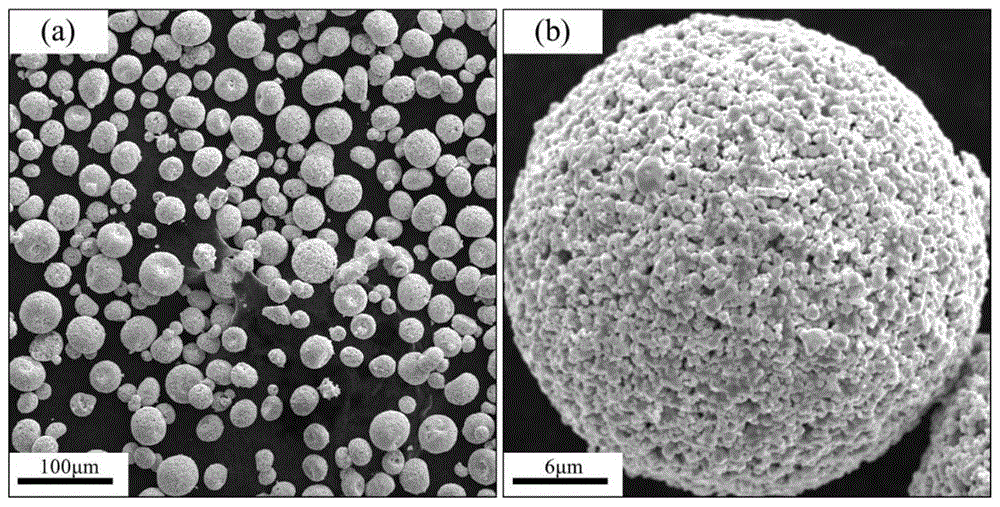
本发明涉及一种适用于3d打印的球形金属复合粉末的制备方法,属于金属粉末制备
技术领域:
。
背景技术:
:目前,钨铜复合材料的制备工艺主要为熔渗法以及粉末冶金法。然而,这两种制备方法都存在一定局限性,熔渗法易产生闭孔、铜池以及钨的团聚等问题。对粉末冶金烧结法而言,因钨铜之间较差的润湿性导致难以制得高致密钨铜块体复合材料。此外,某些部件所需的模具结构较为复杂使得工业制造成本较高。因此,目前有限的制备方法是制约钨铜复合材料获得更广泛应用的关键问题所在。选择性激光熔化(slm)是一种增材制造技术,其工作原理是通过预先设定的三维模型,控制激光束选择性融化粉末,通过逐层叠加的方式直接制造具有复杂结构的三维部件。这种成形方式可大幅度降低复杂零部件的生产成本并有效缩短生产周期,因此slm具有显著优势及潜力成为制备钨铜块体复合材料的新技术。对于slm而言,打印粉末的质量直接影响打印过程及打印件性能。例如,粉末需具有高球形度、高流动性以及较窄的粒径分布,以确保打印过程中铺粉环节的顺利进行。对于适用于slm的打印用粉末制备研究现状而言,主要通过两种方式获得,一种是将球形钨粉和铜粉机械混合作为初始打印粉末;另一种是直接在打印过程中将w、cu两种粉末铺粉至激光工作区作为初始粉末。目前尚未有关于球形钨铜复合粉末的制备方法报道,更缺乏将其用作3d打印初始粉末的研究。虽然目前有诸多制备球形金属粉末的方法,如气雾化法、等离子球化法等,但这些方法的共性是均需在金属粉末处于熔融态下完成球化,因此,这些方法不适用于熔点相差较大的两种组分的金属(如w熔点3422℃、cu熔点1084℃)形成复合粉末的制备。技术实现要素:针对上述领域背景,为了解决现有技术的局限,本发明提供了一种适用于3d打印需求的高纯度球形钨铜复合粉末的制备方法。本发明提供的制备方法的工艺流程和原理是:采用平均粒径均为0.5~3μm的钨粉和铜粉作为初始原料配制料浆,然后对料浆进行喷雾干燥,获得微米级别的钨铜复合粉末。通过调节雾化器频率等参数,控制造粒粉末的形貌以及粒径分布;最后对造粒后复合粉末进行热处理,通过脱胶和致密化固结作用,获得球形度、流动性和氧含量满足3d打印要求的球形钨铜复合粉末。本方法与其他工艺方法相比,可得到熔点差异较大的两相复合球形粉末,且粉末粒径易于控制,工艺流程简单,成本较低。本发明提供的一种适用于3d打印的球形钨铜复合粉末的制备方法,包括以下步骤:(1)将钨粉和铜粉按照一定化学比例进行配比(w:cu质量比为4:1~1:1),并与聚乙二醇20000、去离子水混合配制料浆,球磨1-2h后得到稳定料浆,金属粉末质量为料浆总质量的60%~75%,聚乙二醇20000为粉末质量的3%~4%;(2)对步骤(1)制备的料浆进行离心喷雾干燥,进风温度为120℃,雾化器频率45~60hz,进料速度15~25r/min,获得粒径在50μm以下的球形金属复合颗粒;(3)采用真空烧结炉对步骤(2)获得的球形颗粒进行两段式热处理,第一阶段在通氢气气氛下,热处理温度为400℃,保温时间1h;第二阶段在氩气气氛下进行,热处理温度为790~810℃,保温时间0.5~1h。最终得到高球形度和流动性的微米级球形钨铜复合粉末,可满足3d打印用粉末需求。目前虽然有制备球形钨合金粉末的喷雾干燥法等方法以及制备球形钨铜材料的包覆法等,但尚未有喷雾造粒法制备球形w-cu复合粉末的技术。与以往有关制备球形金属或合金粉末的方法相比,本发明的主要技术特色和优势有:(1)解决了熔点差异大且润湿性差的两种组分制备球形复合粉末的难题。由于熔点差异大,无法在熔融状态共存球化;同时,对喷雾干燥和热处理工艺的要求很高,相关制备参数及其组合并不能从已有的方法中外延得到,尤其是对温度、时间等的确定要求非常苛刻,既要保证cu适度熔化以起到固结粉末作用,同时温度又不能过高以免造成cu从粉末中脱出,从而导致cu与w分离,破坏球形结构。(2)选择微米级的铜粉和钨粉作为原材料,与其他造粒工艺使用纳米粉相比,大大降低了生产成本。(3)在料浆的配制过程中,聚乙二醇同时作为料浆中的有机粘结剂以及分散剂,避免金属粉末发生团聚,使其能在料浆中均匀分散。(4)稳定均匀料浆的制备对造粒粉末的形貌及粉末收得率有着至关重要的作用,本发明中,混料过程使用球磨工艺,可以避免大颗粒粉末沉入料浆底部,使有机粘结剂颗粒表面的吸附不平衡。(5)与将球形钨粉和球形铜粉进行简单的机械混合相比,造粒后复合粉末中钨与铜两相分布更为均匀,通过调控各工艺步骤的参数组合,可以制备球形度较好、高流动性,且满足不同粒径需求的适用于3d打印的钨铜复合粉末。(6)造粒后的热处理工艺,对最终获得满足3d打印要求的金属粉末非常重要。本发明中热处理温度是经过大量试验探索得到的,采用两阶段式热处理方式,第一阶段热处理是为了脱除有机粘结剂,在微正压氢气气氛下进行,氢气压力为1015mbar~1030mbar;第二阶段热处理的作用是使造粒粉末颗粒内部铜颗粒发生轻微熔化形成固相粘结,同时还需保证复合粉末颗粒间不发生整体烧结,避免形成卫星球,提高粉末品质。(7)本方法采用喷雾干燥工艺制粉,步骤简单,粉末的球形度和粒径分布可控性较强,相对于现有的球形金属粉末制备工艺,生产成本较低。附图说明图1本发明实施例1制备得到的球形w-30cu复合粉末的显微形貌图。图2本发明实施例1制备得到的球形w-30cu复合粉末的粒径分布统计图。图3本发明实施例2制备得到的球形w-40cu复合粉末的显微形貌图。图4本发明实施例2制备得到的球形w-40cu复合粉末的粒径分布统计图。表1本发明实施例1、实施例2得到的钨铜复合粉末颗粒的球形度、流动性检测结果。具体实施方式例1、将平均粒径均为1μm高纯钨粉和铜粉按照质量比为7:3的比例混合,与质量为3%金属粉末总质量的聚乙二醇20000和去离子水配制悬浊液料浆,金属粉末总质量占料浆质量的75%。混料球磨1h得到均匀稳定的悬浊液料浆,利用离心雾化干燥设备进行团聚造粒,进风温度为120℃,雾化器频率50hz,进料速度20r/min,获得球形复合粉末;采用真空烧结炉对喷雾干燥得到的粉末进行热处理,第一阶段热处理温度为400℃,通氢气气氛下保温1h,氢气压力为1030mbar;第二阶段热处理温度为800℃,氩气气氛下保温0.5h,得到高球形度和高流动性的微米级球形钨铜复合粉末。制备得到的复合粉末的显微形貌图和粒径分布统计图如图1和2。其球形度和流动性测量结果见表1。例2、将平均粒径均为1μm高纯钨粉和铜粉按照质量比为3:2的比例混合,与质量为4%金属粉末总质量的聚乙二醇20000和去离子水配制悬浊液料浆,金属粉末总质量占料浆质量的70%。混料球磨1h得到均匀稳定的悬浊液料浆,利用离心雾化干燥设备进行团聚造粒,进风温度为120℃,雾化器频率55hz,进料速度25r/min,获得球形复合粉末;采用真空烧结炉对喷雾干燥得到的粉末进行热处理,第一阶段热处理温度为400℃,通氢气气氛下保温1h,氢气压力为1020mbar;第二阶段热处理温度为790℃,氩气气氛下保温1h,得到高球形度和高流动性的微米级球形钨铜复合粉末。制备得到的复合粉末的显微形貌图和粒径分布统计图如图3和4。其球形度和流动性测量结果见表1。表1本发明实施例1和实施例2制备得到的金属粉末的物性参数球形度(%)流动性(s/50g)氧含量(%)实施例1>95450.03实施例2>95480.04当前第1页12