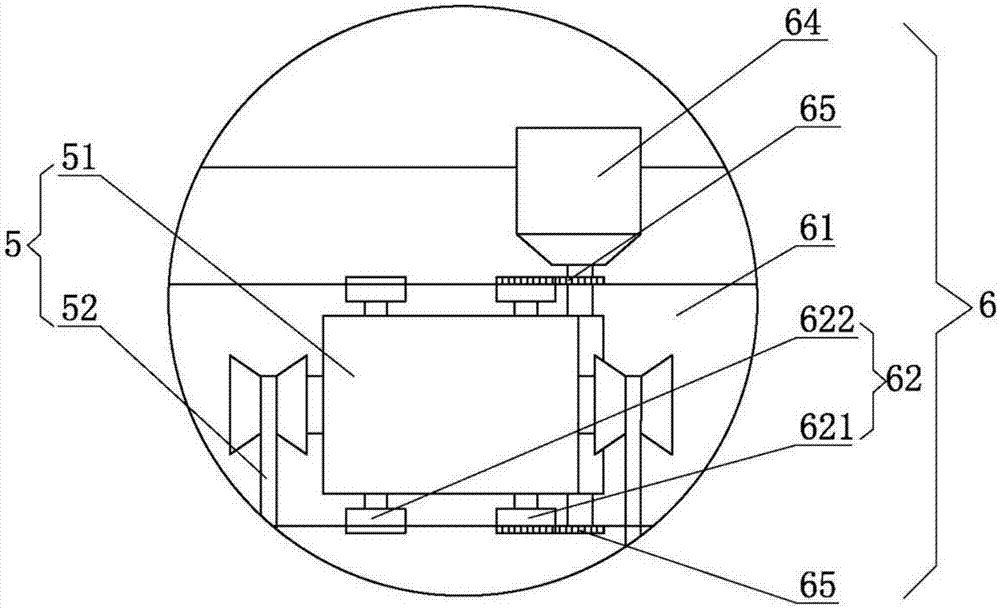
本发明涉及轨道车辆零部件的热处理
技术领域:
,尤其涉及一种车轴淬火冷却系统及其热处理工艺。
背景技术:
:轨道交通车辆用车轴是各种车辆中涉及安全的最重要的运动和承载部件之一。由于车轴承受着动载荷,受力状态比较复杂,如弯曲载荷、扭转载荷、弯扭复合载荷,并受到一定冲击,特别是高速动车组车轴等,其受力状态更为复杂。因此,高速动车组车轴和机车车轴等在服役过程中可能会因为疲劳、弯曲、扭转或拉伸应力等而发生断裂,其中疲劳断裂是高速车轴的普遍断裂形式。为确保车辆的安全运行,高速动车组和机车等用车轴必须具有足够的可靠性和疲劳安全系数,所以通常对车轴进行“淬火+高温回火”的调质热处理,以提高车轴的强韧性和耐疲劳性能。其中,淬火是将经过高温加热并保温适当时间后的钢材或合金快速冷却以提高钢材的硬度、强度以及耐磨性等性能的方法。现有的车轴淬火冷却工艺中一般是采用天车等吊装设备将从加热炉出来的钢材吊起,并浸入到淬火液中进行淬火冷却,由于淬火工件一直处于一个静止位置,因此冷却过程中则主要是依靠淬火液自身来与淬火工件进行热交换。这种方法存在以下缺点:1淬火工件的冷却速度除了受淬火介质的影响比较大之外,还主要受淬火液自身流动速度的影响,但是对于淬火工件周围淬火液的流速控制则较为不易,使得淬火工件的冷却速度受到影响,而且会使淬火工件冷却不均匀,影响淬火工件的性能;2运用吊挂的方式对车轴完成淬火,淬火前的需要将车轴固定牢固,需要消耗人力完成,而且一次淬火的工件有限,不能批量淬火,淬火效率低,使淬火成本提高。如何设计一种淬火效率高、淬火质量好、淬火成本低的淬火设备是目前亟待解决的问题。技术实现要素:为了解决上述技术问题,本发明提供了一种车轴淬火冷却系统及其热处理工艺,目的在于,解决现有技术中车轴淬火冷却效率低的问题,此淬火冷却系统结构简单、操作方便,不仅可以使车轴多个方向运动冷却,而且实现了车轴的批量淬火,冷却更均匀,有效提高了工作效率。为实现上述目的,本发明解决其技术问题所采用的技术方案是:所述车轴淬火冷却系统,包括操作平台、操作平台上设置的淬火槽和淬火操作装置,其特征在于,所述淬火操作装置包括移动车轴的机械手、淬火槽内的车轴容置箱、淬火槽两侧分别设置的驱动车轴容置箱沿竖直方向和淬火槽的宽度方向运动的第一动力机构以及驱动车轴容置箱沿淬火槽长度方向运动的第二动力机构。进一步地,所述第一动力机构包括双头电机和与双头电机的输出轴相连的绳索,绳索的另一端与车轴容置箱固定相连。进一步地,所述车轴容置箱包括容纳车轴的箱体和箱体两侧分别固定的倾斜支架,倾斜支架的端部与绳索相连。进一步地,所述倾斜支架设置为固定支杆,固定支杆的端部铰接有橡胶滚轮,橡胶滚轮中部与绳索的一端固定相连。进一步地,所述车轴容置箱设置为钢骨架结构。进一步地,所述第二动力机构包括沿淬火槽长度方向分别设置的相互平行的导轨、双头电机底部设置的与导轨滑动连接的滚子和驱动滚子沿导轨运动的动力组件。进一步地,所述动力组件包括与双头电机底部连接的液压缸。进一步地,所述双头电机底部设置有四个滚子,包括两个主动轮和两个从动轮,两个主动轮的轮缘上设置有齿形结构,所述动力组件包括微型电机,微型电机的输出轴上设置有与齿形结构相啮合的齿轮。一种运用所述的淬火冷却系统对车轴进行的热处理工艺,其特征在于,包括以下步骤:(1)正火:以70℃/h~90℃/h加热车轴至温度880℃~900℃,加热保温时间280min~300min,空冷;(2)淬火:以70℃/h~90℃/h加热车轴至温度850℃~870℃,加热保温时间250min~270min,然后采用所述淬火冷却系统对车轴进行快速均匀冷却,直至车轴冷却直至室温;(3)回火:以70℃/h~90℃/h加热车轴至温度620℃~640℃,加热保温时间400min~420min,空冷。进一步地,所述步骤2中,运用所述淬火冷却系统对车轴进行快速均匀水冷的具体方法是:(1)机械手将正火处理后的车轴抓取到车轴容置箱内,并通过双头电机驱动车轴容置箱向下运动,使车轴完全浸入淬火槽内的淬火液中;(2)微型电机驱动双头电机沿着淬火槽的长度方向在导轨上做一次往复运动,使车轴在淬火液中沿双头电机的运动方向进行冷却;(3)淬火槽两侧的双头电机同时正转后同时反转,带动车轴容置箱沿淬火槽的宽度方向做一次往复运动,使车轴在淬火液中沿车轴容置箱的运动方向进行冷却;(4)淬火槽一侧的双头电机正转后反转,同时淬火槽另一侧的双头电机反转后正转,带动车轴容置箱沿竖直方向做一次往复运动,使车轴在淬火液中沿竖直运动方向进行冷却;(5)重复上述步骤2、步骤3和步骤4直至淬火结束,然后通过驱动淬火槽两侧双头电机反向运转带动车轴容置箱上升,将车轴提升至淬火液液面以上。本发明的有益效果是:1、本发明中的车轴淬火冷却系统通过淬火操作装置可同时对多个车轴进行淬火,而且使车轴在三个方向上移动并冷却,并且可根据车轴的冷却需要通过控制第一动力机构和第二动力机构灵活控制车轴的运动速度,有利于调节车轴与淬火液之间的热交换速率,使车轴冷却更加均匀;而且通过控制第一动力机构可使车轴分别沿竖直方向和淬火槽的宽度方向运动,整体结构简单,可实现自动化操作,节省了人力,降低了加工成本;2、将所述车轴淬火冷却系统运用到车轴的热处理工艺中,使车轴依次通过正火、淬火和回火工艺,提高了车轴的强度,提高了车轴组织和性能的均匀性,使车轴可承受复杂的载荷冲击,提高了车轴的强韧性和耐疲劳性能;综上,所述车轴淬火冷却系统结构简单、操作方便,不仅可以使车轴多个方向运动冷却,而且实现了车轴的批量淬火,冷却均匀,工作效率更高,将此系统运用到车轴的热处理工艺中,提高了车轴的强韧性和耐疲劳性能。附图说明下面对本发明说明书各幅附图表达的内容及图中的标记作简要说明:图1为本发明的结构示意图;图2为图1中放大部分的结构示意图;图3为本发明另一种结构的结构示意图;上述图中的标记均为:1.操作平台,2.淬火槽,3.机械手,4.车轴容置箱,41.箱体,42.倾斜支架,5.第一动力机构,51.双头电机,52.绳索,53.橡胶滚轮,6.第二动力机构,61.导轨,62.滚子,621.主动轮,622.从动轮,63.液压缸,64.微型电机,65.齿轮。具体实施方式下面对照附图,通过对最优实施例的描述,对本发明的具体实施方式作进一步详细的说明。本发明具体的实施方案为:如图1所示,一种车轴淬火冷却系统,包括操作平台1、操作平台1上设置的淬火槽2和淬火操作装置,淬火操作装置包括移动车轴的机械手3、淬火槽2内的车轴容置箱4、淬火槽2两侧分别设置的驱动车轴容置箱4沿竖直方向和淬火槽2的宽度方向运动的第一动力机构5以及驱动车轴容置箱4沿淬火槽2长度方向运动的第二动力机构6。为了进一步提高车轴容纳量,车轴容置箱4、第一动力机构5和第二动力机构6可设置有多个。具体地,如图2所示,第一动力机构5包括双头电机51和与双头电机51的输出轴相连的绳索52,绳索52的另一端与车轴容置箱4固定相连,通过双头电机51输出轴的转动使绳索52伸长或缩短,从而使与绳索52相连的车轴容置箱4沿竖直方向和淬火槽2的宽度方向运动,即两个双头电机51转向相反且转速相同时,使两侧的绳索52伸长或缩短相同的距离,则使车轴容置箱4沿竖直方向平稳上升或下降;两个双头电机51转向相同且转速相同时,使一侧的绳索52伸长而另一侧的绳索52缩短,使车轴容置箱4沿淬火槽2的宽度方向运动。具体地,车轴容置箱4包括容纳车轴的箱体41和箱体41两侧分别固定的倾斜支架42,倾斜支架42的端部与绳索52相连,倾斜支架42增加了箱体41的稳定性,避免了箱体41的歪斜;倾斜支架42设置为固定支杆,固定支杆的端部铰接有橡胶滚轮53,橡胶滚轮53中部与绳索52的一端固定相连,优化地,箱体41每侧的固定支杆至少设置两个,每个固定支杆上铰接橡胶滚轮53,当车轴容置箱4运动时减少与操作平台1的摩擦,使车轴容置箱4的运动更灵活;优化地,车轴容置箱4设置为钢骨架结构,使内部的车轴可以充分与淬火液接触,进一步提高淬火效果。具体地,第二动力机构6包括沿淬火槽2长度方向分别设置的相互平行的导轨61、双头电机51底部设置的与导轨61滑动连接的滚子62和驱动滚子62沿导轨61运动的动力组件,动力组件通过驱动滚子62沿导轨61运动,使双头电机51沿淬火槽2的长度方向运动,进而实现车轴沿淬火槽2的长度方向运动冷却;具体地,如图3所示,动力组件包括与双头电机51底部连接的液压缸63,通过液压缸63中活塞杆的运动实现双头电机51沿淬火槽2的长度方向的运动,另一种结构是,如图1和图2所示,双头电机51底部设置有四个滚子62,包括两个主动轮621和两个从动轮622,两个主动轮621的轮缘上设置有齿形结构,动力组件包括微型电机64,微型电机64的输出轴上设置有与齿形结构相啮合的齿轮65,通过微型电机64的运转,带动齿轮65转动,齿轮65带动两个主动轮621运行,两个从动轮622也沿导轨61运动,使双头电机51沿淬火槽2的长度方向运动,进而实现车轴沿淬火槽2的长度方向运动冷却。一种运用所述淬火冷却系统对车轴进行的热处理工艺,包括以下步骤:1、正火:以70℃/h~90℃/h加热车轴至温度880℃~900℃,加热保温时间280min~300min,空冷;2、淬火:以70℃/h~90℃/h加热车轴至温度850℃~870℃,加热保温时间250min~270min,然后采用淬火冷却系统对车轴进行快速均匀冷却,直至车轴冷却直至室温;运用淬火冷却系统对车轴进行快速均匀水冷的具体方法是:(1)机械手3将正火处理后的车轴抓取到车轴容置箱4内,并通过双头电机51驱动车轴容置箱4向下运动,使车轴完全浸入淬火槽2内的淬火液中;其中,淬火槽2的长×宽×高为12m×10m×8m,淬火槽2中淬火液为水或其他冷却液,车轴容置箱4的长×宽×高为5m×2.5m×0.5m,以一种EA4T车轴为例,此车轴尺寸为Ф250mm×2200mm,车轴容置箱4中可加入约15支车轴。(2)微型电机64驱动双头电机51沿着淬火槽2的长度方向在导轨61上做一次往复运动,使车轴在淬火液中沿双头电机51的运动方向进行冷却;(3)淬火槽2两侧的双头电机51同时正转后同时反转,带动车轴容置箱4沿淬火槽2的宽度方向做一次往复运动,使车轴在淬火液中沿车轴容置箱4的运动方向进行冷却;(4)淬火槽2一侧的双头电机51正转后反转,同时淬火槽2另一侧的双头电机51反转后正转,带动车轴容置箱4沿竖直方向做一次往复运动,使车轴在淬火液中沿竖直运动方向进行冷却;(5)重复上述步骤(2)、步骤(3)和步骤(4)直至淬火结束,然后通过驱动淬火槽2两侧双头电机51反向运转带动车轴容置箱4上升,将车轴提升至淬火液液面以上。3、回火:以70℃/h~90℃/h加热车轴至温度620℃~640℃,加热保温时间400min~420min,空冷。通过上述热处理工艺得到的多个EA4T车轴的熔炼化学成分质量百分比(wt%),选择了其中两个车轴,如下表1:表1EA4T车轴的熔炼化学成分质量百分比(wt%)序号CSiMnPSCrMoVAls10.250.320.770.0100.0011.040.290.050.02920.280.210.830.0070.0011.150.260.040.033根据EA4T车轴标准规定,车轴中的化学成分应满足表2的规定:表2EA4T车轴的化学成分/%由表2可以看出,通过上述热处理工艺得到的车轴的化学成分中,C、Si、Mn、Cr、Mo符合要求,而对于P、S、V等杂质的含量要求降至允许限量之下,也满足要求,而且车轴中还含有大于0.020%含量的Als(酸溶铝),具有细化晶粒的作用,进一步提高了车轴的质量。EA4T车轴经过上述热处理后的性能指标如表3所示,即实心轴1/2R处或空心轴内外表面间1/2距离处要达到的值:表3EA4T车轴热处理后性能指标根据EA4T车轴标准规定,实心轴1/2R处或空心轴内外表面间1/2距离处要达到的值要符合表4规定的力学性能指标:表4实心轴1/2R处或空心轴内外表面间1/2距离处要达到的值由表4可以看出,经过上述热处理工艺得到的车轴符合力学性能要求,对于钢种EA4T热处理后的组织应由贝氏体/退火马氏体显微组织结构组成,而且晶粒度不能低于5级,满足金相组织要求。其中表2和表4的车轴性能标准来自于南车青岛四方机车车辆股份有限公司技术工程部的刘军辉发表的文章《EA4T车轴热处理工艺研究》。综上,所述车轴淬火冷却系统结构简单、操作方便,不仅可以使车轴多个方向运动冷却,而且实现了车轴的批量淬火,冷却均匀,工作效率更高,将此系统运用到车轴的热处理工艺中,提高了车轴的强韧性和耐疲劳性能。以上所述,只是用图解说明本发明的一些原理,本说明书并非是要将本发明局限在所示所述的具体结构和适用范围内,故凡是所有可能被利用的相应修改以及等同物,均属于本发明所申请的专利范围。当前第1页1 2 3