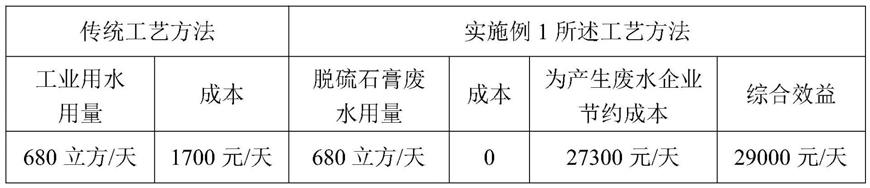
1.本发明涉及固废液废综合利用技术领域,尤其涉及脱硫石膏废水的综合利用方法。
背景技术:2.蒸压加气混凝土砌块是以粉煤灰、石灰、水泥、石膏、矿渣等为主要原料,加入适量发气剂、调节剂、气泡稳定剂、经配料搅拌、浇注、静停、切割和高压蒸养等工艺过程而制成的一种多孔混凝土制品。传统工艺技术主要采用粉煤灰、石灰、水泥为主要原材料,石膏、铝粉为辅助原材料,按照一定比例加入工业用水,搅拌混合后,进行静养发气,切割蒸压,此过程中使用的工业用水比例较大,平均用水量达到了340千克/立方砌块,耗水量成本较高。
技术实现要素:3.本发明的目的在于提供出一种固废液废利用、生产蒸压加气混凝土砌块的脱硫石膏废水的综合利用方法。
4.本发明所采用的技术方案为:脱硫石膏废水的综合利用方法,包括以下步骤:
5.步骤一:制浆过程:使用制浆搅拌器,加入重量为900
‑
1200kg的脱硫石膏废水、重量为1250
‑
1550kg的粉煤灰,搅拌30分钟,测量浆料扩散度达到19
‑
22cm,使用蒸汽将制浆温度加热到40
‑
50摄氏度;
6.步骤二:浇注过程:将步骤一制备好的浆料使用浆料泵打到浇注搅拌罐内,加入重量为280
‑
350kg的rgm混凝土增强剂浆料,再向浇注搅拌罐内加入重量为280
‑
350kg的白灰,加入重量为2.2
‑
2.7kg的铝粉,搅拌均匀后,将浆料浇注到高度为4.8m的模箱内;
7.步骤三:静养过程:将步骤二已经浇注浆料的模箱移动到静养间静止发气,静养间温度保持在50
±
5摄氏度,静养发气时间为80
‑
90分钟;
8.步骤四:切割过程:经过步骤三静养发气结束后,坯体达到具备切割的软硬度后,使用行车将模箱和坯体吊到切割机,按照客户需求的规格尺寸切割;
9.步骤五:蒸压过程:完成步骤四切割后的砌块坯体,使用行车进行编组进入蒸压釜内,通过压力为0.9
‑
1.2mpa、温度为175
‑
195摄氏度的蒸汽蒸压5
‑
6小时后,就可制出蒸压加气混凝土砌块成品。
10.所述脱硫石膏废水占比重的百分比计数为35
‑
45%,所述粉煤灰占比重的百分比计数为55
‑
65%。
11.所述模箱的体积为3.5立方。
12.所述蒸压加气混凝土砌块成品的出釜强度在3.5mpa以上、容量在625kg/m3以内。
13.所述rgm混凝土增强剂为赤泥与石膏的混合物,其中,赤泥的重量为84
‑
140kg、石膏的重量为168
‑
245kg;赤泥占比重的百分比计数为30
‑
40%、石膏占比重的百分比计数为60
‑
70%。
14.所述rgm混凝土增强剂的扩散度为19
‑
22cm。
15.所述石膏为白石膏、脱硫石膏、红石膏中的一种或多种。
16.所述赤泥与石膏过滤直径0.5cm以上的颗粒后,充分混合均匀制成rgm混凝土增强剂。
17.本发明的有益效果:
18.本发明是使用脱硫石膏废水代替工业用水,用于生产蒸压加气混凝土砌块,成本较低,性价比高,生产的蒸压加气混凝土砌块成品强度达标;利用火力发电厂、钛白粉厂等企业生产过程中产生的脱硫石膏废水,既解决了这些企业发展面临的环保难题,也为这些企业处理脱硫石膏废水节省了很大的成本。
具体实施方式
19.本发明不受下述实施例的限制,可根据本发明的技术方案与实际情况来确定具体的实施方式。
20.脱硫石膏废水的综合利用方法,包括以下步骤:
21.步骤一:制浆过程:使用制浆搅拌器,加入重量为900
‑
1200kg的脱硫石膏废水、重量为1250
‑
1550kg的粉煤灰,搅拌30分钟,测量浆料扩散度达到19
‑
22cm,使用蒸汽将制浆温度加热到40
‑
50摄氏度;
22.步骤二:浇注过程:将步骤一制备好的浆料使用浆料泵打到浇注搅拌罐内,加入重量为280
‑
350kg的rgm混凝土增强剂浆料,再向浇注搅拌罐内加入重量为280
‑
350kg的白灰,加入重量为2.2
‑
2.7kg的铝粉,搅拌均匀后,将浆料浇注到高度为4.8m的模箱内;
23.步骤三:静养过程:将步骤二已经浇注浆料的模箱移动到静养间静止发气,静养间温度保持在50
±
5摄氏度,静养发气时间为80
‑
90分钟;
24.步骤四:切割过程:经过步骤三静养发气结束后,坯体达到具备切割的软硬度后,使用行车将模箱和坯体吊到切割机,按照客户需求的规格尺寸切割;
25.步骤五:蒸压过程:完成步骤四切割后的砌块坯体,使用行车进行编组进入蒸压釜内,通过压力为0.9
‑
1.2mpa、温度为175
‑
195摄氏度的蒸汽蒸压5
‑
6小时后,就可制出蒸压加气混凝土砌块成品。
26.所述脱硫石膏废水占比重的百分比计数为35
‑
45%,所述粉煤灰占比重的百分比计数为55
‑
65%。
27.所述模箱的体积为3.5立方。
28.所述蒸压加气混凝土砌块成品的出釜强度在3.5mpa以上、容量在625kg/m3以内。
29.所述rgm混凝土增强剂为赤泥与石膏的混合物,其中,赤泥的重量为84
‑
140kg、石膏的重量为168
‑
245kg;赤泥占比重的百分比计数为30
‑
40%、石膏占比重的百分比计数为60
‑
70%。
30.所述rgm混凝土增强剂的扩散度为19
‑
22cm。
31.所述石膏为白石膏、脱硫石膏、红石膏中的一种或多种。
32.所述赤泥与石膏过滤直径0.5cm以上的颗粒后,充分混合均匀制成rgm混凝土增强剂。
33.实施例1:
34.本实施例所述蒸压加气混凝土砌块的生产工艺,包括以下步骤:
35.步骤一:制浆过程:使用制浆搅拌器,加入重量为1050kg的脱硫石膏废水、重量为1400kg的粉煤灰,搅拌30分钟,测量浆料扩散度达到19
‑
22cm,使用蒸汽将制浆温度加热到45摄氏度;
36.步骤二:浇注过程:将步骤一制备好的浆料使用浆料泵打到浇注搅拌罐内,加入重量为310kg的rgm混凝土增强剂浆料(扩散度19
‑
22cm),再向浇注搅拌罐内加入重量为310kg的白灰,加入重量为2.5kg的铝粉,搅拌均匀后,将浆料浇注到高度为4.8m的模箱(体积为3.5立方)内;
37.所述rgm混凝土增强剂为赤泥和石膏的混合物,其中,所述赤泥的重量为108.5kg、石膏的重量为201.5kg,赤泥占比重的百分比计数为35%、石膏占比重的百分比计数为65%;所述赤泥和石膏过滤掉直径0.5cm以上的颗粒后,再充分混合均匀,制得rgm混凝土增强剂;所述石膏为白石膏、脱硫石膏、红石膏中的一种或者几种。
38.步骤三:静养过程:将步骤二已经浇注浆料的模箱移动到静养间静止发气,静养间温度保持在50摄氏度,静养发气时间为85分钟;
39.步骤四:切割过程:经过步骤三静养发气结束后,坯体达到具备切割的软硬度后,使用行车将模箱和坯体吊到切割机,按照客户需求的规格尺寸切割;
40.步骤五:蒸压过程:完成步骤四切割后的砌块坯体,使用行车进行编组进入蒸压釜内,通过压力为1.1mpa、温度为185摄氏度的蒸汽蒸压5.5小时后,就可制出蒸压加气混凝土砌块成品。
41.实施例2:
42.本实施例所述蒸压加气混凝土砌块的生产工艺,包括以下步骤:
43.步骤一:制浆过程:使用制浆搅拌器,加入重量为900kg的脱硫石膏废水、重量为1250kg的粉煤灰,搅拌30分钟,测量浆料扩散度达到19
‑
22cm,使用蒸汽将制浆温度加热到42摄氏度;
44.步骤二:浇注过程:将步骤一制备好的浆料使用浆料泵打到浇注搅拌罐内,加入重量为280kg的rgm混凝土增强剂浆料(扩散度19
‑
22cm),再向浇注搅拌罐内加入重量为280kg的白灰,加入重量为2.2kg的铝粉,搅拌均匀后,将浆料浇注到高度为4.8m的模箱(体积为3.5立方)内;
45.所述rgm混凝土增强剂为赤泥和石膏的混合物,其中,所述赤泥的重量为84kg、石膏的重量为196kg,赤泥占比重的百分比计数为30%、石膏占比重的百分比计数为70%;所述赤泥和石膏过滤掉直径0.5cm以上的颗粒后,再充分混合均匀,制得rgm混凝土增强剂;所述石膏为白石膏、脱硫石膏、红石膏中的一种或者几种。
46.步骤三:静养过程:将步骤二已经浇注浆料的模箱移动到静养间静止发气,静养间温度保持在50摄氏度,静养发气时间为85分钟;
47.步骤四:切割过程:经过步骤三静养发气结束后,坯体达到具备切割的软硬度后,使用行车将模箱和坯体吊到切割机,按照客户需求的规格尺寸切割;
48.步骤五:蒸压过程:完成步骤四切割后的砌块坯体,使用行车进行编组进入蒸压釜内,通过压力为1.1mpa、温度为185摄氏度的蒸汽蒸压5.5小时后,就可制出蒸压加气混凝土砌块成品。
49.实施例3:
50.本实施例所述蒸压加气混凝土砌块的生产工艺,包括以下步骤:
51.步骤一:制浆过程:使用制浆搅拌器,加入重量为900kg的脱硫石膏废水、重量为1250kg的粉煤灰,搅拌30分钟,测量浆料扩散度达到19
‑
22cm,使用蒸汽将制浆温度加热到42摄氏度;
52.步骤二:浇注过程:将步骤一制备好的浆料使用浆料泵打到浇注搅拌罐内,加入重量为280kg的rgm混凝土增强剂浆料(扩散度19
‑
22cm),再向浇注搅拌罐内加入重量为280kg的白灰,加入重量为2.2kg的铝粉,搅拌均匀后,将浆料浇注到高度为4.8m的模箱(体积为3.5立方)内;
53.所述rgm混凝土增强剂为赤泥和石膏的混合物,其中,所述赤泥的重量为112kg、石膏的重量为168kg,赤泥占比重的百分比计数为40%、石膏占比重的百分比计数为60%;所述赤泥和石膏过滤掉直径0.5cm以上的颗粒后,再充分混合均匀,制得rgm混凝土增强剂;所述石膏为白石膏、脱硫石膏、红石膏中的一种或者几种。
54.步骤三:静养过程:将步骤二已经浇注浆料的模箱移动到静养间静止发气,静养间温度保持在50摄氏度,静养发气时间为85分钟;
55.步骤四:切割过程:经过步骤三静养发气结束后,坯体达到具备切割的软硬度后,使用行车将模箱和坯体吊到切割机,按照客户需求的规格尺寸切割;
56.步骤五:蒸压过程:完成步骤四切割后的砌块坯体,使用行车进行编组进入蒸压釜内,通过压力为1.1mpa、温度为185摄氏度的蒸汽蒸压5.5小时后,就可制出蒸压加气混凝土砌块成品。
57.实施例4:
58.本实施例所述蒸压加气混凝土砌块的生产工艺,包括以下步骤:
59.步骤一:制浆过程:使用制浆搅拌器,加入重量为1200kg的脱硫石膏废水、重量为1550kg的粉煤灰,搅拌30分钟,测量浆料扩散度达到19
‑
22cm,使用蒸汽将制浆温度加热到48摄氏度;
60.步骤二:浇注过程:将步骤一制备好的浆料使用浆料泵打到浇注搅拌罐内,加入重量为350kg的rgm混凝土增强剂浆料(扩散度19
‑
22cm),再向浇注搅拌罐内加入重量为350kg的白灰,加入重量为2.7kg的铝粉,搅拌均匀后,将浆料浇注到高度为4.8m的模箱(体积为3.5立方)内;
61.所述rgm混凝土增强剂为赤泥和石膏的混合物,其中,所述赤泥的重量为140kg、石膏的重量为210kg,赤泥占比重的百分比计数为40%、石膏占比重的百分比计数为60%;所述赤泥和石膏过滤掉直径0.5cm以上的颗粒后,再充分混合均匀,制得rgm混凝土增强剂;所述石膏为白石膏、脱硫石膏、红石膏中的一种或者几种。
62.步骤三:静养过程:将步骤二已经浇注浆料的模箱移动到静养间静止发气,静养间温度保持在50摄氏度,静养发气时间为85分钟;
63.步骤四:切割过程:经过步骤三静养发气结束后,坯体达到具备切割的软硬度后,使用行车将模箱和坯体吊到切割机,按照客户需求的规格尺寸切割;
64.步骤五:蒸压过程:完成步骤四切割后的砌块坯体,使用行车进行编组进入蒸压釜内,通过压力为1.1mpa、温度为185摄氏度的蒸汽蒸压5.5小时后,就可制出蒸压加气混凝土砌块成品。
65.实施例5:
66.本实施例所述蒸压加气混凝土砌块的生产工艺,包括以下步骤:
67.步骤一:制浆过程:使用制浆搅拌器,加入重量为1200kg的脱硫石膏废水、重量为1550kg的粉煤灰,搅拌30分钟,测量浆料扩散度达到19
‑
22cm,使用蒸汽将制浆温度加热到48摄氏度;
68.步骤二:浇注过程:将步骤一制备好的浆料使用浆料泵打到浇注搅拌罐内,加入重量为350kg的rgm混凝土增强剂浆料(扩散度19
‑
22cm),再向浇注搅拌罐内加入重量为350kg的白灰,加入重量为2.7kg的铝粉,搅拌均匀后,将浆料浇注到高度为4.8m的模箱(体积为3.5立方)内;
69.所述rgm混凝土增强剂为赤泥和石膏的混合物,其中,所述赤泥的重量为105kg、石膏的重量为245kg,赤泥占比重的百分比计数为30%、石膏占比重的百分比计数为70%;所述赤泥和石膏过滤掉直径0.5cm以上的颗粒后,再充分混合均匀,制得rgm混凝土增强剂;所述石膏为白石膏、脱硫石膏、红石膏中的一种或者几种。
70.步骤三:静养过程:将步骤二已经浇注浆料的模箱移动到静养间静止发气,静养间温度保持在50摄氏度,静养发气时间为85分钟;
71.步骤四:切割过程:经过步骤三静养发气结束后,坯体达到具备切割的软硬度后,使用行车将模箱和坯体吊到切割机,按照客户需求的规格尺寸切割;
72.步骤五:蒸压过程:完成步骤四切割后的砌块坯体,使用行车进行编组进入蒸压釜内,通过压力为1.1mpa、温度为185摄氏度的蒸汽蒸压5.5小时后,就可制出蒸压加气混凝土砌块成品。
73.选取产量为2000立方/天的蒸汽加压混凝土砌块工厂,采用传统工艺和实施例1所述工艺的成本数据见下表:
[0074][0075]
由此可见,本发明生产的蒸压加气混凝土砌块,使用脱硫石膏废水代替工业用水,每生产1立方蒸压加气混凝土砌块,比传统工艺方法节约成本0.85元,一个每天产量为2000立方的蒸压加气混凝土砌块工厂,每天可节省资金1700元,每年可节省60万元;本发明科学地利用了火力发电厂、钛白粉厂等企业生产过程中产生的脱硫石膏废水,既解决了这些企业发展面临的环保难题,也为这些企业处理脱硫石膏废水节省了很大的成本,目前这些企业处理脱硫石膏废水的传统方法成本为40元/立方;一个每天产量为2000立方的蒸压加气混凝土砌块工厂,利用该技术方法,每综合利用1立方脱硫石膏废水,可以节省上下游企业综合成本29000元/天。
[0076]
以上实施例仅用以说明本发明的技术方案,而非对其限制;尽管参照前述实施例对本发明进行了详细的说明,本领域的普通技术人员应当理解:其依然可以对前述实施例所记载的技术方案进行修改,或者对其中部分技术特征进行等同替换;而这些修改或者替换,并不使相应技术方案的本质脱离本发明实施例技术方案的精神和范围。