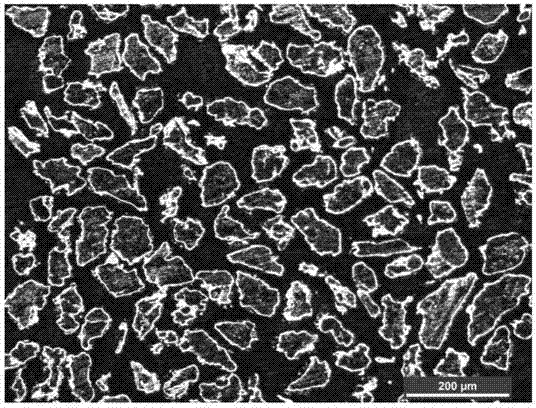
本发明属于汽车制动系统和传动系统
技术领域:
,涉及一种耐磨材料、摩擦材料及其生产工艺,尤其涉及一种高强度耐磨材料、摩擦材料及其等离子转移弧焊接生产工艺。
背景技术:
摩擦材料,属于耐磨材料的一种,是一种应用在动力机械上,依靠摩擦作用来执行制动和传动功能的部件材料。任何机械设备与运动的各种车辆都必须要有制动或传动装置,而摩擦材料就是这种制动或传动装置上的关键性部件,其最主要的功能是通过摩擦来吸收或传递动力,由衬体(基体)和耐磨材料组成,主要包括制动器衬片(刹车片)和离合器面片(离合器片)。刹车片用于制动,吸收动能;而离合器片用于传动,传递动力,从而使得机械设备与各种机动车辆能够安全可靠地工作,所以说摩擦材料是一种应用广泛又甚关键地材料。汽车用摩擦材料主要是用于制造制动摩擦片和离合器片,从配方上分有半金属型摩擦材料、少金属型摩擦材料、复合纤维摩擦材料、陶瓷纤维摩擦材料以及石棉基摩擦材料(已基本废弃)等等。其中,刹车片包括用于盘式制动器的刹车片、用于鼓式制动器的刹车蹄和用于大卡车的来令片,通常刹车片就统指刹车片和刹车蹄,而不是刹车盘。离合器片也是一种以摩擦为主要功能、兼有结构性能要求的复合材料。以双离合变速箱的双离合模块为例,一种是干式,使用干式摩擦片作为离合器,一种是湿式,使用液力变矩器作为离合器。干式离合器通过多片金属摩擦片进行动力传输,摩擦片被压得越紧,传动比例越高,摩擦片被压死,满额传动,摩擦片分离,传动中断。而湿式的主动盘和从动盘的连接是靠封闭空间里面油液润滑,油压越高传动比例越高。随着全社会对环保和汽车安全性能的要求越来越高,而摩擦材料则是汽车上主要用于制造制动系和传动系的零件,更加要求有足够高的而且稳定的摩擦系数和较好的耐磨性,而且由于是与摩擦副共同进行工作,与摩擦材料相匹配的摩擦副(芯片)一般是强化处理的合金钢,硬度和强度都比较高。所以相应的摩擦材料则是耗材,耐磨性需要适度,而不是越高越好。耐磨性差会使得在制动和传动过程中,在与摩擦副摩擦的时候,导致质量损耗,极大地影响了摩擦副的工作,功率输出以及使用寿命;而耐磨性过高又会导致摩擦副的不正常损耗。因而现有的摩擦片材料主要由金属片(衬体),以及覆盖在其表面的耐磨材料组成,其中耐磨材料主要是铜基粉末冶金或其他耐磨材料构成的复合耐磨材料。在现有的摩擦材料中,金属烧结摩擦材料因为其优良的耐磨性能、耐高温性能、高的导热性能、高强度和稳定性在各行业里的制动部件拥有广泛的用途。一般说来,金属烧结耐磨材料主要有五个组元:金属粘接相,润滑剂,摩擦介质,耐磨剂和填充料。金属粘接相提供连续网络和摩擦部件的强度,大约重量比在50%~80%之间,一般是铜基或铁基,其中需要添加低熔点金属粉末比如锡和锌--低熔点在烧结过程中呈液态从而使得摩擦材料进行液相烧结致密化,同时和铁或者铜合金化增加强度。金属粘接相的选择主要是依据工作温度和摩擦材料的强度,铜基摩擦材料的广泛使用主要是因为其中等强度和良好的导热传热性能。润滑剂占重量的5%~25%,一般是铅,一氧化铅(铅黄),方铅矿,二硫化鉧,石墨等。摩擦剂占重量20%左右,一般是以下一种或者几种混和物:硅化物,氧化铝,氧化镁,碳化硅以及多种形式的铝硅化合物。耐磨剂一般以分离的颗粒或者在烧结过程中反应产生物(如渗碳体和铸铁颗粒),主要用在干性摩擦材料来降低摩擦系数和延长寿命。填料一般是出于经济原因考虑,比如铁在铜基摩擦材料中,一些其它形式的碳或者矿物质。然而,现有的金属烧结摩擦材料仍然存在以下问题,1、预烧结很难保证粘结相和润滑组元的结合强度和工件质量的一致性;2、钢芯板和钢背需要进行复杂的电解电镀等前处理,工艺复杂,污染环境;3、因为金属的易氧化性,所以烧结在还原气氛下进行,工艺过程复杂,工艺成本和人力成本高。因此,如何找到一种合适的摩擦材料和生产工艺,解决现有的金属烧结摩擦材料存在的上述问题,已成为诸多研发型企业的一线研究人员亟待解决的问题之一。技术实现要素:有鉴于此,本发明要解决的技术问题在于提供一种耐磨材料、摩擦材料及其生产工艺,特别是一种含有高强度耐磨材料的摩擦材料及其等离子转移弧焊接生产工艺,本发明提供的能够通过有效调节金属基体(即摩擦材料的强度)和摩擦材料中的石墨含量(即摩擦系数和磨损性能),来生产对应不同工况和技术要求的摩擦材料,而且通过pta焊接技术能够有效改善当前制动摩擦材料的喷撒法和烧结技术等生产工艺存在的多种实际问题。本发明提供了一种耐磨材料,按原料质量百分比计,包括:活性金属1~28.5重量份;润滑组元0.5~30重量份;所述润滑组元包括石墨和/或二氧化钼;镍合金基体70~95重量份。优选的,所述耐磨材料原料中还包括铁和/或摩擦剂;所述铁的加入量为0~10重量份;所述摩擦剂的加入量为0~20重量份;所述镍合金基体为低熔点镍合金基体。优选的,所述活性金属包括镍、铁、铜、钛及其合金中的一种或多种;所述摩擦剂包括硅化物、氧化铝、氧化镁、碳化硅和铝硅化合物中的一种或多种;所述镍合金基体的熔点为980~1250℃;所述镍合金基体包括ni-(4~20)cr-(1~10)si-(0.5~5)b;所述耐磨材料为用于传动摩擦材料或制动摩擦材料的耐磨材料。优选的,所述原料中,所述镍合金基体的粒径为30~180微米;所述原料中,润滑组元的加入方式为以活性金属包覆润滑组元复合材料的方式加入;所述活性金属包覆润滑组元复合材料的粒径为33~200微米;所述原料中,摩擦剂的加入方式为以活性金属包覆摩擦剂复合材料的方式加入;所述活性金属包覆摩擦剂复合材料的粒径为33~200微米。优选的,所述活性金属包覆润滑组元复合材料中,所述润滑组元的粒径为30~180微米;所述活性金属包覆润滑组元复合材料中,所述活性金属层的厚度为3~40微米;所述活性金属包覆摩擦剂复合材料中,所述摩擦剂的粒径为30~180微米;所述活性金属包覆摩擦剂复合材料中,所述活性金属层的厚度为3~40微米。本发明提供了一种摩擦材料,所述摩擦材料包括衬体和复合在所述衬体表面的耐磨材料;所述耐磨材料为上述技术方案任意一项所述的耐磨材料;所述摩擦材料包括传动摩擦材料或制动摩擦材料。本发明还提供了一种摩擦材料的生产工艺,包括以下步骤:a)将活性金属包覆润滑组元复合材料粉末和镍合金基体粉末混合后,得到混合粉末;b)将上述步骤得到的混合粉末,采用等离子转移弧焊接在衬体表面后,得到摩擦材料。优选的,所述混合的方式为v型混合;所述混合的时间为30~120分钟;所述等离子转移弧焊接的电流为40~80a;所述混合粉末,采用等离子转移弧焊接在衬体表面后,可以直接成型。优选的,所述衬体的材质包括钢、合金钢、调质处理后的42crmov或30crmnsi;所述活性金属包覆润滑组元复合材料粉末,由活性金属气雾化后对润滑组元粉末进行包覆后得到;所述混合粉末中还包括铁粉和/或活性金属包覆摩擦剂复合材料粉末;所述活性金属包覆摩擦剂复合材料粉末,由活性金属气雾化后对摩擦剂粉末进行包覆后得到。优选的,所述等离子转移弧焊接的焊接途径和/或焊接参数可由计算机程序控制,或实现计算机远程中央控制;所述混合粉末,采用等离子转移弧焊接在衬体表面后,可以在衬体表面形成特定设计的结构或形貌;所述等离子转移弧焊接可以在衬体的两面进行等离子转移弧焊接;所述等离子转移弧焊接后,还包括后续加工工序;所述后续加工工序包括车、铣、刨、磨和钳工序中的一种或多种。本发明提供了一种耐磨材料,按原料质量百分比计,包括1~28.5重量份的活性金属、0.5~30重量份的润滑组元以及70~95重量份的镍合金基体;所述润滑组元包括石墨和/或二氧化钼。本发明针对现有的金属烧结摩擦材料存在预烧结中粘结相和润滑组元的结合强度和工件质量的一致性差,工艺过程复杂,污染环境、工艺成本和人力成本高等诸多实际生产问题。参见图1,图1为现有传统的摩擦材料的宏观和微观组织图。其中,粘接相是白色铜基合金cu-sn-zn-ni粉末颗粒;润滑组元是黑色片状石墨。其中润滑组元和摩擦组元的配比是关键提供摩擦系数和摩擦运行中的稳定性。而且目前该部件的铜基摩擦材料的工艺,通常是把按比例混好的粉喷撒在钢板上,在750~850℃进行预烧结;然后在90~400mpa压制成型,最后叠加烧结调节钢板基体的物理力学性能。本发明针对上述烧结工艺存在的问题,创造性的采用了等离子转移弧(pta)焊接的方式,并基于此得到了一种新型配方的耐磨材料与之相配合,能够通过有效调节金属基体(即摩擦材料的强度)和摩擦材料中的石墨含量(即摩擦系数和磨损性能)等原料粉末的组分,来生产对应不同工况和技术要求的摩擦材料,而且通过pta焊接技术,在摩擦材料的衬体表面直接成型,大大简化了工艺流程、极大地提高了生产效率,有效的改善当前制动摩擦材料的喷撒法和烧结技术等生产工艺存在的一致性差,工艺过程复杂,污染环境、工艺成本和人力成本高等诸多实际生产问题。同时使用程序化的pta加工方法还可以进行功能化设计摩擦副部件。实验结果表明,本发明采用pta加工后的摩擦材料,金属基体的硬度在hb180~280之间,石墨状态保存良好,室温下与钢的干摩擦系数在0.12~0.35之间。附图说明图1为现有传统的摩擦材料的宏观和微观组织图;图2为本发明实施例1采用气雾化法制备的镍包覆石墨粉横截面组织图;图3为本发明实施例1配料后的混合料样品的横截面组织结构图;图4为本发明实施例1制备的摩擦材料的微观金相图;图5为本发明实施例2制备的摩擦材料的微观金相图;图6为本发明实施例3制备的摩擦材料的微观金相图。具体实施方式为了进一步理解本发明,下面结合实施例对本发明优选实施方案进行描述,但是应当理解,这些描述只是为进一步说明本发明的特征和优点,而不是对本发明权利要求的限制。本发明所有原料,对其来源没有特别限制,在市场上购买的或按照本领域技术人员熟知的常规方法制备的即可。本发明所用原料,对其纯度没有特别限制,本发明优选为工业纯或摩擦材料领域的常规纯度即可。本发明所有原料,其牌号和简称均属于本领域常规牌号和简称,每个牌号和简称在其相关用途的领域内均是清楚明确的,本领域技术人员根据牌号、简称以及相应的用途,能够从市售中购买得到或常规方法制备得到。本发明所有工艺,其简称均属于本领域的常规简称,每个简称在其相关用途的领域内均是清楚明确的,本领域技术人员根据简称,能够理解其常规的工艺步骤。本发明提供了一种耐磨材料,按原料质量百分比计,包括:活性金属1~28.5重量份;润滑组元0.5~30重量份;所述润滑组元包括石墨和/或二氧化钼;镍合金基体70~95重量份。本发明对所述活性金属没有特别限制,以本领域技术人员熟知的活性金属即可,本领域技术人员可以根据实际应用情况、技术要求和质量要求进行选择和调整,本发明所述活性金属泛指耐磨材料中常用的活性较高的金属,优选包括镍、铁、铜、钛及其合金中的一种或多种,更优选为镍、铁、铜、钛及其合金,更优选为镍。本发明所述活性金属的加入量为1~28.5重量份,优选为5~25重量份,更优选为8~23重量份,更优选为10~20重量份,更优选为12~18重量份。本发明对所述润滑组元的具体选择没有特别限制,以本领域技术人员熟知的用于摩擦材料的润滑组分即可,本领域技术人员可以根据实际应用情况、技术要求和质量要求进行选择和调整,本发明所述润滑组元包括石墨和/或二氧化钼,优选为石墨或二氧化钼。本发明所述润滑组元的加入量为0.5~30重量份,优选为1~25重量份,优选为5~20重量份,更优选为10~15重量份。本发明原则上对所述润滑组元的加入方式没有特别限制,以本领域技术人员熟知的加入方式即可,本领域技术人员可以根据实际应用情况、技术要求和质量要求进行选择和调整,本发明所述润滑组元特别优选以活性金属包覆润滑组元复合材料的方式加入,即原料采用活性金属包覆润滑组元这种复合材料。本发明原则上对所述活性金属包覆润滑组元复合材料的具体参数没有特别限制,本领域技术人员可以根据实际应用情况、技术要求和质量要求进行选择和调整,本发明为便于润滑组元在摩擦材料生产工艺中的溶解和析出,所述活性金属包覆润滑组元复合材料的粒径优选为33~200微米,更优选为50~180微米,更优选为70~160微米,更优选为90~140微米,更优选为110~120微米。所述润滑组元的粒径优选为30~180微米,更优选为50~160微米,更优选为70~140微米,更优选为90~120微米。所述活性金属包覆润滑组元复合材料中,所述活性金属层的厚度优选为3~40微米,更优选为8~35微米,更优选为13~30微米,更优选为18~25微米。本发明原则上对所述镍合金基体的具体选择没有特别限制,以本领域技术人员熟知的镍合金即可,本领域技术人员可以根据实际应用情况、技术要求和质量要求进行选择和调整,本发明所述镍合金基体优选为低熔点镍合金基体,所述镍合金基体的熔点优选为980~1250℃,更优选为1030~1200℃,更优选为1080~1150℃;更优选为自熔性镍基合金粉末,具体可以包括ni-(4~20)cr-(1~10)si-(0.5~5)b。其中,cr含量可以为4~20,也可以为7~18,也可以为10~15;si含量可以为1~10,也可以为3~8,也可以为5~6;b含量可以为0.5~5,也可以为1.5~4,也可以为2.5~3。本发明所述镍合金基体的加入量为70~95重量份,优选为75~90重量份,更优选为80~85重量份。本发明所述镍合金基体的粒径优选为30~180微米,更优选为50~160微米,更优选为70~140微米,更优选为90~120微米。本发明为更好的提高耐磨材料的性能和应用范围,所述耐磨材料原料中优选还包括铁和/或摩擦剂,更优选还包括铁和摩擦剂。本发明对所述摩擦剂的具体选择没有特别限制,以本领域技术人员熟知的常用于摩擦材料的摩擦剂即可,本领域技术人员可以根据实际应用情况、技术要求和质量要求进行选择和调整,本发明所述摩擦剂优选包括硅化物、氧化铝、氧化镁、碳化硅和铝硅化合物中的一种或多种,更优选为硅化物、氧化铝、氧化镁、碳化硅或铝硅化合物。本发明对所述铁的加入量没有特别限制,以本领域技术人员熟知的摩擦材料中铁的加入量即可,本领域技术人员可以根据实际应用情况、技术要求和质量要求进行选择和调整,本发明所述铁的加入量优选为0~10重量份,更优选为0.01~10重量份,更优选为1~9重量份,更优选为3~8重量份,更优选为5~6重量份。本发明所述摩擦剂的加入量优选为0~20重量份,更优选为0.01~20重量份,更优选为1~18重量份,更优选为5~15重量份,更优选为8~12重量份。本发明原则上对所述摩擦剂的加入方式没有特别限制,以本领域技术人员熟知的加入方式即可,本领域技术人员可以根据实际应用情况、技术要求和质量要求进行选择和调整,本发明所述摩擦剂特别优选以活性金属包覆摩擦剂复合材料的方式加入,即原料采用活性金属包覆摩擦剂这种复合材料。本发明原则上对所述活性金属包覆摩擦剂复合材料的具体参数没有特别限制,本领域技术人员可以根据实际应用情况、技术要求和质量要求进行选择和调整,本发明为便于摩擦剂更好的发挥作用,所述活性金属包覆摩擦剂复合材料的粒径优选为33~200微米,更优选为50~180微米,更优选为70~160微米,更优选为90~140微米,更优选为110~120微米。所述摩擦剂的粒径优选为30~180微米,更优选为50~160微米,更优选为70~140微米,更优选为90~120微米。所述活性金属包覆摩擦剂复合材料中,所述摩擦剂的质量含量优选小于等于40%,更优选为0.01%~40%,更优选为1%~35%,更优选为5%~30%,更优选为10%~25%。所述活性金属包覆摩擦剂复合材料中,所述活性金属层的厚度优选为3~40微米,更优选为8~35微米,更优选为13~30微米,更优选为18~25微米。本发明上述步骤得到了一种耐磨材料,是一种用于摩擦材料的耐磨材料,具体可以为用于传动摩擦材料或制动摩擦材料的耐磨材料。本发明以镍等活性金属为研究对象,使用镍基和铁是从摩擦材料的强度磨耗性能考虑,然而其导热性的不足(和铜及铜合金相比)可以从合金化或者添加高导热率组分(比如碳纤维和石墨烯材料等等)来进行改善。本发明还提供了一种摩擦材料,所述摩擦材料包括衬体和复合在所述衬体表面的耐磨材料;所述耐磨材料为上述技术方案任意一项所述的耐磨材料。本发明上述摩擦材料中,采用的原料、加入方式以及参数条件的选择,及其相应的优选原则,如无特别注明,与本发明前述步骤提供的耐磨材料中的原料、加入方式以及参数条件的选择,及其相应的优选原则均优选一一对应,在此不再一一赘述。本发明原则上对摩擦材料没有特别限制,以本领域技术人员熟知的摩擦材料即可,本领域技术人员可以根据实际应用情况、技术要求和质量要求进行选择和调整,本发明所述摩擦材料优选包括传动摩擦材料或制动摩擦材料。本发明对所述衬体的定义和选择没有特别限制,以本领域技术人员熟知的摩擦材料的衬体或基体或基底的常规定义和选择即可,本领域技术人员可以根据实际应用情况、技术要求和质量要求进行选择和调整,本发明所述衬体的材质优选包括钢、合金钢、调质处理后的42crmov或30crmnsi。本发明还提供了一种摩擦材料的生产工艺,包括以下步骤:a)将活性金属包覆润滑组元复合材料粉末和镍合金基体粉末混合后,得到混合粉末;b)将上述步骤得到的混合粉末,采用等离子转移弧焊接在衬体表面后,得到摩擦材料。本发明上述生产工艺中,采用的原料、加入方式以及参数条件的选择,及其相应的优选原则,如无特别注明,与本发明前述步骤提供的耐磨材料或摩擦材料中的原料、加入方式以及参数条件的选择,及其相应的优选原则均优选一一对应,在此不再一一赘述。本发明首先将活性金属包覆润滑组元复合材料粉末和镍合金基体粉末混合后,得到混合粉末。本发明对所述活性金属包覆润滑组元复合材料粉末的来源没有特别限制,以本领域技术人员熟知的常规来源即可,本领域技术人员可以根据实际生产情况、技术要求和质量要求进行选择和调整,本发明所述活性金属包覆润滑组元复合材料粉末,优选由活性金属气雾化后对润滑组元粉末进行包覆后得到。本发明对上述包覆过程的具体步骤和参数不做特别限制。本发明为更好的提高耐磨材料的性能和应用范围,所述摩擦材料的耐磨材料中优选还包括铁和/或摩擦剂,更优选还包括铁和摩擦剂。即所述混合粉末中优选还包括铁粉和/或活性金属包覆摩擦剂复合材料粉末。具体可以为,将活性金属包覆润滑组元复合材料粉末、铁粉和/或活性金属包覆摩擦剂复合材料粉末、镍合金基体粉末混合后,得到混合粉末。本发明对所述活性金属包覆摩擦剂复合材料粉末的来源没有特别限制,以本领域技术人员熟知的常规来源即可,本领域技术人员可以根据实际生产情况、技术要求和质量要求进行选择和调整,本发明所述活性金属包覆摩擦剂复合材料粉末,优选由活性金属气雾化后对摩擦剂粉末进行包覆后得到。本发明对上述包覆过程的具体步骤和参数不做特别限制。本发明对所述混合的方式和参数没有特别限制,以本领域技术人员熟知的常规混合方式和参数即可,本领域技术人员可以根据实际生产情况、技术要求和质量要求进行选择和调整,本发明所述混合的方式优选为v型混合。本发明所述混合的时间优选为30~120分钟,更优选为50~100分钟,更优选为70~80分钟。本发明随后将上述步骤得到的混合粉末,采用等离子转移弧焊接在衬体表面后,得到摩擦材料。本发明对所述等离子转移弧焊接的参数没有特别限制,以本领域技术人员熟知的常规等离子转移弧焊接的参数即可,本领域技术人员可以根据实际生产情况、技术要求和质量要求进行选择和调整,本发明所述等离子转移弧焊接的电流优选为40~80a,更优选为45~75a,更优选为50~70a,更优选为55~65a。本发明上述步骤将混合粉末,采用等离子转移弧焊接在衬体表面后,可以直接成型,具体的可以采用手工或者自动的方式进行等离子转移弧焊接。在本发明中,当采用自动方式进行焊接时,等离子转移弧焊接的焊接途径和/或焊接参数可由计算机程序控制,或实现计算机远程中央控制。而且本发明中的混合粉末,采用等离子转移弧焊接在衬体表面后,可以在衬体表面形成特定设计的结构或形貌。同时,等离子转移弧焊接还可以实现,在衬体的两面进行等离子转移弧焊接。本发明为更好的提高最终产品的实用性,拓展应用领域,所述等离子转移弧焊接后,优选还包括后续加工工序。本发明对所述后续加工工序的具体步骤没有特别限制,以本领域技术人员熟知的常规后续加工工序即可,本领域技术人员可以根据实际生产情况、技术要求和质量要求进行选择和调整,本发明所述后续加工工序优选包括车、铣、刨、磨和钳工序中的一种或多种,更优选为车、铣、刨、磨和钳工序中的多种。本发明上述步骤提供了一种高强度耐磨材料、摩擦材料及其等离子转移弧焊接生产工艺。本发明采用等离子转移弧(pta)焊接的方式,并基于此得到了一种新型配方的耐磨材料与之相配合,改善了摩擦材料成型中润滑组元与基体的不润湿性,能够通过有效调节金属基体(即摩擦材料的强度)和摩擦材料中的石墨含量(即摩擦系数和磨损性能)等原料粉末的组分和pta操作参数,来生产对应不同工况和技术要求的摩擦材料,而且通过pta焊接技术,在摩擦材料的衬体表面直接成型,大大简化了工艺流程、极大地提高了生产效率,有效的改善当前制动摩擦材料的喷撒法和烧结技术等生产工艺存在的一致性差,工艺过程复杂,污染环境、工艺成本和人力成本高等诸多实际生产问题。同时使用程序化的pta加工方法还可以进行功能化设计摩擦副部件。实验结果表明,本发明采用pta加工后的摩擦材料,金属基体的硬度在hb180~280之间,石墨状态保存良好,室温下与钢的干摩擦系数在0.12~0.35之间。为了进一步说明本发明,以下结合实施例对本发明提供的一种耐磨材料、摩擦材料及其生产工艺进行详细描述,但是应当理解,这些实施例是在以本发明技术方案为前提下进行实施,给出了详细的实施方式和具体的操作过程,只是为进一步说明本发明的特征和优点,而不是对本发明权利要求的限制,本发明的保护范围也不限于下述的实施例。实施例1参见表1,表1为本发明实施例提供的原料配和pta堆焊工艺参数明细。表1镍包覆石墨粉的比例与权利要求1中有冲突其中,本发明石墨粉须经过活性金属包覆。在本发明实施例中采用的是镍气雾化对石墨粉进行包覆处理。参见图2,图2为本发明实施例1采用气雾化法制备的镍包覆石墨粉横截面组织图。其中,镍为75%和石墨25%,尺寸在45~90微米(镍的层厚为3~5微米)。按表1中的比例进行配料,得到混合料,并在表1中的pta电流下,将混合料在衬体表面进行pta堆焊,得到摩擦材料。对本发明实施例1中的混合料进行分析,从混合料取出粉末样品,制样,抛光来分析粉末形貌和尺寸分布。参见图3,图3为本发明实施例1配料后的混合料样品的横截面组织结构图。其中,白色亮圆球状为ni-cr-si-b合金球粉。对本发明实施例1制备的摩擦材料进行表征。参见图4,图4为本发明实施例1制备的摩擦材料的微观金相图。由图4可知,镍包覆石墨粉和镍基合金经过pta后的摩擦材料组织,可以看出石墨分布均匀,虽然石墨的分解和与基体的合金化严重,但是石墨球形保存很好,同时有蠕虫状石墨组织的析出很大程度改进了石墨与基体的界面结合。对本发明实施例1制备的摩擦材料进行性能检测。参见表2,表2为本发明实施例提供的摩擦材料的物理和机械性能。表2实施例1实施例2实施例3实施例4硬度,hb235221258268室温下与钢的干摩擦系数0.210.130.140.18实施例2参见表1,表1为本发明实施例提供的原料配和pta堆焊工艺参数明细。其中,本发明石墨粉须经过活性金属包覆。在本发明实施例中采用的是镍气雾化对石墨粉进行包覆处理。按表1中的比例进行配料,得到混合料,并在表1中的pta电流下,将混合料在衬体表面进行pta堆焊,得到摩擦材料。对本发明实施例2制备的摩擦材料进行表征。参见图5,图5为本发明实施例2制备的摩擦材料的微观金相图。由图5可知,镍包覆石墨粉和镍基合金经过pta后的摩擦材料组织,可以看出石墨分布均匀,而且石墨球形保存很好,同时有蠕虫状石墨组织的析出很大程度改进了石墨与基体的界面结合。对本发明实施例2制备的摩擦材料进行性能检测。参见表2,表2为本发明实施例提供的摩擦材料的物理和机械性能。实施例3参见表1,表1为本发明实施例提供的原料配和pta堆焊工艺参数明细。其中,本发明石墨粉须经过活性金属包覆。在本发明实施例中采用的是镍气雾化对石墨粉进行包覆处理。按表1中的比例进行配料,得到混合料,并在表1中的pta电流下,将混合料在衬体表面进行pta堆焊,同时通过计算机和控制系统对pta焊喷嘴的移动进行编程,一次性得到与设计相符的最终摩擦材料。对本发明实施例3制备的摩擦材料进行表征。参见图6,图6为本发明实施例3制备的摩擦材料的微观金相图。由图6可知,镍包覆石墨粉和镍基合金经过pta后的摩擦材料组织,可以看出石墨分布均匀,而且石墨球形保存很好,同时有蠕虫状石墨组织的析出很大程度改进了石墨与基体的界面结合。对本发明实施例3制备的摩擦材料进行性能检测。参见表2,表2为本发明实施例提供的摩擦材料的物理和机械性能。实施例4参见表1,表1为本发明实施例提供的原料配和pta堆焊工艺参数明细。其中,本发明石墨粉须经过活性金属包覆。在本发明实施例中采用的是镍气雾化对石墨粉进行包覆处理。本发明镍包覆氧化铝摩擦剂经过活性金属包覆。在本发明实施例中采用的是镍气雾化对氧化铝摩擦剂进行包覆处理。按表1中的比例进行配料,得到混合料,并在表1中的pta电流下,将混合料在衬体表面进行pta堆焊,同时通过计算机和控制系统对pta焊喷嘴的移动进行编程,一次性得到与设计相符的最终摩擦材料。对本发明实施例4制备的摩擦材料进行性能检测。参见表2,表2为本发明实施例提供的摩擦材料的物理和机械性能。以上对本发明提供的一种高强度耐磨材料、摩擦材料及其等离子转移弧焊接生产工艺进行了详细的介绍,本文中应用了具体个例对本发明的原理及实施方式进行了阐述,以上实施例的说明只是用于帮助理解本发明的方法及其核心思想,包括最佳方式,并且也使得本领域的任何技术人员都能够实践本发明,包括制造和使用任何装置或系统,和实施任何结合的方法。应当指出,对于本
技术领域:
的普通技术人员来说,在不脱离本发明原理的前提下,还可以对本发明进行若干改进和修饰,这些改进和修饰也落入本发明权利要求的保护范围内。本发明专利保护的范围通过权利要求来限定,并可包括本领域技术人员能够想到的其他实施例。如果这些其他实施例具有不是不同于权利要求文字表述的结构要素,或者如果它们包括与权利要求的文字表述无实质差异的等同结构要素,那么这些其他实施例也应包含在权利要求的范围内。当前第1页12