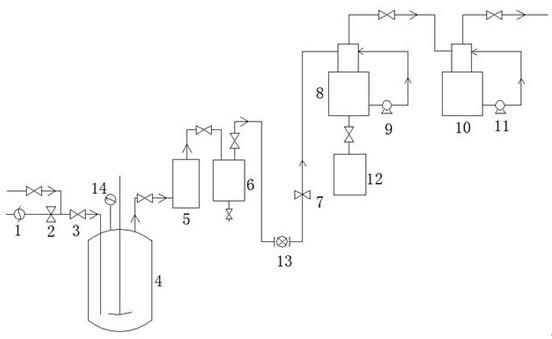
1.本发明属于有机合成技术领域,具体涉及一种脂肪伯胺制备二脂肪仲胺的方法。
背景技术:2.二脂肪仲胺是长碳直链或带支链的双烷基仲胺,作为一种特种胺,具备一般胺类的用途,主要用于矿物浮选、污水处理中的萃取剂、除垢的润滑油添加剂、腐蚀抑制剂、石英砂浮选剂、沥青乳化剂、杀菌剂或高效清洗剂等。如二仲辛胺是n503(苯酚萃取剂)的主要原料,二(2
‑
乙基己基)胺、二正己胺广泛用作表面活性剂的中间体,矿石浮洗、稀有金属的萃取剂、乳化剂等。
3.传统二脂肪仲胺合成方法有以下两种:1)以脂肪醛和脂肪伯胺为主原料,先制得亚胺,亚胺氢化制得二脂肪仲胺,其原料脂肪醛工业化厂家很少,价格高,导致二脂肪仲胺不容易工业化,生产成本高;2)由卤代烃与过量的伯胺反应,其缺点是化学选择性差,不可避免地发生过烷基化反应,且产物复杂,除了生成仲胺,还会产生大量的叔胺和盐副产物,且产物中含有大量未反应的原料伯胺,后处理麻烦、产率低。
技术实现要素:4.针对现有技术中存在的上述问题,本发明的目的在于提供一种反应选择性高、设备简单,投资小,收率高的二脂肪仲胺的制备方法。
5.本发明所述的一种脂肪伯胺制备二脂肪仲胺的方法,采用专制的反应装置,所述反应装置包括反应釜,反应釜上设有冷凝器、氢气进气管、氮气进气管及压力表,氢气进气管、氮气进气管与反应釜之间的管道上设有针形阀,氢气进气管上设有氢气减压阀和氢气调节阀,冷凝器出口依次连接缓冲罐、第一尾气吸收罐及第二尾气吸收罐,尾气从反应釜顶部排出经冷凝器后,尾气夹带的反应液经冷凝后返回反应釜,未及时冷凝的反应液进入缓冲罐中收集,尾气再进入第一尾气吸收罐及第二尾气吸收罐,所述第一尾气吸收罐、第二尾气吸收罐内有水,用于吸收尾气中的氨气;第一尾气吸收罐、第二尾气吸收罐的罐底及罐顶之间分别设有第一循环泵、第二循环泵,尾气在尾气吸收罐中形成内循环,促进氨气的吸收;每个连接管路上分别设有控制阀;其特征在于所述方法包括如下步骤:1)将脂肪伯胺、催化剂投入反应釜内,将水加入第一尾气吸收罐及第二尾气吸收罐中;反应釜用氮气、氢气各置换三次,再关闭氮气管道上的控制阀,打开针形阀及管路上的控制阀,将氢气减压阀设定压力<0.6mpa,并由排气调节阀控制排气流量为100~300l/h,氢气调节阀与反应釜连锁,根据压力表的显示,氢气调节阀控制进氢的流量,保证反应釜内呈正压状态,边进氢边排气,反应釜内加热升温到100~180℃进行脱氨反应,尾气从反应釜顶部依次经过冷凝器、缓冲罐后,尾气夹带的反应液冷凝后返回反应釜或缓冲罐中收集,尾气再进入第一尾气吸收罐及第二尾气吸收罐进行氨气吸收,反应过程中gc分析至伯胺含量<1%,停止加热和排气;2)反应液冷却到室温,滤除催化剂,得到二脂肪仲胺的粗品,精馏得到含量大于
99%的如式(ⅰ)所示的二脂肪仲胺产品; r为直链或带支链的烷基,优选为直链或带支链的c5h
11
、c6h
13
、c8h
17
、c
12
h
25
、c
14
h
29
、c
16
h
33
或c
18
h
37 ;3)尾气中的氨气由第一尾气吸收罐及第二尾气吸收罐中的水吸收,第一尾气吸收罐得到的氨水转入氨水收集罐中收集并回收利用,第二尾气吸收罐中的氨水转入第一尾气吸收罐中、第二尾气吸收罐中加水继续吸收尾气,脱氨后的安全尾气从第二尾气吸收罐顶部排空。
6.进一步地,本发明还限定了脂肪伯胺排气脱氨的温度120
‑
170℃。
7.进一步地,本发明还限定了催化剂的用量为脂肪伯胺质量的0.2
‑
20%,优选2
‑
10%。
8.进一步地,本发明还限定了催化剂为加氢催化剂,选自雷尼镍、ni/al2o3、钯碳、铂碳、钯铝催化剂中的一种或几种混合物。
9.进一步地,本发明还限定了脱氨反应采用边进氢气边排气的方式,脂肪伯胺脱气压力0.2
‑
0.6mpa,优选0.3
‑
0.4mpa。
10.进一步地,本发明还限定了缓冲罐底部设有出料管,出料管上设有控制阀,本发明的缓冲罐设置于冷凝器出口管路上,尾气夹带的反应液在经冷凝器时,未及时冷凝的,可以进入缓冲罐中收集,收集至一定量时,打开底部出料管中的控制阀,将收集的反应液取出,返回反应釜继续反应。
11.进一步地,本发明还限定了缓冲罐及第一尾气吸收罐之间设有排气调节阀及流量计,由排气调节阀调节排气流量大小,并在流量计上显示。
12.进一步地,本发明还限定了第一尾气吸收罐底部连接有氨水收集罐,当氨水浓度达到所需要的浓度时,及时将该氨水放出并收集,同时将第二尾气吸收罐中的稀氨水转至第一尾气吸收罐中,第二尾气吸收罐中补充水,继续吸收氨气,本发明第二尾气吸收罐的底部也可以和第一尾气吸收罐底部设置同样的结构,作为氨水转移罐,便于转换氨水至第一尾气吸收罐中。
13.更进一步地,本发明在氢气进气管、氮气进气管与反应釜之间的管道上设有针形阀,用于对氮气,氢气的进气量进行人工调节。
14.本发明的主反应方程式为:
通过采用上述技术,与现有技术相比,本发明的有益效果如下:1)本发明通过脂肪伯胺和加氢催化剂一步脱氨合成选择性>95%(gc检测)的二脂肪仲胺,解决了脂肪醛和脂肪伯胺合成二脂肪仲胺中脂肪醛难获取的问题;2)本发明通过采用限定的装置,边进气边出气,保证反应釜内呈正压状态,一步合成二脂肪仲胺,设备操作简单,产生副产氨气由水吸收形成工业氨水,作为商品外卖,更经济环保。
附图说明
15.图1为本发明的反应装置结构示意图。
16.图中:1、氢气减压阀;2、氢气调节阀;3、针形阀;4、反应釜;5、冷凝器;6、缓冲罐;7、排气调节阀;8、第一尾气吸收罐;9、第一循环泵;10、第二尾气吸收罐;11、第二循环泵;12、氨水收集罐,13
‑
流量计,14
‑
压力表。
具体实施方式
17.以下结合说明书附图及实施例对本发明作进一步的描述,但本发明的保护范围并不仅限于此:如图1所示,本发明限定的一种脂肪伯胺制备二脂肪仲胺的反应装置,包括反应釜4,反应釜4上设有冷凝器5、搅拌器、氢气进气管、氮气进气管及压力表14,氢气进气管、氮气进气管与反应釜4之间的管道上设有针形阀3,氢气进气管上设有氢气减压阀1和氢气调节阀2,所述冷凝器5出口依次连接缓冲罐6、第一尾气吸收罐8及第二尾气吸收罐10,反应釜4顶部的尾气经冷凝器5,尾气夹带出的反应液冷凝后返回反应釜4中,未及时冷凝的反应液同尾气进入缓冲罐6,在缓冲罐6中储存,缓冲罐6底部设有出料管,出料管上设有控制阀,缓冲罐6内的反应液存有一定量的时候,可以从出料管放出;缓冲罐6出来的尾气再依次进入第一尾气吸收罐8及第二尾气吸收罐10,所述第一尾气吸收罐8、第二尾气吸收罐10内有水,用于吸收尾气中的氨气;第一尾气吸收罐8、第二尾气吸收罐10的罐底及罐顶之间分别设有第一循环泵9、第二循环泵11,尾气在尾气吸收罐中形成内循环,促进氨气的吸收;每个连接管路上分别设有控制阀;为了便于观察流量,本发明在缓冲罐6及第一尾气吸收罐8之间设有排气调节阀7和流量计13,根据实验要求,由排气调节阀7调节排气流量大小,并通过流量计13显示。
18.为了便于氨水的收集,本发明在第一尾气吸收罐8底部连接有氨水收集罐12。
19.本发明gc分析条件:仪器和设备a)气相色谱仪:灵敏度及稳定性符合有关规定的任何型号的气相色谱仪;b)色谱柱:毛细管柱 型号 hp
‑
5 规定50m
×
0.32mm
×
0.52μm或其它相同类型的柱子;c)数据处理机或色谱工作站;d)氢火焰离子化检测器;e)微量进样器,10μl。
20.色谱分析条件设定: a)柱温:初始温度为170℃,升温速率10℃/min,终温280℃(10min);b)柱前压力:100kpa;c) 汽化室温度:280℃;d)检测器温度:280℃;e)载气流量:约20ml/min;f)燃气流量:约40ml/min;g)助燃气流量:约400ml/min。
21.本发明所得二脂肪仲胺产品的标准如下:外观:无色透明液体;含量:>99%; 水份:<0.3%; 色泽:<30#(apha)获得了一系列的产品,有代表性的比如二正己胺,二正戊胺,二正辛胺,二(2
‑
乙基己基)胺,二仲辛胺,二椰油仲胺等。
22.本发明实施例中,第一尾气吸收罐8及第二尾气吸收罐10位于反应釜4所在楼层上楼顶。
23.实施例1:在3000l带冷凝器5的中压反应釜4中,加入2
‑
乙基己胺1700kg,ni/al2o370kg,氮气、氢气各置换三次,氮气管路上的阀门关闭,氢气调节阀2与反应釜4内压力连锁;将氢气减压阀1设定0.6mpa(反应釜内压力小于0.6mpa,氢气调节阀2打开,反之氢气调节阀2关闭),启动搅拌器搅拌,反应釜4内升温到150℃进行脱氨反应,调节排气调节阀7的开度,至排气流量为250l/h,由流量计13显示,保持边进气边排气,若反应釜4的压力,即压力计14显示的压力超过0.6mpa,氢气调节阀2自动切断氢气,反应釜4的压力低于0.6mpa,氢气调节阀2自动加大氢气进气量,也可以通过针形阀3调节,即保证反应釜4内呈正压状态,尾气从反应釜4顶部出口进入冷凝器5,尾气夹带的反应液冷凝后返回反应釜4中继续反应,未及时冷凝的反应液进入缓冲罐6中收集,收集至一定量后再返回至反应釜4中,尾气继续进入第一尾气吸收罐8及第二尾气吸收罐10中,由吸收罐中的水吸收氨气,15h后gc分析,2
‑
乙基己胺:0.56%,二(2
‑
乙基己基)胺:98.2%,关闭氢气调节阀2排气和进气阀,冷却到50℃,经过过滤器去除催化剂并回收,粗品通过精馏得到成品二(2
‑
乙基己基)胺:1500kg,含量99.4%,收率94.2%;取样检测楼顶第一尾气吸收罐8的水中氨浓度达到20%,放出包装外卖,同时将第
二尾气吸收罐10中的水打入第一尾气吸收罐8中,第二尾气吸收罐10补充自来水,继续吸收尾气中的氨气。
24.实施例2:在3000l带冷凝器5的中压反应釜4中,加入2
‑
乙基己胺1700kg,二元雷尼镍催化剂80kg,氮气,氢气各置换三次,氮气管路上的阀门关闭,氢气调节阀2与反应釜4内压力连锁;将氢气减压阀1设定0.4mpa(反应釜内压力小于0.4mpa,氢气调节阀2打开,反之氢气调节阀2关闭),启动搅拌器搅拌,反应釜4内升温到160℃进行脱氨反应,调节排气调节阀7的开度,至排气流量为100l/h,由流量计13显示,边进气边排气,若反应釜4的压力超过0.4mpa,氢气调节阀2自动切断氢气,反应釜4的压力低于0.4mpa,氢气调节阀2自动加大氢气进气量,也可以通过针形阀3调节,即保证反应釜4内呈正压状态,尾气从反应釜4顶部出口进入冷凝器5,尾气夹带的反应液冷凝后返回反应釜4中继续反应,未及时冷凝的反应液进入缓冲罐6中收集,收集至一定量后再返回至反应釜4中,尾气继续进入第一尾气吸收罐8及第二尾气吸收罐10中,由吸收罐中的水吸收,18h后gc分析,2
‑
乙基己胺:0.45%,二(2
‑
乙基己基)胺:98.8%,关闭排气和进气阀,冷却到50℃,经过过滤器去除催化剂并回收,粗品通过精馏得到成品二(2
‑
乙基己基)胺:1510kg,含量99.6%,收率94.9%;取样检测楼顶第一尾气吸收罐8的水中氨浓度达到20%,放出包装外卖,同时将第二尾气吸收罐10中的水打入第一尾气吸收罐8中,第二尾气吸收罐10补充自来水,继续吸收尾气中的氨气。
25.实施例3:在3000l带冷凝器的中压釜中,加入2
‑
乙基己胺1700kg,钯碳催化剂10kg,氮气,氢气各置换三次,氮气管路上的阀门关闭,氢气调节阀2与反应釜4内压力连锁;将氢气减压阀1设定0.3mpa,(反应釜内压力小于0.3mpa,氢气调节阀2打开,反之氢气调节阀2关闭),启动搅拌器搅拌,反应釜4内升温到120℃脱氨反应,调节排气调节阀7的开度,至排气流量为150l/h,由流量计13显示,,边进气边排气,若反应釜4的压力超过0.3mpa,氢气调节阀2自动切断氢气,反应釜4的压力低于0.3mpa,氢气调节阀2自动加大氢气进气量,即保证反应釜4内呈正压状态,也可以通过针形阀3调节,即保证反应釜4内呈正压状态,尾气从反应釜4顶部出口进入冷凝器5,尾气夹带的反应液冷凝后返回反应釜4中继续反应,未及时冷凝的反应液进入缓冲罐6中收集,收集至一定量后再返回至反应釜4中,尾气继续进入第一尾气吸收罐8及第二尾气吸收罐10中,由吸收罐中的水吸收氨气,18h后gc分析,2
‑
乙基己胺:9.45%,二(2
‑
乙基己基)胺:88.8%,36h后gc分析,2
‑
乙基己胺:0.9%,二(2
‑
乙基己基)胺:97.1%,关闭排气和进气阀,冷却到50℃,经过过滤器去除催化剂并回收,粗品通过精馏得到成品二(2
‑
乙基己基)胺:1460kg,含量99.2%,收率92%;取样检测楼顶第一尾气吸收罐8的水中氨浓度达到20%,放出包装外卖,同时将第二尾气吸收罐10中的水打入第一尾气吸收罐8中,第二尾气吸收罐10补充自来水,继续吸收尾气中的氨气。
26.实施例4:在3000l带冷凝器的中压釜中,加入仲辛胺1700kg,四元雷尼镍催化剂100kg,氮气,氢气各置换三次,氮气管路上的阀门关闭,氢气调节阀2与反应釜4内压力连锁;将氢气减压阀1设定0.6mpa(反应釜内压力小于0.6mpa,氢气调节阀2打开,反之氢气调节阀2关
闭),启动搅拌器搅拌,反应釜4内升温到150℃进行脱氨反应,调节排气调节阀7的开度,至排气流量为250l/h,由流量计13显示,保持边进气边排气,若反应釜4的压力超过0.6mpa,氢气调节阀2自动切断氢气,反应釜4的压力低于0.6mpa,氢气调节阀2自动加大氢气进气量,即保证反应釜4内呈正压状态,也可以通过针形阀3调节,即保证反应釜4内呈正压状态,尾气从反应釜4顶部出口进入冷凝器5,尾气夹带的反应液冷凝后返回反应釜4中继续反应,未及时冷凝的反应液进入缓冲罐6中收集,收集至一定量后再返回至反应釜4中,尾气继续进入第一尾气吸收罐8及第二尾气吸收罐10中,由吸收罐中的水吸收氨气,20h后gc分析,仲辛胺:0.9%,二仲辛胺:97.1%,关闭排气和进气阀,冷却到50℃,经过过滤器去除催化剂并回收,粗品通过精馏得到成品二仲辛胺:1508kg,含量99.3%,收率94.8%;取样检测楼顶第一尾气吸收罐8的水中氨浓度达到20%,放出包装外卖,同时将第二尾气吸收罐10中的水打入第一尾气吸收罐8中,第二尾气吸收罐10补充自来水,继续吸收尾气中的氨气。
27.表1 实施例5
‑
8的原料及反应条件表从表1可以看出,本发明采用限定的装置及方法,即使采用回收的催化剂 ,得到的
产品收率也高达92.1%以上,产品含量高达99%以上。