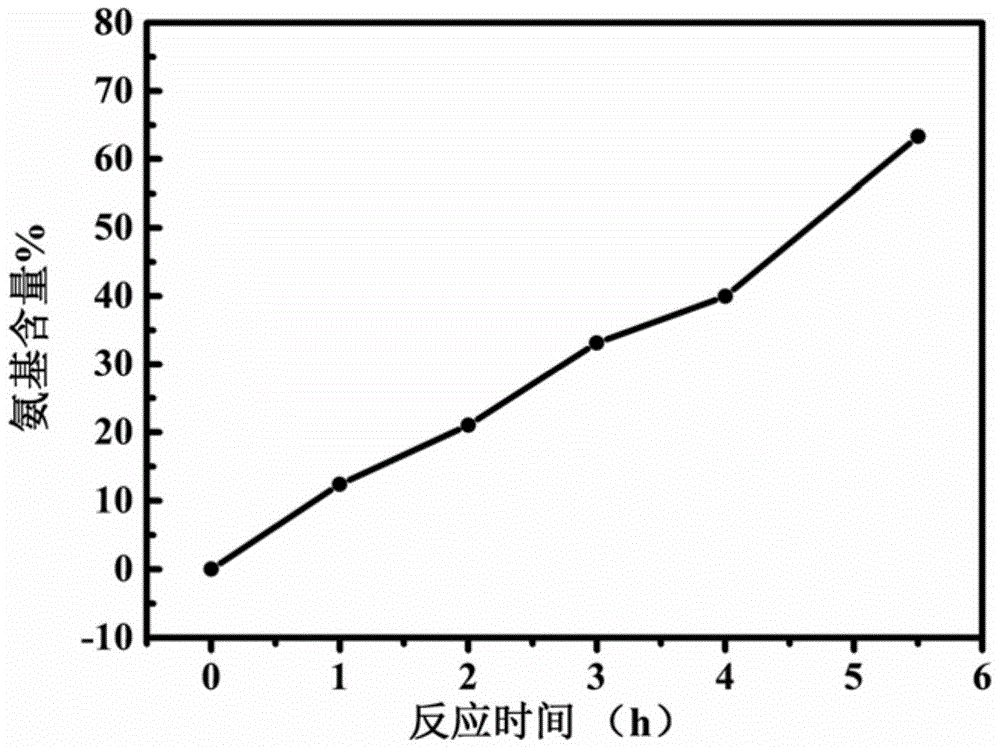
本发明属于有机高分子化合物领域,具体涉及亲水的丁腈橡胶的制备方法及所得产物。
背景技术:丁腈橡胶具有高强度和高耐磨等优良性能,在诸多领域有着广泛的应用,但由于其亲水性及吸湿性差,与其他亲水性材料(如淀粉)的表面相容性较差,所以限制了丁腈橡胶在高分子复合材料中的应用;同时丁腈橡胶中大量不饱和碳碳双键的存在使得丁腈橡胶的耐老化性下降,为降低丁腈橡胶中不饱和双键的存在及提高丁腈橡胶的亲水性,就需要对丁腈橡胶进行改性。目前提高丁腈橡胶亲水性的方法主要有共混法,如2011年,李晓林等将羧基丁腈橡胶与明胶共混制备了亲水性良好的羧基丁腈橡胶/明胶共混物(羧基丁腈橡胶/明胶共混物的制备及其亲水性和吸湿性,合成橡胶工业,2011年第2期)。本发明对丁腈橡胶改性采用催化加氢法,且这种方法可控性强;本发明就使用两步催化加氢法来对丁腈橡胶进行改性,不仅使丁腈橡胶中碳碳双键大幅下降,同时催化氢化丁腈橡胶中的腈基为氨基,从而提高了丁腈橡胶的亲水性,即制备了一种亲水性氨基化氢化丁腈橡胶。本发明采用两步催化加氢法制备的亲水性新型氨基化氢化丁腈橡胶在文献中鲜有报道。
技术实现要素:本发明提出一种制备亲水性新型氨基化氢化丁腈橡胶的方法。具体涉及采用两步法对丁腈橡胶分子链中的碳碳双键及氰基的催化加氢,制备的新型氨基化氢化丁腈橡胶具有良好的亲水性,为开发氨基化氢化丁腈橡胶在填隙剂、高分子复合材料等方面的应用奠定了基础。本发明的第二个目的是提出所述制备方法获得的产物。实现本发明上述目的的技术方案为:一种亲水性氨基化氢化丁腈橡胶的制备方法,包括步骤:(1)将纳米Rh金属催化剂与丁腈橡胶混合,分散均匀;纳米Rh金属催化剂与丁腈橡胶干重的质量比为1~4%(2)将步骤(1)所得混合液加入反应釜中,在1~5MPa氢气压强条件下进行第一步催化加氢,反应过程中保持恒压;反应1~5.5h;(3)对第一步催化加氢反应产物进行离心,除去黑色纳米金属Rh催化剂,向反应物中加入质量分数为0.5~2.0%的RhCl(PPh3)3催化剂,反应温度为75~85℃,在1~5MPa氢气压强下反应1~3h。本制备方法中,两步催化加氢反应顺序不能调换,必须先用纳米Rh催化加氢丁腈橡胶,再用RhCl(PPh3)3进行第二步催化加氢;第一步腈基氢化为氨基的氢化度可达12.42%~63.3%,第二步制备的氨基化氢化丁腈橡胶中碳碳双键的氢化度为100%。其中,步骤(1)采用的纳米Rh金属催化剂,是将RhCl3·3H2O前驱体与去离子水混合,再滴入到氢氧化钠的水合肼溶液中反应制得。优选地,所述步骤(1)中,纳米Rh金属催化剂与丁腈橡胶混合、超声混合均匀。优选地,所述步骤(2)中,反应温度为78~80℃,氢气压强为3~4MPa,反应釜内搅拌器的转速为300~1500r/min。其中,所述步骤(2)中,通过控制步骤(2)的反应时间来控制氨基的产率,其反应时间从1h至6h,腈基氢化为氨基的氢化度从10~15%随时间延长增加至55~65%。其中,所述步骤(3)中,通过对第一步催化加氢反应产物进行离心,除去纳米金属Rh催化剂。优选地,所述步骤(3)中,反应温度为110~130℃,氢气压强为3~4MPa,反应2h。所述的制备方法的步骤(3)反应结束后,还包括对所得产物进行干燥的步骤,干燥温度为45~50℃,干燥时间为10~15h。本发明提出的制备方法制备得到的橡胶。本发明制备的氨基化氢化丁腈橡胶具有良好的亲水性,氨基化氢化丁腈橡胶的亲水性随着氨基含量的增加而增强;进一步地,氨基化氢化丁腈橡胶中氨基的存在为含羧基、环氧基有机物的引入提供了活性位点。本发明的有益效果在于:本发明可制备氨基含量可控的氨基化氢化丁腈橡胶,其中,碳碳双键的氢化度为100%,可制得氨基含量为12.42%~63.3%的氨基化氢化丁腈橡胶。所制氨基化氢化丁腈橡胶具有良好的亲水性;氨基化氢化丁腈橡胶的亲水性随着氨基含量的增加而增强,氨基含量为0%时,接触角为107°氨基含量为12.42%~63.3%时,接触角下降为90.2°~46.2°。本发明制备的新型氨基化氢化丁腈橡胶,氨基的存在为含羧基、环氧基有机物的引入提供了活性位点,可进行进一步地改性,拓宽了丁腈橡胶的应用。附图说明图1是实施例2中氨基化氢化丁腈橡胶制备的路线图。图2是实施例2与实施例3中,氨基化氢化丁腈橡胶HNMR表征的氨基含量随反应时间变化图。图3是实施例2与实施例3中,氨基化氢化丁腈橡胶接触角表征图,其中a~f对应于氨基含量为0%~63.3%。图4是对比例中,氨基化氢化丁腈橡胶HNMR表征结果的氨基含量随反应时间变化图。具体实施方式现以以下实施例来说明本发明,但不用来限制本发明的范围。实施例中使用的手段,如无特别说明,均使用本领域常规的手段。实施例1:制备纳米Rh金属催化剂1、制备RhCl3·3H2O水溶液将263.5mgRhCl3·3H2O盐与40mL去离子水混合,室温磁力搅拌12h,得RhCl3·3H2O前驱体水溶液,即A液;2、制备氢氧化钠的水合肼溶液将氢氧化钠溶解于水合肼溶液中,磁力搅拌均匀,得氢氧化钠的水合肼溶液即B液。氢氧化钠摩尔量为12mmol,氢氧化钠与水合肼的摩尔比为1:2;3、两种溶液的混合将A液在60℃条件下滴入B溶液中,磁力搅拌4h,对制备的产物进行离心抽滤,干燥得到黑色粉末即纳米Rh催化剂。实施例2:氨基化氢化丁腈橡胶的制备1、将实施例1中制备的60mg纳米Rh金属催化剂与丁腈橡胶混合,超声10分钟,混合均匀;纳米Rh金属催化剂与丁腈橡胶干重的质量比为2%。2、将步骤1所得混合液加入反应釜内衬中,在80℃、1000r/min,4MPa氢气压强条件下进行第一步催化加氢,反应5.5h;3、对第一步催化加氢反应产物进行离心,除去黑色纳米金属Rh催化剂,向反应物中加入质量分数占催化加氢反应产物为1%的RhCl(PPh3)3催化剂,在120℃,4MPa氢气压强下反应2h,对反应产物进行干燥:干燥温度50℃,干燥12小时。本实施例制备的氨基化氢化丁腈橡胶路线如图1所示。本实施例制备的氨基化氢化丁腈橡胶氨基含量见表1,氨基含量用核磁表征,氨基含量随反应时间变化见图2。实施例3制备方法同实施例2,区别在于步骤2中反应时间分别为1h,2h,3h,4h。氨基含量见表1,核磁表征结果见图2。对样品进行接触角测试,测试结果见表2及图3。图3中,a~f分别对应于氨基含量为0%,12.42%,21.04%,33.13%,40%,63.3%。表1反应时间对氨基含量的影响反应时间/h12345.5氨基含量%12.4221.0433.134063.3通过表1可知,通过控制反应时间,可以制备氨基含量可控的氨基化氢化丁腈橡胶,随着反应时间的延长,氨基含量逐渐增加。表2氨基含量对接触角的影响氨基含量%012.4221.0433.134063.3接触角/°10790.281.176.566.146.2通过表2可知,氨基含量逐渐增加时,其与蒸馏水的接触角逐渐下降,亲水性增强。实施例4制备方法同实施例2,区别在于步骤2中氢气压强分别为1MPa,2MPa,3MPa,步骤2的反应时间是5.5小时。氨基化氢化丁腈橡胶中的氨基含量见表3。表3氢气压强对氨基含量的影响氢气压强/MPa123氨基含量%151936通过表3可知,氨基化氢化丁腈橡胶中氨基含量随着氢气压强的增加而增加。对比实施例2结果,通过控制反应时间能较好的控制氨基含量,故优先选择控制反应时间来控制氨基化氢化丁腈橡胶中氨基含量。对比例:调换制备方法中步骤2与步骤31、将262mgRhCl(PPh3)3催化剂与丁腈橡胶混合,超声10分钟,混合均匀;RhCl(PPh3)3催化剂与丁腈橡胶干重的质量比为1%;2、将步骤1所得混合液加入反应釜内衬中,在120℃,4MPa氢气压强下反应2h,进行第一步催化加氢反应;3、将第一步反应产物冷却,向其中加入60mg纳米金属Rh催化剂,其中纳米金属Rh催化剂与丁腈橡胶干重的质量比为2%,在80℃、1000r/min,4MPa氢气压强下反应3~19h,隔一段时间取样一次,对反应产物进行干燥,进行HNMR表征,表征结果见图4及表4。表4反应时间对氨基含量的影响反应时间/h37111519氨基含量%6.6913.4516.5520.6921.04对比表4和表1可知,对比实施例中氨基生成速率明显低于实施例2,基于工业化效率考虑,制备氨基含量可控的氢化丁腈橡胶优先选择实施例2的方法。以上制备的亲水性氨基化氢化丁腈橡胶的实施例都是示例性的。本发明采用两步法制备的氨基化氢化丁腈橡胶,第一步是以自制的纳米Rh催化剂部分催化氢化丁腈橡胶中的碳碳双键和腈基,第二步是选择性催化氢化第一步反应产物中残余的碳碳双键,这两步可以制备氨基含量可控的氨基化氢化丁腈橡胶,制备的氨基化氢化丁腈橡胶具有良好的亲水性,为开发氨基化氢化丁腈橡胶在填隙剂、高分子复合材料等方面的应用奠定了基础。本领域的技术人员应知晓,对本发明进行适当的变动,催化加氢顺序,氢气压强,改变催化加氢基体(如改为端羟基液体丁腈),改变反应时间,均在本发明的范围内。