示意性表述不一定指的是相同的实施例或示例。而且,描述的具体特征、结构、材料或者特点可以在任何的一个或多个实施例或示例中以合适的方式结合。尽管已经示出和描述了本发明的实施例,本领域的普通技术人员可以理解:在不脱离本发明的原理和宗旨的情况下可以对这些实施例进行多种变化、修改、替换和变型,本发明的范围由权利要求及其等同物限定。当前第1页12