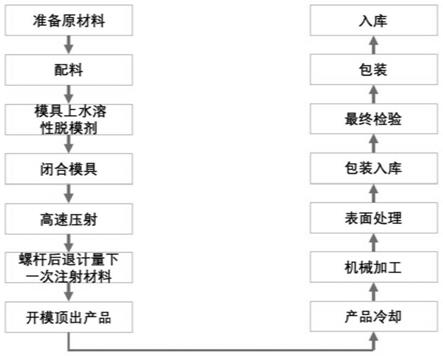
[0001]
本发明属于混凝土工程施工模板制备领域,特别涉及一种镁合金建筑模板半固态压铸及双氟化联合制造方法。
背景技术:[0002]
混凝土模板工程是建筑施工中的主导工种工程之一。模板是混凝土结构工程施工中重要周转材料,是决定混凝土成型质量、支模工作强度、施工效率和成本重要因素。近年来,为了更好地促进我国混凝土施工行业的高效发展,我国把开发新型模板应用技术确立为“建筑业10项新技术”之一,足以显示国家对于模板行业创新发展的高度重视,同时各个地方也出台相关文件提倡研发新型环保模板,如重庆市在2019年11月6日和11月15日分别发布的《重庆市建设领域禁止、限制使用落后技术通告(2019年版)》及《建筑工程清水混凝土施工技术标准(征求意见稿)》。模板材料作为混凝土施工技术最重要的研究内容,也是实现模板体系改革的关键因素。所以急需加大研究力度,开发出更多的新型模板材料,不但要保证模板工程施工的质量、进度和成本,更要满足绿色、环保以及经济可持续发展等新的要求。
[0003]
镁合金的密度仅为铝合金的2/3,钢铁的1/4,比强度和比刚度均优于钢和铝合金,远高于工程塑料;镁合金吸震性能强,减少混凝土浇筑的冲击,降低施工噪音;铸造性能好、自动化生产能力和模具寿命高,可利于采用压铸工艺进行自动化生产;镁合金尺寸稳定,不会因环境温度和时间的变化而造成较大的变化,可防止因变形引起的模板拼接难题。因此,在混凝土施工模板工程领域内,镁合金是一种上述材料无法比拟的、优质的轻质结构材料。
[0004]
针对镁合金建筑模板,目前只有中国专利申请第201510869825.1号和中国专利申请第201910780290.9号对其有报道。专利申请中对镁合金模板均采用传统挤压工艺和传统压铸工艺制造。挤压工艺难以实现镁合金模板的整体制造,必须借助焊接工艺才能制造出现场可用模板,但是由于镁合金材料本身的特性导致现有的焊接工艺难以实现可靠的模板制造。利用传统的压铸技术压铸镁合金模板,容易造成模板内存在型腔内气体以及压铸涂料产生的气体无法顺利排出的问题,这些气体在高压下或者溶解在镁合金内,或者形成许多高压微气孔弥散分布在压铸模板内。
[0005]
此外,镁合金压铸模板在存储和使用过程中容易遭受大气和水环境腐蚀,施工过程中容易被混凝土划伤破坏模板表面,这两种情况都会造成模板粘附混凝土而难以脱落的问题,进而影响混凝土成型表面质量;而现有的表面处理方法也难以有效解决镁合金建筑模板表面存在的问题。
技术实现要素:[0006]
本发明的目的在于提供一种镁合金建筑模板半固态压铸及双氟化联合制造方法,以满足清水混凝土和饰面清水混凝土的对模板的技术要求。
[0007]
为了实现上述目的,本发明采用如下技术方案:
[0008]
一种镁合金建筑模板半固态压铸及双氟化联合制造方法,包括以下步骤:
[0009]
步骤一、采用半固态压铸法制备镁合金建筑模板;
[0010]
步骤二、将步骤一制备的镁合金建筑模板浸入双氟处理液进行双氟化联合处理,获得双氟化联合处理的镁合金建筑模板。
[0011]
本发明进一步的改进在于:双氟处理液按照重量百分比,包括以下组分:无机氟化物20%-30%、有机含氟乳液20%-40%、纳米硅溶胶15%-20%、缓蚀剂组分0.3%-0.5%,硅烷偶联剂0.8%-2%,去离子水20%-43.9%。
[0012]
本发明进一步的改进在于:所述无机氟化物为氢氟酸、氟硅酸、氟钛酸、次氟酸、氢氟酸盐、氟硅酸盐、氟钛酸盐、次氟酸盐中一种或几种。
[0013]
本发明进一步的改进在于:所述有机含氟乳液为含氟水性树脂与水性环氧树脂共混而成的乳液,两者的重量比为8:1-5:1;所述有机含氟乳液具有自交联特征,同时具有自分层特征;所述含氟水性树脂为聚四氟乙烯、聚偏氟乙烯、聚氟乙烯、聚三氟氯乙烯、乙烯-四氟乙烯共聚物、乙烯-三氟氯乙烯共聚物、聚四氟乙烯改性聚合物、聚偏氟乙烯改性聚合物、聚氟乙烯改性聚合物、聚三氟氯乙烯改性聚合物、乙烯-四氟乙烯共聚物的改性聚合物、乙烯-三氟氯乙烯共聚物的改性聚合物中的一种或几种。
[0014]
本发明进一步的改进在于:纳米硅溶胶的粒径控制在50nm-800nm,其中,按照质量百分比,硅溶胶中二氧化硅含量控制在30%-50%,氧化钠杂质含量小于0.2%,其余为水。
[0015]
本发明进一步的改进在于:所述缓蚀剂组分为偏钒酸或偏钒酸盐中的一种或几种。
[0016]
本发明进一步的改进在于:硅烷偶联剂为γ-(2,3-环氧丙氧)丙基三甲氧基硅烷、γ-氨丙基三乙氧基硅烷、γ-甲基丙烯酰氧基丙基和γ-巯丙基三甲氧基硅烷中的一种或多种。
[0017]
本发明进一步的改进在于:步骤二具体包括:
[0018]
将表面清洁干净的镁合金建筑模板浸入所述双氟处理液,处理液工作温度控制在25℃~60℃,处理时间10min~60min,在镁合金建筑模板表面上制备出初始膜层;然后清洗干净,并晾干后于60℃-80℃烘干,在镁合金建筑模板表面形成了一层由无机氟化层、过渡层和有机氟化层三层构成的具有自修复作用的双氟复合膜层体系,获得双氟化联合处理的镁合金建筑模板。
[0019]
本发明进一步的改进在于:步骤一具体包括:
[0020]
s1:模具预热;
[0021]
s2:备料加热:将镁合金颗粒加热熔融为合金半固态浆料;
[0022]
s3:高速压射:闭合模具,抽成真空,将合金半固态浆料高速压射进预热模具型腔中成型;
[0023]
s4:开模冷却:打开模具顶出镁合金建筑模板。
[0024]
本发明进一步的改进在于:步骤一具体包括:
[0025]
s1:模具预热;
[0026]
s2:备料加热:将镁合金颗粒通过自动投料系统投入料斗中,强制输送到粒筒中,粒筒中旋转的螺杆驱使镁合金颗粒向模具方向运动,通入氩气进行保护,加热使粒筒中的合金原料转变为部分熔融状态,在螺旋体的剪切作用下,具有枝晶组织的合金料形成具有
触变结构的温度为570~590℃的合金半固态浆料,固相体积分数为50%~60%;
[0027]
s3:高速压射:闭合模具,抽成真空,通过联合控制速度和压力将合金半固态浆料高速压射进预热模具型腔中成型,压力控制在70~90mpa压射力,速度控制在2~6m/s;
[0028]
s4:开模冷却:螺杆后退计量下一次注射材料,打开模具顶出镁合金建筑模板,对模板进行风冷或水冷、自然降温。
[0029]
相对于现有技术,本发明具有以下有益效果:
[0030]
本发明制造的镁合金模板表面光滑平整,抗拉强度高、伸长率大、硬度高、摩擦系数小,具有优秀的抗划伤能力以及憎水性,可有效降低混凝土骨料造成的摩擦损伤以及来自外界侵蚀介质的腐蚀破坏,阻止水泥引起的化学反应及物理吸附,保证建筑墙面施工质量及脱模效果。
[0031]
与现有的技术相比,采用半固态压铸及双氟化联合制造方法制造的镁合金建筑模板其表面拥有一层稳定的双氟三层复合保护膜层体系,且模板表面光滑平整,抗拉强度高(可达256mpa)、伸长率大(可达11%以上)、硬度高(大于4h)、摩擦系数小(干摩擦系数可低至0.04),憎水性极大改善(接触角可达114
°
以上),同时耐中性盐雾实验可达840小时以上,可实现有效降低混凝土骨料对模板造成的摩擦损伤以及来自外界侵蚀介质的腐蚀破坏,阻止水泥与模板的化学反应及物理吸附,保证建筑墙面施工质量及脱模效果,可有效满足清水混凝土和饰面清水混凝土的对模板的技术要求。
附图说明
[0032]
构成本申请的一部分的说明书附图用来提供对本发明的进一步理解,本发明的示意性实施例及其说明用于解释本发明,并不构成对本发明的不当限定。在附图中:
[0033]
图1是本发明半固态压铸及双氟化联合制造方法制造的镁合金模板示意图。
[0034]
图2是本发明镁合金模板半固态压铸及双氟化联合制造方法工艺流程图。
[0035]
图3是本发明镁合金模板表面双氟三层复合保护膜层体系的示意图。
[0036]
图4是本发明实施例1中镁合金模板表面微观形貌图;
[0037]
图5为本发明实施例1中镁合金模板表面双氟三层复合保护膜层的接触角图。
具体实施方式
[0038]
下面将参考附图并结合实施例来详细说明本发明。需要说明的是,在不冲突的情况下,本申请中的实施例及实施例中的特征可以相互组合。
[0039]
以下详细说明均是示例性的说明,旨在对本发明提供进一步的详细说明。除非另有指明,本发明所采用的所有技术术语与本申请所属领域的一般技术人员的通常理解的含义相同。本发明所使用的术语仅是为了描述具体实施方式,而并非意图限制根据本发明的示例性实施方式。
[0040]
下面将结合本发明实施例,对本发明实施例中的技术方案进行清楚、完整地描述,显然,所描述的实施例仅仅是本发明一部分实施例,而不是全部的实施例。基于本发明中的实施例,本领域普通技术人员在没有做出创造性劳动前提下所获得的所有其他实施例,都属于本发明保护的范围。
[0041]
本发明一种镁合金建筑模板半固态压铸及双氟化联合制造方法,包括以下步骤:
[0042]
步骤一、采用半固态压铸法制备镁合金建筑模板;
[0043]
步骤二、将步骤一制备的镁合金建筑模板浸入双氟处理液进行双氟化联合处理,获得双氟化联合处理的镁合金建筑模板。
[0044]
本发明中,双氟处理液按照重量百分比,包括以下组分:无机氟化物20%-30%、有机含氟乳液20%-40%、纳米硅溶胶15%-20%、缓蚀剂组分0.3%-0.5%,硅烷偶联剂0.8%-2%,去离子水20%-43.9%。
[0045]
实施例1:
[0046]
一种镁合金建筑模板的半固态压铸及双氟化联合制造方法,包括以下操作步骤:
[0047]
s1:上模预热,针对模板进行模具设计,按照模具加工工艺流程(样件-制件数模-编制冲压工艺—模具结构设计-制作模型-机加工-研磨装配-试模-最终检查)完成开模和试模。将模板模具安装至压铸机上,同时将模板模具与相应的所需的周边设备进行连接,在模具上喷涂水溶性脱模剂,有模温要求的,通过模温机对模板模具进行预热。
[0048]
s2:备料加热,准备直径为3~5mm、长度约为10mm的镁合金颗粒,通过自动投料系统投入料斗中,强制输送到粒筒中,粒筒中旋转的螺杆驱使镁合金颗粒向模具方向运动,通入氩气进行保护,通过电阻和感应加热,控制温度为580℃,使粒筒中的合金原料转变为部分熔融状态,并在螺旋体的剪切作用下,形成具有触变结构的合金半固态浆料,固相体积分数为50%。
[0049]
s3:高速压射,闭合模板模具,抽成真空,通过联合控制速度和压力将合金半固态浆料高速压射进预热模具型腔中成型,压力控制在90mpa压射力,速度控制在6m/s。
[0050]
s4:开模冷却,螺杆后退计量下一次注射材料,打开模具顶出模板产品,对模板进行风冷降温。
[0051]
s5:模板表面双氟化学处理:待模板冷却后,进行机加工,随后进行特定双氟化学表面处理。该技术在镁合金模板表面形成的双氟三层复合保护膜层体系示意图如图3所示。双氟化学表面处理技术所用双氟处理液的组成(重量百分比)为:氢氟酸25%、有机含氟乳液20%、100-200nm粒径纳米硅溶胶20%、偏钒酸钾缓蚀剂组分0.5%,γ-(2,3-环氧丙氧)丙基三甲氧基硅烷偶联剂2%,去离子水32.5%。
[0052]
按上述组成比例配制双氟处理液,先向容器中添加20%的去离子水,然后添加25%氢氟酸,搅拌均匀后,再添加偏钒酸钾缓蚀剂组分0.5%,搅拌均匀后再添加-(2,3-环氧丙氧)丙基三甲氧基硅烷偶联剂2%,同步加入100-200nm粒径纳米硅溶胶20%,常温下边搅拌边添加有机含氟乳液20%,补充余下的12.5%去离子水,并搅拌5h,即得双氟处理液。镁合金模板为am50系列,采用本领域技术人员所公知的镁合金表面碱性除油脱脂溶液对模板进行脱脂,脱脂温度为60℃,时间为5分钟;进行两道一次去离子水水洗;将模板缓慢浸入双氟处理液进行双氟化学处理,处理液温度40℃,处理时间40min;进行二次去离子水水洗2次;自然晾干20分钟,然后在80℃烘箱中进行连续烘干40分钟,在镁合金建筑模板1上形成一层由无机氟化层2、过渡层3和有机氟化层4三层构成的具有自修复作用的双氟复合膜层体系(如图3所示)。双氟复合膜层体系中分布纳米溶胶粒子5和缓释分子6。获得双氟复合膜层,其微观形貌如图4所示。
[0053]
经3.5%nacl溶液中的电化学tafel曲线测试,发现经过该膜层处理的am50镁合金模板的自腐蚀电流密度相对于空白镁合金模板提高大于3个数量级,非划格中性盐雾实验
时间可达840小时不破坏,接触角为114
°
(如图5所示),硬度大于4h,干摩擦系数0.04,抗冲击力大于50kg.cm,模板抗拉强度为256mpa以上,伸长率为11.2%。
[0054]
实施例2:
[0055]
一种镁合金建筑模板的半固态压铸及双氟化联合制造方法,包括以下操作步骤:
[0056]
s1:上模预热,针对模板进行模具设计,按照模具加工工艺流程(样件-制件数模-编制冲压工艺—模具结构设计-制作模型-机加工-研磨装配-试模-最终检查)完成开模和试模。将模板模具安装至压铸机上,同时将模板模具与相应的所需的周边设备进行连接,在模具上喷涂水溶性脱模剂,有模温要求的,通过模温机对模板模具进行预热。
[0057]
s2:备料加热,准备直径为3~5mm、长度约为10mm的镁合金颗粒,通过自动投料系统投入料斗中,强制输送到粒筒中,粒筒中旋转的螺杆驱使镁合金颗粒向模具方向运动,通入氩气进行保护,通过电阻和感应加热,控制温度为570℃,使粒筒中的合金原料转变为部分熔融状态,并在螺旋体的剪切作用下,形成具有触变结构的合金半固态浆料,固相体积分数为55%。
[0058]
s3:高速压射,闭合模板模具,抽成真空,通过联合控制速度和压力将合金半固态浆料高速压射进预热模具型腔中成型,压力控制在70mpa压射力,速度控制在5m/s。
[0059]
s4:开模冷却,螺杆后退计量下一次注射材料,打开模具顶出模板产品,对模板进行风冷、自然降温。
[0060]
s5:模板表面双氟化学处理:待模板冷却后,进行机加工,随后进行特定双氟化学表面处理。双氟化学表面处理技术所用双氟处理液的组成(重量百分比)为:氢氟酸22%、有机含氟乳液30%、100-200nm粒径纳米硅溶胶16%、偏钒酸钠缓蚀剂组分0.3%,γ-(2,3-环氧丙氧)丙基三甲氧基硅烷偶联剂1%,去离子水30.7%。按上述组成比例配制双氟处理液,先向容器中添加24%的去离子水,然后添加22%氢氟酸,搅拌均匀后,再添加偏钒酸钠缓蚀剂组分0.3%,搅拌均匀后再添加-(2,3-环氧丙氧)丙基三甲氧基硅烷偶联剂1%,同步加入100-200nm粒径纳米硅溶胶16%,常温下边搅拌边添加有机含氟乳液30%,补充余下的6.7%去离子水,并搅拌4h,即得双氟处理液。镁合金模板为am50系列,采用本领域技术人员所公知的镁合金表面碱性除油脱脂溶液对模板进行脱脂,脱脂温度为60℃,时间为5分钟;进行两道一次去离子水水洗;将模板缓慢浸入双氟处理液进行双氟化学处理,处理液温度45℃,处理时间40min;进行二次去离子水水洗2次;自然晾干30分钟,然后在80℃烘箱中进行连续烘干40分钟,获得双氟复合膜层。
[0061]
经3.5%nacl溶液中的电化学tafel曲线测试,发现经过该膜层处理的am50镁合金模板的自腐蚀电流密度相对于空白镁合金模板提高接近3个数量级,非划格中性盐雾实验时间可达720小时不破坏,接触角为95
°
,硬度4h,干摩擦系数0.05,抗冲击力大于50kg.cm,模板抗拉强度为235mpa,伸长率为9.8%。
[0062]
实施例3:
[0063]
一种镁合金建筑模板的半固态压铸及双氟化联合制造方法,包括以下操作步骤:
[0064]
s1:上模预热,针对模板进行模具设计,按照模具加工工艺流程(样件-制件数模-编制冲压工艺—模具结构设计-制作模型-机加工-研磨装配-试模-最终检查)完成开模和试模。将模板模具安装至压铸机上,同时将模板模具与相应的所需的周边设备进行连接,在模具上喷涂水溶性脱模剂,有模温要求的,通过模温机对模板模具进行预热。
[0065]
s2:备料加热,准备直径为3~5mm、长度约为10mm的镁合金颗粒,通过自动投料系统投入料斗中,强制输送到粒筒中,粒筒中旋转的螺杆驱使镁合金颗粒向模具方向运动,通入氩气进行保护,通过电阻和感应加热,控制温度为590℃,使粒筒中的合金原料转变为部分熔融状态,并在螺旋体的剪切作用下,形成具有触变结构的合金半固态浆料,固相体积分数为60%。
[0066]
s3:高速压射,闭合模板模具,抽成真空,通过联合控制速度和压力将合金半固态浆料高速压射进预热模具型腔中成型,压力控制在80mpa压射力,速度控制在2m/s。
[0067]
s4:开模冷却,螺杆后退计量下一次注射材料,打开模具顶出模板产品,对模板进行风冷、自然降温。
[0068]
s5:模板表面双氟化学处理:待模板冷却后,进行机加工,随后进行特定双氟化学表面处理。双氟化学表面处理技术所用双氟处理液的组成(重量百分比)为:氢氟酸20%、有机含氟乳液35%、100-200nm粒径纳米硅溶胶15%、偏钒酸钾缓蚀剂组分0.4%,γ-巯丙基三甲氧基硅烷偶联剂1.5%,去离子水28.1%。按上述组成比例配制双氟处理液,先向容器中添加20%的去离子水,然后添加20%氢氟酸,搅拌均匀后,再添加偏钒酸钾缓蚀剂组分0.4%,搅拌均匀后再添加γ-巯丙基三甲氧基硅烷偶联剂1.5%,同步加入100-200nm粒径纳米硅溶胶15%,常温下边搅拌边添加有机含氟乳液35%,补充余下的8.1%去离子水,并搅拌4h,即得所需双氟处理液。镁合金模板为am50系列,采用本领域技术人员所公知的镁合金表面碱性除油脱脂溶液对模板进行脱脂,脱脂温度为70℃,时间为3分钟;进行两道一次去离子水水洗;将模板缓慢浸入双氟处理液进行双氟化学处理,处理液温度50℃,处理时间30min;进行二次去离子水水洗2次;自然晾干10分钟,然后在80℃烘箱中进行连续烘干40分钟,获得双氟合膜层。经3.5%nacl溶液中的电化学tafel曲线测试,发现经过该膜层处理的am50镁合金模板的自腐蚀电流密度相对于空白镁合金模板提高大于2个数量级,非划格中性盐雾实验时间可达648小时不破坏,接触角为90
°
,硬度大于4h,干摩擦系数0.05,抗冲击力大于50kg.cm,模板抗拉强度为238mpa,伸长率为10.2%。
[0069]
由技术常识可知,本发明可以通过其它的不脱离其精神实质或必要特征的实施方案来实现。因此,上述公开的实施方案,就各方面而言,都只是举例说明,并不是仅有的。所有在本发明范围内或在等同于本发明的范围内的改变均被本发明包含。