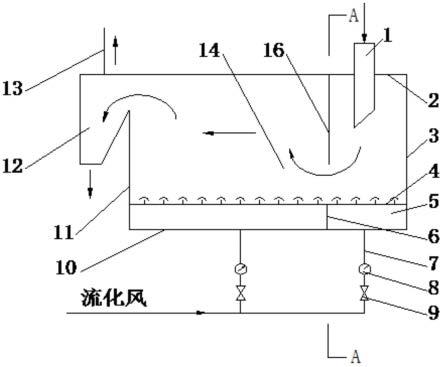
1.本实用新型属于矿物加工技术领域,尤其涉及一种粉体晶型转变反应器装置。
背景技术:2.新能源汽车和电子产品行业的发展对锂的需求越来越大,从锂辉石中提取锂成为了主要来源,目前锂辉石的提取中的一环是将锂辉石进行高温煅烧制备锂辉石熟料,而焙烧制备锂辉石熟料采用的是将回转窑、竖炉作为煅烧设备,但这些设备具有处理能力低、焙烧温度高、能耗高、晶型转变率低、后工序浸出率低、易烧结问题;其次,铁矿选矿时高品位易选铁矿石越来越少,低品位难选铁矿逐渐成为主要来源,传统的回转窑焙烧还原铁矿选矿技术的缺点是产能小、金属回收率低、热耗高。
技术实现要素:3.针对现有技术存在的不足,本实用新型提供一种粉体晶型转变反应器装置,针对锂辉石提锂可降低焙烧温度、降低能耗、提高晶型转变率、提高后工序浸出率、避免烧结、提高处理能力,针对低品位难选铁矿粉体焙烧还原选矿时,具有处理量大、焙烧还原温度低、金属回收率高、热耗低优点。
4.一种粉体晶型转变反应器装置,包括料室,所述料室由顶盖、前侧板、后侧板、侧板及底板组成,料室靠近后侧板的顶盖上装有进料管与料室相通,前侧板靠上部分装有出料管并与其连通,顶盖上靠近前侧板位置设置有向上排气的排气管;所述料室内位于进料管与排气管间设置有隔墙,将料室分成了进料端和出料端;隔墙上靠近顶盖位置开设有排气孔;隔墙下部与布气板之间留有间距;所述料室底部通过布气板间隔有气室,气室通过布气板与料室连通,气室内设置有竖直放置的阻断板,将气室分成单独的两部分,两个气室间之间隔绝;每部分均设置有进气管,进气管与气室连通;进气管进口处依次设置有流量计和阀门;流化风通过进气管通入气室内。
5.所述隔墙下部与布气板之间的间距为进料管内径的1~3倍。
6.所述布气板由花板和风帽组成,或是烧结网,烧结网的透气率为0.1-2。
7.所述料室中进料侧容积小于出料侧容积,其中靠近进料侧的料室水平截面积为靠近出料侧料室的水平截面积的一半或三分之一。
8.所述进料管的下口没入料室的物料层内10~100cm。
9.所述料室中的物料为锂辉石粉体或铁矿石粉体。
10.本实用新型的有益效果是:本实用新型可以解决回转窑、竖炉焙烧锂辉石产量小、焙烧温度高、能耗高、晶型转变率低、后工序浸出率低、易烧结的问题;可以解决采用回转窑还原铁矿石时处理量小、焙烧还原温度高、金属回收率低、热耗高问题。随着当今社会的环保意识的提高和严峻,本实用新型提供的是一种新型的、节能的、环保的粉体相变装置,终将取代传统的锂辉石的回转窑煅烧提锂方法、传统的铁矿石回转窑焙烧还原方法。
附图说明
11.图1为本实用新型提供的粉体相变装置的示意图;
12.图2为图1中的a-a剖面图;
13.其中,
14.1-进料管,2-顶盖,3-后侧板,4-布气板,5-气室,6-隔断板,7-进气管,8-流量计,9
‑ꢀ
阀门,10-底板,11-前侧板,12-出料口,13-排气管,14-料室,15-侧板,16-隔墙,17-排气孔。
具体实施方式
15.为了更好的解释本实用新型,以便于理解,下面结合附图,通过具体实施方式,对本实用新型的技术方案和效果作详细描述。
16.如图1-2所示,一种粉体晶型转变反应器装置,包括料室14,所述料室14由顶盖2、前侧板11、后侧板3、侧板15及底板10组成,料室14靠近后侧板3的顶盖2上装有进料管 1与料室14相通,前侧板11靠上部分装有出料管12并与其连通,顶盖2上靠近前侧板11 位置设置有向上排气的排气管13。所述料室14内位于进料管1与排气管13间设置有隔墙16,将料室14分成了进料端和出料端;隔墙16上靠近顶盖1位置开设有排气孔17。所述隔墙16 用来防止物料从进料管1进入料室14时从料室14上方直接经出料管12短路排出,从而不能有效的控制物料的停留时间。隔墙16将料室一分为二,排气孔17用来平衡两个料室内的压力。隔墙16下部与布气板4之间留有间距,本实施例中该间距为进料管1内径截面积的2倍。所述料室14底部通过布气板4间隔有气室5,气室5通过布气板4与料室14连通,气室5 内设置有竖直放置的阻断板6,将气室5分成单独的两部分,两个气室间之间隔绝;每部分均设置有进气管7,进气管7与气室5连通;进气管7进口处依次设置有流量计8和阀门9;流化风通过进气管7通入气室5内。
17.所述布气板4由花板和风帽组成,或是烧结网,本实施例中烧结网的透气率为0.1。
18.所述料室14中进料侧容积小于出料侧容积,其中靠近进料侧的料室14水平截面积为靠近出料侧料室14的水平截面积的一半或三分之一。
19.本实施例中所述进料管1的下口没入料室14的物料层内20cm。
20.所述料室14中的物料为锂辉石粉体或铁矿石粉体。
21.实施例1
22.上述的一种粉体晶型转变反应器装置的使用方法,本实施例中的物料以锂辉石粉体为例,锂辉石粉体原料粒径为10~500μm,品位为1%~5%。具体包括以下步骤:
23.步骤一:通过阀门9、流量计8调节并计量后,将流化风经进气管7送入气室5,流化风再经布气板4均布后送入料室14。通过控制阀门9的开度,经过流量计8计量来控制流化气体的用量,用量能使锂辉石粉体在料室14水平横截面上的流速达到0.01~0.5m/s即可。所述流化风为空气、氮气或其他易得成本低且不与锂辉石粉体发生反应的气体。
24.步骤二:将高温的锂辉石粉体物料通过进料管1排入料室14的进料端,锂辉石粉体的温度为800~1200℃,本实施例中锂辉石粉体的温度为1100℃;物料在流化风的推动下使物料呈流态化,具有了流体的流动性,随着物料量在料室14的进料端中不断的增多,物料的料位高度与料室14的出料端一侧有了高差,这时物料就通过隔墙16下端与布风板4上表面
之间的空间流入料室14的出料端。
25.步骤三:当物料在料室14出料端中积累的料位高过出料口12下堰时,物料就溢流出去,完成了锂辉石粉体在相变装置中的晶型转变,晶型由
ɑ
型转变为β型,锂辉石粉体的晶型转变率达到98%以上。此过程流化气体不与锂辉石粉体参与反应。
26.步骤四:料室14进料端内的流化风通过隔墙16的排气孔17进入料室14出料端上方空腔内,并汇集料室14出料端内的流化风一并由排气管13排出,进入其他系统。
27.处理锂辉石粉体时,通过改变流化气体的用量或增减锂辉石粉体进入量来改变锂辉石粉体的停留时间,锂辉石粉体在料室14中的停留时间为5~40min。
28.实施例2
29.上述的一种粉体晶型转变反应器装置的使用方法,本实施例中的物料以铁矿石粉体为例,铁矿石粉体原料粒径为10~500μm,品位为15%~50%。具体包括以下步骤:
30.步骤一:通过阀门9、流量计8调节并计量后,将流化风经进气管7送入气室5,流化风再经布气板4均布后送入料室14。通过控制阀门9的开度,经过流量计8计量来控制流化气体的用量,用量使铁矿石粉体在料室14水平横截面上的流速达到0.01~0.5m/s且能够使三氧化二铁完全还原成四氧化三铁。所述流化风为发生炉煤气、高炉煤气、焦炉煤气、转炉煤气或几种煤气的混合物。
31.步骤二:将高温的铁矿石粉体物料通过进料管1排入料室14的进料端,铁矿石粉体的温度为500~600℃,本实施例中铁矿石粉体的温度为530℃;物料在流化风的推动下使物料呈流态化,具有了流体的流动性,随着物料量在料室14的进料端中不断的增多,物料的料位高度与料室14的出料端一侧有了高差,这时物料就通过隔墙16下端与布风板4上表面之间的空间流入料室14的出料端。
32.步骤三:当物料在料室14出料端中积累的料位高过出料口12下堰时,物料就溢流出去,完成了铁矿石粉体的还原。流化气体与铁矿石粉体反生还原反应,铁矿石粉体由三氧化二铁还原成四氧化三铁,铁矿石粉体的金属回收率大于90%。
33.步骤四:料室14进料端内的流化风通过隔墙16的排气孔17进入料室14出料端上方空腔内,并汇集料室14出料端内的流化风一并由排气管13排出,进入其他系统。
34.处理铁矿石粉体时可通过改变流化气体的用量或增减铁矿石粉体进入量来调节铁矿石粉体还原的质量,铁矿石粉体在料室14中的停留时间为8~15min。