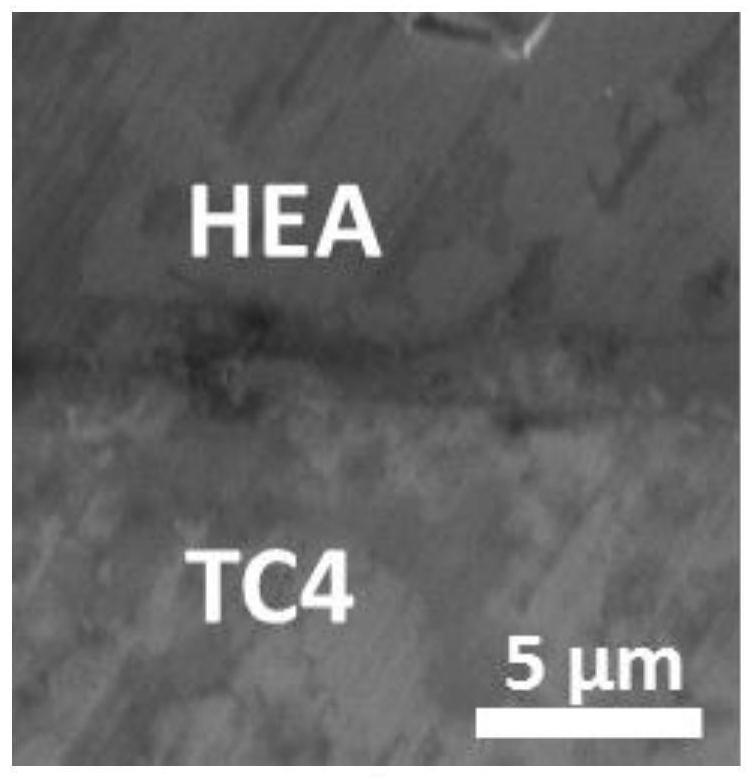
1.本发明涉及高熵合金技术领域,尤其涉及一种高熵合金自润滑材料与钛合金复合构件及其制备方法和应用。
背景技术:2.钛及钛合金因具有优异的综合力学性能,在航空航天领域得到了高度重视和广泛应用。然而其耐磨性能不强,且随着温度的提高,其抗氧化性能明显下降,特别是航空关节轴承等耐磨部件,磨损成为其主要失效形式。高熵合金(hea)展现出优于传统金属材料的性能,如高强度、高耐磨性以及良好的抗辐照性能等,成为近年来合金领域的研究前沿与热点。由钛合金/hea异种金属组成的复合构构件,可将钛合金和hea优良的性能结合起来,使零件在机械性能优异的基础上,耐磨性提高。
3.目前,hea与异种材料的焊接性研究不多,主要涉及成熟hea,如cocrfemnni和cocrfenicu与不锈钢的异种焊接。葡萄牙新里斯本大学的研究人员(j.p.oliveira,jiajia shen,z.zeng,jeong min park,yeon taek choi,n.schell,e.maawad,n.zhou,hyoung seop kim,dissimilar laser welding of a cocrfemnni high entropy alloy to 316stainless steel,script materialia,volume 206,2022,114219)采用激光焊接工艺获得了cocrfemnni与316不锈钢的无缺陷接头。国内李娟等人(李娟,赵宏龙,周念,张英哲,秦庆东,苏向东,cocrfenicu高熵合金与304不锈钢真空扩散焊,金属学报,2021,57,1567-1578)研究了cocrfenicu与304不锈钢的真空扩散焊,结果表明:焊接接头的强度高于母材,可实现高质量的连接。钛合金相关的异种焊接主要集中于对其与不锈钢、铜等的连接中,但是在异种熔焊过程中,两种基材的混合可能促进有害相的形成,特别是与钛合金在熔焊过程中极易生成大量脆性的金属间化合物,使接头处性能恶化。因此,有效阻止金属间化合物的大量生成是异种焊接的难点,且hea与钛合金的焊接目前也尚未相关报道。
技术实现要素:4.本发明的目的在于提供一种高熵合金自润滑材料与钛合金复合构件及其制备方法和应用,所述制备方法可以使高熵合金自润滑材料和钛合金之间实现异种连接,实现焊接界面达到冶金结合,得到组织致密、无缺陷的焊接接头。
5.为了实现上述发明目的,本发明提供以下技术方案:
6.本发明提供了一种高熵合金自润滑材料与钛合金复合构件的制备方法,包括以下步骤:
7.将中熵合金、铝和银混合后,进行放电等离子烧结,得到高熵合金自润滑材料;
8.将所述高熵合金自润滑材料和钛合金进行包套后,进行固相扩散焊接处理,得到所述高熵合金自润滑材料与钛合金复合构件;
9.所述固相扩散焊接处理的过程为:在室温下升压至10mpa,以10~30℃/min的升温
速率升温至600~750℃,保温5~15min,继续升压至30~40mpa,以8~10℃/min的升温速率二次升温至700~900℃后,保温保压15~30min,升压至80~110mpa后,以8~10℃/min的升温速率三次升温至1000~1200℃,保温保压3~7h,空冷。
10.优选的,所述中熵合金、铝和银的质量比为(75~85):(5~15):(5~15)。
11.优选的,所述中熵合金为cocrnife高熵合金;
12.所述钛合金为tc4钛合金。
13.优选的,所述中熵合金的粒径为10~50μm。
14.优选的,所述铝的粒径为10~50μm;
15.所述银的粒径为15~35μm。
16.优选的,所述放电等离子烧结的过程为:在20~40mpa的压力下,以8~10℃/min的升温速率由室温升至700~1000℃,模压10~20min。
17.优选的,所述放电等离子烧结的过程为:在25~35mpa的压力下,以8~10℃/min的升温速率由室温升至900~1000℃,模压15~20min。
18.优选的,所述固相扩散焊接处理的过程为:在室温下升压至10mpa,以15~25℃/min的升温速率升至600~700℃,保温8~12min,继续升压至35~40mpa,以8~10℃/min的升温速率二次升温至700~800℃后,保温保压20~30min,升压至100~110mpa后,以8~10℃/min的升温速率三次升温至1050~1100℃,保温保压5~6h,空冷。
19.本发明还提供了上述技术方案所述的制备方法制备得到的高熵合金自润滑材料与钛合金复合构件。
20.本发明还提供了上述技术方案所述高熵合金自润滑材料与钛合金复合构件在制备高强韧和耐磨零件中的应用。
21.本发明提供了一种高熵合金自润滑材料与钛合金复合构件的制备方法,包括以下步骤:将中熵合金、铝和银混合后,进行放电等离子烧结,得到高熵合金自润滑材料;将所述高熵合金自润滑材料和钛合金进行包套后,在真空条件下进行固相扩散焊接处理,得到所述高熵合金自润滑材料与钛合金复合构件;所述固相扩散焊接处理的过程为:在室温下升压至10mpa,以10~30℃/min的升温速率升至600~750℃,保温5~15min,继续升压至30~40mpa,以8~10℃/min的升温速率二次升温至700~900℃后,保温保压15~30min,升压至80~110mpa后,以8~10℃/min的升温速率三次升温至1000~1200℃,保温保压3~7h,空冷。本发明进行固相扩散焊接处理将钛合金和高熵合金自润滑材料之间由最初的物理接触,然后通过在高温和外加压力的作用下,通过屈服和蠕变机理使表面发生塑性变形,而且表面的接触面积逐渐增大,接触面的原子间相互扩散,形成紧密结合,由于变形引起晶格畸变、位错,空位等缺陷,使界面原子处于高度激活状态,组织成分逐渐均匀化,原始界面消失,实现异种连接,得到了焊接界面达到冶金结合,组织致密,无缺陷的接头,充分发挥各自的优势,能够减低摩擦系数,提高钛合金的耐磨性能。
附图说明
22.图1为实施例1所述hea/tc4自润滑复合材料的sem图;
23.图2为对比例2所述hea/tc4自润滑复合材料的sem图。
具体实施方式
24.本发明提供了一种高熵合金自润滑材料与钛合金复合构件的制备方法,包括以下步骤:
25.将中熵合金、铝和银混合后,进行放电等离子烧结,得到高熵合金自润滑材料;
26.将所述高熵合金自润滑材料和钛合金进行包套后,进行固相扩散焊接处理,得到所述高熵合金自润滑材料与钛合金复合构件;
27.所述固相扩散焊接处理的过程为:在室温下升压至10mpa,以10~30℃/min的升温速率升至600~750℃,保温5~15min,继续升压至30~40mpa,以8~10℃/min的升温速率二次升温至700~900℃后,保温保压15~30min,升压至80~110mpa后,以8~10℃/min的升温速率三次升温至1000~1200℃,保温保压3~7h,空冷。
28.在本发明中,若无特殊说明,所有制备原料均为本领域技术人员熟知的市售产品。
29.本发明将中熵合金、铝和银混合后,进行放电等离子烧结,得到高熵合金自润滑材料。
30.在本发明中,所述中熵合金优选为cocrnife基高熵合金,所述cocrnife基高熵合金优选为等原子比cocrnife合金;所述高熵合金的粒径优选为10~50μm。
31.在本发明中,所述铝的粒径优选为10~50μm。
32.在本发明中,所述银的粒径优选为15~35μm。
33.在本发明中,所述高熵合金、铝和银的质量比优选为(75~85):(5~15):(5~15),更优选为(78~82):(8~12):(8~12)。
34.在本发明中,所述银的作用为固体润滑剂,所述铝的作用为实现与cocrnife制备不同al含量的al
x
cocrnife五元高熵合金。
35.在本发明中,所述混合的方式优选为球磨,本发明对所述球磨的过程没有任何特殊的限定,采用本领域技术人员熟知的过程进行并保证所述高熵合金、铝和银混合均匀即可。
36.在本发明中,所述放电等离子烧结的过程优选为:在20~40mpa的压力下,以8~10℃/min的升温速率由室温升至700~1000℃,模压10~20min;更优选为在25~35mpa的压力下,以8~10℃/min的升温速率由室温升至900~1000℃,模压15~20min。
37.在本发明中,所述放电等离子烧结优选为将所述混合得到的混合物置于石墨模具中进行放电等离子烧结。
38.在本发明中,所述放电等离子烧结的作用是实现al
x
cocrnife基高熵合金自润滑复合材料的制备。
39.所述放电等离子烧结完成后,本发明还包括依次进行的降温和脱模;本发明对所述降温的过程没有任何特殊的限定,采用本领域技术人员熟知的过程降至室温即可;本发明对所述脱模的过程没有任何特殊的限定,采用本领域技术人员熟知的过程进行即可。
40.得到高熵合金自润滑材料后,本发明将所述高熵合金自润滑材料和钛合金进行包套后,进行固相扩散焊接处理,得到所述高熵合金自润滑材料与钛合金复合构件。
41.在本发明中,所述钛合金优选为tc4钛合金,所述tc4钛合金的化学组成优选为ti6al4v。
42.进行包套前,本发明优选分别将所述高熵合金自润滑材料和钛合金进行预处理,
所述预处理优选包括依次进行的打磨和抛光;本发明对所述打磨和抛光的过程没有任何特殊的限定,采用本领域技术人员熟知的过程进行即可。
43.在本发明中,所述包套的过程优选为将所述高熵合金自润滑材料和钛合金置于碳素钢的包套中,抽真空,进行真空封装,得到用于热等静压处理的包套。本发明对所述抽真空的过程没有任何特殊的限定,采用本领域技术人员熟知的过程进行即可。
44.得到用于热等静压处理的包套后,本发明还优选包括将得到的包套进行喷砂处理。本发明对所述喷砂处理的过程没有任何特殊的限定,采用本领域技术人员熟知的过程进行即可。在本发明中,所述喷砂处理的目的是为了将包套表面的油污去除,以便污染设备炉的炉腔。
45.在本发明中,所述固相扩散焊接处理的过程为:在室温下升压至10mpa,以10~30℃/min的升温速率升至600~750℃,保温5~15min,继续升压至30~40mpa,以8~10℃/min的升温速率二次升温至700~900℃后,保温保压15~30min,升压至80~110mpa后,以8~10℃/min的升温速率三次升温至1000~1200℃,保温保压3~7h,空冷;优选为在室温下升压至10mpa,以15~25℃/min的升温速率升至600~700℃,保温8~12min,继续升压至35~40mpa,以8~10℃/min的升温速率二次升温至700~800℃后,保温保压20~30min,升压至100~110mpa后,以8~10℃/min的升温速率三次升温至1050~1100℃,保温保压5~6h,空冷。
46.在本发明中,所述固相扩散焊接处理优选在热等静压设备中进行。
47.在本发明中,将所述固相扩散焊接处理的条件参数控制在上述范围内的作用是使高熵合金自润滑复合材料与钛合金异种界面无缝隙地接触在一起,而且金属连接处几乎不会发生明显的塑性变形和氧化,施加压力后接触面积增加,而大大促进高温下原子的扩散流动,实现具有优异特性和强度的焊缝。
48.本发明还提供了上述技术方案所述的制备方法制备得到的高熵合金自润滑材料与钛合金复合构件。
49.本发明还提供了上述技术方案所述高熵合金自润滑材料与钛合金复合构件在制备高强韧和耐磨零件中的应用。所述高强韧和耐磨零件优选用于航空航天领域或医用民生领域。本发明对所述应用的方法没有任何特殊的限定,采用本领域技术人员熟知的方法进行即可。
50.下面结合实施例对本发明提供的高熵合金自润滑材料与钛合金复合构件及其制备方法和应用进行详细的说明,但是不能把它们理解为对本发明保护范围的限定。
51.实施例1
52.将80重量份的高熵合金粉末(高熵合金的组成为cocrnife,粒径为20μm)、8重量份铝粉(粒径为30μm)和12重量份的银粉(粒径为15μm)进行球磨混合至混合均匀后,至于石墨模具中进行放电等离子烧结(所述放电等离子烧结的过程为:在30mpa的压力下,由室温以10℃/min的速率升至950℃,模压20min)后,降至室温,脱模,得到高熵合金自润滑复合材料;
53.分别将tc4钛合金和所述高熵合金自润滑复合材料进行打磨和抛光,得到预处理后的tc4钛合金和预处理后的高熵合金自润滑复合材料;
54.将tc4钛合金和高熵合金自润滑复合材料置于碳素钢的包套中,抽真空,进行真空
封装,得到用于热等静压处理的包套;
55.将所述包套进行喷砂处理后,置于热等静压设备中进行固相扩散焊接处理(过程为:在室温下升压至10mpa,以20℃/min的升温速率升至600℃,保温10min,继续升压至40mpa,以10℃/min的升温速率二次升温至800℃,在当前压力和温度下,保持20min,升压至100mpa,保压之后以10℃/min的升温速率三次升温至1050℃,保温保压6h,空冷)后,利用机加工将包套内的复合块体取出,将横截面打磨,观察界面,观察结果如图1所示,由图1可知,所述tc4钛合金和高熵合金自润滑复合材料之间的焊接界面结合良好,可以看到有明显的过渡层生成,所述过渡层2.5μm厚;
56.将所述tc4钛合金和高熵合金自润滑复合材料之间的焊接界面进行纤维硬度测试,其中高熵合金自润滑复合材料一侧的侧硬度为412hv,过渡层的硬度为378hv,tc4钛合金一侧的侧硬度为310hv;
57.在室温下进行摩擦磨损试验,分析材料的摩擦磨损行为,所述高熵合金自润滑复合材料侧的侧摩擦系数为0.35,磨损率为3.3
×
10-5
mm/(n
·
m)。
58.实施例2
59.将85重量份的高熵合金粉末(高熵合金的组成为cocrnife,粒径为20μm)、5重量份铝粉(粒径为30μm)和10重量份的银粉(粒径为15μm)进行球磨混合至混合均匀后,至于石墨模具中进行放电等离子烧结(所述放电等离子烧结的过程为:在30mpa的压力下,由室温以10℃/min的升温速率升至950℃,模压20min)后,降至室温,脱模,得到高熵合金自润滑复合材料;
60.分别将tc4钛合金和所述高熵合金自润滑复合材料进行打磨和抛光,得到预处理后的tc4钛合金和预处理后的高熵合金自润滑复合材料;
61.将tc4钛合金和高熵合金自润滑复合材料置于碳素钢的包套中,抽真空,进行真空封装,得到用于热等静压处理的包套;
62.将所述包套进行喷砂处理后,置于热等静压设备中进行固相扩散焊接处理(过程为:在室温下升压至10mpa,以20℃/min的升温速率升至600℃,保温10min,继续升压至40mpa,以10℃/min的升温速率二次升温至700℃,在当前压力和温度下,保持30min,升压至110mpa,保压之后以10℃/min的升温速率三次升温至1050℃,保温保压6h,空冷)后,利用机加工将包套内的复合块体取出,将横截面打磨,观察界面,观察结果为,所述tc4钛合金和高熵合金自润滑复合材料之间的焊接界面结合良好,可以看到有明显的过渡层生成,所述过渡层3μm厚;
63.将所述tc4钛合金和高熵合金自润滑复合材料之间的焊接界面进行纤维硬度测试,其中高熵合金自润滑复合材料一侧的侧硬度为396hv,过渡层的硬度为368hv,tc4钛合金一侧的侧硬度为306hv;
64.在室温下进行摩擦磨损试验,分析材料的摩擦磨损行为,所述高熵合金自润滑复合材料侧的侧摩擦系数为0.4,磨损率为3.9
×
10-5
mm/(n
·
m)。
65.实施例3
66.将80重量份的高熵合金粉末(高熵合金的组成为cocrnife,粒径为30μm)、8重量份铝粉(粒径为30μm)和12重量份的银粉(粒径为20μm)进行球磨混合至混合均匀后,至于石墨模具中进行放电等离子烧结(所述放电等离子烧结的过程为:在30mpa的压力下,由室温以
10℃/min的升温速率升至950℃,模压20min)后,降至室温,脱模,得到高熵合金自润滑复合材料;
67.分别将tc4钛合金和所述高熵合金自润滑复合材料进行打磨和抛光,得到预处理后的tc4钛合金和预处理后的高熵合金自润滑复合材料;
68.将tc4钛合金和高熵合金自润滑复合材料置于碳素钢的包套中,抽真空,进行真空封装,得到用于热等静压处理的包套;
69.将所述包套进行喷砂处理后,置于热等静压设备中进行固相扩散焊接处理(过程为:在室温下升压至10mpa,以20℃/min的升温速率升至600℃,保温10min,继续升压至40mpa,以10℃/min的升温速率二次升温至800℃,在当前压力和温度下,保持30min,升压至110mpa,保压之后以10℃/min的升温速率三次升温至1100℃,保温保压6h,空冷)后,利用机加工将包套内的复合块体取出,将横截面打磨,观察界面,观察结果为,所述tc4钛合金和高熵合金自润滑复合材料(hea/tc4自润滑复合材料)之间的焊接界面结合良好,可以看到有明显的过渡层生成,所述过渡层2.8μm厚;
70.将所述tc4钛合金和高熵合金自润滑复合材料之间的焊接界面进行纤维硬度测试,其中高熵合金自润滑复合材料一侧的侧硬度为420hv,过渡层的硬度为398hv,tc4钛合金一侧的侧硬度为311hv;
71.在室温下进行摩擦磨损试验,分析材料的摩擦磨损行为,所述高熵合金自润滑复合材料侧的侧摩擦系数为0.35,磨损率为3.0
×
10-5
mm/(n
·
m)。
72.对比例1
73.以tc4钛合金作为对比例;
74.对所述tc4钛合金进行室温摩擦磨损试验,分析材料的摩擦磨损行为,其摩擦系数为0.7,磨损率为9.1
×
10-3
mm/(n
·
m)。
75.对比例2
76.将80重量份的高熵合金粉末(高熵合金的组成为cocrnife,粒径为30μm)、8重量份铝粉(粒径为20μm)和12重量份的银粉(粒径为20μm)进行球磨混合至混合均匀后,至于石墨模具中进行放电等离子烧结(所述放电等离子烧结的过程为:在30mpa的压力下,由室温升以10℃/min的升温速率至950℃,模压20min)后,降至室温,脱模,得到高熵合金自润滑复合材料;
77.分别将tc4钛合金和所述高熵合金自润滑复合材料进行打磨和抛光,得到预处理后的tc4钛合金和预处理后的高熵合金自润滑复合材料;
78.将tc4钛合金和高熵合金自润滑复合材料置于碳素钢的包套中,抽真空,进行真空封装,得到用于热等静压处理的包套;
79.将所述包套进行喷砂处理后,置于热等静压设备中进行固相扩散焊接处理(过程为:在室温下升压至10mpa,以20℃/min的升温速率升至600℃,保温10min,继续升压至40mpa,以10℃/min的升温速率二次升温至800℃,在当前压力和温度下,保持30min,升压至110mpa,保温保压6h,空冷)后,利用机加工将包套内的复合块体取出,将横截面打磨,观察界面,观察结果如图2所示,由图2可知,所述tc4钛合金和高熵合金自润滑复合材料(hea/tc4自润滑复合材料)之间异种连接界面,两种合金界面处未形成明显的过渡层,结合性能弱。
80.以上所述仅是本发明的优选实施方式,应当指出,对于本技术领域的普通技术人员来说,在不脱离本发明原理的前提下,还可以做出若干改进和润饰,这些改进和润饰也应视为本发明的保护范围。