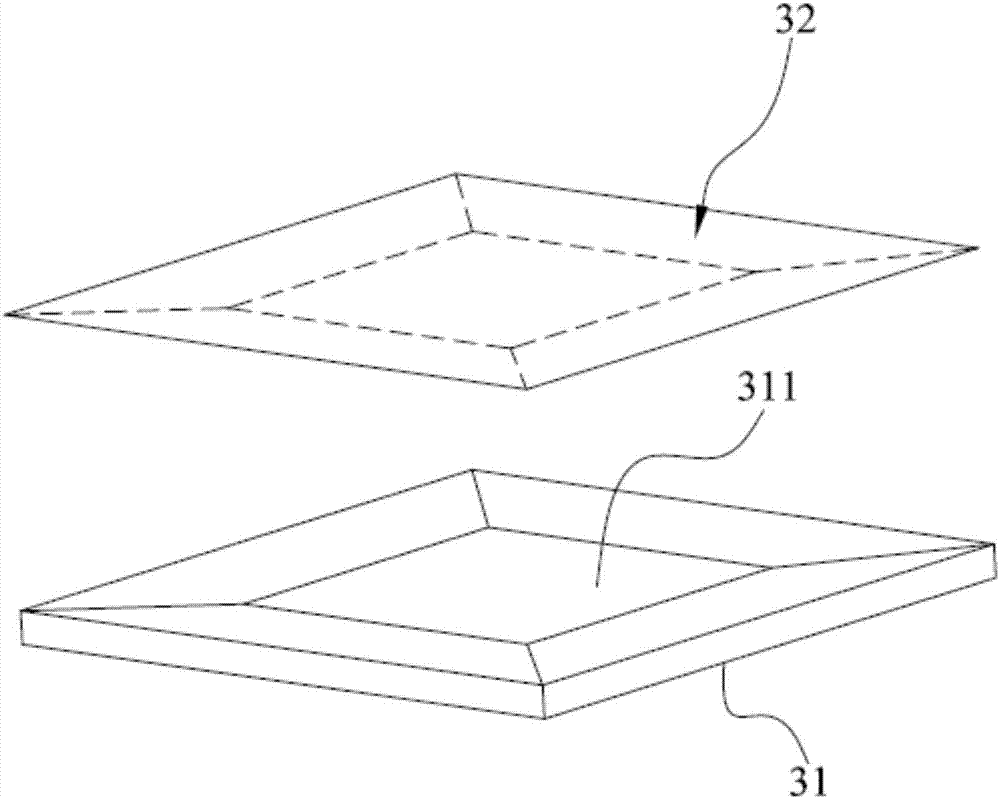
本发明涉及多晶硅铸锭技术邻域,特别涉及一种组合底板及含有该组合底板的多晶硅铸锭炉。
背景技术:
:随着不可再生资源的消之殆尽,加之全球环境的日益恶劣,寻求节能环保的可再生能源成为了全世界的科学家门研究的主要方向。太阳能作为可再生能源的典型代表广泛得到推广,在太阳能的有效利用当中,光电利用是近年来发展最快、最具活力的研究领域。其中,硅材料是光电利用的主要载体,硅晶体的制备是光伏电池的基础。如今,多晶硅铸锭技术是一项制备多硅晶体的成熟技术,其通常依赖多晶硅铸锭炉来进行多硅晶体的制备。多晶硅铸锭炉通常包括炉体及设于所述炉体内的坩埚、底板及若干加热器,若干加热器分别布置于坩埚的侧围及顶部,用于形成热场,坩埚放置于底板的顶部中心区域上,其内用于生长多晶硅。现有技术当中,目前多晶硅铸锭炉使用的底板通常采用石墨板,由于坩埚的侧围存在加热器,加热器将对底板顶部进行辐射,导致底板顶部的温度向放置坩埚的区域中心逐渐减小,而整个底板的导热速率又一致,从而使得底板顶部无法形成均匀热场,从而导致坩埚顶部的热场不均匀,进而导致长晶界面存在过凸或者过凹现象,长晶过程中缺陷大量繁殖,导致低效片占比高。技术实现要素:基于此,本发明的目的是提供一种能够形成均匀热场的组合底板及含有该组合底板的多晶硅铸锭炉,以抑制多晶硅长晶过程中的缺陷繁殖。一种组合底板,包括基板,还包括隔热保温层,所述基板的顶部开设有一填充槽,所述填充槽的槽口边缘与所述基板的顶部边缘重合,所述填充槽的侧壁呈平滑倾斜状,且所述填充槽的槽口的面积大于所述填充槽的底部表面的面积,所述隔热保温层填充于所述填充槽内,以将所述填充槽填平,所述隔热保温层的导热速率小于所述基板的导热速率。一种多晶硅铸锭炉,包括炉体及设于所述炉体内的坩埚及若干加热器,若干所述加热器分别布置于所述坩埚的侧围及顶部,所述多晶硅铸锭炉还包括上述的组合底板,所述坩埚设于所述组合底板的顶部中心。上述组合底板及多晶硅铸锭炉,通过在所述基本的顶部开设有所述填充槽,并使所述填充槽的宽度向底部逐渐减小,然后通过导热速率低的所述隔热保温层将所述填充槽填平,使得所述组合底板填充的所述隔热保温层的厚度向中心区域逐渐减小,从而使得所述组合底板的导热速率向中心逐渐减小。当所述坩埚侧围的所述加热器对所述组合底板进行辐射时,虽然会导致所述组合底板顶部的温度向中心区域逐渐减小,然而由于所述组合底板的导热速率也向中心逐渐减小,两者之间相互综合,使得所述组合底板能够形成均匀热场,在长晶过程中,不会出现长晶界面过凸或者过凹现象的现在,抑制了长晶缺陷的繁殖,提高整锭的长晶效率。进一步地,所述隔热保温层包括依次层叠的第一软毡层、硬毡层及第二软毡层,所述第二软毡层覆盖所述填充槽的整个内表面,所述第一软毡层的顶部平面覆盖所述填充槽的整个槽口,且与所述基板的顶部平面重合。进一步地,所述第一软毡层、所述硬毡层及所述第二软毡层均包括中间平板部及侧缘部,所述第二软毡层与所述硬毡层的形状相同,所述第二软毡层的所述侧缘部由所述第二软毡层的所述中间平板部的边缘斜向上延伸而成,所述第一软毡层的所述侧缘部由所述第一软毡层的所述中间平板部的边缘向外延伸而成,所述侧缘部朝远离对应的所述平板部的方向厚度逐渐减小为零,且所述侧缘部的末缘与所述填充槽的槽口边缘重合。进一步地,所述第一软毡层和所述第二软毡层的所述中间平板部的厚度一致,且厚度位于1mm至2mm之间,所述硬毡层的所述中间平板部的厚度位于1mm至6mm之间,所述第一软毡层、所述硬毡层及所述第二软毡层的所述中间平板部的厚度之和与所述填充槽的深度一致。进一步地,所述隔热保温层包括依次层叠的第一硬毡层、软毡层及第二硬毡层,所述第二硬毡层覆盖所述填充槽的整个内表面,所述第一硬毡层的顶部平面覆盖所述填充槽的整个槽口,且与所述基板的顶部平面重合。进一步地,所述隔热保温层通过螺纹连接结构固设于所述填充槽的底部。进一步地,所述螺纹连接结构包括若干螺栓,所述螺栓从所述隔热保温层的顶部旋入。进一步地,所述填充槽的深度位于3mm至10mm之间。进一步地,所述填充槽的每个侧壁的倾斜角度相同,且所述填充槽的侧壁相对所述填充槽的底部平面倾斜的角度位于2°至6°之间。附图说明图1为本发明第一实施例中的多晶硅铸锭炉的结构示意图。图2为本发明第一实施例中的组合底板的立体结构分解图。图3为本发明第一实施例中的组合底板的立体结构图。图4为沿图3中a-a线的截面结构示意图。图5为图4中i处的放大结构示意图。图6为本发明第二实施例中的组合底板的截面结构示意图。图7为图6中ii处的放大结构示意图。主要元件符号说明:炉体10坩埚20组合底板30、30a加热器40基板31隔热保温层32、32a填充槽311第一软毡层321硬毡层322第二软毡层323螺栓33第一螺纹孔324第二螺纹孔321第一硬毡层325软毡层326第二硬毡层327如下具体实施方式将结合上述附图进一步说明本发明。具体实施方式为了便于理解本发明,下面将参照相关附图对本发明进行更全面的描述。附图中给出了本发明的若干实施例。但是,本发明可以以许多不同的形式来实现,并不限于本文所描述的实施例。相反地,提供这些实施例的目的是使对本发明的公开内容更加透彻全面。需要说明的是,当元件被称为“固设于”另一个元件,它可以直接在另一个元件上或者也可以存在居中的元件。当一个元件被认为是“连接”另一个元件,它可以是直接连接到另一个元件或者可能同时存在居中元件。本文所使用的术语“垂直的”、“水平的”、“左”、“右”以及类似的表述只是为了说明的目的。除非另有定义,本文所使用的所有的技术和科学术语与属于本发明的
技术领域:
的技术人员通常理解的含义相同。本文中在本发明的说明书中所使用的术语只是为了描述具体的实施例的目的,不是旨在于限制本发明。本文所使用的术语“及/或”包括一个或多个相关的所列项目的任意的和所有的组合。请参阅图1,所示为本发明第一实施例中的多晶硅铸锭炉,包括炉体10及设于所述炉体10内的坩埚20、组合底板30及若干加热器40。所述坩埚20的内部用于生长多晶硅,所述坩埚20设于所述组合底板30的顶部中心位置上。若干所述加热器40分别布置于所述坩埚20的侧围及顶部,用于对所述坩埚20形成热场。请参阅图2至5,所示为本发明第一实施例中的组合底板30,包括基板31及隔热保温层32。所述基板31采用石墨材料制作而成,所述基板31的顶部开设有一填充槽311,所述填充槽311的槽口边缘与所述基板31的顶部边缘重合,所述填充槽311的侧壁呈平滑倾斜状,且所述填充槽311的槽口的面积大于所述填充槽311的底部表面的面积,即所述填充槽311的宽度向底部逐渐减小。所述填充槽311的每个侧壁的倾斜角度相同,且所述填充槽311的侧壁相对所述填充槽311的底部平面倾斜的角度位于2°至6°之间。所述填充槽311的深度位于3mm至10mm之间。在本实施例当中,所述填充槽311的侧壁相对所述填充槽311的底部平面倾斜的角度为5°,所述填充槽311的深度为8mm,即所述填充槽311的槽口平面与所述填充槽311的底板平面之间的距离为8mm。所述隔热保温层32填充于所述填充槽311内,以将所述填充槽311填平,所述隔热保温层32的导热速率远小于所述基板31的导热速率。所述隔热保温层32包括依次层叠的第一软毡层321、硬毡层322及第二软毡层323。其中,所述第二软毡层323覆盖所述填充槽311的整个内表面,所述第一软毡层321的顶部平面覆盖所述填充槽311的整个槽口,且与所述基板31的顶部平面重合。其中,所述第一软毡层321、所述硬毡层322及所述第二软毡层323均包括中间平板部及侧缘部。所述第二软毡层323与所述硬毡层322的形状相同,所述第二软毡层323的所述侧缘部由所述第二软毡层323的所述中间平板部的边缘斜向上延伸而成,所述第一软毡层321的所述侧缘部由所述第一软毡层321的所述中间平板部的边缘向外延伸而成,所述侧缘部朝远离对应的所述平板部的方向厚度逐渐减小为零,且所述侧缘部的末缘与所述填充槽311的槽口边缘重合。其中,所述第一软毡层321和所述第二软毡层323的所述中间平板部的厚度一致,且厚度位于1mm至2mm之间,所述硬毡层322的所述中间平板部的厚度位于1mm至6mm之间,所述第一软毡层321、所述硬毡层322及所述第二软毡层323的所述中间平板部的厚度之和与所述填充槽311的深度一致。在本实施例当中,所述第一软毡层321和所述第二软毡层323的所述中间平板部的厚度均为1.5mm,所述硬毡层322的所述中间平板部的厚度为5mm。进一步地,所述隔热保温层32通过螺纹连接结构固设于所述填充槽311的底部。所述螺纹连接结构包括若干螺栓33,所述隔热保温层32的顶部设有若干第一螺纹孔324,所述第一螺纹孔324贯穿所述隔热保温层32。所述填充槽311的底部设有若干第二螺纹孔321,所述第二螺纹孔321贯穿所述基板31。所述第一螺纹孔321及所述第二螺纹孔321的数量与所述螺栓33的数量一致(本实施例当中为4个),且每个所述第一螺纹孔321对应一个所述第二螺纹孔321。所述螺栓33从所述隔热保温层32的顶部旋入到对应的所述第一螺纹孔324及所述第二螺纹孔321内,以将所述隔热保温层32固定于所述填充槽311的底部。通过采用所述螺纹连接结构来固定所述隔热保温层32,便于所述隔热保温层32的拆装更换。综上,本发明上述实施例当中的组合底板及多晶硅铸锭炉,通过在所述基板31的顶部开设有所述填充槽311,并使所述填充槽311的宽度向底部逐渐减小,然后通过导热速率低的所述隔热保温层32将所述填充槽31填平,使得所述组合底板30填充的所述隔热保温层32的厚度向中心区域逐渐增大,从而使得所述组合底板30的导热速率向中心逐渐减小。当所述坩埚20侧围的所述加热器40对所述组合底板30进行辐射时,虽然会导致所述组合底板30顶部的温度向中心区域逐渐减小,然而由于所述组合底板30的导热速率也向中心逐渐减小,两者之间相互综合,使得所述组合底板30能够形成均匀热场,在长晶过程中,不会出现长晶界面过凸或者过凹现象的现在,抑制了长晶缺陷的繁殖,提高整锭的长晶效率。请查阅图6至图7,所示为本发明第二实施例当中的组合底板30a,本实施例当中的组合底板30a与第一实施例当中的组合底板30大抵相同,不同之处在于,本实施例当中的组合底板30a在第一实施例的基础上:本实施例当中的所述隔热保温层32a与第一实施例当中的隔热保温层32的夹层不同。具体地,所述隔热保温层32a包括依次层叠的第一硬毡层325、软毡层326及第二硬毡层327,所述第二硬毡层327覆盖所述填充槽311的整个内表面,所述第一硬毡层325的顶部平面覆盖所述填充槽311的整个槽口,且与所述基板31的顶部平面重合。其中,所述第一硬毡层325、所述软毡层326及所述第二硬毡层327也均包括中间平板部及侧缘部。所述第二硬毡层327与所述软毡层326的形状相同,所述第二硬毡层327的所述侧缘部由所述第二硬毡层327的所述中间平板部的边缘斜向上延伸而成,所述第一硬毡层325的所述侧缘部由所述第一硬毡层325的所述中间平板部的边缘向外延伸而成,所述侧缘部朝远离对应的所述平板部的方向厚度逐渐减小为零,且所述侧缘部的末缘与所述填充槽311的槽口边缘重合。其中,所述第一硬毡层325和所述第二硬毡层327的所述中间平板部的厚度一致,且厚度位于1mm至6mm之间,所述软毡层326的所述中间平板部的厚度位于1mm至2mm之间,所述第一硬毡层325、所述软毡层326及所述第二硬毡层327的所述中间平板部的厚度之和与所述填充槽311的深度一致。在本实施例当中,所述第一硬毡层325和所述第二硬毡层327的所述中间平板部的厚度均为3mm,所述软毡层326的所述中间平板部的厚度为2mm。以上所述实施例仅表达了本发明的几种实施方式,其描述较为具体和详细,但并不能因此而理解为对本发明专利范围的限制。应当指出的是,对于本领域的普通技术人员来说,在不脱离本发明构思的前提下,还可以做出若干变形和改进,这些都属于本发明的保护范围。因此,本发明专利的保护范围应以所附权利要求为准。当前第1页12