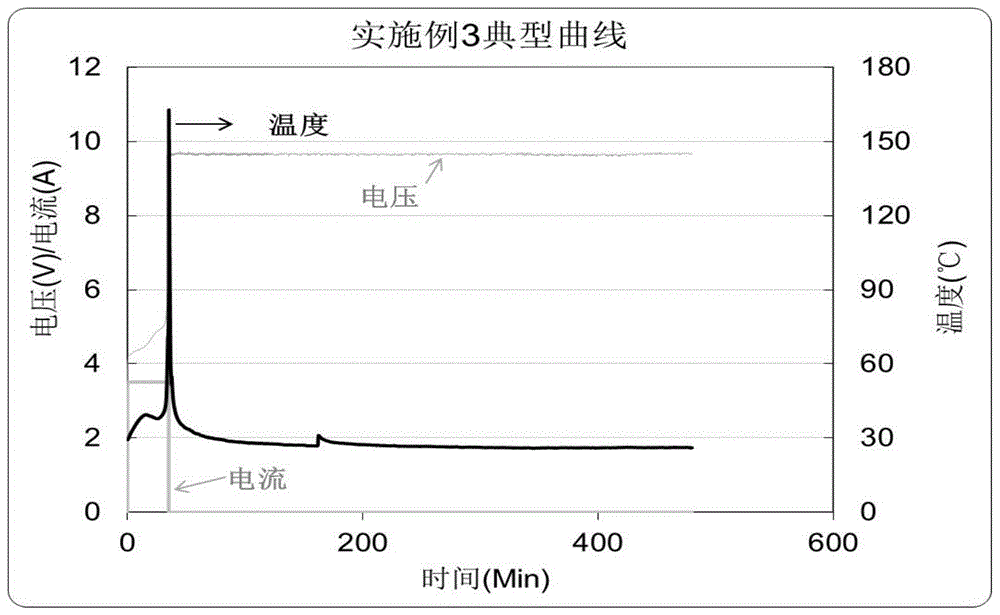
本发明涉及锂离子电池
技术领域:
,主要涉及锂离子电池正极材料领域,具体涉及一种锰酸锂正极材料制备方法。
背景技术:
:近年来随着新能源汽车的兴起,对化学电源/堆的能量密度、安全性、循环寿命、性价比等的要求越来越高,目前锂离子电池中的锂源均以制备成正极材料的方式封装于锂离子电池中,因而正极材料中的锂含量多寡决定了锂电池的能量密度,以及锂离子电池的成本。常见的锂离子电池正极材料主要有钴酸锂、锰酸锂、镍钴锰酸锂和磷酸亚铁锂。其中钴酸锂尽管能量密度高,但因钴储存量有限因而主要用于3c领域的小型锂离子电池中,锰酸锂及磷酸亚铁锂材料能量密度较低,有逐渐边缘化趋势,尽管如此,受市场供需影响,锰酸锂材料仍旧是一款类似“压舱石”的正极材料,仍旧具有较好的市场应用前景。锰酸锂正极材料通常包括尖晶石型锰酸锂(limn2o4)以及层状结构的锰酸锂(limno2),后者因知识产权主要在美国阿贡(argone)实验室,以及合成和电解质的匹配性问题目前研究较少,应用不明朗。尖晶石型锰酸锂limn2o4是hunter博士在1981年首先制得,晶体结构上属于立方晶系,fd3m空间群,由于具有三维通道结构,锂离子可以可逆地从尖晶石晶格中脱嵌,不会引起结构的塌陷,因而具有优异的倍率性能和稳定性。由于锰酸锂中只含有锂和锰两种有价(值)元素。且来源广泛,因此在近年来正极材料市场价格(如钴和镍)涨跌中受市场影响较小,整体价格/成本已接近铅酸电池的价格,因而是锂离子电池中代替铅酸系电池的最有力竞争者。目前市场上推出的锰酸锂材料主要用于功率型锂电池和动力型锂电池中,部分还与含镍高的镍钴锰酸锂混合使用以降低锂电池成本。锰酸锂相对钴酸锂,镍钴锰酸锂等层状结构材料而言,其劣势是能量密度低,尽管理论比容量为148mah/g,但实际发挥的比容量为约为理论比容量的一半(80-90mah/g,而钴酸锂实际发挥的比容量为140-180mah/g),以及压实密度低2.0g/cm3(而钴酸锂的压实密度为4.2g/cm3),此外由于锰酸锂材料结构略微偏离尖晶石结构,因此在锂电池体系中易出现锰(mn3+)的溶出,溶解的锰离子在电压驱动下会迁移并沉积到锂电池的负极片上,导致负极片sei膜(solidelectrolyteinterface固态电解质膜)劣化,进而缩短锰酸锂型锂离子电池的循环寿命,并引起安全风险。据测算,循环200次的锰酸锂电池负极片上沉积的锰离子可达3000ppm以上,并且随着循环的进行,锰的含量会逐步上升,此现象在高温(≥45℃)条件下更为明显,因此如何有效提升锰酸锂电池的高温及安全性能是解决锰酸锂锂电池应用的关键。目前锂离子电池的工作电压在1.5-4.2v之间,为了达到电动汽车的不同电压的使用要求,以及功率要求,需要将多个化学电池进行串/并联成组才能满足要求,在此条件下,成组的单个电池的安全性能尤其重要,某一支电池的性能劣化往往会引起“多米诺骨牌效应”导致整体电池组失效或者起火爆炸,近年来相关的事故屡屡见诸报端。基于汽车工业ppm级的缺陷要求,需要提供高安全性的锂离子电池。中国专利文献cn201110056889.1公开了一种高温循环稳定的尖晶石锰酸锂合成方法,其将原料锂化合物、锰化合物以及al2o3、mgo、tio2、cr2o3的一种或多种按照化学式li(1+x)mn(2-x-y)myo4(0<x<0.3,0<y<0.2,m为al、mg、ti、cr的一种或多种)均匀混合,然后在500~750℃下保温5~20h,冷却后的产物研磨后在800~1200℃下保温10~30h,冷却后的产物与一定量的钴、镍、锂化合物(钴、镍、锂和产物中的锰摩尔比为0.02~0.2)均匀混合,再于500~750℃下保温10~30h,最后产物经冷却后粉碎过筛得到成品。中国专利cn201310711939.4公开了高容量、长寿命锂离子电池锰酸锂正极材料的制备方法。按摩尔比li:mn:m=1~1.1:1.95~2:0~0.05称取锂源、锰盐和掺杂微量金属元素均匀混合,在400~600℃下预烧2~6h,再在700~1000℃下煅烧6~16h,分级除去细小颗粒,磁性吸附金属离子后得到锰酸锂或一次掺杂锰酸锂;再将得到锰酸锂或一次掺杂锰酸锂按照锂质量比0.015~0.03二次掺入锂源,均匀混合(液相混合或固相混合);将混合物在600~850℃下煅烧3~8h,得到一次或二次掺杂煅烧锰酸锂材料。中国专利cn201711080126.4公开了一种改进化学稳定性锰酸锂电池材料的制备工艺,先配制醋酸锂、醋酸硼、醋酸镍、醋酸锰的混合溶液(醋酸锂:醋酸硼:醋酸镍:醋酸锰:间苯二酚:甲醛的摩尔比为1:0.2:0.4:1.4:(3-7):(7-8)),向该混合溶液中加入间苯二酚并搅拌,待间苯二酚完全溶解后加入甲醛溶液;再将上述溶液置于预烧结半成品室上端的容器中,通过预烧结半成品室的热量对溶液加热(50-70℃,反应时间为10-14h)反应形成凝胶;然后打开容器底部的密封板,使凝胶流入预烧结半成品室一侧的容纳室内,再通过预烧结半成品室另一侧的供热室向容纳室供热,并对上述凝胶进行干燥和预烧结半成品;将预烧结半成品后的产物用气流研磨机研磨完成后的粉体输送至容纳室再次预烧结半成品,将再次预烧结半成品后的产物进行研磨,得到锰酸锂电池材料。技术实现要素:本发明解决的技术问题是:现有的锂离子电池用锰酸锂正极材料尽管性价比及安全性高,但在成组使用条件下或者单体电池过大时安全存在风险,且高温循环性能差,因此从材料本身着手亟待开发一种新的简单可行的改进方法。为解决上述技术问题,本发明在研究锰酸锂正极材料制备工艺后,发现早期的锂盐四氟硼酸锂(目前已淘汰,作为离子导体型锂直添加到电解液中使用)尽管离子电导率低,制备的电解质黏度大,但对于锂电池的安全性能似乎有帮助,而联想到安全风险主要来自于正极材料中的锂的缘故,以及四氟硼酸锂电解质的其他未深入研究的性能,如将硼引入到正极材料则有可能会产生相同的作用,基于此开展实验并发现添加硼后合成的材料的确在安全性及抑制锰溶出方面有较好的效果,加入少量硼可以显著提升锰酸锂的安全性能,以及锰酸锂材料制备的锂离了二次电池的高温循环性能,对于锂离子电池正极材料的应用具有重要意义。具体来说,针对现有技术的不足,本发明提供了如下技术方案:本发明提供了一种锰酸锂正极材料,其特征在于,所述锰酸锂正极材料的化学式为li(1+3a+b)mn2barbo(4+3a+2b),其中,r为掺杂元素,0<a<0.1,0<b<0.2。优选的,所述锰酸锂正极材料的化学式为li(1+3a+b)mn2barbo(4+3a+2b),其中,r为掺杂元素,0.005≤a<0.1,0.001≤b<0.2。优选的,所述掺杂元素r选自iia、iiia、iiib、ivb、vib和viii族金属中的一种或两种以上。优选的,所述掺杂元素r选自镁、钛、铝、钴、钇、锆、铈、镧和铪中的一种或两种以上,优选为镁、铝、钴、钇、锆、铈和镧中的一种或两种以上。优选的,所述锰酸锂正极材料的比表面积为0.3-2.0m2/g,优选为0.9-2.0m2/g。优选的,所述锰酸锂正极材料的粒度(dv50)为3-17μm,优选为3-8μm。本发明还提供了一种上述锰酸锂正极材料的制备方法,包括如下步骤:步骤1:将锰源化合物和锂源化合物混合,经过热处理,得到锰酸锂正极材料半成品;步骤2:将步骤1得到的锰酸锂正极材料半成品、含掺杂元素r的化合物混合,经过热处理,得到所述的锰酸锂正极材料;其中,在步骤1或步骤2中进行热处理之前,还加入了硼源化合物。其中,锂源化合物可以分步添加,例如在步骤1中添加一部分后,剩余的再在步骤2中添加。优选的,所述制备方法,其中,步骤1中所述的锰源化合物选自锰的氧化物和/或氢氧化物,优选为四氧化三锰、氢氧化锰、二氧化锰、三氧化二锰、氧化锰和七氧化二锰中的一种或两种以上,更优选为四氧化三锰、氢氧化锰和二氧化锰中的一种或两种以上。优选的,所述制备方法,其中,所述四氧化三锰为球形,其粒度(dv50)为2-15μm;所述二氧化锰为球形,其粒度(dv50)为2-15μm;所述氢氧化锰为球形,其粒度(dv50)为2-15μm。优选的,所述制备方法,其中,步骤1中所述的锂源化合物选自单水氢氧化锂、氢氧化锂、草酸锂、碳酸锂、硝酸锂、醋酸锂、氟化锂、氯化锂、叔丁醇锂和柠檬酸锂中的一种或两种以上,优选为单水氢氧化锂、氢氧化锂、草酸锂和碳酸锂中的一种或两种以上。优选的,所述的制备方法,其中,步骤1中所述的硼源化合物选自硼酸,硼酸钠,四水八硼酸钠,硼酸钾,硼酸锂、硼酸钙、硼酸铝、硼酸铁和硼酸锌中的一种或两种以上,优选为硼酸,硼酸钠,硼酸钾,硼酸锂中的一种或两种以上。优选的,所述制备方法,其中步骤1中热处理的反应温度为100-1000℃,优选为200-800℃;气氛为富氧空气,氧气体积含量为20-96%,优选为45%-70%;热处理时间为5-20h,优选为8-16h;空气流量为180-600nm3/h。优选的,所述制备方法,其中步骤2中热处理的反应温度为750-970℃,优选为700-880℃;气氛为富氧空气,氧气体积含量为50-96%;热处理时间为0.5-6h;空气流量为400-600nm3/h。本发明还提供了一种锰酸锂正极材料,由上述制备方法制备得到。本发明还提供了一种锂离子电池正极,其中,由上述的正极材料和铝箔制备所得。本发明还提供了一种锂离子电池,其中,包含上述的正极材料或正极。本发明还提供上述正极材料、上述正极或上述锂离子电池在锂电能源领域的应用。本发明的优点是:本发明采用硼源与锰源复合生成含硼锰酸锂正极材料,同时对材料进行掺杂改性,制备的锰酸锂材料制备的锂离子二次电池安全性能得到显著提升,附带高温循环性能也得到明显改善,扩大了锰酸锂正极材料应用环境。该方法经济可行,适用性广泛,效果非常明显,具有较好的应用前景。附图说明图1为实施例3的过充性能典型曲线图2为对比例3的过充性能典型曲线具体实施方式鉴于目前锂离子电池用锰酸锂正极材料安全性不可靠及高温循环性能差限制了其应用的问题,本发明提供一种制备含硼锰酸锂正极材料的方法,通过在制备阶段加入硼源再经处理后即可得到锰酸锂正极材料,有利于提升锰酸锂正极材料的安全性能及高温循环性能。该工艺制备简单,经济可行,同时不影响锂离子电池用正极材料的电化学性能。在一种实施方式中,本发明提供了一种锰酸锂正极材料,其特征在于,所述锰酸锂正极材料的化学式为li(1+3a+b)mn2barbo(4+3a+2b),其中,r为掺杂元素,0<a<0.1,0<b<0.2。优选的,所述锰酸锂正极材料的化学式为li(1+3a+b)mn2barbo(4+3a+2b),其中,r为掺杂元素,0.005≤a<0.1,0.001≤b<0.2。优选的,所述掺杂元素r选自iia、iiia、iiib、ivb、vib和viii族金属中的一种或两种以上。优选的,所述掺杂元素r选自镁、钛、铝、钴、钇、锆、铈、镧和铪中的一种或两种以上,优选为镁、铝、钴、钇、锆、铈和镧中的一种或两种以上。优选的,所述锰酸锂正极材料的比表面积为0.3-2.0m2/g,优选为0.9-2.0m2/g。优选的,所述锰酸锂正极材料的粒度(dv50)为3-17μm,优选为3-8μm。本发明还提供了一种上述锰酸锂正极材料的制备方法,包括如下步骤:步骤1:将锰源化合物和锂源化合物混合,经过热处理,得到锰酸锂正极材料半成品;步骤2:将步骤1得到的锰酸锂正极材料半成品、含掺杂元素r的化合物混合,经过热处理,得到所述的锰酸锂正极材料;其中,在步骤1或步骤2中进行热处理之前,还加入了硼源化合物。其中,锂源化合物可以分步添加,例如在步骤1中添加一部分后,剩余的再在步骤2中添加。优选的,所述制备方法,其中,步骤1中所述的锰源化合物选自锰的氧化物和/或氢氧化物,优选为四氧化三锰、氢氧化锰、二氧化锰、三氧化二锰、氧化锰和七氧化二锰中的一种或两种以上,更优选为四氧化三锰、氢氧化锰和二氧化锰中的一种或两种以上。优选的,所述制备方法,其中,所述四氧化三锰为球形,其粒度(dv50)为2-15μm;所述二氧化锰为球形,其粒度(dv50)为2-15μm;所述氢氧化锰为球形,其粒度(dv50)为2-15μm。优选的,所述制备方法,其中,步骤1中所述的锂源化合物选自单水氢氧化锂、氢氧化锂、草酸锂、碳酸锂、硝酸锂、醋酸锂、氟化锂、氯化锂、叔丁醇锂和柠檬酸锂中的一种或两种以上,优选为单水氢氧化锂、氢氧化锂、草酸锂和碳酸锂中的一种或两种以上。优选的,所述的制备方法,其中,步骤1中所述的硼源化合物选自硼酸,硼酸钠,四水八硼酸钠,硼酸钾,硼酸锂、硼酸钙、硼酸铝、硼酸铁和硼酸锌中的一种或两种以上,优选为硼酸,硼酸钠,硼酸钾,硼酸锂中的一种或两种以上。若其为颗粒物时,其粒径dv50为2-200μm。优选的,所述制备方法,其中步骤1中热处理的反应温度为100-1000℃,优选为200-800℃;气氛为富氧空气,氧气体积含量为20-96%,优选为45%-70%;热处理时间为5-20h,优选为8-16h;空气流量为180-600nm3/h。优选的,所述制备方法,其中步骤2中热处理的反应温度为750-970℃,优选为700-880℃;气氛为富氧空气,氧气体积含量为50-96%;热处理时间为0.5-6h;空气流量为400-600nm3/h。本发明还提供了一种锰酸锂正极材料,由上述制备方法制备得到。本发明还提供了一种锂离子电池正极,其中,由上述的正极材料和铝箔制备所得。本发明还提供了一种锂离子电池,其中,包含上述的正极材料或正极。本发明还提供上述锰酸锂正极材料在制造锂离子二次电池、移动式存贮设备和储能电站中的应用。下面通过具体实施例来说明本发明所述锰酸锂正极材料及其制备方法和应用。实施例中所用到各试剂和仪器来源如表1及表2所示。表1本发明实施例中所用试剂信息表2本发明实施例中所用设备信息实施例1选用500l融合机,开启搅拌(400rpm),在搅拌情况下加入76.5kg的四氧化三锰(dv50:9.0μm),再称取35.6kg单水氢氧化锂粉体加入到500l融合机中,再称取6.3kg硼酸,在搅拌情况下按80wt%固含量添加29.5kg去离子水,搅拌0.5h后进一步降低速度(50rpm)搅拌20min出料形成具有一定成型度的膏状物料备用。采用通气24m辊道窑。设置升温区温度为200℃,通入富氧空气(氧含量体积比为60%,气体输入量180nm3/h)条件下将上述膏状物料装入到陶瓷匣钵中进行预烧结,预烧结时间为15h,将物料隔离空气冷却至常温,称取进出物料的重量,统计烧失率(预烧结半成品粉料质量差与预烧结半成品前粉料质量的比值)为33.1%。然后用气旋涡流粉碎机进行粉碎,粉碎时控制环境空气的湿度≤2%,得到半成品。将半成品再次投入到500l融合机中,向其中加入1.7kg纳米三氧化二钇,经混合0.5h后取出物料重新装入陶瓷匣钵中,采用通气24m辊道窑。设置升温区温度为700℃,通入富氧空气条件下(氧含量体积比为70%,气体输入量600nm3/h)烧结8h,将物料隔离空气冷却至常温,称取进出物料的重量,统计烧失率(烧结半成品粉料质量差与烧结半成品前粉料质量的比值)为1.2%。然后用气旋涡流粉碎机进行粉碎,得到锰酸锂正极材料,材料的粒度(dv50)为9.2μm,比表面积为1.16m2/g。用icp对正极材料的元素定量分析后结果如表3所示,经核算所得的化学式为:li1.62mn2b0.2y0.03o4.7。表3实施例1所述正极材料元素表征结果元素limnbyalmgco质量比5.072749.2740.9701.2080.00110.00050.0003原子量6.9454.9410.8189.8126.9824.0058.93摩尔数0.73090.89690.08970.01350.000040.000020.00001元素ninapstiznzr质量比0.00120.00020.00620.01280.00160.00070.0018原子量58.6923.0030.9732.0040.0065.4191.22摩尔数0.000020.000010.00020.00040.000040.000010.00002实施例2选用500l犁刀式混料机,开启搅拌(主轴转速120rpm,侧刀转速1500rpm),在搅拌情况下加入83.9kg的电解二氧化锰(dv50:9.0μm),再称取21.7kg碳酸锂粉体加入到500l犁刀式混料机中,在搅拌情况下添加31.7kg六水硝酸镧,15.3kg去离子水,搅拌2h后进一步降低速度(3-5rpm)搅拌6h出料形成具有一定成型度的粉状物料备用。采用通气24m辊道窑。设置升温区温度为500℃,通入富氧空气(氧含量体积比为65%,气体输入量400nm3/h)条件下将上述膏状物料装入到陶瓷匣钵中进行预烧结,预烧结时间为16h,将物料隔离空气冷却至常温,称取进出物料的重量,统计烧失率为34.9%。然后用气旋涡流粉碎机进行粉碎,粉碎时控制环境空气的湿度≤2%,得到半成品。将半成品再次投入到混合机中,向其中加入用2.0kg去离子水溶解的0.3kg硼酸,经混合3.0h后取出物料重新装入陶瓷匣钵中,采用通气24m辊道窑。设置升温区温度为880℃,通入富氧空气条件下(氧含量体积比为70%,气体输入量600nm3/h)烧结16h,将物料隔离空气冷却至常温,称取进出物料的重量,统计烧失率为2.1%。然后用气旋涡流粉碎机进行粉碎,得到锰酸锂正极材料,材料的粒度(dv50)为9.5μm,比表面积为1.23m2/g,经核算所得的化学式为:li1.18mn2b0.01la0.15o4.3。实施例3选用500l捏合机,开启搅拌(30rpm),在搅拌情况下加入91.8kg的氢氧化锰(dv50:8.5μm),再称取67.2kg草酸锂粉体加入到500l捏合机中,称取7.4kg硼酸钾,以及41.8kg去离子水,搅拌1h后进一步降低速度(10rpm)搅拌30min出料形成具有一定成型度的膏状物料备用。采用通气24m辊道窑。设置升温区温度为750℃,通入富氧空气条件下(氧含量体积比为70%,气体输入量600nm3/h)将上述膏状物料装入到陶瓷匣钵中进行预烧结,预烧结时间为8h,将物料隔离空气冷却至常温,称取进出物料的重量,统计烧失率为53.8%。然后用气旋涡流粉碎机进行粉碎,粉碎时控制环境空气的湿度≤2%,得到半成品,材料的粒度(dv50)为16.0μm,比表面积为0.2m2/g。将半成品再次投入到500l捏合机中,向其中加入用10kg去离子溶解的9.2kg五水硝酸锆,以及5.5kg草酸锂,经混合3.0h后取出物料重新装入陶瓷匣钵中,采用通气24m辊道窑。设置升温区温度为880℃,通入富氧空气条件下(氧含量体积比为70%,气体输入量600nm3/h)烧结12h,将物料隔离空气冷却至常温,称取进出物料的重量,统计烧失率为2.9%。然后用气旋涡流粉碎机进行粉碎,得到锰酸锂正极材料,材料的粒度(dv50)为8.3μm,比表面积为0.91m2/g,经核算所得的化学式为li1.34mn2b0.09zr0.04o4.34。实施例4选用500l陶瓷球磨机。开启搅拌(30rpm,聚氨酯球料与原料重量比1.3:1),在搅拌情况下加入80.9kg的四氧化三锰(dv50:4.0μm),再称取15.4kg氢氧化锂粉体加入到500l陶瓷球磨机中,在搅拌情况下添加2.0kg硼酸,搅拌2h后进一步降低速度(10rpm)搅拌4h出料滤出聚氨酯球形成具有一定成型度的膏状物料备用。采用通气24m辊道窑。设置升温区温度为800℃,通入富氧空气条件下(氧含量体积比为70%,气体输入量200nm3/h)将上述膏状物料装入到陶瓷匣钵中进行预烧结,预烧结时间为8h,将物料隔离空气冷却至常温,称取进出物料的重量,统计烧失率为2.3%。然后用气旋涡流粉碎机进行粉碎,粉碎时控制环境空气的湿度≤2%,得到半成品,材料的粒度(dv50)为6.0μm,比表面积为4.89m2/g。将半成品再次投入到500l陶瓷球磨机中,向其中加入1.49kg纳米氧化镁,以及1.82kg氢氧化锂,经混合6.0h后取出物料重新装入陶瓷匣钵中,采用通气24m辊道窑。设置升温区温度为880℃,通入富氧空气条件下(氧含量体积比为70%,气体输入量600nm3/h)烧结12h,将物料隔离空气冷却至常温,称取进出物料的重量,统计烧失率为0.7%。然后用气旋涡流粉碎机进行粉碎,得到锰酸锂正极材料,材料的粒度(dv50)为4.5μm,比表面积为1.58m2/g,经核算所得的化学式为:li1.32mn2b0.06mg0.06o4.3。实施例5选用500l犁刀式混料机,开启搅拌(主轴转速130rpm,侧刀转速1450rpm),在搅拌情况下加入90.7kg的电解二氧化锰(dv50:3.0μm),再称取33.8kg单水氢氧化锂粉体加入到500l犁刀式混料机中,在搅拌情况下添加1.6kg硼酸,以及32.0kg去离子水,搅拌2h后进一步降低速度(3-5rpm)搅拌4h出料形成具有一定成型度的膏状物料备用。采用通气24m辊道窑。设置升温区温度为400℃,通入富氧空气(氧含量体积比计为45%,气体输入量400nm3/h)条件下将上述膏状物料装入到陶瓷匣钵中进行第一次预烧结,预烧结时间为13h,将物料隔离空气冷却至常温,称取进出物料的重量,统计烧失率为38.6%。然后用气旋涡流粉碎机进行粉碎,粉碎时控制空气的湿度≤2%,得到半成品。将半成品再次投入到500l犁刀式混料机中,向其中加入4.412kg纳米氢氧化亚钴,经混合6.0h后取出物料重新装入陶瓷匣钵中,采用通气24m辊道窑。设置升温区温度为700℃,通入富氧空气条件下(氧含量体积比计为70%,气体输入量600nm3/h)烧结12h,将物料隔离空气冷却至常温,称取进出物料的重量,统计烧失率为3.6%。然后用气旋涡流粉碎机进行粉碎,得到具有最终制备物锰酸锂正极材料,材料的粒度(dv50)为3.2μm,比表面积为1.33m2/g,经核算所得的化学式为li1.25mn2b0.13co0.09o4.34。实施例6选用500ly型混合机,开启搅拌(35rpm),在搅拌情况下加入75.8kg的四氧化三锰(dv50:4.0μm),再称取23.3kg碳酸锂粉体加入到500ly型混合机中,以及经10kg去离子溶解的8.8kg硼酸,在搅拌情况下按80wt%固含量添加38kg去离子水,以及0.21kg纳米氢氧化亚钴(含量以成品计钴含量为500ppm),搅拌2h后进一步降低速度(3-5rpm)搅拌2h出料形成具有一定成型度的膏状物料备用。采用通气24m辊道窑。设置升温区温度为500℃,通入富氧空气(氧含量体积比计为45%,气体输入量400nm3/h)条件下将上述膏状物料装入到陶瓷匣钵中进行预烧结,预烧结时间为15h,将物料隔离空气冷却至常温,称取进出物料的重量,统计烧失率为29.6%。然后用气旋涡流粉碎机进行粉碎,粉碎时控制空气的湿度≤2%,得到预烧结半成品。将半成品再次投入到500ly型混合机中,向其中加入经6kg去离子水溶解的16.785kg四水硫酸铈,经混合6.0h后取出物料重新装入陶瓷匣钵中,采用通气24m辊道窑。设置升温区温度为700℃,通入富氧空气条件下(氧含量体积比计为70%,气体输入量400nm3/h)烧结10h,将物料隔离空气冷却至常温,称取进出物料的重量,统计烧失率为5.2%。然后用气旋涡流粉碎机进行粉碎,得到具有最终制备物锰酸锂正极材料,材料的粒度(dv50)为4.2μm,比表面积为1.97m2/g,经核算所得的化学式为li1.4mn2b0.09ce0.09o4.5。对比例1对比例1与本发明实施例1类似,区别仅在于,未添加硼源化合物,原料混料及预烧结半成品过程中出现板结变硬现象,最终制备的材料的粒度(dv50)为19.0μm,比表面积为4.09m2/g,经核算所得的化学式为:li1.12mn2y0.03o4.2。对比例2对比例2与本发明实施例2类似,区别仅在于,添加硼源化合物(即硼酸)比实施例2过量23%(摩尔量),原料混料及预烧结半成品过程中物料未出现板结,最终制备的材料的粒度(dv50)为15.0μm,比表面积为6.12m2/g,经核算所得的化学式为:li1.84mn2b0.23la0.15o4.57。对比例3对比例3与本发明实施例3类似,区别仅在于,前期未添加硼源化合物,原料经混料及预烧结半成品过程中物料出现板结,最终经粉碎后的物料添加比例与实施例3相合成目标物同量的硼酸锂混合均匀得到对比例3,制备的材料的粒度(dv50)为15.7μm,比表面积为2.09m2/g,经核算所得的化学式为:li1.34mn2b0.09zr0.04o4.34。应用例1:全电池制备取n-甲基吡咯烷酮溶剂2000g加入到5000ml烧杯中,用砂磨机(德国产)以500rpm的转速搅拌,并加入121.8g聚偏氟乙烯(pvdf),加入pvdf后,将搅拌速度逐步提高至1500rpm并搅拌60min,再加入81.2g导电碳superpli,以2000rpm的转速高速分散60min后,取实施例1,实施例2,实施例3,对比例1,对比例2,对比例3制备得到的正极材料样品各3857g锰酸锂物料加到上述溶液中,再降低搅拌转速至1500rpm搅拌120min,出料。将浆料置于kcm400型涂布机的料槽中,对实施例1,实施例2,实施例3,对比例1,对比例2,对比例3的正极材料浆料涂布机烘箱分别设置烘箱区温度分别为60℃、85℃、95℃、105℃和95℃,对应的烘箱区热风量开启度分别为30%、50%、80%、80%和60%,在12μm厚的铝箔上进行双面间隙挤压涂覆,调整涂布机逗号刮刀与涂布机料池带料辊的间隙为320μm左右,控制涂布速度为3m/min,得到正极片,单面涂覆量为188.1g/m2。取1470g去离子水(电阻率17.5mω·cm)加入到5000ml烧杯中,用砂磨机以500rpm的转速搅拌,加入13.8g羧甲基纤维素钠,加入羧甲基纤维素钠(cmc)后,将搅拌速度逐步提高至1200rpm并搅拌60min,再加入13.8g导电碳superpli,1600rpm的转速高速分散60min后,再加入1322.4g人造石墨,降低搅拌转速至1200rpm搅拌120min,然后降低搅拌速度至400rpm,加入72.0g丁苯胶乳(固含量为48%),搅拌60min后出料。将石墨负极浆料置于涂布机料槽中,设置烘箱温度为60℃、85℃、85℃、95℃和75℃,对应的热风量开启度分别为30%、70%、90%、80%和60%,在10μm厚的铜箔上进行双面间隙涂覆,调整涂布机逗号刮刀与涂布机料池带料辊的间隙为300μm左右,控制涂布速度为5m/min,得到正极片,单面涂覆量为90.9g/m2。以压实后(活性物质涂层密度为2.4g/cm3)的正极片作为分组对象,将正极片(长338.6mm、宽43.5mm)、隔膜(14μm厚,长729mm、宽45.5mm)和负极片(长352.9mm、宽43.5mm,活性物质涂层密度为1.5g/cm3)卷绕成裸电池,整理好后装入冲好坑(坑深4.2mm)的铝塑膜(dnp公司,115μm厚,长100.4mm,宽82.5mm)中,进行顶封(185℃/3s,宽度4mm),在85℃下干燥16h,注入3.0g电解液。侧封(195℃/4s,宽度4mm)后,制成383450型软包装锂离子电池。用lip-5ahb06型高温化成机以0.01c在0~3.85v充电,进行化成。化成后,以0.1c在3.0~4.2v充放电,进行容量测试。实验选用的电池设计容量约为580mah。应用例2:dcr测试通常dcr用于产线挑选制程异常锂离子电池及用于锂离子电池分组,实际上其也可以应用于对锂离子电池中材料性能的研究。参考iec-61960标准,将采用实施例1,实施例3,对比例1,对比例3正极材料制备的合格383450型电池焊接出引检测用极耳后,置于高温化成机在20±5℃下进行小电流(0.2c)放电至3.0v,再在常温下以0.5c充电至4.2v。并在该温度下静置4h,再将锂离子电池按100ma的电流放电10s测试该锂离子电池的开路电压u1,再将放电电流提高至1000ma放电1s后测试开路电压u2,按如下公式计算得到直流内阻。rdc=(u1-u2)/(i2-i1)将实施例1,实施例3,对比例1,对比例3制备得到的电池测试样品分别进行测试,得到表4的试验结果。表4实施例及对比例dcr测试结果由表4可见,对比例1的dcr为219mω,对比例3的dcr为232mω,而实施例1的dcr为162mω,实施例3的dcr为146mω。对比例1比实施例1的锂离子电池的dcr高35%,对比例3比实施例3的锂离子电池的dcr高59%。通常锂离子电池的dcr越高,表明该电池在放电时内部能量及功率损耗大,在类串接使用条件下相应的对外输出的能量及功率因数会降低,同时电池体发热量大。从上述结果看,实施例1和3添加了硼元素成份后制备的锂电池的离子电导率相对于对比例1和3方法制备锂离子电池有较大改善。应用例3:80℃/120h高温试验将实施例1,实施例2,对比例1,对比例2制备的383450型锂离子电池满充至4.2v,静置半小时后利用电阻率仪测试其开路电压、内阻,以及用游标卡尺测量电池厚度,然后将电池放入80℃恒温烘箱中放置120h,然后再取出电池冷却后再次用电阻率仪测试其开路电压、内阻,以及用游标卡尺测量电池厚度,得到如表5所示的结果。表5实施例及对比例80℃/120h高温试验结果由表5可见,实施例与对比例相比性能从容量可逆性,平台,内阻的可恢复性等方面看,对比例制备的锂离子电池的容量损失率及放电平台均出现了弱化,表明对比例制备的锂离子电池的可逆性性能变差,表明其电池体系以及对应正极材料的稳定性较差。通常锰酸锂电池的高温性能一直为大众所诟病,主要是锰酸锂的晶体结构是一种准尖晶石结构,由于结构的不完整导致对于锰元素的束缚力不足,在高温作用下锰离子会从正极中溶解出来并在电场作用下进入负极侧,并沉积在负极片上,导致电池高温条件下性能弱化。通过向其中添加硼或者铝元素可以稳定锰酸锂的结构,进而达到提升锰酸锂电池的电化学性能的目的。应用例4:3c/10v过充测试另取实施例1,实施例3,对比例1,对比例3制备的锂离子二次383450型软包装电池按gb/t31485-2015锂电池进行3c/10v过充测试得到如图1,图2及表6所示的结果。表6实施例及对比例钉刺实验结果由表6可见,对比例1和3制备的锂离子电池,在过充实验中出现了包装袋胀气碎裂,电解质泄漏,以及起火燃烧的现象,尽管检测到温度为500℃,但因使用的k型热电偶最高只能检测到500℃,实际的温升可能远大于500℃,从图2曲线中也可看出对比例3锂离子电池的温升非常快。在如此高的温度下,任何解决安全措施的防护均会失效,而实施例1和3制备的锂电池在过充试验中温度上升只有约150℃左右,尽管实施例3也出现了胀气电解质泄漏,但其并未起火燃烧,表明添加经硼及铝元素改性的锰酸锂材料安全性得到了进一步的提升,通常认为具有三维通道结构的钛酸锂及锰酸锂材料安全性较好,但进一步的实践表明当单体电池容量达到60ah以上时,再安全的材料也无济于事,另外在早期锂电池研究中在电解质中加入少量四氟硼酸锂也可以提升锂离子电池的性能,因此仍旧需要从其他角度进一步提升锂电池的安全性能,本发明的构思不失为一种可行的方案。综上所述,本发明通过在锰酸锂材料中引入硼等元素制备成改性的锰酸锂材料,电池的安全性能得到了一定的提升,同时对于锰的溶解也有一定程度的改善,在当前锂离子电池技术路线千差万别的情况下不失为扩展锰酸锂材料应用的一种好的技术方案。本发明所述制备方法经济可行,操作简单,效果明显,具有较好的应用前景。以上通过实施例描述了本发明的具体实施方式,本领域技术人员应理解的是,上文实施例仅出于举例的目的,不应认为以此限定本发明之保护范围,本领域技术人员在不脱离本发明精神的前提下可以对其进行修改、变化或替换,但是,依照本发明所作的各种等同变化,仍属于本发明所涵盖的范围。当前第1页1 2 3