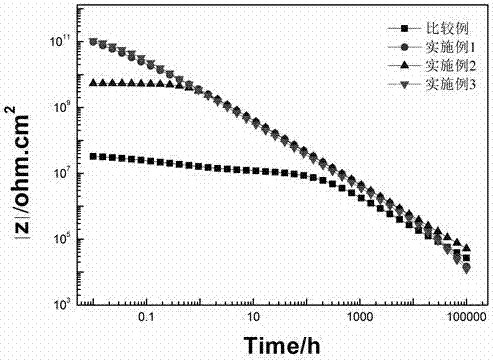
本发明涉及防腐涂料改进,尤其涉及一种稳定型可带锈涂装的环氧防腐涂料,属于涂料
技术领域:
。
背景技术:
:可带锈涂装涂料的应用在保证防腐涂料的施工效果和防护作用的同时,大大降低了对涂装件的表面处理标准,极大的降低了涂料的施工成本,在实际中取得了显著地经济效益。带锈涂料的研究始于上世纪五十年代后期,六十年代中后期开始得到应用。经过几十年的发展,带锈涂料已取得了长足的进展,产品的类型、组成和性能都得到较大的完善。根据作用机理带锈涂料可分为稳定型、转化型和渗透型三种,其中稳定型带锈涂料主要是通过在涂料中添加的活性颜料缓慢的水解而产生络阴离子,其再与活泼的铁锈形成难溶的复杂多酸络合物以达到稳定锈蚀的目的。可作为活性颜料和稳锈剂的物质有磷酸盐(如磷酸锌,三聚磷酸铝等),铬酸盐(如铬酸锌、铬酸钡等)等体系。但稳定的杂多酸生成是在常温、常压下的固相反应,所以反应速度相对较慢,效率较低。此外,铬酸盐不利于环保要求,已限制其使用。因此,需要寻求新的更高效、环保的锈稳定剂。技术实现要素:针对现有技术存在的上述不足,本发明的目的是提供一种新型的稳定型可带锈涂装的环氧防腐涂料,本发明所提出的防腐涂料不但具有较好的锈稳定作用,而且所制备形成的涂层具有较高的附着力和防护性能。本发明的技术方案是这样实现的:一种稳定型可带锈涂装的环氧防腐涂料,由a组分和b两组分组成,a组分与b组分的质量比为60~90:10~30;a组分的质量构成为:环氧树脂15~45%;稀释剂20~40%;锈稳定剂植酸盐3~20%;颜填料10~30%;助剂0.5~5%;b组分的质量构成为:改性酚醛胺固化剂90%~100%;稀释剂0~10%。所述环氧树脂为双酚a环氧树脂、双酚f环氧树脂、改性环氧树脂中的一种或任意两种或三种复配。所述a组分的稀释剂为二甲苯、正丁醇及无水乙醇的混合物;b组分的稀释剂是二甲苯和正丁醇的混合物。所述植酸盐为植酸钠、植酸锌、植酸镁或者植酸钙。所述颜填料为磷酸盐、氧化铁红、钛白粉、玻璃鳞片、云母氧化铁、绢云母、硅微粉、二氧化硅中的两种或多种混合。所述助剂为消泡剂、附着力促进剂、流平剂和分散剂。上述稳定型可带锈涂装的环氧防腐涂料按如下方法制备得到,1)a组分的制备:1.1)将环氧树脂和稀释剂放入反应釜里进行充分搅拌,直至环氧树脂完全溶解于稀释剂中;1.2)在搅拌的情况下,将锈稳定剂植酸盐和颜填料逐一加入到步骤1.1)稀释的环氧树脂中,再加入助剂,继续搅拌至分散均匀,得到浆料;1.3)将步骤1.2)得到的浆料在研磨机中继续研磨,直至颗粒细度小于20μm,得到a组分;2)b组分的制备:如果有稀释剂,则将稀释剂加入改性酚醛胺固化剂中混合均匀即得到b组分,否则改性酚醛胺固化剂直接作为b组分;3)将a组分和b组分混合均匀后即得到可带锈涂装的环氧防腐涂料。本发明采用植酸盐作为锈稳定剂,植酸及植酸盐可从植物中提取,来源广、可再生,同时含有能与金属配位的24个氧原子、12个羟基和6个磷酸酯基,当与金属离子配合时,容易形成多个螯合环,所形成的螯合物稳定性极强,故本发明将植酸盐作为主要的锈稳定剂制备的可带锈涂装涂料具有较高的锈稳定能力,能够直接涂覆于仅除去浮锈的钢结构表面,大大降低了表面处理所需的人力和物力支出,同时对基体有很好的防护作用。此外,本发明的涂料也可以用于无锈的钢结构表面,延长构件的使用寿命。附图说明图1为比较例和实施例在开始浸泡时的电化学阻抗谱。图2为比较例和实施例在3.5%nacl溶液中浸泡600小时的电化学阻抗谱。图3为比较例和实施例在3.5%nacl溶液中浸泡1200小时的电化学阻抗谱。具体实施方式本发明稳定型可带锈涂装的环氧防腐涂料,由a组分和b两组分两部分组成,a组分与b组分的质量比为60~90:10~30;其中a组分的质量构成为:环氧树脂15~45%;稀释剂20~40%;锈稳定剂植酸盐3~20%;颜填料10~30%;助剂0.5~5%;b组分的质量构成为:改性酚醛胺固化剂90%~100%;稀释剂0~10%。其中a组分中的环氧树脂为双酚a环氧树脂、双酚f环氧树脂、改性环氧树脂中的一种或任意两种或三种复配。稀释剂为二甲苯、正丁醇及无水乙醇的混合物。优选地,所述植酸盐为植酸钠、植酸锌、植酸镁或者植酸钙。所述颜填料为磷酸盐、氧化铁红、钛白粉、玻璃鳞片、云母氧化铁、绢云母、硅微粉、二氧化硅中的两种或多种混合。所述助剂为消泡剂、附着力促进剂、流平剂和分散剂。其中消泡剂可选用byk-077、byk-066,附着力促进剂可选用byk-4510,分散剂可选用byk-163、disperbyk-163,流平剂可选用byk-352、byk-354。本发明稳定型可带锈涂装的环氧防腐涂料,按如下方法制备得到,1)a组分的制备:1.1)将环氧树脂和稀释剂放入反应釜里进行充分搅拌,直至环氧树脂完全溶解于稀释剂中;1.2)在搅拌的情况下,将锈稳定剂植酸盐和颜填料逐一加入到步骤1.1)稀释的环氧树脂中,再加入助剂,继续搅拌至分散均匀,得到浆料;1.3)将步骤1.2)得到的浆料在研磨机中继续研磨,直至颗粒细度小于20μm,得到a组分;2)b组分的制备:如果有稀释剂,则将稀释剂加入改性酚醛胺固化剂中混合均匀即得到b组分,否则改性酚醛胺固化剂直接作为b组分;3)将a组分和b组分混合均匀后即得到可带锈涂装的环氧防腐涂料。为了验证本发明防腐涂料性能的改善,以下给出一个按传统方法制备涂料的比较例和三个按本发明方法制备涂料的实施例,然后进行涂层的制备,最后测试不同方法得到的涂料的附着力和耐蚀性。比较例:a组分的制备过程:将100ge44环氧树脂、稀释剂(由二甲苯40g、正丁醇28g、无水乙醇20g混合构成)加入到反应釜中搅拌直至环氧树脂完全溶解稀释后,在搅拌的情况下依次加入颜填料(钛白粉10g、硅微粉20g、云母氧化铁30g、二氧化硅0.5g),三聚磷酸铝20g后,再加入消泡剂1g、附着力促进剂1g、分散剂2.5g、流平剂0.5g,搅拌分散均匀,然后将所得到的浆料在研磨机里研磨至粒径小于20μm,得到a组分。b组分的制备过程:将腰果油改性酚醛胺2040固化剂40g加入稀释剂(由2.1g二甲苯及0.9g正丁醇混合构成)混合均匀后得到b组分。按a组分:b组分=80:15把两组分混合均匀后得到可带锈涂装的环氧防腐涂料。实施例1:a组分的制备过程:将100ge44环氧树脂、稀释剂(由二甲苯40g、正丁醇28g、无水乙醇20g混合构成)加入到反应釜中搅拌直至环氧树脂完全溶解稀释后,在搅拌的情况下依次加入颜填料(钛白粉10g、沉淀硫酸钡10g、氧化铁红20g、二氧化硅0.5g、玻璃鳞片20g),植酸钠20g,再加消泡剂1g、附着力促进剂1g、分散剂2.5g、流平剂0.5g,搅拌分散均匀,然后将所得到的浆料在研磨机里研磨至粒径小于20μm,得到a组分。b组分:腰果油改性酚醛胺2041固化剂50g。按a组分:b组分=80:25把两组分混合均匀后得到可带锈涂装的环氧防腐涂料。实施例2:a组分的制备过程:将80g615环氧树脂、稀释剂(由二甲苯22g、正丁醇13g、无水乙醇20g构成)加入到反应釜中搅拌直至环氧树脂完全溶解稀释后,在搅拌的情况下依次加入颜填料(钛白粉10g、沉淀硫酸钡10g、氧化铁红20g、二氧化硅0.5g),植酸锌30g后,再加入消泡剂1g、附着力促进剂1g、分散剂2.5g、流平剂0.5g,搅拌分散均匀,然后将所得到的浆料在研磨机里研磨至粒径小于20μm,得到a组分。b组分的制备过程:将腰果油改性酚醛胺2015固化剂40g加入0.7g二甲苯及0.3g正丁醇构成的混合溶剂中混合均匀后得到b组分。按a组分:b组分=80:23把两组分混合均匀后得到可带锈涂装的环氧防腐涂料。实施例3:a组分的制备过程:将100ge44环氧树脂、稀释剂(由二甲苯40g、正丁醇20g、无水乙醇20g构成)加入到反应釜中搅拌直至环氧树脂完全溶解稀释后,在搅拌的情况下依次加入颜填料(钛白粉10g,沉淀硫酸钡10g,云母氧化铁20g,二氧化硅0.5g),植酸钙40g,再加入消泡剂1g、附着力促进剂1g、分散剂2.5g、流平剂0.5g,搅拌分散均匀,然后将所得到的浆料在研磨机里研磨至粒径小于20μm,得到a组分。b组分的制备过程:将腰果油改性酚醛胺2040固化剂40g加入2.8g二甲苯及1.2g正丁醇构成的混合溶剂中混合均匀后得到b组分。按a组分:b组分=80:15把两组分混合均匀后得到可带锈涂装的环氧防腐涂料。比较例和实施例制备得到涂料后按下列条件实施后评价:选取制备得到的不同组分的环氧涂料,采用喷涂或涂刷的方式在除去浮锈的碳钢表面制备涂层。涂层干燥后的厚度在150±10μm。利用电化学工作站对涂层的电化学阻抗谱进行测试,表征涂层的耐蚀性。图1~图3为稳定型可带锈涂装的环氧防腐涂料的电化学阻抗谱的测试结果,从图上可以看出,相对于比较例来说,实施例1、2、3的耐蚀性得到了显著的提高。将比较例和实施例1至3制备的稳定型可带锈涂装的环氧防腐涂料进行附着力测试,测试结果列于表1。表1测试项目比较例实施例1实施例2实施例3测试标准浸泡1200小时后涂层附着力(mpa)2.53.83.54.0gb/t5210-2006由表1可以看出,相对于比较例,实施例1、2、3的附着力得到了明显的提高。本发明的上述实施例仅是为说明本发明所作的举例,而并非是对本发明的实施方式的限定。对于所属领域的普通技术人员来说,在上述说明的基础上还可以做出其他不同形式的变化和变动,这里无法对所有的实施方式予以穷举。凡是属于本发明的技术方案所引申出的显而易见的变化或变动仍处于本发明的保护范围之列。当前第1页12