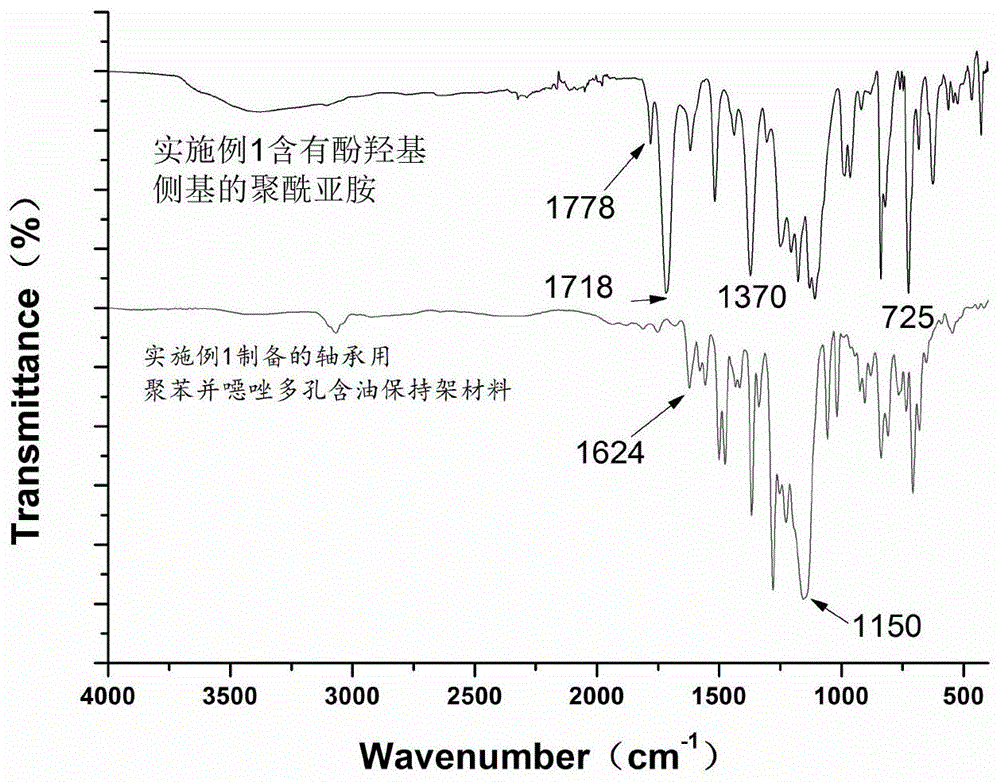
本发明涉及有机材料制备
技术领域:
,尤其涉及一种轴承用聚苯并噁唑多孔含油保持架材料及其制备方法。
背景技术:
:多孔聚合物轴承保持架材料的理化性质和润滑特性直接决定了轴承精度和使役寿命。随着长寿命高精密轴承的发展,聚合物多孔含油材料也在不断向高温、高载、高性能化发展。多孔聚酰亚胺轴承保持架具有贯通的孔结构,不但可以将滚动体互相隔离,还可以利用其内部的孔隙结构含蓄润滑油,实现润滑油的存储与供给。轴承高速运转时,孔隙中吸附的润滑油在离心力作用下甩出参与滚动体与保持架的界面润滑,轴承停止运转时,离心作用甩出的润滑油在毛细作用下重新被吸附到多孔保持架内部并存储起来,供后续运转时再次甩出参与润滑,在不需要外部供油设备的前提下,实现了润滑油由于“离心作用甩出”和“毛细作用回收”、交替作用而形成的“向外供油”-“向内吸油”的多次循环往复,实现轴承保持架的长寿命免维护供油。现有的多孔聚酰亚胺材料基于上海合成树脂研究所的ys-20材料,其颗粒粒径约为10~50μm,颗粒相对较大,采用传统的四柱液压机加压结合限位烧结的制备工艺(如zl200410010165.3和zl201310480892.5),得到的孔隙的平均孔径均在1.0μm以上,而平均孔径大小直接决定了贯通孔隙的毛细作用进而影响了含蓄的润滑油的甩出与吸附,因此,现有的ys-20制备的多孔聚酰亚胺保持架,在3000rpm转速下即可将润滑油甩出,而轴承转速进一步提高时,出油速率过快,导致润滑油在较短的时间内从保持架内部甩出,降低了轴承保持架的供油寿命,且不适用于高速轴承。技术实现要素:有鉴于此,本发明的目的在于提供一种轴承用聚苯并噁唑多孔含油保持架材料及其制备方法。本发明制得的轴承用聚苯并噁唑多孔含油保持架材料的孔径范围为0.33~0.50μm,孔径分布宽度窄,具有较高的含油率和含油保持率,为高速轴承在苛刻条件下的长效免维护自润滑提供了保障。为了实现上述发明目的,本发明提供以下技术方案:本发明提供了轴承用聚苯并噁唑多孔含油保持架材料的制备方法,包括以下步骤:在保护气氛下,将芳香族二元酸酐、芳香族邻羟基二元胺和极性非质子性溶剂混合进行溶液缩聚反应,得到中间体均相溶液;将所述中间体均相溶液与脱水剂混合后进行酰亚胺化反应,得到含有酚羟基侧基的聚酰亚胺模塑粉;将所述含有酚羟基侧基的聚酰亚胺模塑粉进行冷等静压成型,得到冷压毛坯;将所述冷压毛坯进行热等静压可控成型,得到多孔聚苯并噁唑材料;将所述多孔聚苯并噁唑材料进行浸油处理,得到所述轴承用聚苯并噁唑多孔含油保持架材料。优选地,所述芳香族邻羟基二元胺为2,2-双(3-氨基-4-羟基苯基)六氟丙烷;所述芳香族二元酸酐为均苯四甲酸二酐、3,3’,4,4’-二苯醚四甲酸二酐、3,3’,4,4’-联苯四甲酸二酐、3,3’,4,4’-二苯酮四甲酸二酐或4,4’-(六氟异丙烯)二酞酸酐。优选地,所述芳香族二元酸酐与芳香族邻羟基二元胺的摩尔比为1:1。优选地,所述热等静压可控成型的条件为:压强为40~150mpa,由室温以2~10℃/min的升温速率升温至最高温度,所述最高温度为350~550℃,所述最高温度下的保压保温时间为30~300min。优选地,所述酰亚胺化反应的温度为150~160℃,时间为12~24h。优选地,所述冷等静压成型的条件为:压强50~150mpa,保压时间15~90min,温度为室温。优选地,所述冷等静压成型在柔性聚氨酯包套中进行,所述柔性聚氨酯包套的邵氏硬度a为40~60ha。优选地,所述极性非质子性溶剂为n-甲基吡咯烷酮、n,n-二甲基乙酰胺或n,n-二甲基甲酰胺,所述极性非质子性溶剂的质量为所述芳香族二元酸酐和芳香族邻羟基二元胺总质量的3~6倍。优选地,所述脱水剂包括苯、甲苯和二甲苯中的一种或多种,所述脱水剂的质量为中间体均相溶液的质量的20%~40%。本发明还提供了上述技术方案所述的制备方法制得的轴承用聚苯并噁唑多孔含油保持架材料,所述轴承用聚苯并噁唑多孔含油保持架材料的平均孔径为0.33~0.50μm,孔隙率为17.7%~20.7%本发明提供了一种轴承用聚苯并噁唑多孔含油保持架材料的制备方法,包括以下步骤:在保护气氛下,将芳香族二元酸酐、芳香族邻羟基二元胺和极性非质子性溶剂混合进行溶液缩聚反应,得到中间体均相溶液;将所述中间体均相溶液与脱水剂混合后进行酰亚胺化反应,得到含有酚羟基侧基的聚酰亚胺模塑粉;将所述含有酚羟基侧基的聚酰亚胺模塑粉进行冷等静压成型,得到冷压毛坯;将所述冷压毛坯进行热等静压可控成型,得到多孔聚苯并噁唑材料;将所述多孔聚苯并噁唑材料进行浸油处理,得到所述轴承用聚苯并噁唑多孔含油保持架材料。在本发明中,所述含有酚羟基侧基的聚酰亚胺模塑粉的酚羟基侧基与酰亚胺环在热等静压可控成型的过程中发生热重排反应,脱除co2气体分子,原位生成刚性更大、耐温等级更高的聚苯并噁唑片段,脱除的co2气体分子在热等静压可控成型的过程中以气体形式存在,占据一定的空间,形成孔隙,因此可以实现源于内部分子结构变化的造孔,同时由于co2气体的动力学直径较小,因此以co2气体成核得到的孔径相对较小,利用原位脱除的co2气体分子的气相成核作用,实现对多孔材料中孔径大小及分布、孔隙度占比的调控。本发明中聚酰亚胺每个重复单元中含有两个反应性的酚羟基侧基,该酚羟基可进一步与邻位的酰亚胺环发生热重排反应,脱除co2气体分子后原位生成聚苯并噁唑。本发明综合利用了“刚性堆垛”的物理堆砌成孔和“原位脱除co2气体分子”的气相成核造孔两种机制,对多孔材料的孔性能进行调控和优化,大大降低了轴承用聚苯并噁唑多孔含油保持架材料的孔径范围及孔径分布宽度。而且,本发明中,酚羟基侧基可以与邻近的酰亚胺官能团在热等静压可控成型的过程中脱除co2分子转变为刚性更大、耐温等级更高的苯并噁唑(polybenzoxazle,pbo)片段,从而提高了轴承用聚苯并噁唑多孔含油保持架材料的强度和耐温等级。实施例的数据表明,本发明提供的轴承用聚苯并噁唑多孔含油保持架材料,兼具耐高温(dma法测试,储能模量在400℃前无明显降低,长期使用温度350℃以上)、高强度和低摩擦性,具有较高的含油率和含油保持率,为高速轴承在苛刻条件下的长效免维护自润滑提供了保障。本发明制得的轴承用聚苯并噁唑多孔含油保持架材料达到的主要性能指标如下:(1)邵氏硬度(d):≥75;(2)含油摩擦系数:≤0.10(mm-p2摩擦磨损试验机,载荷200n,线速度0.432m/s,120分钟,对偶为不锈钢钢环,润滑油为pao-10);(3)磨痕宽度:≤2.0mm;(4)环张力:≥30mpa;(5)孔径范围:0.33μm~0.50μm;(6)孔隙率:≥17%;(7)含油率:≥15%。进一步地,本发明中利用冷等静压成型和热等静压可控成型,加压方向为立体360°无死角,相对于现有技术中上下双向加压的方式,本发明的加压方式更加均匀,克服了现有限位烧结技术中使用限位工装、密封包套等冗余操作,成型便利,适用于规模化放大生产,放大规模仅仅取决于冷、热等静压成型设备的生产能力(如加压腔体容量、最大压力、最高温度等设备自身的参数能力)。附图说明图1为实施例1所得轴承用聚苯并噁唑多孔含油保持架材料的傅里叶变换红外光谱图(atr-ftir);图2为实施例2~5所得轴承用聚苯并噁唑多孔含油保持架材料的傅里叶变换红外光谱图(atr-ftir);图3为实施例1~5所得轴承用聚苯并噁唑多孔含油保持架材料的高速甩油曲线;图4为对比例1~4所得样品的甩油曲线;图5为实施例1制备的所得轴承用聚苯并噁唑多孔含油保持架材料的dma曲线(5℃/min,1hz);图6为对比例1制备的ys-20材料的dma曲线(5℃/min,1hz);图7为实施例1和对比例1~4所得样品的孔径分布曲线对比图;图8为实施例1~5所得轴承用聚苯并噁唑多孔含油保持架材料与对比例1所得样品的孔径分布曲线对比图;图9为实施例1~5所得轴承用聚苯并噁唑多孔含油保持架材料的含油摩擦曲线。具体实施方式本发明提供了一种轴承用聚苯并噁唑多孔含油保持架材料的制备方法,包括以下步骤:在保护气氛下,将芳香族二元酸酐、芳香族邻羟基二元胺和极性非质子性溶剂混合进行溶液缩聚反应,得到中间体均相溶液;将所述中间体均相溶液与脱水剂混合后进行酰亚胺化反应,得到含有酚羟基侧基的聚酰亚胺模塑粉;将所述含有酚羟基侧基的聚酰亚胺模塑粉进行冷等静压成型,得到冷压毛坯;将所述冷压毛坯进行热等静压可控成型,得到多孔聚苯并噁唑材料;将所述多孔聚苯并噁唑材料进行浸油处理,得到所述轴承用聚苯并噁唑多孔含油保持架材料。若无特殊说明,本发明对各原料的来源没有特殊的限定,采用本领域技术人员熟知的市售商品即可。本发明在保护气氛下,将芳香族二元酸酐、芳香族邻羟基二元胺和极性非质子性溶剂混合进行溶液缩聚反应,得到中间体均相溶液。在本发明中,所述保护气氛优选为氮气或氩气。在本发明中,所述芳香族邻羟基二元胺优选为2,2-双(3-氨基-4-羟基苯基)六氟丙烷(6fap);所述芳香族二元酸酐优选为均苯四甲酸二酐(pmda)、3,3’,4,4’-二苯醚四甲酸二酐(odpa)、3,3’,4,4’-联苯四甲酸二酐(bpda)、3,3’,4,4’-二苯酮四甲酸二酐(btda)或4,4’-(六氟异丙烯)二酞酸酐(6fda)。在本发明中,所述芳香族二元酸酐优选以粉末的形式加入在本发明中,所述粉末优选分批加入,所述分批的次数优选为2~5次,每次加入粉末的质量优选占总质量的20%~50%,更优选为25%,即均分4次加完所述粉末。在本发明的具体实施例中,优选将芳香族二元酸酐、芳香族邻羟基二元胺和极性非质子性溶剂加入三口瓶中进行混合,更优选为在反应容器内,先加入芳香族邻羟基二元胺,然后加入极性非质子性溶剂,搅拌均匀得到混合物,将芳香族二元酸酐以粉末的形式,分批加入混合物中。在本发明中,所述芳香族二元酸酐与芳香族邻羟基二元胺的摩尔比优选为1:1。在本发明中,所述极性非质子性溶剂优选为n-甲基吡咯烷酮(nmp)、n,n-二甲基乙酰胺(dmac)或n,n-二甲基甲酰胺(dmf),所述极性非质子性溶剂的质量优选为所述芳香族二元酸酐和芳香族邻羟基二元胺总质量的3~6倍,更优选为4~5倍,所述极性非质子性溶剂能够使反应物在溶剂中具有一定的浓度,进而使溶液缩聚反应顺利进行。得到中间体均相溶液后,本发明将所述中间体均相溶液与脱水剂混合后进行酰亚胺化反应,得到含有酚羟基侧基的聚酰亚胺模塑粉。在本发明中,所述脱水剂优选包括苯、甲苯和二甲苯中的一种或多种,所述脱水剂的质量优选为中间体均相溶液的质量的20%~40%,更优选为30%,所述脱水剂的质量优选为中间体均相溶液的质量的20%~40%能够保证脱水剂的脱水效率,当所述脱水剂优选为混合物时,本发明对所述混合物中各组分的种类以及用量没有特殊的限定,采用任意比例混合均可。在本发明中,所述酰亚胺化反应的温度优选为150~160℃,时间优选为12~24h,更优选为18~20h。所述酰亚胺化反应完成后,本发明优选将所得酰亚胺化反应产物自然冷却至室温后,倾倒入水中,析出模塑粉,将所得模塑粉过滤收集并用乙醇洗涤除去残留溶剂后,真空烘干,然后依次粉碎和过筛,得到干燥的所述含有酚羟基侧基的聚酰亚胺模塑粉。在本发明中,所述真空烘干的温度优选为150~160℃,真空度优选≤1pa,本发明对所述真空烘干的时间没有特殊的限定,能够完全除去乙醇即可,在本发明的具体实施例中,优选为24h。在本发明中,所述乙醇洗涤的次数优选为3次,每次乙醇的用量优选为极性非质子性溶剂与脱水剂的总质量。在本发明中,所述含有酚羟基侧基的聚酰亚胺模塑粉的平均粒径优选为5~10μm,本发明对所述粉碎和过筛的具体操作没有特殊的限定,能够得到平均粒径为5~10μm的含有酚羟基侧基的聚酰亚胺模塑粉即可。在本发明的具体实施例中,所述粉碎在粉碎机中进行。得到含有酚羟基侧基的聚酰亚胺模塑粉后,本发明将所述含有酚羟基侧基的聚酰亚胺模塑粉进行冷等静压成型,得到冷压毛坯。在本发明中,所述冷等静压成型的条件优选为:压强50~150mpa,更优选为70~120mpa,进一步优选为90mpa,保压时间15~90min,更优选为20~45min,温度为室温,不需要额外的加热或降温。在本发明中,所述冷等静压成型优选在柔性聚氨酯包套中进行,所述柔性聚氨酯包套的邵氏硬度a优选为40~60,更优选为51。在本发明的具体实施例中,所述柔性聚氨酯包套的形状优选为筒形。在本发明中,所述冷等静压成型的介质优选为水。在本发明中,所述冷等静压过程中,所有物料均不发生化学变化,无新物质的生成,发生的仅仅是物理变化,具体为含有酚羟基侧基的聚酰亚胺模塑粉在高压下,堆砌密度增大,其中含有的空气被挤出来。得到冷压毛坯后,本发明将所述冷压毛坯进行热等静压可控成型,得到多孔聚苯并噁唑材料。得到冷压毛坯后,本发明优选将冷压毛坯干燥,所述干燥的作用是除去经过冷等静压成型后吸附的空气中的水分。在本发明中,所述干燥优选为在真空烘箱中进行,所述真空烘箱的真空度优选≤1pa,温度优选为150~300℃,更优选为200~250℃,时间优选为10~30h,更优选为18~20h。在本发明中,所述热等静压可控成型的条件优选为:压强为40~150mpa,由室温以2~10℃/min的升温速率升温至最高温度,所述最高温度为350~550℃,所述最高温度下的保压时间为30~300min。在本发明中,所述热等静压可控成型的压强更优选为70~120mpa,最优选为90mpa,所述升温速率更优选为5℃/min,所述最高温度更优选为400~500℃,最优选为450℃,所述保压时间优选为60~240min,最优选为180min。在本发明中,所述热等静压可控成型优选在热等静压机中进行。在本发明中,所述热等静压可控成型的过程中,酚羟基侧基以co2气体分子形式脱除,原位生成聚苯并噁唑。在本发明中,所述热等静压可控成型优选在高纯氩气的气氛中进行,所述高纯氩气中氩气的体积含量优选为99.999%。以均苯四甲酸二酐和2,2-双(3-氨基-4-羟基苯基)六氟丙烷为例,制备轴承用聚苯并噁唑多孔含油保持架材料的过程中发生的反应过程如式i所示:所述热等静压可控成型过程中发生的反应过程如式ii所示:分别以均苯四甲酸二酐(pmda)、3,3’,4,4’-二苯醚四甲酸二酐(odpa)、3,3’,4,4’-联苯四甲酸二酐(bpda)、3,3’,4,4’-二苯酮四甲酸二酐(btda)和4,4’-(六氟异丙烯)二酞酸酐(6fda)为芳香族二元酸酐,以2,2-双(3-氨基-4-羟基苯基)六氟丙烷(6fap)为芳香族邻羟基二元胺,得到的多孔聚苯并噁唑材料的结构式如式iii所示:所述热等静压可控成型完成后,本发明优选将所得热等静压可控成型产物自然冷却至室温得到所述多孔聚苯并噁唑材料。得到多孔聚苯并噁唑材料后,本发明将所述多孔聚苯并噁唑材料进行浸油处理,得到所述轴承用聚苯并噁唑多孔含油保持架材料。在本发明中,所述浸油处理前优选还包括机加工,得到内径为10~130mm的圆环状轴承保持架。在本发明中,所述浸油处理优选为真空浸油处理,在本发明中,所述真空浸油处理使用的润滑油的型号优选为pao4、pao10或飞马ii号,更优选为pao10,所述真空浸油处理的温度优选为80~120℃,时间优选为24~72h,真空度优选为≤10pa。本发明还提供了上述技术方案任一项所述的制备方法制得的轴承用聚苯并噁唑多孔含油保持架材料,所述轴承用聚苯并噁唑多孔含油保持架材料的平均孔径为0.33~0.50μm,孔隙率为17.7%~20.7%。为了进一步说明本发明,下面结合实例对本发明提供的轴承用聚苯并噁唑多孔含油保持架材料及其制备方法进行详细地描述,但不能将它们理解为对本发明保护范围的限定。本发明中实施例与对比例中多孔含油保持架材料性能均参照美军标mil-p-29609加工为合适的样条后进行测试。实施例1a、常温、常压下,在氮气保护气氛中,在一配有机械搅拌、温度计和冷凝管的5l三口瓶中,加入183.13g(0.50mol)6fap和1500gn-甲基吡咯烷酮(nmp),搅拌0.5小时,使6fap完全溶解得到6fap溶液,分4批缓慢加入109.06g(0.50mol)pmda粉末,每次加入总质量的25%,粉末加完毕后补加253g溶剂nmp,使得反应体系中nmp的质量为两种单体质量的6倍(即质量浓度为14.29wt%),室温下搅拌反应12小时得到中间体均相溶液2145.19g;然后向所述中间体均相溶液中加入甲苯614g,甲苯的用量为所述中间体均相溶液质量的30%,升温至160℃利用甲苯和水的共沸进行酰亚胺化反应12小时,反应完毕,将反应体系倾倒入水中,析出模塑粉粗品;将所述模塑粉粗品过滤收集并用乙醇洗涤3次以尽量除去残留溶剂,每次洗涤乙醇的用量为溶剂nmp和甲苯的质量之和2367g,在真空烘箱中150℃下烘干24小时,然后在粉碎机中粉碎,并过2000目标准筛,收集过筛后的模塑粉,即得含有酚羟基侧基的聚酰亚胺模塑粉;b、在常温下,将所述含有酚羟基侧基的聚酰亚胺模塑粉80.0g,填装入筒形柔性聚氨酯包套(邵氏硬度a为51ha)中,在冷等静压机中,施加90mpa的压强并在此压强下保持30min,脱模后获得冷压毛坯;c、将所述冷压毛坯首先在真空烘箱内(真空度≤1pa)300℃下真空烘干30小时,然后放入热等静压机,以5℃/min的升温速率,升温到350℃,同时充入高纯氩气(氩气的体积含量为99.999%)使压强升高至70mpa,然后在此条件下保持300min,完成热压烧结,自然冷却至室温后取出,得到多孔聚苯并噁唑材料;之后在数控车床上进行机加工,根据实际需求得到从内径10mm到90mm不等的圆环状轴承保持架,然后经过浸油处理,将保持架浸泡在pao10润滑油中,在120℃真空烘箱中1pa真空度下放置48h,即可得到轴承用聚苯并噁唑多孔含油保持架材料。将轴承用聚苯并噁唑多孔含油保持架材料加工为标准测试样条,分别对其环张力、孔性能及含油性能进行评价,结果见表1。分别对含有酚羟基侧基的聚酰亚胺模塑粉、轴承用聚苯并噁唑多孔含油保持架材料进行结构表征。图1为含有酚羟基侧基的聚酰亚胺经高温350℃热等静压处理后转变为聚苯并噁唑的过程中红外光谱变化情况,未热等静压处理前,1718cm-1、1778cm-1、1370cm-1、725cm-1处酰亚胺环的特征吸收很明显,经过高温处理后,这四个特征峰几乎消失,在1624cm-1处出现苯并噁唑环中c=n双键的特征吸收峰,在1150cm-1处出现苯并噁唑环中c-o单键的伸缩振动特征吸收峰,充分证明了热等静压可控成型后,羟基与邻位的酰亚胺环发生热重排反应脱除co2气体分子,官能团由酰亚胺转变为苯并噁唑。实施例2a、常温、常压下,在氮气保护气氛中,在一配有机械搅拌、温度计和冷凝管的5l三口瓶中,加入183.13g(0.50mol)6fap和1500gdmac,搅拌0.5小时,使6fap完全溶解得到6fap溶液,分5批缓慢加入155.11g(0.50mol)odpa粉末,每次加入粉末总质量的20%,粉末加完毕后补加191g溶剂dmac,使得反应体系中dmac的质量为两种单体质量的5倍(即质量浓度为16.67wt%),室温下搅拌反应18小时得到中间体均相溶液2029.24g;然后向所述中间体均相溶液中加入苯406g,苯的用量为所述中间体均相溶液质量的20%,升温至160℃利用苯和水的共沸进行酰亚胺化反应24小时,反应完毕,将反应体系倾倒入水中,析出模塑粉粗品;将所述模塑粉粗品过滤收集并用乙醇洗涤3次以尽量除去残留溶剂,每次洗涤乙醇的用量为溶剂dmac和苯的质量之和2097g,在真空烘箱中150℃下烘干24小时,然后在粉碎机中粉碎,并过1500目标准筛,收集过筛后的模塑粉,即得含有酚羟基侧基的聚酰亚胺模塑粉;b、在常温下,将所述含有酚羟基侧基的聚酰亚胺模塑粉80.0g,填装入筒形柔性聚氨酯包套(邵氏硬度a为40ha)中,在冷等静压机中,施加150mpa的压强并在此压强下保持15min,脱模后获得冷压毛坯;c、将所述冷压毛坯首先在真空烘箱内(真空度≤1pa)150℃下真空烘干30小时,然后放入热等静压机,以2℃/min的升温速率,升温到550℃,同时充入高纯氩气(氩气的体积含量为99.999%)使压强升高至150mpa,然后在此条件下保持30min,完成热压烧结,自然冷却至室温后取出,得到多孔聚苯并噁唑材料;之后在数控车床上进行机加工,根据实际需求得到从内径10mm到90mm不等的圆环状轴承保持架,然后经过浸油处理,将保持架浸泡在pao4润滑油中,在80℃真空烘箱中10pa真空度下放置72h,即可得到轴承用聚苯并噁唑多孔含油保持架材料。将轴承用聚苯并噁唑多孔含油保持架材料加工为标准测试样条,分别对其环张力、孔性能及含油性能进行评价,结果见表1。实施例3a、常温、常压下,在氮气保护气氛中,在一配有机械搅拌、温度计和冷凝管的5l三口瓶中,加入183.13g(0.50mol)6fap和1200gdmf,搅拌0.5小时,使6fap完全溶解得到6fap溶液,分2批缓慢加入147.11g(0.50mol)bpda粉末,每次加入粉末总质量的50%,粉末加完毕后补加121g溶剂dmf,使得反应体系中dmf的质量为两种单体质量的4倍(即质量浓度为20wt%),室温下搅拌反应24小时得到中间体均相溶液1650g;然后向所述中间体均相溶液中加入二甲苯660g,二甲苯的用量为所述中间体均相溶液质量的40%,升温至160℃利用二甲苯和水的共沸进行酰亚胺化反应18小时,反应完毕,将反应体系倾倒入水中,析出模塑粉粗品;将所述模塑粉粗品过滤收集并用乙醇洗涤3次以尽量除去残留溶剂,每次洗涤乙醇的用量为溶剂dmf和二甲苯的质量之和1981g,在真空烘箱中150℃下烘干24小时,然后在粉碎机中粉碎,并过2000目标准筛,收集过筛后的模塑粉,即得含有酚羟基侧基的聚酰亚胺模塑粉;b、在常温下,将所述含有酚羟基侧基的聚酰亚胺模塑粉80.0g,填装入筒形柔性聚氨酯包套(邵氏硬度a为60ha)中,在冷等静压机中,施加120mpa的压强并在此压强下保持20min,脱模后获得冷压毛坯;c、将所述冷压毛坯首先在真空烘箱内(真空度≤1pa)200℃下真空烘干20小时,然后放入热等静压机,以10℃/min的升温速率,升温到500℃,同时充入高纯氩气(氩气的体积含量为99.999%)使压强升高至120mpa,然后在此条件下保持60min,完成热压烧结,自然冷却至室温后取出,得到多孔聚苯并噁唑材料;之后在数控车床上进行机加工,根据实际需求得到从内径10mm到90mm不等的圆环状轴承保持架,然后经过浸油处理,将保持架浸泡在飞马ii号润滑油中,在100℃真空烘箱中10pa真空度下放置24h,即可得到轴承用聚苯并噁唑多孔含油保持架材料。将轴承用聚苯并噁唑多孔含油保持架材料加工为标准测试样条,分别对其环张力、孔性能及含油性能进行评价,结果见表1。实施例4a、常温、常压下,在氮气保护气氛中,在一配有机械搅拌、温度计和冷凝管的5l三口瓶中,加入183.13g(0.50mol)6fap和900gnmp,搅拌0.5小时,使6fap完全溶解得到6fap溶液,分4批缓慢加入161.12g(0.50mol)btda粉末,每次加入粉末总质量的25%,粉末加完毕后补加132g溶剂nmp,使得反应体系中nmp的质量为两种单体质量的3倍(即质量浓度为25wt%),室温下搅拌反应12小时得到中间体均相溶液1376.23g;然后向所述中间体均相溶液中加入甲苯413g,甲苯的用量为所述中间体均相溶液质量的30%,升温至160℃利用甲苯和水的共沸进行酰亚胺化反应12小时,反应完毕,将反应体系倾倒入水中,即可析出模塑粉粗品;将所述模塑粉粗品过滤收集并用乙醇洗涤3次以尽量除去残留溶剂,每次洗涤乙醇的用量为溶剂nmp和甲苯的质量之和1445g,在真空烘箱中150℃下烘干24小时,然后在粉碎机中粉碎,并过2000目标准筛,收集过筛后的模塑粉,即得含有酚羟基侧基的聚酰亚胺模塑粉;b、在常温下,将所述含有酚羟基侧基的聚酰亚胺模塑粉80.0g,填装入筒形柔性聚氨酯包套(邵氏硬度a为51ha)中,在冷等静压机中,施加50mpa的压强并在此压强下保持90min,脱模后获得冷压毛坯;c、将所述冷压毛坯首先在真空烘箱内(真空度≤1pa)250℃下真空烘干18小时,然后放入热等静压机,以5℃/min的升温速率,升温到450℃,同时充入高纯氩气(氩气的体积含量为99.999%)使压强升高至90mpa,然后在此条件下保持180min,完成热压烧结,自然冷却至室温后取出,得到多孔聚苯并噁唑材料;之后在数控车床上进行机加工,根据实际需求得到从内径10mm到90mm不等的圆环状轴承保持架,然后经过浸油处理,将保持架浸泡在pao10润滑油中,在120℃真空烘箱中10pa真空度下放置48h,即可得到轴承用聚苯并噁唑多孔含油保持架材料。将轴承用聚苯并噁唑多孔含油保持架材料加工为标准测试样条,分别对其环张力、孔性能及含油性能进行评价,结果见表1。实施例5a、常温、常压下,在氮气保护气氛中,在一配有机械搅拌、温度计和冷凝管的5l三口瓶中,加入183.13g(0.50mol)6fap和2000gdmac,搅拌0.5小时,使6fap完全溶解得到6fap溶液,分4批缓慢加入222.12g(0.50mol)6fda粉末,每次加入粉末总质量的25%,粉末加完毕后补加432g溶剂dmac,使得反应体系中dmac的质量为两种单体质量的6倍(即质量浓度为14.29wt%),室温下搅拌反应18小时得到中间体均相溶液2837.23g;然后向所述中间体均相溶液中加入甲苯851g,甲苯的用量为所述中间体均相溶液质量的30%,升温至160℃利用甲苯和水的共沸进行酰亚胺化反应18小时,反应完毕,将反应体系倾倒入水中,即可析出模塑粉粗品;将所述模塑粉粗品过滤收集并用乙醇洗涤3次以尽量除去残留溶剂,每次洗涤乙醇的用量为溶剂dmac和甲苯的质量之和3283g,在真空烘箱中150℃下烘干24小时,然后在粉碎机中粉碎,并过2000目标准筛,收集过筛后的模塑粉,即得含有酚羟基侧基的聚酰亚胺模塑粉;b、在常温下,将所述含有酚羟基侧基的聚酰亚胺模塑粉80.0g,填装入筒形柔性聚氨酯包套(邵氏硬度a为51ha)中,在冷等静压机中,施加70mpa的压强并在此压强下保持45min,脱模后获得冷压毛坯;c、将所述冷压毛坯首先在真空烘箱内(真空度≤1pa)300℃下真空烘干10小时,然后放入热等静压机,以5℃/min的升温速率,升温到400℃,同时充入高纯氩气(氩气的体积含量为99.999%)使压强升高至40mpa,然后在此条件下保持240min,完成热压烧结,自然冷却至室温后取出,得到多孔聚苯并噁唑材料;之后在数控车床上进行机加工,根据实际需求得到从内径10mm到90mm不等的圆环状轴承保持架,然后经过浸油处理,将保持架浸泡在pao10润滑油中,在120℃真空烘箱中10pa真空度下放置48h,即可得到轴承用聚苯并噁唑多孔含油保持架材料。将轴承用聚苯并噁唑多孔含油保持架材料加工为标准测试样条,分别对其环张力、孔性能及含油性能进行评价,结果见表1。图2为实施例2~5制备的轴承用聚苯并噁唑多孔含油保持架材料的红外光谱图,其中均可以明显看到1624cm-1处苯并噁唑环特征吸收峰。对比例1在常温下,取购自上海合成树脂研究所的牌号为ys-20的聚酰亚胺模塑粉80.0g,填装入筒形柔性聚氨酯包套(邵氏硬度a为51)中,在冷等静压机中,施加90mpa的压强并在此压强下保持30min,脱模后获得冷压毛坯;将所述冷压毛坯首先在真空烘箱内300℃下真空烘干30小时,然后放入热等静压机,以5℃/min的升温速率升温到350℃,同时充入高纯氩气使压强升高至70mpa,然后在此条件下保持300min,完成热压烧结,自然冷却至室温后取出,发现所述冷压毛坯并未在热等静压过程中发生进一步致密化,相反冷压毛坯的发生了明显的膨胀,密度降低;作为对比例1的后续改进试验,在其他工艺参数完全相同的条件下,将热等静压的温度由350℃依次降低为320℃、300℃、280℃及260℃,以及将热等静压过程中350℃下的气压升高至90mpa、120mpa、150mpa,均同样发生了体积膨胀现象,所述冷压毛坯并未实现致密化,这说明现有的ys-20模塑粉不适合所选热等静压成型工艺,同时也证明了在较高温度下(260℃~350℃)ys-20发生了显著的软化和体积膨胀,其耐温性能以及尺寸稳定性均相对较低。从表1中实施例1与对比例1数据对比可以看出,相比于已有的ys-20,本发明设计合成的轴承用聚苯并噁唑多孔含油保持架材料力学强度相当,但孔径较小,使得材料内部孔洞贯通形成的毛细作用更加明显,孔隙率也较高,导致最终含油率较高。本发明设计的由含有酚羟基侧基的聚酰亚胺经高温热重排转变、脱除co2气体分子原位生成聚苯并噁唑,热重排转变中产生的co2气体分子高温高压下体积膨胀形成孔隙,由于co2气体的动力学直径相对较小,因此在同样条件下形成的孔隙也更小,由此带来的优点为毛细作用更加明显,使得孔隙中含蓄的润滑油要在相对较高的转速下才能甩出,因此适用于高速轴承,其在3000rpm转速下,润滑油完全无法甩出,而在7500rpm转速下,甩油曲线见图3,当转速高于8000rpm时,内部含蓄的润滑油被更快的甩出来;而由于ys-20粒径较大,堆砌出来的孔径较大,因此在较低转速3000rpm下即可将润滑油甩出,甩油曲线见图4,这就证明了本发明解决了传统ys-20材料无法适应高速轴承的技术问题。对比例2按照实施例1中步骤a获得含有酚羟基侧基的聚酰亚胺模塑粉,在室温下,将所述模塑粉80.0g装入筒形金属模具中,在液压机上施加90mpa的压强并保持30min;然后将冷压毛坯从模具中脱出;将所述冷压毛坯首先在真空烘箱内300℃下真空烘干30小时,然后放入热等静压机,以5℃/min的升温速率,升温到350℃,同时充入高纯氩气使压强升高至70mpa,然后在此条件下保持300min,完成热压烧结,自然冷却至室温后取出,得到多孔聚苯并噁唑材料。将其加工为标准测试样条,评价其环张力、孔性能及含油性能等,见表1。从表1中实施例1和对比例2可以看出,同样采用本发明设计的含有酚羟基侧基的模塑粉,相比于金属模具双向加压制备冷压毛坯的传统制备方法,采用冷等静压法制备冷压毛坯具有更优的孔性能和含油性能,且力学强度明显更高。对比例3按照实施例1中步骤a获得含有酚羟基侧基的聚酰亚胺模塑粉,在常温下,将所述聚酰亚胺模塑粉80.0g,填装入筒形柔性聚氨酯包套(邵氏硬度a51)中,在冷等静压机中,施加90mpa的压强并在此压强下保持30min,脱模后获得冷压毛坯;将所述冷压毛坯首先在真空烘箱内300℃下真空烘干30小时,然后放入筒形金属模具内,并以传统的限位装置加压70mpa,以5℃/min的升温速率升温到350℃,然后在此条件下保持300min,完成热压烧结,自然冷却至室温后取出,得到多孔聚苯并噁唑材料。将其加工为标准测试样条,评价其环张力、孔性能及含油性能等,见表1。从表1中实施例1和对比例3可以看出,同样采用本发明设计的含有酚羟基侧基的聚酰亚胺模塑粉,相比于在金属模具内限位加压烧结的传统制备方法,采用热等静压法具有更优的孔性能(平均孔径更小)和含油性能,而力学强度相当。对比例4a、常温、常压下,在氮气保护气氛中,在一配有机械搅拌、温度计和冷凝管的5l三口瓶中,加入167.13g(0.50mol)6fap和1500gnmp,搅拌0.5小时,使6fap完全溶解得到6fap溶液,分4批缓慢加入109.06g(0.50mol)pmda粉末,每次加入粉末总质量的25%,粉末加完毕后补加157g溶剂nmp,使得反应体系中nmp的质量为两种单体质量的6倍(即质量浓度为14.29wt%),室温下搅拌反应12小时得到中间体均相溶液;然后向所述中间体均相溶液中加入甲苯580g,甲苯的用量为所述中间体均相溶液质量的30%,升温至160℃利用甲苯和水的共沸进行酰亚胺化反应12小时,反应完毕,将反应体系倾倒入水中,即可析出模塑粉粗品;将所述模塑粉粗品过滤收集并用乙醇洗涤3次以尽量除去残留溶剂,每次洗涤乙醇的用量为溶剂nmp和甲苯的质量之和2237g,在真空烘箱中150℃下烘干24小时,然后在粉碎机中粉碎,由于模塑粉颗粒较大,只能过200目标准筛,孔隙小于200目筛的无法筛分通过,收集过筛后的模塑粉,即得聚酰亚胺模塑粉(式iv);冷等静压成冷压毛坯及热等静压可控成型与实施例1完全相同,将热等静压成型后的多孔聚酰亚胺加工为标准测试样条,分别对其环张力、孔性能及含油性能进行评价,结果见表1。从表1中实施例1与对比例4的结果可见,对比例4的化学结构与实施例1类似,但由于不含有酚羟基侧基,因此热等静压过程中不存在脱除co2气体分子的热重排转变,因此其由于包夹的空气受热膨胀所形成孔径相对较大,孔隙率及含油率也均较高,但环张力由于孔隙率过高而显著降低。表1实施例1~5以及对比例1~4制得的材料的环张力、孔性能、含油性能对比编号环张力(mpa)平均孔径(μm)孔隙率(%)含油率(wt%)实施例118.430.4620.616.94对比例118.631.2016.012.96对比例213.551.2325.113.68对比例317.650.7919.912.80对比例44.881.6331.816.63实施例219.930.4419.716.33实施例320.810.4420.716.90实施例421.210.4517.715.60实施例519.660.4419.516.26综合对比实施例1和对比例1~4,从图5和图6所示实施例1制备的轴承用聚苯并噁唑多孔含油保持架材料及对比例1ys-20树脂的dma曲线来看(dma曲线的测试过程中的升温速率为5℃/min,频率为1hz),本发明得到的轴承用聚苯并噁唑多孔含油保持架材料具有更高的分子链刚性,耐温等级明显更高,400℃以前材料的储能模量无明显剧烈衰减,因此可以适用于更高的长期使用温度,同样更适合于克服和抵抗轴承高速运转产生的无法忽略的发热效应。从图7和图8所示的孔径分布曲线,可见本发明采用等静压成型可以大大收窄孔径分布的宽度,孔径分布的半峰宽是对比例半峰宽的1/2~1/5,这说明本发明得到的孔径分布更加均一,有利于润滑油的长期含蓄贮存;从实施例1与对比例2、3的孔性能及环张力数据可见,等静压成型对于提高孔径分布的均一性效果显著优于传统的机械冷压方式及限位烧结方式。从图9所示含油以后的摩擦曲线可见,含油后材料的摩擦系数稳定性极高,整个测试过程中几乎没有明显的摩擦系数的波动,而且均稳定在0.10以下,表现出优异的油润滑特性。以上所述仅是本发明的优选实施方式,并非对本发明作任何形式上的限制。应当指出,对于本
技术领域:
的普通技术人员来说,在不脱离本发明原理的前提下,还可以做出若干改进和润饰,这些改进和润饰也应视为本发明的保护范围。当前第1页12