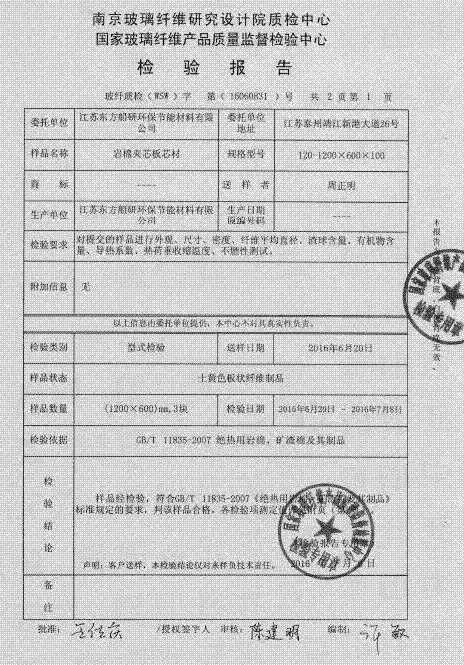
本发明涉及一种岩棉生产中固体废弃物的再利用方法,属岩棉固体废弃物应用
技术领域:
。
背景技术:
::岩棉制品是一种优质的保温节能材料,被广泛使用在各个领域。在我国工业、建筑、船舶等行业岩棉使用比例逐年递增。在建材工业“十二五”发展规划中明确提出:企业要坚持绿色发展。加强节能减排和资源综合利用,大力发展循环经济,推进清洁生产,着力开发集安全、环保、节能于一体的绿色建筑材料,促进建材工业向绿色功能产业转变。在岩棉生产过程,会产生各种废弃物,其中固体废弃物是制约生产的一个重要因素。固体废弃物包括:熔体废液、分离渣球、飞散棉絮、不合格产品等,这些废弃物如果不进行及时处理,随着生产的进行,会造成场地的大量堆积占用,同时通过风系、水系影响,造成很大的环境污染,所以对于岩棉企业来说固体废弃物的再利用已经是刻不容缓的事情了。纵观国外岩棉企业,固体废弃物的再利用已经成为一种生产过程的标准配置,在生产过程中各个环节产生的废弃物均可以回收再利用,整个企业处于零排放、零污染的状态。国外的常规处理方法是废弃物调整成分后,按比例造块再按原料配比由冲天炉熔化,再经过正常生产流程完成循环利用,制成成品。技术实现要素::本发明根据现有技术存在的问题,提供一种固体废弃物循环利用的有效实现方法。本发明的具体技术方案如下:本发明岩棉生产中固体废弃物的再利用方法,包括以下步骤:1)根据工艺要求把岩棉生产的废棉、板、条进行机械粉碎至絮状的废棉料备用;2)把岩棉生产的废矿渣、炉渣进行机械粉碎至颗粒状骨料备用;3)把炼钢生产的废矿渣进行机械细粉碎至细沙状的粉料备用;4)各成分按如下重量份进行配料,混合料中废棉料40~48份,骨料28~35份,粉料10~16份,硅酸盐粘结剂8~15份;向混合料中加水调整含水量至6~10%,充分搅拌均匀后,配料结束;5)通过成型设备将上述混合料压制成型,在压制时通过机械震动将成型中混合料中空气排出,并将混合料压制成料块;6)压制后对料块进行干燥;7)准备玄武岩石和白云石物料,并取上述干燥后料块,分别进行取样分析测出硅、铝、钙、镁的含量;再按以下重量份:玄武岩55~75份,料块5~29份,白云石16~20份进行配料,并控制总酸度系数;当生产岩棉制品时,控制总酸度系数在1.6~1.7范围;当生产矿棉制品时,控制总酸度系数至1.4~1.6范围;8)配好料后加入冲天炉中即可进行岩棉制品或矿棉制品的生产加工。本发明的进一步设计在于:步骤4)配料结束后,放入困料室困料2~3小时,使水分充分均匀。步骤4)中硅酸盐粘结剂采用水泥。步骤6)中所述干燥采用自然干燥或采用干燥室干燥。自然干燥时,可将湿料块放置在平整的场地上进行自然风干3~4天后可入炉使用;干燥室干燥时,在105℃~115℃温度下保持7~10小时即可。步骤5)中,排出空气约占总体积的45~55%左右;混合料压制成料块的体积密度2.5~3.5kg/m。步骤6)中粉碎至0.2~10mm的颗粒。步骤6)中压制的料块的整体规格为8~15cm。步骤7)中玄武岩石和白云石的整体规格为80~150cm;白云石的整体规格为40-80cm。本发明相比现有技术具有如下优点:本发明通过生产工艺的不断尝试、摸索和实验,最终取得了成功。在岩棉生产过程中产生的各种废弃物均可通过成分分析、成分调整、压制造块等工艺手段加以再利用,已经达到了固体废弃物的零排放标准。1、本发明对废弃物的循环再利用的分析在岩棉生产过程中,主要产生废弃物的工艺点为:熔化段、成纤段和成型段。熔化段主要是冲天炉在点炉、挂炉、停炉、更换产品及设备维护中产生的废弃熔体流入地坑;成纤段主要是离心机分离的渣球、集棉机的集棉效果、清理集棉网板的废棉絮等;成型段主要是调整产品产生的产品以及生产过程中的出现的不合格产品等。根据统计:一条年产2万吨产品的达标岩棉生产线,各种原料需求总量约为:3万吨/年,扣去烧失量和各个环节产生的废弃物,合格产品约为2.05万吨/年。从原料到最终产品,制成率约为65%,各种固体废弃物可达1万吨/年。根据地方的固废填埋处理办法,堆埋场地费、运输费、人力费以及其他的一些费用,固废的处理费用约为:50元/吨,1万吨约需要50万元,这个金额对于企业来说是个非常沉重的负担和包袱。如果将这些废弃物进行成分调整并造块回用代替一部分原料,即可变废为宝,不但可以省去原有的处理费用,还可以大大降低原料的采购费用,直接降低了产品的成本。仍然按照年产2万吨的生产线来计算,可利用的废弃物算为1万吨,按比例混入一部分的矿渣、玄武岩、粘结剂等,造块后重量为2.2万吨。从原料成本上算,2.2万吨原料矿渣需要525万元左右,利用废棉、废渣制成的原料及生产成本只有245万元左右,在相等原料的情况下,成本节约了280万元左右,加上50万的处理费用,两项共节约费用330万元,这对常规岩棉厂家来说是个非常利好的事情,可为企业创下可观的效益。2、废弃物的化学成份分析和调整固体废弃物是不可以直接粉碎造块,需要进行合理配料,造块过程中固废与辅料粉碎、配比、混合、成型的过程,因此各类原料可以充分的均匀混合,大大增加了高温时固~固相、固~液相、液~液相反应的接触面积,有利于共熔化合物的产生,有利于熔炼的顺利进行,并可保证熔体的成分均匀性一致。3、造块工艺路线的制定本发明生产料块具有一定的热稳定性,在冲天炉内熔化时从常温突然上升到500℃以上,不会由于温度突然升高造成爆裂粉碎,同时熔化过程不会由于温度升高直接在炉内解体,而是从外层逐步熔解。本发明合理控制了料块的含水量,在熔化时不能对冲天炉造成额外的负担。本发明考虑到上述料块的化学及物理性能,料块工艺路线进行了合理设计:第一,本发明中,料块的原料要按照比例粉碎成骨料和粉料,没有骨料造块后没有骨架支撑,缺少粉料粘结强度不够,因此两者要充分搅拌混合均匀。第二,加入硅酸盐类粘结剂增加其成型强度。第三,压料成型时,混合料的空气排出,料块的体积密度较高,保证了料块有较好的机械强度。第四,料块经困料和烘干后,均匀度好,可形成具有较高机械强度的料块。附图说明:图1为本发明实施例制备的岩棉夹芯板芯材进行检测结果之一。图2为本发明实施例制备的岩棉夹芯板芯材进行检测结果之二。图3为本发明实施例制备的岩棉夹芯板芯材进行检测结果之三。具体实施方式:下面结合附图对本发明做进一步的描述,但各实例不作为对本发明的限制。实施例一:本发明岩棉生产中固体废弃物的再利用方法,包括以下步骤:1)根据工艺要求把岩棉生产的废棉、板、条进行机械粉碎至絮状的废棉料备用;2)把岩棉生产的废矿渣、炉渣进行机械粉碎至0.2~10mm颗粒状骨料备用;3)把高炉矿渣进行机械细粉碎至细沙状的粉料备用;4)各成分按如下重量份进行配料,混合料中废棉料44.4份,骨料30.6份,粉料13.7份,硅酸盐粘结剂11.3份(350水泥);向混合好的混合料中加水调整含水量至8%,充分搅拌均匀后,放入困料室困料2.5小时,使水分均匀。5)通过液压成型设备将上述混合料压制成型,在压制时通过机械震动器震动,将成型中混合料中空气排出,排出空气约占总体积的50%左右,并将混合料压制成整体规格为8~15cm的料块,要求体积密度2.5~3.5kg/m,以保证料块有较好的机械强度;6)压制后对料块进行干燥,自然干燥时,可将湿料块放置在平整的场地上利用阳光和风进行自然风干4天后入炉使用;7)准备玄武岩石和白云石物料,玄武岩石整体规格为80~150cm;白云石的整体规格为40-80cm;并取上述干燥后料块,三者分别进行取样分析测出硅、铝、钙、镁的含量;再按以下重量份:玄武岩60.1份,料块23.3份,白云石16.6份,进行配料,并控制总酸度系数。本实例生产岩棉制品时,控制总酸度系数在1.6~1.7范围;计算公式:酸度系数=(硅+铝)/(钙+镁),总酸度系数计算时,公式中四种成份为三种物料中硅、铝、钙、镁的氧化物重量之和;本实例中得到总酸度系数1.63。一般情况下调节时,当酸度系数偏小时,增大玄武岩加入量;当酸度系数偏大时,增大料块的加入量。各类配料的化学成份检测表:单位:质量百分比原料名称SiO2Al2O3CaOMgOMk料块29.34%16.87%32.71%10.16%1.08白云石微量微量29.8%19.77%玄武岩44.45%17.23%7.6%9.82%3.548)配好料后加入冲天炉中即可进行岩棉制品或矿棉制品的生产加工。实施例二:本发明岩棉生产中固体废弃物的再利用方法,包括以下步骤:1)根据工艺要求把岩棉生产的废棉、板、条进行机械粉碎至絮状的废棉料备用;2)把岩棉生产的废矿渣、炉渣进行机械粉碎至0.2~10mm颗粒状骨料备用;3)把高炉矿渣进行机械细粉碎至细沙状的粉料备用;4)各成分按如下重量份进行配料,混合料其中废棉料45份,骨料30份,粉料15份,硅酸盐粘结剂10份(350水泥);向混合料中加水调整含水量至8%,充分搅拌均匀后,配料结束;配好料后放入困料室困料3小时,使水分充分均匀。5)通过液压成型设备将上述混合料压制成型,在压制时通过机械震动器震动,将成型中混合料中空气排出,排出空气约占总体积的50%左右,并将混合料压制成整体规格为8~15cm的料块,要求体积密度2.5~3.5kg/m,以保证料块有较好的机械强度;6)压制后对料块进行干燥,干燥室干燥时,在110℃温度下保持8小时,即可形成具有较高机械强度的料块。7)准备玄武岩石和白云石物料,玄武岩石整体规格为80~150cm;白云石的整体规格为40~80cm;并取上述干燥后料块,三者分别进行取样分析测出硅、铝、钙、镁的含量;再按以下重量份:玄武岩40.8份,料块54.6份,白云石4.6份进行配料,并控制总酸度系数。本实例生产矿棉制品时,控制总酸度系数至1.4~1.6范围;计算公式:酸度系数Mk=(硅+铝)/(钙+镁),总酸度系数计算时,四种成份为三种物料中硅、铝、钙、镁的氧化物重量之和;本实例得到总酸度系数1.48各类配料的化学成份检测表:单位:质量百分比原料名称SiO2Al2O3CaOMgOMk料块29.34%16.87%32.71%10.16%1.08白云石微量微量29.8%19.77%玄武岩粉44.45%17.23%7.6%9.82%3.548)配好料后加入冲天炉中即可进行岩棉制品或矿棉制品的生产加工。实施例三:本实例中:步骤4)中,各成分按如下重量份进行配料,混合料中废棉料45份,骨料32份,粉料10份,硅酸盐粘结剂9份(350水泥);步骤7)中,按重量份:玄武岩60.1份,料块23.3份,白云石16.6份进行配料,并控制总酸度系数为1.63。其余条件及制备过程同实施例一。测试实例:试样:实例一配好的料,混合后投入冲天炉内,通过鼓风、鼓氧融化,熔体经离心机离心成纤,在吹离风、负压风的共同作用下吸附在集棉机上,在经过固化炉烘干、飞锯切割,最终制成岩棉制品。检验单位:南京玻璃纤维研究设计院质检中心、国家玻璃纤维产品质量监督检验中心。检验结果如下表1、表2,并如图1-图3所示。由检验结果可知,本发明制备的岩棉夹芯板芯材外观、尺寸、密度、纤维平均直径、渣球含量、有机物含量、导热系数、热荷重收缩温度、不燃性测试各项指标准合格。由此可见,本发明岩棉生产中固体废弃物的再利用方法,工艺设计合,得到的产品性能质量可靠,可广泛应用于实际生产中,具有可观的市场前景。表1:表2:当前第1页1 2 3