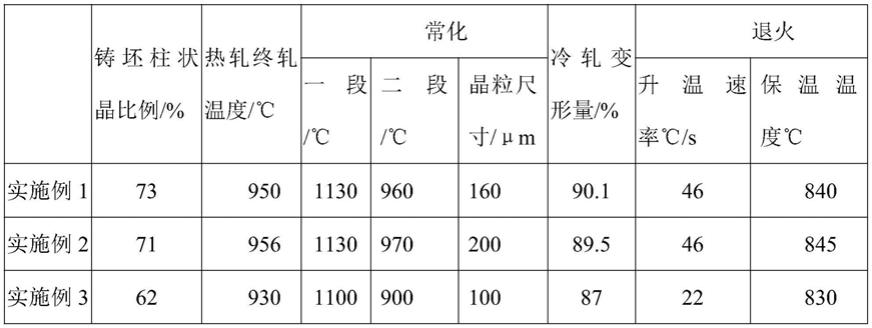
1.本发明涉及钢铁冶炼技术领域,特别涉及一种优化高磁感取向硅钢初次再结晶织构的控制方法。
背景技术:2.在晶粒取向中《001》晶向是最容易被磁化的方向,取向硅钢是通过抑制剂的作用使具有goss织构的晶粒吞噬相邻非goss织构晶粒而异常长大,最终获得沿轧制方向取向一致的《001》晶向。因此合理的抑制剂和合适的织构是获得低铁损高磁感的关键。其中对于抑制剂控制的工艺方法阐述较多,而对织构的控制阐述较少。
3.在高磁感取向硅钢生产中,为了得到更精准的goss织构,需要在初次再结晶后织构中存在少量的{111}《001》晶粒以及较多的与{111}《001》晶粒具有σ9重位晶界关系的{111}《112》和{114}《481》晶粒。其中{114}晶粒位向的分散性比{111}晶粒更小,基体中{114}晶粒增多,以后形成的[110]《001》晶粒位向更精准,因此提高初次再结晶后{114}晶粒的比例是提高磁感应强度的重要手段,为此,我们提出一种优化高磁感取向硅钢初次再结晶织构的控制方法来解决上述问题。
技术实现要素:[0004]
为了克服现有技术的不足,本发明的目的在于提供在高磁感取向硅钢生产中,为了得到更精准的goss织构,需要在初次再结晶后织构中存在少量的{110}《001》晶粒以及较多的与{110}《001》晶粒具有σ9重位晶界关系的{111}《112》和{114}《481》晶粒,其中{114}]晶粒位向的分散性比{111}晶粒更小,基体中{114}晶粒增多,以后形成的{110}《001》晶粒位向更精准。
[0005]
一种优化高磁感取向硅钢初次再结晶织构的控制方法的目的是通过提高{114}晶粒比例实现提高磁性能,针对现有技术生产高磁感取向硅钢存在的问题,提出了通过常化工艺获得较大尺寸的晶粒和提高冷轧压下率并针对常化晶粒尺寸确定脱碳退火工艺的方法,实现了通过优化高磁感取向硅钢初次再结晶织构提高磁性能的目的。
[0006]
本发明的上述技术目的是通过以下技术方案得以实现的:
[0007]
一种优化高磁感取向硅钢初次再结晶织构的控制方法,具体操作步骤如下:
[0008]
步骤1:冶炼后浇铸成200~250mm规格铸坯,浇铸过程中采用强水冷工艺,冷却水配比为0.9~1.1l/kg柱状晶比例控制在60~80%;
[0009]
步骤2:加热温度为1150~1200℃,加热时间200~300min。
[0010]
步骤3:粗轧开轧温度为1060~1130℃,粗轧终轧温度为1020~1050℃,粗轧道次变形量为25%~35%,粗轧总变形量为75~85%,精轧开轧温度为1000~1020℃,精轧终轧温度为940~980℃,精轧道次变形量为20~50%,精轧总变形量为85~95%,卷取温度控制在520~560℃;
[0011]
步骤4:采用两段式常化工艺,常化高温段保温温度为1100~1150℃,保温60~
80s,保证抑制剂的充分固溶,然后降温到950~1000℃保温160~180s,一方面促进抑制剂的充分析出,另一方面促进晶粒长大,然后以2~5℃/s冷却速率进行缓冷进一步促进再结晶后的晶粒长大,冷却到730~750℃时采用水冷,冷却速度为40~60℃/s,常化后获得晶粒尺寸d=150~300μm;
[0012]
步骤5:采用二十辊可逆轧机进行冷轧,总变形量控制在89~92%,道次变形量为25~40%,时效轧制温度控制在200~260℃。
[0013]
步骤6:脱碳退火升温阶段升温速率30℃/s以上,脱碳退火温度t=800+3.18d0.5(℃)。
[0014]
进一步的,还有步骤7:进行高温退火和平整拉伸。
[0015]
进一步的,在步骤3中的脱碳退火温度按下式计算:t=800+3.18d0.5(℃)。
[0016]
综上所述,本发明具有以下有益效果:
[0017]
①
连铸采用强冷工艺以提高{100}织构比例,脱碳拖火后可以获得较多的{114}织构;
[0018]
②
脱碳退火时{114}织构的晶粒在晶内形核而{111}在晶界形核,因为为了获得较多的{114}织构需要在常化过程获得尺寸较大的晶粒;
[0019]
③
提高冷轧压下率可以提高畸变能从而提高再结晶形核率率,因为晶界面积有限,因此晶内形核得到发展,进而促进了{114}织构的发展;
[0020]
④
提高脱碳退火升温速度可以提高再结晶形核率进而促进了{114}织构的发展,脱碳退火温度和晶粒大小有着直接关系,常化晶粒较大时再结晶温度会升高,因此采用更高的退火温度,常化晶粒较小时再结晶温度会降低,因此采用较低的退火温度;
[0021]
⑤
提高h2比例可促进{110}织构的发展。
具体实施方式
[0022]
下面将对本发明实施例中的技术方案进行清楚、完整地描述,显然,所描述的实施例仅是本发明的一部分实施例,而不是全部的实施例。基于本发明中的实施例,本领域普通技术人员在没有做出创造性劳动前提下所获得的所有其它实施例,都属于本发明保护的范围。
[0023]
实施例1
[0024]
本发明较优实施例中一种优化高磁感取向硅钢初次再结晶织构的控制方法,具体操作步骤如下:
[0025]
步骤1:冶炼后浇铸成250mm规格铸坯,浇铸过程中采用强水冷工艺,冷却水配比为1.1l/kg柱状晶比例控制在80%;
[0026]
步骤2:加热温度为1200℃,加热时间300min。
[0027]
步骤3:粗轧开轧温度为1130℃,粗轧终轧温度为1050℃,粗轧道次变形量为35%,粗轧总变形量为85%,精轧开轧温度为1020℃,精轧终轧温度为980℃,精轧道次变形量为50%,精轧总变形量为95%,卷取温度控制在560℃;
[0028]
步骤4:采用两段式常化工艺,常化高温段保温温度为1150℃,保温80s,保证抑制剂的充分固溶,然后降温到1000℃保温180s,一方面促进抑制剂的充分析出,另一方面促进晶粒长大,然后以5℃/s冷却速率进行缓冷进一步促进再结晶后的晶粒长大,冷却到750℃
时采用水冷,冷却速度为60℃/s,常化后获得晶粒尺寸为300μm;
[0029]
步骤5:采用二十辊可逆轧机进行冷轧,总变形量控制在92%,道次变形量为40%,时效轧制温度控制在260℃;
[0030]
步骤6:脱碳退火升温阶段升温速率30℃/s以上,炉内氛围为60%的氢气,脱碳退火温度t=800+3.18d0.5(℃);
[0031]
步骤7:进行高温退火和平整拉伸。
[0032]
实施例2
[0033]
本发明较优实施例中一种优化高磁感取向硅钢初次再结晶织构的控制方法,具体操作步骤如下:
[0034]
步骤1:冶炼后浇铸成200mm规格铸坯,浇铸过程中采用强水冷工艺,冷却水配比为0.9l/kg柱状晶比例控制在60%;
[0035]
步骤2:加热温度为1150℃,加热时间200min。
[0036]
步骤3:粗轧开轧温度为1060℃,粗轧终轧温度为1020℃,粗轧道次变形量为25%,粗轧总变形量为75%,精轧开轧温度为1000℃,精轧终轧温度为940℃,精轧道次变形量为20%,精轧总变形量为85%,卷取温度控制在520℃;
[0037]
步骤4:采用两段式常化工艺,常化高温段保温温度为1100℃,保温60s,保证抑制剂的充分固溶,然后降温到950℃保温160s,一方面促进抑制剂的充分析出,另一方面促进晶粒长大,然后以2℃/s冷却速率进行缓冷进一步促进再结晶后的晶粒长大,冷却到730℃时采用水冷,冷却速度为40℃/s,常化后获得晶粒尺寸为150μm;
[0038]
步骤5:采用二十辊可逆轧机进行冷轧,总变形量控制在89%,道次变形量为25%,时效轧制温度控制在200℃;
[0039]
步骤6:脱碳退火升温阶段升温速率30℃/s以上,炉内氛围为40%的氢气,脱碳退火温度t=800+3.18d0.5(℃);
[0040]
步骤7:进行高温退火和平整拉伸。
[0041]
实施例3
[0042]
本发明较优实施例中一种优化高磁感取向硅钢初次再结晶织构的控制方法,具体操作步骤如下:
[0043]
步骤1:冶炼后浇铸成230mm规格铸坯,浇铸过程中采用强水冷工艺,冷却水配比为1.0l/kg柱状晶比例控制在70%;
[0044]
步骤2:加热温度为1180℃,加热时间250min。
[0045]
步骤3:粗轧开轧温度为1100℃,粗轧终轧温度为1040℃,粗轧道次变形量为30%,粗轧总变形量为80%,精轧开轧温度为1010℃,精轧终轧温度为960℃,精轧道次变形量为35%,精轧总变形量为90%,卷取温度控制在540℃;
[0046]
步骤4:采用两段式常化工艺,常化高温段保温温度为1130℃,保温70s,保证抑制剂的充分固溶,然后降温到980℃保温170s,一方面促进抑制剂的充分析出,另一方面促进晶粒长大,然后以4℃/s冷却速率进行缓冷进一步促进再结晶后的晶粒长大,冷却到740℃时采用水冷,冷却速度为50℃/s,常化后获得晶粒尺寸为230μm;
[0047]
步骤5:采用二十辊可逆轧机进行冷轧,总变形量控制在90%,道次变形量为33%,时效轧制温度控制在230℃;
[0048]
步骤6:脱碳退火升温阶段升温速率30℃/s以上,炉内氛围为50%的氢气,脱碳退火温度t=800+3.18d0.5(℃);
[0049]
步骤7:进行高温退火和平整拉伸。
[0050]
本发明实施例1~2的工艺参数见表1;本发明实施例1~2的成材率和性能情况见表2(表中对比例为常规工艺数据)。
[0051]
表1实施例1~3的工艺参数
[0052][0053]
表2
[0054] {114}《481》{111}《112》{100}《011》{110}《001》p1.7b8实施例129.7%17.3%6.2%2.53%0.98w/kg1.93t实施例230.3%16.3%6.3%2.61%1.03w/kg1.93t实施例322.6%20.17%6.9%2.46%1.06w/kg1.90t
[0055]
综上所述:
[0056]
①
连铸采用强冷工艺以提高{100}织构比例,脱碳拖火后可以获得较多的{114}织构;
[0057]
②
脱碳退火时{114}织构的晶粒在晶内形核而{111}在晶界形核,因为为了获得较多的{114}织构需要在常化过程获得尺寸较大的晶粒;
[0058]
③
提高冷轧压下率可以提高畸变能从而提高再结晶形核率率,因为晶界面积有限,因此晶内形核得到发展,进而促进了{114}织构的发展;
[0059]
④
提高脱碳退火升温速度可以提高再结晶形核率进而促进了{114}织构的发展,脱碳退火温度和晶粒大小有着直接关系,常化晶粒较大时再结晶温度会升高,因此采用更高的退火温度,常化晶粒较小时再结晶温度会降低,因此采用较低的退火温度;
[0060]
⑤
提高h2比例可促进{110}织构的发展。
[0061]
以上显示和描述了本发明的基本原理和主要特征和本发明的优点。本行业的技术人员应该了解,本发明不受上述实施例的限制,上述实施例和说明书中描述的只是说明本发明的原理,在不脱离本发明精神和范围的前提下,本发明还会有各种变化和改进,这些变化和改进都落入要求保护的本发明范围内。本发明要求保护范围由所附的权利要求书及其等效物界定。