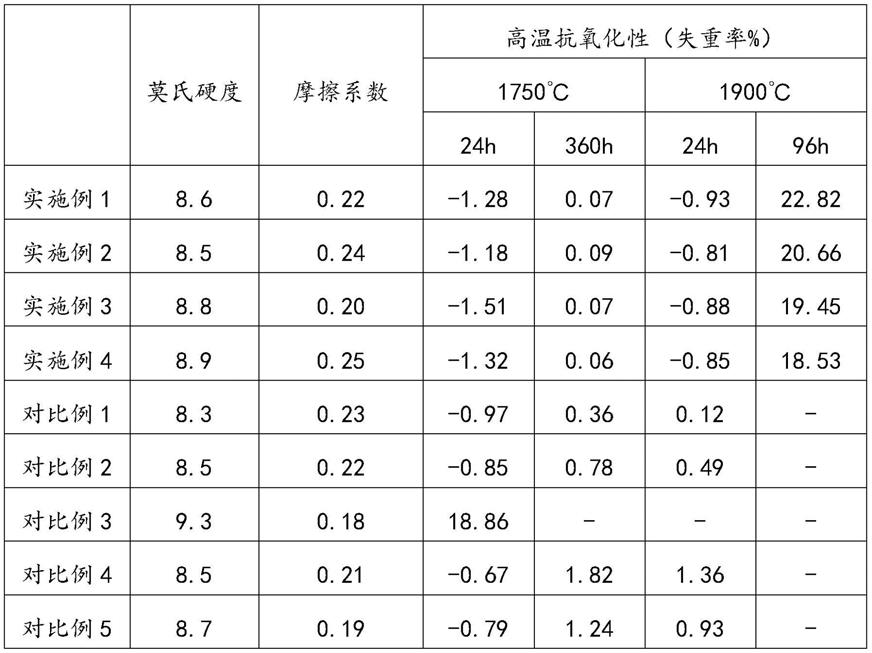
1.本发明属于碳基复合材料技术领域,尤其涉及一种高性能的碳碳坩埚表面涂层及其制备方法。
背景技术:2.随着各国政府和人民对资源、环境保护意识和力度的增强,太阳能这一绿色环保产业在我国发展突飞猛进,单晶硅炉的数量由2000年的800台左右迅速增加至现在的8000台左右,由此导致单晶硅炉必不可少的坩埚的需求急剧增长,从而也带动了碳/碳复合材料坩埚在单晶硅炉使用领域的快速发展。碳/碳复合材料坩埚,是由高强度纤维和炭素基质构成的复合材料加工而成的高技术产品,较之石墨制品节能、大幅度省材,且性能优异,具有长寿命、高比强度、耐高温、耐腐蚀、热膨胀系数小、耐急冷急热不变形不开裂等优良性能,是替代单晶炉石墨坩埚的理想的升级产品。
3.然而,由于碳/碳复合材料坩埚中的碳纤维是不被硅化的,则在坩埚表面可以看到一些不连续的小蚀坑。随着坩埚使用的进行,表面露出的碳纤维被磨平,这样使更里层的热解炭又会被硅化,如此反复进行,碳/碳复合材料逐渐变薄,其变薄的速度主要取决于热解炭的结构和拆炉清理时产生的摩擦。针对上述问题,目前通常使采用在碳/碳复合材料表面进行涂层处理,较为成熟的涂层方案是在碳/碳复合材料表层涂敷一层很薄的sic。sic材料的硬度高、热导率高、抗热震性好、化学稳定性高,同时它能与碳基体具有较好的热膨胀相容性,是一种优异的高温涂层,可有效提高碳碳复合材料的高温强度、抗高温氧化能力和抗高温冲击能力,延长了碳碳坩埚的使用寿命和耐损程度。
4.为了使碳/碳复合材料表面涂层能在更高温和更苛刻条件下使用,各国研发人员研究了复合涂层对碳/碳复合材料进行处理,通常采用sic
‑
al2o3‑
莫来石、sic/ar
‑
al
‑
si涂层、si
‑
mo涂层、sic
‑
wsi2/mosi2等涂层体系。然而,目前的复合涂层在高温氧化环境下,生成的sio2保护膜能有效的阻挡氧气的渗入,但是随着氧化温度的升高和氧化时间的延长,目前研究的外涂层高温抗氧化能力均不太理想(现有的复合涂层最佳可达到的抗氧化温度为1650℃),而内涂层生成的sio2黏度降低,挥发严重,保护膜表面生成空洞或者气孔等缺陷,从而使涂层丧失氧化保护能力。
技术实现要素:5.本发明的目的是提供一种高性能的碳碳坩埚表面涂层,该涂层具有优异的高温强度、高温韧性和高耐磨性,并且抗热震性好、化学稳定性好,同时与碳碳基体具有较高的热膨胀相容性,显著提高了碳碳坩埚的使用寿命和耐损程度,且使碳碳坩埚能在1750℃下长期抗氧化使用。
6.为了实现本发明的目的,本发明提供了一种高性能的碳碳坩埚表面涂层,所述涂层主要通过先在碳碳坩埚的基底上先后沉积一层sic过渡层和一层lab6/y3al5o
12
外涂层,所述sic过渡层采用包埋法沉积,所述lab6/y3al5o
12
外涂层采用料浆法涂覆而成。
7.本发明以sic为内涂层,其与碳碳坩埚的热膨胀系数相差小,且具有优异的抗高温氧化性能和耐腐蚀性,在高温氧化环境下生成的sio2,能阻止氧气的渗入,采用lab6/y3al5o
12
复合层作为外涂层,即在sic过渡层外涂覆lab6和y3al5o
12
的复合层,可提高表面涂层的强度、耐高温性能,也能降低氧渗透力,从而可显著提高碳碳坩埚的高温使用温度,使其在1750℃下能长期抗氧化,提高了碳碳坩埚的使用寿命,同时,使本发明具有更佳优异的力学强度和耐腐蚀性。
8.进一步的,所述sic过渡层的厚度为120~200μm,所述lab6/y3al5o
12
外涂层的厚度为150~180μm。
9.本发明sic过渡层厚度若低于120μm,则降低了表面涂层的高温抗氧化能力,使其在1750℃下氧化失重率较高,无法长期有效的隔绝氧气;若厚度高于200μm,并不会随着厚度的增加,而对抗氧化能力有更好的改善,反而增加了成本。本发明lab6/y3al5o
12
外涂层的厚度若低于150μm,则不能有效地使碳碳坩埚在较高的温度下,保证较长时间的抗氧化能力,并且厚度较低,易使sio2在较长时间的高温下,易挥发,从而影响碳碳坩埚的高温抗氧化性能和使用寿命;若厚度高于180μm,并不会随着厚度的增加,而对抗氧化能力和对sic过渡层有更好的改善和保护,反而增加了成本。
10.本发明还提供了一种高性能的碳碳坩埚表面涂层的制备方法,包括以下步骤:
11.(1)基体预处理:将碳碳坩埚置于配置有乙醇的容器中,放入超声波清洗器中清洗,超声10~20min,重复清洗3次,以清除碳碳坩埚表面的污渍。
12.(2)将si粉、c粉和b2o3粉置于球磨机中,球磨15~20h,得均匀的a粉料;将si粉、c粉和al2o3粉置于球磨机中,球磨15~20h,得均匀的b粉料。
13.(3)将a粉料置于石墨反应装置中,然后将预处理后的碳碳坩埚埋入a粉料中进行一次包埋处理;在氩气的环境下,将温度升至2100~2200℃,反应2~3h,降至室温;再将一次包埋后的碳碳坩埚埋入b粉料中进行多次包埋处理。
14.本发明采用si粉、c粉和b2o3粉作为a料对碳碳坩埚进行首次包埋,b2o3粉起到一定的催化剂作用,催化si和c反应,但主要目的使促进si粉渗透,使其渗透入碳碳基体中,增加了sic过渡层与碳碳基体间的相容性,使其与碳碳坩埚结合紧密,也减少了碳碳复合材料晶体中间隙和孔洞,使得sic涂层更加致密。本发明采用si粉、c粉和al2o3粉作为b料,对碳碳坩埚进行第二次包埋或多次包埋,al2o3粉主要起到催化剂的作用,催化si和c反应,并且在界面处反应,增强涂层与碳碳基体的结合强度,在高温烧结过程中,首次包埋过程中的b2o3粉熔点低,具有良好的流动性,可以进一步将粉体带入包埋后的涂层孔隙中,使得本发明的sic涂层更加致密,降低了本发明高温条件下,氧气的渗入,因此,该包埋工艺也提高了碳碳坩埚表面涂层的强度和高温抗氧化性能。
15.(4)将多次包埋处理后的碳碳坩埚浸渍于有机硅浸渍剂中,在90~100℃下浸渍3~4h,经过滤,干燥,得待处理碳碳坩埚。
16.使用包埋法得到的sic过渡层比较致密,但均匀性不太好,因此,本发明采用有机硅浸渍剂进行处理,浸渍剂中的硅烷小分子结构可均匀作用于sic过渡层,与sic过渡层有着良好的亲和力,能轻易渗透到碳碳基层内部,经过高温浸渍,可解决过渡层均匀性不好,且提高过渡层与外涂层、过渡层与碳碳基体间的粘结性,从而进一步提高表面涂层的使用寿命。
17.(5)外涂层料浆的配制:将b粉、la2o3粉、y3al5o
12
粉和al粉按适当比例混合均匀,置于球磨机中,球磨12~24h,过300目筛网;然后获得的混合粉末与粘结剂、水混合,用磁力搅拌成料浆,再将料刷将料浆均匀涂刷在待处理碳碳坩埚表面,干燥,然后置于高温热压炉中进行热处理,获得所需的碳碳坩埚表面涂层。
18.本发明的b粉和la2o3粉在高温热压炉中,在al粉的作用下,反应生成lab6,并与y3al5o
12
粉在粘结剂的作用下,生成lab6/y3al5o
12
涂层。本发明中采用的钇铝石榴石(y3al5o
12
)的熔点较高(1950℃),并且热膨胀系数与sic相近,与过渡层有较好的结合力,该钇铝石榴石与lab6晶体在高温下作用生成的涂层,有优异的高温抗氧化能力,延长了碳碳坩埚的使用寿命,且能在1750℃下长期使用。
19.进一步的,所述步骤(2)中a粉料的si粉、c粉和b2o3粉质量比为(3.5~4.5):1:(0.6~0.8)。
20.进一步的,所述步骤(2)中b粉料的si粉、c粉和al2o3粉质量比为(3.5~4.5):1:1。
21.进一步的,所述步骤(3)中一次包埋处理的过程为:将预处理后的碳碳坩埚埋入a粉料中,在氩气的氛围下,将温度升至2100~2200℃,反应2~3h,然后以10~15℃/min的速率冷却至室温。
22.进一步的,所述步骤(3)中所述多次包埋处理是指将一次包埋后的碳碳坩埚埋入b粉料中进行一次及以上的包埋处理,以达到所需厚度的sic过渡层,其包埋处理过程为:将一次包埋后的碳碳坩埚埋入b粉料中,在氩气的氛围下,将温度升至1900~2000℃,反应2~3h,然后以8~10℃/min的速率冷却至室温。
23.进一步的,所述步骤(5)中,所述b粉、la2o3粉、y3al5o
12
粉和al粉的质量比为(1~2):(3~4):1:(0.2~0.3)。
24.进一步的,所述步骤(5)中,所述粘结剂的质量为所述混合粉末质量的3~5%;所述水的质量为所述混合粉末质量的1.5~3倍。
25.进一步的,所述步骤(5)中,所述热处理过程为:将高温热压炉中的压力设置为10~15mpa,先以3~5℃/min的速率升温至150~200℃,保温1.5~2h;然后以5~10℃/min的速率升温至500~700℃,保温2~3h;再以3~5℃/min的速率升温至1500~1700℃,保温6~8h,自然冷却至室温。
26.本发明采用多段热处理,其作用为:在低温150~200℃时,可使有机硅浸渍剂作用于过渡层与外涂层粘结效果好,并能有效作用于两个涂层中,并且在低温下使水分和气体挥发掉,减少快速加热条件下孔隙的增加,提高了表面涂层的致密度,减少分布不均的情况发生;500~700℃过程中,使有机成分炭化,能进一步提高表面涂层的致密度;1500~1700℃烧结过程中,使lab6和y3al5o
12
晶体间相互作用、相互融合,并与过渡层间相互渗透,提高外涂层与过渡层之间的结合力,减少表面涂层内部的孔隙率,降低氧气的渗透,从而提高了碳碳坩埚的使用寿命和高温抗氧化力。
27.本发明取得了以下有益效果:
28.1、本发明采用sic作为过渡层,以lab6/y3al5o
12
复合层作为外涂层,显著提高了表面涂层与碳碳坩埚间的结合力,提高了表面涂层的高温强度、高温抗氧化性能、耐磨性、抗震性和韧性。sic过渡层采用多次包埋法制备,制备方法简单,可提高过渡层的致密度,减少过渡层的孔隙率,降低氧气渗入率,以此来进一步提高高温使用寿命。lab6/y3al5o
12
复合层
采用耐高温的lab6和y3al5o
12
制得,并将两者结合,使其作用与碳碳坩埚的外涂层,其在保证较高的硬度和强度的同时,还使本发明具有优异的高温抗氧化能力,扩大了碳碳坩埚的高温使用范围。
29.2、本发明采用有机硅浸渍剂对sic过渡层进行浸渍处理,改善了包埋法制得的过渡层不均匀性,并提高了过渡层与外涂层、碳碳基体间的结合力,进一步提高了本发明的强度和韧性,也延长了本发明的使用寿命。
30.3、本发明采用多段热处理方法,减少了表面涂层内部的孔隙率,降低氧气的渗透,提高了碳碳坩埚的使用寿命和高温抗氧化力。
31.4、本发明的表面涂层是采用包埋法和料浆法复合制备而成,使用包埋法制得过渡层,然后采用料浆法在外涂层浆料涂刷在过渡层上,制备方法简单,且易操作,涂层厚度易控制,适合于产业化生产。
具体实施方式
32.下面对本发明实施例中的技术方案进行清楚、完整地描述,显然,所描述的实施例仅是本发明一部分实施例,而不是全部的实施例。基于本发明中的实施例,本领域普通技术人员在没有做出创造性劳动前提下所获得的所有其它实施例,都属于本发明保护的范围。
33.本发明中使用的有机硅浸渍剂为青岛卓能达建筑科技有限公司提供的。
34.下面结合具体实施例对本发明的高性能的碳碳坩埚表面涂层预以说明。
35.实施例1
36.本实施例中提供的碳碳坩埚表面涂层是由sic过渡层和lab6/y3al5o
12
外涂层,其是先在碳碳坩埚的表面采用包埋法沉积sic过渡层,然后再通过料浆法涂覆lab6/y3al5o
12
外涂层。该碳碳坩埚表面涂层的制备方法,包括以下步骤:
37.(1)基体预处理:将碳碳坩埚置于配置有乙醇的容器中,放入超声波清洗器中清洗,超声15min,重复清洗3次,以清除碳碳坩埚表面的污渍。
38.(2)将si粉、c粉和b2o3粉置于球磨机中,球磨速率为600r/min,以去离子水为介质,球磨18h,干燥,得均匀的a粉料;将si粉、c粉和al2o3粉置于球磨机中,球磨速率为600r/min,以去离子水为介质,球磨18h,得均匀的b粉料。
39.(3)将a粉料置于石墨反应装置中,然后将预处理后的碳碳坩埚埋入a粉料中,在氩气的氛围下,将温度升至2200℃,反应3h,然后以10℃/min的速率冷却至室温。再将一次包埋后的碳碳坩埚埋入b粉料中,在氩气的氛围下,将温度升至2000℃,反应3h,然后以10℃/min的速率冷却至室温。再以上述相同的方法将包埋后的碳碳坩埚埋入b粉料中进行再一次包埋,即可。
40.(4)将三次包埋处理后的碳碳坩埚浸渍于有机硅浸渍剂中,在90℃下浸渍4h,经过滤,干燥,得待处理碳碳坩埚。
41.(5)外涂层料浆的配制:将b粉、la2o3粉、y3al5o
12
粉和al粉按适当比例混合均匀,置于球磨机中,球磨速率为800r/min,以去离子水为介质,球磨24h,干燥,过300目筛网,得混合粉末;然后将混合粉末与粘结剂、去离子水混合,用磁力搅拌成料浆,再用料刷将料浆均匀涂刷在待处理碳碳坩埚表面,置于90℃的烘箱中干燥3h,然后置于高温热压炉中进行热处理,获得所需的碳碳坩埚表面涂层。
42.本实施例中,a粉料的si粉、c粉和b2o3粉质量比为3.5:1:0.6。
43.本实施例中,b粉料的si粉、c粉和al2o3粉质量比为3.5:1:1。
44.本实施例中,b粉、la2o3粉、y3al5o
12
粉和al粉的质量比为1:3:1:0.2。
45.本实施例的步骤(5)中,使用的粘结剂为聚乙烯醇缩丁醛,该粘结剂的使用质量为混合粉末质量的3%,使用的去离子水的质量为混合粉末质量的1.5倍。
46.本实施例的步骤(5)的热处理过程为:将高温热压炉中的压力设置为10mpa,先以3℃/min的速率升温至200℃,保温1.5h;然后以5℃/min的速率升温至700℃,保温2h;再以3℃/min的速率升温至1700℃,保温6h,自然冷却至室温。
47.实施例2
48.本实施例中提供的碳碳坩埚表面涂层的组成、配方和制备方法与实施例1中相同,不同的如下所示:
49.本实施例中,a粉料的si粉、c粉和b2o3粉质量比为4.5:1:0.8。
50.本实施例中,b粉料的si粉、c粉和al2o3粉质量比为4.5:1:1。
51.本实施例中,b粉、la2o3粉、y3al5o
12
粉和al粉的质量比为2:4:1:0.3。
52.本实施例的步骤(5)中,使用的粘结剂为聚乙烯醇缩丁醛,该粘结剂的使用质量为混合粉末质量的5%,使用的去离子水的质量为混合粉末质量的3倍。
53.本实施例的步骤(5)的热处理过程为:将高温热压炉中的压力设置为15mpa,先以5℃/min的速率升温至150℃,保温2h;然后以10℃/min的速率升温至500℃,保温3h;再以5℃/min的速率升温至1500℃,保温8h,自然冷却至室温。
54.实施例3
55.本实施例中提供的碳碳坩埚表面涂层的组成、配方和制备方法与实施例1中相同,不同的如下所示:
56.本实施例中,a粉料的si粉、c粉和b2o3粉质量比为4:1:0.7。
57.本实施例中,b粉料的si粉、c粉和al2o3粉质量比为4:1:1。
58.本实施例中,b粉、la2o3粉、y3al5o
12
粉和al粉的质量比为1:4:1:0.2。
59.本实施例的步骤(5)中,使用的粘结剂为聚乙烯醇缩丁醛,该粘结剂的使用质量为混合粉末质量的4%,使用的去离子水的质量为混合粉末质量的2倍。
60.本实施例的步骤(5)的热处理过程为:将高温热压炉中的压力设置为12mpa,先以4℃/min的速率升温至180℃,保温2h;然后以8℃/min的速率升温至600℃,保温3h;再以4℃/min的速率升温至1600℃,保温7h,自然冷却至室温。
61.实施例3
62.本实施例中提供的碳碳坩埚表面涂层的组成、配方和制备方法与实施例1中相同,不同的如下所示:
63.本实施例中,a粉料的si粉、c粉和b2o3粉质量比为4.5:1:0.6。
64.本实施例中,b粉料的si粉、c粉和al2o3粉质量比为4.2:1:1。
65.本实施例中,b粉、la2o3粉、y3al5o
12
粉和al粉的质量比为1.5:4:1:0.2。
66.本实施例的步骤(5)中,使用的粘结剂为聚乙烯醇缩丁醛,该粘结剂的使用质量为混合粉末质量的5%,使用的去离子水的质量为混合粉末质量的2.5倍。
67.本实施例的步骤(5)的热处理过程为:将高温热压炉中的压力设置为15mpa,先以5
℃/min的速率升温至180℃,保温2h;然后以5℃/min的速率升温至700℃,保温3h;再以3℃/min的速率升温至1700℃,保温6h,自然冷却至室温。
68.对比例1
69.一种碳碳坩埚表面涂层,其组成、原料和制备方法均与实施例4中相同,不同的是,本对比例中未使用a料对碳碳坩埚进行包埋处理,仅使用b料对碳碳坩埚进行三次包埋处理,而得到与实施例4中sic过渡层相同的厚度。
70.对比例2
71.一种碳碳坩埚表面涂层,其组成、原料和制备方法均与实施例4中相同,不同的是,本对比例中未采用有机硅浸渍剂对碳碳坩埚进行浸渍处理。
72.对比例3
73.一种碳碳坩埚表面涂层,其组成、原料和制备方法均与实施例4中相同,不同的是,本对比例中表面涂层为sic涂层,即没有有机硅浸渍剂的处理和没有涂覆外涂层,仅对碳碳坩埚表面进行了sic包埋处理。
74.对比例4
75.一种碳碳坩埚表面涂层,其组成、原料和制备方法均与实施例4中相同,不同的是,本对比例的外涂层原料未加入y3al5o
12
粉。
76.对比例5
77.一种碳碳坩埚表面涂层,其组成、原料和制备方法均与实施例4中相同,不同的是,本对比例的热处理过程为:将高温热压炉中的压力设置为15mpa,以10℃/min的速率升温至1700℃,保温8h,自然冷却至室温。
78.值得注意的是,本发明中优选的,sic过渡层的厚度为120~200μm,lab6/y3al5o
12
外涂层的厚度为150~180μm。并且,本发明实施例和对比例中的外涂层厚度均为170
±
2μm,sic过渡层的厚度为150
±
2μm。
79.将上述实施例1
‑
4和对比例1
‑
5制得的碳碳坩埚的表面涂层进行致密度、弯曲强度、断裂韧性的进行测试,检测结果见表1。
80.表1碳碳坩埚表面涂层的力学性能检测结果
81.致密度(%)弯曲强度(mpa)断裂韧性(mpa.m
1/2
)实施例196.37095.2实施例295.46964.6实施例395.87155.3实施例496.57285.1对比例191.56584.1对比例293.76523.5对比例389.84782.9对比例493.26033.8对比例590.25833.2
82.根据以上实施例1
‑
4和对比例1
‑
5的表1的对比实验结果,可以看出,本发明的致密度高,弯曲强度和断裂韧性值较高,即表main涂层的致密度和力学性能均很好,且包埋方法、有机硅浸渍剂、外涂层的组分以及热处理方式均对致密度和力学性能的影响较大。
83.将上述实施例1
‑
4和对比例1
‑
5制得的碳碳坩埚的表面涂层进行硬度、耐摩擦性能、力学性能和高温抗氧化性能进行测试,检测结果见表2。
84.硬度:采用hv
‑
1000型维氏硬度计测量,试验力为100gf,正四棱锥金刚石压头,随机检测6个不同位置的点,取去除一个最大值和一个最小值后的平均数为表面硬度。
85.耐摩擦性能:高温摩擦磨损试验机检测,载荷20n,干磨条件下对摩球为sic。
86.高温抗氧化性测试方法为:涂层的氧化实验在高温管式炉中的静态空气中进行,将带有涂层的碳碳坩埚试样置于刚玉坩埚中,随后将坩埚放入已到达设定温度的管式炉中。每隔一段时间将坩埚取出,冷却后称取试样重量,再将坩埚放回管式炉中,如此反复直至达到预定实验时间。失重率=(原试样重量
‑
高温处理后的试样重量)/原试样重量
×
100%,其中,原试样重量和试样重量均是指表面涂层重量。
87.表2碳碳坩埚表面涂层的其它性能检测结果
[0088][0089]
根据以上实施例1
‑
4和对比例1
‑
5的表2的对比实验结果,可以看出,本发明具有优异的高温抗氧化性能,且能在1750℃下长期使用,且包埋方法、有机硅浸渍剂、外涂层的组分以及热处理方式均对本发明涂层的高温抗氧化性能的影响较大。
[0090]
以上所述实施例的各技术特征可以进行任意组合,为使描述简洁,未对上述实施例中的各个技术特征所有可能的组合都进行描述,然而,只要这些技术特征的组合不存在矛盾,都应当认为是本说明书记载的范围。
[0091]
以上所述实施例仅表达了本发明的几种实施方式,其描述较为具体和详细,但并不能因此而理解为对本发明专利范围的限制。应当指出的是,对于本领域的普通技术人员来说,在不脱离本发明构思的前提下,还可以做出若干变形和改进,这些都属于本发明的保护范围。