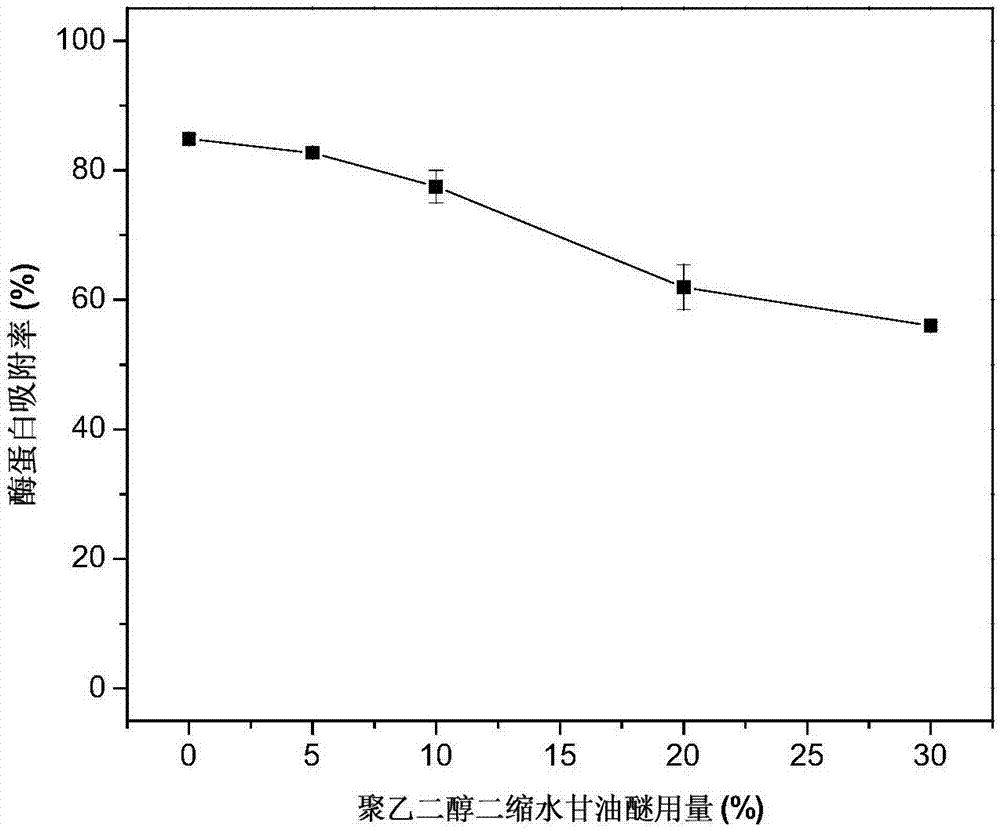
本发明涉及木屑预处理及酶解,具体涉及一种通过组合预处理促进木屑酶解的方法。
背景技术:
:随着人类社会对化石资源需求的日益增长和过度开采,地球上化石资源不可避免地面临着枯竭殆尽的命运。木质纤维原料是地球上最为丰富的可再生资源,它通过植物的光合作用将太阳能捕捉并以聚合物的形式储存起来。利用工业生物技术将木质纤维原料转化为可替代能源及化学品等是缓解化石资源短缺的重要途径之一。木质纤维原料主要包括阔叶材、针叶材、能源作物、农作物秸秆、农林废弃物以及城市纤维垃圾等。杨树是我国重要的经济树种,目前已形成从育种、培育、加工利用和家具生产的完整产业链。据不完全统计,我国杨木人工林种植面积已达800万公顷以上,其种植面积和蓄积量均居世界首位。由此带动了我国杨木加工产业的迅猛发展,因此产生的杨木加工木屑总量也极为可观。然而,目前这些杨木木屑利用率较低,主要用于农民家庭染料,少部分用于刨花板生产、制浆造纸和食用菌基料。因此,在能源制约及环境污染的大背景下,以杨木木屑为原料,通过工业生物技术,将其转化为能源或化学品具有重要的意义。杨木木屑中的纤维素在纤维素酶催化下可降解成单糖,继而被不同微生物发酵成各种能源或化学品。然而,与其它木质纤维原料一样,杨木木屑中纤维素、半纤维素和木质素形成致密的结构,不利于纤维素酶对纤维素的作用。因此,木质纤维原料在进行纤维素酶水解前必须进行预处理,从而破坏木质纤维素的致密结构,以达到提高酶水解效率的目的。常用的预处理方法有稀酸预处理、蒸汽爆破预处理、碱法预处理、水热预处理等。在稀酸预处理过程中,原料中半纤维素大量水解,使得纤维素可及性提高,大大增强了原料纤维素酶水解性能。碱法处理则有效断裂酯键或醚键,从而有利于木质素的溶出。然而,不同种类木质纤维原料的结构差异性导致同样的预处理方法往往呈现出不同的预处理效果。前期研究结果表明,采用常规的稀酸法处理草本原料,如玉米秸秆,可实现预处理玉米秸秆的高效纤维素酶水解。然而,针对于木本原料,即使提高稀酸预处理强度,其稀酸预处理杨木木屑的纤维素酶水解得率仍处于较低水平。同样,前期研究结果表明,聚乙二醇二缩水甘油醚辅助低温碱处理玉米秸秆,使得玉米秸秆木质素在碱预处理过程中实现木质素原位接枝修饰,从而降低木质素疏水性,缓解木质素对纤维素酶的无效吸附,显著提高纤维素酶水解得率。然而,对于杨木木屑,聚乙二醇二缩水甘油醚辅助的低温碱处理无法破除致密结构。如果提高预处理温度或预处理碱用量,则往往使得木本原料中纤维素或半纤维素的回收率显著下降。因此,为提高杨木木屑的纤维素酶水解性能,建立杨木木屑的高效预处理策略成为亟待解决的问题。技术实现要素:发明目的:为了解决现有木屑预处理效果差、酶解得率低的问题,本发明提供了一种通过组合预处理促进木屑酶解的方法。技术方案:本发明所述一种通过组合预处理促进木屑酶解的方法,包括以下步骤:(1)使用酸性水溶液对木屑进行酸预处理,固液分离得到含低聚木糖的酸性水溶液和滤渣;(2)使用碱性水溶液对步骤(1)得到的滤渣进行碱预处理,所述碱性水溶液中添加聚乙二醇缩水甘油醚;碱处理结束后固液分离得到富含纤维素的物料;(3)使用纤维素酶酶解步骤(2)得到的富含纤维素的物料,得到葡萄糖。优选地,所述木屑为杨木木屑。步骤(1)中,所述酸性水溶液为体积浓度为5-10%的醋酸水溶液,或质量浓度为0.1-2%的硫酸水溶液或盐酸水溶液,木屑和酸性水溶液的固液比为1g:5-20mL(固液比按木屑绝干重计,木屑含水量低,所含水分不计入酸性水溶液中),所述酸预处理的条件如下:140-190℃处理0.4-1.0h。优选将滤渣经水洗、过滤后用于后续的碱处理。步骤(2)中,所述碱性水溶液为10-50g/L的氢氧化钠水溶液,所述滤渣和氢氧化钠水溶液的固液比为1g:5-20mL(固液比按滤渣绝干重计,滤渣所含水分计入氢氧化钠水溶液中,用于计算氢氧化钠水溶液的浓度和体积),所述碱预处理的条件如下:60-90℃处理1-4h;优选氢氧化钠水溶液的浓度为30-50g/L。所述聚乙二醇缩水甘油醚为聚乙二醇单缩水甘油醚、聚乙二醇二缩水甘油醚中的任意一种或两种的组合。所述聚乙二醇缩水甘油醚的质量为所述滤渣质量的5-30%,优选20-30%,滤渣质量按绝干重计。优选将富含纤维素的物料经水洗、过滤,洗去残余的碱液、溶出的木质素及糖分。步骤(3)中,酶解体系包括如下组分:纤维素酶、步骤(2)得到的富含纤维素的物料、柠檬酸缓冲液和水,纤维素酶酶解纤维素得到葡萄糖;其中富含纤维素的物料中的水分计入酶解体系。所述酶解体系中纤维素的浓度为10-100g/L,纤维素酶的用量为10-40FPU/g纤维素。所述酶解体系在45-55℃,pH4.0-6.0条件下酶解48-72h。其中纤维素酶的酶活定义如下:一个滤纸酶活力的国际单位(FPU)等于在标准反应条件下每分钟生成1μmol葡萄糖量的酶量。有益效果:与现有技术相比,本发明的杨木木屑的高效组合预处理方法,在醋酸处理后,进行添加聚乙二醇缩水甘油醚的碱预处理,有效减弱了酶水解过程中木质素对纤维素酶的非特异性吸附,有利于促进纤维素酶水解的进行。醋酸处理有效水解了木质素中的芳基醚键,从而释放了更多的游离酚羟基,为聚乙二醇缩水甘油醚的接枝修饰提供了更多的反应位点。这有效地提高了木质素的亲水性修饰程度,进一步加强了木质素原位修饰对酶非特异性吸附的缓解作用。试验结果表明,与单独采用醋酸处理或聚乙二醇缩水甘油醚辅助碱预处理杨木木屑的酶解得率相比,本发明的组合预处理使得酶水解得率由30%提高至80%以上。同时本发明可实现低聚木糖联产,为杨木木屑各组分的综合利用提供了一个新途径。附图说明图1为组合处理杨木木屑酶水解72h后酶蛋白吸附率结果图。具体实施方式以下实施例中,葡萄糖和木糖浓度采用高效液相色谱法(HPLC)测定。色谱条件如下:色谱仪:Agillent1200高效液相色谱仪;色谱柱:Bio-RadAminexHPX-87H;流动相:0.005mol/L硫酸,流速:0.6mL/min;柱温:55℃;检测器:示差折光检测器;进样量:10μL。外标法测定。以下实施例中,醋酸处理液中低聚木糖浓度采用间接酸解法测定。具体测定方法如下:取10mL醋酸处理液,用氢氧化钠将pH调节至7.0左右,并定容至50mL;取10mL处理后的样品溶液于酸解瓶中,并加入10mL8%(w/v)硫酸,于121℃下处理60min。采用HPLC测定酸解后样品中和醋酸处理液中的木糖浓度,并通过酸解前后木糖浓度差计算低聚木糖浓度。低聚木糖浓度(g/L)=酸解后样品中木糖浓度g/L×2×5-醋酸处理液中木糖浓度g/L。式中:2和5均为稀释倍数。实施例中,聚乙二醇二缩水甘油醚和聚乙二醇单缩水甘油醚用量以醋酸处理杨木木屑绝干重计,以聚乙二醇二缩水甘油醚用量20%(g/g)为例,指预处理100g绝干醋酸处理杨木木屑,聚乙二醇二缩水甘油醚用量为20g,聚乙二醇二缩水甘油醚分子量为500。实施例1一种杨木木屑的高效组合预处理方法,步骤如下:(1)称取绝干重为200g杨木木屑,用5%(v/v)醋酸水溶液,于固液比1:10(g/mL,下同),170℃下处理0.5h。(2)醋酸处理结束后,进行固液分离,产生的处理液为富含低聚木糖的醋酸水溶液,其低聚木糖浓度及得率见表1;其产生的固体残渣经水洗、过滤后得到醋酸处理杨木木屑,其主要成分分析见表1。其中,低聚木糖得率(%)=(水解液中低聚糖浓度g/L×10)÷(1000g×木聚糖含量)×100%。式中:1为醋酸处理总体积,L;1000为底物绝干重,g。(3)称取绝干重为20g上述醋酸处理杨木木屑,用10-50g/L氢氧化钠水溶液,聚乙二醇二缩水甘油醚用量20%,固液比1:10g/mL,70℃下共处理3h。其中,聚乙二醇二缩水甘油醚质量按醋酸处理杨木木屑绝干重计。(4)组合处理结束后,物料经水洗及过滤收集。聚乙二醇二缩水甘油醚辅助组合处理杨木木屑的主要成分分析见表2。(5)分别称取纤维素绝干重为1.00g的上述组合处理杨木木屑于250mL水解瓶中,在每个水解瓶中加入1mol/L柠檬酸缓冲液2.5mL、酶用量为20FPU/g纤维素的纤维素酶和适量蒸馏水,使酶解体系中水分总体积为50mL,用玻棒将反应体系充分混匀后盖上盖子,于150rpm、pH4.8、50℃的恒温摇床中酶解72h。酶解结束后,分别将水解物用离心机于10000rpm条件下离心5min,取上清液测定其中的葡萄糖浓度,并计算酶水解得率,数据取双平行试验平均值。其中,纤维素酶解得率(%)=(水解液中葡萄糖浓度g/L×0.9)×0.05÷(底物绝干重g×葡聚糖含量)×100%。式中:0.9为葡萄糖与纤维素的转换系数;0.95为纤维二糖与纤维素的转换系数;0.05为水解液体积,L。醋酸处理杨木木屑主要成分分析及低聚木糖得率见表1。表1醋酸处理杨木木屑主要成分分析及低聚木糖得率表1结果表明,醋酸处理使得杨木木屑中木聚糖水解为单糖及低聚木糖,木聚糖含量显著下降,而葡聚糖和酸不溶木质素含量显著升高。此外,在醋酸处理液中检测到低聚木糖,基于未处理杨木木屑中木聚糖的含量计算其低聚木糖得率达37.60%。添加20%聚乙二醇二缩水甘油醚的组合处理杨木木屑主要成分分析以及酶解得率见表2。表2聚乙二醇二缩水甘油醚辅助组合处理杨木木屑的主要成分分析及酶解得率表2结果表明,在相同聚乙二醇二缩水甘油醚用量下(20%,g/g),随着预处理碱用量的增加,组合处理杨木木屑中葡聚糖含量逐渐增加,而木聚糖及酸不溶木质素含量逐渐降低,同时纤维素酶解得率显著提高。实施例2一种杨木木屑的高效组合预处理方法,步骤如下:(1)称取绝干重为200g杨木木屑,用5%(v/v)醋酸水溶液,于固液比1:10(g/mL,下同),170℃下处理0.5h。(2)醋酸处理结束后,进行固液分离,分别收集处理液和处理固体残渣;固体残渣经水洗、过滤后待用。(3)称取绝干重为20g上述醋酸处理杨木木屑,用30g/L氢氧化钠水溶液,聚乙二醇二缩水甘油醚用量为5-30%,固液比1:10g/mL,70℃下共处理3h。其中,聚乙二醇二缩水甘油醚质量按醋酸处理杨木木屑绝干重计。(4)组合处理结束后,物料经水洗及过滤收集。聚乙二醇二缩水甘油醚辅助组合处理杨木木屑的主要成分分析见表3。(5)分别称取纤维素绝干重为1.00g的上述组合处理杨木木屑于250mL水解瓶中,在每个水解瓶中加入1mol/L柠檬酸缓冲液2.5mL、酶用量为20FPU/g纤维素的纤维素酶和适量蒸馏水,使酶解体系中水分总体积为50mL,用玻棒将反应体系充分混匀后盖上盖子,于150rpm、pH4.8、50℃的恒温摇床中酶解72h。酶解结束后,分别将水解物用离心机于10000rpm条件下离心5min,取上清液测定其中的葡萄糖浓度,并计算酶水解得率,数据取双平行试验平均值。聚乙二醇二缩水甘油醚辅助组合处理杨木木屑72h酶解得率见表3。表3聚乙二醇二缩水甘油醚辅助组合处理杨木木屑的主要成分分析及酶解得率从表3结果表明,在相同碱浓度下(30g/L),随着聚乙二醇二缩水甘油醚用量的增加,预处理玉米秸秆中酸不溶木质素含量逐渐增加,预处理物料酶解得率逐渐升高。当聚乙二醇二缩水甘油醚用量超过20%时,酶解得率的升高趋势趋于平缓。实施例3一种杨木木屑的高效组合预处理方法,纤维素酶吸附情况试验,具体步骤如下:(1)称取绝干重为200g杨木木屑,用5%(v/v)醋酸水溶液,于固液比1:10(g/mL,下同),170℃下处理0.5h。(2)醋酸处理结束后,进行固液分离,分别收集处理液和处理固体残渣;固体残渣经水洗、过滤后待用。(3)称取绝干重为20g上述醋酸处理杨木木屑,用30g/L氢氧化钠水溶液,聚乙二醇二缩水甘油醚用量为5-30%,固液比1:10g/mL,70℃下共处理3h。(4)组合处理结束后,物料经水洗及过滤收集,用于纤维素酶解操作。(5)分别称取纤维素绝干重为1.00g的上述组合处理杨木木屑于250mL水解瓶中,在每个水解瓶中加入1mol/L柠檬酸缓冲液2.5mL、酶用量为20FPU/g纤维素的纤维素酶和适量蒸馏水,使酶解体系中水分总体积为50mL,用玻棒将反应体系充分混匀后盖上盖子,于150rpm、pH4.8、50℃的恒温摇床中酶解72h。(6)酶解72h后,分别将水解物用离心机于10000rpm条件下离心5min,取上清液测定其中游离酶蛋白的浓度,并计算相对酶蛋白含量,数据取双平行试验平均值。其中,酶蛋白吸附率(%)=(酶解体系中添加的总酶蛋白浓度g/L-上清液中酶蛋白浓度g/L)÷(酶解体系中添加的总酶蛋白浓度g/L)×100%。以与组合处理中未添加聚乙二醇二缩水甘油醚为对照,进行同步试验。结果如图1所示,在未添加聚乙二醇二缩水甘油醚组合处理的杨木木屑酶解对照试验中,酶解72h后组合处理杨木木屑对纤维素酶吸附量达总酶蛋白含量的84.8%。然而,在试验样的酶解试验中,随着聚乙二醇二缩水甘油醚添加量增加,酶解72h后组合处理杨木木屑对纤维素酶的吸附率逐渐降低。当聚乙二醇二缩水甘油醚添加量为30%时,其72h酶蛋白吸附率下降至56.0%,远低于对照组。说明添加聚乙二醇二缩水甘油醚辅助组合处理杨木木屑降低了物料对纤维素酶的非特异性吸附。实施例4一种杨木木屑的高效组合预处理方法,木质素酚羟基含量测定,具体步骤如下:(1)称取绝干重为200g杨木木屑,用5%(v/v)醋酸水溶液,于固液比1:10(g/mL,下同),170℃下处理0.5h;醋酸处理结束后,进行固液分离,分别收集处理液和处理固体残渣;固体残渣经水洗、过滤后待用,记作物料1。(2)称取绝干重为20g杨木木屑,用30g/L氢氧化钠水溶液,固液比1:10g/mL,70℃下共处理3h;处理结束后,物料经水洗及过滤收集待用,记作物料2。(3)称取绝干重为20g上述醋酸处理杨木木屑(物料1),用30g/L氢氧化钠水溶液,固液比1:10g/mL,70℃下共处理3h;未添加聚乙二醇二缩水甘油醚的组合处理结束后,物料经水洗及过滤收集,计做物料3。(4)称取绝干重为20g上述醋酸处理杨木木屑(物料1),用30g/L氢氧化钠水溶液,聚乙二醇二缩水甘油醚用量为20%,固液比1:10g/mL,70℃下共处理3h;组合处理结束后,物料经水洗及过滤收集,计做物料4。(5)取上述物料1-4,干燥处理后,于球磨机中进行球磨处理,球磨速度为600rpm,有效球磨时间为6h。(6)取上述球磨木粉于二氧六环/水(96:4,v/v)溶剂中进行木质素提取,固液比为为1:10,提取所得木质素为磨木木质素。(7)采用31P核磁共振技术分析上述4种磨木木质素的酚羟基含量,结果如表4所示。表4四种预处理杨木木屑中木质素酚羟基含量(mmol/g)物料1物料2物料3物料4酚羟基含量1.791.012.070.12从表4结果表明,在单独采用低温碱处理杨木木屑(物料2)中,其木质素的游离酚羟基含量最低(1.01mmol/g)。单独采用醋酸处理以及未添加聚乙二醇二缩水甘油醚辅助的组合处理后,预处理杨木木屑(物料1和物料3)中木质素的游离酚羟基含量显著升高。说明醋酸处理有效水解了木质素中的芳基醚键,从而释放了游离的酚羟基,为聚乙二醇二缩水甘油醚的接枝修饰提供了更多的反应位点。此外,在添加聚乙二醇二缩水甘油醚辅助的组合处理杨木木屑(物料4)中,木质素的游离酚羟基含量显著下降至0.12mmol/g,进一步说明聚乙二醇二缩水甘油醚成功的接枝于木质素酚羟基上。实施例5方法同实施例1,不同的地方如下:步骤(1)中醋酸水溶液的体积浓度为10%,杨木木屑和醋酸水溶液的固液比为1:5(g/mL),140℃处理1.0h;步骤(3)中滤渣和氢氧化钠水溶液的固液比为1:5(g/mL),添加的为聚乙二醇单缩水甘油醚,60℃处理4h;步骤(5)中称取纤维素绝干重为5.00g的组合杨木木屑,纤维素酶的用量为40FPU/g纤维素,55℃酶解72h。实施例6方法同实施例1,不同的地方如下:步骤(1)中醋酸水溶液的体积浓度为10%,杨木木屑和醋酸水溶液的固液比为1:20(g/mL),190℃处理0.4h;步骤(3)中滤渣和氢氧化钠水溶液的固液比为1:20(g/mL),90℃处理1h;步骤(5)中称取纤维素绝干重为0.5g的组合杨木木屑,纤维素酶的用量为10FPU/g纤维素,45℃酶解48h。对比例1一种杨木木屑醋酸处理方法,即单独采用醋酸对杨木木屑进行预处理,不进行碱处理,步骤同实施例2中的步骤(1)、(2)和(5),不包括步骤(3)和(4)。其中,步骤(2)得到的醋酸处理杨木木屑的主要成分分析和酶解得率见表5。表5醋酸处理杨木木屑的主要成分分析及酶解得率表5结果表明,单独采用醋酸处理杨木木屑,其酶解得率仅为32.31%,远低于实施例1和实施例2中添加聚乙二醇二缩水甘油醚辅助的组合处理杨木木屑酶解得率(52.63-83.48%)。对比例2一种杨木木屑聚乙二醇二缩水甘油醚辅助碱处理方法,即单独采用聚乙二醇二缩水甘油醚辅助碱法对杨木木屑进行预处理,具体步骤如下:(1)称取绝干重为20g杨木木屑,用30-50g/L氢氧化钠水溶液,聚乙二醇二缩水甘油醚用量为20%,固液比1:10g/mL,70℃下共处理3h。(2)处理结束后,物料经水洗及过滤收集;添加聚乙二醇二缩水甘油醚辅助碱处理杨木木屑的主要成分分析见表6。(3)分别称取纤维素绝干重为1.00g的上述组合处理杨木木屑于250mL水解瓶中,在每个水解瓶中加入1mol/L柠檬酸缓冲液2.5mL、酶用量为20FPU/g纤维素的纤维素酶和适量蒸馏水,使酶解体系中水分总体积为50mL,用玻棒将反应体系充分混匀后盖上盖子,于150rpm、pH4.8、50℃的恒温摇床中酶解72h。酶解结束后,分别将水解物用离心机于10000rpm条件下离心5min,取上清液测定其中的葡萄糖浓度,并计算酶水解得率,数据取双平行试验平均值,结果见表6。表6添加聚乙二醇二缩水甘油醚辅助碱处理杨木木屑的主要成分分析及酶解得率从表6结果表明,在相同聚乙二醇二缩水甘油醚用量下(20%,g/g),当碱预处理碱浓度为30-50g/L时,其酶解得率仅为30.13-35.32%,同样远低于实施例1和实施例2中添加聚乙二醇二缩水甘油醚辅助的组合处理杨木木屑酶解得率(52.63-83.48%)。对比例3一种杨木木屑的高效组合预处理方法,步骤同实施例1,但在碱处理时不添加聚乙二醇二缩水甘油醚,未添加聚乙二醇二缩水甘油醚辅助组合处理杨木木屑的主要成分分析和酶解结果见表7。表7未添加聚乙二醇二缩水甘油醚辅助组合处理杨木木屑的主要成分分析及酶解得率表7结果表明,与实施例1的结果相比,在相同碱用量下,实施例1中酸不溶木质素含量(表2)均高于本实施例中酸不溶木质素含量。这是聚乙二醇二缩水甘油醚接枝修饰木质素的结果。另外,在相同碱浓度处理条件下,本实施例的酶解得率均低于实施例1的酶解得率,在处理碱浓度为30g/L时,实施例1的酶解得率为80.86%(表1),比本实施例的酶解得率(37.89%)提高了2.13倍。当前第1页1 2 3