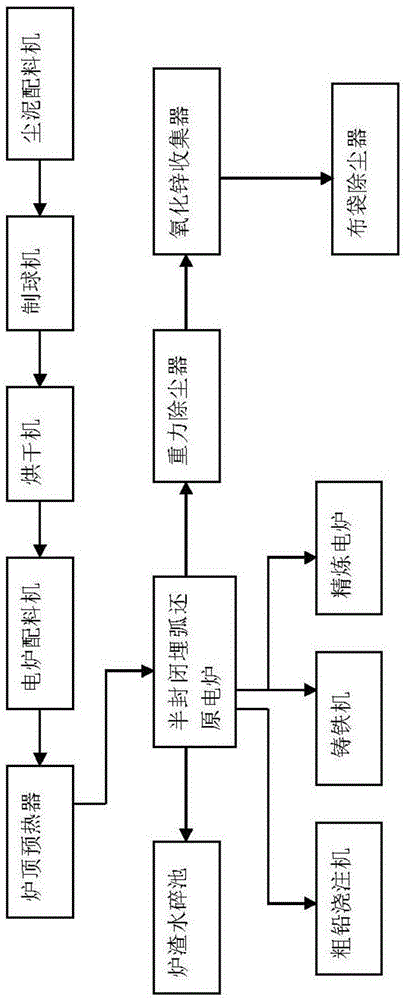
本实用新型涉及资源综合化利用和环境治理
技术领域:
,尤其是一种钢铁厂含锌尘泥电炉法回收氧化锌系统。
背景技术:
:钢铁厂尘泥主要来自于生铁高炉(瓦斯灰),炼钢转炉、炼钢电炉、烧结机、竖炉球团等工序的除尘环节。尘泥的含铁量tfe一般在25~70%之间,其中高炉、转炉及炼钢电炉产生的尘泥,除含铁外,还含有较高的锌、铅及碱金属等炼铁、炼钢生产中需控制的有害元素。钢铁厂尘泥产生量约为粗钢产量8~12%左右,以2018年9.28亿吨/a粗钢产量按10%计算,其年产尘泥约为9280万吨,其中含锌、铅尘泥约占4%左右,约3700万吨,其数量非常大,带来的环境压力也非常大。对于钢铁厂中的烧结、球团环节产生的尘泥,由于含铁量较高,含zn、pb等有害杂质较低,可直接进行返烧再利用,而对于高炉、电炉和转炉产生的尘泥,因含锌、铅等重金属杂质,含锌烧结难以有效地去除这些杂质,含锌烧结矿会影响高炉冶炼正常操作和炉衬寿命。因此,对这类冶金尘泥的处理,首先是需回收或除去尘泥中的重金属元素,其次再回收铁、碳等有价元素,方可实现环境治理及尘泥二次资源的有效利用。目前,国内外对钢铁厂含锌、铅尘泥的处理工艺主要分物理法、湿法、火法三种工艺方法。物理法工艺的主要缺点是锌的富集率较低,因此,物理法一般只作为湿法或火法工艺的预处理工艺。湿法工艺主要是利用尘泥中氧化锌两性氧化物的特性,采用酸浸或碱浸富集锌,湿法只适合于处理含锌≥10%以上的尘泥,且运营成本高,单机产能低,环境治理难度大,且尘泥中铁、碳元素浪费大。因此,钢铁厂尘泥一般未采用湿法处理。火法工艺是在高温还原条件下,使锌氧化物被还原而实现与铁等固相分离,锌回收率高,铁、碳等有价元素均可得到回收利用,投资及运营成本较低,适合钢铁厂尘泥的处理。目前,国内外用火法工艺处理钢铁厂含锌、铅尘泥的典型工艺主要有以下二种。(一)回转窑工艺回转窑工艺回收含锌废物中的氧化锌是一种传统成熟的生产工艺,含锌尘泥在回转窑1300℃左右高温下,其氧化锌被碳及一氧化碳还原成锌蒸气进入气相而得到富集回收,含铁尘泥经除去锌后作为炉渣经冷却后再磁选或重选富集后回用,炉渣金属化率较低,约40%左右,附加值低。因此,回转窑法回收尘泥中的锌元素,其锌含量低于10%会出现亏本,该方法只适合于处理高锌尘泥。(二)转底炉法、转底炉工艺是近30年来新发展起来的直接还原铁工艺,该工艺适用在含锌、铁尘泥的处理上,可以实现尘泥的除锌、尘泥中的铁金属化率较回转窑高,可达到70%左右,但尘泥中铅仍只能进入烟尘回收,利用率较低。以上二种典型的生产工艺虽可实现尘泥中锌、铅元素的去除,但由于还原后矿球金属化率仍仅40~80%,总体资源利用效率仍较低,经济效益较差。为了获得较高的资源利用效率,北京科技大学在公告号cn1034889618实用新型专利中提供了《一种密闭冲天炉处理钢铁厂含锌、铅粉尘工艺方法》。该方法是以钢铁厂含锌、铅尘泥为主要原料,配加一定量焦炭作还原剂,经混合制球、矿球经炉顶预热处理后,送入密闭冲天炉进行冶炼,冲天炉炉顶锌蒸汽经铅雨冷凝器,冷凝回收粗锌,铁水、粗铅、炉渣定期从炉缸中排出,铁水和粗铅经浇铸成型获得生铁及粗铅产品,炉渣经水碎后作建筑材料利用。该方法较“回转窑法”和“转底炉法”相比较,最大的特点是尘泥资源得到了有效利用,生产产品的附加值较高,金属元素回收率较高。然而,该方法存在的不足之处在于:1、碳排放高,能耗较高。由于冲天炉熔炼是由底焦燃烧,热量交换和冶金反应三个基本过程组成,其高温还原条件完全靠焦炭燃烧及热风炉风温提供,能源消耗及碳排放高,生产成本较高,环境治理难度较大;2、单炉产量低,难以实现规模化工业生产。冲天炉由于属铸造行业中一种铸件熔炼设备,无法实现大型化和规模化生产;3、基建占地面积大,由于冲天炉除炉本体外,还需配套热风系统建设,基建占地面积大。技术实现要素:针对现有技术的情况,本实用新型的目的在于提供一种环境友好、单炉产能高、生产成本低,且能实现资源二次利用和可产业化规模生产的钢铁厂含锌尘泥电炉法回收氧化锌系统。为了实现上述的技术目的,本实用新型所采用的技术方案为:钢铁厂含锌尘泥电炉法回收氧化锌系统,其包括半封闭埋孤还原电炉、炉渣水碎池、重力除尘器、氧化锌收集器、粗铅浇注机和铸铁机,所述的半封闭埋弧还原电炉具有氧化锌气体出口、出铁口、出渣口和出铅口,其中,氧化锌气体出口、出渣口、出铁口和出铅口在水平方向上的投影为由上至下依序设置,所述的氧化锌气体出口与重力除尘器连接,重力除尘器与氧化锌收集器连接,所述的出渣口与炉渣水碎池连接,所述的出铁口与铸铁机连接,所述的出铅口与粗铅浇注机连接。作为实施之一,其还包括依序设置且相互连接的尘泥配料机、制球机、烘干机、电炉配料机,所述电炉配料机的出料口与半封闭埋弧还原电炉连接。即,本实用新型方案送入半封闭埋弧还原电炉的物料可以是半成品物料,也可以直接是原始物料进行依序处理后,送入半封闭埋弧还原电炉中。其中,所述的尘泥配料机、制球机、烘干机、电炉配料机、铸铁机、粗铅浇注机均为常规的冶金设备,其可以根据生产规模进行设计选型,便不一一赘述。进一步,所述的出铁口与铸铁机之间还设有一连接支路且该连接支路上连接有精炼调制电炉,进一步,所述精炼调制电炉与半封闭埋弧还原电炉配套,用于生铁铁水脱磷、脱硫,成份调制及铁水热兑保温使用。进一步,所述的氧化锌收集器还连接有布袋除尘器。进一步,所述的电炉配料机与半封闭埋弧还原电炉之间还连接有用于预热物料的炉顶预热器,用于尘泥矿球入电炉前进行预热处理。进一步,所述的半封闭埋弧还原电炉为直流电半封闭埋弧还原电炉或交流电半封闭埋弧还原电炉。进一步,所述半封闭埋弧还原电炉为专门用于尘泥熔炼的非标设备,设备的各项工艺参数根据尘泥成份结构及年处理量,尘泥冶金性能进行设计制造。尤其是,半封闭埋弧还原电炉的冶炼过程为埋弧操作,与加热为高温电弧加热的敞弧电炉区别在于其高温热源既来源电弧也来源于炉料和炉渣的电阻热,因此电炉还原温度低,炉料还原反应充分,金属元素回收率高,从而使尘泥中铅金属元素得以从炉底回收粗铅。进一步,所述的半封闭埋弧还原电炉包括:炉体,其上端具有呈凹形结构的炉腔,所述炉腔的下部侧面设有出渣口和出铁口,其中,出渣口和出铁口在水平方向上的投影为出渣口在上,出铁口在下,另外,炉腔的下方设有一集铅槽,所述的集铅槽水平延伸出炉体且形成出铅口;集铅槽与炉腔下部之间布设有碳砖层;炉盖,盖设于炉腔上方并与炉体上端面具有间隙,所述的间隙处形成氧化锌气体出口,所述的氧化锌气体出口用于放出锌蒸汽;自焙电极,其一端由炉盖穿入到炉腔中部;下料管,输出端穿入炉盖且延伸至炉腔上部。进一步,所述的炉体为耐火砖砌成,集铅槽水平延伸处与出渣口或出铁口的对应位置设有隔离层。需要说明的是:本方案的系统还可以用于不锈钢含锌尘泥回收氧化锌和含铬生铁。钢铁厂含锌尘泥电炉法回收氧化锌系统的运行方法,其包括如下步骤:(1)通过尘泥配料机将尘泥中的瓦斯灰、转炉灰、电炉灰、粉煤或焦粉中的一种以上,按比例搭配,并配以尘泥质量3%~8%的粘合剂进行混均后输送至制球机;(2)通过制球机将尘泥配料机输出的物料进行制成矿球,然后输入到烘干机中;(3)通过烘干机对制球机输入的矿球进行烘干和预还原处理,再将处理后的物料输入到电炉配料机中;(4)通过电炉配料机将造渣剂、还原剂与处理后的矿球进行混合并输入到半封闭埋弧还原电炉中或经炉顶预热器预热后,再输入到半封闭埋弧还原电炉中;(5)半封闭埋弧还原电炉对输入的物料进行冶炼;(6)通过出渣口放出冶炼炉渣;(7)通过出铁口放出冶炼生成的铁水;(8)通过氧化锌气体出口将冶炼生成的锌蒸汽输出并经重力除尘器获得氧化锌,继而输送至氧化锌收集器中;(9)通过出铅口放出粗铅。进一步,步骤(7)还包括对生成的铁水进行检测,对不符合预设要求的铁水需进行精炼,对符合预设要求的铁水进行浇注成生铁,或热兑或成型成铸件。进一步,所述粉煤或焦粉的固定碳≥75%,灰份≤15%,尘泥成份应满足tfe≥45%,zn≥4%,1.1≤c/o≤1.3。进一步,步骤(4)中造渣剂应根据尘泥矿球化学成份,按炉渣碱度r=cao/sio2=1~1.2进行调整计算,造渣剂可以为硅石或石灰石(白云石)等,还原剂为焦炭,炭的配入量根据尘泥矿球含碳和氧的成份,碳/氧<1%时,应配入焦碳,碳/氧=1.1~1.4范围调整。进一步,步骤(5)中电炉还原冶炼时间2.5~4小时/炉,冶炼温度为1200℃~1450℃,优选的:矿球进入电炉炉顶经预热器煤气燃烧预热矿球至400℃左右进入电炉炉膛熔炼。进一步,如还原电炉容量设计日处理尘泥矿球>100吨/d,则设计出渣口与出铁口分开,电炉熔炼时间完成(按炉次)应先进行出渣操作,出完渣再进行出铁操作,如日处理矿球量≤100t/d,则出渣出铁为一个出口,步骤(6)和步骤(7)一并操作。进一步,对于步骤(7)如生铁铁水成份不符合相关标准或不符合客户要求,可进行精炼操作。需要进一步说明的是,如果生铁铁水用于直接热兑至炼钢车间,精炼电炉还可作为生铁铁水的贮存和保温,如果生产铸造生铁铁水,可通过精炼炉调制保温进行铸件直接浇注。进一步,步骤(8)氧化锌回收操作每4~8小时回收一次,根据尘泥含锌量决定回收操作时间。尤其是粗铅回收操作为2~5天开一次铅眼,视尘泥含铅量确定。采用上述的技术方案,本实用新型与现有技术相比,其具有的有益效果为:1、采用本实用新型系统及对于方案进行的锌、铅、铁金属元素回收率高,回收率≥95%;2、本实用新型系统使用尘泥生产的生铁及氧化锌、粗铅附加值高,尘泥资源得到了高效利用;3、本实用新型系统生产的生铁铁水可按相关标准和客户具体要求控制;4、应用本实用新型系统的钢厂自身处理尘泥可实现铁水热兑;5、本实用新型系统生产成本低,经济效益好。附图说明下面结合说明书附图和具体实施方式对本实用新型方案做进一步的阐述:图1为本实用新型系统的简要设备连接和物料传输方向示意图;图2为本实用新型系统的半封闭埋弧还原电炉冶炼原理和简要结构示意简图;图3为本实用新型系统的实施步骤流程图。具体实施方式如图1所示,本实用新型系统包括依序设置且相互连接的尘泥配料机、制球机、烘干机、电炉配料机和半封闭埋孤还原电炉;其还包括炉渣水碎池、重力除尘器、氧化锌收集器、粗铅浇注机和铸铁机,所述的半封闭埋弧还原电炉具有氧化锌气体出口、出铁口、出渣口和出铅口,其中,氧化锌气体出口、出渣口、出铁口和出铅口在水平方向上的投影为由上至下依序设置,所述的氧化锌气体出口与重力除尘器连接,重力除尘器与氧化锌收集器连接,所述的出渣口与炉渣水碎池连接,所述的出铁口与铸铁机连接,所述的出铅口与粗铅浇注机连接。其中,所述的尘泥配料机、制球机、烘干机、电炉配料机、铸铁机、粗铅浇注机均为常规的冶金设备,其可以根据生产规模进行设计选型,便不一一赘述。进一步,所述的出铁口与铸铁机之间还设有一连接支路且该连接支路上连接有精炼调制电炉,进一步,所述精炼调制电炉与半封闭埋弧还原电炉配套,用于生铁铁水脱磷、脱硫,成份调制及铁水热兑保温使用。另外,所述的氧化锌收集器还连接有布袋除尘器;进一步,所述的电炉配料机与半封闭埋弧还原电炉之间还连接有用于预热物料的炉顶预热器,用于尘泥矿球入电炉前进行预热处理;进一步,所述的半封闭埋弧还原电炉为直流电半封闭埋弧还原电炉或交流电半封闭埋弧还原电炉。再者,所述半封闭埋弧还原电炉为专门用于尘泥熔炼的非标设备,设备的各项工艺参数根据尘泥成份结构及年处理量,尘泥冶金性能进行设计制造。尤其是,半封闭埋弧还原电炉的冶炼过程为埋弧操作,与加热为高温电弧加热的敞弧电炉区别在于其高温热源既来源电弧也来源于炉料和炉渣的电阻热,因此电炉还原温度低,炉料还原反应充分,金属元素回收率高,从而使尘泥中铅金属元素得以从炉底回收粗铅。结合图2所示,本实用新型系统的半封闭埋弧还原电炉包括:炉体1,其上端具有呈凹形结构的炉腔11,所述炉腔11的下部侧面设有出渣口13和出铁口14,其中,出渣口13和出铁口14在水平方向上的投影为出渣口13在上,出铁口14在下,另外,炉腔11的下方设有一集铅槽151,所述的集铅槽151水平延伸出炉体且形成出铅口15;集铅槽151与炉腔11下部之间布设有碳砖层2;炉盖16,盖设于炉腔11上方并与炉体1上端面具有间隙,所述的间隙处形成氧化锌气体出口12,所述的氧化锌气体出口12用于放出锌蒸汽;自焙电极3,其一端由炉盖16穿入到炉腔11中部;下料管4,输出端穿入炉盖16且延伸至炉腔11上部。其中,所述的炉体1为耐火砖砌成,集铅槽151水平延伸处与出渣口13或出铁口14的对应位置设有隔离层21。需要说明的是:本方案的系统还可以用于不锈钢含锌尘泥回收氧化锌和含铬生铁。该半封闭埋弧还原电路的炉腔11内在冶炼的时候,对应形成不同的冶炼区,分别为:①铁水区;②料渣区;③高温还原反应区(温度大致在1350~1650℃);④炉料预还原反应与熔化区(温度大致在1200~1350℃);⑤渣皮及烧结区(温度大致在900~1200℃);⑥炉料预热区(温度大致在600~900℃);⑦炉料区(温度大致在400~600℃)。钢铁厂含锌尘泥电炉法回收氧化锌系统的运行方法,其包括如下步骤:(1)通过尘泥配料机将尘泥中的瓦斯灰、转炉灰、电炉灰、粉煤或焦粉中的一种以上,按比例搭配,并配以尘泥质量3%~8%的粘合剂进行混均后输送至制球机,其中,所述粉煤或焦粉的固定碳≥75%,灰份≤15%,尘泥成份应满足tfe≥45%,zn≥4%,1.1≤c/o≤1.3;(2)通过制球机将尘泥配料机输出的物料进行制成矿球,然后输入到烘干机中;(3)通过烘干机对制球机输入的矿球进行烘干和预还原处理,再将处理后的物料输入到电炉配料机中;(4)通过电炉配料机将造渣剂、还原剂与处理后的矿球进行混合并输入到半封闭埋弧还原电炉中或经炉顶预热器预热后,再输入到半封闭埋弧还原电炉中,造渣剂应根据尘泥矿球化学成份,按炉渣碱度r=cao/sio2=1~1.2进行调整计算,造渣剂可以为硅石或石灰石(白云石)等,还原剂为焦炭,炭的配入量根据尘泥矿球含碳和氧的成份,碳/氧<1%时,应配入焦碳,碳/氧=1.1~1.4范围调整;(5)半封闭埋弧还原电炉对输入的物料进行冶炼,其中,电炉还原冶炼时间2.5~4小时/炉,冶炼温度为1200℃~1450℃,优选的:矿球进入电炉炉顶经预热器煤气燃烧预热矿球至400℃左右进入电炉炉膛熔炼;(6)通过出渣口放出冶炼炉渣;(7)通过出铁口放出冶炼生成的铁水,对生成的铁水进行检测,对不符合预设要求的铁水需进行精炼,对符合预设要求的铁水进行浇注成生铁,或热兑或成型成铸件,需要进一步说明的是,如果生铁铁水用于直接热兑至炼钢车间,精炼电炉还可作为生铁铁水的贮存和保温,如果生产铸造生铁铁水,可通过精炼炉调制保温进行铸件直接浇注;(8)通过氧化锌气体出口将冶炼生成的锌蒸汽输出并经重力除尘器获得氧化锌,继而输送至氧化锌收集器中;(9)通过出铅口放出粗铅。其中,氧化锌回收操作每4~8小时回收一次,根据尘泥含锌量决定回收操作时间。尤其是粗铅回收操作为2~5天开一次铅眼,视尘泥含铅量确定;进一步,如还原电炉容量设计日处理尘泥矿球>100吨/d,则设计出渣口与出铁口分开,电炉熔炼时间完成(按炉次)应先进行出渣操作,出完渣再进行出铁操作,如日处理矿球量≤100t/d,则出渣出铁为一个出口,步骤(6)和步骤(7)一并操作。本实用新型方案所提及的钢铁厂含锌尘泥的主要化学成分如以下表1所示:表1钢铁厂含锌尘泥化学成分表以下结合具体运算实例对本实用新型方案做进一步的直观表述。实施例1本实施例1使用表1尘泥搭配,使用电炉设备后为半封闭埋孤还原电炉,电炉处理能力为60000吨/a(按300天/a计),处理数量按10000吨计算。根据表1中各尘泥的化学成份,本实施例选用高炉瓦斯灰40%,转炉尘泥30%,电炉尘泥30%配比进行混匀制球,混合矿球的数量及化学成份经加权平均计算见下表2所示。表2尘泥混合球主要成份表单位:%按照图3所示工艺流程图,将表2中混合球经烘干机烘干(h20=o)后,配矿球重量的5%焦丁(兰炭)作还原剂,配矿球重量的2%硅石作造渣剂,其中还原剂c=82%,灰份=14.5%,硅石sio2=97.5%,每批混合球按500kg重,经plc电炉配料机进行配料,电炉配料单如下表3所示表3电炉配料表本配料计算炉渣碱度r=ca+mg/sio2=1.24。将上述配料单配好的混合料由电炉自动送料机送至炉顶加热器预热混合料至500℃左右,再经下料管送至半封闭埋孤还原电炉进行冶炼,其中:冶炼温度控制在1350℃~1700℃间,冶炼时间为3.5小时/炉(其中2.5小时由出渣口出一次渣,3.5小时出铁),氧化锌每8小时回收一次,粗铅经电炉排铅口回收,每3天回收一次,冶炼炉渣经水碎池水碎后作建筑材料。还原电炉的冶炼原理及温度分布详见图2。本实施例处理尘泥回收的氧化锌及生铁、粗铅产品见下表4所示表4产品及原料耗用统计表名称混合球焦丁硅石生铁氧化锌粗铅数量(t)10000500200471847370金属回收率95%92%94%注:氧化锌含zn≥97%,粗铅pb≥96%有益效果分析:一、本实施例生产的产品价值计算1、生铁4718t×2655元/吨=1252.62万元;(生铁不含税单价:2655元/吨);2、氧化锌:473吨×8420元/吨=398.27万元;(氧化锌不含税单价:8420元/吨);3、粗铅:74t×14697元/吨=108.76万元。(粗铅不含税单价:14697元/吨)。合计:不含税产品价值σ108.76+398.27+1252.63=1759.65万元二、本实施例1生产加工成本计算吨尘泥加工成本计算见下表5所示表5每吨尘泥加工成本计算表序号名称数量单位单价金额(元)备注1电费1200度0.50600(不含税)2焦丁0.05吨140070(不含税)3电极糊0.03吨3500105(不含税)4钢材0.007吨350024.50(不含税)5硅石0.02吨3006(不含税)6劳保、低易品17.67设备维修17.68工资609管理费1010折旧50按年处理量6万吨折11财务费用2012税费25(增值税和附加费)13合计1005.70本实施例共加工尘泥10000吨,共需支付成本费用为:σ10000万吨×1005.70元/吨=1025.7万元。三、经济效益计算:1、产品、不含税收入(按表4及市场价)计算合计:1759.56万元;2、毛收入=1759.65万元-1005.7万元=753.95万元;3、应缴所得税为:753.95×25%=188.49万元;4、创利=753.95万元-188.49万元=565.46万元;由此可见,本实用新型系统所产生的经济效益显著。实施例2本实施例仍以实施例1中表1尘泥、实施数量仍为10000吨,其余工艺操作步骤与实施例1相同,不同的是本实施例选用的高炉瓦斯灰50%,电炉灰50%,搭配尘泥混合球成份见下表6所示表6尘泥混合球主要成份表名称数量(t)tfefe0fe203znpbcpscaomyosio2al2o3混合球1000041.319.8548.064.711.29515.230.0960.543.9351.124.191.325本实施例电炉配料单见表7所示表7电炉配料单r=cao+mgo/r=1.25本实施例造渣剂使用白云石,还原剂与实施例1相同。本实施例电炉还原冶炼及氧化锌、粗铅回收操作与实施例1相同本实施例生产的产品及原料耗用见下表8表8产品及原料耗用统计表名称混合球焦丁白云石生铁氧化锌粗铅数量(t)100008002004219621.25126金属回收率95%92%94%注:氧化锌含zn≥97%,粗铅pb≥96%有益效果:一、产品收入(不含税)1、生铁:4219吨×2655/吨=1120万元;(生铁不含税单价:2655元/吨);2、氧化锌:621.5吨×8420元/吨=523.09万元;(氧化锌不含税单价:8420元/吨);3、粗铅:126吨×14697=185.18万元。((粗铅不含税单价:14697元/吨);合计收入=1120+523.09+185.18=1828.27万元。二、成本方面本实施例增加焦丁消耗300吨,成本增加300×1400=42万元,其它成本与实施例1相同,总成本费用合计=1005.7万元+42万元=1047.7万元。三、效益比较本实施例利润为:毛利=1828.27万元-1047.7万元=780.57万元,所得税=780.57万元×0.25=195.14万元;纯利=585.43万元。实施例3本实施例选用一种高炉瓦斯灰,各工艺步骤仍与实施例1完全相同,但因尘泥化学成份不一样,产生的产品收益和成本有所不同。表9本实施例矿球主要成份表名称数量(t)tfefeofe2o3znpbcpscaomgosio2al2o3矿球1000035.210.4538.826.610.9430.210.1011.044.310.866.252.13根据表10所示,本实施例的电炉配方见下表10表10电炉配料单其中,瓦斯灰碳已过剩,不需再配碳。本实施例生产产品及消耗见统计表11所示表11名称瓦斯灰焦丁白云石生铁氧化锌粗铅数量(t)10000/1000353088990金属回收率93%94%92%注:氧化锌含zn≥97%,粗铅pb≥96%有益效果:一、产品收入(不含税)1、生铁:3530.25t×2655元/t=937.2万元;(生铁不含税单价:2655元/吨);2、氧化锌:889t×8420元/t=748.53万元;(氧化锌不含税单价:8420元/吨);3、粗铅:90t×14697元/t=132.27万元;不含税单价:14697元/吨);合计收入=1818万元。二、成本方面1、节约焦丁(与实施例1比较)500t×1400=70万元,节约硅石200t×300=6万元;2、增加白云石用量1000吨×200=20万元;两项相抵后,成本费可节约:76万元-20万元=50万元。本实施例成本费用=1005.70万元-50万元=955.7万元。三、效益计算1、毛利=1818万元-955.7万元=862.3万元;2、(增值税)=862.3×0.25=215.58万元;3、纯利润=646.72万元;综上所述,以上三种实施方式随着尘泥混合锌量的增加,利润税收随之增加,若按平均值计算:(1)(实施例1)、(实施例2)、(实施例3)平均纯利为:(565.64十585.43十646.72)/3=599.26万元;(2)平均税费为:(188,49+195.14+215.58)/3=199.73万元(所得税)+30万元(增值税)=229.74万元。按全年全国钢铁厂以上三种尘泥年产废量3700万吨计算,则采用本实用新型专利技术,年创利润599.26×3700万=221.亿元,年交税费229.74×3700万元=85亿元。以上描述了本实用新型的具体实施方式,但是本领域的技术人员应当理解,这仅是举例说明,本领域的技术人员在不背离本实用新型的原理和实质的前提下,可以对此实施方式做出多种变更或修改,但这些变更和修改均落入本实用新型的保护范围。当前第1页12