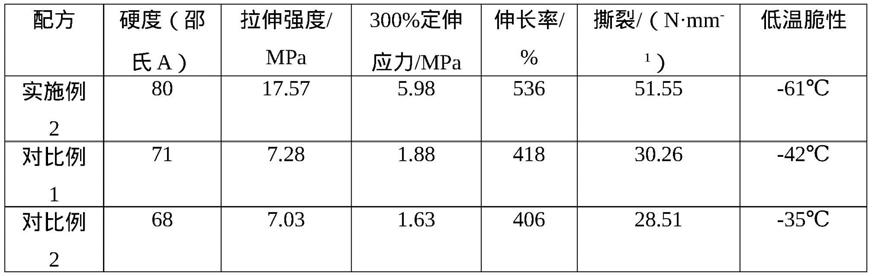
1.本发明涉及电缆生产制造材料技术领域,具体来说是一种用于电缆的橡胶复合材料的制备方法和应用。
背景技术:2.随着经济飞速发展,电子信息技术作为其中重要方面也得到了长足的进步,使得电线电缆的需求也日益增多;目前电线电缆的外层多是高分子材料,但高分子材料大多是易燃或者可燃材料,一旦发生火灾火焰传播非常快,放出大量的热,并且难以熄灭;一些材料在加热或点火时会释放出大量的烟尘颗粒和有毒物质,这些物质不单对环境产生了非常不利的破坏,更加严重的是不利于人们逃生,危及人民生命财产安全。因此对高效阻燃低烟电线电缆料的开发成为一个热点问题。电缆料除了要求具有一定的力学性能、耐磨性、耐屈挠性能、耐热老化性能外,必须提高其电缆料的阻燃性才能安全使用。
3.上世纪七十年代起对阻燃电缆料有所研究,但是初期的研究主要集中在含卤阻燃剂阻燃高聚物,普遍应用的是溴系阻燃材料,主要采用的溴系阻燃剂为四溴双酚a、十溴二苯醚等,而这种含卤素的材料在受热或者被点燃过程中会产生大量的烟尘和毒性气体,对人体和环境造成严重的损害,不利于火灾事故的抢救。为了克服现有技术含卤阻燃材料存在的严重问题,人们在开发无卤、低烟、无毒的阻燃剂和阻燃电缆料上面做了很多的工作,如英国的bp公司、美国的联碳公司、日本的大日本油墨公司等,都有相应的实现了工业化生产和应用的产品,他们通常是在电缆料中添加氢氧化铝和氢氧化镁等无机阻燃剂。
4.金属氢氧化物阻燃剂是目前应用较为广泛的阻燃剂,在阻燃剂领域占有相当重要的位置,金属氢氧化物阻燃剂的代表主要有氢氧化铝、氢氧化镁、水滑石、合成水菱镁矿等,金属氢氧化物的优点有:易制得、无毒无害、燃烧不会产生有毒有害气体、具有一定的成炭抑烟效果、可起到填充的作用,然而它的最大的缺点是需要很大的添加量才能表现出不错的阻燃效果,并且它与基体之间的相容性较差,而无卤阻燃剂大量添加会损害基体橡胶的物理性能,继而对复合材料的力学性能和加工流动性造成不利的影响。
5.氯磺化聚乙烯的分子链结构中不存在不饱和烃,属于饱和型橡胶,因此相较于其他不饱和烃型橡胶,氯磺化聚乙烯具有优异的耐臭氧、耐天后候老化性能,突出的耐热老化性能,在120
‑
140℃高温下能够连续使用数年,同时具有较好的耐水、耐油、耐化学品腐蚀等性能,且氯磺化聚乙烯的耐燃性能也好,是仅次于氯丁橡胶的耐燃橡胶。在加工过程中,氯磺化聚乙烯还能够与天然橡胶、丁苯橡胶、丁基橡胶、丁腈橡胶或氯丁橡胶等以任意配比并用,而氯磺化聚乙烯的主要缺点在于耐低温性能较差,其玻璃化转变温度约在
‑
43~19℃,硫化胶的脆性温度也仅为
‑
60~
‑
40℃,所以在橡胶加工成电缆料的过程中提升氯磺化聚乙烯的耐寒性能也是非常有必要的。
技术实现要素:6.针对上述存在的技术不足,本发明的目的是提供了一种用于电缆的橡胶复合材料
的制备方法和应用,本发明采用改性硅灰石材料和膨胀型阻燃剂代替目前常用的金属氢氧化物阻燃剂,采用聚乙二醇和丁腈橡胶对硅灰石进行改性,聚乙二醇不仅提升硅灰石的相容性,且与氧化丁腈橡胶进行酯化反应,改性硅灰石材料再与氯磺化聚乙烯、氯磺化聚乙烯再生胶形成复合材料,在保证电缆料具有良好的工艺性能、力学性能、耐磨性和耐屈挠性能的基础上,提高电缆材料的阻燃性及耐低温性能,达到或优于企业的标准;同时克服了金属氢氧化物阻燃剂相容性差及大量添加损害基体橡胶的缺陷。
7.为解决上述技术问题,本发明采用如下技术方案:
8.一种用于电缆的橡胶复合材料,由如下重量份数的原料制成:氯磺化聚乙烯100份;氯磺化聚乙烯再生胶20
‑
30份;改性硅灰石材料60
‑
95份;膨胀型阻燃剂5
‑
15份;增塑剂10
‑
25份;填充补强剂20
‑
40份;硫化料1
‑
10份;
9.其中,所述改性硅灰石材料由如下重量份数的原料制成:硅灰石10份;聚乙二醇30
‑
40份;丁腈橡胶20
‑
45份。
10.优选的,所述膨胀型阻燃剂由聚磷酸铵和季戊四醇共混制得,且聚磷酸铵与季戊四醇的质量比为2.5
‑
3.5:1。
11.优选的,所述氯磺化聚乙烯为氯磺化聚乙烯csm
‑
40。
12.优选的,所述增塑剂为磷酸二苯异辛酯、磷酸二苯异丙苯酯、磷酸三甲苯酯中的一种或几种的混合。
13.优选的,所述填充补强剂为白炭黑或炭黑。
14.优选的,所述硫化料包括硫化剂和硫化促进剂,硫化剂为mgo,硫化促进剂为硫脲,硫化剂与硫化促进剂质量比为3
‑
5:1。
15.本发明还保护了改性硅灰石材料的制备方法,包括如下步骤:
16.(1)称量:按照如下重量份数称取原料:硅灰石10份;聚乙二醇30
‑
40份;丁腈橡胶20
‑
45份,备用;
17.(2)改性硅灰石的制备:
18.将硅灰石与聚乙二醇共混于无水乙醇中,浸泡40
‑
50min,烘干至恒重后,依次用无水乙醇和纯净水冲洗,再烘干至恒重,得到聚乙二醇包覆硅灰石材料;
19.将丁腈橡胶浸泡于氧化液中6
‑
7d,得到氧化丁腈橡胶;
20.其中,氧化液包括5wt%kbr、5wt%ki和体积分数为50%的h2so4;
21.将氧化丁腈橡胶剪碎并溶解于二氯甲烷中,于常温下加入催化剂并搅拌15~30min,然后加入聚乙二醇包覆硅灰石材料并搅拌4~6h,干燥得到改性硅灰石材料;
22.其中,催化剂包括n'n
‑
二环己基碳二亚胺和4
‑
二甲氨基吡啶,n'n
‑
二环己基碳二亚胺的体积与4
‑
二甲氨基吡啶的质量之比为2ml:1g,催化剂占总量的5%。
23.本发明还保护了一种用于电缆的橡胶复合材料的制备方法,其特征在于,包括如下步骤:
24.(1)称量:按如下重量份数称取原料:氯磺化聚乙烯100份;氯磺化聚乙烯再生胶20
‑
30份;改性硅灰石60
‑
95份;膨胀型阻燃剂5
‑
15份;增塑剂10
‑
25份;填充补强剂20
‑
40份;硫化料1
‑
10份,备用;
25.(2)橡胶复合材料的制备:于开炼机内设置初始辊距,将氯磺化聚乙烯、氯磺化聚乙烯再生胶、改性硅灰石材料置于两辊筒之间塑炼5
‑
7次,调大辊距,按顺序依次加入填充
补强剂、膨胀型阻燃剂、增塑剂、硫化料后,再将辊距调节至初始辊距,混炼8
‑
10次,下片,得到橡胶复合材料。
26.优选的,所述开炼机的初始辊距为0.5
‑
1mm,所述调大的辊距为2
‑
3mm。
27.本发明还保护了一种用于电缆的橡胶复合材料在制备高阻燃外护套材料中的应用。
28.与现有技术相比,本发明具有的有益效果是:
29.(1)硅灰石是一种链状晶体结构的偏硅酸盐矿物,化学式为casio3,具有良好的耐高温性能,热膨胀系数小,无毒无味且耐化学药品腐蚀,同时其来源广泛、成本低廉,在橡胶改性中常作为增强或耐磨填料来使用;本发明对硅灰石进行改性,得到了既能够做为阻燃材料代替金属氢氧化物阻燃剂,又能够做为增强填料的功能性硅灰石,将功能性硅灰石应用于阻燃氯磺化聚乙烯电缆料中,功能性硅灰石提升了电缆料的阻燃性能。
30.(2)丁腈橡胶是丙烯腈和丁二烯的无规共聚物、是耐油性优异的弹性体,本发明中丁腈橡胶为低丙烯腈丁腈橡胶,丙烯腈的含量为18
‑
20%,使得丁腈橡胶在满足耐油性的前提下,具有优良的耐寒性;丁腈橡胶胶料的脆性温度可以达到
‑
61℃,压缩耐寒系数在
‑
40和
‑
50℃下分别达到0.69和0.61,是一种能够达到耐寒性要求的材料;
31.本发明采用丁腈橡胶对硅灰石进行改性,先将硅灰石采用聚乙二醇进行表面改性,使得聚乙二醇物理吸附在硅灰石表面,研究表明,聚乙二醇与硅灰石的物理吸附性能较强,即使无水乙醇和80℃的纯净水也无法洗脱,得到聚乙二醇包覆硅灰石材料;
32.将丁腈橡胶在酸性介质中进行水解,腈能够水解得到酰胺或酸,具体的水解原理为:rcn+h2o=rconh2或rcn+2h2o=rcooh+nh2;在氧化液中,浓硫酸将样品表面的c
‑
c键打开,碳原子氧化成羰基、羟基和羧基等极性基团,化学惰性表面变成有极性基团的表面,从而使橡胶表面活化或极性化,得到氧化丁腈橡胶;
33.氧化丁腈橡胶再与聚乙二醇进行酯化反应后,得到改性硅灰石材料,再将改性硅灰石材料与氯磺化聚乙烯共混制得复合材料,通过硅灰石阻燃,丁腈橡胶提升耐低温性能,继而得到了既克服低温缺陷又阻燃的复合材料。
34.(3)硅系阻燃剂因其无卤、低烟、阻燃效率高、环境友好、改善材料的加工性能、对聚合物的机械性能影响不大等优点,已成为无卤阻燃剂中一个重要的研究方向。以硅原子在分子中存在不同的形式,硅系阻燃剂一般可分为无机硅系阻燃剂和有机硅系阻燃剂,无机硅系阻燃剂主要包括二氧化硅、高岭土、云母粉、蒙脱土、硅灰石等硅酸盐化合物,兼具补强和阻燃的效果;本发明采用表面活性剂对硅灰石进行改性,表面活性剂通过极性基团与硅灰石颗粒表面进行作用,覆盖于硅灰石颗粒表面,增强硅灰石填料的亲油性,从而极大地改善其与氯磺化聚乙烯的相容性,增强填充效果。
35.(4)本发明还添加了膨胀阻燃剂,膨胀阻燃剂包括聚磷酸铵和季戊四醇,在燃烧时聚磷酸铵与季戊四醇表面会生成炭质泡沫层,起到隔热、隔氧、抑烟、防滴等功效,具有优良的阻燃性能,且生成的气体低烟、低毒、无腐蚀性;改性硅灰石提供了阻燃材料同时增强了力学性能,而其阻燃性能与金属氢氧化物阻燃剂相比较差,因此通过添加膨胀阻燃剂不仅提升阻燃性能,而且起到隔热、隔氧、抑烟、防滴的功效。
36.(5)氯磺化聚乙烯是以聚乙烯为主原料,经氯化、氯磺化反应而制得的具有高饱和化学结构的含氯特殊弹性体材料,属高性能品质的热塑性特种橡胶品种;由于其分子结构
中含有氯磺酰活性基团,故表现出高活性,而尤以耐化学介质腐蚀、抗臭氧氧化及耐油侵蚀、阻燃等性能突出,还具有抗候变、耐热、抗离子辐射、耐低温、抗磨蚀和电绝缘性及优异的机械性能。因此本发明以氯磺化聚乙烯为基体树脂,再加入氯磺化聚乙烯再生胶、硫化料和填充补强剂,确定了适用于氯磺化聚乙烯阻燃的配方。
具体实施方式
37.下面对本发明的具体实施方式进行详细描述,但应当理解本发明的保护范围并不受具体实施方式的限制。基于本发明中的实施例,本领域普通技术人员在没有做出创造性劳动的前提下所获得的所有其他实施例,都属于本发明保护的范围。本发明各实施例中所述实验方法,如无特殊说明,均为常规方法。
38.实施例1
39.一种用于电缆的橡胶复合材料的制备方法,包括如下步骤:
40.(1)称量:按如下重量份数称取原料:氯磺化聚乙烯100份;氯磺化聚乙烯再生胶20份;改性硅灰石60份;膨胀型阻燃剂15份;增塑剂10份;填充补强剂40份;硫化料1份,备用;
41.(2)改性硅灰石的制备:
42.称量:按照如下重量份数称取原料:硅灰石10份;聚乙二醇30份;丁腈橡胶20份,备用;
43.将硅灰石与聚乙二醇共混于无水乙醇中,浸泡40min,烘干至恒重后,依次用无水乙醇和80℃纯净水冲洗,再烘干至恒重,得到聚乙二醇包覆硅灰石材料;
44.将丁腈橡胶浸泡于氧化液中7d,得到氧化丁腈橡胶;
45.其中,氧化液包括5wt%kbr、5wt%ki和体积分数为50%的h2so4;
46.将氧化丁腈橡胶剪碎并溶解于二氯甲烷中,于常温下加入催化剂并搅拌30min,然后加入聚乙二醇包覆硅灰石材料并搅拌6h,干燥得到改性硅灰石材料;
47.其中,催化剂包括n'n
‑
二环己基碳二亚胺和4
‑
二甲氨基吡啶,n'n
‑
二环己基碳二亚胺的体积与4
‑
二甲氨基吡啶的质量之比为2ml:1g;催化剂占总量的5%;
48.(3)橡胶复合材料的制备:于开炼机内设置初始辊距,将氯磺化聚乙烯、改性硅灰石材料和氯磺化聚乙烯再生胶置于两辊筒之间塑炼5次,调大辊距,按顺序依次加入填充补强剂、膨胀型阻燃剂、增塑剂、硫化料后,再将辊距调节至初始辊距,混炼10次,下片,得到橡胶复合材料。
49.实施例2
50.一种用于电缆的橡胶复合材料的制备方法,包括如下步骤:
51.(1)称量:按如下重量份数称取原料:氯磺化聚乙烯100份;氯磺化聚乙烯再生胶25份;改性硅灰石80份;膨胀型阻燃剂10份;增塑剂15份;填充补强剂30份;硫化料5份,备用;
52.(2)改性硅灰石的制备:
53.称量:按照如下重量份数称取原料:硅灰石10份;聚乙二醇40份;丁腈橡胶30份,备用;
54.将硅灰石与聚乙二醇共混于无水乙醇中,浸泡45min,烘干至恒重后,依次用无水乙醇和80℃纯净水冲洗,再烘干至恒重,得到聚乙二醇包覆硅灰石材料;
55.将丁腈橡胶浸泡于氧化液中6d,得到氧化丁腈橡胶;
56.其中,氧化液包括5wt%kbr、5wt%ki和体积分数为50%的h2so4;
57.将氧化丁腈橡胶剪碎并溶解于二氯甲烷中,于常温下加入催化剂并搅拌25min,然后加入聚乙二醇包覆硅灰石材料并搅拌5h,干燥得到改性硅灰石材料;
58.其中,催化剂包括n'n
‑
二环己基碳二亚胺和4
‑
二甲氨基吡啶,n'n
‑
二环己基碳二亚胺的体积与4
‑
二甲氨基吡啶的质量之比为2ml:1g;催化剂占总量的5%;
59.(3)橡胶复合材料的制备:于开炼机内设置初始辊距,将氯磺化聚乙烯、改性硅灰石材料和氯磺化聚乙烯再生胶置于两辊筒之间塑炼6次,调大辊距,按顺序依次加入填充补强剂、膨胀型阻燃剂、增塑剂、硫化料后,再将辊距调节至初始辊距,混炼9次,下片,得到橡胶复合材料。
60.实施例3
61.一种用于电缆的橡胶复合材料的制备方法,包括如下步骤:
62.(1)称量:按如下重量份数称取原料:氯磺化聚乙烯100份;氯磺化聚乙烯再生胶30份;改性硅灰石95份;膨胀型阻燃剂5份;增塑剂25份;填充补强剂20份;硫化料10份,备用;
63.(2)改性硅灰石的制备:
64.称量:按照如下重量份数称取原料:硅灰石10份;聚乙二醇40份;丁腈橡胶45份,备用;
65.将硅灰石与聚乙二醇共混于无水乙醇中,浸泡50min,烘干至恒重后,依次用无水乙醇和80℃纯净水冲洗,再烘干至恒重,得到聚乙二醇包覆硅灰石材料;
66.将丁腈橡胶浸泡于氧化液中7d,得到氧化丁腈橡胶;
67.其中,氧化液包括5wt%kbr、5wt%ki和体积分数为50%的h2so4;
68.将氧化丁腈橡胶剪碎并溶解于二氯甲烷中,于常温下加入催化剂并搅拌15min,然后加入聚乙二醇包覆硅灰石材料并搅拌4h,干燥得到改性硅灰石材料;
69.其中,催化剂包括n'n
‑
二环己基碳二亚胺和4
‑
二甲氨基吡啶,n'n
‑
二环己基碳二亚胺的体积与4
‑
二甲氨基吡啶的质量之比为2ml:1g;催化剂占总量的5%;
70.(4)橡胶复合材料的制备:于开炼机内设置初始辊距,将氯磺化聚乙烯、改性硅灰石材料和氯磺化聚乙烯再生胶置于两辊筒之间塑炼7次,调大辊距,按顺序依次加入填充补强剂、膨胀型阻燃剂、增塑剂、硫化料后,再将辊距调节至初始辊距,混炼8次,下片,得到橡胶复合材料。
71.对比例1
72.与实施例2的制备步骤相同,不同之处仅在于,将改性硅灰石材料替换为等量的氢氧化铝。
73.对比例2
74.与实施例2的制备步骤相同,不同之处仅在于,将改性硅灰石材料替换为等量的硅灰石。
75.对比例3
76.与实施例2的制备步骤相同,不同之处仅在于,不添加改性硅灰石材料。
77.本发明实施例1
‑
3均制得性能优异的电缆橡胶复合材料,且性能相近,下面以实施例2为例,对实施例2、对比例1
‑
3进行对比研究,具体研究方法及结果如下:
78.性能测试:
79.工艺性能、力学性能测试等均采用相应的最新国家标准,热空气老化和耐油条件:100℃下72h,介质为机油。
80.结果:
81.(1)改性硅灰石对复合材料的力学性能影响
82.表1复合材料力学性能对照表
[0083][0084]
实施例2添加的是改性硅灰石材料,对比例1添加的是氢氧化铝,对比例2添加的是未改性硅灰石,与对比例1及对比例2相比,实施例2材料的力学性能可见得到了明显的提升;加入不同的阻燃剂,胶料的硬度、拉伸强度、定伸应力、伸长率和撕裂强度等力学性能,可以看出,实施例2材料的力学性能优于对比例1,对比例1优于对比例2,说明改性硅灰石有效提升了电缆料的力学性能,主要原因在于改性硅灰石提升了与阻燃氯磺化聚乙烯电缆料的相容性,实施例2材料的力学性能明显优于对比例2,说明实施例2中的硅灰石实现了有效的改性,改性后的硅灰石与阻燃氯磺化聚乙烯电缆料实现了有效的共混,继而通过丁腈橡胶的共混提升了复合材料的力学性能。对比低温脆性来看,实施例2能够于更低的温度下保持稳定,因此具有更加优异的耐低温性能。
[0085]
(2)电缆料抗老化性能研究
[0086]
表2复合材料抗老化性能对照表
[0087][0088]
由表2可以看出,老化后胶料的硬度均较老化前有所增加,但是硬度变化值不明显;胶料老化后的拉伸强度大于老化前,且拉伸强度变化率最不明显的是实施例2;胶料老化后的伸长率均小于老化前,且伸长率变化百分率最不明显的是实施例2,说明热空气老化和油性环境中,实施例2的性能变化最少,耐老化性能最佳。
[0089]
(3)电缆料氧指数研究
[0090]
氧指数是在规定条件下,试样在氧、氮混合气流中,维持平稳燃烧所需的最低氧气浓度,以氧所占体积百分数表示,实施例2、对比例1
‑
3的氧指数见表3:
[0091]
表3实施例2、对比例1
‑
3的氧指数对照表
[0092]
测试项目实施例2对比例1对比例2对比例3
氧指数/%39.235.429.432.6
[0093]
由表3能够看出,对比例2的氧指数最小,其电缆阻燃性能相对较差,实施例2的阻燃性能最佳,明显优于对比例2及对比例3,说明在复合材料中,改性硅灰石和膨胀型阻燃剂的共同作用有效提升了阻燃性能;另外,阻燃效果优于对比例1的氢氧化铝,说明改性硅灰石和膨胀型阻燃剂的共同作用优于氢氧化铝和膨胀型阻燃剂的共同作用,间接的说明了改性硅灰石有效的替代了氢氧化铝作为阻燃材料。
[0094]
显然,本领域的技术人员可以对本发明进行各种改动和变型而不脱离本发明的精神和范围。这样,倘若本发明的这些修改和变型属于本发明权利要求及其等同技术的范围之内,则本发明也意图包含这些改动和变型在内。