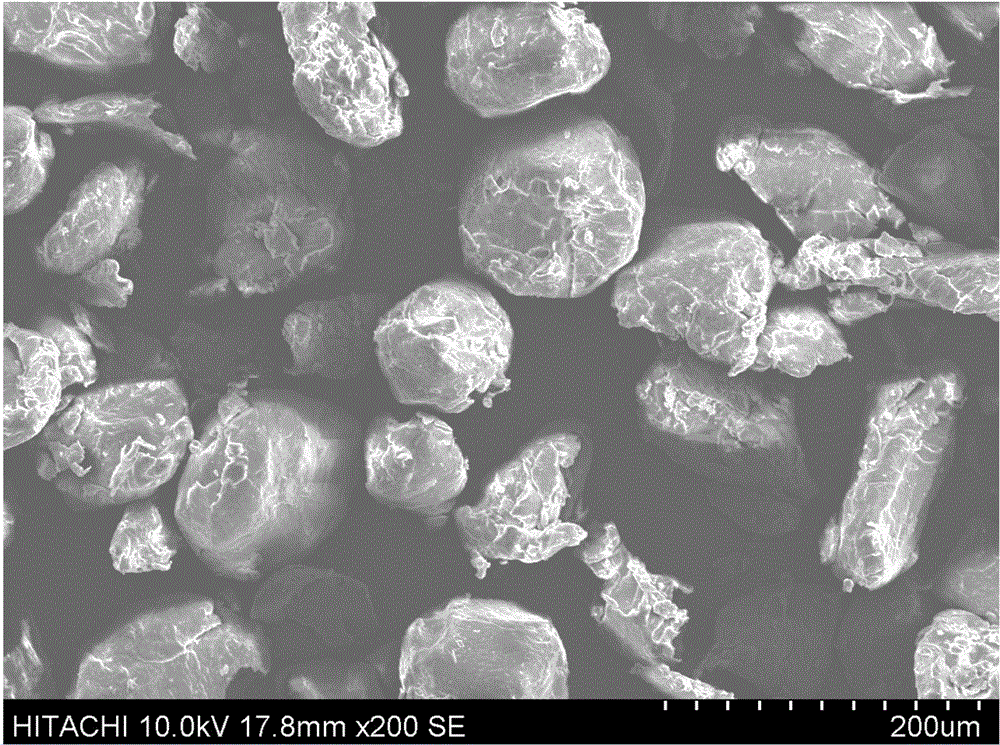
本发明涉及绿色高分子材料
技术领域:
,特别是涉及一种3d打印粉末及其制备方法。
背景技术:
:3d打印技术与传统技术相比,可设计性强,工序简单,能耗低,适合定制化生产,可大大缩短从设计到制件的生产周期,因此目前在医疗、艺术等个性化需求较强的领域被广泛应用。针对不同应用领域,开发了不同材料种类的3d打印粉末。在高分子3d打印粉末材料中,聚酰胺3d打印粉末的研究和应用是重要的研究领域之一。目前,制备聚酰胺3d打印粉末的方法主要为深冷粉碎法结合研磨法。专利cn107151441a、专利cn108017905a等专利利用深冷粉碎法,对聚酰胺颗粒料进行破碎获得粒径较小的聚酰胺3d打印粉末,但是该技术获得的粉末颗粒形状均一度差,粉体流动性差。并且如需实现功能性,只能通过与功能性添加剂共混改性,存在混合不均的缺陷,对制件性能稳定性造成影响。现有聚酰胺3d打印粉末通常使用的都是以纯聚酰胺树脂原材料,基于聚酰胺废料回收提纯过程与制备3d打印粉末过程一体化的技术鲜有报道。3d打印粉末的流动性与树脂流动性不同,粉体的流动性直接影响铺粉的均匀性或送粉的稳定性。粉末流动性太差,易造成粉层厚度不均,扫描区域内的熔化量不均,导致制件内部结构不均,影响成形质量;而高流动性的粉末易于流化,沉积均匀,粉末利用率高,有利于提高3d打印成形件的尺寸精度和表面均匀致密化。粉末的流动性不仅与粒径有关,而且与粉末颗粒表面摩擦性、凹凸程度(圆润)有关,只有粒径均一、表面摩擦力均一、圆润的3d打印粉末才具有良好的粉末流动性。现有技术中,难以实现3d打印粉末中抗氧剂均匀分散。抗氧剂一般会在螺杆的高温和剪切下充分熔融,部分氧功能化合物团聚和析出,造成树脂基体中的抗氧剂分布不均匀,3d打印粉末表面具有凹凸不平的光稳定剂析出物。如果通过扫描电镜观察制件中有比抗氧剂颗粒自身粒径大很多的颗粒或空洞,则说明抗氧剂有团聚和析出。技术实现要素:本发明目的在于,提高一种抗氧剂在树脂基体中分布均匀、颗粒圆润、粒径与堆积密度适宜的3d打印粉末及其制备方法,使其制备的3d打印制件具有更优秀的抗氧化性能。本发明是通过以下技术方案实现的:一种3d打印粉末,按重量份计,包括以下组分:聚酰胺树脂100份;抗氧剂0.1-3份;所述的抗氧剂的粒径均以小于10微米的形态分散于聚酰胺树脂基体中;3d打印粉末的粒径分布范围是d(0.1)<20微米且d(0.9)<110微米,粉体流动性为≤10s/50g,堆积密度0.45-0.65g/cm3。对于抗氧剂的选择,只要满足以下条件即可:能溶于本发明工艺的复配溶剂,并且能够喷入水中后与聚酰胺一起析出。具体的,所述的抗氧剂选自如下化合物中的至少一种:抗氧剂1:四[β-(3,5-二叔丁基-4-羟基苯基)丙酸]季戊四醇酯,cas号:6683-19-8,抗氧剂1010的主要成分;抗氧剂2:n,n’-双-(3-(3,5-二叔丁基-4-羟基苯基)丙酰基)己二胺,cas号:23128-74-7,抗氧剂1098的主要成分;抗氧剂3:β-(3,5-二叔丁基-4-羟基苯基)丙酸十八碳醇酯,cas号:2082-79-3,songnox1076的主要成分;抗氧剂4:己二醇双[3-(3,5-二叔丁基-4-羟基苯基)丙酸酯],cas号35074-77-2,抗氧剂259的主要成分:抗氧剂5:1,3,5-三甲基-2,4,6-三(3,5-叔丁基-4-羟基苄基)苯,cas号1709-70-2,抗氧剂330的主要成分;抗氧剂6:1,3,5-三(3,5-二叔丁基-4-羟基苯基丙酰氧基乙基)异氰尿酸酯,cas号34137-09-2,抗氧剂3125的主要成分;抗氧剂7:1,3,5-三(3,5-二叔丁基-4-羟基苄基)异氰尿酸,cas号27676-62-6,抗氧剂3114的主要成分;抗氧剂8:3,9-双[1,1-二甲基-2-[(3-叔丁基-4-羟基-5-甲基苯基)丙酰氧基]乙基]-2,4,8,10-四氧杂螺[5.5]十一烷,cas号90498-90-1,抗氧剂ga-80的主要成分;抗氧剂9:1,3,5-三(4-叔丁基-3-羟基-2,6-二甲基苄基)-1,3,5-三嗪-2,4,6-(1h,3h,5h)-三酮,cas号40601-76-1,抗氧剂1790的主要成分;抗氧剂10:n,n’-双[β-(3,5-二叔丁基-4-羟基苯基)丙酰]肼,cas号32687-78-8,抗氧剂1024的主要成分;抗氧剂11:三乙二醇醚-二(3-叔丁基-4-羟基-5-甲基苯基)丙酸酯,cas号36443-68-2,songonx2450的主要成分;抗氧剂12:季戊四醇四(3-月桂基硫代丙酸酯),cas号29598-76-3,抗氧剂thanox412s的主要成分;抗氧剂13:2,4-二(十二烷基硫甲基)-6-甲基苯酚,cas号110675-26-8,抗氧剂1726的主要成分;抗氧剂14:2,4-二(正辛基硫亚甲基)-6-甲基苯酚,cas号,110553-27-0,抗氧剂1520的主要成分;抗氧剂15:二丁基羟基甲苯,cas号204-881-4,抗氧剂264的主要成分;抗氧剂16:4,4'-硫代双(6-叔丁基-3-甲基苯酚),cas号202-525-2,抗氧剂300的主要成分;抗氧剂17:三(2.4-二叔丁级苯级)亚磷酸酯,cas号31570-04-4,抗氧剂168的主要成分。所述的抗氧剂在聚酰胺树脂基体中分布是通过以下方法检测:将3d打印粉末以3d打印方式制成样条,截取样条中的一段置于溶液中浸泡24小时溶解样条表面的抗氧剂但是不溶解聚酰胺,之后用扫描电子显微镜观察样条截面形貌。具体的,将3d打印粉末以3d打印方式制成样条,截取样条中的一段置于可溶抗氧剂但是不可溶聚酰胺的溶液中(比如:氯仿、甲苯、dmf、乙酸乙酯、丙酮等),浸泡处理24小时,之后用扫描电子显微镜观察样条截面形貌,截面形貌中的孔洞分布形态即为抗氧剂的分布形态,孔洞均匀且直径小于5微米说明抗氧剂分布均匀且没有发生团聚和析出;部分区域平滑无孔洞而部分区域有孔洞且直径大于20微米说明抗氧剂分布不均有团聚和析出的情况。通过扫描电镜显微镜(一般100-300微米或更高精度)也可以看到3d打印粉末表面的突起、圆润度情况。通过本发明方法得到的3d打印粉末的粉体流动性为≤10s/50g。3d打印粉末流动性使用粉体流动仪测试。通过本发明方法得到的3d打印粉末的粒径分布范围是d(0.1)<20微米且d(0.9)<110微米。粒径范围的测试方法为按照标准gb/t19077-2016进行测试。d(0.1)<20微米表示10%的3d打印粉末的粒径小于20微米,d(0.9)<110微米表示90%的3d打印粉末的粒径小于110微米。通过本发明方法得到的3d打印粉末的堆积密度0.45-0.65g/cm3。堆积密度的测试方法为利用树脂的自重,将试样从规定的高度自由落入已知容积的容器中,测量单位体积的树脂的质量,即得到堆积密度的大小。3d打印粉末的粒径与堆积密度影响着3d打印过程中材料的熔融过程。过低的堆积密度与过大的粒径会导致3d打印耗时更长(特别是延长3d打印粉末的受高温熔融时长);过高的堆积密度与过小的粒径会导致3d打印过程中3d打印粉末受热不均匀,使制件性能受到影响。优选的,3d打印粉末树脂基体中,抗氧剂的粒径均小于5微米,3d打印粉末的粒径分布范围是d(0.1)<30微米且d(0.9)<90微米,粉体流动性为≤9s/50g,堆积密度0.53-0.62g/cm3。通过本发明的方法,可以处理绝大部分种类的聚酰胺,经过实验,以下聚酰胺都可以通过本发明的方法制备得到上述性能的3d打印粉末。所述的聚酰胺树脂为脂肪族聚酰胺、半芳香族聚酰胺中的至少一种;所述的脂肪族聚酰胺选自pa6、pa66、pa12、pa1010、pa1012、pa11、pa610、pa69、pa1212中的至少一种;所述的半芳香族聚酰胺选自pa5t、pa6t610、pa6t6i、pa6t1010、pa10t、pa10t10i、pa10t1010、pa10t1012、pa10t6t中的至少一种。本发明具体实施方式举例pa12、pa66、pa10t。上述的3d打印粉末的制备方法,包括以下步骤:(a)将聚酰胺原料加入复配溶剂中,加热达到50℃至溶液回流的温度并搅拌至溶解(如有不溶物,增加过滤工序将不溶物滤除;如溶液颜色较深,则增加脱色处理工序),得到聚酰胺澄清溶液;(b)将抗氧剂加入聚酰胺澄清溶液中,搅拌至溶解,得到抗氧功能性聚酰胺溶液;(c)将抗氧功能性聚酰胺溶液以喷雾方式喷入去离子水中,析出3d打印粉末,期间,去离子水的温度维持0-60℃范围内;所述的复配溶剂,按重量份计,包括10-30份苯酚、15-40份甲苯;聚酰胺原料与复配溶剂重量比为1:10-1:2;析出过程中,抗氧功能性聚酰胺溶液与去离子水的重量比为1:5-1:50。脱色处理工序为加入脱色剂,将溶液升温达到50℃至溶液回流温度保持0.5-2小时,再降温至低于50℃后过滤。所述的脱色剂选自活性炭、活性白土中的至少一种。优选的,步骤(a)将溶液加热达到100℃至溶液回流温度,步骤(c)中,析出3d打印粉末时,去离子水的温度维持20-50℃范围内。通过控制此步骤中去离子的温度来控制聚酰胺与抗氧剂的析出与结晶速率,能够进一步缩小抗氧剂在树脂基体中的粒径分布,同时使3d打印粉末颗粒更圆润、粒径分布更窄。所述的聚酰胺原料来源于聚酰胺新料、聚酰胺回收料、聚酰胺废料中的至少一种;聚酰胺新料是新合成得到的,其中含有大于等于99wt%的聚酰胺树脂;聚酰胺回收料是将聚酰胺废料通过回收工艺处理得到的聚酰胺,其中含有大于等于99wt%的聚酰胺树脂;聚酰胺废料为报废丢弃的聚酰胺制品,其中聚酰胺树脂含量范围是25-90wt%。步骤(b)中,也可以通过与其他功能改性剂一同加入聚酰胺澄清溶液中同时进行多功能改性。本发明与现有技术相比,具有如下有益效果:本发明克服了现有3d打印粉末制备技术的缺陷,提供了一种3d打印粉末及其制备方法。本发明的3d打印粉末不同于共混改性获得的材料,抗氧剂在3d打印粉末的树脂基体中粒径细小且分布不团聚(粒径均小于10微米,优选小于5微米)、3d打印粉末形状圆润流动性较好,利用其打印获得的制件平整,抗氧化性能优秀。本发明还提供了该3d打印粉末的制备方法,该抗氧化功能性3d打印粉末可以来源于聚酰胺废料也可以来源于聚酰胺新料。本方法可一体化完成聚酰胺废料的提纯和3d打印粉末制备过程。工艺的最后步骤采用喷雾的方式将聚酰胺溶液喷到水中,这样可以实现聚酰胺充分、粒径均一、圆润无凹凸的析出,无需筛选即可使得3d打印粉末的粒径分布范围是d(0.1)<20微米且d(0.9)<110微米,粉体流动性为≤10s/50g,堆积密度0.45-0.65g/cm3。附图说明图1:本发明实施例1的表面圆润的3d打印粉末扫描电镜照片,形状圆润均一性强。图2:市售的3d打印粉末扫描电镜照片,颗粒粒径不均,形状各异表面凹凸多。图3:对比例3的3d打印粉末扫描电镜照片,颗粒粒径不均,形状各异表面凹凸多。图4:本发明实施例1的3d打印粉末利用3d打印方式制备的样条经刻蚀处理后的形貌,抗氧剂分布均匀,无团聚和析出的现象。图5:通过共混方法制备得到的3d打印粉末(对比例3),利用3d打印方式制备的样条经刻蚀处理后的形貌,抗氧剂分布不均,有明显的团聚现象。具体实施方式下面结合具体实施例对本发明进行详细说明。以下实施例将有助于本领域的技术人员进一步理解本发明,但不以任何形式限制本发明。应当指出的是,对本领域的普通技术人员来说,在不脱离本发明构思的前提下,还可以做出若干变形和改进。这些都属于本发明的保护范围。本发明所用原料来源如下:聚酰胺废料pa12:来自水暖管道、汽车发动机周边零件等回收料,含有少量色粉,理论上pa12含量约为95%-97%。聚酰胺废料pa66:来自机械设备中齿轮、轴承等零部件的回收料,含有玻纤增强,理论上pa66含量约为65%-70%。聚酰胺废料pa10t:来自发动机周边零部件回收料,含有玻纤增强,理论上pa10t含量为60-70%。pa12新料:阿科玛,p201tl;pa12回收料:自制,将上述聚酰胺废料pa12粉碎,加入3倍聚酰胺废料重量的复配溶剂(重量比苯酚:甲苯=1:1),加热至80℃搅拌溶解,降温至30℃后过滤得到聚酰胺溶液;再将聚酰胺溶液加入去离子水中,分离掉液体得到pa12回收料。苯酚:工业纯;甲苯:工业纯;抗氧剂1:抗氧剂1010,市售;抗氧剂3:songnox1076,市售;抗氧剂4:抗氧剂259,市售;抗氧剂11:songonx2450,市售;抗氧剂10:抗氧剂1024,市售;抗氧剂12:thanox412s,市售;n,n’-双-(3-(3,5-二叔丁基-4-羟基苯基)丙酰基)己二胺:市售。各项性能测试方法考察3d打印粉末中抗氧剂的分布:将实施例和对比例3d打印粉末通过3d打印成样条后参照说明书列举的方法处理样条的一面,再进行(1)测试。(1)sem形貌分析测试:将试样固定在样品台并黏在导电胶上,表面镀金作为导电层,置于样品舱中抽真空,并调整电流电压,观察样品形貌,统计得到抗氧剂孔洞粒径。扫描至20微米-500微米之间。(2)3d打印粉末流动性测试:使用粉体流动仪,按照使用方法测试。(3)3d打印粉末粒径测试:按照标准gb/t19077-2016进行测试。(4)3d打印粉末堆积密度测试:利用树脂的自重,将试样从规定的高度自由落入已知容积的容器中,测量单位体积的树脂的质量,即得到堆积密度的大小(测试标准gb/t20316.2-2006)。(5)通过sem考察3d打印粉末外观:将试样固定在样品台并黏在导电胶上,表面镀金作为导电层,置于样品舱中抽真空,并调整电流电压,观察样品形貌,扫描至20微米-500微米之间。实施例1:将100g聚酰胺废料pa12加入复配溶剂(100g苯酚/200g甲苯)中,加热至温度80℃搅拌至溶解,再加入10g活性炭,保温搅拌0.5小时,降温至40℃后过滤,得到聚酰胺澄清溶液;将0.8g抗氧剂1加入聚酰胺澄清溶液中,搅拌至充分溶解,得到功能性聚酰胺溶液;再将功能性聚酰胺溶液以喷雾方式喷入4000g去离子水中(去离子水温度维持0-10℃),析出聚酰胺3d打印粉末;干燥后称量,再进行其他性能的测试。实施例2:实施例2与实施例1的区别在于,抗氧剂3与活性炭一同加入。实施例3:实施例3与实施例1的区别在于,抗氧剂为4。实施例4:实施例4与实施例1的区别在于,抗氧剂为11。实施例5:实施例5与实施例1的区别在于,抗氧剂为10。实施例6:实施例6与实施例1的区别在于,采用n,n’-双-(3-(3,5-二叔丁基-4-羟基苯基)丙酰基)己二胺代替抗氧剂a。实施例7:将100g聚酰胺废料pa10t加入复配溶剂(100g苯酚/200g甲苯)中,加热至温度100℃搅拌至溶解,再加入10g活性炭,升温至120℃,保温搅拌1小时,降温至40℃后过滤,得到聚酰胺澄清溶液;将0.5g抗氧剂1加入聚酰胺澄清溶液中,搅拌至充分溶解,得到功能性聚酰胺溶液;再将功能性聚酰胺溶液以喷雾方式喷入4000g去离子水中(去离子水温度维持25-30℃),析出聚酰胺3d打印粉末;干燥后称量,再进行其他性能的测试。实施例8:将100g聚酰胺废料pa66加入复配溶剂(80g苯酚/160g甲苯)中,加热至温度105℃搅拌至溶解,再加入10g活性炭,保温搅拌0.5小时,降温至50℃后过滤,得到聚酰胺澄清溶液;将0.8g抗氧剂1加入聚酰胺澄清溶液中,搅拌至充分溶解,得到功能性聚酰胺溶液;再将功能性聚酰胺溶液以喷雾方式喷入4000g去离子水中(去离子水温度维持30-35℃),析出聚酰胺3d打印粉末;干燥后称量,再进行其他性能的测试。实施例9:将100g的pa12新料加入复配溶剂(100g苯酚/200g甲苯)中,加热至温度100℃搅拌至溶解,保温搅拌1小时,降温至50℃后过滤,得到聚酰胺澄清溶液;将1.0g抗氧剂12加入聚酰胺澄清溶液中,搅拌至充分溶解,得到功能性聚酰胺溶液;再将功能性聚酰胺溶液以喷雾方式喷入4000g去离子水中(去离子水温度维持20-30℃),析出聚酰胺3d打印粉末;干燥后称量,再进行其他性能的测试。实施例10:将100g的pa12回收料加入复配溶剂(100g苯酚/200g甲苯)中,加热至温度110℃搅拌至溶解,再加入10g活性炭,保温搅拌0.5小时,降温至50℃后过滤,得到聚酰胺澄清溶液;将1.0g抗氧剂12加入聚酰胺澄清溶液中,搅拌至充分溶解,得到功能性聚酰胺溶液;再将功能性聚酰胺溶液以喷雾方式喷入4000g去离子水中(去离子水温度维持30-40℃),析出聚酰胺3d打印粉末;干燥后称量,再进行其他性能的测试。实施例11:实施例11与实施例1的区别在于,步骤(a)中将溶液加热至温度60℃搅拌至溶解,去离子水温度维持50-60℃。对比例1:将100g聚酰胺废料pa12加入复配溶剂(100g苯酚/200g甲苯)中,加热至温度100℃搅拌至溶解,再加入10g活性炭,保温搅拌0.5小时,降温至40℃后过滤,得到聚酰胺澄清溶液;将0.8g抗氧剂1加入聚酰胺澄清溶液中,搅拌至充分溶解,得到功能性聚酰胺溶液;在10分钟内向功能性聚酰胺溶液加入4000g去离子水,析出聚酰胺抗氧化改性颗粒;干燥后将粒料在液氮中低温冷冻至-120℃以下,使之实现脆化易粉碎状态,再将冷冻好的粒料投入低温粉碎机腔体内,通过叶轮高速旋转进行粉碎加工;由气流筛分机进行分级并收集,选择粒度在120~400目范围内的3d打印粉末。对比例2:将100g聚酰胺废料pa12加入1500g的复合溶剂中(甲酸15%、盐酸10%、乙酸35%、水40%),在80℃下搅拌溶解4h,后离心分离(转速为4000r/min)的到清液,再清液中投入0.8g抗氧剂1,搅拌均匀,再将溶液通入1500g的去离子水中,析出pa12沉淀,沉淀,去离子水洗涤pa12颗粒至ph呈中性,干燥后将粒料在液氮中低温冷冻至-120℃以下,使之实现脆化易粉碎状态,再将冷冻好的粒料投入低温粉碎机腔体内,通过叶轮高速旋转进行粉碎加工;由气流筛分机进行分级并收集,选择粒度在120~400目范围内的3d打印粉末。对比例3:将100g聚酰胺废料pa12加入复配溶剂(100g苯酚/200g甲苯)中,加热至温度100℃搅拌至溶解,再加入10g活性炭,保温搅拌0.5小时,降温至40℃后过滤,得到聚酰胺澄清溶液;再将聚酰胺澄清溶液通入4000g去离子水中,析出回收聚酰胺pa12。将干燥后的回收聚酰胺pa12与0.8g抗氧剂1通过双螺杆挤出机挤出造粒(螺杆长径比为45:1,一区170℃,二区180℃,三区190℃,四区205℃,五区215℃,六区225℃,七区235℃,八区240℃,九区245℃,机头温度240℃,转速为350转/分),再将粒料在液氮中低温冷冻至-120℃以下,使之实现脆化易粉碎状态,再将冷冻好的粒料投入低温粉碎机腔体内,通过叶轮高速旋转进行粉碎加工;由气流筛分机进行分级并收集,选择粒度在120~400目范围内的3d打印粉末。表1:实施例和对比例3d打印粉末各项性能测试结果实施例1实施例2实施例3实施例4实施例5实施例6抗氧剂孔洞粒径,微米<10<10<10<10<10<103d打印粉流动性测试,s/50g9.19.09.89.99.39.03d打印粉末粒径测试d(0.1),微米18.918.419.217.719.018.63d打印粉末粒径测试d(0.9),微米103.1103.5107.4106.0100.2108.23d打印粉末堆积密度测试,g/cm30.500.510.500.520.530.52续表1:实施例7实施例8实施例9实施例10实施例11抗氧剂孔洞粒径,微米<5<5<5<5<103d打印粉流动性测试,s/50g8.48.67.98.19.03d打印粉末粒径测试d(0.1),微米28.726.628.127.419.33d打印粉末粒径测试d(0.9),微米87.589.188.586.6101.63d打印粉末堆积密度测试,g/cm30.550.590.600.570.51续表1:对比例1对比例2对比例3抗氧剂孔洞粒径,微米>10>10>153d打印粉流动性测试,s/50g16.215.119.43d打印粉末粒径测试d(0.1),微米13.521.819.73d打印粉末粒径测试d(0.9),微米482.2410.0453.63d打印粉末堆积密度测试,g/cm30.400.410.39由实施例和对比例1-3的对比可知,通过本发明的方法得到的3d打印粉末,其中抗氧剂无明显的团聚现象,在树脂基体中分布的粒径小于5微米,并且3d打印粉末粒径均一性强,堆积密度高。而通过其他方法得到的3d打印粉末,抗氧剂有明显的团聚现象,并且3d打印粉末粒径均一性差,堆积密度低。当前第1页12