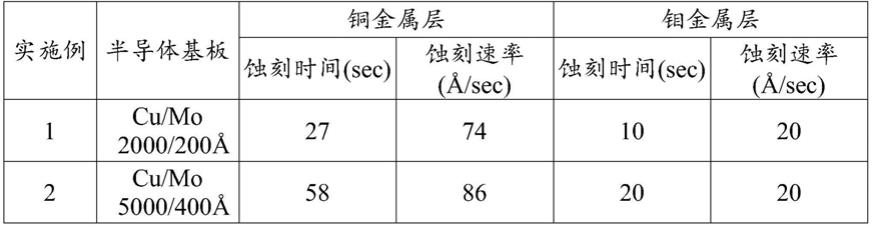
1.本发明涉及一种蚀刻液及蚀刻方法,特别涉及一种金属蚀刻液及金属蚀刻方法。
背景技术:2.随着半导体与平板显示器的大尺寸化,为了降低装置的电阻并提升其电流传导速率,多使用铜金属作为半导体基板上的布线材料。然而,由于铜金属与半导体基板(例如:玻璃基板)的结合性不佳,一般会在铜金属层与基板之间设置一层钼金属结合层,以使铜金属与半导体基板能够良好结合。
3.一般而言,主要是以湿蚀刻处理具有铜、钼等金属的金属多层膜。湿蚀刻是通过蚀刻液中的氧化剂氧化并溶解未被屏蔽(mask)遮蔽的目标金属,而未被溶解的金属则形成预定图案的技术。
4.在现有技术中,蚀刻液的氧化剂主要为过氧化氢。含有过氧化氢的蚀刻液酸虽然有高的理论使用寿命,然而在实际应用,例如金属被氧化溶解后所产生的金属离子会催化过氧化氢的分解,于是导致使用寿命下降。况且,使用浓度过高的过氧化氢作为氧化剂可能会产生燃烧或爆炸的危险。此外,为了延长蚀刻液的使用寿命,多以添加过氧化氢稳定剂、调整ph值、或控制反应温度等手段来实现。
技术实现要素:5.有鉴于上述问题,本发明的目的在于提供一种金属蚀刻液,所述蚀刻液包括:5至30wt%的氧化剂;2.5至15wt%的氨基酸;2.5至15wt%的磷酸盐;2.5至15wt%的非氨基酸类羧酸;以及余量的水;其中,所述氧化剂包含过氧化氢及过硫酸盐,且所述过氧化氢及所述过硫酸盐的使用重量比介于1:1.5至1:5。
6.优选地,所述过硫酸盐包括:由过硫酸钠、过硫酸钾、过硫酸铵、过硫酸氢钠、过硫酸氢钾和过硫酸氢铵所组成的群组中选出的至少一种。
7.优选地,所述氨基酸包括:由亚氨基二乙酸、亚氨基二丁酸、氨基三乙酸、氨基甲酸、氨基丁酸、乙二胺四乙酸、乙二胺四亚甲基膦酸、二乙烯三胺五乙酸、氨基三亚甲基膦酸、1-羟基亚乙基-1,1-二磷酸、二亚乙基三胺五亚甲基膦酸、亮氨酸、异亮氨酸、肌氨酸、丙氨酸、谷氨酸、赖氨酸、蛋氨酸、苯丙氨酸、谷氨酰胺、甘氨酸、胱氨酸、丝氨酸、精氨酸、天门冬氨酸和天冬酰胺所组成的群组中选出的至少一种。
8.优选地,所述磷酸盐包括:由磷酸钠、磷酸钾、磷酸铵、磷酸氢二钠、磷酸氢二钾、磷酸氢二铵、磷酸二氢钠、磷酸二氢钾、磷酸二氢铵所组成的群组中选出的至少一种。
9.优选地,所述非氨基酸类羧酸包括:由2-羟基丁二酸、乙二酸、甲酸、乙酸、丙酸、丁酸、戊酸、己酸、庚酸、辛酸、十二烷酸、十六烷酸、十四烷酸、硬脂酸、乙醇酸、丁二酸、二甘醇酸、己二酸、反乌头酸、水杨酸、丙二酸、丙烷-1,2,3-三羧酸、丙酮酸、戊二酸、乳酸、亚甲基丁二酸、亚麻油酸、亚麻酸、油酸、苯乙醇酸、苯甲酸、邻苯二甲酸、间苯二甲酸、对苯二甲酸、酒石酸、顺丁烯二酸、反丁烯二酸、羟基丁酸和柠檬酸所组成的群组中选出的至少一种。
10.优选地,所述金属蚀刻液还包括0.01至0.1wt%的唑类化合物。
11.优选地,所述唑类化合物包括:由吡唑、咪唑、恶唑、苯并吡唑、苯并咪唑、1,2,4-三唑、3-氨基-1,2,4-三唑、苯并三唑、甲基苯并三唑、羟甲基苯并三唑、四唑、5-甲基四唑、5-苯基四唑、5-氨基四唑和氯化三苯基四唑所组成的群组中选出的至少一种。
12.本发明另一目的在于提供一种蚀刻方法,所述方法包括:准备步骤,提供基板,且所述基板上包含金属层膜及遮蔽所述金属层膜的屏蔽膜;以及蚀刻步骤,使用本发明的金属蚀刻液对所述金属层膜中未被所述屏蔽膜遮蔽的部分进行蚀刻;其中,所述金属层膜包含由铜及钼所组成的群组中选出的至少一种或其合金。
13.优选地,所述金属层膜至少包含第一金属层和第二金属层,且所述第一金属层包含铜或其合金,所述第二金属层包含钼或其合金。
14.优选地,所述第一金属层的厚度介于1000至所述第二金属层的厚度介于100至
15.优选地,所述金属蚀刻液对所述第一金属层的蚀刻速率为70至所述金属蚀刻液对所述第二金属层的蚀刻速率为15至
16.优选地,所述蚀刻步骤中所述金属蚀刻液的铜负载浓度在8000ppm以下。
17.根据本发明的金属蚀刻液及金属蚀刻方法,通过同时使用过硫酸盐和过氧化氢作为氧化剂,并且调整两者之间的使用重量比,因此来蚀刻金属层时可以减少由于过氧化氢的自催化反应造成的蚀刻不稳定问题,而具有稳定的蚀刻速率,且可以增加蚀刻液中的铜溶解负载量以延长蚀刻液的使用寿命,以及降低过氧化氢的使用浓度以提升使用安全性。并且,通过使用特定组成的氨基酸、磷酸盐和非氨基酸类羧酸,可以使蚀刻而成的金属层膜具有平整的侧蚀面、更佳的蚀刻均匀性、更均一的蚀刻角,且没有底层金属残留。
附图说明
18.图1为本发明实施方式中金属蚀刻方法的流程图。
19.图2为本发明实施方式中金属蚀刻液的在0至8000ppm的铜添加浓度的温度曲线图。
20.图3为本发明实施方式中半导体基板被金属蚀刻液蚀刻后的sem剖面图。
21.图4为本发明实施方式中半导体基板被金属蚀刻液蚀刻后的另一sem剖面图。
22.附图标记说明:s101:准备步骤;s102:蚀刻步骤。
具体实施方式
23.在本发明的以下描述中,将在所属技术领域的技术人员能够轻易理解范围内省略现有技术的详细说明。
24.根据本发明,提供一种金属蚀刻液,所述膜蚀刻液包括以下组成物:5至30wt%的氧化剂;2.5至15wt%的氨基酸;2.5至15wt%的磷酸盐;2.5至15wt%的非氨基酸类羧酸;以及余量的水。本发明的金属蚀刻液不易受金属铜离子影响,有稳定的蚀刻速率、蚀刻液寿命长且有良好的铜溶解负载量,并且由于降低了过氧化氢的浓度,还具有不易燃烧或爆炸的优点。
25.在本发明中氧化剂的含量介于5至30wt%,当氧化剂含量低于5wt%时,蚀刻速率过慢且蚀刻效果不佳;而当氧化剂含量高于30wt%时,蚀刻速率过快而导致蚀刻均匀性下降。
26.本发明的氧化剂包含过氧化氢及过硫酸盐,且过氧化氢及过硫酸盐的使用重量比可介于1:1.5至1:5。当使用重量比低于1:1.5时,蚀刻液的蚀刻速率过慢而当使用重量比高于1:5,蚀刻液的蚀刻速率过快,且过氧化氢浓度过高而容易燃烧或爆炸。
27.其中,所述金属负载浓度是指蚀刻液溶解金属时的金属浓度,可作为是否需要更换蚀刻液的指标,因此越高的金属负载浓度代表有越高的使用寿命,其中优选多以铜负载浓度为代表。本发明的蚀刻液通过将过氧化氢及过硫酸盐的使用重量比设定在1:1.5至1:5时,在蚀刻液中的铜负载浓度至少高达8000ppm的情况下仍具有良好的蚀刻效果,具有良好的蚀刻液使用寿命及使用安全性。
28.本发明的过硫酸盐主要是通过其过硫酸根来提供氧化能力。优选地,所述过硫酸盐包括:由过硫酸钠、过硫酸钾、过硫酸铵、过硫酸氢钠、过硫酸氢钾和过硫酸氢铵所组成的群组中选出的至少一种。
29.优选地,本发明的氨基酸包括:由亚氨基二乙酸、亚氨基二丁酸、氨基三乙酸、氨基甲酸、氨基丁酸、乙二胺四乙酸、乙二胺四亚甲基膦酸、二乙烯三胺五乙酸、氨基三亚甲基膦酸、1-羟基亚乙基-1,1-二磷酸、二亚乙基三胺五亚甲基膦酸、亮氨酸、异亮氨酸、肌氨酸、丙氨酸、谷氨酸、赖氨酸、蛋氨酸、苯丙氨酸、谷氨酰胺、甘氨酸、胱氨酸、丝氨酸、精氨酸、天门冬氨酸和天冬酰胺所组成的群组中选出的至少一种。
30.优选地,本发明的磷酸盐包括:由磷酸钠、磷酸钾、磷酸铵、磷酸氢二钠、磷酸氢二钾、磷酸氢二铵、磷酸二氢钠、磷酸二氢钾、磷酸二氢铵所组成的群组中选出的至少一种。
31.优选地,本发明的非氨基酸类羧酸包括:由2-羟基丁二酸、乙二酸、甲酸、乙酸、丙酸、丁酸、戊酸、己酸、庚酸、辛酸、十二烷酸、十六烷酸、十四烷酸、硬脂酸、乙醇酸、丁二酸、二甘醇酸、己二酸、反乌头酸、水杨酸、丙二酸、丙烷-1,2,3-三羧酸、丙酮酸、戊二酸、乳酸、亚甲基丁二酸、亚麻油酸、亚麻酸、油酸、苯乙醇酸、苯甲酸、邻苯二甲酸、间苯二甲酸、对苯二甲酸、酒石酸、顺丁烯二酸、反丁烯二酸、羟基丁酸和柠檬酸所组成的群组中选出的至少一种。
32.在本发明中,由于氨基酸和非氨基酸类羧酸均属于有机酸,在蚀刻时可以提供氢离子而作为使金属氧化溶解为金属离子的反应物,因此有利于金属层膜的蚀刻,且不需要使用氯化物即可以避免底层金属(例如钼)的残留。
33.并且,由于本发明的氨基酸、磷酸盐和非氨基酸类羧酸均可以作为螯合剂,与蚀刻产生的金属(例如铜)离子螯合,遮蔽金属离子以避免金属离子催化过氧化氢的分解,通过上述具有不同结构的三种螯合剂可以提供充份稳定过氧化氢以延长蚀刻液的使用寿命的功能。
34.此外,由于本发明的磷酸盐具有多质子特性,而氨基酸同时具有可结合氢离子的氨基与可释放氢离子的羧基,两者均可以作为ph调节剂(酸碱缓冲剂),稳定蚀刻液的ph值,有利于蚀刻反应进行,并且避免过氧化氢因ph值的剧烈变化而分解,也可以稳定过氧化氢并延长蚀刻液的使用寿命。
35.优选地,本发明的金属蚀刻液还包括0.01至0.1wt%的唑类化合物。
36.优选地,本发明的唑类化合物包括:由吡唑、咪唑、恶唑、苯并吡唑、苯并咪唑、1,2,4-三唑、3-氨基-1,2,4-三唑、苯并三唑、甲基苯并三唑、羟甲基苯并三唑、四唑、5-甲基四唑、5-苯基四唑、5-氨基四唑和氯化三苯基四唑所组成的群组中选出的至少一种。
37.在本发明中,由于唑类化合物可以作为蚀刻抑制剂,其可以降低侧蚀,并通过调节不同金属(例如铜、钼)的蚀刻选择比,避免形成大于或等于90
°
的蚀刻角(即倒倾角),并且,由于降低了蚀刻速率,可以使侧蚀深度更均匀,并使蚀刻角更均一且使角度界于更精准的范围。
38.此外,本发明的氨基酸、磷酸盐和非氨基酸类羧酸与金属离子螯合所形成的络合物也具有上述蚀刻抑制剂的功能。
39.因此,本发明的金属蚀刻液,通过使用特定组成的氨基酸、磷酸盐和非氨基酸类羧酸,可以使由所述蚀刻液蚀刻而成的金属层膜具有更小的侧蚀、更佳的蚀刻均匀性、更均一的蚀刻角,且没有底层金属残留,并提高蚀刻液的使用安全性。
40.以下,配合图1来说明根据本发明另提供的一种金属蚀刻方法,然而本发明的金属蚀刻方法并不局限于图1所示的方法,而是可在任一个步骤的前后,根据需要加入表面处理、清洗、干燥等的惯用手段。本发明的金属蚀刻方法包括以下步骤:准备步骤s101,提供基板,且所述基板上包含金属层膜及遮蔽所述金属层膜的屏蔽膜;以及蚀刻步骤s102,使用本发明的金属蚀刻液对所述金属层膜中未被所述屏蔽膜遮蔽的部分进行蚀刻。
41.优选地,本发明的金属层膜包含由铜及钼所组成的群组中选出的至少一种或其合金。优选地,本发明的金属层膜可为由这些金属中的至少一种及其合金组成的单一金属层。
42.优选地,本发明的金属层膜至少包含第一金属层及第二金属层,且所述第一金属层包含铜或其合金,所述第二金属层包含钼或其合金。优选地,本发明的金属层膜为包含上述第一金属层及上述第二金属层的配置时,第一金属层覆盖于第二金属层的上表面,且屏蔽膜覆盖于第一金属层的上表面。
43.优选地,本发明的基板可以是玻璃基板。
44.优选地,本发明的第一金属层的厚度介于1000至且第二金属层的厚度介于100至
45.优选地,本发明的金属蚀刻液对所述第一金属层的蚀刻速率为70至且对所述第二金属层的蚀刻速率为15至
46.优选地,本发明中的金属蚀刻液中的铜负载浓度在8000ppm以下时,所述金属蚀刻液可以维持良好的蚀刻效果。
47.优选地,在25至38℃的温度使用本发明的蚀刻液进行蚀刻,所述金属层膜的蚀刻角度具有良好的均一性。
48.为了验证本发明的金属蚀刻液及金属蚀刻方法的功效,以下通过实施例的方式来说明本发明的蚀刻性能、使用寿命及安全性。
49.[实施例1]
[0050]
首先,使去离子水中含有10wt%的过硫酸铵、5wt%的过氧化氢、6.5wt%的甘氨酸、10wt%的磷酸铵、5wt%的冰醋酸,搅拌使其混合均匀,制备金属蚀刻液。
[0051]
准备玻璃基板,且在玻璃基板上由下而上依序包含厚度为的钼金属层、厚度为的铜金属层以及屏蔽膜而制得半导体基板。在32℃的温度下,将半导体基板静置于所制备的金属蚀刻液中,肉眼观察(watch and stop)未被屏蔽膜遮蔽的铜金属层与钼金属层的蚀刻状态,并记录蚀刻时间。在铜金属的颜色(红橙色)和钼金属的颜色(灰黑色)完全消失时,分别表示未被屏蔽遮蔽的铜金属层和钼金属层已蚀刻完,记录金属层各自的蚀刻时间,并由金属层的厚度和蚀刻时间计算蚀刻速率,测试结果记载于下述表1。
[0052]
接着取另一全新半导体基板及全新蚀刻液,使用130%的总蚀刻时间进行蚀刻。在实施例1中,所需总蚀刻时间为(27+10)
×
130%=约50秒。
[0053]
在完成的130%蚀刻并清洗干燥后,使用扫描式电子显微镜(sem,hitachi)观察未被屏蔽膜遮蔽的铜/钼金属层在被蚀刻后的左侧(l)和右侧(r)的侧蚀深度和蚀刻角,分别均选取6个点进行重复测试,并计算重复测试的侧蚀深度和蚀刻角的变异系数值(c.v.),实验条件及测试结果均记载于下述表2。
[0054]
[实施例2]
[0055]
在实施例2中,以与实施例1相同的方式制备金属蚀刻液、半导体基板并蚀刻金属层膜,除了将半导体基板的铜/钼金属层的厚度分别改变为之外。具体实验条件及测试结果如下表1和表2所示。
[0056]
[表1]
[0057][0058]
[表2]
[0059][0060]
根据表1的结果,本发明的蚀刻液对厚度介于2000至的铜金属层的蚀刻速
率介于70至对厚度介于200至的钼金属层的蚀刻速率介于15至可证实本发明具有良好的蚀刻速率。
[0061]
根据表2的结果,本发明的蚀刻液对上述不同厚度的铜/钼金属层膜的单侧侧蚀均小于500nm,小于现有技术的单侧小于1μm的侧蚀;且蚀刻角介于45
°
至55
°
之间,相比于现有技术的介于20
°
至60
°
之间的蚀刻角,将蚀刻角限制为更精准的范围。并且,根据上述重复测试结果,侧蚀和蚀刻角的变异系数均小于5%,没有显着差异,具有良好的侧蚀均匀性和蚀刻角均一性。
[0062]
[实施例3]
[0063]
在实施例3中,除了将半导体基板的铜/钼金属层的厚度分别改变为之外,以与实施例1相同的方式制备金属蚀刻液、半导体基板并蚀刻金属层膜,但不控制蚀刻液的温度,同时记录蚀刻后的蚀刻液温度。并且,以与实施例1相同的方式测试侧蚀深度和蚀刻角,除了分别仅选取1个点进行测试之外。蚀刻液中的铜添加浓度及测试结果均记载于下述表3。
[0064]
[实施例4至7]
[0065]
在实施例4至7中,除了将半导体基板的铜/钼金属层的厚度分别改变为之外,以与实施例1相同的方式制备半导体基板及蚀刻金属层膜,但不控制蚀刻液的温度,且分别沿用实施例3至6中蚀刻开始后经过2小时的蚀刻液,并且分别向蚀刻液中添加2000ppm的铜粉,然后进行蚀刻。并且,以与实施例3相同的方式测试温度、侧蚀深度和蚀刻角。自实施例3开始的蚀刻累积时间和铜累积添加浓度及测试结果如下表3所示。
[0066]
此外,在实施例7中,在蚀刻结束(累积时间8小时)之后蚀刻液中的铜添加浓度将到达8000ppm,此后持续观察蚀刻液的温度变化至累积时间至48小时。
[0067]
另外,进一步计算实施例3至7中的在0至8000ppm的铜添加浓度范围(铜累积添加浓度范围)内的侧蚀深度和蚀刻角的变异系数值。计算结果如下表3所示。
[0068]
[表3]
[0069][0070]
根据表3的结果,在0至8000ppm的铜添加浓度范围内的对金属层膜进行蚀刻相同的时间,侧蚀的变异系数小于10%,没有显着差异,表示在8000ppm的铜添加浓度范围内随着铜添加浓度的增加的蚀刻速率不变,本发明的蚀刻液可不受金属离子催化的影响,并且具有稳定的蚀刻速率及良好的蚀刻稳定性。
[0071]
并且,根据表3的结果,在0至8000ppm的铜添加浓度范围内的对金属层膜进行蚀刻相同的时间,蚀刻角的变异系数小于5%,没有显着差异,表示在8000ppm的铜添加浓度范围
内,对蚀刻角的控制效果不变,同样证实具有良好的蚀刻稳定性。如表3及图2所示,本发明的蚀刻液即使在铜添加浓度高达8000ppm(即,铜负载浓度至少高达8000ppm)的情况下,蚀刻液的温度均位于23
±
0.5℃的范围。此外,在48小时内持续观察,蚀刻液的温度也位于23
±
0.5℃的范围。由上述结果可知,本发明的蚀刻液即使在含有高浓度的金属(例如,8000ppm以下的铜负载浓度)的情况下,反应速率依旧稳定且具有良好的温度稳定性,从而避免升温造成过氧化氢加速分解而降低蚀刻液使用寿命及蚀刻稳定性的问题,并且不会因为升温造成过氧化氢爆炸或燃烧,具有良好的使用安全性。
[0072]
此外,根据实施例3至7的结果,虽然蚀刻时间累积至8小时,但其侧蚀深度未显着改变,显示整体的蚀刻速率并未衰退,在蚀刻过程中蚀刻液具有高度稳定性。
[0073]
另外,根据表3的结果,本发明的蚀刻液即使在铜添加浓度高达8000ppm(即,铜负载浓度至少高达8000ppm)的情况下,对铜/钼金属层膜的单侧侧蚀仍小于450nm,小于现有技术的单侧小于1μm的侧蚀;并且,蚀刻角介于40
°
至50
°
之间,相比于现有技术的界于20
°
至60
°
之间的蚀刻角,将蚀刻角限制为更精准的范围。
[0074]
如图3和图4所示,使用扫描式电子显微镜(sem,hitachi)观察实施例2在完成130%的过蚀刻后的结构型态,玻璃基板上没有钼金属残留,并且铜/钼金属层呈现约45
°
的蚀刻角。
[0075]
综上所述,本发明的金属蚀刻液及金属蚀刻方法,通过同时使用过硫酸盐和过氧化氢作为氧化剂,并且调整两者之间的使用重量比,因此来蚀刻金属层时可以减少由于过氧化氢的自催化反应造成的蚀刻不稳定问题并且减少由于高浓度的过氧化氢造成的安全性问题,从而具有良好的蚀刻速率,并且可以增加蚀刻液中的铜溶解负载量以延长蚀刻液的使用寿命。
[0076]
并且,本发明的金属蚀刻液及金属蚀刻方法,通过使用特定组成的氨基酸、磷酸盐和非氨基酸类羧酸,可以使蚀刻而成的金属层膜具有平整的侧蚀面、更佳的蚀刻均匀性、更均一的蚀刻角,且没有底层钼金属残留。
[0077]
以上所述的是本发明的优选实施方式,应当指出对于本技术领域的普通人员来说,在不脱离本发明所述的原理前提下还可以作出若干改进和润饰,这些改进和润饰也在本发明的保护范围内。