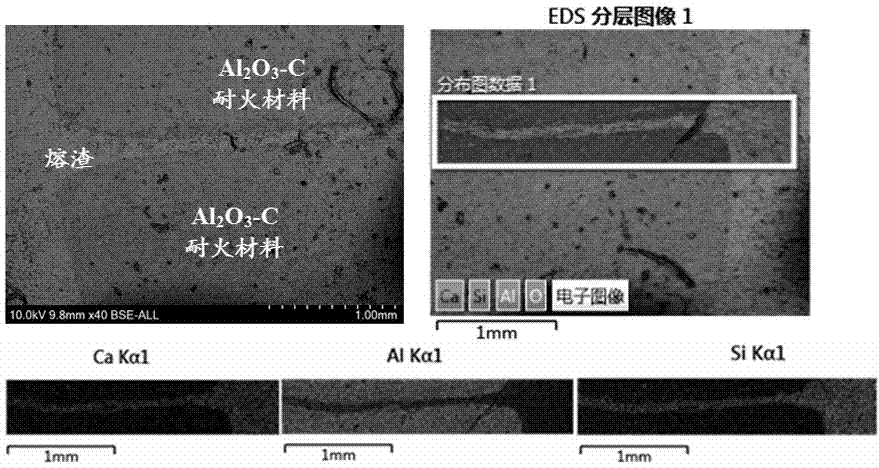
本发明属于冶金耐火材料
技术领域:
,具体涉及一种含碳耐火材料抗熔渣侵蚀的保护方法,改变含碳耐火材料与高温熔渣之间的界面接触角以及界面张力,降低熔渣在耐火材料中渗透深度,实现含碳耐火材料长寿化。
背景技术:
:铝碳耐火材料(al2o3-c)或镁碳耐火材料(mgo-c)具有优良的抗渣侵能力、高的抗热震性和良好的导热性,被广泛应用于钢铁冶金领域,如钢包内衬、侵入式水口以及连铸机内衬等。作为钢包内衬材料,在洁净钢冶炼过程中,因受高温钢水的物理冲刷以及炉渣的化学侵蚀等作用,不仅其服役寿命逐渐下降,而且受侵蚀剥落的耐火材料极易进入钢液,成为大颗粒夹杂物(>100μm),严重影响钢的洁净度。因此,降低耐火材料损耗对于提高钢水质量和延长冶金部件服役寿命均具有重大现实意义。转炉炼钢过程中,通过调整熔渣成分实现“溅渣护炉”,从而提高耐火材料的服役寿命。由于钢铁生产过程中冶炼不同钢种对炉渣成分的要求也不同,单纯依靠改变渣成分不能满足冶炼的工艺要求,必须寻找一种突破熔渣成分束缚,且操作简便的耐火材料保护方法。技术实现要素:本发明公开了一种含碳耐火材料抗熔渣侵蚀的保护方法,通过对熔渣体系提供适宜外加电压,减缓熔渣在耐火材料中的渗透深度,实现对含碳耐火材料的物理保护。为达到上述发明目的,本发明采用如下技术方案:一种抗熔渣侵蚀含碳耐火材料的保护方法,包括以下步骤,将含碳耐火材料脱碳处理后与熔渣接触,然后将脱碳处理的耐火材料与熔渣分别连接电源的正极、负极;然后于0~4v通电处理,实现含碳耐火材料抗熔渣侵蚀的保护。可有效抑制熔渣在含碳耐火材料中的物理渗透,可显著提高含碳耐火材料的抗渣侵能力,可实现提高含碳耐火材料服役寿命3~4倍以上。本发明还公开了一种抗熔渣侵蚀含碳耐火材料,其制备方法包括以下步骤,将含碳耐火材料脱碳处理后与熔渣接触,然后将脱碳处理的耐火材料与熔渣分别连接电源的两级;然后于0~4v通电处理,得到抗熔渣侵蚀含碳耐火材料。本发明还公开了一种抗熔渣侵蚀钢包,其制备方法包括以下步骤,将含碳耐火材料脱碳处理后作为内衬制备钢包;然后将内衬与熔渣接触,再将内衬与熔渣分别连接电源的两极;然后于0~4v通电处理,制备得到抗熔渣侵蚀钢包。本发明还公开了一种保护钢包抗熔渣侵蚀方法,包括以下步骤,将含碳耐火材料脱碳处理后作为内衬制备钢包;然后将内衬与熔渣接触,再将内衬与熔渣分别连接电源的两极;然后于0~4v通电处理,实现钢包抗熔渣侵蚀的保护,实现提高钢包抗渣侵能力,延长钢包服役寿命。本发明还公开了一种熔炼过程中减少钢液增碳量的方法,包括以下步骤,钢水注入钢包中后,将钢包内衬含碳耐火材料(优选脱碳处理后的含碳耐火材料)、钢水表面熔渣分别连接直流电源的两级,于0~4v通电处理,熔炼结束后放出钢液,实现熔炼过程中钢液增碳量的减少。本发明首次公开了这种工业化方法,直接用于工业化冶钢过程,既提高了钢包渣线抗渣侵蚀能力,又不会对熔渣成份产生影响,避免钢包耐火材料脱落引起大颗粒夹杂物,尤其是不会影响钢水性质,氧含量几乎不变,特别是钢液增碳量减少。上述技术方案中,熔渣由炉渣熔解得到,炉渣包括二氧化硅、氧化钙、氧化铝,将三种无机粉末混合,然后加热得到熔渣。本发明通过耐火材料表面脱碳处理增加介质层,对耐火材料实现有效物理保护,该方法不会改变熔渣成份,而且有效提高电润湿电压范围,这是本发明创造性所在,有效解决了现有电化学处理技术会改变熔渣成份的问题,为耐火材料抗渣侵蚀突破性技术。上述技术方案中,将含碳耐火材料置于马弗炉中进行表面浅层脱碳处理,处理温度为500℃,脱碳时间为20min;形成一定厚度的介质层;本发明中,熔渣具有一定的导电能力(1873k时,电导率为0.5~1.0ω-1·cm-1),可作为导电液体,含碳耐火材料具有一定的导电能力,特别在系统中引入了一定厚度的介电层,可消除熔渣电解,并极大提高电极两端电压范围,实现对含碳耐火材料的物理保护,扩大本发明应用领域。上述技术方案中,在加热条件下将含碳耐火材料脱碳处理后与熔渣接触,为保持熔渣具有足够的流动性,加热温度为1550~1650℃。上述技术方案中,铝碳耐火材料为铝碳砖,镁碳耐火材料为镁碳砖,均具有一定的导电性能,广泛作为炼钢钢包内衬和水口材料。上述技术方案中,所述含碳耐火材料为铝碳耐火材料时,脱碳处理的耐火材料与熔渣分别连接电源的正极、负极,所述含碳耐火材料为镁碳耐火材料时,脱碳处理的耐火材料与熔渣分别连接电源的负极、正极;比如铝碳耐火材料与钼棒连接后通过电极引线连接到直流电源的正极,镁碳耐火材料与钼棒连接后通过电极引线连接到直流电源的负极。上述技术方案中,熔渣插入钼棒后通过电极引线连接直流电源的负极或者正极。上述技术方案中,将无机粉末混合,配制成炉渣;将炉渣加热熔清,得到熔渣;将含碳耐火材料与熔渣通过电极引线分别连接直流电源的两极;启动电源,调整电压在一定的范围内,通电处理,拿出耐火材料进行空冷,利用sem观察熔渣在耐火材料中的渗透情况。本发明中,耐火材料、熔渣、钼棒、直流电源之间形成电系统。比如将尺寸φ10×25mm2铝碳耐火材料通过高温水泥用钼棒连接牢固作为阳极(若镁碳耐火材料则作为阴极),然后缓慢浸入熔渣中,再以钼棒插入熔渣作为阴极(阳极),阳极和阴极通过电极引线连接在直流电源的正极和负极;通过调节外加电势大小改变界面电效果,从而降低熔渣在耐火材料中的渗透深度,实现对耐火材料的有效保护。本发明中,炉渣碱度w(cao)/w(sio2)=0.8~2.3,炉渣中al2o3的质量百分数为11.5~35%,制备过程的温度为1550~1650℃,始终保持熔渣为液态,保证处理过程中熔渣与耐火材料之间界面接触,尤其是本发明方法适用大部分钢种冶炼要求,解决了现有抗渣侵蚀方法适应性弱、特异性强的问题,极大利于工业化应用。由于上述技术方案的运用,本发明与现有技术相比具有下列优点:本发明首次以铝碳耐火材料为正极(或者镁碳耐火材料为负极),通过外加一定的电压,成功减缓熔渣在含碳耐火材料中的渗透深度,实现对耐火材料的物理保护;特别是本发明没有在耐火材料表面形成新抗侵蚀材料层,没有改变耐火材料以及熔渣的成份。本发明通过调整施加在液体—固体电极之间的电势,来改变液体和固体之间的表面张力,从而改变两者之间的接触角,达到降低熔渣在耐火材料中渗透深度的效果;尤其是在系统中引入了介电层,可消除熔渣电解,并极大提高电极两端电压范围,扩大其应用领域。本发明限定炉渣基础物性,在通电处理时降低耐火材料与熔渣之间的界面张力,增大熔渣与耐火材料之间的接触角,提高界面处熔渣粘度,从而可降低熔渣对耐火材料的侵蚀。本发明通过限定外加电压、处理时间,结合熔渣,一方面可以使耐火材料/熔渣界面张力变小,一方面又避免界面接触角变小,从而可以大幅提高耐火材料抗渣侵蚀能力,解决现有技术耐火材料/熔渣界面张力变小的同时界面接触角也变小的缺陷。本发明公开的实施方法简单可控,易于操作,适合工业化生产;并且可以根据实际炼钢工艺进行调节,实用性更加广泛。试验证实:在耐火材料和熔渣之间施加0~4v的外加电势,可以将熔渣在耐火材料中的水平渗透深度降低3~4倍以上,实现耐火材料的长寿化。附图说明图1为实施例一中阳极铝碳耐火材料截面的sem和eds图;图2为实施例一中阴极铝碳耐火材料截面的sem和eds图;图3为实施例二中阴极镁碳耐火材料界面的sem和eds图;图4为实施例三中铝碳耐火材料表面形貌图。具体实施方式下面结合实施例、附图对本发明作进一步描述:本实施例所用熔渣的原料组成范围见表1所示:表1实施例选用的熔渣组成,质量分数/%实施例caosio2al2o3r=w(cao)/w(sio2)一4048.511.50.8二4520352.3三4040201.00实施例一根据表1所示的成分配制碱度为0.8的熔渣,将熔渣置于石墨坩埚内并在高温电阻炉内加热熔清。当温度达到1550℃后保持20min,以均匀熔渣成分。将固定在钼棒上的表面脱碳的铝碳砖(φ10×25mm2)作为阳极连接到直流电源的正极,使用另一根钼棒连接到电源的负极构成阴极(反向接入直流电源,即将钼棒和耐火材料分别接入直流电源的正极和负极,构成系统中的阳极和阴极,作对比),将阴极钼棒、阳极耐火材料试样浸入熔渣内5mm,打开直流电源,调整槽电压为3v,通电30min后取出样品,观察两种条件下(阳极保护和阴极保护)耐火材料表面的侵蚀状况。利用sem和eds观察本发明条件下,耐火材料界面侵蚀情况。对于作为阳极的铝碳耐火材料表面形成一层较为致密的覆盖层(~200μm),eds显示其表面al离子浓度明显高于耐火材料基体内部,而且界面清晰,无明显渗透层,如附图1所示,说明本发明方法使得耐火材料表面形成致密氧化铝层,限制氧化铝向炉渣扩散。而对于作为阴极的铝碳耐火材料表面没有发现任何覆盖层,腐蚀界面模糊,且明显观察到熔渣在耐火材料基体内部较深的渗透轨迹,见附图2所示,eds表明熔渣中al离子浓度明显高于初始渣成分。相比于本发明效果,无外加电场的耐火材料界面腐蚀较为严重,熔渣在耐火材料中的水平渗透深度约为400~500um。实施例二根据表1所示的成分配制碱度为0.8的熔渣,将熔渣置于石墨坩埚内并在高温电阻炉内加热熔清。当温度达到1550℃后保持20min,以均匀熔渣成分。将固定在钼棒上镁碳砖(φ10×25mm2)作为阴极连接到直流电源的负极,使用另一根钼棒连接到电源的正极构成阳极,将阳极钼棒、阴极耐火材料试样浸入熔渣内5mm,打开直流电源,调整槽电压为4v,通电30min后取出样品,观察两镁碳耐火材料表面的侵蚀状况。利用sem观察本发明条件下,阴极保护的mgo-c耐火材料界面侵蚀情况。侵蚀界面清晰,界面无任何覆盖层,如图3所示,但是熔渣在耐火材料内部的渗透深度(75μm)明显较无电场时渗透深度(320μm)要小,eds表明界面附近熔渣中al3+、si4+和ca2+浓度高于熔渣中的离子浓度,表明阴极区域熔渣的粘度增加,从而减缓熔渣在镁碳耐火材料中的渗透。实施例三根据表1所示的成分配制碱度为2.3的熔渣样品,将混合粉末放置于石墨坩埚内并在高温电阻炉内加热熔清。当温度达到1650℃后保持20min,以均匀熔渣成分。将脱碳的铝碳耐火材料和钼棒分别接入直流电源正极和负极,将钼棒、耐火材料试样浸入熔渣内5mm,打开直流电源,调整槽电压为2v,通电60min后取出样品,观察耐火材料表面的侵蚀状况。经过60min处理后,耐火材料的表面形状较为规则,如附图4所示。利用sem和eds对铝碳耐火材料截面进行观察,可以发现铝碳耐火材料表面致密氧化铝覆盖层的厚度有所增加(~300μm),eds显示其表面al离子浓度明显高于耐火材料基体内部,而且界面清晰,无明显渗透层。实施例四根据表1所示的成分配制碱度为1.0的熔渣样品,将混合粉末放置于石墨坩埚内并在高温电阻炉内加热熔清。当温度达到1600℃后保持20min,以均匀熔渣成分。将铝碳耐火材料和钼棒分别接入直流电源正极和负极,将钼棒、耐火材料试样浸入熔渣内5mm,打开直流电源,调整槽电压为4v,通电60min后取出样品,得到处理后的样品。处理后的耐火材料表面规则,侵蚀截面显示表面仍有一定厚度的氧化铝覆盖层(~150μm),eds显示覆盖层内al离子浓度明显高于耐火材料基体内部,界面清晰,无明显渗透层。实施例五以实施例四中试验条件为测试条件,将槽电压调整为5v,则侵蚀后铝碳耐火材料表面仍然覆盖一层致密的覆盖层(~150μm),但是阴极区域可见少量si金属单质,表明该电压可引起熔渣发生电解,从而改变初始渣成分。因此,本发明首次实施的外加电场的物理保护电压范围为0~4v,有效解决了现有技术熔渣成份变化的问题,这在现有技术未见报道,取得了意想不到的技术效果。实施例六以某厂熔炼车间的120t钢包为处理对象,采用实施例一中的熔渣组分,熔渣随着钢水注入钢包中并浮于钢水表面;然后以钢包内衬al2o3-c砖为整体阳极,钼棒为阴极,将电极引线连接耐火材料和钼棒,分别与直流电源的正极和负极连接;设置电压为3v,处理60分钟,关闭电源,拆除引线,测试最终钢制品的性能,钢中氧含量变化不大,但钢液增碳量减少,因钢包耐火材料脱落引起的大颗粒夹杂物数量减少80%以上。说明本发明可以有效实现铝碳耐火材料作为钢包渣线的物理保护,减缓熔渣和钢液对耐火材料的侵蚀溶解,避免了耐火材料污染钢水,最终保证钢品质。实施例七以某厂熔炼车间的120t钢包为处理对象,采用实施例一中的熔渣组分,熔渣随着钢水注入钢包中并浮于钢水表面;然后以钢包内衬mg-c砖为整体阴极,钼棒为阳极,将电极引线连接耐火材料和钼棒,分别与直流电源的负极和正极连接;设置电压为4v,处理60分钟,关闭电源,拆除引线,测试最终钢制品的性能,钢中氧含量变化不大,但钢液增碳量减少,因钢包耐火材料脱落引起的大颗粒夹杂物数量减少65%以上。说明本发明可以有效实现镁碳耐火材料作为钢包渣线的物理保护,减缓熔渣和钢液对耐火材料的侵蚀溶解,避免了耐火材料污染钢水,最终保证钢品质。本发明的抗侵蚀钢包可以利用表面脱碳后的含碳耐火材料制备钢包内衬,然后以含碳耐火材料(钢包内衬)和钼棒连接电源的两极,于0~4v持续通电处理,实现钢包抗熔渣侵蚀的保护。本发明在生产过程中持续保持这种外电场的存在,没有形成高熔点覆盖层,耐火材料能得到良好的保护,尤其针对镁碳耐火材料,这与现有技术的思想不一样,避免了现有技术在耐火材料表面形成致密覆盖层并持续存在的问题;本发明实施例中试验时间是为了表征本发明对耐火材料的保护效果。当前第1页12