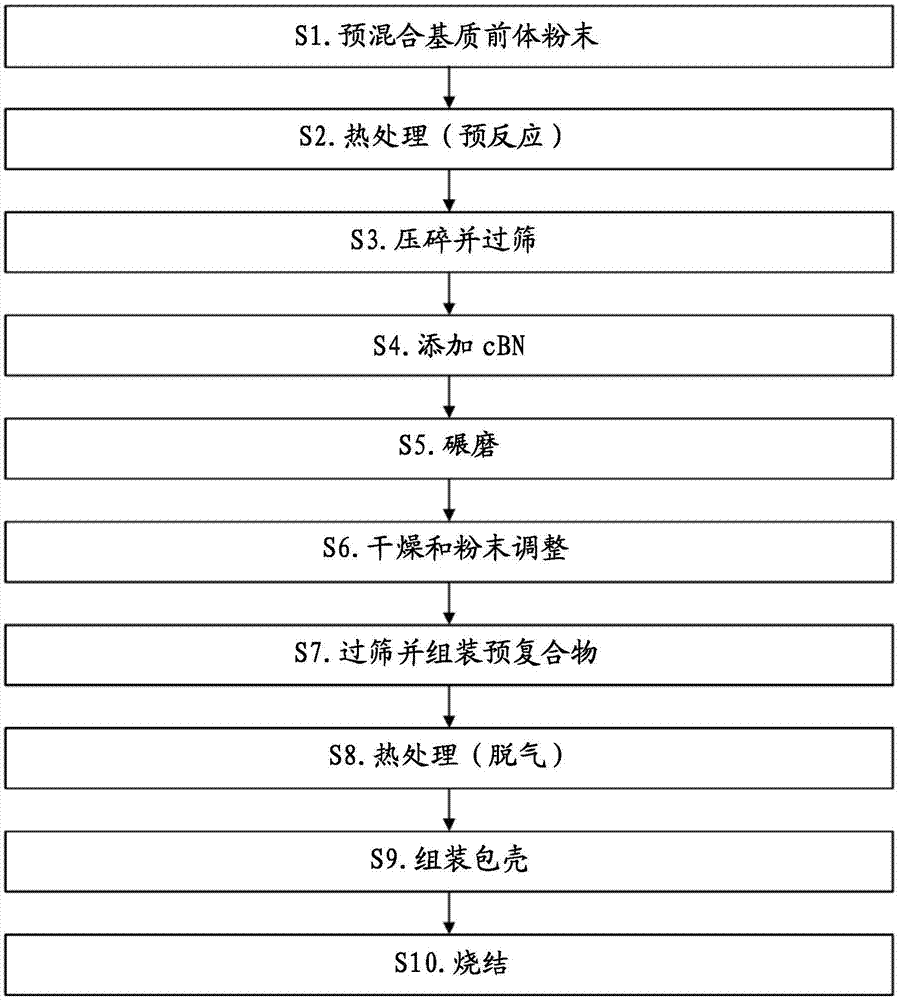
本发明涉及烧结聚晶立方氮化硼材料领域,以及制造这种材料的方法。
背景技术:
:聚晶超硬材料,如聚晶金刚石(pcd)和聚晶立方氮化硼(pcbn),可用于各种工具,用于切割、机加工、钻孔或降解硬质或磨蚀性材料,如岩石、金属、陶瓷、复合材料和含木材料。磨料压块广泛用于切割、铣削、磨碎(grinding)、钻孔和其它磨削(abrasive)操作。它们通常含有分散在第二相基质中的超硬磨料颗粒。基质可以是金属或陶瓷或金属陶瓷。超硬磨料颗粒可以是金刚石、立方氮化硼(cbn)、碳化硅或氮化硅等。在通常使用的高压和高温压实制造工艺期间,这些颗粒可以彼此结合,从而形成聚晶物质,或者可以通过第二相材料的基质结合以形成烧结的聚晶物体。此类物体通常被称为聚晶金刚石或聚晶立方氮化硼,其中它们分别包含金刚石或cbn作为超硬磨料。美国专利us4,334,928教导了一种用于工具的烧结压块,其基本上由20至80体积%的立方氮化硼组成;以及余量是至少一种基质化合物材料的基质,所述基质化合物材料选自周期表的iva或va过渡金属的碳化物、氮化物、碳氮化物、硼化物和硅化物、它们的混合物和它们的固溶体化合物。所述基质在烧结体中形成连续的粘合结构,其中高压氮化硼散布在连续基质中。该专利中概述的方法均涉及使用机械研磨/混合技术(如球磨,研钵等)来合并所需材料。烧结的聚晶物体可以通过将它们形成于基底上而被“支撑”。可用于形成合适基底的粘结碳化钨是由分散在例如钴基质中的碳化物颗粒形成,通过将碳化钨颗粒/晶粒和钴混合在一起然后加热固化。为了形成具有超硬材料层(如pcd或pcbn)的切割元件,在难熔金属外壳(例如铌外壳)中,将金刚石颗粒或晶粒或cbn晶粒放置在粘结碳化钨物体附近,并且经受高压和高温使得金刚石晶粒或cbn晶粒之间发生晶粒间键合,从而形成聚晶超硬金刚石或聚晶cbn层。在一些情况下,基底可以在附着到超硬材料层之前完全固化,而在其它情况下,基底可以是生坯态(未完全固化)。在后一种情况下,基底可在hthp烧结工艺期间完全固化。基底可以是粉末形式,并且可以在用于烧结超硬材料层的烧结工艺期间固化。图1显示了用于制造烧结pcbn材料的示例性方法。以下编号对应于图1的编号:s1.将基质前体粉末预混合。基质前体粉末的实例包括钛和铝的碳化物和/或氮化物。基质前体粉末的典型平均颗粒尺寸为1至10μm。s2.将基质前体粉末在超过1000℃下热处理至少一小时,以引发基质前体颗粒之间的预反应从而形成“饼状物”(cake)。s3.将饼状物压碎并过筛以获得所需粒级的颗粒。s4.将平均颗粒尺寸为0.5至15μm的立方氮化硼(cbn)颗粒添加到过筛后的基质前体粉末中。s5.将所得混合粉末碾磨以将基质前体粉末破碎至期望尺寸(典型为50至700nm)并使基质前体粉末与cbn颗粒紧密混合。该过程可能需要数小时,并且涉及使用诸如碳化钨球的研磨介质。s6.将得到的研磨粉末在真空或低压下在60℃以上干燥以除去溶剂,随后通过缓慢地使氧气进入系统以钝化金属表面(如铝)来进行调整。s7.将干燥的粉末过筛并制备预复合组合件。s8.预复合组合件在700℃以上进行热处理,以去除任何吸附的水或气体。s9.将脱气的预复合组合件组装到适合于烧结的包壳中。s10.在至少1250℃和至少4gpa的高压高温(hpht)工艺中烧结包壳以形成烧结的pcbn材料。整个工艺非常耗时并且在商业规模上可能需要多达五天。在碾磨(attritionmill)过程期间,粉末可从研磨介质吸取杂质。图2是烧结pcbn材料的显微照片,其中用碳化钨球进行碾磨。白色颗粒(其实例以黑色圆圈突出显示)是碳化钨颗粒。烧结的pcbn材料可含有至多8重量%的碳化钨。已知这些颗粒对pcbn材料的性质具有不利影响,特别是在诸如硬质部件车削的应用中。此外,在碾磨期间吸取的碳化钨不受控制,因此不同的批次可能包含不同量的碳化钨,具有不同的尺寸分布,从而导致在用于工具应用时烧结pcbn材料具有不可预测的性能。发明概述目的是提供一种烧结pcbn材料,其具有大幅降低的碳化钨含量。根据第一方面,提供了一种制造pcbn材料的方法。提供包含平均颗粒尺寸不大于250nm的颗粒的基质前体粉末。还提供包含平均颗粒尺寸为至少0.2μm的cbn颗粒的cbn粉末。将基质前体粉末和cbn粉末紧密混合。将紧密混合的粉末在至少1100℃的温度和至少3.5gpa的压力下烧结以形成pcbn材料,该pcbn材料包含分散在基质材料中的立方氮化硼cbn的颗粒。该方法的一个优点是不使用研磨介质,因此得到的pcbn不含来自研磨介质的杂质,例如碳化钨。另一个优点是不需要碾磨步骤,因此制备pcbn的总时间减少。另一个优点是基质前体颗粒的小尺寸使它们在烧结步骤期间反应性更大。作为一种选择,该方法包括提供包含平均颗粒尺寸不大于100nm的颗粒的基质前体粉末。将基质粉末和cbn粉末紧密混合的步骤任选地包括将基质前体粉末和cbn粉末分散在溶剂中,使用超声混合器混合溶剂、基质前体粉末和cbn粉末,并且除去溶剂从而留下基质前体颗粒和cbn颗粒的紧密混合的粉末。作为一种替代选择,将基质粉末和cbn粉末紧密混合的步骤包括干式声学混合。作为一种选择,该方法包括提供平均尺寸在0.2和15μm之间的cbn粉末颗粒。cbn颗粒任选地具有大于1μm的平均尺寸。作为进一步的选择,cbn颗粒的平均尺寸在5μm至10μm的范围内。cbn颗粒任选地具有多模态的平均尺寸分布。得到的pcbn材料任选地包含小于80体积%的cbn颗粒。作为一种选择,基质材料包含选自钛和铝中任何的化合物的材料。示例性基质材料包括碳氮化钛、碳化钛、氮化钛、二硼化钛、氮化铝和氧化铝中的任何。根据第二方面,提供了一种制造pcbn材料的方法。该方法包括提供包含颗粒的基质前体粉末。使用研磨介质碾磨基质前体粉末以实现不大于1μm的平均颗粒尺寸。将研磨的基质前体粉末与包含平均颗粒尺寸为至少0.2μm的颗粒的cbn粉末紧密混合。将紧密混合的粉末在至少1100℃的温度和至少3.5gpa的压力下烧结以形成pcbn材料,该pcbn材料包含分散在基质材料中的立方氮化硼cbn的颗粒。该方法的一个优点是所得pcbn材料具有小于0.5重量%的非常低的来自研磨介质的杂质含量,因为在加入cbn后不进行碾磨。作为一种选择,将基质粉末和cbn粉末紧密混合的步骤包括将研磨过的基质前体粉末和cbn粉末分散在溶剂中,使用超声混合器混合溶剂、基质前体粉末和cbn粉末,并且除去溶剂从而留下基质前体颗粒和cbn颗粒的紧密混合的粉末。作为另一种选择,将表面活性剂加入溶剂中。作为一种替代选择,将基质粉末和cbn粉末紧密混合的步骤包括干式声学混合。作为一种选择,研磨过的基质前体粉末包含平均颗粒尺寸不大于200nm的颗粒。cbn颗粒任选地具有0.2至15μm,或大于1μm的平均尺寸。cbn颗粒任选地具有多模态平均尺寸分布。得到的pcbn材料任选地包含小于80体积%的cbn颗粒。作为一种选择,基质材料包含选自钛和铝中任何的化合物的材料。示例性材料包括碳氮化钛、碳化钛、氮化钛、二硼化钛、氮化铝和氧化铝中的任何。作为一种选择,将基质前体粉末碾磨以实现不大于700nm的平均颗粒尺寸。作为另一种选择,将基质前体粉末碾磨以实现不大于500nm的平均颗粒尺寸。根据第三方面,提供了一种聚晶立方氮化硼(pcbn)材料。该pcbn材料包含分散在基质材料中的立方氮化硼(cbn)的颗粒,该基质材料包含至少一种含钛化合物。该pcbn材料包含不大于0.5重量%的来自研磨介质的杂质。作为一种选择,pcbn材料不包含研磨介质杂质。研磨介质杂质任选地包括选自碳化钨、碳化硅、氧化铝、氧化锆、碳化钛和碳化硼中任何的材料,因为它们通常用作碾磨的研磨介质。cbn颗粒任选地具有0.2至15μm的平均尺寸。作为进一步的选择,cbn颗粒具有大于1μm的平均尺寸。作为一种选择,cbn颗粒具有多模态的平均尺寸分布。pcbn材料任选地包含小于80体积%的cbn颗粒。基质材料任选地包含选自钛和铝中任何的化合物的材料。作为另一种选择,基质材料包含碳氮化钛、碳化钛、氮化钛、二硼化钛、氮化铝和氧化铝中的任何。根据第四方面,提供了一种工具,其包括如第三方面中所述的烧结聚晶材料,该工具用于切割、铣削、磨碎、钻孔或其它磨削应用中的任何。附图简述现在将通过实例并参考附图来描述非限制性实施方案,其中:图1是显示制造烧结pcbn材料的已知示例性方法的流程图;图2是显示根据图1中所示步骤制造的示例性烧结pcbn材料的显微照片;图3是显示制造基本上没有碳化钨含量的烧结pcbn材料的方法的示例性步骤的流程图。图4是显示制造具有大幅降低的碳化钨含量的烧结pcbn材料的方法的示例性步骤的流程图;图5是显示制造不含碳化钨的烧结pcbn材料的方法的示例性步骤的流程图。图6是显示制造具有大幅降低的碳化钨含量的烧结pcbn材料的方法的示例性步骤的流程图;图7是不用碳化钨制造的样品的扫描电子显微照片;图8是用极低碳化钨制造的样品的扫描电子显微照片;图9的x射线衍射图显示了使用碾磨制造的现有技术pcbn材料的碳化钨的存在;图10的x射线衍射图显示了仅对粘合剂前体粉末使用碾磨制造的示例性pcbn材料的碳化钨的存在;图11显示了在h05机加工测试中使用pcbn材料制造的工具的实测的后刀面耐磨性;和图12显示了在h05机加工测试中使用pcbn材料制造的工具的实测的月牙洼磨损耐受性。详细说明发明人已经认识到,通过消除碾磨步骤,可以消除在碾磨步骤期间来自研磨介质的杂质的存在。碾磨不仅用于将基质前体颗粒破碎成所需的尺寸,而且还用于将基质前体颗粒和cbn颗粒紧密混合并分散。在第一实施方案中,已发现使用已经具有合适的所需尺寸的基质前体粉末,并且使用碾磨之外的技术来紧密混合基质前体颗粒和cbn颗粒能够导致不含研磨介质杂质的烧结pcbn材料。转向图3,示出了示出根据第一实施方案的示例性步骤的流程图。以下编号对应于图3的编号:s11.提供基质前体粉末的纳米颗粒,该颗粒具有不大于200nm的平均颗粒尺寸。s12.还提供cbn粉末。cbn粉末中的cbn颗粒的平均尺寸是至少0.2μm。cbn的尺寸分布可以是单模态或多模态(包括双模态)。s13.使用不需要研磨介质的技术,例如通过在溶剂中超声混合或通过干式声学混合,将cbn粉末和基质前体粉末紧密混合。s14.将混合粉末在高压高温(hpht)压机中在至少1100℃的温度和至少3.5gpa的压力下烧结,以便在含有至少一种钛化合物的基质中形成包含cbn颗粒的pcbn材料。示例性的基质材料是碳氮化钛、碳化钛、氮化钛、二硼化钛、氮化铝和氧化铝。也可以存在其它材料,例如基于铪的化合物。得到的烧结pcbn材料根本不含碳化钨,或通常由研磨介质产生的其它杂质,因为不存在使用碳化钨的碾磨步骤。除了制备不含碳化钨或其它研磨介质杂质的pcbn之外,缺少碾磨和预反应步骤意味着制备烧结pcbn材料的时间大幅减少。将纳米颗粒用于前体基质粉末的优点是它们具有高的表面积因此在烧结期间极具反应性。虽然将纳米粉末用于基质前体粉末具有许多优点,但使用纳米尺寸的基质前体粉末可能并不总是合适的。包含小颗粒的纳米粉末可导致粉末处理问题,例如附聚和应对纳米粉末的增强反应性。发明人已经认识到,在碾磨期间来自研磨介质的大多数吸取物(pickup)是由cbn的存在引起的。诸如碳化钨球的研磨介质比基质前体粉末更硬,因此基质前体粉末不太可能降解碳化钨球。然而,cbn比碳化钨球更硬,因此会使碳化钨球降解,从而导致碳化钨吸取。在第二个具体实施方案中,在不存在cbn的情况下碾磨基质前体粉末以减少基质前体粉末的颗粒尺寸。随后将cbn颗粒添加到基质前体粉末中并紧密混合,随后压制和烧结以形成烧结的pcbn材料。已经发现,该技术可以导致烧结的pcbn材料,该材料具有小于0.5%重量百分比的碳化钨。转向图4,其是显示根据第二实施方案的示例性步骤的流程图。以下编号对应于图4的编号:s15.提供基质前体粉末。s16.使用研磨介质如碳化钨球对基质前体粉末进行碾磨,以减小颗粒尺寸并紧密混合基质前体粉末。平均颗粒尺寸减小到至多700nm。典型地,这可以是约200至250nm。s17.在碾磨之后,除去研磨介质并以所需的量将cbn颗粒添加到研磨过的基质前体粉末中。s18.使用不需要研磨介质的技术,例如通过在溶剂中超声混合或者通过干式声学混合,将混合基质前体粉末和cbn颗粒紧密混合。s19.将混合粉末在高压高温(hpht)压机中在至少1100℃的温度和至少3.5gpa的压力下烧结,以便在含至少一种钛化合物的基质中形成包含cbn颗粒的pcbn材料。示例性的基质材料是碳氮化钛、碳化钛、氮化钛、二硼化钛、氮化铝和氧化铝。也可以存在其它材料,例如基于铪的化合物。图4中描述的技术克服了在第一具体实施方案中使用纳米粉末时遇到的粉末处理的一些问题。在基质前体粉末的碾磨期间存在少量的碳化钨吸取,但与cbn颗粒被碾磨时观察到的碳化钨吸取量相比,这可忽略不计。烧结的pcbn材料具有小于0.5重量%的碳化钨含量。对于上述第一和第二实施方案两者,存在将基质前体粉末与cbn颗粒紧密混合的步骤。如上所述,这可以通过超声混合来完成。这可以在溶剂中,在该情形中将粉末分散在溶剂中,超声混合,然后除去溶剂。可添加表面活性剂以稳定溶剂中的粉末。示例性溶剂包括己烷、乙醇和异丙醇。实施例如图3中所述,使用包含纳米粉末的基质前体粉末制造第一组实施例pcbn材料。图5更详细地示出了步骤,以下编号对应于图5的编号:s20.纳米基质前体粉末的平均颗粒尺寸为约50nm至100nm。制备各种基质材料。s21.在各种溶剂中使用超声混合器将基质前体粉末紧密混合。超声混合器是branson2000bdc,20khz,2.2kw全波,50mm直径喇叭,振幅为40-60%。s22.将立方氮化硼(cbn)颗粒添加到混合基质前体粉末中。s23.将混合基质前体粉末和cbn颗粒超声混合20分钟。s24.将得到的混合粉末在低压(小于500毫巴)和60℃以上干燥以除去溶剂。通过缓慢引入氧气以提供任何铝表面的钝化,对粉末进行调整(condition)。s25.将干燥的粉末过筛并制备预复合组合件。s26.将预复合组合件在大于1025℃下热处理2小时,以除去任何吸附的水或气体。可以在低压下进行该热处理。s27.将脱气的预复合组合件组装到适合于烧结的包壳中。s28.将包壳在hpht压机中在1250℃和5.5gpa下烧结以形成烧结pcbn材料。还使用图1所示的技术制备参比pcbn材料,以显示经历碾磨和吸取研磨介质的材料,和没有机会吸取任何研磨介质的pcbn材料之间的差异。表1显示了实施例的组成和一些制造参数。表1如图4所示,通过在添加cbn之前碾磨基质前体粉末来制造第二种pcbn材料。图6更详细示出了步骤,以下编号对应于图6的编号:s29.预混合具有1至10μm的平均颗粒尺寸的基质前体粉末。s30.将基质前体粉末在约1025℃下热处理至少1小时,以引发基质前体颗粒之间的预反应并形成“饼状物”。s31.将饼状物压碎并过筛以获得所需粒级的颗粒。s32。将所得粉末碾磨以将基质前体粉末破碎至期望尺寸(典型为50至700nm)并使基质前体粉末紧密混合。使用碳化钨研磨介质进行碾磨。s33.将立方氮化硼(cbn)颗粒添加到混合基质前体粉末中。s34.将混合的基质粉末和cbn颗粒超声混合20分钟。s35.将得到的混合粉末在低压(小于500毫巴)和60℃以上干燥以除去溶剂。通过缓慢引入氧气以提供任何铝表面的钝化,对粉末进行调整。s36.将干燥的粉末过筛并制备预复合组合件。s37.将预复合组合件在大于1025℃下热处理2小时,以除去任何吸附的水或气体。可以在低压下进行该热处理。s38.将脱气的预复合组合件组装到适合于烧结的包壳中。s39.将包壳在hpht压机中在1250℃和5.5gpa下烧结以形成烧结pcbn材料。表2显示了根据图6制造的实施例的组成和一些制造参数。表2实施例cbn体积%基质组成重量%溶剂186045tic/45tin/10al己烷图7是实施例9的扫描电子显微照片。与图2不同,根本不存在碳化钨,因为没有进行碾磨步骤。图8是实施例18的扫描电子显微照片。在该情形中,存在非常少量的碳化钨。碳化钨颗粒的实例以白色圆圈突显。碳化钨的量据估计为约0.2重量%。实施例1至17的x射线衍射(xrd)没有示出碳化钨迹线。与此相反,参比样品的xrd清楚示出归因于碳化钨的峰,如图9所示。相比之下,由实施例18获得的xrd迹线显示出非常小的碳化钨迹线,正如所预期的。分析一些样品以测量它们的密度、声速(sos)、比表面积(ssa)和硬度。所得数据如表3所示。表3实施例密度g/cm3soskm/sssag/m2维氏硬度gpa14.2111.5122.3323.7924.2211.6622.3325.3334.1111.7621.1425.1244.2011.8321.1426.3854.0112.6022.6627.8464.2211.4523.8726.0274.1911.5523.1525.5684.2011.4525.6625.3894.0512.3524.4428.35参比-12.3917.1129-30将一些实施例pcbn材料形成机加工工具并在h05机加工测试中测试(vc=200m/min,进给速度为0.1mm/rev,切削深度为0.15mm,工件sae8620,硬度为60-62hrc,在a:glidemeisterctx500车床上进行。使用vb测量后刀面耐磨性。实施例1、2和4以及参比样品的后刀面耐磨性如图11所示。样品1、2和4具有略微改善的后刀面耐磨性。通过kt测量月牙洼磨损耐受性(也称为耐化学磨损性)。与参比样品相比,实施例1、2和4都具有略微改善的月牙洼磨损耐受性,如图12所示。这种改进被认为是来自较低cbn含量和较低碳化钨含量的组合。上述两个具体实施方案各自提供了生产pcbn材料的方式,其中没有研磨介质吸取或具有显著减少的研磨介质吸取(使得研磨介质占pcbn材料的小于0.5重量%)。这允许pcbn材料具有更加可控和可预测的待制备性质。此外,该技术还减少了制备pcbn材料的时间。使用干式声学混合技术制备另一组示例性粉末。在100ml聚酰胺罐中,将碳氮化钛(tic0.5n0.5)粉末(1.3μm平均颗粒尺寸)与铝(6μm平均颗粒尺寸)以90:10(重量%)的比率预混合。在罐中称取36gtic0.5n0.5和4gal,将其密封并置于labrami干式声学混合器中并在40g下运行2分钟并且在不同实验中以60g运行2分钟。然后将预混合的粉末与颗粒尺寸为4-5μm和6-7μm的立方氮化硼粉末结合,以制备60体积%和70体积%的复合物。该第二步结合也在40g和60g的不同条件下进行。条件如下表4所示。表4预混合后混合cbn颗粒尺寸(μm)40g,2min40g,5min4-540g,2min40g,5min6-760g,2min60g,5min4-560g,2min60g,5min6-7最终的粉末在带式高压高温设备中在约5.5gpa和1400℃下烧结。将烧结材料切割并抛光,sem中的显微结构分析显示所得材料的显微结构是均匀的。在另一组实验中,将单独的tic和tin粉末(平均颗粒尺寸1-2微米)以80g一起预混合2分钟。然后将4-5μm的cbn颗粒与tic/tin粉末以80g混合30秒并以100g混合2分钟。在另一步骤中,将6μm铝添加到系统中并且以80g混合30秒并以100g混合2分钟。将粉末以足够的量混合以制备60体积%cbn的组合物,剩余的tic/tin:al重量比为90:10。所得粉末和烧结材料的分析显示为均匀的结构。最后,将90g的1.3μmcbn与10g的6μm铝以80g混合5分钟。所得显微结构显示出大的附聚物。在另一个实验中,在labrami混合器中在100ml的聚酰胺罐中以20g的量混合这些粉末,在罐中具有200重量%的0.7mmwc球。使混合物以80g运行30秒并以100g运行2分钟。最终烧结材料的显微结构显示出均匀的结构。定义如本文所用,pcbn材料是指一种超硬材料,其包含分散在包括金属或陶瓷的基质内的cbn晶粒。pcbn是超硬材料的一个例子。如本文所用,“pcbn结构”包括pcbn材料的物体。“基质材料”应理解为意指完全或部分填充聚晶结构内的孔隙、间隙或间隙区域的基质材料。术语“基质前体粉末”用于指当经受高压高温烧结工艺时变为基质材料的粉末。大量晶粒的多模态尺寸分布应理解为意指晶粒具有多于一个峰的尺寸分布,每个峰对应于各自的“模态”。可以通过提供多于一个源的多个晶粒来制造多模态聚晶物体,每个源包括具有显著不同平均尺寸的晶粒,并将来自这些源的晶粒或颗粒掺混在一起。在一个实施方案中,pcbn材料可包括具有多模态分布的cbn晶粒。以上描述涉及平均颗粒尺寸。这是使用等效圆直径(ecd)技术测量的。可以通过激光衍射测量多个松散、不受限制且非附聚的晶粒的ecd分布,其中将晶粒随机设置在入射光的路径中,并且测量光被晶粒衍射引起的衍射图案。衍射图案可以在数学上解释为好似它是由多个球形晶粒产生的,其直径分布是按照ecd计算和报告的。晶粒尺寸分布的方面可以使用各种术语和符号按各种统计特性表示。这些术语的具体例子包括平均、中间和模态。尺寸分布可以被认为是对应于一系列相应尺寸通道的一组值di,其中每个di是对应于各个通道i的几何平均ecd值,i是1至所用通道数n的范围内的整数。通过激光衍射方法获得的平均值可以基于晶粒体积的分布最容易地表达,根据公知的数学公式,体积平均值可以表示为d[4,3]。结果可以转换为表面积分布,根据众所周知的数学公式,其平均值为d[3,2]。除非另有说明,则本公开中使用的尺寸分布的平均值是指基于体积的平均值d[4,3]。尺寸分布的中间值d50是将多个晶粒分成两个相等群体的值,一个群体由具有高于该值的ecd尺寸的晶粒组成,另一半具有至多该值的ecd尺寸。尺寸分布的模态是与晶粒的最高频率对应的值,其可呈现为分布的峰(分布可以包括多于一个局部最大频率并且被称为多模态)。可以提供各种其它值d(y),其表示的尺寸是指:在分布中存在分数y的多个晶粒低于该尺寸。例如,d(0.9)是指90%的晶粒低于该尺寸的ecd尺寸,d(0.5)是指50%的晶粒低于该尺寸的ecd尺寸,d(0.1)是指10%的晶粒低于该尺寸的ecd尺寸。虽然已经参考实施方案具体显示和描述了本发明,但是本领域的技术人员将理解,在不脱离由所附权利要求书限定的本发明范围的情况下,可以在形式和细节上进行各种改变。例如,尽管所有实施例均使用cbn作为超硬相,但是应当理解,相同的技术可以用于分散在基质材料中的其它类型的超硬材料。当前第1页12