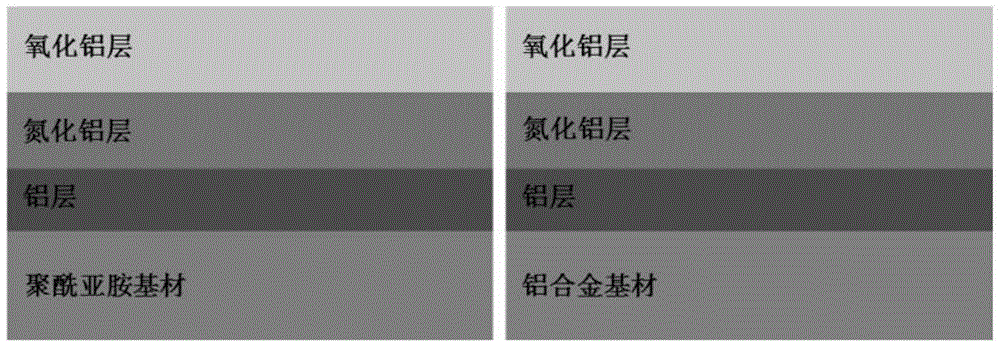
本发明涉及表面工程
技术领域:
,具体涉及一种太阳吸收率可设计的热控涂层及制备方法。
背景技术:
:热控涂层是一类用于调节固体表面光学、热学性能从而达到热控制目的的功能涂层,是航天器热控系统所采用的一种非常重要的材料。热控涂层通过调整物体表面的热辐射性质,维持外表面能量吸收和辐射的平衡,从而达到控制物体温度的目的。其最重要的两个参数是太阳吸收率和太阳吸收率。随着未来航天器向着微小化、高度集成化、功能多样化需求的发展,对航天器及其相关设备表面热控涂层的热控性能指标提出了更高要求。热控涂层必须实现精确控温、长效寿命及高性能等要求。同时针对不同的空间环境和航天器指标要求,热控涂层也需要灵活地改变其热控性能。目前,国内航天器所使用的热控涂层主要包括:有机白漆、黑漆、osr、化学氧化膜、铝合金阳极氧化层等,但是只能满足较低的太阳吸收率和较高的太阳吸收率,无法实现热控涂层太阳吸收率在一定范围内可设计。鉴于上述缺陷,本发明创作者经过长时间的研究和实践终于获得了本发明。技术实现要素:为解决上述技术缺陷,本发明采用的技术方案在于,提供一种太阳吸收率可设计的热控涂层,在基材表面由内向外依次设置第一层镀层、第二层镀层和第三层镀层,所述第一层镀层为纯铝层,所述第二层镀层为氮化铝层,所述第三层镀层为氧化铝层。较佳的,所述基材为铝合金基,所述第一层镀层厚度为0nm~300nm;所述第一层镀层厚度为0nm~250nm;所述第三层镀层厚度为0nm~20nm,所述热控涂层的太阳吸收率为0.10到0.92。较佳的,所述基材为聚酰亚胺,所述第一层镀层厚度为0nm~300nm;所述第一层镀层厚度为0nm~250nm;所述第三层镀层厚度为0nm~20nm,所述热控涂层的太阳吸收率为0.10到0.90。较佳的,所述第一层镀层厚度为不能低于100nm。较佳的,一种所述太阳吸收率可设计的热控涂层的制备方法,所述第一层镀层、所述第二层镀层和所述第三层镀层采用真空镀膜的方式制备。较佳的,所述第一层镀层镀制的工艺参数:真空度为6×10-1pa~8×10-1pa;氩气进气量为120sccm,电压为550v;电流为3a;溅射时间为500s。较佳的,所述第二层镀层镀制工艺参数:真空度为6×10-1pa~8×10-1pa;氩气进气量为120sccm;氮气进气量为45sccm;电压为550v;电流为3a;溅射时间为250s。较佳的,所述第三层镀层镀制工艺参数:真空度为6×10-1pa~8×10-1pa;氩气进气量为120sccm;功率为1200w,溅射时间为400s。与现有技术比较本发明的有益效果在于:1,通过本发明的制备方法在铝合金基材表面制备得到的热控涂层,通过对镀制膜层的厚度设计,热控涂层的太阳吸收率可实现0.10到0.92范围内的调节;2,通过本发明的制备方法在聚酰亚胺基材表面制备得到的热控涂层,通过对镀制膜层的厚度设计,热控涂层的太阳吸收率可实现0.10到0.90范围内的调节;3,通过该制备方法制备得到的复合型热控涂层具有良好的耐空间原子氧、质子、电子、紫外辐照的性能。经过空间原子氧、质子、电子、紫外辐照试验后,热控涂层的太阳吸收率指标变化不超过0.02;4,该方法的基材材料可推广至金属、塑料、陶瓷或复合材料。附图说明图1为所述太阳吸收率可设计的热控涂层的立体示意图;图2为不同基材表面太阳吸收率与氮化铝层厚度关系图;图3为实施例一、实施例二、实施例三的样品实物图;图4为实施例一、实施例二、实施例三的样品表面形态扫描电镜图。具体实施方式以下结合附图,对本发明上述的和另外的技术特征和优点作更详细的说明。如图1所示,图1为所述太阳吸收率可设计的热控涂层的立体示意图;本发明所述太阳吸收率可设计的热控涂层制备方法,复合型膜系结构设计,基材表面第一层镀层为纯铝层,作为低吸收率金属层;第二层镀层为氮化铝层,作为高吸收率陶瓷层;第三层为氧化铝层,作为保护层和减反射层。所述的一种太阳吸收率可设计的热控涂层制备方法,其特征在于:采用的真空镀膜设备为可以将靶材离化为等离子体的真空设备,优选设备为真空磁控溅射设备或离子束反应溅射设备。所述太阳吸收率可设计的热控涂层制备方法,对于铝合金基材,第一层纯铝层镀制厚度0nm~300nm;第二层氮化铝层镀制厚度0nm~250nm;第三层氧化铝层镀制厚度为0nm~20nm;通过镀制厚度调节在铝合金材料表面制备得到热控涂层太阳吸收率可从0.10到0.92进行设计。所述太阳吸收率可设计的热控涂层制备方法,对于聚酰亚胺基材,第一层纯铝层镀制厚度0nm~300nm;第二层氮化铝层镀制厚度0nm~250nm;第三层氧化铝层镀制厚度为0nm~20nm;通过镀制厚度调节在聚酰亚胺材料表面制备得到热控涂层太阳吸收率可从0.10到0.90进行设计。通过所述太阳吸收率可设计的热控涂层制备方法制备得到的复合型热控涂层能耐空间原子氧、质子、电子、紫外辐照环境。经过空间原子氧、质子、电子、紫外辐照试验后,热控涂层的太阳吸收率指标变化不超过0.02。本发明的金属陶瓷复合型涂层为铝层-氮化铝层-氧化铝层。随着材料中金属微粒体积分数增加,薄膜性质由绝缘性向金属性转变,其折射率和消光系数也呈梯度变化。因此,复合型涂层可以通过选择合适膜层厚度、颗粒浓度、颗粒形状及大小来优化涂层的选择性。金属陶瓷复合型吸收涂层主要由最表层的减反层(氧化铝对太阳光起增透的作用)、最底层的金属红外反射层(铝层对长波长的红外光起高反射的作用)以及中间的吸收层(氮化铝)。金属陶瓷复合型吸收涂层借鉴了多层渐变型和光干涉相消原理,随着中间吸收层厚度的增加可以得到更高的太阳吸收率。以下实施例所用设备及材料:磁控溅射沉积设备一台;金属铝靶材(99%);氮气(纯度:99.999%);氧气(纯度:99.999%);氩气(纯度:99.999%)。聚酰亚胺和铝合金基材表面第一层镀制的纯铝层厚度不能低于100nm,否则无法实现低太阳吸收率(小于0.14)的调节。如图2所示,图2为不同基材表面太阳吸收率与氮化铝层厚度关系图。本发明通过大量实验数据建立了不同基材表面太阳吸收率与氮化铝层厚度之间关联关系。当第一层纯铝层厚度为100nm,第三层氧化铝层为10nm时,aln膜层厚度与样件太阳吸收率管辖如下表所示。aln厚度(nm)聚酰亚胺样件太阳吸收率铝合金样件太阳吸收率00.110.1100.230.31200.430.51400.590.62600.690.72800.750.81000.810.851200.850.891400.870.91600.890.911800.90.922000.90.92实施例一将铝合金试验件(5片),聚酰亚胺试验件(5片)放入磁控溅射沉积设备中进行膜层镀制。其中,第一层纯铝层厚度为100nm,第二层氮化铝层为0nm,第三层氧化铝层为10nm。铝层镀制工艺参数:真空度6×10-1pa~8×10-1pa;氩气进气量120sccm,电压550v;电流3a;溅射时间500s。该实例中不镀制氮化铝层。氧化铝镀制工艺参数:真空度6×10-1pa~8×10-1pa;氩气进气量120sccm;功率1200w,溅射时间10s。热辐射性能指标测试实施例一试验件太阳吸收率测试结果如下表:编号聚酰亚胺样件太阳吸收率铝合金样件太阳吸收率10.110.1020.110.1030.100.1140.100.1050.100.11铝合金试验件(5片),聚酰亚胺试验件(5片)经过空间原子氧、质子、电子、紫外辐照试验后,热控涂层的太阳吸收率指标变化未超过0.02。实施例二将铝合金试验件(5片),聚酰亚胺试验件(5片)放入磁控溅射沉积设备中进行膜层镀制。其中,第一层纯铝层厚度为100nm,第二层氮化铝层为10nm,第三层氧化铝层为10nm。铝层镀制工艺参数:真空度6×10-1pa~8×10-1pa;氩气进气量120sccm,电压550v;电流3a;溅射时间500s。氮化铝层镀制工艺参数:真空度6×10-1pa~8×10-1pa;氩气进气量120sccm;氮气进气量45sccm;电压550v;电流3a;溅射时间250s。氧化铝镀制工艺参数:真空度6×10-1pa~8×10-1pa;氩气进气量120sccm;功率1200w,溅射时间400s。热辐射性能指标测试实施例二试验件太阳吸收率测试结果如下表:编号聚酰亚胺样件太阳吸收率铝合金样件太阳吸收率10.250.3420.260.3330.240.3240.250.3350.270.34铝合金试验件(5片),聚酰亚胺试验件(5片)经过空间原子氧、质子、电子、紫外辐照试验后,热控涂层的太阳吸收率指标变化未超过0.02。实施例三将铝合金试验件(5片),聚酰亚胺试验件(5片)放入磁控溅射沉积设备中进行膜层镀制。其中,第一层纯铝层厚度为100nm,第二层氮化铝层为80nm,第三层氧化铝层为10nm。铝层镀制工艺参数:真空度6×10-1pa~8×10-1pa;氩气进气量120sccm,电压550v;电流3a;溅射时间500s。氮化铝层镀制工艺参数:真空度6×10-1pa~8×10-1pa;氩气进气量120sccm;氮气进气量45sccm;电压550v;电流3a;溅射时间500s。氧化铝镀制工艺参数:真空度6×10-1pa~8×10-1pa;氩气进气量120sccm;功率1200w,溅射时间400s。热辐射性能指标测试实施例三试验件太阳吸收率测试结果如下表:编号聚酰亚胺样件太阳吸收率铝合金样件太阳吸收率10.750.8020.740.8030.760.8240.750.8150.740.79铝合金试验件(5片),聚酰亚胺试验件(5片)经过空间原子氧、质子、电子、紫外辐照试验后,热控涂层的太阳吸收率指标变化未超过0.02。如图3、图4所示,图3中(a)为实施例一的样品实物图,(b)为实施例二的样品实物图,(c)为实施例三的样品实物图;图4为中(a)为实施例一的样品表面形态扫描电镜图,(b)为实施例二的样品表面形态扫描电镜图,(c)为实施例三的样品表面形态扫描电镜图。实施例四将铝合金试验件(5片),聚酰亚胺试验件(5片)放入磁控溅射沉积设备中进行膜层镀制。其中,第一层纯铝层厚度为100nm,第二层氮化铝层为160nm,第三层氧化铝层为10nm。铝层镀制工艺参数:真空度6×10-1pa~8×10-1pa;氩气进气量120sccm,电压550v;电流3a;溅射时间500s。氮化铝层镀制工艺参数:真空度6×10-1pa~8×10-1pa;氩气进气量120sccm;氮气进气量45sccm;电压550v;电流3a;溅射时间1250s。氧化铝镀制工艺参数:真空度6×10-1pa~8×10-1pa;氩气进气量120sccm;功率1200w,溅射时间400s。热辐射性能指标测试实施例四试验件太阳吸收率测试结果如下表:编号聚酰亚胺样件太阳吸收率铝合金样件太阳吸收率10.900.9220.880.9130.910.9340.890.9050.890.92铝合金试验件(5片),聚酰亚胺试验件(5片)经过空间原子氧、质子、电子、紫外辐照试验后,热控涂层的太阳吸收率指标变化未超过0.02。以上所述仅为本发明的较佳实施例,对本发明而言仅仅是说明性的,而非限制性的。本专业技术人员理解,在本发明权利要求所限定的精神和范围内可对其进行许多改变,修改,甚至等效,但都将落入本发明的保护范围内。当前第1页12