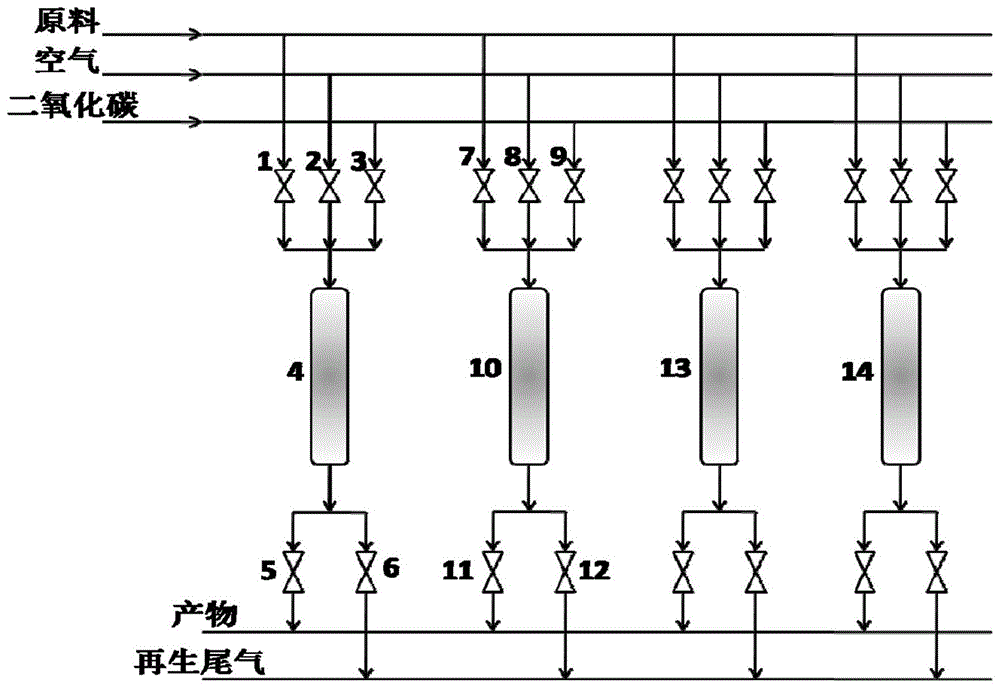
本发明涉及一种二氧化碳氧化乙苯脱氢制苯乙烯的连续化生产工艺。
背景技术:
:苯乙烯是合成树脂、橡胶、塑料等高分子材料的最重要单体之一。乙苯直接脱氢是工业上生产苯乙烯的主要工艺技术,占全球苯乙烯产量85%以上。然而,在该工艺过程中,存在以下几点问题:(1)乙苯脱氢反应为强吸热反应(△ho298.15k=+117.6kj/mol),导致工艺操作温度高,一般控制在600~700℃;(2)需要大量的过热水蒸气作为稀释剂以降低反应物乙苯的分压,而水的气化潜热较大,且反应过程对反应后水蒸气的气化潜热并未回收利用,仅冷凝成液体,大量水蒸气的使用导致能耗巨大;(3)该工艺使用fe-k系工业催化剂,但活性组分不稳定,易因k的流失而失活,导致催化剂无法循环利用。现如今,工业生产中,“环境友好”、“节能降耗”、努力实现“绿色化”的趋势不断深入各大石化产业链,在这样的背景下发展新的乙苯脱氢工艺十分必要。为此,相继研究了以co2、o2、n2o等作为氧化剂的乙苯氧化脱氢制苯乙烯技术。其中,co2氧化乙苯脱氢工艺可以明显克服传统乙苯直接脱氢的缺陷,粗略估计,生产一吨苯乙烯的能耗为(1.5~1.9×108卡),与过热水蒸气工艺相比降低约一个数量级(1.5×109卡),同时在提高苯乙烯选择性、温室气体co2活化转化等方面也具有突出的优点,表现出了很好的发展前景,因此受到国内外研究学者的广泛关注。尽管前人对co2氧化乙苯脱氢的高效催化剂筛选、反应机理等已进行了深入研究,而且在改善催化剂活性及co2氧化乙苯脱氢反应机理等方面取得了一些突破性进展。但是,迄今为止所研究报道的催化剂的稳定性较差,严重制约了co2氧化乙苯脱氢技术的工业化应用。技术实现要素:本发明的目的是针对目前乙苯直接脱氢能耗大,以及目前二氧化碳氧化乙苯脱氢催化剂长周期稳定性差和催化剂循环利用的问题,提供一种工艺流程简单、设备投入低、能耗小、催化剂稳定性及再生性能较好的二氧化碳氧化乙苯制苯乙烯的连续化生产工艺。针对上述目的,本发明采用的技术方案为:将乙苯和二氧化碳通入装填有钒系催化剂的固定床反应器,进行二氧化碳氧化乙苯脱氢制苯乙烯反应;氧化脱氢反应完后,固定床反应器进入再生模式进行再生反应,再生模式时,先采用二氧化碳为吹扫气进行吹扫,然后采用空气或空气和二氧化碳的混合气为再生气进行再生反应;上述固定床反应器至少为3个以上,其中至少有一个固定床反应器进行再生反应,其余固定床反应器同时进行氧化脱氢反应。上述钒系催化剂的质量百分比组成为:五氧化二钒3%~15%、二氧化铈1%~5%、二氧化锆1%~5%、三氧化二铝74%~94%。上述工艺过程中,所述乙苯和二氧化碳的摩尔比为5~30,氧化脱氢反应的温度为500~600℃、压力为0~0.1mpa、时间为50~200h,氧化脱氢反应中乙苯的质量空速为0.5~2h-1。上述工艺过程中,乙苯转化率低于40%时进行再生反应,所述再生反应的温度450~550℃、压力为0.01~0.1mpa、时间5~20h,再生气的体积空速为200~1000h-1。上述工艺过程中,采用二氧化碳吹扫后,脱附的乙苯和二氧化碳的混合气直接通入氧化脱氢反应的固定床反应器,进行原料回收利用;再生反应后尾气经分离纯化,得到的二氧化碳作为原料继续进入氧化脱氢反应的固定床反应器参与反应。上述的固定床反应器为绝热固定床反应器或等温固定床反应器。本发明的有益效果如下:1、本发明利用钒基催化剂优良的活性和再生性能,同时结合多个反应器同时进行氧化脱氢反应,且至少一个反应器进行再生反应的工艺模式,实现了二氧化碳氧化乙苯脱氢制苯乙烯的连续高效生产。2、本发明再生反应时,采用原料气二氧化碳作为吹扫气,避免了水蒸气或者其他惰性气体的使用,降低了成本,且吹扫后流出的气体为二氧化碳和未反应的乙苯,无须冷却分离可直接循环利用。3、本发明再生反应时,采用空气和二氧化碳作为再生气,再生尾气产生的二氧化碳,经分离纯化,可继续循环使用。4、本发明整个工艺流程简单,设备投入低,苯乙烯选择性高(97%以上),能耗小,催化剂循环使用寿命每年达7200h以上(一年中除再生时间外,催化剂能够进行催化脱氢反应的时间)。附图说明图1是二氧化碳氧化乙苯制苯乙烯的工艺流程示意图。图2是实施例1中的催化剂催化二氧化碳氧化乙苯脱氢的催化性能。图3是实施例2和3中的催化剂催化二氧化碳氧化乙苯脱氢的催化性能。具体实施方式下面结合附图和实施例对本发明进一步详细说明,但本发明的保护范围不仅限于这些实施例。实施例1将14.5g聚乙二醇、0.339g硝酸铈、0.293g硝酸锆、22.5g硝酸铝加入到150ml去离子水中,搅拌溶解,用氨水调节ph至10,继续搅拌3h,转入水热反应釜中110℃恒温晶化72h,冷却至室温,离心分离,用蒸馏水洗至中性,80℃干燥12h,然后在空气中550℃焙烧4h,得到载体a。将0.081g偏钒酸铵及0.175g草酸溶于2ml去离子水中,待形成透明溶液后加入1g载体a中进行等体积浸渍,常温静置老化12h,放入烘箱80℃干燥8h,取出,在空气气氛下550℃焙烧4h,获得钒系催化剂,其质量百分比组成为:五氧化二钒6%、二氧化铈4.1%、二氧化锆2.9%、三氧化二铝87%。采用上述催化剂进行二氧化碳氧化乙苯脱氢制苯乙烯,具体工艺流程如下:如图1所示,固定床反应器4和13为工作状态下的脱氢反应器。以反应器4为例,详细工艺流程如下。原料乙苯经高温二氧化碳预热后,通过阀门1进入填装催化剂的固定床反应器4,经脱氢反应后的产物通过阀门5,进入下一步的分离提纯,原料回收再利用。反应一段时间,当乙苯转化率低于40%时,停止反应,关闭阀门1,打开阀门7和阀门11,启动固定床反应器10,将原料切换至另一个装有新鲜催化剂的固定床反应器10中,保证脱氢反应持续进行。固定床反应器4进行再生反应。再生过程包括:打开阀门3,二氧化碳进入反应器中,吹扫催化剂,一方面通过阀门5带走未反应的乙苯,进行回收利用,另一方面带走一部分热量,将温度降到450~550℃;然后关闭阀门5,打开阀门2和阀门6,切入二氧化碳和空气混合气作为再生气(空气和二氧化体碳积比为1:1),进行再生反应,再生尾气经处理后,将其中的二氧化碳回收,作为反应原料继续使用。关闭阀门2,二氧化碳吹扫一段时间后,关闭阀门3和阀门6,再生后的固定床反应器4进入待用状态。可通过优化再生周期和再生时间,保证至少两个反应器同时进行脱氢反应,一个反应器进行再生反应。同时可根据实际生产和工艺需求,合理控制14甚至更多的备用固定床反应器的启用。本实施例中,脱氢反应的温度为550℃,床层压力0.03mpa,乙苯质量空速0.6h-1,二氧化碳和乙苯摩尔比为20。脱氢反应进行200h后乙苯转化率低于40%,此时进行催化剂再生反应,再生温度480℃、压力0.05mpa、再生气的体积空速500h-1。反应结果见表1和图2。实施例2将7.45g异丙醇铝加入60ml乙醇与甲苯体积比1:1的混合溶液中,充分混合,得到异丙醇铝溶液;将0.239g硝酸铈、0.158g硝酸锆加入9ml乙醇中搅拌至完全溶解后,加入上述异丙醇铝溶液中,混合均匀后90℃回流3h,常温静置12h,加入5ml水作沉淀剂,形成凝胶后80℃干燥12h,然后在550℃焙烧4h,记做载体b。将0.081g偏钒酸铵与0.175g草酸溶于2ml去离子水中,待形成透明溶液后加入1g载体b进行等体积浸渍,静置12h,放入烘箱80℃干燥5h,取出,在空气中550℃焙烧4h,获得钒系催化剂,其质量百分比组成为:五氧化二钒6%、二氧化铈4.8%、二氧化锆2.5%、三氧化二铝86.7%。采用上述催化剂,按照实施例1的工艺流程进行二氧化碳氧化乙苯脱氢制苯乙烯,脱氢反应的温度为550℃,床层压力0.02mpa,乙苯质量空速0.6h-1,二氧化碳和乙苯摩尔比为20。脱氢反应进行130h后乙苯转化率低于40%,此时进行催化剂再生反应,再生温度500℃、压力0.05mpa,再生气的体积空速500h-1。反应结果见表1和图3。实施例3本实施例的催化剂为实施例2中经过再生后的催化剂,其他工艺条件与实施例2相同。反应结果见表1和图3。实施例4将7.45g异丙醇铝加入60ml乙醇与甲苯体积比1:1的混合溶液中,充分混合,得到异丙醇铝溶液;将0.239g硝酸铈、0.158g硝酸锆加入9ml乙醇中搅拌至完全溶解后,加入上述异丙醇铝溶液中,混合均匀后,再加入0.148g偏钒酸铵与0.320g草酸,90℃回流3h,常温静置12h,加入5ml水作沉淀剂,形成凝胶后80℃干燥12h,然后在550℃焙烧4h,获得钒系催化剂,其质量百分比组成为:五氧化二钒6%、二氧化铈4.6%、二氧化锆2.4%、三氧化二铝87%。采用上述催化剂,按照实施例1的工艺流程进行二氧化碳氧化乙苯脱氢制苯乙烯,脱氢反应的温度为550℃,床层压力0.05mpa,乙苯质量空速0.6h-1。脱氢反应进行150h后乙苯转化率低于40%,此时进行催化剂再生反应,再生温度500℃、压力0.05mpa,再生气的体积空速500h-1。反应结果见表1。实施例5将14.5g聚乙二醇、0.3390g硝酸铈、0.2929g硝酸锆、22.5g硝酸铝、0.119g偏钒酸铵、0.257g草酸加入到150ml去离子水中,搅拌溶解,用氨水调节ph至9.5~11.0,继续搅拌3小时,转入水热反应釜中110℃恒温晶化72h,冷却至室温,离心分离,用蒸馏水洗至中性,80℃干燥12h,然后在空气中550℃焙烧4h,获得钒系催化剂,其质量百分比组成为:五氧化二钒6%、二氧化铈4.6%、二氧化锆2.4%、三氧化二铝87%。采用上述催化剂,按照实施例1的工艺流程进行二氧化碳氧化乙苯脱氢制苯乙烯,脱氢反应温度550℃,床层压力0.05mpa,乙苯质量空速0.6h-1。脱氢反应进行180h后乙苯转化率低于40%,此时进行催化剂再生反应。再生气为空气,再生温度500℃,再生压力0.05mpa,体积空速500h-1。反应结果见表1。表1不同实施例与对比例的催化剂性能结果乙苯转化率/(%)苯乙烯选择性/(%)再生周期/h再生时间/h实施例170982008实施例2589813010实施例3599813010实施例465971508实施例5639818012注:表中再生周期是指乙苯转化率低于40%时的脱氢反应时间。由表1及图1~3可见,不同的催化剂的制备方法制备的钒基催化剂都表现出优良的催化活性(乙苯初始转化率大于55%,苯乙烯选择性97%以上)。同时稳定性好,能够在长时间催化反应中(100~200h),保持较高的乙苯转化率(大于40%)。实施例2和3的反应结果说明,钒基催化剂具有优良的再生性能(再生前后,催化剂活性无明显变化)。因此将钒基催化剂的优势与图1的工艺流程结合,通过优化脱氢反应条件以及再生反应的周期和时间,能够很好地实现二氧化碳氧化乙苯制苯乙烯的连续化生产。当前第1页12