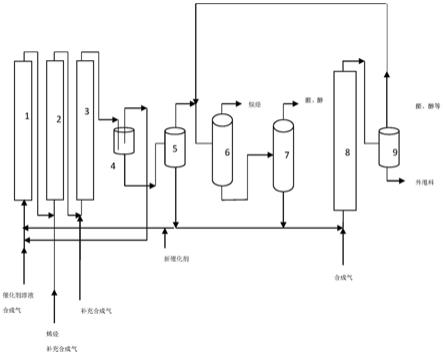
1.本发明涉及含氧化合物的制备,具体涉及一种通过烯烃氢甲酰化反应制备醛、醇的方法和装置。
背景技术:2.烯烃与一氧化碳及氢气在催化剂作用下发生氢甲酰化反应,加氢甲酰化方法包括在反应条件下使烯属不饱和化合物与一氧化碳和氢气在催化剂的存在下接触以产生一种或多种醛、醇。工业生产中氢甲酰化反应所用的催化剂一般为钴(co)基或铑(rh)基催化剂。
3.cn102123978a公开了一种加氢甲酰化α-烯烃以产生包含正构醛和一种或多种异构醛的两种或更多种醛的方法,所述正构醛与一种或多种异构醛的目标摩尔比在3/1-60/1的可选择范围内。该方法使用包含对称的杯芳烃二亚磷酸酯配体的过渡金属-配体配合物催化剂。
4.cn108586219a公开了一种烯烃氢甲酰化反应制备醛的方法,制备方法如下:步骤一:在第一反应釜内进行c2~c4烯烃与一氧化碳和氢气在催化剂作用下经氢甲酰化反应连续化地制备醛,同时其温度90℃和压力为2.5mpa;步骤二:在第二反应釜内进行加热,加热温度为70-80℃,同时在第二反应釜内通入惰性气体;步骤三:将第一反应釜与第二反应釜连通,将第一反应釜制备醛引入第二反应釜内;步骤四:在步骤三中引入时,通过等压且不等温度的情况下进行,且引入后进行二次引入;该技术反应过程复杂,而且采用铑-膦络合催化剂,价格昂贵。
5.与钴催化剂相比铑络合物反应活性更高,可以在更温和的温度和压力下反应。但铑催化剂高温性能差,用于高级烯烃羰基化有一定困难,现有铑催化剂对端烯烃催化效果较好,但是对内烯烃活性较差,催化剂为油溶性和产物分离也较困难,使得后处理较为复杂,铑作为贵金属资源稀少,价格昂贵,其回收再利用成本较高。
6.cn1257140c公开了一种加氢甲酰化具有6-20个碳原子的烯烃的连续方法,其中:a)将钴(ii)盐水溶液与氢和一氧化碳充分接触以形成加氢甲酰化活性钴催化剂,然后将包含该钴催化剂的水相与烯烃和任选的有机溶剂以及氢和一氧化碳在至少一个反应区中充分接触,在此,钴催化剂被萃取到有机相中并将烯烃加氢甲酰化,b)将来自反应区的排出物在酸性钴(ii)盐水溶液的存在下用氧进行处理,其中钴催化剂分解形成钴(ii)盐且这些物质被反萃取到水相中;并随后分离各相,c)钴(ii)盐水溶液以未变化的形式再循环至步骤a)。该方法工艺过程复杂。
7.de59704070d1公开了制备具有7-18个碳原子的醇的方法,包括在含钴催化剂有机相的存在下,在50-220℃的温度和100-400巴的压力下,用合成气体加氢甲酰化相应的烯烃,接着氢化由此获得的醛,其中在不与水或仅少量与水可混合的有机溶剂的存在下,使钴盐水溶液与合成气体反应形成钴催化剂,用不与水或仅少量与水可混合的有机萃取剂从水相中萃取所形成的钴催化剂来制备含钴催化剂的有机相。形成钴催化剂、在有机相中萃取所形成的钴催化剂并且加氢甲酰化相应的烯烃是在一步法中进行的。该方法反应时间一般
10小时以上,钴氢甲酰化催化剂反应压力高,如25mpa左右,装置固定投资大。
8.在氢甲酰化反应过程中,随着催化剂的物料不断循环使用,循环物料中重质物含量会缓慢增加,影响装置的正常运行,因此物料循环使用一定时间后,需要将部分含催化剂的重质物料外甩出反应器,这部分外甩的物料按废液处理,对环境保护造成很大压力。外甩物料量的多少也决定着氢甲酰化工艺的工业实施前景。
技术实现要素:9.本发明提供一种通过烯烃氢甲酰化反应连续制备醛和/或醇的方法,该方法工艺流程简单,烯烃转化率高,目标产物收率高,而且可以大幅度减少废液排放,有良好的工业应用前景。
10.本发明还提供一种连续制备醛、醇的装置。
11.第一方面,本发明提供的连续制备醛、醇的方法,包括以下步骤:
12.(a)将钴-膦络合物催化剂溶液与烯烃通入氢甲酰化反应器,在合成气环境下进行氢甲酰化反应;
13.(b)对反应粗产物进行分离,轻组分中得到醇、醛和烷烃混合产物,重组分中得到含钴-膦络合物催化剂的物料;
14.(c)含钴-膦催化剂的物料大部分返回反应器入口循环使用;少部分进入后处理反应器,在合成气的气氛下进行后处理;
15.(d)对后处理反应器的流出物料进行蒸馏分离,塔顶得到醇等产物,塔底残余物料排出反应器。
16.本技术发明人在研究中发现,随着含催化剂的物料不断循环使用,循环物料中重质物含量会缓慢增加,分析表明,重质物料中大分子含羰基副产物的含量明显增加。本技术发明人提出,将这部分物料送至后处理反应器,通入合成气但不通入烯烃,在氢甲酰化反应的条件下进行后处理,令人预料不到的是,其中的大分子重质副产物又会重新分解为醇等产物,这不仅使目标产物收率进一步增加,而且可以明显减少外甩物料量,进而显著减少废液排放,减轻氢甲酰化工艺的环保问题。
17.根据本发明方法,在氢甲酰化反应之前,还可以在预处理反应器中对催化剂溶液进行预处理,预处理反应器可以为高压釜或管式反应器。预处理在合成气气氛下进行,预处理反应器温度为50℃~150℃,优选75℃~130℃,更优选90℃~120℃,压力1mpa~12mpa,优选3mpa~10mpa,更优选5mpa~8mpa,预处理时间0.1-10小时,优选1-3小时。催化剂预处理有利于钴-膦催化剂活性单元形成,减少催化剂分解,提高催化剂的活性和稳定性,延长催化剂使用寿命。
18.如果进行预处理,含钴膦络合物催化剂的物料可循环至预处理反应器入口循环再用。
19.根据本发明方法,含钴-膦络合物催化剂的物料返回氢甲酰反应器和/或预处理反应器入口时,可根据需要补加少量新催化剂。
20.根据本发明方法,步骤(a)中,所述钴-膦络合物催化剂溶液中,钴的质量浓度为0.05%-3%,优选0.2%~2%,更优选0.5%~1.5%,最优选0.6%~1%。
21.所述钴-膦络合物催化剂溶液中,含钴原料与膦配体的钴、磷质量比可以为1:
(0.1-3),优选1:(0.2-2),更优选1:(0.3-1)。
22.所述的含钴原料可以为钴盐,也可以是钴氧化物,其中钴盐可以是无机酸钴,也可以是有机酸钴,例如选自碳酸钴、硝酸钴、醋酸钴、乙酰丙酸钴、甲酸钴、八羰基二钴和环烷酸钴中的一种或几种。
23.所述膦配体可以为本领域公知的各种配体,例如亚磷酸酯、三苯基膦、三烷基膦、二-(三苯基膦)、烷基苯基膦等中的一种或几种,优选三苯基膦或三丁基膦。
24.所述钴-膦络合物催化剂溶液可以按照公知的方法制备,例如:将含钴原料与膦配体溶解于溶剂中,充入co、h2气体至压力为1-6mpa,优选2-4mpa,在80-180℃,优选100-150℃下进行反应0.5-24h,优选1-15小时,更优选3-10小时,得到钴-膦催化剂溶液。
25.所述钴-膦络合物催化剂溶液中的溶剂可以为本领域公知的各种溶剂,例如烯烃、烷烃、醇等等,优选包含c1~c20各种类型的醇,此外,溶剂中可以包含产物或原料。
26.所述溶剂优选强溶解性混合溶剂。所述强溶解性混合溶剂中可以含有以下组分:(1)c8-c16的高碳醇,(2)总碳数为c16-c30的羟基醛,和/或总碳数为c16-c30的醇醛缩合物,组分(1)与组分(2)的质量比为1:0.05-4,优选1:0.1-3,更优选1:0.2-2。采用强溶解性混合溶剂可以提高催化剂浓度,降低反应温度,以及提高醇和醛的总收率。
27.所述醇醛缩合物是由c8-c16的醛与c8-c16的高碳醇反应得到,所得到的醇醛缩合物的总碳数为c16-c32,优选c18-c27。
28.所述醇醛缩合物可以按常规方法制备,例如:以c8-c16的醛与c8-c16的高碳醇为原料,二者摩尔比为1:(0.7-2),加入酸性催化剂如硫酸、甲基苯磺酸,在常压、10-50℃下,反应0.4-3小时进行反应,反应粗产物经蒸馏分离得到。
29.所述羟基醛是由二分子或三分子c8-c16的醛反应得到,所得到的羟基醛总碳数为c16-c32,优选c18-c27。
30.所述羟基醛可以按常规方法制备,例如:以c8-c16的醛为原料,以稀碱(如5%-10%氢氧化钠溶液)为催化剂,在常压、低温下(如0-10℃)反应0.1-3小时,反应粗产物经蒸馏分离即可得到羟基醛。
31.根据本发明方法,步骤(a)所述的烯烃为c1~c30烯烃,优选c6~c20烯烃,烯烃可为直链烯烃和/或支链烯烃,支链烯烃支链数可≥1。本发明尤其适用于含有2,4,4-三甲基-1-戊烯、2,4,4-三甲基-2-戊烯等中一种或一种以上的碳八烯烃混合物。三甲基多支链烯烃由于空间位阻大,氢甲酰化难度高于少支链烯烃。
32.所述的合成气是指一氧化碳和氢气的混合气,其中,一氧化碳和氢气摩尔比4:1~1:4,优选3:1~1:3,更优选2:1~1:2。
33.根据本发明方法,所述氢甲酰化反应器为管式反应器,烯烃、合成气和含有催化剂的溶液从管式反应器下部流入,反应产物从管式反应器上部流出。也可从管式反应器上部流入,反应产物从管式反应器下部流出。反应完毕后,从反应粗产物中蒸出部分醇、醛、烷烃及烯烃原料,剩余含催化剂的溶液循环至预反应器进行预处理,预处理后催化剂溶液送至氢甲酰化反应器入口,重新进入反应器被使用。
34.所述氢甲酰化反应器温度为60℃~250℃,优选100℃~220℃,更优选100℃~180℃;最优选110℃~140℃,反应器可有两个或两个以上,反应器之间串联使用,优选二个反应器串联,反应器温度可相同,也可不同,反应温度可采用前高后低或前低后高,如果一反
温度大于二反温度,有助于减少催化剂在较高反应温度区停留时间,减少催化剂分解。反应压力可以为1mpa~12mpa,优选2mpa~10mpa,更优选5mpa~8mpa。反应时间1-40小时,优选3-20小时,更优选5-10小时。
35.合成气可从预处理反应器和/或氢甲酰化反应器下部流入,也可从多个氢甲酰化反应器下部流入,另外,流入不同反应器的合成气中co与h2比例可相同或不同,这样可以方便调节每个反应器中烯烃与co、h2之间比例至最佳,有利于更高转化率和更优选择性。合成气与烯烃摩尔比(1~12):1,优选(3~6):1。
36.催化剂溶液与烯烃质量比(0.1-10):1,优选(2-5):1。
37.根据本发明方法,步骤(b)中,所述的粗产物分离可以先进行气液分离,再进行蒸馏分离。
38.所述气液分离可以在气液分离罐中降温不降压的条件下进行,气液分离温度0℃-100℃,优选20℃-80℃,更优选20℃-40℃。
39.其中,汽液分离后得到的气相物流基本为合成气,经冷凝和/或吸收后,剩余合成气可以循环至预反应器和/或反应器入口,重复使用。
40.气液分离后的液相物流可以通过蒸馏装置进行蒸馏分离,顶部出料为含醇、烷烃和醛的混合产物,底部得到含钴-膦络合物催化剂的重质物料。
41.所述蒸馏分离装置可以为真空蒸馏釜、精馏塔或薄膜蒸发器等本领域人员容易想到的蒸馏分离装置。其中真空蒸馏釜或精馏塔压力≤10-2
mpa,优选≤10-3
mpa,更优选≤10-4
mpa,回流比1-10:1,塔釜温度为70-200℃;薄膜蒸发器压力≤10mmhg,优选≤6mmhg,更优选≤1mmhg条件下,加热面温度35-150℃,优选40-100℃,更优选45-70℃,停留时间1~30分钟,优选1~10分钟,更优选1~2分钟。
42.优选地,从蒸馏装置塔顶得到的混合物还可以进入产品蒸馏塔进一步分离。所述产品蒸馏塔可以是常压蒸馏塔或精馏塔,得到烷烃,高纯度醇和醛。压力可以为常压,回流比1-10:1,塔釜温度为100℃-300℃,优选150℃-200℃。
43.优选地,所述产品蒸馏可以通过第一产品蒸馏塔和第二产品蒸馏塔分两次进行,先蒸出烷烃等轻组分,再蒸出醇、醛等产物。第二产品蒸馏塔下部排出的重质物料进入后处理反应器。
44.优选地,如果目标产物是得到更多的醇,还可以对得到的醇和醛的混合物进行加氢处理,使醛转变为醇。
45.根据本发明方法,步骤(c)中,所述后处理反应器为管式反应器,含有催化剂的重质物料可以从管式反应器下部流入,从上部流出,也可从管式反应器上部流入,从下部流出;同时向反应器中通入合成气但不通入烯烃,使重质物进一步分解为醇和醛等产物。
46.所述后处理反应器为管式反应器,反应温度为60℃~250℃,优选100℃~200℃,更优选120℃~190℃;反应压力1mpa~12mpa,优选3mpa~10mpa,更优选5mpa~8mpa;停留时间为0.5-20小时,优选1-7小时。
47.所述含重质物料进入后处理反应器的物料量可根据催化剂的活性和产物收率等情况决定。而且后处理反应器可以与氢甲酰化反应同步运行,也可以在氢甲酰化反应进行一段时间后再开启,也可以间歇开启。
48.根据本发明方法,步骤(d)中,经过后处理的物料进入外甩料蒸馏塔,可以是常压
蒸馏塔或精馏塔,塔顶蒸出醇等产物,排出或返回产品蒸馏塔。塔底得到残余重质物料,外甩排出。蒸馏塔压力可以为常压,回流比1-10:1,塔釜温度为100℃-300℃,优选150℃-200℃。
49.第二方面,本发明还提供一种通过烯烃氢甲酰化反应连续制备醛、醇的装置,其中包括:预处理反应器,管式反应器,气液分离器,蒸馏分离装置,后处理反应器,外甩料蒸馏塔,以及催化剂溶液、合成气和烯烃的进料管线,用于将反应产物从管式反应器输送到气液分离器的管线,用于将液相物流从气液分离器下部输送到蒸馏分离装置的管线,用于将分离出的合成气从气液分离器上部返回预处理反应器和/或管式反应器的管线,用于将混合产物在蒸馏装置上部排出的管线,用于将含催化剂的物料从蒸馏分离装置下部输送到后处理反应器的管线,用于将含催化剂的物料从蒸馏分离装置下部返回预处理反应器和/或管式反应器的管线,后处理反应器与外甩料蒸馏塔的连接管线,外甩料蒸馏塔上部和下部的出料管线。
50.根据本发明的一种优选实施方式,催化剂溶液从预处理反应器底部流入,并从预处理反应器上部流出,经预处理后催化剂溶液与烯烃从管式反应器底部流入,上部流出,反应粗产物进入气液分离器,其中,气体通过冷浴收集凝液后剩余合成气循环至预处理反应器或氢甲酰化反应器再用,液体进入蒸馏分离装置,从上部蒸出得到混合产物,大部分剩余催化剂溶液从底部循环至预反应器循环使用,少量含重质物料从后处理反应器下部进入,上部流出,经过后处理的物料进入外甩料蒸馏塔,从蒸馏塔上部得到醇等产物,下部排出含重质物的外甩料。
51.优选地,还包括产品蒸馏塔,优选包括第一产品蒸馏塔和第二产品蒸馏塔,混合产物从蒸馏分离装置上部进入第一产品蒸馏塔的管线,第一产品蒸馏塔与第二产品蒸馏塔之间的连接管线,第二产品蒸馏塔下部与后处理反应器下部的连接管线,以及第一产品蒸馏塔和第二产品蒸馏塔上部的出料管线。
52.所述产品蒸馏塔可以是蒸馏釜或精馏塔。
53.优选地,还包括向预反应器和/或各反应器补充合成气或催化剂的管线,以及向后处理反应器补充合成气的进气管线。
54.优选地,所述管式反应器由二或多根管式反应器串联组成。
55.其中,所述蒸馏分离装置可以是蒸馏釜、精馏塔或薄膜蒸发器。
56.其中,所述外甩料蒸馏塔可以是蒸馏釜或精馏塔。优选蒸出的醇等产物返回第一产品蒸馏塔。
57.优选地,还可以包括加氢装置,从产品蒸馏塔和外甩料蒸馏塔得到的醇和醛进一步加氢,可以得到高收率的醇。
58.本发明具有以下优点:
59.1、对含重质物的外甩物料进行后处理,重质副产物又会重新分解为醇等产物,显著降低外甩物料量,减少废液排放,有利于环保,具有工业化前景。
60.2、催化剂预处理工艺可以显著降低钴-膦催化剂分解,有利于钴-膦催化剂活性单元形成,提高催化剂的活性和稳定性,延长催化剂使用寿命。
61.3、采用强溶解性溶剂可以提高催化剂浓度,降低反应温度,以及提高醇和醛的总收率,减少烷烃生成。
62.4、产物分离工艺简单,醇、醛选择性高。
63.5、适用的烯烃原料广泛,尤其适用于空间位阻大的多支链烯烃氢甲酰化反应,反应压力低,装置投资和加工成本显著降低。
附图说明
64.图1为本发明优选的一种实施方式。其中:
65.1预处理反应器;2管式反应器;3管式反应器;4气液分离器;5蒸馏分离装置;6第一产品蒸馏塔;7第二产品蒸馏塔;8后处理反应器;9外甩料蒸馏塔。
具体实施方式
66.下面通过实例进一步说明本发明,但本发明并不限于此。
67.实施例中的烯烃原料为市售碳八烯烃,组成为:2,4,4-三甲基-1-戊烯75.1%,2,4,4-三甲基-2-戊烯21.2%,其余为多支链烯烃。
68.催化剂制备例1
69.将环烷酸钴与三苯基膦溶解于异壬醇中,溶液中钴含量0.075wt%,磷含量0.06wt%,用合成气h2/co(2:1)将空气置换干净,充入co、h2气体至压力为2mpa,在400转/分搅拌下,140℃反应12h,得到钴-膦催化剂溶液a1。催化剂见组成表1。
70.催化剂制备例2
71.将环烷酸钴与三苯基膦加入强溶解性溶液(含羟醛38.1wt%的异壬醇溶液)中,其中钴含量0.7wt%,磷含量0.4wt%,用合成气h2/co(2:1)将空气置换干净,充入co、h2气体至压力为2mpa,在400转/分搅拌下,140℃反应12h,得到钴-膦催化剂溶液a2。催化剂见组成表1。
72.催化剂制备例3
73.将环烷酸钴与三苯基膦加入强溶解性溶液(含羟醛23.1wt%、醇醛缩合物39.8wt%的异壬醇溶液)中,其中钴含量0.6%,磷含量0.3%,用合成气h2/co(2:1)将空气置换干净,充入co、h2气体至压力为2mpa,在400转/分搅拌下,140℃反应12h,得到钴-膦催化剂溶液a3。催化剂见组成表1。
74.催化剂制备例4
75.将环烷酸钴与三苯基膦溶解于异壬醇中,溶液中钴含量0.07wt%,磷含量0.04wt%,用合成气h2/co(2:1)将空气置换干净,充入co、h2气体至压力为2mpa,在400转/分搅拌下,140℃反应12h,得到钴-膦催化剂溶液a4。催化剂见组成表1。
76.实施例1
77.碳八烯烃与催化剂溶液a1分别用高压计量泵自储罐分别送入反应器和预处理反应器,催化剂溶液与合成气(co/h2摩尔比为1:2),从底部流入管式预处理反应器,并从上部流出,催化剂溶液中钴浓度0.075%,预处理反应器温度100℃,压力8mpa,停留时间1小时,经预处理后催化剂溶液与碳八烯烃按照73g:30g从氢甲酰化反应器底部流入,上部流出,氢甲酰化反应器由二根管式反应器串联组成,由插入反应器中心带套管的热电偶测量反应温度,合成气与烯烃摩尔比3:1,氢甲酰化反应器反1温度180℃,反2温度175℃,压力8mpa,停留时间8小时,反应后原料转化率99%,对产物进行色谱分析,产物组成见表2。
78.反应粗产物进入气液分离器,其中,气体通过冷浴收集凝液后剩余合成气循环至预处理反应器再用,液体进入薄膜蒸发器,薄膜蒸发器压力6mmhg,加热面温度85℃,停留时间0.7分钟条件下,薄膜蒸发器蒸出产物后,剩余催化剂溶液循环至预处理反应器循环使用。薄膜蒸发器蒸出产物进入产品精馏塔,在常压,回流比2:1,塔釜温度为﹤194℃精馏,蒸出烷烃等轻组分,在常压,回流比1:1,塔釜温度为194℃精馏,蒸出产物异壬醇,纯度98%。
79.经多次循环后,少量含重质物料从下部进入后处理反应器,上部流出,在反应温度120℃、6mpa,合成气气氛下使重质物进一步分解为异壬醇等产物,反应1小时后,取样进行色谱分析,主要含羰基重质物减少61%,经过后处理的物料进入精馏塔,在常压,回流比1:1,塔釜温度为194℃,蒸出异壬醇,残余料外甩。
80.实施例2
81.碳八烯烃与催化剂溶液a2分别用高压计量泵自储罐分别送入反应器和预处理反应器,催化剂溶液与合成气(co/h2摩尔比为1:2),从底部流入管式预处理反应器,并从上部流出,催化剂溶液中钴浓度0.7%,预处理反应器温度100℃,压力8mpa,停留时间1小时,经预处理后催化剂溶液与碳八烯烃按照73g:44g从氢甲酰化反应器底部流入,上部流出,氢甲酰化反应器由二根管式反应器串联组成,由插入反应器中心带套管的热电偶测量反应温度,合成气与烯烃摩尔比3:1,合成气从预处理反应器下部进入反应器,氢甲酰化反应器反1温度120℃,反2温度120℃,压力8mpa,停留时间8小时,c8烯烃转化率97.3%,对产物进行色谱分析,产物组成见表2。
82.反应粗产物进入气液分离器,其中,气体通过冷浴收集凝液后剩余合成气循环至预处理反应器再用,液体进入薄膜蒸发器,薄膜蒸发器压力4mmhg,加热面温度70℃,停留时间1分钟条件下,薄膜蒸发器蒸出产物后,剩余催化剂溶液循环至预处理反应器循环使用。薄膜蒸发器蒸出产物进入产品精馏塔,在常压,回流比1:1,塔釜温度为﹤194℃精馏,蒸出烷烃等轻组分,在常压,回流比1:2,塔釜温度为194℃精馏,蒸出产物异壬醇,纯度98%。
83.经多次循环后,少量含重质物料从后处理反应器下部进入,上部流出,在反应温度160℃、7mpa,合成气气氛下使重质物分解为异壬醇等产物,反应7小时后,取样进行色谱分析,,主要含羰基重质物减少91%,经后处理的物料进入精馏塔,在常压,回流比1:1,塔釜温度为194℃,蒸出异壬醇等产物后,残余料外甩。
84.实施例3
85.碳八烯烃与催化剂溶液a3分别用高压计量泵自储罐分别送入反应器和预处理反应器,催化剂溶液与合成气(co/h2摩尔比为1:1.5),从底部流入管式预处理反应器,并从上部流出,催化剂溶液中钴浓度0.6%,预处理反应器温度120℃,压力8mpa,停留时间1小时,经预处理后催化剂溶液与碳八烯烃按照73g:44g从氢甲酰化反应器底部流入,上部流出,氢甲酰化反应器由二根管式反应器串联组成,由插入反应器中心带套管的热电偶测量反应温度,合成气与烯烃摩尔比6:1,合成气从预处理反应器下部进入反应器,氢甲酰化反应器反1温度140℃,反2温度140℃,压力8mpa,停留时间4小时,c8烯烃转化率96.3%,对产物进行色谱分析,产物组成见表2。
86.反应粗产物进入气液分离器,其中,气体通过冷浴收集凝液后剩余合成气循环至预处理反应器再用,液体进入薄膜蒸发器,薄膜蒸发器压力0.6mmhg,加热面温度50℃,停留时间1分钟条件下,薄膜蒸发器蒸出产物后,剩余催化剂溶液循环至预处理反应器循环使
用。薄膜蒸发器蒸出产物进入产品精馏塔,在常压,回流比2:1,塔釜温度为﹤194℃精馏,蒸出烷烃等轻组分,在常压,回流比1:1,塔釜温度为194℃精馏,蒸出产物异壬醇,纯度98%。
87.经多次循环后,少量含重质物料从后处理反应器下部进入,上部流出,在反应温度160℃、7mpa,合成气气氛下使重质物分解为异壬醇等产物,反应2小时后,色谱分析表明,主要含羰基重质物减少79%,经后处理的物料进入精馏塔,在常压,回流比1:1,塔釜温度为194℃,蒸出异壬醇等产物后,残余料外甩。
88.实施例4
89.碳八烯烃与催化剂溶液a4分别用高压计量泵自储罐分别送入反应器和预处理反应器,催化剂溶液与合成气(co/h2摩尔比为1:1.5),从底部流入管式预反应器,并从上部流出,催化剂溶液中钴浓度0.07%,预处理反应器温度100℃,压力8mpa,停留时间1小时,经预处理后催化剂溶液与碳八烯烃按照73g:40g从氢甲酰化反应器底部流入,上部流出,氢甲酰化反应器由二根管式反应器串联组成,由插入反应器中心带套管的热电偶测量反应温度,合成气与烯烃摩尔比4.5:1,氢甲酰化反应器反1温度180℃,反2温度177℃,压力8mpa,停留时间8小时,反应后原料转化率97.9%,对产物进行色谱分析,产物组成见表2。
90.反应粗产物进入气液分离器,其中,气体通过冷浴收集凝液后剩余合成气循环至预反应器再用,液体进入薄膜蒸发器,薄膜蒸发器压力0.9mmhg,加热面温度60℃,停留时间1分钟条件下,薄膜蒸发器蒸出产物后,剩余催化剂溶液循环至预反应器循环使用。薄膜蒸发器蒸出产物进入产品精馏塔,,在常压,回流比3:1,塔釜温度为﹤193℃精馏,蒸出烷烃等轻组分,在常压,回流比2:1,塔釜温度为193℃精馏,蒸出产物异壬醇,纯度98%。
91.经多次循环后,少量含重质物料从后处理反应器下部进入,上部流出,在反应温度180℃、8mpa,合成气气氛下使重质物进一步分解为异壬醇等产物,反应2小时后,取样进行色谱分析,主要含羰基重质物减少81%,经过后处理的物料进入精馏塔在常压,回流比1:1,塔釜温度为193℃,蒸出异壬醇等产物,残余料外甩。
92.表1
[0093][0094][0095]
表2
[0096]