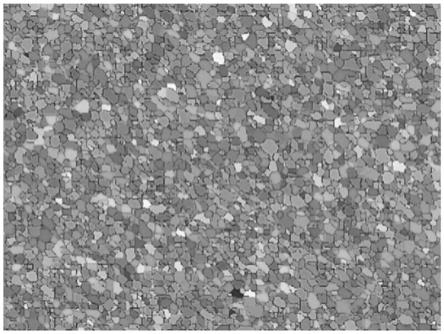
1.本发明涉及钛材热处理技术领域,具体的说是一种细化钛材晶粒的复合形变热处理工艺。
背景技术:2.电解铜箔是ccl、pcb和锂离子电池生产的重要基础原材料之一,阴极辊是电解制造铜箔的核心设备,且阴极辊钛材的质量直接影响铜箔的质量,阴极辊钛材晶粒组织特征则直接影响铜箔初始沉积层晶体结构,进而影响铜箔性能。但随着阴极辊尺寸的增大,对其晶粒度和组织均匀性的控制愈发困难。因此,调控整体旋压成形超大尺寸阴极辊的晶粒组织,是阴极辊制造亟待解决的关键问题。
3.目前阴极辊用钛材的加工工艺多为轧制变形-高温退火(温度560℃,时间1h)方式,所得晶粒评价尺寸一般在10μm以上,过于粗大的晶粒难以适应现阶段高质量电解铜箔的生产。
4.因此,探索合适热处理工艺,改进提升阴极辊用钛材的晶粒组织结构,有利于保证阴极辊的产品品质,提高阴极辊的生产效率,进而提高铜箔的质量。
技术实现要素:5.为了解决现有技术中的不足,本发明提供一种细化钛材晶粒的复合形变热处理工艺,采用本发明的工艺,通过对工业纯钛进行“旋压-退火-轧制-退火”复合变形热处理,可以细化晶粒,均匀化晶粒尺寸,因而能获得性能符合要求和质量稳定的阴极辊用钛材组织。
6.为了实现上述目的,本发明采用的具体方案为:一种细化钛材晶粒的复合形变热处理工艺,主要包括如下步骤:步骤一、对工业纯钛进行旋压变形,变形量为50%~60%;步骤二、对旋压变形后的钛材进行400℃~500℃到温退火,退火时间为0.5~1 h,退火后进行淬火处理;步骤三、对淬火后的钛材进行轧制冷变形,变形量为50%~70%;步骤四、对轧制变形后的钛材进行500℃到温退火,退火时间为1 h,然后淬火处理,即得到晶粒尺寸细小的钛材。
7.进一步地,步骤一中,工业纯钛所包含的组分及含量为:ti≥99.8%、fe≤0.05%、c≤0.03%、n≤0.03%、o≤0.06%、h≤0.002%。
8.进一步地,步骤二中,对旋压变形后的钛材进行400℃~500℃到温退火的具体方法为:在真空气氛管式电阻炉内通入氩气作为保护气体,将炉温升至400℃~500℃的目标温度,到达目标温度后,将旋压变形后的钛材置于热处理炉内进行退火。
9.进一步地,步骤三中,轧制冷变形的变形量为50%~60%。
10.进一步地,步骤四中,对轧制变形后的钛材进行500℃到温退火的具体方法为:在真空气氛管式电阻炉内通入氩气作为保护气体,将炉温升至500℃的目标温度,到达目标温
度后,将轧制变形后的钛材置于热处理炉内进行退火。
11.进一步地,步骤二或步骤四中,淬火方法为空冷淬火。
12.有益效果:本发明的本质在于有效利用大变形所得位错亚结构的中低温回复形核过程,进行晶粒的细化。相对于传统轧制变形,旋压变形在钛材中引入更大的剪切应力,钛材内部晶粒分裂更为严重,形成的位错亚结构更为细小,这种结构经400℃-500℃中低温回复退火后,可以很大程度的保留大变形阶段细化的亚结构;经轧制变形后,位错亚结构进一步得到细化,且位错亚结构更趋于沿轧制方向呈带状分布,而在此基础上再次进行400℃-500℃中低温退火,使得样品基本完成再结晶,且保留两次变形阶段的细晶特征。另外,因为两次退火温度均为中低温,晶粒尺寸在保持细小的同时,尺寸的分布也更为均匀,基本无异常粗大晶粒的出现。
附图说明
13.图1为钛材旋压变形后的样品图。
14.图2为实施例1中旋压变形后钛材样品外表面的晶粒组织图。
15.图3为实施例1中轧制后钛材样品外表面的晶粒组织图。
16.图4为实施例1中二次退火后钛材样品外表面的晶粒组织图。
17.图5为实施例2中轧制后钛材样品外表面的晶粒组织图。
18.图6为实施例2中二次退火后钛材样品外表面的晶粒组织图。
具体实施方式
19.下面将结合具体实施例对本发明的技术方案进行清楚、完整地描述,显然,所描述的实施例仅仅是本发明一部分实施例,而不是全部的实施例。基于本发明中的实施例,本领域普通技术人员在没有做出创造性劳动的前提下所获得的所有其他实施例,都属于本发明的保护范围。
20.一种细化钛材晶粒的复合形变热处理工艺,主要包括如下步骤:步骤一、选取工业纯钛,工业纯钛所包含的组分及含量为:ti≥99.8%、fe≤0.05%、c≤0.03%、n≤0.03%、o≤0.06%、h≤0.002%,对工业纯钛进行旋压变形,变形量为50%~60%;步骤二、在真空气氛管式电阻炉内通入氩气作为保护气体,将炉温升至400℃~500℃的目标温度,到达目标温度后,将旋压变形后的钛材置于热处理炉内进行退火,退火时间为0.5~1 h,退火后进行空冷淬火处理;步骤三、对淬火后的钛材进行轧制冷变形,变形量为50%~70%,优选地,变形量为50%~ 60%;步骤四、在真空气氛管式电阻炉内通入氩气作为保护气体,将炉温升至500℃的目标温度,到达目标温度后,将轧制变形后的钛材置于热处理炉内进行退火,退火时间为1 h,然后水淬处理,即得到晶粒尺寸细小的钛材;其中,旋压变形的变形量指的是相比初始钛材的变形量,轧制变形的变形量指的是相比旋压变形的变形量。本发明中的旋压变形和轧制变形引入的剪切应力的方向不同,本质是在变形过程了改变了钛材的应变路径,使得钛材晶粒得以较大程度分裂的同时,不
至于产生单一方向较强的应变累积,以致形成明显的剪切带或裂纹。另外,轧制作为二次变形的工艺,可以一定程度调整细晶的排列方向,使其沿轧向分布,优化取向分布。
21.实施例1一种细化钛材晶粒的复合形变热处理工艺,主要包括如下步骤:步骤一、选取工业纯钛,工业纯钛所包含的组分及含量为:ti≥99.8%、fe≤0.05%、c≤0.03%、n≤0.03%、o≤0.06%、h≤0.002%,对工业纯钛进行旋压变形,变形量为50%;图1为旋压变形后的钛材样品图,图2为旋压变形后钛材样品外表面的微观组织图,通过背散射电子衍射(electron backscatter diffraction, ebsd)技术及数据重构,可以看到变形后的样品表面以变形晶粒组织为主,由重构的组织图片可见,钛材内部存在较多的大尺寸变形晶粒,且分布不均匀;步骤二、在真空气氛管式电阻炉内通入氩气作为保护气体,将炉温升至400℃的目标温度,到达目标温度后,将旋压变形后的钛材置于热处理炉内进行一次退火,一次退火时间为0.5h,退火后进行空冷淬火处理;步骤三、对淬火后的钛材进行轧制冷变形,变形量为50%;图3为轧制后的晶粒组织图,由图可知钛材组织仍以变形晶粒为主,但大尺寸晶粒数目明显减少,且分布相对均匀;步骤四、在真空气氛管式电阻炉内通入氩气作为保护气体,将炉温升至500℃的目标温度,到达目标温度后,将轧制变形后的钛材置于热处理炉内进行二次退火,二次退火时间为1h,然后空冷淬火处理,即得到晶粒尺寸细小的钛材。图4为二次退火后的钛材组织图,可以看出,经过最终的复合形变热处理后,钛材内部形成了较为等轴的晶粒组织,晶粒平均晶粒尺寸为3.39
ꢀµ
m,且尺寸分布较为均匀。
22.实施例2实施例2与实施例1的不同之处仅在于:步骤二中,将炉温升至500℃的目标温度,到达目标温度后,将旋压变形后的钛材置于热处理炉内进行一次退火,一次退火时间为1h。其余均与实施例1相同。
23.图5为实施例2中轧制后钛材的组织图,可以看到,钛材组织以变形晶粒为主,大尺寸晶粒数目有所减少,且分布相对均匀。图6为二次退火后钛材的组织图,可以看到经过最终的复合形变热处理后,钛材内部形成了较为等轴的晶粒组织,晶粒平均晶粒尺寸为3.86 μm,且尺寸分布较为均匀。
24.综上可知,本发明的复合形变热处理工艺,能有效细化钛材的晶粒,优化组织,因而能够获得性能符合要求和质量稳定的阴极辊用钛材产品。
25.以上所述,仅是本发明的较佳实施例而已,并非随本发明作任何形式上的限制。凡根据本发明的实质所做的等效变换或修饰,都应该涵盖在本发明的保护范围之内。