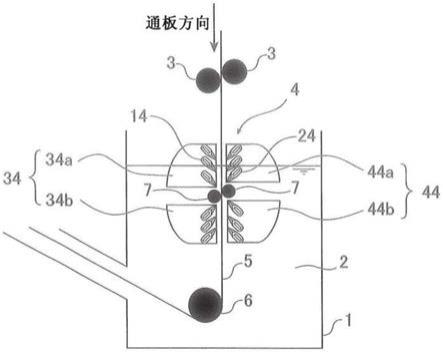
1.本发明涉及将金属板在连续进行通板的同时进行退火的连续退火设备中的淬火装置和淬火方法以及钢板的制造方法。
背景技术:2.在以钢板为代表的金属板的制造中,在连续退火设备中,将金属板加热后进行冷却,引起相变等,从而进行材质的改善。近年来,在汽车业界,为了兼顾车身的轻量化与碰撞安全性,薄壁化的高张力钢板(高张力钢板,high tensile strength steel sheets)的需求增加。在高张力钢板的制造时,将钢板快速冷却的技术变得重要。作为钢板的冷却速度最快的技术之一,已知水淬法。水淬法中,在将加热后的钢板浸渍在水中的同时,利用设置在水中的淬火喷嘴将冷却水向钢板喷射,由此进行钢板的淬火。在钢板的淬火时,存在钢板产生翘曲、波状变形等形状不良的问题。为了防止这样的钢板淬火时的形状不良,以往提出了各种各样的方法。
3.例如,在专利文献1中,为了抑制连续退火炉中的淬火时产生的金属板的波状变形,作为被供于淬火工序的钢板的张力变更手段,提出了在淬火部前后设置张力辊的方法。另外,在专利文献2中提出了通过在淬火时对钢板的表面和背面的至少宽度方向的全部区域赋予张力而将钢板矫正为平坦状的方法。另外,在专利文献3中提出了通过将淬火中的金属板利用一对约束辊进行约束而防止钢板的变形的方法。
4.但是,专利文献1记载的方法中,可能会由于对高温的钢板赋予大的张力而引起钢板的断裂。另外,与高温的钢板接触的淬火部前的张力辊产生大的热凸度,导致张力辊与钢板在宽度方向上不均匀地接触。结果存在如下问题:在钢板产生压弯、缺陷,因此,无法改善钢板形状。
5.另外,专利文献2记载的方法中,通过将张力设定为15n/mm2而使翘曲量减少至数mm程度,但可能由于这样的高张力而使钢带产生扭曲。
6.另外,专利文献3记载的方法中,虽然能够防止淬火时的钢板的变形,但金属板从约束辊通过时,一时地金属板的冷却速度降低,由此存在金属板的特性降低的问题。具体而言,有时会因金属板的冷却速度的降低而无法得到具有期望的拉伸强度的金属板。
7.本申请人在专利文献4中公开了用于解决这些问题的技术。在专利文献4中提出了如下方法:将淬火中的金属板利用一对或两个以上约束辊进行约束,并且从最靠近约束辊的喷嘴朝向约束辊一方倾斜地喷出液体。
8.现有技术文献
9.专利文献
10.专利文献1:日本特开2011
‑
184773号公报
11.专利文献2:日本特开平11
‑
193418号公报
12.专利文献3:日本专利第6094722号公报
13.专利文献4:日本特开2017
‑
119912号公报
技术实现要素:14.发明所要解决的问题
15.但是,专利文献4记载的方法中,虽然能够防止淬火时的钢板的变形、并且抑制约束辊附近处金属板的冷却速度的降低,但存在金属板的板宽方向的冷却速度变得不均匀的问题。具体而言,金属板的边缘部的冷却速度与中央部相比变高,由于冷却速度的不均匀性,金属板的边缘部的拉伸强度与中央部相比有时变高。
16.本发明人为了解决这样的问题而反复进行了深入研究,结果得出如下所述的见解。约束辊与金属板在板宽方向整面进行接触,因此,从与约束辊相邻的喷嘴喷出的水的出路仅是金属板的板宽方向,与金属板的中央部碰撞的水横向流动。因此,金属板上的冷却速度具有金属板的边缘部与中央部相比变高的倾向。
17.本发明是基于上述的见解而完成的。即,本发明的课题在于提供能够抑制在淬火时金属板所产生的形状不良、并且能够在抑制金属板的冷却速度的降低的同时防止金属板的板宽方向的冷却速度的不均匀性的淬火装置和淬火方法以及钢板的制造方法。
18.用于解决问题的方法
19.用于解决上述问题的方法如下所述。
20.[1]一种淬火装置,其具备:
[0021]
收容有浸渍高温金属板的液体的槽;
[0022]
至少一部分设置在上述槽的液体中且具备向上述金属板的两面喷射上述液体的两个以上喷嘴的喷出装置;和
[0023]
设置在上述喷出装置的入口侧端部与出口侧端部之间且将上述金属板从两面夹住的约束辊,
[0024]
上述喷出装置中,至少与上述约束辊相邻的喷嘴从与上述金属板垂直的方向朝向上述约束辊一方倾斜,
[0025]
上述约束辊在辊表面具有使从上述相邻的喷嘴喷出的液体沿着上述金属板的长度方向流出的沟槽。
[0026]
[2]如上述[1]所述的淬火装置,其中,上述沟槽为围绕上述约束辊的轴的轮形,包含上述轮形的平面相对于上述约束辊的轴垂直。
[0027]
[3]如上述[1]所述的淬火装置,其中,上述沟槽为围绕上述约束辊的轴的轮形,包含上述轮形的平面相对于上述约束辊的轴倾斜。
[0028]
[4]如上述[2]或[3]所述的淬火装置,其中,上述沟槽的宽度为10mm以上且50mm以下、深度为5mm以上且30mm以下,沿着上述约束辊的轴线方向的沟槽的间隔为50mm以上且200mm以下。
[0029]
[5]如上述[1]所述的淬火装置,其中,上述沟槽为以上述约束辊的轴为中心的螺旋状。
[0030]
[6]如上述[5]所述的淬火装置,其中,上述沟槽的宽度为10mm以上且50mm以下、深度为5mm以上且30mm以下,与沿着上述约束辊的轴线方向的一周前的沟槽的间隔为50mm以上且200mm以下。
[0031]
[7]如上述[1]~[6]中任一项所述的淬火装置,其中,与上述约束辊相邻的喷嘴的液体喷出方向与上述金属板所形成的角度为20
°
以上且60
°
以下。
[0032]
[8]一种淬火方法,其中,使用上述[1]~[7]中任一项所述的淬火装置进行骤冷淬火。
[0033]
[9]一种钢板的制造方法,其中,在制造钢板时,使用上述[8]所述的淬火方法。
[0034]
发明効果
[0035]
根据本发明,能够抑制在淬火时金属板所产生的形状不良、并且能够在抑制金属板的冷却速度的降低的同时防止金属板的板宽方向的冷却速度的不均匀性。
附图说明
[0036]
图1是表示本发明的一个实施方式的淬火装置的基本构成的说明图。
[0037]
图2是表示图1的喷出装置的附近的放大图。
[0038]
图3是从侧面观察本发明的一个实施方式中的约束辊的一例的放大图。
[0039]
图4是从侧面观察本发明的一个实施方式中的约束辊的其他例的放大图。
[0040]
图5是从侧面观察以往的约束辊的放大图。
[0041]
图6是表示本发明例1的结果的图。
[0042]
图7是表示本发明例2的结果的图。
[0043]
图8是表示比较例1的结果的图。
[0044]
图9是表示比较例2的结果的图。
[0045]
图10是表示比较例3的结果的图。
[0046]
图11是表示本发明例1、2和比较例1~3的结果的图。
[0047]
图12是从搬运方向正对地观察钢板的示意图。
具体实施方式
[0048]
以下,参考附图对本发明的一个实施方式具体地进行说明。
[0049]
图1是表示本发明的一个实施方式的淬火装置的基本构成的图。图2是图1所示的淬火装置的喷出装置4附近的放大图。淬火装置可以应用于设置在连续退火炉的均热区的出口侧的冷却设备。图1中示出设置在连续退火炉的均热区的出口的一对密封辊3。淬火装置具备收容有作为用于冷却金属板5的冷却介质(液体)的水2的水槽1、用于对金属板5的两面喷吹水2而进行冷却的喷出装置4和对金属板5进行约束而防止变形的约束辊7。喷出装置4的至少一部分设置在槽1的液体中(水2中)。另外,在喷出装置4的出口侧设置使金属板5浸渍在水中并且改变金属板5的搬运方向(通板方向)的沉没辊6。
[0050]
喷出装置4包含喷出水的两个以上喷嘴14、24以及保持喷嘴14、24的喷嘴单元34、44。在一对喷嘴单元34与44之间设置有间隙。在金属板5从上述间隙中通板时,从喷嘴14、24朝向金属板5的表面和背面喷出水。图1和图2的例子中,将金属板5的左侧设定为表面,将右侧设定为背面。在图的左侧,以使喷嘴14朝向金属板5的表面的方式配置喷嘴单元34,在图的右侧,以使喷嘴24朝向金属板5的背面的方式配置喷嘴单元44。
[0051]
图1和图2的例子中,喷嘴单元34和44各自沿着搬运方向被分割为各2个。在金属板5的表面侧设置入口侧喷嘴单元34a和出口侧喷嘴单元34b,在背面侧设置入口侧喷嘴单元44a和出口侧喷嘴单元44b。约束辊7设置在入口侧喷嘴单元34a、44a与出口侧喷嘴单元34b、44b之间。由此,约束辊7设置在喷出装置的入口侧端部(入口侧喷嘴单元34a、44a的入口侧
端面)与出口侧端部(出口侧喷嘴单元34b、44b的出口侧端面)之间。
[0052]
入口侧喷嘴单元34a、44a以使一部分浸渍在水中、其余部分从水上露出的方式设置。通板过来的金属板5被装入到露出于水上的入口侧喷嘴单元34a、44a的内侧的间隙,接着浸渍于水中,从喷嘴14和24喷出水。在入口侧喷嘴单元34a、44a设置有两个以上喷嘴14、24。一部分喷嘴(例如图1的设置在入口侧喷嘴单元34a、44a的最上方的喷嘴)形成喷嘴的开口部位于水面的上部、喷嘴的开口部的至少一部分未浸渍在水中的状态。为了抑制高温的金属板5被导入水中时产生的水的喷起,开口部位于水面的上部的喷嘴以能够朝向斜下方喷出水的方式朝向下方倾斜地设置。
[0053]
金属板5在从入口侧喷嘴单元34a、44a通过后利用约束辊7进行约束。为了防止金属板5的骤冷时可能产生的变形,约束辊7在水中将金属板5从两面(表面和背面)夹住。一对约束辊7优选使中心轴在金属板5的搬运方向上错开地配置。通过使中心轴错开地配置,能够增大金属板5的约束力,能够提高形状矫正力。作为一例,优选使各自的中心轴在搬运方向上错开40mm以上且150mm以下地配置约束辊7,更优选错开80mm以上且100mm以下地进行配置。
[0054]
另外,优选以利用约束辊7挤入金属板5而将金属板5卷绕于约束辊7上的方式进行通板。通过挤入金属板5,能够提高矫正力。关于基于1个约束辊7的挤入量,在以如图1和图2那样使金属板5以直线状通板的情况作为基准(0mm)的情况下,优选在水平方向上设定为0mm以上且2.5mm以下。更优选设定为0.5mm以上且1.0mm以下。
[0055]
金属板5从约束辊7通过后,从出口侧喷嘴单元34b、44b的间隙通过。此时,也利用设置在出口侧喷嘴单元34b、44b的喷嘴14、24向金属板5的表面和背面喷出水。
[0056]
图1的例子中,入口侧喷嘴单元34a、44a和出口侧喷嘴单元34b、44b以将约束辊7从上下夹着的方式设置,在与约束辊7重叠的高度上未设置喷嘴单元和喷嘴。这样的例子中,位于入口侧喷嘴单元34a、44a的最靠出口侧的喷嘴14a、24a以及位于出口侧喷嘴单元34b、44b的最靠入口侧的喷嘴14b、24b成为与约束辊7相邻的喷嘴。以下,有时将上述相邻的喷嘴称为“相邻喷嘴”。
[0057]
上述相邻喷嘴不是水平的,而是以喷嘴的开口部从水平面朝向约束辊7一方的方式倾斜地设置。即,上述相邻喷嘴从相对于金属板5垂直的方向朝向约束辊7一方倾斜。更具体而言,图2中的相邻喷嘴14a、24a朝向下方倾斜地安装,相邻喷嘴14b、24b朝向上方倾斜地安装。这样使相邻喷嘴倾斜时,与使相邻喷嘴水平地设置时相比,能够使从相邻喷嘴喷出的水到达至更靠近约束辊7与金属板5的接触点的位置。由此,能够防止由于在约束辊7的附近处从喷嘴喷出的水难以与金属板5的表面和背面接触而引起的、约束辊7附近处的对金属板5的冷却能力的降低。
[0058]
图1和图2的例子中,对于相邻喷嘴以外的其他喷嘴,也全部设置为倾斜成与相邻喷嘴相同的方向,但也可以像以往那样水平地设置相邻喷嘴以外的喷嘴。但是,从使金属板5上的水的接触位置尽可能地均匀的观点考虑,优选使各喷嘴单元中的全部喷嘴向相同方向倾斜相同角度。
[0059]
像图2那样,作为相邻喷嘴的倾斜角度,可以设定相邻喷嘴的轴线方向(液体喷出方向(水的喷出方向))与金属板所形成的角度中形成锐角的角度θ。需要说明的是,水以一定的宽度从喷嘴喷出,但可以采用从喷嘴喷出的水的中心轴线的方向作为上述水的喷出方
向。
[0060]
角度θ可以根据从相邻喷嘴喷出的水的喷出量、相邻喷嘴的开口部与约束辊7的距离、相邻喷嘴的开口部与金属板5的表面和背面的距离等来设定。作为角度θ的优选例,可以列举20
°
以上且60
°
以下。角度θ为20
°
以上且60
°
以下时,从相邻喷嘴喷出的水流到达至更靠近约束辊7与金属板5的接触位置的附近,可以充分地得到抑制约束辊7附近处的对金属板5的冷却速度降低的效果。
[0061]
另外,进一步优选将角度θ设定为30
°
以上且45
°
以下。需要说明的是,使喷嘴倾斜时,以能够从喷嘴倾斜地喷射水的方式至少使喷嘴的前端倾斜即可。
[0062]
另外,本发明的淬火装置可以具备沿着金属板5的搬运方向形成为一体的、非分割型的喷嘴单元。
[0063]
虽然未图示,但喷出装置4中的各喷嘴与在中途设置有泵的配管连接。利用泵将水槽1内的水2汲取到配管内,并压送至喷嘴14、24,由此,从喷嘴14、24的开口部喷出高压水。
[0064]
另外,水槽1内的水2以达到适合于淬火的水温的方式进行维持。水槽1内的水2的一部分被送至外部的冷却塔等冷却设备中冷却,然后,冷却后的水2被返回至水槽1,由此防止水槽1内的水温升高。例如,作为水槽1内的水温,优选超过0℃且50℃以下,特别优选为10℃以上且40℃以下。
[0065]
另外,本发明的一个实施方式的淬火装置中,具备与以往的约束辊不同的约束辊。
[0066]
图5是从侧面观察以往的约束辊7(7x)的图。使用约束辊7x时,约束辊7与金属板5在板宽方向整面进行接触,由此,从约束辊7的相邻喷嘴喷出的水的出路仅是板宽方向,与金属板5的中央部碰撞的水横向流动。因此,金属板5上的冷却速度具有与金属板5的中央部相比边缘部变高的倾向。
[0067]
与此相对,图3是从侧面观察本发明的一个实施方式中的约束辊7(7a)的图,图4是从侧面观察本发明的一个实施方式中的其他约束辊7(7b)的图。
[0068]
图3和图4的例子中,在约束辊7a、7b的辊表面设置有围绕约束辊的轴的轮形的沟槽7a,约束辊7a、7b与金属板5不会在金属板5的板宽方向整面进行接触。因此,从约束辊7a、7b的相邻喷嘴喷出的水的出路不仅是金属板5的板宽方向,还沿着通板方向存在,与金属板5的中央部碰撞的水不仅横向流动,还会纵向流动。即,沟槽7a发挥使从相邻的喷嘴喷出的水沿着金属板5的通板方向(金属板5的长度方向)流出、从而抑制朝向金属板5的边缘部的横向流动的作用。因此,金属板5上的冷却速度在金属板5的中央部与边缘部没有差异,在板宽方向上变得均匀。
[0069]
关于沟槽7a的形状,可以如图3的约束辊7a那样使包含轮形的平面相对于约束辊的轴线方向垂直,也可以如图4的约束辊7b那样使包含轮形的平面相对于约束辊的轴线方向倾斜。在如图4的约束辊7b那样相对于约束辊的轴线方向倾斜的情况下,能够使金属板5的表面性状保持于更良好的状态,因此更优选。
[0070]
轮形的沟槽7a的宽度(沿着约束辊7的轴线方向的一边)优选为10mm以上且50mm以下,更优选为10mm以上且30mm以下,进一步优选为15mm以上且25mm以下。
[0071]
轮形的沟槽7a的深度优选为5mm以上且30mm以下,更优选为5mm以上且15mm以下,进一步优选为8mm以上且12mm以下。沿着约束辊7的轴线方向的沟槽7a彼此的间隔优选为50mm以上且200mm以下,更优选为50mm以上且150mm以下,进一步优选为75mm以上且125mm以
下。在此,沟槽7a彼此的间隔设定为相邻的沟槽的端部之间的距离。
[0072]
需要说明的是,虽然未图示,但沟槽7a的形状可以为以约束辊的轴为中心的螺旋状。在螺旋状的沟槽的情况下,优选宽度为10mm以上且50mm以下、深度为5mm以上且30mm以下、与沿着约束辊7的轴线方向的一周前的沟槽的间隔为50mm以上且200mm以下。
[0073]
在螺旋状的沟槽的情况下,沟槽的形状的更优选的范围、进一步优选的范围也与约束辊7a同样。
[0074]
另外,为了防止金属板与约束辊的滑移,优选将约束辊7设定为驱动辊。此外,为了调整金属板5的矫正力,优选将约束辊7设定为可以根据需要进行开闭(可以控制对于金属板5的挤入量)。
[0075]
约束辊7由热传导率优良、并且具备能够耐受金属板5的夹压时的载荷的强度的材质形成即可。作为约束辊7的材质,可以列举例如sus304、sus310、陶瓷等。
[0076]
如上所述的本发明的实施方式的淬火装置和使用该淬火装置的淬火方法能够应用于钢板的制造,特别优选应用于高强度冷轧钢板(高张力钢板)的制造方法。更具体而言,优选应用于拉伸强度为580mpa以上的钢板的制造方法。拉伸强度的上限没有特别限制,作为一例,可以为1600mpa以下。在高张力钢板的制造时,通过将钢板快速冷却而进行致密的组织控制变得重要。通过应用该实施方式,能够抑制在淬火时产生的形状不良,并且能够在防止约束辊7附近处的冷却速度的降低的同时使板宽方向的冷却速度均匀,能够可靠地制造期望强度的高张力钢板。
[0077]
作为高强度冷轧钢板的组成的具体例,可以列举如下示例:以质量%计,c为0.04%以上且0.25%以下、si为0.01%以上且2.50%以下、mn为0.80%以上且3.70%以下、p为0.001%以上且0.090%以下、s为0.0001%以上且0.0050%以下、sol.al为0.005%以上且0.065%以下,根据需要使cr、mo、nb、v、ni、cu和ti的至少一种以上各自为0.5%以下,进一步根据需要使b、sb各自为0.01%以下,余量由fe和不可避免的杂质构成。
[0078]
需要说明的是,本发明的实施方式不限定于对钢板进行骤冷的例子,能够应用于钢板以外的金属板整体的骤冷,另外,也能够应用于使用水以外的液体的淬火。
[0079]
实施例
[0080]
以下,使用实施例对本发明更具体地进行说明。
[0081]
(本发明例1)
[0082]
在制造板厚为1.0mm、板宽为1000mm且拉伸强度为1470mpa级的高张力冷轧钢板时,使用图1~3所示的淬火装置和约束辊7a,以1.0m/s的通板速度进行淬火。需要说明的是,喷出装置4中,使喷嘴14、24倾斜的角度θ全部设定为30
°
。在此,约束辊7a的中心轴在通板方向上错开80mm地配置,约束辊7a向金属板5的挤入量全部设定为0.5mm。另外,关于沟槽7a,宽度设定为20mm,深度设定为10mm,沟槽7a彼此的间隔设定为100mm。
[0083]
另外,在淬火装置中测定通板中的钢板的温度。具体而言,使用热电偶型的温度计,经时地测定钢板的被测定区域的温度。需要说明的是,钢板的冷却开始温度(即将进入喷出装置4之前的温度)为740℃,冷却结束温度(刚从水槽1出来之后的温度)为30℃。根据冷却开始后的经过时间与钢板的温度的关系,计算出钢板与约束辊7a接触的瞬间的、钢板的板宽方向的冷却速度分布。将结果示于图6中。
[0084]
另外,在通板后测定钢板的翘曲量。具体而言,使用从搬运方向正对地观察钢板的
图12来进行说明。在钢板发生翘曲时,在钢板的宽度方向上形成高度较高的部分和高度较低的部分。在通板后的钢板中,测定高度最高的部分与高度最低的部分的高度之差作为翘曲量。
[0085]
(本发明例2)
[0086]
将约束辊7a的沟槽7a设定为宽度10mm、深度5mm,将沟槽7a彼此的间隔设为200mm,除此以外,与本发明例1同样地进行实验。将结果示于图7中。
[0087]
(比较例1)
[0088]
使用专利文献4记载的淬火装置和图5所示的约束辊7x,除此以外,与本发明例1同样地进行实验。将结果示于图8中。
[0089]
(比较例2)
[0090]
使用专利文献3记载的淬火装置和图5所示的约束辊7x,除此以外,与本发明例1同样地进行实验。需要说明的是,相邻喷嘴的倾斜角度为90
°
。将结果示于图9中。
[0091]
(比较例3)
[0092]
将约束辊7a的沟槽7a设定为宽度5mm、深度2mm,将沟槽7a彼此的间隔设定为300mm,除此以外,与本发明例1同样地进行实验。将结果示于图10中。
[0093]
<冷却速度的评价>
[0094]
图6、7(本发明例1、2)中,钢板的板宽方向的冷却速度分布不依赖于板宽位置地大致恒定,大致均匀地被冷却。冷却速度为1500℃/s。
[0095]
另一方面,图8(比较例1)中,边缘部与中央部相比冷却速度变高,被不均匀地冷却。冷却速度在中央部为1500℃/s、在边缘为2000℃/s。
[0096]
同样地,图9(比较例2)中,边缘部与中央部相比冷却速度变高,被不均匀地冷却。冷却速度在中央部为900℃/s、在边缘为1200℃/s,与图6在中央部进行比较时,冷却速度降低了约40%(从1500℃/s至900℃/s)。
[0097]
图10(比较例3)中,边缘部与中央部相比冷却速度变高,被不均匀地冷却。冷却速度在中央部为1500℃/s、在边缘为1700℃/s。
[0098]
在钢板的板宽中央部与边缘部的冷却速度存在100℃以上的差别的情况下,产生了不均匀性。
[0099]
由此表明,通过应用本发明,能够抑制约束辊附近处的金属板的冷却速度的降低、并且防止板宽方向的冷却速度的不均匀性。
[0100]
<拉伸强度的评价>
[0101]
通过本发明例1、2制造的钢板的拉伸强度在整个板宽方向上为约1470mpa。
[0102]
与此相对,通过比较例1制造的钢板的拉伸强度在板宽中央部为约1470mpa、但在边缘部为约1550mpa,观察到拉伸强度的不均匀性。
[0103]
另外,通过比较例2制造的钢板的拉伸强度在板宽中央部为约1350mpa、在边缘部为约1400mpa,观察到拉伸强度的降低和不均匀性。
[0104]
另外,通过比较例3制造的钢板的拉伸强度在板宽中央部为约1470mpa、但在边缘部为约1520mpa,观察到拉伸强度的不均匀性。
[0105]
在钢板的板宽中央部和边缘部的拉伸强度存在30mpa以上的差别的情况下,判断为存在拉伸强度的不均匀性。
[0106]
由此表明,通过应用本发明,能够防止伴随约束辊附近处的冷却速度的降低、不均匀性而产生的钢板的特性降低、不均匀性。
[0107]
<翘曲量的评价>
[0108]
将本发明例1、2和比较例1、2、3中测定的钢板的翘曲量的结果示于图11中。
[0109]
本发明例1、2和比较例1、2、3中,钢板的翘曲量均为同等程度,确认了:即使像本发明这样使约束辊具备沟槽,也能够防止淬火时的钢板的变形。
[0110]
产业上的可利用性
[0111]
根据本发明,可以提供能够抑制在淬火时金属板所产生的形状不良、并且能够在抑制金属板的冷却速度的降低的同时使金属板的板宽方向的冷却速度均匀的、淬火装置、淬火方法和使用上述淬火方法的钢板的制造方法。
[0112]
符号说明
[0113]
1 水槽
[0114]
2 水
[0115]
3 密封辊
[0116]
4 喷出装置
[0117]
5 金属板
[0118]
6 沉没辊
[0119]
7 约束辊
[0120]
7a 约束辊
[0121]
7b 约束辊
[0122]
7x 约束辊
[0123]
7a 沟槽
[0124]
14、24 喷嘴
[0125]
14a、24a 相邻喷嘴
[0126]
14b、24b 相邻喷嘴
[0127]
34、44 喷嘴单元
[0128]
34a、44a 入口侧喷嘴单元
[0129]
34b、44b 出口侧喷嘴单元