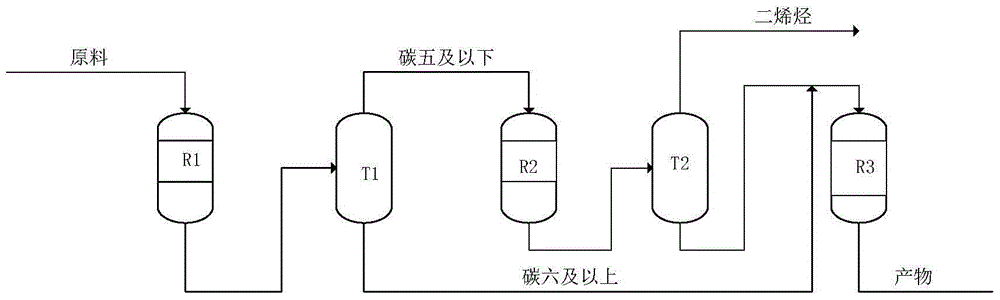
本发明提供了一种将催化脱氢技术、氧化脱氢技术与醚化技术相结合,由炼厂拔头油等轻烃生产二烯烃及高辛烷值汽油组分的工艺方法。
背景技术:
:进入“十二五”,随着中国石油广东石化2000万吨/年炼油、昆明1000万吨/年炼油、四川石化炼化一体化工程、抚顺石化80万吨/年乙烯、大庆石化120万吨/年乙烯改扩建等项目的推进,中国石油的炼油能力和乙烯产能还将进一步扩大,炼厂副产的拔头油、戊烷油、焦化石脑油等的产量也在大幅增加。以烷烃为主要组分的拔头油、戊烷油、焦化石脑油等主要通过异构化技术、高温芳构化技术改制为汽油,但是生成干气量较大,损失严重,收率不高。拔头油、戊烷油等不仅价格低廉,且运输成本高、运输过程中损失大,对炼厂来说属于低价值产品。随着我国国民经济的飞速发展,汽车保有量的不断增加,对车用燃料汽油的需求量越来越大。同时,也随着环保要求对汽油质量标准的日趋严格,车用汽油质量标准正在向低硫含量、低烯烃含量、低蒸汽压和高辛烷值的方向发展。市场对增产高质量汽油和对低硫、低烯烃含量、高辛烷值汽油调合组分具有极大需求,该方面的技术开发也成为国内各研究单位和企业关注的热点问题。丁二烯是合成橡胶的主要原料,占总原料的71%,2015年丁二烯需求量将达到350万吨。中国丁二烯来源比较单一,主要使用碳四抽提法,由乙烯装置生产,按2015年乙烯能力2100万吨计算,丁二烯总资源量为284~294万吨,丁二烯将出现严重缺口。丁二烯的另一重要来源是丁烯氧化脱氢技术。丁烯氧化脱氢以正构丁烯为原料,国产的正丁烯脱氢催化剂在国内相关单位的共同努力下,经历了三元钼系催化剂、六元钼系催化剂、H-198铁系和B-O2铁系催化剂,反应床也由最初的导向挡板流化床发展到后来的二段轴向绝热固定床。然而自20世纪80年代开始,随着国内大型乙烯装置的不断新建,丁二烯的生产工艺逐步被成本更低廉的碳四抽提法所取代,众多的正丁烯氧化脱氢装置逐渐停产,因此国产正丁烯氧化脱氢技术没能得到进一步的发展。但长远来看,受乙烯裂解装置原料轻质化影响,抽提法新增的丁二烯产能将越来越难以满足未来下游合成橡胶对丁二烯的需求。戊二烯化学性质活泼,是生产聚异戊二烯橡胶、特种橡胶、石油树脂、农药、医药、香料、固化剂、阻燃剂等多种石油化工产品和精细化工产品的重要化工原料。戊二烯主要是从石油裂解制乙烯副产物的分离提纯得到的,因而其产能和利用率受地域分散和工艺状况的严重限制。然而,在拔头油、焦化轻石脑油、油田轻烃、戊烷油以及其它装置回收的碳四碳五碳六烃类等的改制利用技术中,主要是通过烷烃的异构化、芳构化进行的,其目的产物主要也是改善了辛烷值和稳定性的汽油调和组分。一面是二烯烃市场的巨大缺口,另一面却是富含碳四碳五碳六烷烃油品改制技术需要进一步开发,本发明主要是针对以上情况,在利用碳四碳五碳六烷烃原料来生产丁二烯、戊二烯的同时,将剩余的部分作为生产高辛烷值汽油组分的原料。利用烷烃催化脱氢生产烯烃的过程中,异构烷烃转化为异构烯烃的转化率较正构烷烃转化为正构烯烃的转化率高。而利用氧化脱氢法生产二烯烃的过程中,正构烯烃做主要贡献,异构烯烃利用率较低。在醚化技术中叔碳烯烃的转化率在90%以上,正构烯烃几乎不转化。综合以上三种技术特点,将三种技术结合使用,将会在改制和利用富含碳四碳五碳六烷烃原料过程中,更加精细化的提高该类产品的附加值。技术实现要素:本发明的目的在于提供一种拔头油类轻烃转化方法,特别是一种将以C4/C5/C6烷烃为主要成分的拔头油、焦化轻石脑油、油田轻烃、戊烷油等在生产丁二烯、戊二烯的同时,生产高辛烷值汽油组分的方法。一种拔头油类轻烃转化方法,至少包括如下步骤:第一步将富含碳四碳五碳六烷烃的原料与氢气送入催化脱氢单元,生产富含烯烃的物流a;第二步将物流a送入分离单元I,分为碳六及以上烃类物流b与碳五及以下烃类物流c;第三步将物流c、含有氧化剂的物料流和水或水蒸汽再送入氧化脱氢单元,生产富含二烯烃的物流d;第四步物流d进入分离单元II,将二烯烃分离后得到物流e;第五步,将物流e、物流b与醇类物流送入醚化单元反应,生产高辛烷值汽油组分。本发明中富含碳四碳五碳六烷烃的原料是指炼厂在生产过程中所副产的以碳四碳五碳六烷烃为主要组分的烃类,如拔头油、焦化轻石脑油、油田轻烃、戊烷油以及其它装置回收的碳四碳五碳六烃类等,一般链烷烃的含量在90%以上,最好为95%。原料95%的馏程在75℃以下,最好是在70℃以下,可以是同一种原料,也可以是不同原料混合。本发明未特别说明的百分比均为质量%。本发明催化脱氢单元中并不特别限定催化脱氢催化剂,要求催化脱氢产物(物流a)中烯烃含量不低于35%,最好使得烯烃含量在45%以上。本发明中催化脱氢单元的反应条件最好为:480~700℃,压力0.01~3MPa,液体体积空速为0.1~10h-1。特别推荐的反应条件为:560~650℃,压力0.4~1.2MPa,液体体积空速为2~7h-1。本发明中在催化脱氢单元中,氢气与进入催化脱氢单元中所有烃类物质的摩尔比为0.01~1:1,最好为0.1~0.5:1。本发明中分离单元I中,要求物流c中,碳数大于6的烃类不高于1%,本发明对分离方法不作要求,但比较推荐精馏。本发明中氧化脱氢单元的催化剂也不做特别要求,能满足正丁烯与正戊烯转化率分别不低于70%,最好分别不低于75%的要求即可。氧化脱氢催化剂可以是使用一些耐高温的骨架材料负载特定比率的主活性组分和助活性组分来完成的。其中,耐高温的骨架结构可以是金属丝网、多空整料或是不同形状的氧化铝、二氧化硅、氧化锆、堇青石、氧化钛、富铝红柱石、稳定的氧化铝、稳定的氧化锆等,也可以是以上耐高温材料两种或者两种以上的混合物。活性组分的负载方式可以为微湿含浸法、化学气相沉积法、共沉淀法等。主活性组分可以为3%~8%的镧系金属元素或者镧系金属元素的氧化物,或者为以上几种物质的相互混合,具体可以是钐、铈、镨、铽,及其氧化物中一种或者几种的组合;也可以是0.2%~1%铂系元素与它们的组合,具体可以是钌、銠、钯、锇、铱或铂中的一种或者几种。催化剂中最好也包含0.01%~0.07%第VIII族的金属、第VIII族的金属氧化物或者它们的组合,具体为铁,氧化铁,镍,氧化镍,钯,氧化钯,铂,氧化铂,帆,氧化钒,铬,氧化铬,锰,氧化锰等中的一种或者几种的组合。还可以添加0.1%以下的碱土金属和稀土元素作为助活性组分。氧化脱氢催化剂最好为共沉淀方法制备的同时具有尖晶石或者六面体结构的铁酸盐与α-氧化铁结构的催化剂。铁酸盐中的金属离子可以为,锌,钡,镁,钙,锶,镍,铜中的一种或者几种。比较推荐的一种采用共沉淀方法制备的尖晶石-α-氧化铁结构的氧化脱氢催化剂中,尖晶石含量45-60%,铁酸锌的含量2.8%~4.4%,其它铁酸盐含量和不高于3%。本发明中氧化脱氢单元反应条件是依据不同的催化剂而略有不同,但最好为:温度为280℃~410℃,优选310℃~395℃,压力0~100KPa,优选0~40KPa,体积空速10~500h-1,优选60~400h-1。本发明未特别说明的空速均为液时体积空速。本发明中氧化脱氢单元的氧化剂可以为氧气,富氧气、空气等含有氧分子或者含有氧化性强的氧原子物料流,本发明中优选空气、富氧气和氧气。特别优选富氧气。特别推荐氧气含量在32%~45%之间的富氧气流。其中,含有氧化剂的物流中以氧气计,氧气与进入氧化脱氢单元中所有烃类物料的烯烃摩尔比为0.1~1.0:1,优选0.3~0.85:1。本单元的进料过程中,加入一定比率的水或水蒸气,以防止催化剂的结焦和催化剂床层由于结焦而导致温度上升过快的问题。水蒸气与进入该氧化脱氢单元的所有烃类物料的质量比可以为0.5~30:1,优选5~20:1。本发明中氧化脱氢单元的反应器可以为固定床反应器、流化床反应器、移动床反应器、涓流床反应器,也可以为催化精馏反应器、固定床反应管束,还可以为以上反应器的串联和\或并联。优选反应器为两台或多台固定床反应器或流化床反应器的并联方式,方便催化剂的再生和工艺过程的连续。本发明中分离单元II中分离方法可以为萃取,精馏,也可以为萃取精馏,共沸精馏,膜分离,化学吸收等。可以使用技术比较成熟的分离技术,来得到合格的丁二烯、戊二烯产品及物流e。由于物流e为芳构化单元的原料,所以要求物流e中二烯烃的质量含量不高于0.3%,最好不高于0.1%。为了得到合格的二烯烃产品和芳构化单元的原料,本分离单元中的分离方法和分离装置可以分别为多种形式的结合。本发明中醚化单元中并不特别限定醚化催化剂,要求叔碳烯烃的转化率不低于92%。本发明中醚化单元中的醇类物流是指碳原子个数不大于4的低碳醇,特别推荐甲醇、乙醇,最好为甲醇。本发明的醚化单元中,醇类与进入醚化反应器中所有烃类物料中的叔碳烯烃的摩尔比为0.8~1.5:1,最好为0.95~1.3:1。本发明中醚化单元的反应条件为:45~90℃,最好为55~75℃,压力为0.4~3.0MPa,最好为0.5~2MPa,体积空速为0.1~5h-1,最好为1~2h-1。本发明中对醚化单元中使用的醚化反应器不特别限定,可以为固定床、移动床悬浮床,催化蒸馏反应器等中的一种或者几种的组合。但最好为催化蒸馏技术,可以使叔碳烯烃转化的较为完全。在醚化单元回收的醇类可以循环至醚化反应器入口循环使用。本发明的分离单元中还可有加入不凝气体的分离装置,如闪蒸罐、吸收/解析塔、冷却装置以及压缩装置等。本发明更具体的实施方式为:链烷烃的含量在90%以上,95%的馏程在75℃以下的碳四碳五碳六烷烃原料进入催化脱氢单元,在温度480~700℃,压力0.01~3MPa,体积空速为0.1~10h-1,氢气与进入催化脱氢单元的所有烃类物质的摩尔比为0.1~1:1的条件下进行催化脱氢后,分离为碳六及以上烃类和碳五及以下烃类两股物流;碳五及以下烃类进入氧化脱氢单元,在温度为280℃~410℃,压力0~100KPa,体积空速10~500h-1,氧气与进入氧化脱氢单元的所有烃类物料中烯烃的摩尔比为0.1~1.0︰1,水蒸气与进入氧化脱氢单元的所有烃类物料的质量比为0.5~30︰1的工艺条件下,与氧气含量在32%~45%之间的富氧气流混合进行氧化脱氢,反应后物流分离出二烯烃,剩余物料流与催化脱氢产物中分离出来的碳六及以上烃类一起进入醚化单元,在温度为45~90℃,压力为0.4~3.0MPa,体积空速为0.1~5h-1,醇类与进入醚化单元中所有烃类物料中的叔碳烯烃摩尔比为0.8~1.5:1的条件下,生产高辛烷值汽油组分。本发明的优点在于富含碳四碳五碳六烷烃的物流,经过催化脱氢及氧化脱氢生产丁二烯和戊二烯后的副产烃物流,进入醚化反应器,生产出优质的高辛烷值汽油组分,相比现有技术,更进一步的提高了富含碳四碳五碳六烷烃物流的利用率和附加值。在利用烷烃催化脱氢生产烯烃的过程中,异构烷烃转化为异构烯烃的转化率较正构烷烃转化为正构烯烃的转化率高。而利用氧化脱氢法生产二烯烃的过程中,正构烯烃做主要贡献,异构烯烃利用率较低。在醚化技术中叔碳烯烃的转化率在90%以上,正构烯烃几乎不转化。综合以上三种技术特点及协同作用,将会在改制和利用富含碳四碳五碳六烷烃原料过程中,更加精细化的提高该类产品的附加值。本发明者通过催化脱氢,为醚化单元提供富含烯烃的原料的同时发现,在C4~C6烷烃催化脱氢的过程中,会产生一定含量的戊二烯和丁二烯,己二烯的踪迹则不明显。二烯烃的出现会影响醚化单元中异构烯烃的转化率、高辛烷值汽油收率以及汽油中醚类化合物的含量,严重影响该工艺对C4~C6烷烃改制后的影响。通过分离或者加氢的手段来处理二烯烃的过程,只会增加本工艺的成本和工艺复杂性。另一方面,二烯烃市场的巨大缺口,市场价格不断走高。发明者在催化脱氢和醚化两个反应单元之间,加入氧化脱氢生产二烯烃单元和二烯烃分离单元,在生产高辛烷值汽油的过程中,副产一定量的高价值的二烯烃,无疑提高了本工艺的经济效益和市场竞争性,也为更加精细化的利用低碳烷烃类提供了另外一种工艺。另外,在氧化脱氢过程中,由于副反应的发生,会产生少量的酮和醛。醛和酮产生的量太高,直接影响了二烯烃选择性的同时,处理洗涤醛和酮产生的废水过程也会增加工艺成本。本发明中,通过控制富氧气流中氧气含量来控制进入反应体系物料总量,来控制反应体系中氧原子、烯烃与催化剂的接触时间,从另外一方面控制反应停留时间。这个方法在这个多种烯烃氧化的复杂反应中,不但能保证单烯烃充分转化为二烯烃,而且非常有效地控制了醇类和醛类的产生,提高了二烯烃的收率和选择性。附图说明图1为应用本发明的一种工艺流程示意图。图中:R1-催化脱氢反应器,R2-氧化脱氢反应器,R3-醚化反应器,T1、T2为分离系统I、II。具体实施方式下面通过实施例详述本发明。表1~表2为实施例采用的原料的性质,其中原料A为独山子炼油厂加氢裂化轻烃,原料B为独山子炼油厂戊烷油。甲醇采用市售沧州正源化工有限公司生产的甲醇,其中甲醇的质量含量为99.5%。乙醇采用市售宜兴市秋云化工有限公司生产的无水乙醇,其中乙醇的质量含量为99.5%。表1原料A组成(W%)组分环烷烃支链烷烃直链烷烃芳烃C45.818.82C50.9250.8714.47C61.7515.471.380.11C70.120.220.01C80.05表2原料B组成(W%)组分环烷烃支链烷烃直链烷烃烯烃C40.2311.600.07C50.3250.1531.360.86C63.022.13实施例均采用如图1所示工艺,在实施例1~3中催化脱氢反应器和醚化反应器均为200ml加压固定床反应器,单个间歇操作,氧化脱氢单元采用100ml的悬浮床反应器。实施例4~6中,催化脱氢反应器和醚化反应器均为200ml加压固定床反应器两个反应器循环使用,氧化脱氢单元采用100ml的悬浮床反应器。分析样品为反应2.5小时后的瞬时样。分离单元I(T1)中采用理论塔板数为18的精馏塔。分离单元II(T2)中采用旋风分离器脱水后,闪蒸除去不凝气体,萃取法分离出二烯烃。实施例中制备催化剂所采用的原料中,田菁粉为工业级,其它均为市售化学纯试剂。水为去离子蒸馏水。富氧气流是由工业级纯氧与空气混合配置。实施例中,烯烃的含量、二烯烃的收率、芳构化产物的收率、芳烃含量的计算方法如下:烯烃的含量=催化脱氢产物中所产生的丁烯、戊烯的质量/催化脱氢产物中所有烃类的质量*100醇类的质量收率=氧化脱氢反应单元所产生的醇类质量和/进入氧化脱氢单元中烃类物料的质量*100酮类的质量收率=氧化脱氢反应单元所产生的酮类质量和/进入氧化脱氢单元中烃类物料的质量*100二烯烃的质量收率=氧化脱氢单元所产生的二烯烃质量/进入氧化脱氢单元中烃类物料的质量*100醚化产物的收率=醚化所有产物脱除不凝气体后的质量/进入醚化反应单元烃类物料的质量*100醚类化合物的含量=所产生的所有醚类物质的质量/所产生的醚化产物的质量*100实施例1催化脱氢催化剂采用海泰公司HTPB-DH脱氢催化剂,其中以Al2O3为载体以Pt和Cl为活性组分,其中Pt的质量含量为1%,氯质量含量为2%,比表面积为200m2/g,孔容0.5ml/g,直径为1.59mm,堆密度0.6g/cm3。烯烃氧化脱氢催化剂采用专利CN102671714A中实施例2的制备方法制备,具体制备方法如下:将17克六水合硝酸镁溶解在20ml蒸馏水里,然后加入20克氧化锆,在80℃对上述混合溶液进行蒸发干燥12小时之后,在马弗炉内,550℃下的空气氛围中加热所得的固体样品3小时,然后用偏钒酸氨水溶液浸渍样品。偏钒酸氨水溶液是通过将5克偏钒酸氨与10.6克草酸溶解在少量蒸馏水中制备。经过偏钒酸氨溶液浸渍的样品在在80℃下干燥12小时,然后在在马弗炉内,550℃下的空气氛围中加热所得的固体样品3小时,最后筛分为40~80目待用。醚化催化剂为南大合成化学有限公司所生产的新型醚化反应催化剂,其粒度为16-50目,堆积密度0.55-0.65g/ml,比表面积大于20m2/g,孔径大于10nm,孔容大于0.2cc/g。在催化脱氢反应器中,在氢气与烃类物料(原料A)摩尔比为0.5:1,反应温度570℃,体积空速3.0h-1,反应压力1.7MPa的条件下进行烷烃催化脱氢反应,得到产物中烯烃含量为58.4%。催化脱氢产物经过分离单元I分离后,分离为碳六及碳六以上烃类与碳五及碳五以下烃类两股物流,碳五及以下烃类与空气、水蒸汽经过预热进入氧化脱氢反应器,在380℃,50KPa,体积空速60h-1,烯烃:氧=1:0.85(摩尔比),烃类物料:水=1:5(质量比)的条件下进行烯烃的氧化脱氢反应。反应产物中二烯烃的质量收率为17.1%,醇类的质量收率为0.91%,酮类的质量收率为0.45%。氧化脱氢反应产物经分离单元II,分离出二烯烃后的产物与分离单元I中分离出的碳六及以上组分混合进入醚化反应器中,醚化的反应条件是:反应温度45℃,体积空速2h-1,反应压力1.5MPa,其中甲醇与进入醚化反应器的烃类物料的叔碳烯烃摩尔比为1.2:1。反应产物脱除不凝气体以后,收率为114.4%,其中醚类化合物的含量为55.6%。实施例2催化脱氢催化剂采用CN101940922A中实施例4的方法制备。其具体步骤为:先称取117.5克的氧化铬,溶于去离子水中充分搅拌,配制成重量浓度为47%氧化铬溶液。再配置重量浓度为3.86%的硝酸钾水溶液。然后将55.0克拟薄水铝石、2.2克膨润土,与7.59克配制好的氧化铬溶液充分混合,捏合、挤成小球。然后在120℃下干燥3小时,然后在500℃恒温3小时,在620℃恒温2小时,最后在20%水和80%空气下760℃焙烧4小时。再取配制好的氧化铬溶液11.39克,将焙烧好的样品浸渍20分钟,在120℃干燥3小时,在550℃恒温焙烧5小时。再取配制好的硝酸钾水溶液浸渍,在120℃干燥3小时,在620℃恒温焙烧6小时备用。烯烃氧化脱氢催化剂采用专利CN99106660.X中实施例1中催化剂的制备方法,其具体制备方法如下:将43.5g的二氧化锰粉末与1000ml水在同一容器中搅拌加热10分钟后,再加入1.09克三氧化锑粉末,将体系加热至80℃后搅拌2小时,然后将温度加热至90℃再搅拌4小时,当体系形成糊状物,在120℃下干燥14小时,制成粉末,成型,最后筛分为40~80目待用。醚化催化剂使用丹东明珠特种树脂有限公司生产的D005-II树脂催化剂。其粒度范围0.315~1.25mm,湿真密度1180~1200g/l,总交换容量≥5.2mmol/g[H+],机械强度≥95%(H型)。使用原料B。在脱氢反应器中,在氢气与物料(原料B)摩尔比为0.3:1,反应温度600℃,体积空速5.0h-1,反应压力1.1MPa进行烷烃催化脱氢反应,反应得到脱氢产物中烯烃含量为66.7%。催化脱氢产物经过分离单元I,分离为碳五及以下与碳六及以上两股物流。其中碳五及以下与含氧气35%的富氧气流、水混合进入氧化脱氢反应器中在390℃,大气压,体积空速500h-1,烯烃:氧=1:1(摩尔比),烃类物料(分离单元I中分离出的碳五及以下烃类):水=1:16(质量比)的条件下进行烯烃氧化脱氢反应,反应产物中二烯烃的质量收率为28.9%,醇类的质量收率为0.48%,酮类的质量收率为0.27%。分离出二烯烃后的氧化脱氢产物与分离单元II中分离出的碳六及以上组分混合进入醚化反应器中,醚化的反应条件是:反应温度80℃,体积空速3.0h-1,反应压力1.0MPa,其中甲醇与进入醚化反应器的烃类物料的叔碳烯烃摩尔比为1.1:1。反应产物脱除不凝气体以后,收率为98.1%,其中醚类化合物的含量为60.5%。实施例3催化脱氢催化剂采用专利CN101618319中实施例1的方法制备。将2.24克氧化钙与3.1克聚乙二醇溶于120ml去离子水中,240℃水热处理24小时,600℃灼烧5小时后,将其用适量无水乙醇与7.2克硝酸铬、6克三氧化二铝混合均匀,干燥十二小时后研磨均匀,在550℃下灼烧3小时后备用。烯烃氧化脱氢催化剂采用专利200780013916.9中制备例2的方法制得,其具体步骤如下:将69克的钼酸铵溶解于500ml蒸馏水中搅拌,然后将108.1克的硝酸铋加入到5.3%的硝酸溶液中搅拌至完全溶解后,滴加到钼酸铵溶液中。然后滴加氨水使上述溶液的pH至1.5,搅拌1小时后,减压抽滤获得固体样品,再在100℃下对固体样品干燥26个小时后,在马弗炉中475℃下,煅烧24小时,最后破碎筛分为20~80目待用。醚化催化剂为丹东明珠特种树脂有限公司生产的D005-II树脂催化剂。其粒度范围0.315~1.25mm,湿真密度1180~1200g/l,总交换容量≥5.2mmol/g[H+],机械强度≥95%(H型)。使用原料A。在脱氢反应器中氢气与烃类物料(原料A)摩尔比为0.15:1,在反应温度650℃,体积空速8.0h-1,反应压力2.4MPa的条件下进行烷烃催化脱氢反应,产物中烯烃含量为41.4%。催化脱氢产物经过分离单元I,分离为碳五及以下与碳六及以上两股物流。其中碳五及以下与含氧气40%的富氧气流、水混合进入氧化脱氢反应器中,在280℃,10Kpa,体积空速300h-1,烯烃:氧=1:0.55(摩尔比),烃类物料(分离单元I中分离出的碳五及以下烃类):水=1:30(质量比)条件下进行氧化脱氢反应。反应产物中二烯烃含量为15.1%,醇类的质量收率为0.72%,酮类的质量收率为0.38%。经过分离单元II分离后,分离出二烯烃后的物流与分离单元I中分离出的碳六及以上组分混合进入醚化反应器中,醚化的反应条件是:反应温度65℃,体积空速4h-1,反应压力0.4MP,其中甲醇与进入醚化反应器的烃类物料中的叔碳烯烃的摩尔比为1.3:1。反应产物脱除不凝气体以后,收率为99.5%,其中醚类化合物的含量为59.2%。实施例4脱氢催化剂采用CN101940922A中实施例4的方法制备。其具体步骤为:先称取117.5克的氧化铬,溶于去离子水中充分搅拌,配制成重量浓度为47%氧化铬溶液。再配置重量浓度为3.86%的硝酸钾水溶液。然后将55.0克拟薄水铝石、2.2克膨润土,与7.59克配制好的氧化铬溶液充分混合,捏合、挤成小球。然后在120℃下干燥3小时,然后在500℃恒温3小时,在620℃恒温2小时,最后在20%水和80%空气下760℃焙烧4小时。再取配制好的氧化铬溶液11.39克,将焙烧好的样品浸渍20分钟,在120℃干燥3小时,在550℃恒温焙烧5小时。再取配制好的硝酸钾水溶液浸渍,在120℃干燥3小时,在620℃恒温焙烧6小时备用。烯烃氧化脱氢催化剂采用专利200880014941.3中制备实施例2的方法制得,其具体步骤如下:将14.2克氯化锌和56.1克六水合氯化铁溶解于800ml蒸馏水中,充分搅拌至完全溶解后,滴加3M的氢氧化钠水溶液调节上述溶液的pH值到8,然后在室温下搅拌12小时后减压抽滤获得固体样品。将固体样品在175℃下干燥16小时,在650℃下煅烧12小时,最后破碎筛分为20~65目待用。醚化催化剂使用江苏奥科石油化学技术有限公司所生产的大孔强酸性树脂催化剂,其粒度为0.315-1.25mm,堆积密度0.77-0.85g/ml,比表面积大于20-70m2/g,孔径大于20-50nm,孔容大于0.3-0.5cc/g。原料B进入脱氢反应器中,在氢气与烃类物料(原料B)的摩尔比为0.01:1,反应温度550℃,体积空速10.0h-1,反应压力3.0MPa的条件下进行反应,得到脱氢产物中烯烃含量为49.8%。催化脱氢产物经过分离单元I,分离为碳五及以下与碳六及以上两股物流。其中碳五及以下与含氧气32%的富氧气流、水经混合进入氧化脱氢反应器中,在340℃,大气压,体积空速250h-1,烯烃:氧=1:0.1(摩尔比),烃类物料(分离单元I中分离出的碳五及以下烃类):水=1:0.5(质量比)的条件下反应,得到产物中二烯烃的含量为28.1%,醇类的质量收率为0.69%,酮类的质量收率为0.37%。氧化脱氢产物经过分离单元II,分离出二烯烃后的物流与分离单元I中分离出的碳六及以上组分混合进入醚化反应器中,醚化的反应条件是:反应温度75℃,体积空速5h-1,反应压力3MPa,其中甲醇与进入醚化反应器的烃类物料中的叔碳烯烃的摩尔比为1.5:1。反应产物脱除不凝气体以后,收率为98.2%,其中醚类化合物的含量为50.3%。实施例5脱氢催化剂采用专利CN96121452.X中实施例9的方法制备。称取17克Cr(NO3)3·9H2O,1.1克Cu(NO3)2·3H2O,80.8克Al(NO3)3·9H2O,用共沉淀法制备催化剂,沉淀剂选用10%的KOH(或NaOH)溶液,硝酸盐溶解于蒸馏水中,边搅拌边加入沉淀剂,使其完全形成凝胶,且pH值为8.5~9,老化3小时,过滤,在110℃下,干燥20小时,在650℃焙烧7小时,经破碎筛分后备用。烯烃氧化脱氢催化剂采用CN96113127中实施例4中方法制得,具体步骤如下:将177克Fe(NO3)3·9H2O,43.3克Zn(NO3)2·6H2O,43克Ca(NO3)2·4H2O,1.5克Co(NO3)2·6H2O溶于500ml的蒸馏水中,快速搅拌下滴入20%的氨水沉淀,沉淀过程中加入1克的田菁粉。溶液中pH值到8.5时,结束氨水滴入。沉淀物在80℃加热老化1小时,在55℃老化30分钟,过滤,每次用1000ml水洗涤,共两次。滤饼在110℃干燥12小时,在650℃煅烧14小时,最后筛分为40~80目待用。醚化催化剂采用凯瑞化工有限公司生产的醚化树脂催化剂,其粒度范围0.335~1.25mm,湿真密度0.75~0.85g/ml,总交换容量≥5.2mmol/g,机械强度≥95%。使用原料A。在催化脱氢反应器中,氢气与烃类物料(原料A)摩尔比为0.25:1,反应温度480℃,体积空速0.1h-1,反应压力0.01MPa的条件下催化脱氢,反应得到脱氢产物中烯烃含量为40.1%。催化脱氢后经过分离单元I分离为碳五及以下与碳六及以上两股物流,碳五及以下物流进入氧化脱氢反应器,与纯氧气、水经过预热进入氧化脱氢反应器中在300℃,75KPa,体积空速10h-1,烯烃:氧=1:0.68(摩尔比),烃类物料(分离单元I中分离出的碳五及以下烃类):水=1:30(质量比)的条件下进行氧化脱氢反应。经过分离单元II,分离出二烯烃,其收率为10.8%,醇类的质量收率为1.31%,酮类的质量收率为0.88%。将分离单位II分离出二烯烃后的物流与分离单元I分离出的碳六及以上组分混合进入醚化反应器中,醚化的反应条件是:反应温度55℃,体积空速0.1h-1,反应压力2.0MPa,其中乙醇与进入醚化反应器的烃类物料中的叔碳烯烃的摩尔比为0.8:1。分离出不凝气以后,醚化产物的收率为107.6%,其中醚类化合物的含量为55.4%。实施例6脱氢催化剂采用专利CN101623633A中实施例1中催化剂制备的步骤制备催化剂。首先ZSM-5分子筛原粉置于0.16M的SnCl2·2H2O溶液中于80℃浸渍10hr,使得催化剂中的Sn的负载量达到4wt%,然后再120℃下干燥6hr。干燥后的样品在550℃空气氛围下焙烧4hr。焙烧后的粉末在0.03M的H2PtCl6·6H2O溶液中在80℃下浸渍4hr,使最终制得Pt含量为20wt%的催化剂,然后在120℃下干燥6hr,在550℃下焙烧4hr。后在550℃氢气还原12hr备用。烯烃氧化脱氢催化剂采用专利CN103055890中实施例1的制备方法制备,具体步骤如下:首先将280克的铁粉与80.3克的锌粉加入到1000毫升1M的硝酸溶液中,待溶解完全后,再加入97.1克硝酸锰与3.3克硝酸镁,完全溶解后,在溶液温度60℃的条件下,滴加20%的氨水并充分搅拌,至pH值在7.5后,溶液温度继续保持60℃,继续搅拌老化60分钟,过滤浆液并洗涤至pH值在7.0~9.0,然后将滤饼挤条后,200℃干燥12小时,500℃煅烧48小时后,将条状催化剂短碎为2~3毫米待用。醚化催化剂采用石油化工科学院研发的RZE-3沸石醚化催化剂,外形为直径8mm球形,堆积密度0.71g/cm3,比表面积487m2/g,孔容0.464mL/g,平均孔径175nm,强度>20N。使用原料B。在氢气与烃类物料(原料B)摩尔比为0.1:1,反应温度700℃,体积空速1.0h-1,反应压力0.15MPa进行催化脱氢,反应得到脱氢产物中烯烃含量为59.8%。催化脱氢产物经过分离单元I分离以后,碳五及以下烃类进入氧化脱氢反应器,与含氧气45%的富氧气流、水经过预热进入氧化脱氢反应器中,在350℃,压力100KPa,体积空速350h-1,烯烃:氧=1:0.3(摩尔比),烃类物料(分离单元I中分离出的碳五及以下烃类):水=20(质量比)的条件下进行烯烃氧化脱氢反应。氧化脱氢产物经过分离单元II,分离出二烯烃,二烯烃的收率为28.7%,醇类的质量收率为0.83%,酮类的质量收率为0.46%。将分离单位II分离出二烯烃后的物流与分离单元I分离出的碳六及以上组分混合进入醚化反应器中。醚化反应条件是:反应温度90℃,体积空速1.4h-1,反应压力3.0MPa,其中甲醇与进入醚化反应器的烃类物料中的叔碳烯烃的摩尔比为0.95:1。分离出不凝气以后,醚化产物的收率为100.1%,其中醚类化合物含量为61.9%。对比例1催化脱氢催化剂采用CN101940922A中实施例4的方法制备。其具体步骤为:先称取117.5克的氧化铬,溶于去离子水中充分搅拌,配制成重量浓度为47%氧化铬溶液。在配置重量浓度为3.86%的硝酸钾水溶液。然后将55.0克拟薄水铝石、2.2克膨润土,与7.59克配制好的氧化铬溶液充分混合,捏合、挤成小球。然后再120℃下干燥3小时,然后再500℃恒温3小时,在620℃恒温2小时,最后在20%水和80%空气下760℃焙烧4小时。再取配制好的氧化铬溶液11.39克,将焙烧好的样品浸渍20分钟,在120℃干燥3小时,在550℃恒温焙烧5小时。再取配制好的硝酸钾水溶液浸渍,在120℃干燥3小时,在620℃恒温焙烧6小时备用。醚化催化剂使用丹东明珠特种树脂有限公司生产的D005-II树脂催化剂。其粒度范围0.315~1.25mm,湿真密度1180~1200g/l,总交换容量≥5.2mmol/g[H+],机械强度≥95%(H型)。原料B在催化脱氢反应器中,在氢气与烃类摩尔比为0.3:1,反应温度600℃,体积空速5.0h-1,反应压力1.1MPa进行烷烃催化脱氢反应,反应得到脱氢产物中烯烃含量为66.7%。催化脱氢产物与甲醇混合进入醚化反应器中,醚化的反应条件是:反应温度80℃,体积空速3.0h-1,反应压力1.0MPa,其中甲醇与进入醚化反应器的烃类物料中的叔碳烯烃的摩尔比为1.1:1。反应产物脱除不凝气体以后,收率为96.1%,其中醚类化合物的含量为36.7%。当然,本发明还可有其它多种实施例,在不背离本发明精神及其实质的情况下,熟悉本领域的技术人员可根据本发明作出各种相应的改变和变形,但这些相应的改变和变形都应属于本发明权利要求的保护范围。当前第1页1 2 3