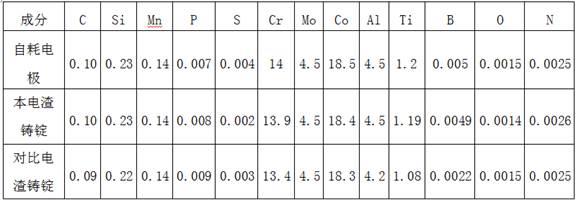
1.本发明涉及一种电渣重熔方法,尤其是一种电渣重熔含硼高温合金精确控制硼的方法。
背景技术:2.高温合金具有优异的使用性能,广泛用于飞机发动机、汽轮机、柴油机等机械设备的制造领域。高温合金的工作温度可达600~1300℃,在此条件下晶界强度是材料的最薄弱环节。据统计,晶界断裂贡献了高温合金失效的50%份额。所以,高温合金的发展逐渐形成两个方向:一是消除晶界,直接铸造成单晶高温合金,使用温度可达1300℃,一般作为发动机叶片材料,如第三代单晶高温合金cmsx-10、rene n6等;二是强化晶界,在多晶高温合金中加入c、zr、mg、b等元素,增加高温下晶界强度,这类材料一般是变形高温合金,是制作涡轮盘、燃烧室等部件的主要材料,如astroloy、haynes r-41、udimet 720等合金。
3.硼作为高温合金晶界强化元素应用比较广泛,几乎1/2的高温合金牌号都含有b,含硼高温合金的生产一般采用真空感应熔炼+真空自耗双联工艺,以防止硼的氧化。如使用电渣重熔工艺生产,b含量不易控制,收得率在20~70%之间,这显然是不可行的。
4.然而真空自耗生产含硼高温合金也存在问题,一是成本较高,相比电渣重熔增加约30%成本支出;二是表面质量差,进一步加工前需对钢锭扒皮处理。所以,一直以来,冶金工作者力图解决电渣炉稳定生产含硼高温合金的工艺难题。
5.专利cn201910467868.5公开了一种电渣重熔过程硼合金化的方法,该方法是在冶炼含硼钢时,间歇往渣中加入al和b-fe,进行al脱氧和b合金化;该方法很新颖,但因为b元素是间歇分批加入存在增铝和硼吸收率不均匀的可能。
6.专利cn201610357245.9公开了一种稳定提高含硼电渣钢硼收得率的冶炼方法,该方法为保证b元素的收得率,往渣中加入al和si-fe粉进行脱氧;该方法的弊端是al、si-fe加入量不好控制,过量加入会增铝增硅、欠量则烧b。
技术实现要素:7.本发明要解决的技术问题是提供一种电渣重熔含硼高温合金精确控制硼的方法,以提升并稳定b的收得率。
8.为解决上述技术问题,本发明所采取的方法工艺为:(1)所述电渣重熔用渣系成分及其质量分数为:caf
2 40%~50%、mgf
2 2%~5%、cao 25%~30%、al2o
3 20%~25%、tio
2 2%~5%,b2o
3 0.1%~0.5%、b-fe合金0.01%~0.04%和bn 0.1%~0.3%;所述b-fe合金中b质量分数为20%~30%;(2)固渣启动,整个冶炼过程均采用n
2-ar混合气体作为保护气体,化渣及重熔期氮的体积分数是合金中硼含量的150~300倍;(3)补缩期减少保护气体中氮的体积分数至重熔期的1/4~1/3,熔炼结束后,继续维持保护气体通入0.5~1h。
浓度,降低等式左边o2的分压。
18.以上是根据质量守恒定律得出的抑制条件,而从能量角度讲想要抑制反应的进行,需降低它们的生成吉布斯自由能,分析如下:所述反应式(a)是吸热反应,低温有利于降低吉布斯自由能的生成,所以电渣时尽量控制渣温不要太高,控制功率输入时倾向于适当降低电压。所述反应式(b)是放热反应,高温有利于降低吉布斯自由能的生成,要求渣温越高越好,需高电压操作,这就产生了矛盾。进一步分析,不难得出,反应式(a)是反应式(b)的前提条件,若无反应式(a),反应式(b)则不能进行,所以当这两个反应的条件相矛盾时,控制前一级反应是最为关键。
19.根据以上分析,本方法拟采用全新的技术方案解决上述两个问题,一是根据高温合金中硼相对含量设计适合冶炼特定成分的渣系,在“渣池-熔滴-熔池”的液相条件下有效抑制反应式(a)和反应式(b)的进行,提高b收得率;二是在冶炼过程中创造极低氧、适量氮的保护气氛,从“气相”条件有效抑制氮化硼分解和氮的烧损。
20.本电渣重熔含硼高温合金精确控制硼的方法的渣系改进以熔炼合金的化学成分为基础,所述含硼高温合金的目标成分(质量分数)为:c 0.10%~0.20%,si≤0.25%,mn≤0.25%,p≤0.010%,s≤0.010%,cr 13%~16%,mo 4.5%~5.5%,co 18.0%~22.0%,al 4.5%~5.0%,ti 1.2%~1.5%,b 0.005%~0.030%,ni 余量。本方法所述渣系及熔炼工艺如下所述:(1)电渣用渣系主要成分为(wt):caf
2 40%~50%、mgf
2 2%~5%、cao 25%~30%、al2o
3 20%~25%、tio
2 2%~5%;根据高温合金中的b含量多少,在渣中掺入质量分数为0.1~0.5%的b2o3、0.01~0.04%的b-fe合金和0.1~0.3%的bn;其中b-fe合金中b质量分数为20%~30%;所述渣系先经1400~1500℃预熔30~40min,冷却后破碎,使用前在400~600℃炉内烘烤6~8h;(2)冶炼用自耗电极经过打磨去除表面夹渣及氧化层,整个冶炼过程均采用n
2-ar混合气体作为保护气体,电渣过程气氛氧含量控制在0.01%以内;(3)结晶器中通入n
2-ar混合气体置换空气,待氧含量下降为0.01vol%及以下时起弧化渣;化渣期及重熔期n
2-ar混合气体中氮的体积分数是合金中目标硼含量的150~300倍;(4)进入重熔期,调整电压为d
结
+(10~15)v、电流为150d
结
+(500~1500)a,所述d
结
为结晶器直径,单位:cm;(5)补缩期逐步调整电流、电压至重熔期的1/3~1/2,n
2-ar混合气体中氮的体积分数逐步调整至重熔期的1/4~1/3。熔炼结束后,继续维持保护气体通入0.5~1h。
21.实施例1:本电渣重熔含硼高温合金精确控制硼的方法具体如下所述。
22.自耗电极规格为φ120
×
1800mm;成分见表1,余量为ni。结晶器规格φ160
×
1100mm。渣成分(wt):caf
2 40%、mgf
2 2%、cao 30%、al2o
3 23%、tio
2 4.79%、b2o
3 0.1%、b-fe 0.01%、bn 0.1%,其中b-fe中b含量为30wt%;渣量6kg。
23.(1)自耗电极打磨光亮、焊接备用;所述渣料先经1400℃预熔35min,冷却后破碎,使用前放置在400℃加热炉烘烤8h;(2)铺设固渣引弧剂、安装电极,向结晶器内通入n
2-ar混合气体,至气氛中o2含量0.008%;其中,n
2-ar混合气体中n2含量为1.5vol%;(3)给电启动,加渣、化渣12分钟,化渣期末调整电压为26v、电流为2900a;进入重
熔期,控制电压在26~31v、电流2900~3200a波动,至重熔期结束;(4)剩余15kg自耗电极时开始补缩,补缩期逐步调整电压9~16.5v、电流970~1600a波动,调整n
2-ar混合气体中n2体积占比至0.4%,补缩期持续20min,至熔炼结束;(5)持续通气30min后脱模,铸锭置于450℃加热炉内缓冷;即可得到本实施例的高温合金电渣铸锭,检测本电渣铸锭成分,结果见表1;(6)对比例:使用60f/20/0/20渣系冶炼同样成分电极,纯氩气保护做对比试验,渣系成分(wt):caf
2 60%、cao 20%、al2o
3 20%;得到常规工艺的对比电渣铸锭。检测对比电渣铸锭,结果见表1。
24.表1:实施例1和对比例所得电渣铸锭成分(wt%)由表1得出,本电渣铸锭中b收得率98%,o、n基本没变,其他元素收得率也在98%以上;对比电渣铸锭中b收得率仅为44%,其他成分收得率也较低,al为93.3%、ti仅为90%。
25.实施例2:本电渣重熔含硼高温合金精确控制硼的方法具体如下所述。
26.电渣重熔自耗电极为φ220
×
1800mm规格含硼高温合金;成分见表2,余量为ni。结晶器规格φ300
×
1300mm。渣成分(wt):caf
2 40%、mgf
2 5%、cao 25%、al2o
3 24.48%、tio
2 5%、b2o
3 0.3%、b-fe 0.02%、bn 0.2%,其中b-fe中b含量为25wt%;渣量28kg。
27.(1)自耗电极打磨光亮、焊接假电极备用;所述渣料先经1500℃预熔35min,冷却后破碎,使用前放置在500℃加热炉烘烤8h;(2)铺设固渣引弧剂、安装电极,向结晶器内通入n
2-ar混合气体,至气氛中o2含量0.006%;其中,n
2-ar混合气体中n2含量为2vol%;(3)给电启动,加渣、化渣26分钟,化渣期末调整电压为40v、电流为5000a;进入重熔期,控制电压在40~45v、电流5000~6000a波动,至重熔期结束;(4)自耗电极剩余50kg时开始补缩,补缩期逐步调整电压至14~22.5v、电流1700~3000a波动,调整n
2-ar混合气体中n2体积占比至0.65%,补缩期持续45min,至熔炼结束;(5)持续通气50min后脱模,铸锭置于400℃加热炉内缓冷;即可得到本实施例的高温合金电渣铸锭,检测本电渣铸锭成分,结果见表2;(6)对比例:使用70f/0/0/30渣系冶炼同样成分电极,纯氩气保护做对比试验,渣系成分(wt):caf
2 70%、al2o
3 30%;得到常规工艺的对比电渣铸锭。检测对比电渣铸锭,结果见表2。
28.表2:实施例2和对比例所得电渣铸锭成分(wt%)
由表2得出,本电渣铸锭中b收得率100%,o、n没有增加,其他元素收得率也在98%以上;对比电渣铸锭中b收得率仅为30%,其他成分收得率也较低,al为93%、ti仅为84.7%。
29.实施例3:本电渣重熔含硼高温合金精确控制硼的方法具体如下所述。
30.电渣重熔自耗电极规格为φ300
×
1800mm;成分见表3,余量为ni。结晶器规格φ400
×
1400mm。渣成分(wt):caf
2 50%、mgf
2 2%、cao 25%、al2o
3 20%、tio
2 2.32%、b2o
3 0.4%、b-fe 0.03%、bn 0.25%,其中b-fe中b含量为20wt%;渣量46kg。
31.(1)自耗电极打磨光亮、焊接备用;所述渣料先经1450℃预熔30min,冷却后破碎,使用前放置在600℃加热炉烘烤6h;(2)铺设固渣引弧剂、安装电极,向结晶器内通入n
2-ar混合气体,至气氛中o2含量0.01%;其中,n
2-ar混合气体中n2含量为3vol%;(3)给电启动,加渣,化渣42分钟,化渣期末调整电压为52v、电流为6500a;进入重熔期,控制电压在52~55v、电流6500~7500a波动,至重熔期结束;(4)自耗电极剩余100kg时开始补缩,补缩期逐步调整电压至17.5~27.5v、电流2200~3700a波动,调整n
2-ar混合气体中n2体积占比至1%,补缩期持续95min,至熔炼结束;(5)持续通气60min后脱模,铸锭置于500℃加热炉内缓冷;即可得到本实施例的高温合金电渣铸锭,检测本电渣铸锭成分,结果见表3;(6)对比例:使用40f/30/0/30渣系冶炼同样成分电极,纯氩气保护做对比试验,渣系成分(wt):caf
2 40%、cao 30%、al2o
3 30%;得到常规工艺的对比电渣铸锭。检测对比电渣铸锭,结果见表3。
32.表3:实施例3和对比例所得电渣铸锭成分(wt%)由表3得出,本电渣铸锭中b收得率95%,o、n基本没变,其他元素收得率也在98%以上;对比电渣铸锭中b收得率仅为35%,其他成分收得率也较低,al为88.5%、ti仅为86.7%。
33.实施例4:本电渣重熔含硼高温合金精确控制硼的方法具体如下所述。
34.电渣重熔自耗电极规格为φ400
×
2200mm;成分见表4,余量为ni。结晶器规格φ550
×
1600mm。渣成分(wt):caf
2 45%、mgf
2 3%、cao 24.16%、al2o
3 25%、tio
2 2%、b2o
3 0.5%、b-fe 0.04%、bn 0.3%,其中b-fe中b含量为30wt%;渣量98kg。
35.(1)自耗电极打磨光亮、焊接备用;所述渣料先经1420℃预熔40min,冷却后破碎,使用前渣料放置在600℃加热炉烘烤7h;(2)铺设固渣引弧剂、安装电极,向结晶器内通入n
2-ar混合气体,至气氛中o2含量0.009%;其中,n
2-ar混合气体中n2含量为5vol%;(3)给电启动,加渣,化渣70分钟,化渣期末调整电压为65v、电流为8250a;进入重熔期,控制电压在65~70v、电流8750~9250a波动,至重熔期结束;(4)自耗电极剩余160kg时开始补缩,补缩期逐步调整电压至22~35v、电流2950~4600a波动,调整n
2-ar混合气体中n2体积占比至1.25%,补缩期持续120min,至熔炼结束;(5)持续通气60min后脱模,铸锭置于600℃加热炉内缓冷;即可得到本实施例的高温合金电渣铸锭,检测本电渣铸锭成分,结果见表4;(6)使用50f/20/0/25/5ti渣系冶炼同样成分电极,纯氩气保护做对比试验,渣系成分(wt):caf
2 50%、cao 20%、al2o
3 25%、tio
2 5%;得到常规工艺的对比电渣铸锭。检测对比电渣铸锭,结果见表4。
36.表4:实施例4和对比例所得电渣铸锭成分(wt%)由表4得出,本电渣铸锭中b收得率96.7%,o、n略有降低,其他元素收得率也在98%以上;对比电渣铸锭可以稳定al、ti收得率在98%以上,但b收得率仅为53.3%。