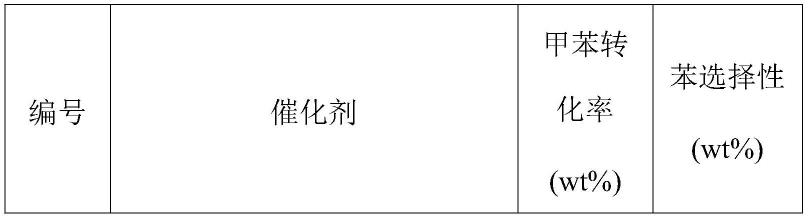
1.本发明属于甲苯歧化制苯技术领域,具体涉及一种甲苯歧化制苯工艺。
背景技术:2.芳烃是石油化工工业的重要基础原料,在总数近千万种的已知有机化合物中,芳烃化合物约占30%,其中苯(b)、甲苯(t)、二甲苯(x)的产量和规模仅次于乙烯、丙烯,被称为一级基本有机原料,主要用于合成高分子聚酯纤维和塑料,还在医药、农药、染料等领域有极其广泛的用途。
3.目前芳烃的大规模工业生产是通过芳烃联合装置实现的,典型的芳烃联合装置包括石脑油加氢、催化重整、裂解汽油加氢等生产芳烃的装置以及芳烃转化和芳烃分离装置,主产品是苯和二甲苯(主要是对二甲苯px和邻二甲苯ox)。涉及的关键性技术有:催化重整、芳烃抽提、甲苯歧化、烷基转移、二甲苯异构化及px分离等芳烃转化技术。其中,甲苯歧化单元是芳烃联合装置中关键单元之一,起物流转换枢纽和有效调整芳烃原料与产品结构的重要作用。
4.除了甲苯可以歧化生成苯和二甲苯外,以往还有较传统的甲苯脱烷基制苯工艺,这类脱烷基制苯工艺包含催化脱烷基和热脱烷基二种。催化脱烷基典型的操作条件是575-650℃,压力为2.5-6.0mpa,热脱烷基温度可高达760℃。两者的基本工艺流程是相似的,用富氢气体循环控制放热反应段的温度。液体产品通过除去轻组分稳定化,再用白土处理,最后精馏得到苯产品,甲苯和重组分循环回装置。
5.美国arco公司和烃研究公司开发了had热脱烷基工艺,在低浓度下操作可得到较高的苯收率。美国gulf公司开发的thd工艺与之相似。这些工艺适宜转化来自btx分离的主要含有甲苯等芳烃的工艺物料。三菱化学的mhc工艺是一种能处理大量非芳烃组分的热脱烷基工艺,可以使用纯度较低的氢,降低对补充氢的要求。
6.houdry开发的以甲苯为原料的“detol”工艺、以加氢裂解汽油为原料的“pyrotol”工艺、以焦化粗苯为原料的“litol”工艺这些都是催化脱烷基工艺。其中houdry的pyrotol工艺基本目的是裂解汽油中的芳烃脱烷基。pyrotol工艺流程与litol工艺非常相似,要求原料预处理脱除戊烷,至少除去部分c9+馏分。切割的原料被蒸发,并通过预处理反应器,使二烯烃、环二烯烃和苯乙烯选择加氢。在pyrotol反应器中,芳烃被脱烷基生成苯。其他反应包括非芳烃裂解成轻质烃(主要是c1-c3)和脱硫。未反应的甲苯和重质芳烃循环返回反应段。目前,由于上述的脱烷基制苯工艺能耗高、收率低,且易于产生污染,同时临氢脱烷基的cr2o3/al2o3催化剂活性温度高、抗积炭能力差,且这类催化剂在实际工业生产使用中容易引起飞温失活,现今工业上已被甲苯歧化增产苯工艺所取代。目前,进一步提高催化剂进料空速、提高苯的收率、降低反应氢烃比、节能降耗,仍然是甲苯歧化制苯的发展方向。
7.对于甲苯歧化制苯反应而言,甲苯歧化反应的转化率和选择性与催化剂孔道结构、酸性酸强度直接相关,精准优化共晶分子筛催化剂的结构与组成,对获得具有高选择性、高芳烃处理能力、高转化率、较低氢耗、高苯纯度的高性能催化剂具有十分重要的作用。
技术实现要素:8.为了克服现有技术的不足,本发明提供一种甲苯歧化制苯工艺,利用负载金属的氢化共晶分子筛制成的催化剂具有高甲苯转化率、高苯选择性、高稳定性的特点,能够提高甲苯转化率,增大苯选择性,并且制苯过程稳定。
9.本发明的上述目的是通过以下技术方案实现的:一种甲苯歧化制苯工艺,具体步骤为:
10.1.加热甲苯:甲苯与循环未反应的甲苯混合预热后与循环氢压缩机中的循环氢一起进入管式炉加热至405~420℃;
11.2.甲苯歧化制苯反应:步骤1中加热后的混合气体进入固定床微型反应器,所述固定床微型反应器中装有甲苯歧化制苯催化剂,并在反应器上下各填装惰性玻璃珠,反应温度405~420℃,反应压力3.0mpa;
12.3.苯分离:反应后反应产物出固定床微型反应器,反应产物进行换热、冷却至30℃、气液分离,气体回到循环氢压缩机,液体经汽提塔除去非芳烃化合物后经白土塔稳定处理后分离苯、甲苯、二甲苯以及很少量二甲苯以上芳烃组分,甲苯回循环反应系统与新的甲苯再次进行歧化制苯工艺。
13.其中,所述甲苯歧化制苯催化剂中氢型共晶分子筛质量分数为40~90%,粘结剂质量分数为10~60%,活性金属或金属氧化物质量分数为0.1~20%,助剂质量分数为1~2%。
14.所述甲苯歧化制苯催化剂的制备方法具体为:
15.1)制备共晶分子筛:将硅源、铝源、无机酸、有机模板剂、水配制成复合分子筛反应体系,再晶化制备共晶分子筛;
16.2)共晶分子筛改性为氢型共晶分子筛:将步骤1)所述共晶分子筛置于含体积分数为0.15%氯化铵的水溶液中,共晶分子筛与氯化铵水溶液的体积比为3:20,在90℃下离子交换6小时,滤去母液,重复离子交换2~4次,洗涤后于120℃烘干2小时,得到混合铵型沸石。在将得到的铵型分子筛在550℃焙烧4小时,得到氢型共晶分子筛;
17.3)制备氢型共晶分子筛催化剂:将步骤2)所述氢型共晶分子筛与粘接剂、助剂混捏、挤条成型并破碎长度为2~4mm的催化剂颗粒。在马弗炉中520℃焙烧2小时,经筛选即得到氢型共晶分子筛催化剂;
18.4)氢型共晶分子筛催化剂负载活性金属或金属氧化物:通过真空浸渍将活性金属或金属氧化物负载与步骤3)所述氢型共晶分子筛催化剂上经500℃焙烧2小时后得到高活性甲苯歧化制苯催化剂。
19.所述氢型共晶分子筛中氧化硅和氧化铝的摩尔比为5~80,比表面积为300~800m2/g,孔容为0.25~0.80cm3/g。
20.所述氢型共晶分子筛是zsm-5/zsm-12、zsm-5/β、mor/β、mor/zsm-12、zsm-5/mor、y/mcm-22共晶分子筛中的一种或几种改性后产物。
21.所述共晶分子筛为两种不同晶体结构分子筛的复合晶体,其中二种分子筛的重量比率为1/9~9/1。
22.所述的活性金属或金属氧化物中的金属种类包含铑、镍、钴、铜、钼、银、铱、镧、钇、钌、锆、锑、铌中的一种或几种。
23.所述的粘结剂为硅溶胶、氧化铝、天然黏土、凹凸棒土、水玻璃、甲基纤维素、聚乙烯醇、石蜡、淀粉、塑料树脂、皂土、糊精中的一种或几种。
24.所述的助剂为助挤剂、扩孔及或强度助剂。选自田菁粉、干淀粉、甲基纤维素、羧甲基纤维素钠、甘油、润滑油、石墨、硬脂酸、石蜡、松香、聚丙烯酰胺中的一种或几种。
25.所述步骤4)可进行多次,将多种金属负载于甲苯歧化制苯催化剂上。
26.本发明与现有技术相比的有益效果是:
27.1.使用的甲苯歧化制苯催化剂具有高甲苯转化率、高苯选择性、高稳定的特点,整体性能优于单组分普通分子筛与二种简单混合分子筛催化剂的性能。并且,制备过程简单,满足大规模工业生产与应用的要求。
28.2.制备方法包括共晶分子筛的改性修饰,较共晶分子筛免去了对催化剂的毒性,提高催化剂整体性能,同时兼具共晶分子筛的比表面积高于对应相同重量比率二种分子筛混合物的8%~12%,共晶分子筛的孔容高于对应相同重量比率二种分子筛混合物的7%~10%的优势。
29.3.本发明使用的甲苯歧化制苯工艺甲苯转化率较同类型工艺高9~26%,苯选择性较同类型工艺高5~12%。
具体实施方式
30.下面通过具体实施例详述本发明,但不限制本发明的保护范围。如无特殊说明,本发明所采用的实验方法均为常规方法,所用实验器材、材料、试剂等均可从商业途径获得。下述实施例中所采用的固定床微型反应器、循环氢压缩机、汽提塔、白土塔、回循环反应系统均为本领域常规设备。
31.实施例1
32.将硅源、铝源、无机酸、有机模板剂、水配制成复合分子筛反应体系,再晶化制备出钠型zsm-5/zsm-12共晶分子筛,将zsm-5/zsm-12共晶分子筛置于含体积分数为0.15%氯化铵的水溶液中,共晶分子筛与氯化铵水溶液的体积比为3:20,在90℃下离子交换6小时,滤去母液,重复离子交换2~4次,洗涤后于120℃烘干2小时,得到混合铵型沸石。再将得到的铵型分子筛在550℃焙烧4小时,得到氢型zsm-5/zsm-12共晶分子筛。
33.将氢型zsm-5/zsm-12共晶分子筛(xrd粉末衍射法分析测得重量比率为4.5/5.5)、硅溶胶、田菁粉按照80:20:5的比例混捏、挤条成型并破碎长度为2~4mm的催化剂颗粒。在马弗炉中520℃焙烧2小时,经筛选即得到zsm-5/zsm-12共晶分子筛催化剂。然后通过真空浸渍,将4wt%mo负载于催化剂上,经500℃焙烧2小时后得到4%mo-zsm-5/zsm-12催化剂。将4%mo-zsm-5/zsm-12催化剂再通过等体积浸渍的方法将0.1wt%rh负载于催化剂上,得到4%mo-0.1%rh-zsm-5/zsm-12共晶分子筛催化剂。
34.甲苯与循环未反应的甲苯混合预热后与循环氢压缩机中的循环氢一起进入管式炉加热至410℃;加热后的混合气体进入固定床微型反应器,固定床微型反应器中装有4%mo-0.1%rh-zsm-5/zsm-12共晶分子筛催化剂,并在反应器上下各填装惰性玻璃珠,反应温度410℃,反应压力3.0mpa,在h2气氛中,原料质量空速为2.0h-1
的条件下进行活性评价,反应产物用气相色谱仪进行定量分析,分析结果列于表1。反应后反应产物出固定床微型反应器,反应产物进行换热、冷却至30℃、气液分离,气体回到循环氢压缩机,液体经汽提塔除去
非芳烃化合物后经白土塔稳定处理后分离苯、甲苯、二甲苯以及很少量二甲苯以上芳烃组分,甲苯回循环反应系统与新的甲苯再次进行歧化制苯工艺。
35.实施例2
36.将硅源、铝源、无机酸、有机模板剂、水配制成复合分子筛反应体系,再晶化制备出钠型mor/zsm-12共晶分子筛,将mor/zsm-12共晶分子筛置于含体积分数为0.15%氯化铵的水溶液中,共晶分子筛与氯化铵水溶液的体积比为3:20,在90℃下离子交换6小时,滤去母液,重复离子交换2~4次,洗涤后于120℃烘干2小时,得到混合铵型沸石。再将得到的铵型分子筛在550℃焙烧4小时,得到氢型mor/zsm-12共晶分子筛。
37.通过等体积浸渍的方法将3wt%cu和0.5wt%ni负载到氢型mor/zsm-12共晶分子筛(xrd粉末衍射法分析测得重量比率为2.5/7.5)上,得到3%cu-0.5%ni-mor/zsm-12分子筛,然后将3%cu-0.5%ni-mor/zsm-12分子筛、氧化铝、甲基纤维素按照80:20:3的比例混捏、挤条成型并破碎长度为2~4mm的催化剂颗粒。在马弗炉中520℃焙烧2小时,经筛选即得到3%cu-0.5%ni-mor/zsm-12共晶分子筛催化剂。
38.甲苯与循环未反应的甲苯混合预热后与循环氢压缩机中的循环氢一起进入管式炉加热至416℃;加热后的混合气体进入固定床微型反应器,固定床微型反应器中装有3%cu-0.5%ni-mor/zsm-12共晶分子筛催化剂,并在反应器上下各填装惰性玻璃珠,反应温度416℃,反应压力3.0mpa,在h2气氛中,原料质量空速为2.0h-1
的条件下进行活性评价,反应产物用气相色谱仪进行定量分析,分析结果列于表1。反应后反应产物出固定床微型反应器,反应产物进行换热、冷却至30℃、气液分离,气体回到循环氢压缩机,液体经汽提塔除去非芳烃化合物后经白土塔稳定处理后分离苯、甲苯、二甲苯以及很少量二甲苯以上芳烃组分,甲苯回循环反应系统与新的甲苯再次进行歧化制苯工艺。
39.实施例3
40.将硅源、铝源、无机酸、有机模板剂、水配制成复合分子筛反应体系,再晶化制备出钠型mor/zsm-5共晶分子筛,将mor/zsm-5共晶分子筛置于含体积分数为0.15%氯化铵的水溶液中,共晶分子筛与氯化铵水溶液的体积比为3:20,在90℃下离子交换6小时,滤去母液,重复离子交换2~4次,洗涤后于120℃烘干2小时,得到混合铵型沸石。再将得到的铵型分子筛在550℃焙烧4小时,得到氢型mor/zsm-5共晶分子筛。
41.将氢型mor/zsm-5共晶分子筛(xrd粉末衍射法分析测得重量比率为6.5/3.5)、氧化铝、田菁粉按照75:25:5的比例混捏、挤条成型并破碎长度为2~4mm的催化剂颗粒。在马弗炉中520℃焙烧2小时,经筛选即得到mor/zsm-5共晶分子筛。然后通过真空浸渍,将0.15wt%ru负载于催化剂上,经500℃焙烧2小时后得到0.15%ru-mor/zsm-5催化剂。将0.15%ru-mor/zsm-5催化剂再通过等体积浸渍的方法将2wt%la负载于催化剂上,得到0.15%ru-2%la-mor/zsm-5共晶分子筛催化剂。
42.甲苯与循环未反应的甲苯混合预热后与循环氢压缩机中的循环氢一起进入管式炉加热至405℃;加热后的混合气体进入固定床微型反应器,固定床微型反应器中装有0.15%ru-2%la-mor/zsm-5共晶分子筛催化剂,并在反应器上下各填装惰性玻璃珠,反应温度405℃,反应压力3.0mpa,在h2气氛中,原料质量空速为2.0h-1
的条件下进行活性评价,反应产物用气相色谱仪进行定量分析,分析结果列于表1。反应后反应产物出固定床微型反应器,反应产物进行换热、冷却至30℃、气液分离,气体回到循环氢压缩机,液体经汽提塔除
去非芳烃化合物后经白土塔稳定处理后分离苯、甲苯、二甲苯以及很少量二甲苯以上芳烃组分,甲苯回循环反应系统与新的甲苯再次进行歧化制苯工艺。
43.实施例4
44.将硅源、铝源、无机酸、有机模板剂、水配制成复合分子筛反应体系,再晶化制备出钠型mor/β共晶分子筛,将mor/β共晶分子筛置于含体积分数为0.15%氯化铵的水溶液中,共晶分子筛与氯化铵水溶液的体积比为3:20,在90℃下离子交换6小时,滤去母液,重复离子交换2~4次,洗涤后于120℃烘干2小时,得到混合铵型沸石。再将得到的铵型分子筛在550℃焙烧4小时,得到氢型mor/β共晶分子筛。
45.通过等体积浸渍的方法同时将2wt%mo、1wt%ag和0.2wt%ir负载到氢型mor/β共晶分子筛(xrd粉末衍射法分析测得重量比率为9.5/0.5),然后将浸渍后的分子筛、氧化铝、甲基纤维素按照70:30:8的比例混捏、挤条成型并破碎长度为2~4mm的催化剂颗粒。在马弗炉中520℃焙烧2小时,经筛选得到2%mo-1%ag-0.2%ir-mor/β共晶分子筛催化剂。
46.甲苯与循环未反应的甲苯混合预热后与循环氢压缩机中的循环氢一起进入管式炉加热至408℃;加热后的混合气体进入固定床微型反应器,固定床微型反应器中装有2%mo-1%ag-0.2%ir-mor/β共晶分子筛催化剂,并在反应器上下各填装惰性玻璃珠,反应温度408℃,反应压力3.0mpa,在h2气氛中,原料质量空速为2.0h-1
的条件下进行活性评价,反应产物用气相色谱仪进行定量分析,分析结果列于表1。反应后反应产物出固定床微型反应器,反应产物进行换热、冷却至30℃、气液分离,气体回到循环氢压缩机,液体经汽提塔除去非芳烃化合物后经白土塔稳定处理后分离苯、甲苯、二甲苯以及很少量二甲苯以上芳烃组分,甲苯回循环反应系统与新的甲苯再次进行歧化制苯工艺。
47.对比例1
48.通过等体积浸渍的方法将2wt%mo负载到氢型mor分子筛上,然后将2%mo-mor分子筛、氧化铝、聚乙烯醇、田菁粉按照70:30:2:6的比例混捏、挤条成型并破碎长度为2~4mm的催化剂颗粒。在马弗炉中520℃焙烧2小时,经筛选得到2%mo-1%ag-0.2%re-mor分子筛催化剂。
49.将上述催化剂装入固定床微型反应器中,上下各填装惰性玻璃珠,反应原料为甲苯,在反应温度为405℃,反应压力为3.0mpa,在h2气氛中,原料质量空速为2.0h-1
的条件下进行活性评价,反应产物用气相色谱仪进行定量分析,分析结果列于表1。
50.对比例2
51.通过等体积浸渍的方法同时将4%mo、0.1%rh负载到氢型zsm-5分子筛上,然后将浸渍后的分子筛、凹凸棒土、田菁粉按照70:30:6的比例混捏、挤条成型并破碎长度为2~4mm的催化剂颗粒。在马弗炉中520℃焙烧2小时,经筛选得到4%mo-0.1%rh-zsm-5分子筛催化剂。
52.将上述催化剂装入固定床微型反应器中,上下各填装惰性玻璃珠,反应原料为甲苯,在反应温度为420℃,反应压力为3.0mpa,在h2气氛中,原料质量空速为2.0h-1
的条件下进行活性评价,反应产物用气相色谱仪进行定量分析,分析结果列于表1。
53.对比例3
54.将氢型zsm-5与zsm-12二种分子筛混合(重量比率为4.5/5.5)、硅溶胶、田菁粉按照80:20:5的比例混捏、挤条成型并破碎长度为2~4mm的催化剂颗粒。在马弗炉中520℃焙
烧2小时,经筛选即得到zsm-5/zsm-12共晶分子筛催化剂。然后通过真空浸渍,将4wt%mo负载于催化剂上,经500℃焙烧2小时后得到4%mo-zsm-5/zsm-12催化剂。将4%mo-zsm-5/zsm-12催化剂再通过等体积浸渍的方法将0.1wt%rh负载于催化剂上,得到4%mo-0.1%rh-zsm-5/zsm-12混合分子筛催化剂。
55.将上述催化剂装入固定床微型反应器中,上下各填装惰性玻璃珠,反应原料为甲苯,在反应温度为410℃,反应压力为3.0mpa,在h2气氛中,原料质量空速为2.0h-1
的条件下进行活性评价,反应产物用气相色谱仪进行定量分析,分析结果列于表1。
56.对比例4
57.通过等体积浸渍的方法将3wt%cu和0.5wt%ni负载到氢型mor与zsm-12二种混合分子筛(重量比率为4.5/5.5)上,得到3%cu-0.5%ni-mor/zsm-12分子筛,然后将3%cu-0.5%ni-mor/zsm-12分子筛、氧化铝、甲基纤维素按照80:20:3的比例混捏、挤条成型并破碎长度为2~4mm的催化剂颗粒。在马弗炉中520℃焙烧2小时,经筛选即得到3%cu-0.5%ni-mor/zsm-12混合分子筛催化剂。
58.将上述催化剂装入固定床微型反应器中,上下各填装惰性玻璃珠,反应原料为甲苯,在反应温度为416℃,反应压力为3.0mpa,在h2气氛中,原料质量空速为2.0h-1
的条件下进行活性评价,反应产物用气相色谱仪进行定量分析,分析结果列于表1。上述混合分子筛与共晶分子筛制备的催化剂孔容与比表面积的对比分析结果列于表2。
59.表1:
60.[0061][0062]
表2:
[0063]
[0064][0065]
从与对比例比较可以看出,实施例较对比例的转化率明显得到提高,可以提高9~26%,苯选择性可以提高5~12%,从比表面和孔容对比可以看出,采用共晶分子筛为原料的得到的分子筛比表面和孔容得到明显提高,催化剂的活性得到增强。
[0066]
以上所述实施方式仅为本发明的优选实施例,而并非本发明可行实施的全部实施例。对于本领域一般技术人员而言,在不背离本发明原理和精神的前提下对其所作出的任何显而易见的改动,都应当被认为包含在本发明的权利要求保护范围之内。