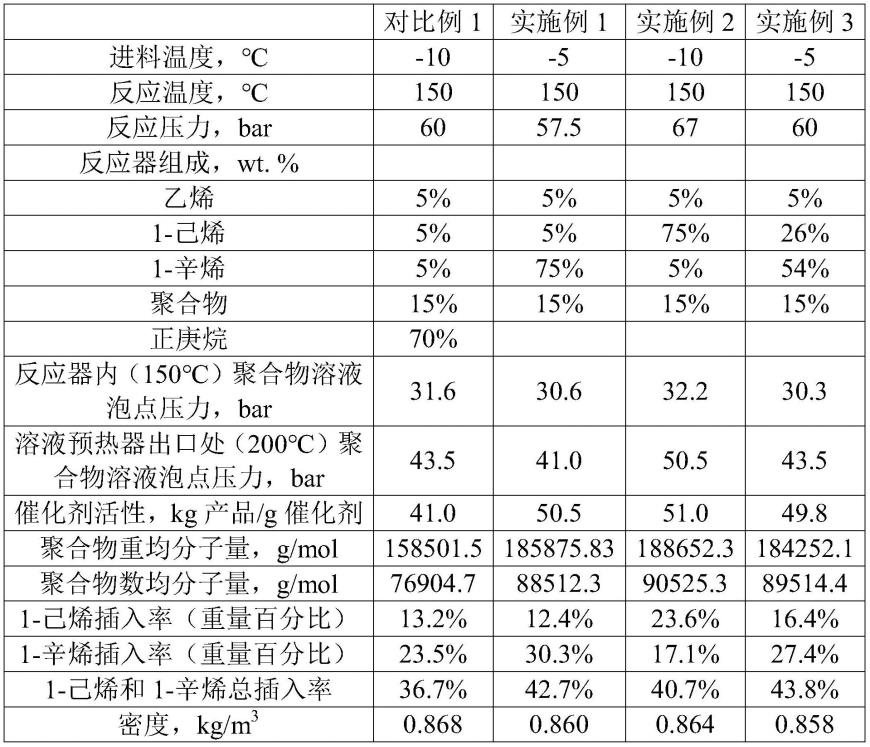
1.本发明涉及烯烃溶液聚合生产技术领域,具体涉及一种乙烯、1-丁烯、1-己烯三元共聚和1-己烯、1-己烯、1-辛烯三元共聚的溶液聚合方法。
背景技术:2.聚烯烃产品广泛应用于不同种类的产品,如管道、汽车部件、薄膜、食品包装、电器外壳等,根据应用场景,市场对聚烯烃材料性能的要求不同。高共聚单体含量的乙烯与α-烯烃共聚物是一类高性能热塑性弹性体,与普通聚烯烃塑料相比,其分子链内共聚单体的含量更高,密度更低,被广泛应用在聚合物改性、医疗等领域。目前工业上热塑性弹性体的生产采用溶液法工艺,溶液法是指将聚合物溶于液体聚合体系的聚合方法,比如惰性溶剂中,溶液聚合是均相液体聚合体系,具有聚合时间短、产品牌号切换方便等特点和优势。热塑性弹性体的溶液聚合方法在40-160℃的温度和低于20mpa的压力下进行,并在超过65wt%惰性溶剂存在的聚合体系中的操作。
3.专利cn 10380999 b公布了一种乙烯和α-烯烃的溶液聚合方法,特征在于采用两种烃类混合的混合溶剂,在溶液聚合压力和温度下,其中一种溶剂处于超临界状态,该方法可以降低反应体系粘度,进而降低聚合反应下游脱除溶剂的难度,即“脱挥”过程的能耗。专利cn 1152062 c公布了一种采用非绝热的环管反应器溶液聚合工艺,溶剂、单体和催化剂等在反应气体内形成流体环路,流体通过热交换器移热。专利cn 1898275 a公布了一种乙烯和至少一种c3-c20的α烯烃在催化剂、稀释剂(溶剂)和氢气存在下的淤浆或溶液聚合方法,其特征在于稀释剂(溶剂)从出口管线回收至氢气进料管线。本领域所知,烯烃溶液聚合的相稳定至关重要,影响操作稳定性。专利cn 115023448 a公布一种避免乙烯-1-辛烯共聚物溶液聚合期间相分离的方法,其通过先对用于乙烯-1-辛烯共聚物溶液聚合的聚合物体系进行建模,进而确定反应压力和温度条件,以确保聚合后的乙烯-1-辛烯共聚物在聚合过程期间完全溶解在溶剂中。cn 114929763 a公布专利一种避免乙烯-1-丁烯共聚物溶液聚合期间相分离的方法。cn 111630071 a提出一种将满足90℃《沸点《130℃的惰性烃进料到所述溶液聚合反应器;和/或在所述聚合反应期间积聚满足90℃《沸点《130℃的惰性烃;和/或将满足90℃《沸点《130℃的惰性烃进料到排出的流出物流中。
4.乙烯和两种烯烃的三元共聚产品具备独特的产品性能,这类产品也广泛使用溶液聚合工艺生产。专利cn 107614541 b公布了一种用于生产乙烯-丙烯-二烯橡胶或基于丙烯的弹性体的连续溶液聚合方法,通过控制加热聚合物溶液的温度和控制分离的压力,提高分离效率。专利cn 105377916 b公布了一种在茂金属和溶剂存在下,制备乙烯-α-烯烃-二烯烃的共聚物的溶液聚合方法,包括在150℃~160℃和5-10bar的条件下,通过气液分离器移除所述溶剂和未反应单体的过程。
5.烯烃溶液聚合工艺采用较多溶剂,溶剂的选择直接影响聚合反应的稳定性、操作性、产品性能等要点,尽管本领域已经提出众多方法,包括采用不同比例的单种或多种烃类作为溶剂以及改进分离流程提高分离效率,但是,仍需要寻找一种新的聚合工艺,制备乙
烯-1-丁烯-1-己烯三元共聚聚合物和乙烯-1-己烯-1-辛烯三元共聚聚合物,既能实现聚合产品多样性,也能简化工艺流程和降低工艺的能耗。
6.定义:
[0007]“溶液聚合”是指将聚合物溶于液体聚合介质,比如惰性溶剂或单体或它们的共混物中,溶液聚合为均相,是指其中聚合物产物溶于聚合介质。这样的体系优选不是混浊的。
[0008]“α-烯烃”是指双键在分子链端部的单烯烃,如1-丁烯、1-己烯、1-辛烯。
技术实现要素:[0009]
本发明提供了一种烯烃三元共聚的溶液聚合方法,通过限定参与聚合的乙烯之外的两种烯烃的种类及其在反应器中聚合物溶液中的质量分数,结合循环流股的套用,从反应器的操作压力和聚合物产品的角度实现了缺乏惰性溶剂的情况下的三元烯烃的溶液均相聚合。
[0010]
如本领域中已知的,烯烃的聚合可以在缺乏聚合惰性溶剂的情况下发生。专利申请cn 114630844 a提供一种用于在缺乏惰性溶剂的情况下,使式ch2=chr1所示的第一烯烃与式ch2=chr2所示的第二烯烃聚合,其中r1是氢或具有1-8个碳原子的烃基,r2是具有3-8个碳原子的烃基。虽然上述专利申请公开了一种无惰性溶剂的两种烯烃聚合的方法,但是未涉及三元共聚,也没有针对三元共聚特点,优化流程的操作条件。三元共聚相比于二元共聚,其不同单体的配比情况更复杂,聚合产品的性质直接受不同单体的在聚合物的插入率影响,而单体的不同浓度会直接影响插入率;此外,溶液聚合相比于其他聚合方法,如气相法和淤浆法,其相稳定非常关键,专利申请cn 114929763 a和cn 111630071 a都公布了维持在溶剂存在的情况下的溶液聚合的相稳定的方法。三元溶液聚合反应器的相稳定取决于反应器的温度(t)、压力(p)和反应器内组成(c),表达为如下:
[0011]
f(t,p,c)=0
[0012]
即,在一定的温度和压力下,为了维持相稳定,其组成必须限定在一定范围内;或者,在一定的温度和组成情况下,其压力必须限定在一定的范围。聚合催化剂的性能对于温度通常是敏感的,即催化剂需要适宜的温度下。对于三元聚合体系,需确定合理的反应器的压力和三种不同单体的质量比,以实现在温和的反应条件下,即较低的压力,得到性能不同的聚合物产品。
[0013]
本发明结合上述内容提出一种烯烃三元共聚的溶液聚合方法,在催化剂存在并且缺乏惰性溶剂的情况下,在反应器中聚合乙烯和其它两种烯烃,得到三元共聚的聚合物,所述其它两种烯烃分别如式ch2=cha和式ch2=chb所示,其中a、b分别为具有1-8个碳原子的烃基,且a和b的碳数加和不小于5,所述其它两种烯烃在所述反应器内的聚合物溶液中的总质量分数是75~90%,具体步骤包括:
[0014]
a)将主催化剂、助催化剂、乙烯和所述其它两种烯烃进料至反应器,在反应器内发生聚合反应后,出料得到聚合物溶液;
[0015]
b)将所述聚合物溶液进料到溶液预热器,获得温度更高的聚合物溶液,再进料到分离和回收单元;或者,
[0016]
直接将所述聚合物溶液进料到分离和回收单元;
[0017]
c)进入分离和回收单元的聚合物溶液进行分离操作,得到聚合物产品以及包含乙
辛烯的三元共聚,而且,针对乙烯-1-丁烯-1-己烯、乙烯-1-己烯-1-辛烯三元共聚的溶液聚合方法,采用本发明的缺乏惰性溶剂的工艺优于采用溶剂的工艺。根据本领域已知,乙烯、1-丁烯、1-己烯三元共聚,适合采用包含5个c的烷烃做溶剂,如戊烷c5h
14
,或7个c和7个c以上的烷烃类做溶剂,后者具有更高的聚合物溶解性能,但是溶剂脱除过程能耗较大,6个c的烷烃做溶剂则会导致溶剂和己烯共聚单体分离困难;乙烯、1-己烯、1-辛烯三元共聚,适合采用包含7个c,如正庚烷c7h
16
,或8个c以及8个以上的烃类做溶剂,后者具有更高的聚合物溶解性能,但是溶剂脱除过程能耗较大。本发明采用的无惰性溶剂聚合方法,避免了分离工段中分离溶剂和共聚单体的步骤,简化了工艺步骤,也降低了脱挥和分离的能耗;同时,本发明采用单个或多个反应器串联,在不同反应器可以聚合得到二元和/或三元共聚产品,提供产品性能和工艺的产品多样性。
[0033]
综合以上技术方案,本发明的方案具有如下优点:(1)简化分离流程和降低能耗;(2)工艺的产品多样品。
附图说明
[0034]
图1、图2为本发明以乙烯-1-己烯-1-辛烯为例的溶液聚合工艺流程简要示意图。
具体实施方式
[0035]
下面结合附图及具体实施例,进一步阐述本发明。应理解,这些实施例仅用于说明本发明而不用于限制本发明的范围。下列实施例中未注明具体条件的操作方法,通常按照常规条件,或按照制造厂商所建议的条件。
[0036]
如图1所示,本发明提供一种溶液聚合的方法,以乙烯、1-己烯和1-辛烯共聚为例,该方法使用的聚合装置主要包括反应单元(1)、分离和回收单元(2),所述反应单元设反应器和进料管,乙烯单体、1-己烯和1-辛烯共聚单体、主催化剂和助催化剂可以全部合并为一个进料管连接该反应器,也可以通过独立的进料管线连接反应器,反应单元还设有循环管线,用于接收来自分离和回收单元的循环流股;从反应器出口获得的聚合物溶液输送至分离和回收单元,分离和回收单元对混合物料进行系列操作,以对物料进行分离、回收、循环,最终得到聚合物产品以及循环流股。值得注意的是,本发明所提出的方法不限于单个反应器的工艺,也可以用于两个反应器串联的工艺或两个以上反应器的工艺。如图2所示,聚合装置主要包括反应器#1(1)、反应器#2(3)、分离和回收单元(2),所述反应器#1设进料管,乙烯单体、1-己烯和1-辛烯共聚单体、主催化剂和助催化剂可以全部合并为一个进料管连接该反应器,也可以通过独立的进料管线连接反应器,反应器#1还设有循环管线,用于接收来自分离和回收单元的循环流股;所述反应器#1出口与反应器#2入口相连,将从反应器#1出口获得的第一聚合物溶液与新鲜和/或循环的乙烯单体、1-己烯和1-辛烯共聚单体混合流股混合后,进入反应器#2反应;从反应器#2出口获得的第二聚合物溶液输送至分离和回收单元,分离和回收单元对混合物料进行系列操作,以对物料进行分离、回收、循环,最终得到聚合物产品以及循环流股。
[0037]
本领域已知,釜式反应器是一种低高径比的圆筒形反应器,反应器内通常设有单层或多层搅拌(如机械搅拌)装置,可在反应器壁处设置夹套,或在反应器内设置换热面,也可通过外循环进行换热。管式反应器是一种呈管状、长径比很大的连续操作反应器,属于平
推流反应器。绝热反应器是指不与外界进行热交换的反应器,非绝热反应器指与外界进行热交换的反应器。
[0038]
本领域已知,聚合催化剂可以是的能将乙烯、1-己烯和1-辛烯共聚的任何催化剂,包括z-n催化剂、茂金属催化剂、后茂金属催化剂,如主催化剂为限定几何构型催化剂(cgc),助催化剂为甲基铝氧烷(mao)等。本领域已知,烯烃聚合中,主催化剂和/或助催化剂可能需要使用惰性溶剂和/或稀释剂共同进料,此时体系中会不可避免的引入少量惰性溶剂和/或稀释剂,这类情况也在本发明所述方法范围内。
[0039]
本发明方法过程可以采用一个或多个搅拌釜反应器或管式反应器,管式反应器为包含静态混合器的反应器,反应器可以为绝热反应器和非绝热反应器。
[0040]
如本领域中已知的,烯烃的聚合可以在缺乏聚合惰性溶剂的情况下发生,专利申请cn 114630844 a提供一种用于在缺乏惰性溶剂的情况下,使式ch2=chr1所示的第一烯烃与式ch2=chr2所示的第二烯烃聚合,其中r1是氢或具有1-8个碳原子的烃基,r2是具有3-8个碳原子的烃基。虽然上述专利申请公开了一种无惰性溶剂的两种烯烃聚合的方法,但是未涉及三元共聚,也没有针对三元共聚特点,优化流程的操作条件。根据本发明提出的方法,乙烯单体、1-己烯和1-辛烯共聚单体,或,乙烯单体、1-丁烯和1己烯共聚单体在主催化剂和助催化剂作用下,发生聚合反应获得聚合物,聚合物是乙烯、1-己烯和1-辛烯,或,乙烯、1-丁烯和1-己烯共聚得到的三元共聚聚合物。本发明方法通过优化反应器内的物质组成,实现了(1)三元共聚溶液法工艺可在较低的反应压力进行,(2)共聚单体在反应器内组成的比例可以实现产品的多样化,(3)无惰性溶剂的溶液聚合方法实现简化回收和分离流程的目的。
[0041]
如本领域已知,通过添加少量链转移常数大的物质可以降低聚合物分子量,合适的链转移剂有许多,例如氢,可以任选地用于溶液聚合中以控制聚合物的分子量。
[0042]
本领域已知,获得聚合物溶液后,需通过分离和回收单元将未反应的单体、共聚单体、氢气以及溶剂(如果存在)和其他由原料引入的杂质组分脱除以获得聚合物产品。未反应单体、共聚单体和溶剂(如果存在)可以通过循环管线进行回用。
[0043]
本领域已知,“分离和回收单元”是一个包括多步回收、分离操作的系统,烯烃溶液聚合工艺的回收和分离单元通常包含多级闪蒸、脱挥、精馏分离等过程。如,专利cn 106414509 b和专利cn 108602900 b所公开了利用多级气-液相分离的溶剂和单体回收方法。“闪蒸分离”是气-液相分离常用的方法,表示通过压力降低导致相分离的分离步骤,专利cn 109715675 b公开的一种利用闪蒸分离器从聚合物溶液中分离烃类化合物的方法,专利cn 108779194 b公开了一种可以减少闪蒸分离是气相中聚合物夹带的聚合物溶液分离方法。
[0044]
本领域已知,聚合物溶液的回收和分离过程通常需要在需要150-220℃左右的高温,聚合物溶液的加热通过设置于反应器出口和分离系统入口之间的溶液预热器实现。
[0045]
本领域已知,催化剂在离开聚合反应器时,通常仍具有一定活性,聚合物溶液进行下游回收和分离单元之前,需使催化剂失活,避免在分离步骤期间聚合物的进一步不受控制的聚合或热降解。如本领域已知,注入失活剂是一种使催化剂失活的方法,如水,硬脂酸钠;也可以通过升高温度使催化剂失活,如专利tw 202134297 a。
[0046]
实施例和对比例采用相同的主催化剂和助催化剂以及相同的流程,区别主要在于
对比例采用惰性溶剂(正庚烷或正戊烷),而实施例没有采用惰性溶剂,在不同实施例中1-己烯和1-辛烯的进料比例不一致、1-丁烯和1-己烯的进料比例不一致以生成不同的产品。下面以各实施例、对比例为例介绍本发明所述方法。
[0047]
实施例1
[0048]
按所述方法进行,采用单个绝热釜式反应器,内设搅拌部件,反应压力57.5bar,停留时间为8min;催化剂选用cgc为主催化剂,mao为助催化剂,分子量调节剂选用氢气,失活剂选用水;进料组成如下:乙烯单体进料90.57kg/h,1-己烯进料45.75kg/h、1-辛烯进料530.3kg/h,加入0.0019kg/h主催化剂与0.019kg/h助催化剂,通入氢气0.01kg/h;进料组分采用全部混合后为一条流股后,换热至-5℃进料至釜式反应器,釜式反应器出口温度为150℃;聚合条件(反应器内组分)如下:乙烯5wt%,1-己烯5wt%、1-辛烯75wt%,聚合物15wt%;分离系统采用三级闪蒸方式,第一级为中压闪蒸,闪蒸罐设16bar,聚合物溶液进入一级闪蒸前,通过溶液预热器加热至200℃;第二级为低压闪蒸,闪蒸罐设3bar,分离温度为190℃;第三级也为低压闪蒸,闪蒸罐设1bar,分离温度为190℃;第一级闪蒸气相经换热器降温至40℃后,直接循环回用至反应单元,第二级和第三级闪蒸气相经热量回收单元后,输送至下游精馏分离单元,以分离部分组分。
[0049]
实施例2
[0050]
按照实施例1的方法进行聚合,区别在于反应器的进料组成如下:乙烯单体进料92.62kg/h,1-己烯进料523.57kg/h、1-辛烯进料50.47kg/h,加入0.0020kg/h主催化剂与0.020kg/h助催化剂,通入氢气0.013kg/h;进料组分采用全部混合后为一条流股后,换热至-10℃进料至釜式反应器,釜式反应器出口温度为150℃;聚合条件(反应器内组分)如下:乙烯5wt%,1-己烯75wt%、1-辛烯5wt%,聚合物15wt%,其余步骤同实施例1。
[0051]
实施例3
[0052]
按照实施例1的方法进行聚合,区别在于反应器的进料组成如下:乙烯单体进料89.50kg/h,1-己烯进料189.77kg/h、1-辛烯进料387.40kg/h,加入0.0020kg/h主催化剂与0.02kg/h助催化剂,通入氢气0.015kg/h;进料组分采用全部混合后为一条流股后,换热至-5℃进料至釜式反应器,釜式反应器出口温度为150℃;聚合条件(反应器内组分)如下:乙烯5wt%,1-己烯26wt%、1-辛烯54wt%,聚合物15wt%,其余步骤同实施例1。
[0053]
对比例1
[0054]
按照实施例1的方法进行聚合,区别在于反应器的进料组成如下:乙烯单体进料96.57kg/h,1-己烯进料46.57kg/h、1-辛烯进料56.86kg/h,溶剂正庚烷466.67kg/h,加入0.0024kg/h主催化剂与0.024kg/h助催化剂,通入氢气0.012kg/h;进料组分采用全部混合后为一条流股后,换热至-10℃进料至釜式反应器,釜式反应器出口温度为150℃;聚合条件(反应器内组分)如下:乙烯5wt%,1-己烯5wt%、1-辛烯5wt%,正庚烷70%,聚合物15wt%,其余步骤同实施例1。
[0055]
实施例1、实施例2、实施例3和对比例1的聚合工艺条件以及关键指标对比情况如表1所示,其反应压力是根据溶液预热器出口的聚合物溶液泡点压力所确定,此处的泡点压力越高则反应器压力越高。根据表1所示结果可知,实施例1在不采用惰性溶剂的情况下,可以实现更低的聚合物压力,同时其回收工段能耗,即脱挥能耗,与采用正庚烷作为溶剂的对比例1相近。相比于实施例1,实施例2在在更高的1-己烯和更低1-辛烯质量分数下,其溶液
预热器出口处的聚合物溶液泡点压力高于对比例1,但其回收工段能耗更低。在实施例2的基础上,实施例3降低反应器中1-己烯质量分数和提高降低反应器中1-辛烯质量分数下,其溶液预热器出口处的聚合物溶液泡点压力跟对比例1相同,且其回收工段能耗更低。实施例1、实施例2和实施例3没有引入惰性溶剂,故不需要在分离工段设置溶剂和共聚单体的分离设备,如精馏塔。本领域已知,精馏分离通常是高投资费用和高操作费用(能耗高)的设备。此外,实施例1、实施例2和实施例3通过调整1-己烯和1-辛烯进料量可以实现不同共聚单体插入率的三元共聚聚合物。
[0056]
表1聚合工艺条件以及关键指标对比
[0057][0058][0059]
实施例4
[0060]
按所述方法进行,采用单个绝热釜式反应器,内设搅拌部件,反应压力165bar,停留时间为10min;催化剂选用cgc为主催化剂,mao为助催化剂,分子量调节剂选用氢气,失活剂选用水;进料组成如下:乙烯单体进料91.5kg/h,1-丁烯进料148.3kg/h,1-己烯进料426.7kg/h,加入0.0021kg/h主催化剂与0.021kg/h助催化剂,通入氢气0.011kg/h;进料组
分采用全部混合后为一条流股后,换热至-14℃进料至釜式反应器,釜式反应器出口温度为150℃;聚合条件(反应器内组分)如下:乙烯5wt%、1-丁烯20wt%、1-己烯60wt%、聚合物15wt%;分离系统采用三级闪蒸方式,第一级为中压闪蒸,闪蒸罐设16bar,聚合物溶液进入一级闪蒸前,通过溶液预热器加热至200℃;第二级为低压闪蒸,闪蒸罐设3bar,分离温度为190℃;第三级也为低压闪蒸,闪蒸罐设1bar,分离温度为190℃;第一级闪蒸气相经换热器降温至40℃后,直接循环回用至反应单元,第二级和第三级闪蒸气相经热量回收单元后,输送至下游精馏分离单元,以分离部分组分。
[0061]
实施例5
[0062]
按照实施例4的方法进行聚合,区别在于反应器的进料组成如下:乙烯单体进料88.0kg/h,1-丁烯进料281.5kg/h,1-己烯进料291.8kg/h,加入0.0020kg/h主催化剂与0.020kg/h助催化剂,通入氢气0.012kg/h;进料组分采用全部混合后为一条流股后,换热至-19℃进料至釜式反应器,釜式反应器出口温度为150℃;聚合条件(反应器内组分)如下:乙烯5wt%、1-丁烯39wt%、1-己烯41wt%、聚合物15wt%,其余步骤同实施例1。
[0063]
实施例6
[0064]
按照实施例4的方法进行聚合,区别在于反应器的进料组成如下:乙烯单体进料92.4kg/h,1-丁烯进料218.2kg/h,1-己烯进料356.1kg/h,加入0.0020kg/h主催化剂与0.02kg/h助催化剂,通入氢气0.013kg/h;进料组分采用全部混合后为一条流股后,换热至12.5℃进料至釜式反应器,釜式反应器出口温度为150℃;聚合条件(反应器内组分)如下:乙烯5wt%、1-丁烯30wt%、1-己烯50wt%、聚合物15wt%,其余步骤同实施例1。
[0065]
对比例2
[0066]
按照实施例4的方法进行聚合,区别在于反应器的进料组成如下:乙烯单体进料94.8kg/h,1-丁烯进料48.7kg/h,1-己烯进料56.4kg/h,正戊烷溶剂466.7kg/h,加入0.0025kg/h主催化剂与0.025kg/h助催化剂,通入氢气0.012kg/h;进料组分采用全部混合后为一条流股后,换热至-10℃进料至釜式反应器,釜式反应器出口温度为150℃;聚合条件(反应器内组分)如下:乙烯5wt%、1-丁烯5wt%、1-己烯5wt%、正戊烷70%,聚合物15wt%,其余步骤同实施例1。
[0067]
实施例4、实施例5、实施例6和对比例2的聚合工艺条件以及关键指标对比情况如表2所示,其反应压力是根据溶液预热器出口的聚合物溶液泡点压力所确定,此处的泡点压力越高则反应器压力越高。根据表2所示结果可知,实施例4在不采用惰性溶剂的情况下,可以实现更低的聚合物压力,同时其回收工段能耗,即脱挥能耗,与采用正戊烷作为溶剂的对比例2相近。相比于实施例4,实施例5在在更低的1-己烯和更高1-丁烯质量分数下,其溶液预热器出口处的聚合物溶液泡点压力等于对比例2,其回收工段能耗更低。在实施例5的基础上,实施例6在降低反应器中1-丁烯质量分数和提高反应器中1-己烯质量分数下,其溶液预热器出口处的聚合物溶液泡点压力同样低于对比例2。实施例4、实施例5和实施例6没有引入惰性溶剂,故不需要在分离工段设置溶剂和共聚单体的分离设备,如精馏塔。本领域已知,精馏分离通常是高投资费用和高操作费用(能耗高)的设备。此外,实施例4、实施例5和实施例6通过调整1-丁烯和1-己烯进料量可以实现不同共聚单体插入率的三元共聚聚合物。
[0068]
值得注意的是,如果在对比例1和对比例2中采用具有更高含碳元素数目的烷烃做
溶剂,虽然可以降低反应压力,但是其脱挥难度更大,同时也需要设置溶剂和共聚单体分离的设备。或者,基于本发明的方法,在采用惰性溶剂的溶液聚合中,增加聚合反应器中共聚单体的质量分数,也存在可以降低反应器压力的方法,但是惰性溶剂和共聚单体的分离无法避免,仍然需要较高的分离设备费用投资和能耗。综述所述,本发明所述的方法更优。
[0069]
表2聚合工艺条件以及关键指标对比
[0070][0071]
此外应理解,在阅读了本发明的上述描述内容之后,本领域技术人员可以对本发明作各种改动或修改,这些等价形式同样落于本技术所附权利要求书所限定的范围。