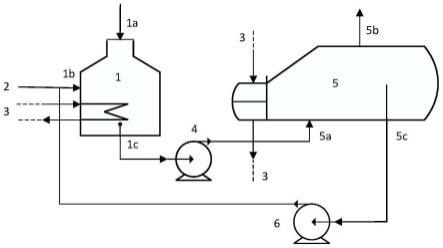
1.本发明属于氨气制备技术领域,涉及一种碳酸氢铵溶液循环分解制氨系统及方法。
背景技术:2.no
x
是造成大气污染、光化学烟雾、酸雨的主要根源之一。根据“超净排放”标准,2020年之前燃煤锅炉的no
x
排放必须降至50mg/nm3以下,这对脱硝技术提出了严格的要求。在众多脱硝技术中,利用氨气作为还原剂的选择性催化还原(scr)脱硝工艺效率高应用广泛。
3.目前,脱硝系统常用的制氨试剂包括液氨、氨水和尿素三种。液氨法虽然具有成本低、系统简单等优点,但氨是国家规定的乙类危险品,存在重大安全隐患。液氨在运输和储存过程中都存在一定的危险性,遇到明火极易燃烧和爆炸,极大地限制了其工业应用。氨水也是一种危险化学品,低浓度的氨水刺激眼睛、皮肤和呼吸系统。氨水的含氨量低,造成运输体积大,运输成本比液氨高,且需要大型存储设备,氨气制备时也需要消耗大量热能。因此,在scr脱硝技术中很少使用氨水法。尿素法的主要优势在于其安全性,但尿素原料成本高,且系统的投资和运行成本都要高于液氨系统。此外,尿素分解可能生成异氰酸和缩二脲等副产物,异氰酸是引起设备管道腐蚀的主要因素,而缩二脲不溶于水,与飞灰一起造成设备以及scr催化剂的堵塞甚至中毒。
4.随着=烟气净化技术的不断发展,国家和地方对于脱硝系统还原剂的安全性提出了新的要求。为了积极响应国家政策,加强对危险化学品的治理改造,急需研究开发在满足安全要求的基础上,更加高效经济的新型脱硝还原剂。
5.碳酸氢铵常温常压下以固态颗粒储存,是我国除了尿素之外的第二大氮肥,来源广泛。与液氨和氨水相比,碳酸氢铵在储存和运输方面不存在安全问题。与尿素相比,碳酸氢铵分解温度低,在100℃以下就可以从颗粒态直接热解生成氨气,且热解速度随温度升高迅速增大;同时,碳酸氢铵比尿素价格便宜,因此碳酸氢铵制氨系统潜在经济性更好。
6.目前,利用碳酸氢铵作为scr制氨试剂的技术方案和系统中,主要可以分为固体热解制氨和溶液湿法制氨两类。其中,固体热解法通过文丘里混合器和送粉风机来实现碳酸氢铵进料控制(cn200910086856、cn201010276538),在实际运行中会出现碳酸氢铵给料不均匀,制备的氨气容易出现波动,影响到最终的脱硝效果。
7.表1
[0008][0009]
溶液湿法制氨工艺主要通过将高浓度的碳酸氢铵溶液在热解炉中(cn201010194802)或直接喷入脱硝段烟道内(cn202111307077)完全分解,实现氨气制备。
这类工艺有以下几个缺陷:
①
未考虑到碳酸氢铵溶解度低的问题(cn202111307077),在40℃储存时的碳酸氢铵饱和溶液浓度只有26%(表1),这导致在后续加热分解时水蒸发会浪费大量的热能。
②
未考虑到碳酸氢铵溶液在储存时分解的可能(cn201010194802),碳酸氢铵溶液在90℃储存时,虽然溶解度有很大的提升,但是会导致大量氨气的逸出(表1),存在储存风险,同时也会造成原料的浪费。
③
未考虑到碳酸氢铵溶液分解的能耗主要来自于水的蒸发,碳酸氢铵溶液在接近水的沸点时(》90℃)才开始显著分解,随着分解率的提升水的蒸发率也逐渐提升;现有工艺以碳酸氢铵溶液完全分解为目标,此时溶液中的水蒸发吸热产生的能耗很大,导致碳酸氢铵制氨工艺的经济性较差。
技术实现要素:[0010]
本发明的目的在于克服上述现有技术的缺点,提供了一种碳酸氢铵溶液循环分解制氨系统及方法,该系统及方法具有热量损失小、氨气不易逸出及经济性较好的特点。
[0011]
为达到上述目的,本发明所述的碳酸氢铵溶液循环分解制氨系统包括溶液储罐、补充水入口、第一加热装置、第二加热装置及反应器;
[0012]
溶液储罐内设置有第一加热装置,补充水入口与溶液储罐上的储罐液体入口相连通,溶液储罐的顶部设置有碳酸氢铵固体加料口,溶液储罐侧面上的储罐溶液出口与反应器底部的反应器溶液入口相连通,反应器侧面的反应器溶液出口与溶液储罐上的储罐液体入口相连通。
[0013]
所述第一加热装置及第二加热装置为蒸汽盘管或者电加热器。
[0014]
所述第一加热装置及第二加热装置为蒸汽盘管。
[0015]
溶液储罐侧面上的储罐溶液出口经进料泵与反应器底部的反应器溶液入口相连通。
[0016]
反应器侧面的反应器溶液出口经循环泵与溶液储罐上的储罐液体入口相连通。
[0017]
本发明所述的碳酸氢铵溶液循环分解制氨方法包括以下步骤:
[0018]
1)将碳酸氢铵固体经碳酸氢铵固体加料口投入溶液储罐中,补充水及循环溶液混合后经储罐液体入口进入溶液储罐中,以配制碳酸氢铵溶液;
[0019]
2)通过第一加热装置加热溶液储罐内的碳酸氢铵溶液并维持在预设温度范围内,使碳酸氢铵固体完全溶解;
[0020]
3)将碳酸氢铵溶液从储罐溶液出口流出,再进入到反应器中,反应器中设置有第二加热装置,控制反应器内的反应温度在90℃以下,控制碳酸氢铵溶液的一次转化率小于60%;
[0021]
4)反应器内反应产生的产品气经产品气出口排出,反应后的碳酸氢铵溶液经反应器溶液出口排出,再循环回到溶液储罐中再次利用。
[0022]
步骤2)中的预设温度范围为60-80℃,溶液储罐内的压力为常压。
[0023]
步骤3)中反应器内的反应温度为84-88℃,反应器内的反应压力为常压。
[0024]
步骤3)中碳酸氢铵溶液的一次转化率在20-60%之间。
[0025]
本发明具有以下有益效果:
[0026]
本发明所述的碳酸氢铵溶液循环分解制氨系统及方法在具体操作时,利用较高浓度的碳酸氢铵溶液在系统中循环利用发生分解反应,通过降低碳酸氢铵溶液在反应器中的
一次转化率,限制水的蒸发吸热,减小系统能耗,热量损失小,提升碳酸氢铵溶液制氨的经济性;在溶液储罐中,通过第一加热装置控制溶液存储温度,在保证碳酸氢铵完全溶解的情况下,不产生显著的分解损失,氨气不易逸出。
附图说明
[0027]
图1为本发明的结构示意图。
[0028]
其中,1为溶液储罐、2为补充水入口、31为第一加热装置、32为第二加热装置、4为进料泵、5为反应器、6为循环泵、1a为碳酸氢铵固体加料口、1b为储罐液体入口、1c为储罐溶液出口、5a为反应器溶液入口、5b为产品气出口、5c为反应器溶液出口。
具体实施方式
[0029]
为了使本技术领域的人员更好地理解本发明方案,下面将结合本发明实施例中的附图,对本发明实施例中的技术方案进行清楚、完整地描述,显然,所描述的实施例仅仅是本发明一部分的实施例,不是全部的实施例,而并非要限制本发明公开的范围。此外,在以下说明中,省略了对公知结构和技术的描述,以避免不必要的混淆本发明公开的概念。基于本发明中的实施例,本领域普通技术人员在没有做出创造性劳动前提下所获得的所有其他实施例,都应当属于本发明保护的范围。
[0030]
在附图中示出了根据本发明公开实施例的结构示意图。这些图并非是按比例绘制的,其中为了清楚表达的目的,放大了某些细节,并且可能省略了某些细节。图中所示出的各种区域、层的形状及它们之间的相对大小、位置关系仅是示例性的,实际中可能由于制造公差或技术限制而有所偏差,并且本领域技术人员根据实际所需可以另外设计具有不同形状、大小、相对位置的区域/层。
[0031]
实施例一
[0032]
参考图1,本发明所述的碳酸氢铵溶液循环分解制氨系统包括溶液储罐1、补充水入口2、第一加热装置31、第二加热装置32、进料泵4、反应器5及循环泵6;
[0033]
溶液储罐1内设置有第一加热装置31,补充水入口2与溶液储罐1上的储罐液体入口1b相连通,溶液储罐1的顶部设置有碳酸氢铵固体加料口1a,溶液储罐1侧面上的储罐溶液出口1c经进料泵4与反应器5底部的反应器溶液入口5a相连通,反应器5侧面的反应器溶液出口5c经循环泵6与溶液储罐1上的储罐液体入口1b相连通。
[0034]
反应器5的顶部设置有产品气出口5b,反应器5内设置有第二加热装置32,所述第一加热装置31及第二加热装置32为蒸汽盘管或者电加热器,优选的,第一加热装置31及第二加热装置32为蒸汽盘管,用于维持溶液温度并提供反应热量。
[0035]
本发明所述的碳酸氢铵溶液循环分解制氨方法包括以下步骤:
[0036]
1)将碳酸氢铵固体从碳酸氢铵固体加料口1a投入溶液储罐1中溶解,补充水及循环溶液混合后从储罐液体入口1b进入溶液储罐1中,以配制碳酸氢铵溶液;
[0037]
2)通过第一加热装置31加热溶液储罐1内的碳酸氢铵溶液并维持在预设温度范围内,使碳酸氢铵固体完全溶解,同时不发生显著分解;
[0038]
3)将碳酸氢铵溶液从储罐溶液出口1c流出,再经进料泵4进入到反应器5中,反应器5中设置有第二加热装置32,控制反应器5内的反应温度在90℃以下,控制碳酸氢铵溶液
的一次转化率小于60%;
[0039]
4)反应器5内反应产生的产品气经产品气出口5b排出,用于脱硝还原反应,反应后的碳酸氢铵溶液经反应器溶液出口5c排出,再经循环泵6循环回到溶液储罐1中再次利用。
[0040]
步骤2)中的预设温度范围为60-80℃,溶液储罐1内的压力为常压。
[0041]
步骤3)中反应器5内的反应温度为84-88℃,最优选为85-87℃,反应器5内的反应压力为常压。
[0042]
步骤3)中碳酸氢铵溶液的一次转化率在20-60%之间,最优选为35-45%之间。
[0043]
第一加热装置31及第二加热装置32为加热盘管或电加热器,优选的,利用工厂或电厂90-120℃之间低温蒸汽或烟气的加热盘管,对低品位热源的余热进行回收利用。
[0044]
实施例二
[0045]
本实施例以18kmol/h产氨量为目标,补充的18kmol/h碳酸氢铵固体从碳酸氢铵固体加料口1a投入溶液储罐1中溶解,23kmol/h的补充水和循环溶液混合后从储罐液体入口1b进入溶液储罐1,配成质量分数为42%的碳酸氢铵溶液。溶液储罐1内设置有蒸汽盘管,使溶液储罐1内温度维持在70℃,此时碳酸氢铵固体完全溶解,同时不发生显著分解。碳酸氢铵溶液从储罐溶液出口1c流出,经进料泵4进入到反应器5,反应器5中底部设置蒸汽盘管,控制反应器5内的反应温度在86℃。反应产生的气体从上方气体出口排出,用于脱硝还原反应,反应后的碳酸氢铵溶液从反应器溶液出口5c排出,经循环泵6循环回到溶液储罐1,溶液储存和反应均在常压下进行,蒸汽盘管中加热蒸汽温度为110℃。
[0046]
溶液在溶液储罐1中的nh3损失小于0.01%,反应器5中碳酸氢铵的一次转化率为40%,产品气中nh3体积分数为23.4%,co2体积分数23.4%,h2o体积分数为53.1%,循环液体流量6.0m3/h,系统能耗1164kw。
[0047]
实施例三
[0048]
如实施例2所述,其他条件不变,溶液储存温度维持在75℃,补充水减少到21kmol/h,溶液储罐1内配成质量分数为43%的碳酸氢铵溶液。
[0049]
溶液在溶液储罐1中的nh3损失小于0.1%,反应器5中碳酸氢铵的一次转化率为40%,产品气中nh3体积分数为24.3%,co2体积分数23.8%,h2o体积分数为51.8%,循环液体流量5.6m3/h,系统能耗1136kw。
[0050]
实施例四
[0051]
如实施例2所述,其他条件不变,溶液储存温度维持在65℃,补充水增加到25kmol/h以使碳酸氢铵固体完全溶解,溶液储罐1内配成质量分数为41%的碳酸氢铵溶液。
[0052]
溶液在溶液储罐1中的nh3损失小于0.01%,反应器5中碳酸氢铵的一次转化率为40%,产品气中nh3体积分数为22.9%,co2体积分数22.9%,h2o体积分数为54.2%,循环液体流量6.2m3/h,系统能耗1186kw。
[0053]
实施例五
[0054]
如实施例2所述,其他条件不变,控制反应器5内反应温度在85℃,补充水减少到18kmol/h,溶液储罐1内配成质量分数为43%的碳酸氢铵溶液。
[0055]
溶液在溶液储罐1中的nh3损失小于0.01%,反应器5中碳酸氢铵的一次转化率为30%,产品气中nh3体积分数为24.9%,co2体积分数24.9%,h2o体积分数为50.1%,循环液体流量8.3m3/h,系统能耗1104kw。
[0056]
实施例六
[0057]
如实施例2所述,其他条件不变,控制反应器5内反应温度在87℃,补充水增加到27kmol/h以使碳酸氢铵固体完全溶解,溶液储罐1内配成质量分数为41%的碳酸氢铵溶液。
[0058]
溶液在溶液储罐1中的nh3损失小于0.01%,反应器5中碳酸氢铵的一次转化率为50%,产品气中nh3体积分数为22.2%,co2体积分数22.2%,h2o体积分数为55.6%,循环液体流量4.5m3/h,系统能耗1220kw。
[0059]
对比例一
[0060]
如实施例2所述,其他条件不变,溶液储罐1的温度维持在50℃,补充水需要增加到33kmol/h以使碳酸氢铵固体完全溶解,配成质量分数为34%的碳酸氢铵溶液。反应器5内反应温度需要提高到88℃,以达到产氨目标,系统能耗1462kw。
[0061]
对比例二
[0062]
如实施例2所述,其他条件不变,溶液储罐1温度维持在85℃,碳酸氢铵溶液在溶液储罐1内大量分解,nh3损失大于35%。
[0063]
对比例三
[0064]
如实施例2所述,其他条件不变,控制反应器5内反应温度在90℃,补充水需要增加到51kmol/h。产品气中nh3体积分数为17.9%,co2体积分数14.6%,h2o体积分数为67.5%,系统能耗1535kw。
[0065]
对比例四
[0066]
如实施例2所述,其他条件不变,控制反应器5内的反应温度在80℃,补充水降低到11kmol/h。反应器5中碳酸氢铵的一次转化率小于10%,循环液体流量42.0m3/h,系统能耗1388kw。
[0067]
与现有技术相比,本发明具有如下有益效果:
[0068]
a)提高安全性,降低原料成本:本发明采用碳酸氢铵作为制氨试剂,碳酸氢铵是我国除了尿素之外的第二大氮肥,运输储存安全,避免使用液氨及氨水时在运输储存方面的安全隐患。与尿素相比,2022年3月份市场上尿素的价格为2900元/吨,而碳酸氢铵的价格为950元/吨。即每生产1kg nh3气体,使用尿素作为还原剂的原料成本为5.12元,而使用碳酸氢铵作为还原剂的原料成本为4.42元,因此采用碳酸氢铵作为制氨试剂原料成本更低。
[0069]
b)减少溶液循环量,控制储存分解损失:本发明在实验探究的基础上选取碳酸氢铵溶液的储存温度在60-80℃之间,在该温度下碳酸氢铵饱和溶液的浓度可以达到37-52%,在相同氨出力的情况下减少了系统中的溶液量,有利于减小设备体积。此外,在该温度下碳酸氢铵溶液在储存时氨气的逸出率在0.5%以下,避免了碳酸氢铵溶液在储存时的大量分解。
[0070]
c)降低制氨过程能耗:本发明通过减小反应温度,降低反应器5中碳酸氢铵溶液的一次转化率在20-60%之间,从而减少了该条件下水的蒸发吸热,降低了反应能耗。未完全反应的碳酸氢铵溶液循环回到溶液储罐1,配成碳酸氢铵浓溶液后再次利用。
[0071]
d)余热利用:降低一次转化率后分解反应在《90℃的条件下进行,因此只需要110℃左右的热源来为分解反应供热。可以充分利用工业或电厂中的低品位辅助蒸汽作为热能来源,充分利用了工业余热,有利于节能减排,提高系统经济性。