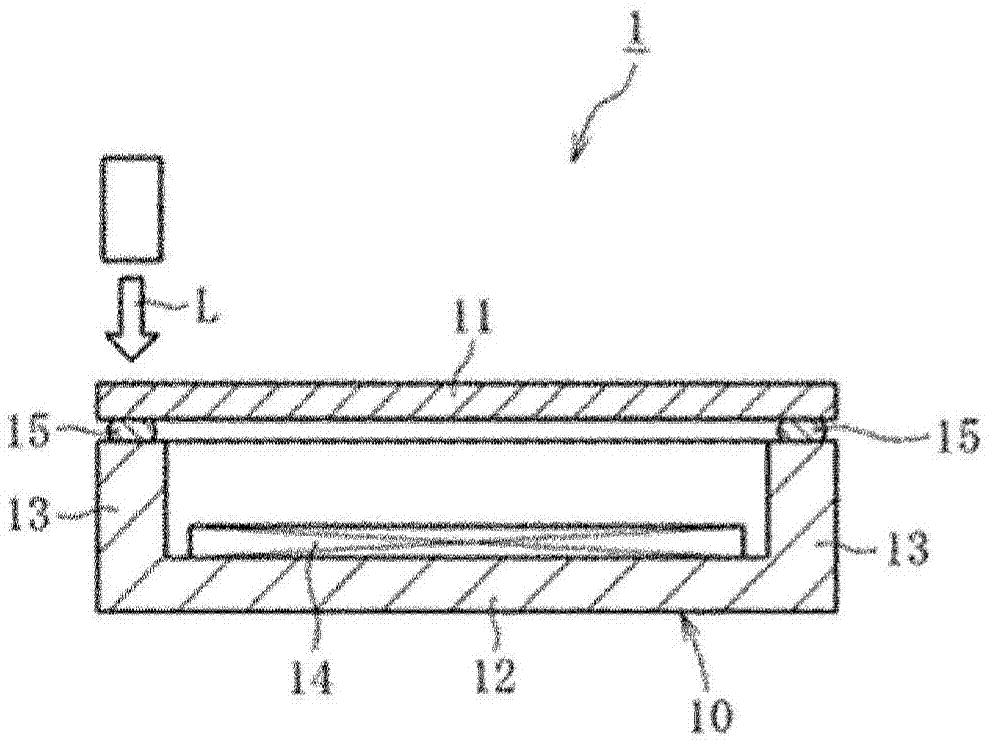
本发明涉及复合陶瓷粉末、密封材料以及复合陶瓷粉末的制造方法,特别涉及与玻璃粉末混合而使用的复合陶瓷粉末、密封材料以及复合陶瓷粉末的制造方法。
背景技术:
:作为密封材料,一般使用包含玻璃粉末和陶瓷粉末的复合粉末材料。该密封材料与树脂系的粘结剂相比,化学耐久性、耐热性优异,而且适于确保气密性。作为密封用玻璃粉末,使用高膨胀的低熔点玻璃、例如pbo系玻璃、bi2o3系玻璃等(参照专利文献1、2等)。另外,密封材料用于低膨胀基板、例如氧化铝基板、玻璃基板等的密封,但在该情况下,若密封材料的热膨胀系数过高,则存在密封后在密封材料层、低膨胀基板中产生不当的残留应变,而在密封材料层、低膨胀基板中产生裂纹,以至于气密泄露等的风险。因此,在被密封物为低膨胀的情况下,使密封材料的热膨胀系数降低变得重要。特别是使用bi2o3系玻璃作为玻璃粉末的情况下,使bi2o3系玻璃的热膨胀系数降低自然会有界限,因此使陶瓷粉末的热膨胀系数降低变得重要。因此,若使用负膨胀的陶瓷粉末,则能够使密封材料的热膨胀系数有效地降低。作为负膨胀的陶瓷粉末,已知铝硅酸锂系(以下,las系)的陶瓷粉末。而且,las系陶瓷粉末的负膨胀是通过析出的β-石英固溶体等的晶粒的负膨胀来体现的。现有技术文献专利文献专利文献1:日本特开昭63-315536号公报专利文献2:日本特开平8-59294号公报技术实现要素:发明要解决的课题然而,若将包含bi2o3系玻璃粉末和las系陶瓷粉末的密封材料进行烧成,则las系陶瓷粉末的表层向bi2o3系玻璃中溶出而扩散,密封材料中的las系陶瓷粉末的结晶量降低,有妨碍密封材料的低膨胀化的风险。本发明鉴于上述情况而完成,其技术课题是,创造低膨胀(特别是负膨胀)且在烧成工序(特别是密封工序)中难以向玻璃中扩散的陶瓷粉末。用于解决课题的手段本发明人等经过潜心努力的结果发现,通过对las系陶瓷粉末添加、混合tio2粉末和/或zro2粉末,能够解决上述技术课题,作为本发明提出。即,本发明的复合陶瓷粉末的特征在于,包含β-锂霞石或β-石英固溶体作为主结晶(析出量最多的结晶)析出的las系陶瓷粉末以及tio2粉末和/或zro2粉末。las系结晶(li2o-al2o3-nsio2)内,β-锂霞石(li2o-al2o3-2sio2)、和在β-锂霞石基础上进一步固溶有sio2的β-石英固溶体(li2o-al2o3-nsio2:n>2)具有负膨胀特性。另一方面,las系结晶(li2o-al2o3-nsio2)内,若sio2固溶到n超过4附近,则向具有正的热膨胀系数的β-锂辉石固溶体转移。因此,本发明涉及的las系陶瓷粉末中,β-锂霞石或β-石英固溶体作为主结晶析出。本发明的复合陶瓷粉末对las系陶瓷粉末添加、混合了tio2粉末和/或zro2粉末。由此,能够维持热膨胀降低效果。能够维持热膨胀降低效果的理由虽然没有实验性地阐明,但推测若对las系陶瓷粉末添加、混合tio2粉末和/或zro2粉末,则las系陶瓷粉末的表层变得难以向玻璃中扩散,因此las系陶瓷粉末的结晶量不降低,能够维持热膨胀降低效果。另外,本发明的复合陶瓷粉末优选las系陶瓷粉末以摩尔%计含有li2o10~35%、al2o310~35%和sio230~80%作为组成。如此一来,正膨胀的β-锂辉石固溶体变得难以析出,因此容易使负膨胀特性降低。另外,本发明的复合陶瓷粉末优选tio2粉末和zro2粉末的总量为0.05~10质量%。另外,本发明的复合陶瓷粉末优选实质上不含玻璃相。如此一来,烧成工序(特别是密封工序)中las系陶瓷粉末的特定成分(特别是li2o)变得难以向玻璃中溶入,因此玻璃变得不易失透,另外容易维持密封材料的热膨胀系数。在此,有无玻璃相可以用x射线衍射装置等来判定。例如,若结晶化度为95%以上,则可以判定实质上不含玻璃相。需要说明的是,“结晶化度”是指,通过利用粉末法测定x射线衍射,从而分别算出相当于非晶质的质量的晕的面积、和相当于结晶的质量的峰的面积后,通过[峰的面积]×100/[峰的面积+晕的面积](%)的算是求出的值。若以固相反应制作las系陶瓷粉末,则能够得到实质上不含玻璃相的las系陶瓷粉末。另一方面,若以熔融法制作las系陶瓷粉末,则在las系陶瓷粉末中残存玻璃相。需要说明的是,熔融法是,使原料配合料暂时熔解而得到玻璃熔液后,将得到的玻璃熔液冷却、粉碎,根据需要进行热处理,来制作las系陶瓷粉末的方法。本发明的密封材料的特征在于,在包含玻璃粉末和陶瓷粉末的密封材料中,作为陶瓷粉末,包含β-锂霞石或β-石英固溶体作为主结晶析出的las系陶瓷粉末以及tio2粉末和/或zro2粉末。在此,在本发明的密封材料中,las系陶瓷粉末与tio2粉末和/或zro2粉末的混合没有必要在与玻璃粉末的混合前进行,可以与玻璃粉末的混合同时进行。本发明的复合陶瓷粉末的制造方法的特征在于,具有:将原料配合料烧成,通过固相反应得到β-锂霞石或β-石英固溶体作为主结晶析出的烧结体的工序;将该烧结体粉碎,得到las系陶瓷粉末的工序;将得到的las系陶瓷粉末以及tio2粉末和/或zro2粉末混合,得到复合陶瓷粉末的工序。本发明的复合陶瓷粉末的制造方法具有将原料配合料烧成并通过固相反应得到烧结体的工序,若以固相反应制作烧结体,则在烧结体中不会残留玻璃相。其结果是,密封时las系陶瓷粉末的特定成分(特别是li2o)难以向玻璃中溶入,因此密封材料变得不易失透,而且容易使密封材料的热膨胀系数降低。另外,本发明的复合陶瓷粉末的制造方法优选在las系陶瓷粉末的li、al和si的导入原料的全部或一部分中使用包含li、al和si的预备烧结体的粉碎物。如此一来,析出结晶的均质化成为可能,能够降低las系陶瓷粉末的特性变动。另外,本发明的复合陶瓷粉末的制造方法优选在las系陶瓷粉末的li、al和si的导入原料的全部或一部分中使用氧化物原料、氢氧化物原料、碳酸盐原料中的任意者。另外,本发明的复合陶瓷粉末的制造方法优选:为了得到以摩尔%计含有li2o10~35%、al2o310~35%和sio230~80%作为组成的las系陶瓷粉末,将原料配合料进行调合。另外,本发明的复合陶瓷粉末的制造方法优选:将原料配合料以1000~1450℃烧成,通过固相反应得到β-锂霞石或β-石英固溶体作为主结晶析出的烧结体。如此一来,能够在烧结体中不残存玻璃相地使las系结晶适当析出。另外,本发明的复合陶瓷粉末的制造方法优选:按照las系陶瓷粉末中实质上不含微裂纹的方式将烧结体粉碎。如此一来,las系陶瓷粉末的粒径变小,因此能够适宜地应用于密封材料层的厚度小的气密封装体。需要说明的是,若las系陶瓷粉末的平均粒径d50小于10μm,则成为las系陶瓷粉末中实质上不含微裂纹的状态。附图说明图1为用于说明本发明的气密封装体的一实施方式的示意剖视图。图2为表2中记载的试样no.3(粉碎前)的las系陶瓷粉末的电子显微镜照片。图3为表2中记载的试样no.3(粉碎后)的las系陶瓷粉末的电子显微镜照片。图4为表2中记载的试样no.4(粉碎前)的las系陶瓷粉末的电子显微镜照片。图5为表2中记载的试样no.4(粉碎后)的las系陶瓷粉末的电子显微镜照片。具体实施方式本发明涉及的las系陶瓷粉末优选β-锂霞石或β-石英固溶体作为主结晶析出,除此以外的结晶不析出,但只要不明显损害本发明的效果,除此以外的结晶可以少量析出。本发明涉及的las系陶瓷粉末优选以摩尔%计含有li2o10~35%(优选16~30%)、al2o310~35%(优选16~30%)和sio230~80%(优选40~70%)作为组成。若陶瓷粉末的组成成为上述范围以外,则β-锂霞石或β-石英固溶体难以作为主结晶析出,并且若粒径变小,则难以维持低膨胀特性。需要说明的是,除了上述成分以外,还可以将烧结助剂等其它成分以10%以下的范围导入。本发明的复合陶瓷粉末中,tio2粉末与zro2粉末的含量优选以总量计为0.05~10质量%、特别是0.1~4质量%。tio2粉末与zro2粉末的各自的含量优选为0.05~10质量%、特别是0.1~4质量%。若tio2粉末与zro2粉末的含量过少,则密封工序中las系陶瓷粉末的表层变得容易向玻璃中溶出、扩散。其结果是,密封材料中的las系陶瓷粉末的结晶量减少,密封材料的热膨胀系数容易上升。另一方面,若tio2粉末与zro2粉末的含量过多,则tio2粉末与zro2粉末自身的热膨胀系数反映到密封材料的热膨胀系数中,密封材料的热膨胀系数容易上升。复合陶瓷粉末的平均粒径d50优选为20μm以下、10μm以下、7μm以下、5μm以下、特别是1~3μm。另外,复合陶瓷粉末的最大粒径dmax优选为50μm以下、30μm以下、20μm以下、15μm以下、特别是2~10μm。一般来说,陶瓷粉末的粒径越小、比表面积越大,则密封工序中陶瓷粉末的表层越容易向玻璃中溶入。因此,复合陶瓷粉末的粒径越小、比表面积越大,则本发明的效果越相对地变大。在此,“平均粒径d50”是指用激光衍射法测定的值,表示在用激光衍射法测定时的体积基准的累积粒度分布曲线中,其累积量从粒子小的一侧开始累积为50%的粒径。“最大粒径dmax”是指用激光衍射法测定的值,表示在用激光衍射法测定时的体积基准的累积粒度分布曲线中,其累积量从粒子小的一侧开始累积为99%的粒径。对于本发明的复合陶瓷粉末而言,30~300℃时的热膨胀系数优选为负(低于0×10-7/℃)、-1×10-7/℃以下、-3×10-7/℃以下、-6×10-7/℃以下、特别是-20×10-7/℃以上且-9×10-7/℃以下。若30~300℃时的热膨胀系数过高,则难以使密封材料的热膨胀系数充分降低。需要说明的是,“30~300℃时的热膨胀系数”可以用tma(推杆式热膨胀系数测定)测定。需要说明的是,虽然难以直接测定复合陶瓷粉末的热膨胀系数,但若以规定体积比将玻璃粉末与复合陶瓷粉末混合、烧成,并测定所得到的烧成体的热膨胀系数,则能够通过计算求得复合陶瓷粉末单体的热膨胀系数。本发明的密封材料的特征在于,在包含玻璃粉末与陶瓷粉末的密封材料中,作为陶瓷粉末,包含β-锂霞石或β-石英固溶体作为主结晶析出的las系陶瓷粉末以及tio2粉末和/或zro2粉末。本发明的密封材料的技术特征与本发明的复合陶瓷粉末的技术特征的一部分重复,对于该重复部分省略详细说明。本发明的密封材料中,复合陶瓷粉末的含量优选为1~45体积%、10~45体积%、15~40体积%、特别是20~35体积%。若复合陶瓷粉末的含量过多,则玻璃粉末的含量相对地变少,难以确保所期望的流动性及热稳定性。需要说明的是,若复合陶瓷粉末的含量过少,则复合陶瓷粉末的添加效果不足。本发明的密封材料中,可以添加除las系陶瓷粉末、tio2粉末、zro2粉末以外的陶瓷粉末,例如,可以包含选自堇青石、锆石、氧化铝、莫来石、硅锌矿、磷酸锆、磷酸钨酸锆、钨酸锆等中的一种或两种以上。但是,它们的含量以总量计优选为0~15体积%、特别是0体积%以上且小于10体积%。本发明的密封材料中,作为玻璃粉末,可以使用各种玻璃粉末。例如,bi2o3系玻璃、v2o5系玻璃、sno系玻璃在低熔点特性的方面适宜,bi2o3系玻璃在热稳定性、耐水性的方面特别优选。在此,“~系玻璃”是指,含有明示的成分作为必需成分,且明示的成分的含量为25摩尔%以上、优选为30摩尔%以上、更优选为35摩尔%以上的玻璃。需要说明的是,从环境角度出发,玻璃粉末优选在玻璃组成中实质上不含pbo(小于0.1摩尔%)。bi2o3系玻璃优选以摩尔%计含有bi2o328~60%、b2o33~37%和zno1~30%作为玻璃组成。以下说明按照上述方式限定各成分的含有范围的理由。需要说明的是,在玻璃组成范围的说明中,%显示是指摩尔%。bi2o3是用于使软化点降低的主要成分,其含量优选为28~60%、33~55%、特别是35~45%。若bi2o3的含量过少,则软化点变得过高,流动性变得容易降低。另一方面,若bi2o3的含量过多,则烧成时玻璃变得容易失透,因该失透,流动性变得容易降低。b2o3是作为玻璃形成成分所必需的成分,其含量优选为1~37%、特别是3~30%。若b2o3的含量过少,则难以形成玻璃网络,因此烧成时玻璃变得容易失透。另一方面,若b2o3的含量过多,则玻璃的粘性变高,流动性变得容易降低。zno是提高耐失透性的成分,其含量优选为1~30%、3~25%、5~22%、特别是9~20%。若zno的含量成为上述范围外,则玻璃组成的成分平衡受损,耐失透性变得容易降低。除了上述成分以外,例如还可以添加以下的成分。sio2是提高耐水性的成分,具有使软化点上升的作用。因此,sio2的含量优选为0~5%、0~3%、0~2%、特别是0~1%。另外,若sio2的含量过多,则烧成时玻璃变得容易失透。al2o3是提高耐水性的成分,其含量优选为0~10%、0~5%、特别是0.1~2%。若al2o3的含量过多,则有软化点不当地上升的风险。li2o、na2o和k2o是使耐失透性降低的成分。因此,li2o、na2o和k2o的各自的含量优选为0~5%、0~3%、特别是0%以上且低于1%。mgo、cao、sro和bao是提高耐失透性的成分,是使软化点上升的成分。因此,mgo、cao、sro和bao的含量分别为0~20%、0~10%、特别是0~5%。为了降低bi2o3系玻璃的软化点,需要在玻璃组成中大量导入bi2o3,但若使bi2o3的含量增加,则烧成时玻璃变得容易失透,因该失透而流动性变得容易降低。特别是若bi2o3的含量成为30%以上,则该倾向变得显著。作为其对策,若添加cuo,则即使bi2o3的含量为30%以上,也能有效地抑制玻璃的失透。若进一步添加cuo,则能够提高激光密封时的激光吸收特性。cuo的含量优选为0~40%、5~35%、10~30%、特别是15~25%。若cuo的含量过多,则玻璃组成的成分平衡受损,反而耐失透性变得容易降低。fe2o3是提高耐失透性和激光吸收特性的成分,其含量优选为0~10%、0.1~5%、特别是0.5~3%。若fe2o3的含量过多,则玻璃组成的成分平衡受损,反而耐失透性变得容易降低。sb2o3是提高耐失透性的成分,其含量优选为0~5%、特别是0~2%。若sb2o3的含量过多,则玻璃组成的成分平衡受损,反而耐失透性变得容易降低。玻璃粉末的平均粒径d50优选为小于15μm、0.5~10μm、特别是1~5μm。玻璃粉末的平均粒径d50越小,则玻璃粉末的软化点越降低。本发明的密封材料除了玻璃粉末与陶瓷粉末以外,还可以导入其它粉末材料。例如,为了提高激光吸收特性,可以包含1~15体积%的mn-fe-al系氧化物、碳、mn-fe-cr系氧化物等激光吸收剂。另外可以导入玻璃珠、间隔物等。本发明的密封材料优选用于激光密封(基于照射激光的密封)。在进行激光密封的情况下,若减小密封材料层的厚度,则能够显著地提高激光密封性。另外,若减小密封材料层的厚度,则能够有助于气密封装体的低厚度化、小型化。为了减小密封材料层的厚度,必须减小密封材料中的陶瓷粉末的粒径。但是,一般来说,若陶瓷粉末的粒径变小,具体来说若小到20μm以下、特别是小于10μm,则晶界的微裂纹变少,密封材料的热膨胀系数上升。其结果是,难以使密封材料的热膨胀系数适当地降低。另一方面,对于本发明的密封材料而言,即使复合陶瓷粉末的粒径小,也能维持低膨胀特性。因此,本发明的密封材料适合激光密封。本发明的密封材料可以以粉末状态供使用,但是若与媒液均匀地混炼并浆料化则变得容易操作,而优选。媒液通常包含溶剂和树脂。树脂是以调整浆料的粘性为目的而添加的。另外,还可以根据需要添加表面活性剂、增稠剂等。制作的浆料使用分配器、丝网印刷机等涂布机被涂布于被密封物的表面。作为树脂,可以使用丙烯酸酯(丙烯酸树脂)、乙基纤维素、聚乙二醇衍生物、硝基纤维素、聚甲基苯乙烯、聚碳酸乙烯酯、甲基丙烯酸酯等。尤其丙烯酸酯、硝基纤维素由于热分解性良好,因而优选。作为溶剂,可以使用n,n′-二甲基甲酰胺(dmf)、α-萜品醇、高级醇、γ-丁内酯(γ-bl)、四氢化萘、丁基卡必醇乙酸酯、乙酸乙酯、乙酸异戊酯、二乙二醇单乙醚、二乙二醇单乙醚乙酸酯、苯甲醇、甲苯、3-甲氧基-3-甲基丁醇、水、三乙二醇单甲醚、三乙二醇二甲醚、二丙二醇单甲醚、二丙二醇单丁醚、三丙二醇单甲醚、三丙二醇单丁醚、碳酸丙烯酯、二甲基亚砜(dmso)、n-甲基-2-吡咯烷酮等。尤其α-萜品醇为高粘性,树脂等的溶解性也良好,因此优选。本发明的密封材料激光密封时的流动性高,且热膨胀系数低,因此能够适宜地应用于气密封装体的封装体基体与玻璃盖的激光密封。本发明的气密封装体的特征在于,在封装体基体与玻璃盖隔着密封材料层而气密密封的气密封装体中,该密封材料层为密封材料的烧结体,该密封材料为上述密封材料。以下,对于本发明涉及的气密封装体进行详细说明。封装体基体优选具有基部和设于基部上的框部。如此一来,容易在封装体基体的框部内收纳传感器元件等内部元件。封装体基体的框部优选沿着封装体基体的外侧端缘区域以边框状形成。如此一来,能够扩大作为器件发挥功能的有效面积。另外容易将传感器元件等内部元件收纳于封装体基体内的空间,且布线接合等也变得容易进行。框部的顶部的配设有密封材料层的区域的表面的表面粗糙度ra优选小于1.0μm。若该表面的表面粗糙度ra变大,则激光密封的精度变得容易降低。在此,“表面粗糙度ra”例如可以通过触针式或非接触式的激光膜厚计、表面粗糙度计来测定。框部的顶部的宽度优选为100~7000μm、200~6000μm、特别是300~5000μm。若框部的顶部的宽度过窄,则密封材料层与框部的顶部的位置对准变得困难。另一方面,若框部的顶部的宽度过宽,则作为器件发挥功能的有效面积变小。封装体基体优选为玻璃陶瓷、氮化铝、氧化铝中的任意者、或它们的复合材料(例如,将氮化铝与玻璃陶瓷一体化的复合材料)。玻璃陶瓷容易与密封材料层形成反应层,因此以激光密封能够确保牢固的密封强度。而且能够容易地形成导热孔,因此能够适当地防止气密封装体温度过度上升的情况。氮化铝和氧化铝的放热性良好,因此能够适当防止气密封装体的温度过度上升的情况。玻璃陶瓷、氮化铝、氧化铝优选分散有黑色颜料(以分散有黑色颜料的状态烧结而成)。如此一来,封装体基体能够吸收透过密封材料层的激光。其结果是激光密封时封装体基体的与密封材料层接触的地方被加热,因此能够促进在密封材料层与封装体基体的界面形成反应层。分散有黑色颜料的封装体基体优选具有吸收所要照射的激光的性质,例如,厚度0.5mm、所要照射的激光的波长(808nm)下的总光线透射率优选为10%以下(期望为5%以下)。如此一来,在封装体基体与密封材料层的界面,密封材料层的温度变得容易上升。封装体基体的基部的厚度优选为0.1~2.5mm、特别是0.2~1.5mm。由此,能够实现气密封装体的薄型化。封装体基体的框部的高度、即从封装体基体减去基部的厚度的高度优选为100~2500μm、特别是200~1500μm。如此一来,容易适当地收纳内部元件,并且实现气密封装体的薄型化。作为玻璃盖,可以使用各种玻璃。例如,可以使用无碱玻璃、碱硼硅酸玻璃、碱石灰玻璃。需要说明的是,玻璃盖可以是将多张玻璃板贴合的层叠玻璃。可以在玻璃盖的内部元件侧的表面形成功能膜,也可以在玻璃盖的外侧的表面形成功能膜。尤其作为功能膜优选防反射膜。由此,能够降低在玻璃盖的表面反射的光。玻璃盖的厚度优选为0.1mm以上、0.15~2.0mm、特别是0.2~1.0mm。若玻璃盖的厚度小,则气密封装体的强度容易降低。另一方面,若玻璃盖的厚度大,则难以实现气密封装体的薄型化。密封材料层具有通过吸收激光而软化变形,在封装体基体的表层形成反应层,将封装体基体与玻璃盖气密一体化的功能。玻璃盖与密封材料层的热膨胀系数差优选小于50×10-7/℃、小于40×10-7/℃、特别是30×10-7/℃以下。若该热膨胀系数差过大,则在密封部分残留的应力不当地变高,气密封装体的气密可靠性容易降低。密封材料层优选按照与框部的接触位置从框部的顶部的内侧端缘分离的方式形成,并且按照从框部的顶部的外侧端缘分离的方式形成,进一步优选在距框部的顶部的内侧端缘分离50μm以上、60μm以上、70~2000μm、特别是80~1000μm的位置形成。若框部的顶部的内侧端缘与密封材料层的间距过短,则在激光密封时,因局部加热产生的热难以逃散,因此冷却过程中玻璃盖容易破损。另一方面,若框部的顶部的内侧端缘与密封材料层的间距过长,则气密封装体的小型化变得困难。另外密封材料层优选在距框部的顶部的外侧端缘分离50μm以上、60μm以上、70~2000μm、特别是80~1000μm的位置形成。若框部的顶部的外侧端缘与密封材料层的间距过短,则在激光密封时,因局部加热产生的热难以逃散,因此冷却过程中玻璃盖容易破损。另一方面,若框部的顶部的外侧端缘与密封材料层的间距过长,则气密封装体的小型化变得困难。密封材料层优选按照与玻璃盖的接触位置距玻璃盖的端缘分离50μm以上、60μm以上、70~1500μm、特别是80~800μm分离的方式形成。若玻璃盖的端缘与密封材料层的间距过短,则在激光密封时,在玻璃盖的端缘区域,玻璃盖的内部元件侧的表面与外侧的表面的表面温度差变大,玻璃盖容易破损。密封材料层优选在框部的顶部的宽度方向的中心线上形成、即在框部的顶部的中央区域形成。如此一来,在激光密封时,因局部加热产生的热容易逃散,因此玻璃盖变得难以破损。需要说明的是,在框部的顶部的宽度充分大的情况下,可以不在框部的顶部的宽度方向的中心线上形成密封材料层。密封材料层的平均厚度优选小于8.0μm、特别是1.0μm以上且小于7.0μm。密封材料层的平均厚度越小,则气密封装体内的α射线放出率越少,因此容易防止内部元件的软错误(softerror)。密封材料层的平均厚度越小,则激光密封的精度越提高。此外,密封材料层与玻璃盖的热膨胀系数不匹配时,还可以降低激光密封后在密封部分残留的应力。需要说明的是,作为按照上述方式限制密封材料层的平均厚度的方法,可以举出薄薄地涂布密封材料浆料的方法、对密封材料层的表面进行研磨处理的方法。密封材料层的最大宽度优选为1μm以上且2000μm以下,特别是100μm以上且1500μm以下。若窄化密封材料层的最大宽度,则容易使密封材料层从框部的端缘分离,因此容易降低激光密封后在密封部分残留的应力。此外,能够窄化封装体基体的框部的宽度,能够扩大作为器件发挥功能的有效面积。另一方面,若密封材料层的最大宽度过窄,则在密封材料层施加大的剪切应力的情况下,密封材料层容易主体破坏。进而激光密封的精度容易降低。以下,参照附图对本发明进行说明。图1为用于说明本发明涉及的气密封装体的一实施方式的示意剖视图。由图1可知,气密封装体1具备封装体基体10和玻璃盖11。另外,封装体基体10具有基部12和在基部12的外周端缘上的边框状的框部13。而且,在封装体基体10的被框部13包围的空间内收纳有内部元件14。需要说明的是,在封装体基体10内,形成有将内部元件14与外部电连接的电布线(未图示)。密封材料层15是密封材料的烧结体,该密封材料包含玻璃粉末和本发明的复合陶瓷粉末,实质上不含激光吸收材。另外,密封材料层15在封装体基体10的框部13的顶部与玻璃盖11的内部元件14侧的表面之间,遍布框部13的顶部的全周配设。密封材料层15的宽度小于封装体基体10的框部13的顶部的宽度,而且从玻璃盖11的端缘分离。而且密封材料层15的平均厚度小于8.0μm。上述气密封装体1可以按照以下方式制作。首先按照密封材料层15与框部13的顶部相接的方式,将预先形成了密封材料层15的玻璃盖11载置于封装体基体10上。接着,一边使用按压夹具按压玻璃盖11,一边从璃盖11侧沿着密封材料层15照射从激光照射装置射出的激光l。由此,密封材料层15软化流动,与封装体基体10的框部13的顶部的表层发生反应,从而封装体基体10与玻璃盖11被气密一体化,形成气密封装体1的气密结构。本发明的复合陶瓷粉末的制造方法的特征在于,具有:将原料配合料烧成,通过固相反应得到β-锂霞石或β-石英固溶体作为主结晶析出的烧结体的工序;将该烧结体粉碎,得到las系陶瓷粉末的工序;将得到的las系陶瓷粉末以及tio2粉末和/或zro2粉末混合,得到复合陶瓷粉末的工序。本发明的复合陶瓷粉末的制造方法的技术特征与本发明的复合陶瓷粉末和密封材料的技术特征一部分重复,对于该重复部分省略详细说明。作为las系陶瓷粉末的li、al和si的导入原料,可以使用各种原料,其中,优选使用包含li、al和si的预备烧结体的粉碎物。若对于导入原料的全部或一部分进行预备烧结,则析出结晶的均质化成为可能,能够降低las系陶瓷粉末的特性变动。另外,除了包含li、al和si的预备烧结体的粉碎物以外,还可以使用氧化物原料、氢氧化物原料、碳酸盐原料等。需要说明的是,期望las系陶瓷粉末的原料配合料通过球磨等以湿式粉碎混合。如此一来,原料配合料的均匀性提高,因此能够促进固相反应。las系陶瓷粉末的原料配合料的烧成可以用电炉、煤气炉等进行。原料配合料的烧成温度优选为1000~1450℃、特别是1250~1400℃。若烧成温度过低,则las系陶瓷粉末的析出结晶量容易变少。另一方面,若烧成温度过高,则烧结体的一部分玻璃化,容易在烧结体中残存玻璃相。另外由于烧结体的烧结度变高,因而烧结体的粉碎变得困难。原料配合料的烧成时间优选为15~40小时。若烧成时间过短,则las系陶瓷粉末的析出结晶量容易变少。另一方面,若烧成时间过长,则烧结体的烧结度变高,因而烧结体的粉碎变得困难。烧结体的粉碎可以用球磨机、颚式破碎机、喷磨机、盘磨机、光谱磨机(spectromill)、研磨机、混合磨机等进行,从运行成本和粉碎效率的观点出发,优选使用球磨机,以湿式或干式进行。烧结体的粉碎粒度优选调整到实质上不含微裂纹的程度。如此一来,las系陶瓷粉末的粒径变小,因此能够适宜地应用于密封材料层的厚度小的气密封装体。将烧结体粉碎后,优选根据需要进行筛分或空气分级,调整las系陶瓷粉末的粒径。为了均匀化,las系陶瓷粉末以及tio2粉末和/或zro2粉末的混合优选利用球磨机等以湿式进行。实施例以下,基于实施例,对本发明进行详细说明。需要说明的是,以下的实施例仅为例示。本发明不受以下的实施例任何限定。(预备烧结体的粉碎物的制作)将表1中记载的原料放入内容积3.6l的氧化铝制釜内,以湿式粉碎混合12小时,制作原料配合料。需要说明的是,粉碎混合时,作为粉碎球使用φ3.0mm、3000g的氧化锆、作为分散剂使用600ml的醇。【表1】(质量%)ab氢氧化铝4433碳酸锂2317氧化硅3350接着,将原料配合料干燥、压碎,利用电炉以800℃保持8小时后,以1350℃烧成16小时。需要说明的是,将从室温至800℃的升温速度设为5℃/分钟,将从800℃至1350℃的升温速度设为1℃/分钟,将从1350℃开始的降温速度设为1℃/分钟。进而,对于得到的烧结体,干式粉碎和湿式粉碎到平均粒径d50成为1.0μm为止后,以350目的试验筛分级,制作预备烧结体的粉碎物a、b。(las系陶瓷粉末的制作)将表2中记载的原料配合料放入内容积3.6l的氧化铝制釜内,以湿式粉碎混合12小时,制作原料配合料。需要说明的是,粉碎混合时,作为粉碎球使用φ3.0mm、3000g的氧化锆,作为分散剂使用600ml的醇。【表2】接着,将原料配合料干燥、压碎,利用电炉以800℃保持8小时后,以1350℃烧成16小时。需要说明的是,将从室温至800℃的升温速度设为5℃/分钟,将从800℃至1350℃的升温速度设为1℃/分钟,将从1350℃开始的降温速度设为1℃/分钟。接着,对得到的烧结体,干式粉碎到平均粒径d50成为25μm为止。图2为表2中记载的试样no.3(粉碎前)的las系陶瓷粉末的电子显微镜照片。图3为表2中记载的试样no.3(粉碎后)的las系陶瓷粉末的电子显微镜照片。图4为表2中记载的no.4(粉碎前)的las系陶瓷粉末的电子显微镜照片。图5为表2中记载的试样no.4(粉碎后)的las系陶瓷粉末的电子显微镜照片。观察图2~5可知,通过粉碎,试样no.3、4的las系陶瓷粉末中实质上不含微裂纹。其后,对于表2中记载的las系陶瓷粉末,添加表2中记载的陶瓷粉末(tio2粉末和/或zro2粉末),进而以干式和湿式粉碎混合到复合陶瓷粉末的平均粒径d50成为1.0μm为止。其后,将得到的复合陶瓷粉末用350目的试验筛分级,得到试样no.1~6。将试样no.1~6的全体组成示于表2。(bi2o3系玻璃粉末的制作)为了得到以摩尔%计含有bi2o336%、b2o328%、zno4%、bao4%、cuo25%、fe2o31%和al2o31%作为玻璃组成的bi2o3系玻璃粉末,准备调合了各种氧化物、碳酸盐等原料的玻璃配合料,将其放入铂坩埚中以1000~1100℃熔融2小时。接着,将得到的玻璃熔液利用水冷辊成形为薄片状。最后,将薄片状的玻璃利用球磨机粉碎后进行空气分级,得到bi2o3系玻璃粉末。需要说明的是,bi2o3系玻璃粉末的平均粒径d50为2.5μm,最大粒径dmax为10μm,30~300℃时的热膨胀系数为104×10-7/℃。(密封材料的制作)将上述bi2o3系玻璃粉末与表2中记载的陶瓷粉末按照以体积比计为75∶25的方式混合,得到密封材料。通过将得到的密封材料以500℃烧成,从而得到致密的烧成体后,将该烧成体加工成规定形状,制作tma(推杆式热膨胀系数测定)用的测定试样。使用该测定试样,以30~300℃的温度范围进行tma。基于得到的密封材料的热膨胀系数,算出复合陶瓷粉末的热膨胀系数α。将其结果示于表2。由表2可知,试样no.1~3由于包含tio2粉末和/或zro2粉末,因而是负膨胀。另一方面,试样no.4~6由于不含tio2粉末与zro2粉末,因而是正膨胀或零膨胀。(利用熔融法制作的陶瓷粉末的参考例)将表3中记载的原料配合料放入内容积3.6l的氧化铝制釜内,以湿式粉碎混合12小时。需要说明的是,粉碎混合时,作为粉碎球使用φ3.0mm、3000g的氧化锆,作为分散剂使用600ml的醇。【表3】(质量%)氢氧化铝44碳酸锂23氧化硅33接着,将原料配合料放入铂坩埚中,以1580℃熔解1小时后,将得到的玻璃熔液流出到成形辊(双辊)之间进行冷却,且成形为膜状。接着,将得到的膜用球磨机粉碎,用250目可通过的筛进行分级后,用电炉以800℃保持12小时。需要说明的是,将从室温至800℃的升温速度设为5℃/分钟,将从800℃开始的降温速度设为1℃/分钟。进而,将得到的烧结体以干式和湿式粉碎到成为平均粒径d50=1.0μm后,用350目的试验筛分级,得到las系陶瓷粉末。最后,将上述bi2o3系玻璃粉末与las系陶瓷粉末按照以体积比计为75∶25的方式混合,得到密封材料。将得到的密封材料以500℃烧成,从而得到致密的烧成体后,将该烧成体加工成规定形状,制作tma用的测定试样。使用该测定试样,以30~300℃的温度范围进行tma。基于得到的密封材料的热膨胀系数,算出las系陶瓷粉末的热膨胀系数。其结果是,las系陶瓷粉末的热膨胀系数为10×10-7/℃。符号说明1气密封装体10封装体基体11玻璃盖12基部13框部14内部元件15密封材料层l激光当前第1页12