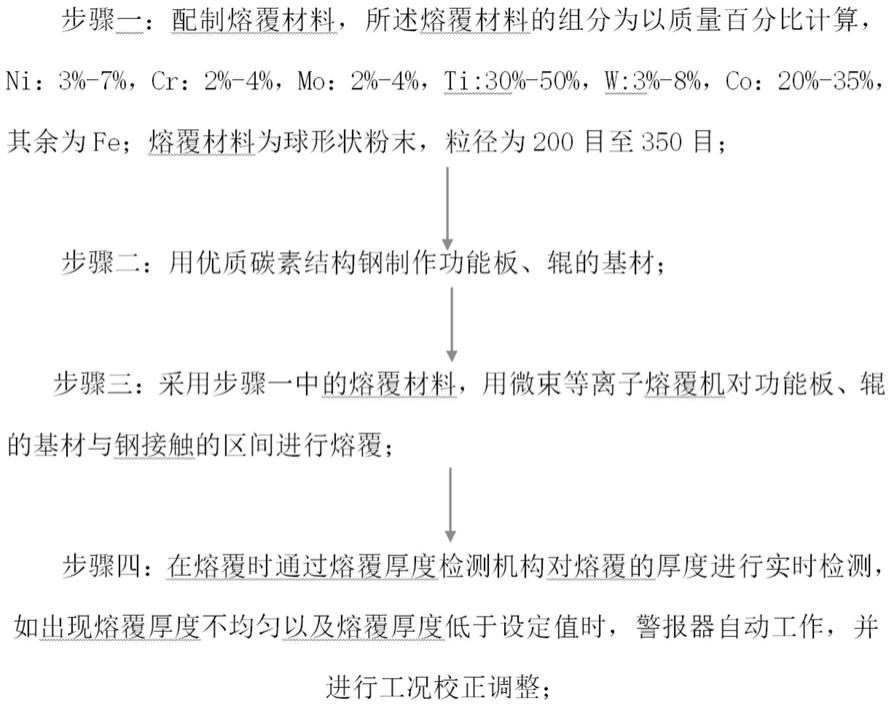
1.本发明属于复合制造技术领域,特别是涉及一种微束等离子熔敷制备热轧产线功能板、辊的工艺方法。
背景技术:2.热轧就是轧钢过程中或轧钢之前需要对材料进行加热的,一般要加热到再结晶温度以上,如:1000度以上。随着技术的不断升级,市场对热轧产品精度要求越来越高,对产线各类工艺、工况备件的质量、性能要求也越来越高。
3.热轧功能板、辊是热轧生产线影响产品质量和轧线作业效率的最核心的功能组件之一,对热轧产品的质量起着非常重要的作用。为了增强热轧功能板、辊的耐磨性能,现有技术在热轧功能板、辊的制造过程中通过(1) 提高单质产品的合金含量;(2)表面堆焊合金材料;(3)表面激光熔覆 ni基耐磨合金等方式来实现,但是由于各方式均存在不足(生产难度大、成本高、产线适用受到限制等)而存在各类问题,因此我们对此进行改进,提出了一种微束等离子熔敷制备热轧功能板、辊的工艺方法。
技术实现要素:4.本发明的目的在于提供一种微束等离子熔敷制备热轧功能板、辊的工艺方法,以解决现有的问题:现有技术主要有以下几种不同的工艺方法: (1)单一均质,指产品本体为同一组分,缺点在于耐磨耐热元素含量低,产品性能差;耐热耐磨元素高,制造工艺困难,成本高;(2)堆焊复合,指在功能板、辊的表面堆焊一层新材料,缺点在于堆焊工艺热输入量大,对材料的稀释率高,工件变形大,后续加工量大,功能材料起不到应有效果,使用寿命达不到预期;(3)激光熔敷复合,指在功能板、辊的表面激光熔覆一层约1mm厚的耐磨合金层,缺点在于成本高,功能层厚度设计受限,另外对于产线的适用性受限,例如,激光熔覆的功能板、辊,绝大部分熔敷材料属于ni基粉末,对于不锈钢产线,功能板、辊会出现结瘤粘钢现象。
5.为解决上述技术问题,本发明是通过以下技术方案实现的:
6.本发明为一种微束等离子熔敷制备热轧产线功能板、辊的工艺方法,微束等离子熔敷制备热轧功能板、辊的工艺方法包括以下步骤:
7.步骤一:配制熔覆材料,所述熔覆材料的组分为以质量百分比计算, ni:3%-7%,cr:2%-4%,mo:2%-4%,ti:30%-50%,w:3%-8%,co:20%-35%,其余为fe;熔覆材料为球形状粉末,粒径为200目至350目;
8.步骤二:用优质碳素结构钢制作热轧功能板、辊的基材;
9.步骤三:采用步骤一中的熔覆材料,用微束等离子熔覆机对热轧功能板、辊的基材进行熔覆;
10.步骤四:在熔覆时通过熔覆厚度检测机构对熔覆的厚度进行实时检测,如出现熔覆厚度不均匀以及熔覆厚度低于设定值时,警报器自动工作,并进行校正。
11.步骤五:将熔敷好的功能板、辊,按照图纸精度要求进行精加工。
12.进一步地,所述采用微束等离子熔覆机进行焊接,焊接时主弧电流60a 至80a,维弧电流5a至15a。
13.进一步地,所述基值电流15a至60a,熔覆厚度为1mm至5mm。
14.进一步地,所述采用送粉器将熔覆材料送入热轧功能板、辊基材与钢接触的功能区的上方。
15.进一步地,所述熔覆材料的组分为以质量百分比计算,ni:3%-7%,cr: 2%-4%,mo:2%-4%,ti:30%-50%,w:3%-8%,co:20%-35%,其余为fe;
16.进一步地,所述微束等离子熔覆机的焊接方式为摆动和递进,摆动宽度6mm至8mm。
17.进一步地,所述熔覆厚度检测机构包括磁性熔覆厚度测量仪和涡流式熔覆厚度测量仪的一种。
18.进一步地,所述热轧功能板、辊包括钢铁领域热轧(带、型、管)生产线与钢材接触的移钢机衬板、热卷箱入口侧导板、热卷箱出口侧导板、精轧导位板、卷曲侧导板、各类输送辊道、活套辊、夹送辊、导辊、导槽等。
19.本发明具有以下有益效果:
20.1、本发明通过将耐高温、耐磨损的合金材料熔覆在热轧产线功能板、辊功能区的表面,大大提高了热轧产线功能板、辊耐高温、耐磨损的性能,增加了使用寿命,避免热轧功能板、辊出现结瘤粘钢及耐磨性差的情况。微束等离子熔覆分区复合制造的功能板、辊较目前其它技术路线下生产的功能板、辊具有更理想的功能层厚度设计、更高的精度保持能力、更宽泛的产线适用性、更高的性价比优势。
21.2、本发明通过在熔覆时通过熔覆厚度检测机构对熔覆的厚度进行实时检测,可以提高微束等离子熔覆耐磨合金层厚度的均匀性,避免出现产品局部失效带来的影响。
22.当然,实施本发明的任一产品并不一定需要同时达到以上所述的所有优点。
附图说明
23.为了更清楚地说明本发明实施例的技术方案,下面将对实施例描述所需要使用的附图作简单地介绍,显而易见地,下面描述中的附图仅仅是本发明的一些实施例,对于本领域普通技术人员来讲,在不付出创造性劳动的前提下,还可以根据这些附图获得其他的附图。
24.图1为本发明的整体连接框图。
具体实施方式
25.下面将结合本发明实施例中的附图,对本发明实施例中的技术方案进行清楚、完整地描述,显然,所描述的实施例仅仅是本发明一部分实施例,而不是全部的实施例。基于本发明中的实施例,本领域普通技术人员在没有作出创造性劳动前提下所获得的所有其它实施例,都属于本发明保护的范围。
26.请参阅图1所示,本发明为一种微束等离子熔敷制备热轧产线功能板、辊的工艺方法,微束等离子熔敷制备热轧产线功能板、辊的工艺方法包括以下步骤:
27.步骤一:配制熔覆材料,所述熔覆材料的组分为以质量百分比计算, ni:3%-7%,
cr:2%-4%,mo:2%-4%,ti:30%-50%,w:3%-8%,co:20%-35%,其余为fe;熔覆材料为球形状粉末,粒径为200目至350目。
28.通过将耐高温、耐磨损的合金材料熔覆在热轧功能板、辊的表面,大大提高了热轧功能板、辊耐高温、耐磨损的性能,增加了使用寿命,避免热轧功能板、辊出现结瘤粘钢及耐磨性差的现象,微束等离子熔覆功能板、辊较目前其他工艺路线下生产的功能板、辊具有明显的性价比及产线适用性优势,且使功能板、辊基材可以重复利用避免造成资源的浪费;
29.步骤二:用优质碳素结构钢制作热轧功能板、辊的基材。
30.首次熔敷与后续再制造过程均要保证设定的功能板、辊熔敷区基材的表面光洁且无疲劳裂纹;热轧功能板、辊基材是热轧功能板、辊的主体,即移钢机衬板、热卷箱入口侧导板、热卷箱出口侧导板、精轧导板、卷曲侧导板、各种传输辊道、活套辊、导辊、导槽等在轧线与红钢之间产生滚动或滑动摩擦的功能板、辊的主体,也就是,不带有熔覆材料的热轧功能板、辊的基体;
31.步骤三:采用步骤一中的熔覆材料,用微束等离子熔覆机对热轧功能板、辊的基材进行熔覆。
32.将耐高温、耐磨损的合金材料熔覆在热轧功能板、辊的表面,大大提高了热轧功能板、辊耐高温、耐磨损的性能,增加了使用寿命,该组分能够使热轧功能板、辊的耐磨性能、耐疲劳性能和使用寿命都得以明显提高。
33.步骤四:在熔覆时通过熔覆厚度检测机构对熔覆的厚度进行实时检测,如出现熔覆厚度不均匀以及熔覆厚度低于设定值时,警报器自动工作,并进行校正。
34.步骤五:将熔敷好的功能板、辊,按照图纸精度要求进行精加工。
35.通过在熔覆时通过熔覆厚度检测机构对熔覆的厚度进行实时检测,可以提高等离子熔覆耐磨合金层厚度的均匀性,避免出现在线使用时间短的现象;
36.优选地,所述采用微束等离子熔覆机进行焊接,焊接时主弧电流60a 至80a,维弧电流5a至15a。采用微束等离子熔覆机进行焊接,焊接时主弧电流60a至80a,维弧电流5a至15a,基值电流15a至60a,熔覆厚度为 1mm至5mm。
37.优选地,所述采用送粉器将熔覆材料送入热轧功能板、辊基材与钢接触的功能区的上方。微束等离子熔覆机的焊接方式为摆动和递进,摆动宽度6mm至8mm。
38.优选地,所述熔覆厚度检测机构包括磁性熔覆厚度测量仪和涡流式熔覆厚度测量仪的一种。
39.优选地,所述热轧功能板、辊包括钢铁领域热轧(带、型、管)生产线与钢材接触的移钢机衬板、热卷箱入口侧导板、热卷箱出口侧导板、精轧导位板、卷曲侧导板、各类输送辊道、活套辊、夹送辊、导辊、导槽等
40.本实施例的一个具体应用为:配制熔覆材料,熔覆材料的组分为以质量百分比计算,ni:3%-7%,cr:2%-4%,mo:2%-4%,ti:30%-50%,w:3%-8%, co:20%-35%,其余为fe,熔覆材料为球形状粉末,粒径为200目至350目,用优质碳素结构钢制作热轧功能板、辊的基材,采用上述的熔覆材料,用微束等离子熔覆机对热轧功能板、辊的基材进行熔覆,在熔覆时通过熔覆厚度检测机构对熔覆的厚度进行实时检测,如出现熔覆厚度不均匀以及熔覆厚度低于设定值时,警报器自动工作,并进行校正。
41.在本说明书的描述中,参考术语“一个实施例”、“示例”、“具体示例”等的描述意指
结合该实施例或示例描述的具体特征、结构、材料或者特点包含于本发明的至少一个实施例或示例中。在本说明书中,对上述术语的示意性表述不一定指的是相同的实施例或示例。而且,描述的具体特征、结构、材料或者特点可以在任何的一个或多个实施例或示例中以合适的方式结合。
42.以上公开的本发明优选实施例只是用于帮助阐述本发明。优选实施例并没有详尽叙述所有的细节,也不限制该发明仅为所述的具体实施方式。显然,根据本说明书的内容,可作很多的修改和变化。本说明书选取并具体描述这些实施例,是为了更好地解释本发明的原理和实际应用,从而使所属技术领域技术人员能很好地理解和利用本发明。本发明仅受权利要求书及其全部范围和等效物的限制。