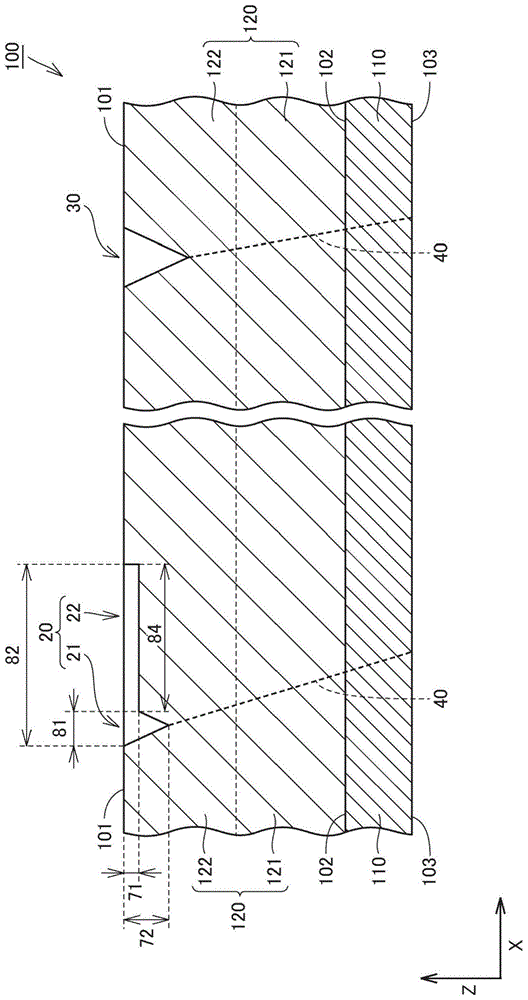
本公开涉及一种外延晶片以及制造该外延晶片的方法。
背景技术:
:日本专利公布No.2014-17439(专利文献1)公开了一种用于制造外延晶片的半导体制造装置。引用列表专利文献PTD1:日本专利公布No.2014-17439技术实现要素:根据本公开的外延晶片包括具有第一主表面的碳化硅膜。在碳化硅膜的第一主表面中形成凹槽部。凹槽部沿第一主表面在一个方向上延伸。而且,凹槽部在该一个方向上的宽度是凹槽部在垂直于该一个方向的方向上的宽度的两倍或更大。而且,凹槽部距第一主表面的最大深度不大于10nm。根据本公开的制造外延晶片的方法包括如下步骤:制备具有第二主表面的碳化硅衬底;以及在第二主表面上外延生长碳化硅膜。外延生长碳化硅膜的步骤包括如下步骤:采用具有C/Si比小于1的源材料气体在第二主表面上外延生长第一膜;使用包括(i)具有C/Si比小于1的源材料气体以及(ii)氢气的混合气体重新构建第一膜的表面;以及使用具有C/Si比小于1的源材料气体在第一膜的重新构建的表面上外延生长第二膜。附图说明图1是示出本公开的外延晶片的一部分的横截面视图。图2是示出本公开的外延晶片的一部分的平面视图。图3是示出本公开的外延晶片的一部分的平面视图。图4是示意性示出用于制造本公开的外延晶片的方法的流程图。图5是示出外延生长装置的构造的示意图。图6是示出沿图5中的线段VI-VI截取的截面的示意图。具体实施方式[本公开的实施例的描述]首先列出并描述本公开的实施例。[1]根据本公开的外延晶片100包括具有第一主表面101的碳化硅膜120。凹槽部20形成在第一主表面101中,凹槽部20沿第一主表面101在一个方向上延伸,在该一个方向上的凹槽部20的宽度是在垂直于该一个方向的方向上的凹槽部20的宽度的两倍或更大,凹槽部20距第一主表面101的最大深度不大于10nm。以下,将凹槽部20在该一个方向上的宽度称为“第二宽度82”,将凹槽部20在垂直于该一个方向的方向上的宽度称为“第三宽度83”,且将凹槽部20距第一主表面101的最大深度称为“第二深度72”。当在碳化硅衬底上外延生长碳化硅膜时,会在碳化硅膜的表面中形成微小的凹坑部。这些凹坑部的每一个都是由于从碳化硅衬底传递至碳化硅膜的穿透位错形成的,且它们是具有约几十纳米深度的凹陷。本发明人已经发现这些凹坑部致使形成在碳化硅膜表面的氧化膜的厚度的变化增加,且膜厚度的变化是降低碳化硅半导体装置长期可靠性的一个因素。本发明人已经发现可以在特定外延生长条件下抑制凹坑部的形成。根据该生长条件,凹坑部减少,但是会形成比凹坑部浅且在一个方向上延伸的多个凹槽部。但是,这些凹槽部比凹坑部浅且因此与凹坑部的影响相比具有对氧化膜的膜厚度较小的影响。在上述外延晶片100中,在碳化硅膜120的第一主表面101中将凹槽部20形成为在一个方向上延伸使得第二宽度82与第三宽度83的比不小于2,且具有不大于10nm的第二深度72。即,通过控制碳化硅膜120的外延生长的条件等,外延晶片100具备比各具有几十纳米深度的上述凹坑部更多数量的凹槽部20。因此,根据外延晶片100,与其中形成大量凹坑部的常规外延晶片相比,可减小氧化膜的膜厚度的变化。可通过使用预定缺陷检查装置观察第一主表面101而指定“凹槽部”的形状。因此,可测量凹槽部20的第二宽度82以及第三宽度83。对于缺陷检查装置来说,例如可采用Lasertec公司提供的WASAVI系列“SICA6X”(物镜:x10)。而且,可使用AFM(原子力显微镜)测量“凹槽部”的深度。[2]在上述外延晶片100中,凹槽部20可包括第一凹槽部21以及连接至第一凹槽部21的第二凹槽部22。第一凹槽部21在该一个方向上形成在凹槽部20的一端部中。第二凹槽部22可在该一个方向上从第一凹槽部21延伸至与该一个端部相反的另一个端部,且作为第二凹槽部22的距第一主表面101的深度的第一深度71可小于作为第一凹槽部21的最大深度的第二深度72。在其中形成具有上述结构的凹槽部20的外延晶片100中,抑制了否则将致使氧化膜的膜厚度变化增大的凹坑部的形成。因此,根据外延晶片100,可减少氧化膜的膜厚度变化。[3]外延晶片100可进一步包括具有相对于(0001)面具有不大于±4°的偏离角的第二主表面102的碳化硅衬底110。碳化硅膜120可以是形成在第二主表面102上的碳化硅单晶膜,且凹槽部20可形成为在台阶流动生长方向上从碳化硅膜120中的穿透位错40延伸,所述台阶流动生长方向为沿着偏离角的偏离方向如上所述,凹槽部20可形成为在台阶流动生长方向上延伸。在其中形成了这样的凹槽部20的外延晶片100中,抑制了否则将致使碳化硅半导体装置的长期可靠性降低的微小凹坑的形成。因此,根据外延晶片100,可减小氧化膜的膜厚度的变化。[4]在外延晶片100中,偏离方向可以处于相对于<11-20>方向不大于±5°的范围。因此,第二主表面102可在预定偏离方向上相对于(0001)面倾斜。[5]在外延晶片100中,偏离方向可以处于相对于<01-10>方向不大于±5°的范围。因此,第二主表面102可在预定偏离方向上相对于(0001)面倾斜。[6]一种根据本公开的制造外延晶片的方法,包括如下步骤:制备具有第二主表面102的碳化硅衬底110(S10);以及在第二主表面上外延生长碳化硅膜(S20)。外延生长碳化硅膜的步骤包括如下步骤:使用具有C/Si比小于1的源材料气体在第二主表面102上外延生长第一膜121;使用包括(i)具有C/Si比小于1的源材料气体以及(ii)氢气的混合气体重新构建第一膜121的表面;以及使用具有C/Si比不小于1的源材料气体在第一膜121的重新构建的表面上外延生长第二膜122。在上述[6]中,“C/Si比”代表源材料气体中的碳(C)原子数与硅(Si)原子数的比。“重新构建表面”的表达指示通过由氢气蚀刻以及通过源材料气体的外延生长改变第一膜的表面性质。通过重新构建的步骤,可减小、增加或基本上不改变第一膜的厚度。在重新构建表面的步骤中,与一般外延生长相比可减小源材料气体的流率与氢气流率的比,使得由氢气蚀刻与由源材料气体的外延生长具可比性。例如,考虑调整氢气的流率以及源材料气体的流率以获得约0±0.5μm/h的膜形成速率。上述穿透位错包括穿透螺旋位错、穿透边缘位错、以及其中混合了这些位错的复合位错。这些位错以下述方式由伯格斯(Burgers)矢量b表达:穿透螺旋位错(b=<0001>);穿透边缘位错(b=1/3<11-20>);以及复合位错(b=<0001>+1/3<11-20>)。考虑对氧化膜的膜厚度变化存在影响的凹坑部是由于穿透螺旋位错、穿透边缘位错以及复合位错形成的。由于穿透螺旋位错以及复合位错而形成的凹坑部在具有较深深度的位错周围都涉及相对较大的应力。在上述[6]中,重新构建第一膜的表面,借此可预期获得实现由于穿透螺旋位错以及复合位错而形成浅凹坑部的效果。除此之外,源材料气体的C/Si比从小于1的值改变至不小于1的值且随后生长第二膜。因此,考虑增强实现由穿透螺旋位错和复合位错导致的浅凹坑部的效果。[本公开的实施例的细节]以下参考附图,将说明本公开的一个实施例(以下称为“本实施例”)的具体示例。应当注意到在下述附图中,相同或相应的部分由相同参考符号指定且不再重复说明。而且,在本说明书中,单独定向由[]表示,组定向由<>表示,且单独的平面由()表示,且组平面由{}表示。此外,负索引在晶体学中应该是通过置于数字上方的“-”(横杠)进行的,但是在本说明书中通过将负号置于数字前进行表示。<外延晶片的结构>首先,参考图1至图3,下文说明根据本实施例的外延晶片的构造。图1部分地示出根据本实施例的外延晶片的截面结构。图2和图3的每个部分地示出根据本实施例的外延晶片的平面结构。图1示出沿图2和图3中所示的线段I-I截取的截面结构。如图1中所示,根据本实施例的外延晶片100具有碳化硅衬底110以及碳化硅膜120。碳化硅衬底110例如由碳化硅单晶组成。碳化硅单晶例如具有六方晶体结构且具有4H多晶型。碳化硅衬底110包括诸如氮(N)的n型杂质且因此具有n型导电性。碳化硅衬底110具有不小于100mm(不小于4英寸)的直径,优选地,例如不小于150mm(不小于6英寸)。碳化硅衬底110具有第二主表面102以及与第二主表面102相反的第三主表面103。如图1中所示,第二主表面102是其上形成了碳化硅膜120的主表面。第二主表面102具有相对于(0001)面(以下称为“硅(Si)面”)不大于±4°的偏离角。该偏离角的偏离方向例如可处于相对于<11-20>方向不大于±5°的范围或可处于相对于<01-10>方向不大于±5°的范围。碳化硅膜120是通过诸如CVD的气相外延形成在第二主表面102上的碳化硅单晶膜。更具体地,碳化硅膜120是由采用硅烷(SiH4)以及丙烷(C3H8)作为源材料气体且氮气(N2)或者氨气(NH3)作为掺杂气体的CVD形成的外延生长层。而且,碳化硅膜120包括氮(N)原子,其通过氮气或氨气的热分解产生,且因此具有n型导电类型。碳化硅膜120的n型杂质浓度低于碳化硅衬底110的n型杂质浓度。应当注意,因为如上所述第二主表面102相对于(0001)面具有偏离角,因此通过台阶流动生长形成碳化硅膜120。因此,碳化硅膜120与碳化硅衬底110一样也由4H型碳化硅组成,且因此抑制其中混合多晶型的不同类型。碳化硅膜120例如具有约不小于10μm且不大于50μm的厚度。凹槽部20形成在碳化硅膜120的一个表面(即第一主表面101)中。如图2中所示,在第一主表面101的平面图中,凹槽部20沿第一主表面101在一个方向上延伸。更具体地,凹槽部20在作为沿相对于(0001)面的主表面101的偏离角的偏离方向的台阶流动生长方向上延伸。换言之,凹槽部20在相对于<11-20>方向不大于±5°的范围内的方向上或在相对于<01-10>方向不大于±5°的范围内的方向上延伸。应当注意到绘制图1至图3使得“台阶流动生长方向”对应于图1至图3的X轴方向。在图1至图3的每一个中,X轴方向、Y轴方向以及Z轴方向彼此正交。图2和图3每一个中所示的Y轴方向代表垂直于台阶流动生长方向的方向。图1中所示的Z轴方向代表碳化硅膜的厚度方向。凹槽部20在上述一个方向上的宽度(第二宽度82)是其在垂直于该一个方向的方向上的宽度(第三宽度83)的两倍或更大(优选地,五倍或更大)。第二宽度82不小于15nm且不大于50μm,优选不小于25μm且不大于35μm。而且,第三宽度83不小于1μm且不大于5μm,优选不小于2μm且不大于3μm。如图1中所示,凹槽部20形成为在台阶流动生长方向上从碳化硅膜120中包括的穿透位错40延伸。更具体地,凹槽部20包括:形成在穿透位错40上的第一凹槽部21、以及形成为连接至第一凹槽部21且从第一凹槽部21在台阶流动生长方向上延伸的第二凹槽部22。第一凹槽部21在台阶流动生长方向上形成在凹槽部20的一端部处(图1中的左端部)。而且,第一凹槽部21距第一主表面101的最大深度(第二深度)不大于10nm。如图1中所示,第二深度72是整个凹槽部20中的最大深度。而且,第一凹槽部21优选具有不大于1μm的宽度(第一宽度81),且更优选具有不大于0.5μm的宽度(第一宽度81)。如图1中所示,第二凹槽部22形成为从其与第一凹槽部21连接的部分延伸至与上述一个端部相反的另一个端部(图1中的右端部)。而且,形成第二凹槽部22使得第二凹槽部22距第一主表面101的深度(第一深度71)小于第一凹槽部21的最大深度(第二深度72)。更具体地,第二凹槽部22在保持浅于第二深度72的深度的同时在台阶流动生长方向上延伸。第一深度71优选不大于3nm,更优选不大于2nm,且进一步优选不大于1nm。而且,第二凹槽部22例如具有不小于20μm(优选地,不小于25μm)的宽度(第四宽度84)。<用于制造外延晶片的方法>随后,下文描述根据本实施例的用于制造外延晶片的方法。如图4中所示,制造方法包括:制备碳化硅衬底的步骤(S10);以及外延生长碳化硅膜的步骤(S20)。首先,如步骤(S10),执行制备碳化硅衬底的步骤。在本步骤(S10)中,例如采用升华-再结晶方法将通过晶体生长获得的4H型碳化硅晶锭(未示出)切割成预定厚度,由此制备具有第二主表面102以及第三主表面103的碳化硅衬底110(图1)。随后,如步骤(S20),执行生长碳化硅膜的步骤。在本步骤(S20)中,如图1中所示,使用CVD在碳化硅衬底110的第二主表面102上外延生长碳化硅膜120。首先,下文描述本步骤(S20)中采用的外延生长装置1的构造。图5是外延生长装置1的侧视图。图6是沿图5中的线段VI-VI的外延生长装置1的截面图。如图5和图6中所示,外延生长装置1主要包括加热元件6、热绝缘体5、石英管4、以及感应加热线圈3。例如,加热元件6的每个由碳材料组成。如图6中所示,加热元件6具有包括弯曲部7和平坦部8的半圆柱状中空结构。提供并设置两个加热元件6使得它们的相应平坦部8彼此面对。由这些平坦部8围绕的空间是用作用于执行对碳化硅衬底110进行处理的空间的通道2。热绝缘体5是构造为将通道2与外延生长装置1的外部热绝缘的构件。提供热绝缘体5以围绕加热元件6的外周部。提供石英管4以围绕热绝缘体5的外周部。感应加热线圈3缠绕在石英管4的外周部。随后,下文描述采用上述外延生长装置1的晶体生长工艺。首先,将步骤(S10)中制备的碳化硅衬底110置于外延生长装置1的通道2中。更具体地,碳化硅衬底110置于提供在一个加热元件6上的基座(未示出)上。1.外延生长第一膜的步骤(S21)随后,执行外延生长第一膜的步骤。在本步骤中,具有C/Si比小于1的源材料气体用于在碳化硅衬底110的第二主表面102上外延生长第一膜121(参见图1)。首先,在通道2中的气体置换之后,在让载气流动的同时通道2中的压力被调整为诸如60mbar至100mbar(6kPa至10kPa)的预定压力。载气例如可以是氢气(H2),氩气(Ar),氦气(He)等等。载气的流速例如约为50slm至200slm。这里采用的用于流速的单位(即“slm(标准升每分钟)”)代表标准条件(0℃以及101.3kPa)下的“L/min”。随后,预定交流提供至感应加热线圈,由此对加热元件6进行感应加热。因此,通道2以及具有其上放置了碳化硅衬底110的基座被加热至预定反应温度。此时,例如将基座加热至约1500℃至1750℃。随后,提供源材料气体。源材料气体包括Si源气体以及C源气体。Si源气体的示例包括硅烷(SiH4)气体、乙硅烷(Si2H6)气体、二氯甲硅烷(SiH2Cl2)气体、三氯硅烷(SiHCl3)气体、四氯化硅(SiCl4)气体等等。即,Si源气体可以是选自由硅烷气体、乙硅烷气体、二氯甲硅烷气体、三氯硅烷气体以及四氯化硅气体组成的群组中的至少一种。C源气体的示例包括甲烷(CH4)气体、乙烷(C2H6)气体、丙烷(C3H8)气体、乙炔(C2H2)气体等等。即,C源气体可以是选自由甲烷气体、乙烷气体、丙烷气体以及乙炔气体组成的群组中的至少一种。源材料气体可包括掺杂剂气体。掺杂剂气体的示例包括氮气、氨气等。外延生长第一膜的步骤中的源材料气体例如可以是硅烷气体和丙烷气体的混合气体。在外延生长第一膜的步骤中,将源材料气体的C/Si比调整为小于1。例如,C/Si比可以不小于0.5、不小于0.6或不小于0.7,只要C/Si比小于1即可。而且,例如,C/Si比可以不大于0.95、不大于0.9或不大于0.8。硅烷气体的流速以及丙烷气体的流速例如可在约10至100sccm的范围内适当调整以实现期望C/Si比。这里采用的用于流速的单位(即“sccm(标准立方厘米每分钟)”)代表标准条件(0℃以及101.3kPa)下的“mL/min”。外延生长第一膜的步骤中的膜形成速率例如约不小于3μm/h且不大于30μm/h。第一膜例如具有不小于0.1μm且不大于150μm的厚度。第一膜的厚度可以不小于0.2μm、可以不小于1μm、可以不小于10μm、或可以不小于15μm。而且,第一膜的厚度可以不大于100μm、可以不大于75μm、或可以不大于50μm。2.重新构造第一膜表面的步骤(S22)随后执行重新构造第一膜表面的步骤。可接续外延生长第一膜的步骤执行重新构造表面的步骤。替选地,可在外延生长第一膜的步骤以及重新构造表面的步骤之间提供预定暂停时间。在重新构造表面的步骤中,基座的温度可增加约10℃至30℃。在重新构造表面的步骤中,采用包括具有C/Si比小于1的源材料气体以及氢气的混合气体。源材料气体的C/Si比可低于外延生长第一膜的步骤中的C/Si比。C/Si比可不小于0.5、不小于0.6或不小于0.7,只要C/Si比小于1即可。而且,例如,C/Si比可不大于0.95、不大于0.9或不大于0.8。在重新构造表面的步骤中,可在外延生长第一膜的步骤以及外延生长第二膜的下述步骤的每一个中采用不同于源材料气体的源材料气体。以此方式,可预期增强实现较浅凹坑部的效果。例如,考虑这样构造使得在外延生长第一膜的步骤以及外延生长第二膜的下述步骤的每一个中,采用硅烷气体以及丙烷气体,而在重新构造表面的步骤中,采用二氯甲硅烷以及乙炔。在重新构建表面的步骤中,与外延生长第一膜的步骤以及外延生长第二膜的下述步骤中的流速比值相比,可降低源材料气体的流速与氢气的流速的比值。因此,预期会增强获得较浅凹坑部的效果。混合气体中的氢气的流速例如约不小于100slm且不大于150slm。氢气的流速例如可以约为120slm。混合气体中的Si源气体的流速例如可以不小于1sccm且不大于5sccm。Si源气体的流速下限可以为2sccm。Si源气体的流速上限可以为4sccm。混合气体中的C源气体的流速例如可以不小于0.3sccm且不大于1.6sccm。C源气体的流速下限可以为0.5sccm或0.7sccm。C源气体的上限可以为1.4sccm或1.2sccm。在重新构建表面的步骤中,希望调整各种条件使得由氢气蚀刻与由源材料气体的外延生长具有可比性。例如,考虑调整氢气的流速以及源材料气体的流速以获得约0±0.5μm/h的薄膜形成速率。薄膜形成速率可调整为约0±0.4μm/h、可调整为约0±0.3μm/h、可调整为约0±0.2μm/h,或可调整为约0±0.1μm/h。因此,预期会增强获得较浅凹坑部的效果。重新构建表面的步骤中的处理时间例如约不小于30分钟且不大于10小时。处理时间可不大于8小时、可不大于6小时、可不大于4小时或可不大于2小时。3.外延生长第二膜的步骤(S23)在重新构建第一膜的表面之后,执行在这个表面上外延生长第二膜的步骤。采用具有C/Si比不小于1的源材料气体形成第二膜122(参见图1)。例如,C/Si比可以不小于1.05、可以不小于1.1、可以不小于1.2、可以不小于1.3、或可以不小于1.4,只要C/Si比不小于1即可。而且,C/Si比可以不大于2.0、可以不大于1.8、或可以不大于1.6。外延生长第二膜的步骤中的源材料气体可与外延生长第一膜的步骤中采用的源材料气体相同或不同。源材料气体例如可以是硅烷气体和丙烷气体。例如,可在约10至100sccm的范围内适当调整硅烷气体的流速以及丙烷气体的流速以实现所需C/Si比。载气的流速例如可约为50slm至200slm。外延生长第二膜的步骤中的膜形成速率例如可约不小于5μm/h且不大于100μm/h。第二膜例如具有不小于1μm且不大于150μm的厚度。而且,第二膜的厚度可不小于5μm、可不小于10μm、且可不小于15μm。而且,第二膜的厚度可不大于100μm、可不大于75μm、或可不大于50μm。第二膜122的厚度可与第一膜121的厚度相同或不同。第二膜122可薄于第一膜121。例如,第二膜122的厚度与第一膜121的厚度的比值可约不小于0.01且不大于0.9。这里,厚度的比表示将第二膜的厚度除以已经通过重新构建表面的步骤的第一膜的厚度而获得的值。该厚度比可不大于0.8、可不大于0.7、可不大于0.6、可不大于0.5、可不大于0.4、可不大于0.3、可不大于0.2或可不大于0.1。因此,预期增强获得较浅凹坑部的效果。如上所述,如图1中所示,形成了包括第一膜121以及第二膜122的碳化硅膜120。在碳化硅膜120中,第一膜和第二膜可完全合并使得它们彼此不能区别开来。通过如上所述顺序执行步骤(S10)至步骤(S23)、可制成其中在碳化硅膜120的表面中形成凹槽部20的外延晶片100。[评估]1.样本的生产制备了每个具有150mm直径的碳化硅衬底110。在每个碳化硅衬底110中,第二主表面102的偏离方向是<11-20>方向且第二主表面102相对于(0001)面具有4°的偏离角。样本1具有使用根据本公开的制造方法形成的碳化硅膜。样本2具有使用从根据本公开的制造方法中省略重新构建第一膜的表面的步骤(S22)而获得的制造方法形成的碳化硅膜。在每个样本1和样本2中,碳化硅膜都具有15μm的膜厚度。2.凹槽部的形状的评估在每个样本中,使用缺陷检查装置以及AFM测定第一主表面101中形成的凹槽部的形状。结果在表1中示出。这里采用的用于检查缺陷位置的装置是由Lasertec公司提供的WASAVI系列“SICA6X”(物镜:x10)。这里采用的AFM例如可以是Veeco提供的“Dimension300”。而且,对于AFM的悬臂(探针)来说,例如可采用Bruker提供的“NCHV-10V”。对于AFM的测量条件来说,测量模式设定为敲击模式,敲击模式中的测量面积设定为具有每个边为20μm的正方形,且测量深度设定为1.0μm。而且,在测量面积中的扫描速度设定为一个循环5秒、每个扫描线的数据量设定为512点、且扫描线的数量设定为512的条件下执行敲击模式中的采样。而且,悬臂的位移控制设定为15.50nm。[表1]样本1样本2第一凹槽部的最大深度(第二深度)3nm25nm第二凹槽部的深度(第一深度)不大于1nm-一个方向上的宽度(第二宽度)25μm1μm垂直方向上的宽度(第三宽度)2μm1μm如表1中所示,在样本1中,检测到其中第二宽度82是第三宽度83两倍或更大的凹槽部20。第二宽度82是沿着第一主表面101在台阶流动生长方向(即“一个方向”)上即在台阶流动生长方向上延伸的宽度,且第三宽度83是在垂直于台阶流动生长方向的方向上的宽度。进一步,由于对样本1中的凹槽部20的形状进行的详细检查,因此发现展现了最大深度的部分包括在凹槽部20的一端部中。展现了最大深度的部分的深度是3nm。从这个部分延伸至另一个端部的部分的深度不大于1nm。即,样本1中的凹槽部20包括第一凹槽部21以及连接至第一凹槽部21的第二凹槽部22,其中第一凹槽部21在台阶流动生长方向上形成在凹槽部20的一个端部处,第二凹槽部22在台阶流动生长方向上从第一凹槽部21延伸至与一个端部相反的另一个端部,且作为距第一主表面101的深度的第一深度71小于作为第一凹槽部的最大深度的第二深度72。另一方面,在样本2中,检测到多个凹槽部(即凹坑部30),在其中每一个中第二宽度82以及第三宽度83基本相同且第二深度72(即最大深度)大于10nm。在表1中,出于方便起见,样本2中的凹槽部的最大深度在用于第一凹槽部的最大深度的列中示出。3.氧化膜的膜厚度的变化的评估通过在包括氧气的气氛下加热样本1和2,在碳化硅膜120的第一主表面101上形成了氧化膜。进一步,使用透射电子显微镜观察氧化膜以测量氧化膜的膜厚度的变化。结果在表2中示出。[表2]样本1样本2不具有凹槽部的部分的膜厚度(nm)5252凹槽部附近的最小膜厚度(nm)5149凹槽部附近的最大膜厚度(nm)5160膜厚度的变化(A/B)-1/-1+8/-3在表2中的“膜厚度的变化”列中,“A/B”示出为表示凹槽部附近的最大膜厚度以及不具有凹槽部的部分的膜厚度之间的差(A),以及凹槽部附近的最小膜厚度以及不具有凹槽部的部分的膜厚度之间的差(B)。这里,指示如果A和B两者都是较小的数值则膜厚度的变化较小。如表2中所示,样本1中的膜厚度的变化小于样本2,且因此样本1优异。本文公开的实施例在任意方面都是描述性而非限制性的。本发明的范围由权利要求项定义,而不是由上述实施例定义,且旨在涵盖等效于权利要求项的范围和含义内的任意变型。参考符号列表1:外延生长装置;2:通道;3:感应加热线圈;4:石英管;5:热绝缘体;6:加热元件;7:弯曲部;8:平坦部;100:外延晶片;101:第一主表面;102:第二主表面;103:第三主表面;110:碳化硅衬底;120:碳化硅膜;121:第一膜;122:第二膜;20:凹槽部;21:第一凹槽部;22:第二凹槽部;30:凹坑部;40:穿透位错;71:第一深度;72:第二深度;81:第一宽度;82:第二宽度;83:第三宽度;84:第四宽度。当前第1页1 2 3